
книги / Перспективные композиционные и керамические материалы
..pdfкой пластичной массы, содержащей водный раствор поливинилацетата. Толщина пленок составляет 200 мкм. После их резки и сушки на поверхность пленок наносят графитовое покрытие, укладывают пленки в слоистые заготовки, подвергают последние прессованию и последующему спеканию. Проведение процесса спекания при температуре 2040 °С в атмосфере аргона позволяет получить материал с плотностью 98 % от теоретической. По сравнению с плотной карбидкремниевой керамикой прочность при изгибе композита (633 МПа) лишь незначительно превышала прочность монолитной керамики (500 МПа). Однако материалы существенно отличались характеристиками разрушения. Трещиностойкостькомпозита достигала величины 15 МПа · м1/2, тогда как трещиностойкостьмонолитной керамики составляла лишь 3,6 МПа · м1/2.
Слоистые структуры подобного типа могут быть созданы не только из плотных керамических пленок, но и из дискретных волокон, например карбида кремния или диоксида циркония. Однако такие материалы характеризуются значительной анизотропией свойств.
В настоящее время большое внимание уделяется созданию функ- ционально-градиентных материалов (ФГМ), свойства которых постепенно изменяются при переходе от одной поверхности к другой.
Так, слоистый керамический композиционный материал, внешние слои которого состоят из ZrO2-3 мол.% Y2O3, c одной стороны, и чистого Al2O3 – с другой, а в промежуточных слоях содержание оксида алюминия увеличивается от 20 до 80 %, полученный методом диффузионной сварки, имеет прочность при изгибе ФГМ ZrO2/Al2O3 при деформации 17 % 375 МПа в условиях приложения растягивающего напряжения со стороны Al2O3 и 1340 МПа – со стороны ZrO2. Эти значения выше прочности монолитных материалов (360 МПа для Al2O3
и 750 МПа для ZrO2-3 мол.% Y2O3).
Направленно-закристаллизованные керамические композиты
Специфическую группу композиционных материалов типа керами- ка–керамика представляют так называемые естественные (in situ) волокнистоупрочненные и слоистые керамические материалы. Их получают путем направленной кристаллизации керамических эвтектик, на-
пример, в системах Al2O3-ZrO2, CaZrO3-ZrO2, MgO-MgAlO4, SiC-B4C, Al2O3-TiB2, ZrO2-ZrC-ZrB2 и др. Методы получения заимствованы из технологии выращивания монокристаллов тугоплавких соединений: зонная плавка, метод внутренней плавленной зоны, метод Бриджмена
171
идр. В основе всех перечисленных методов лежит создание в зоне кристаллизации теплового поля с градиентом температуры. Поскольку структура композита формируется «in situ», исключаются трудоемкие операции получения волокон и последующего введения их в матрицу, технологический процесс представляет собой единую операцию, обеспечивающую при оптимальных параметрах равномерное распределение в матрице армирующих волокон.
Характерной особенностью направленно-закристаллизованных композитов обычно является четко выраженная структурная анизотропия составляющих фаз, что, в свою очередь, приводит к анизотропии физических характеристик и позволяет формировать не только собственно материал, но и заготовки изделий с определенной ориентацией структуры.
Основное достоинство керамических материалов, полученных методом направленной кристаллизации, – высокая термическая стабильность структуры, т.е. способность сохранять композитную структуру вплоть до температуры, составляющей 0,98 от температуры плавления, в силу чего эти материалы способны сохранять прочностные и другие структурно чувствительные свойства при эксплуатации в условиях высоких температур. Например, направленно-закристаллизованная эвтек-
тика Al2O3-ZrO2 сохраняет предел прочности при растяжении 520 МПа до температуры выше 1600 ºС. Поэтому эти материалы рассматриваются как потенциальные заменители суперсплавов в турбинных лопатках ГТД, работающих без охлаждения. Бинарные направленно-закристаллизо- ванные карбидные эвтектики обладают более высокой износостойкостью в сравнении со спеченными монолитными материалами и могут быть рекомендованы для использования в парах трения, в том числе
ивысокотемпературных. Благодаря своим уникальным анизотропным свойствам многие композиционные материалы из направленно-закрис- таллизованных керамических эвтектик могут найти применение в качестве текстурированных материалов в электронных приборах, как оптические отражатели, пьезоэлектрики и ферромагнетики. Направленно-
закристаллизованная эвтектика СаО-P2O5 может быть использована как материал для высокопрочных биологически активных имплантатов.
Весьма перспективными являются композиционные материалы, содержащие бориды переходных и редкоземельных металлов. Эти соединения отличаются высокими термодинамической стабильностью,
172
температурами плавления, твердостью; во многих случаях они обладают интересными функциональными свойствами: высокой электропроводностью, устойчивостью к распылению, малыми значениями работы выхода электронов, специфическими ядерными свойствами.
Для квазибинарных систем боридных фаз редкоземельных и переходных металлов МеIВ6 и МеIIВ2 характерен эвтектический тип взаимодействия. Для них характерно также практическое отсутствие взаимной растворимости компонентов в твердом состоянии, что обеспечивает стабильность фазового состава. Благодаря эвтектическому типу взаимодействия боридных фаз и особенности их структуры в процессе совместной кристаллизации происходит образование двух взаимно проникающих типов кристаллитов, причем кубическая гексаборидная фаза кристаллизуется в виде крупных кристаллов, а гексагональная диборидная фаза кристаллизуется в видепластинчатых или игольчатых кристаллов.
В процессе кристаллизации расплава смеси фаз LaB6-ZrB2 степень совершенства структуры в основном определяется как составом материала, так и условиями кристаллизации. Во всех случаях формируется матричная фаза гексаборида лантана, в которой равномерно распределены волокна (нитевидные кристаллы) диборида циркония. Ориентация волокон соответствует направлению теплоотвода. Размеры нитевидных кристаллов обычно 0,4–0,6 мкм в диаметре при отношении длины к диаметру 500–1000.
Регулярность структуры композиционных материалов на основе боридов существенно зависит от степени отклонения от эвтектического состава: отклонение в ту или иную сторону изменяет структуру и резко ухудшает механические свойства композиций.
Структура полученных материалов также существенно зависит от параметров технологического процесса кристаллизации. При малой (<5 мм/мин) скорости перемещения расплавленной зоны вследствие всестороннего теплоотвода ориентированная структура не реализуется. Повышение скорости кристаллизации от 5 до 10 мм/мин приводит к формированию более однородного материала с равномерным распределением волокон, практически постоянных по толщине; средний размер волокон составляет 0,25 мкм (рис. 5.13, 5.14). При скоростях кристаллизации более 12,5 мм/мин гомогенная расплавленная зона не успевает сформироваться, и полученная структура оказывается крайне неоднородной.
173
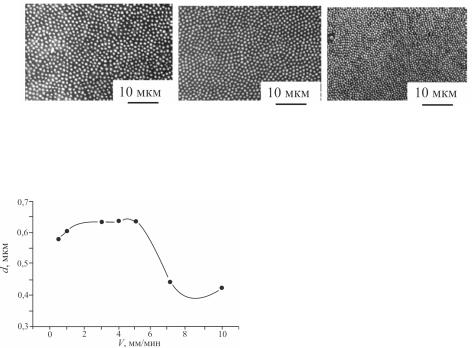
а б в
Рис. 5.13. Изменение структуры композита LaB6-ZrB2 в зависимости от скорости кристаллизации, мм/мин: а – 3; б – 5; в – 10
Кроме того, материал характеризуется появлением пористости. Также с возрастанием скорости подачи заготовки в зону происходит увеличение количества волокон, приходящихся на 1 см2 площади. Природа вводимого диборида IV группы периодиче-
ской системы (TiB2, ZrB2, HfB2)
также влияет на изменение этой характеристики: по мере возрастания атомной массы металла, образующего диборид, возраста-
ет количество армирующих волокон в 1 см2 площади.
Причиной задержки формирования и развития трещин в материа-
лах такого |
типа, а |
следовательно, повышения |
трещиностойкости |
и прочности |
является |
энергоемкое взаимодействие |
фронта трещины |
с элементами структуры, в данном случае с дисперсными нитевидными кристаллами второй фазы, которое приводит к тому, что разрушение волокон происходит не в плоскости распространения трещины, а на некотором расстоянии от нее. Процесс разрушения сопровождается вытягиванием волокна из матрицы, что требует дополнительных энергетических затрат на развитие трещины.
Полученные самоармированные композиционные материалы обладают высокой прочностью. Их механические свойства значительно превосходят аналогичные характеристики индивидуальных фаз. Материалы, соответствующие эвтектическому составу, обладают наибольшими значениями прочностных свойств: их эффективная вязкость разрушения K1С составляет15–25 МПа·м1/2, предел прочности при изгибе 100–1200 МПа.
174
|
|
|
Таблица 5.8 |
Характеристики механических свойств |
|||
|
эвтектических сплавов LaB6-МеB2 |
||
|
|
|
|
Материал |
|
Предел прочности |
Трещиностойкость, |
|
при изгибе, МПа |
МПа·м1/2 |
|
LaB6-ZrB2 |
|
1000–1320 |
15,2–18,3 |
LaB6-HfB2 |
|
1150–1250 |
11,0–14,4 |
LaB6-TiB2 |
|
388–656 |
15,2–16,5 |
В табл. 5.8 представлены механические свойства эвтектических сплавов LaB6-МеB2. При избытке матричной фазы (LaB6) появляются неармированные участки, что резко снижает K1С материала. При избытке армирующей фазы (ZrB2) нарушаются однородность волокон по длине и их распределение, что также приводитк снижениюK1С до 9–10 МПа·м1/2.
5.1.4. Применение керамических композиционных материалов
Керамика, армированная нитевидными кристаллами или дискретными волокнами, благодаря сочетанию высоких прочностных свойств, трещиностойкости, твердости, жаростойкости – перспективный материал для изготовления деталей и узлов двигателей внутреннего сгорания, других энергетических установок, режущего инструмента, фильер для волочения металлов, металлургической оснастки, неперетачиваемых пластин для металлорежущего инструмента. Такие пластины в процессе эксплуатации подвержены экстремальным воздействиям высоких давлений и температур. Типичными являются удельные нагрузки 500–800 МПа и температуры выше 1000 °С. Армирование оксидной керамики нитевидными кристаллами карбида кремния позволяет не только повысить трещиностойкость, твердость и термостойкость, но и значительно улучшить статистическую однородность распределения свойств материала, что значительно повышает эксплуатационные характеристики керамического режущего инструмента. Неперетачиваемые пластины из алюмооксидной керамики, армированной нитевидными кристаллами SiC, целесообразно применять для высокоскоростной механической обработки высокопрочных сталей, жаропрочных никелевых сплавов, чугунов. Скорости обработки таких материалов при использовании керамических композиционных сменных пластин
175

могут быть повышены в несколько раз по сравнению со скоростями обработки инструментом из твердых сплавов.
При создании авиационных двигателей нового поколения для снижения веса, уменьшения расхода топлива и уменьшения вредных выбросов используются легкие и очень стойкие огнеупорные материалы – керамические композиты.
Керамические композиционные материалы, армированные непрерывными волокнами, могут найти применение при изготовлении теплообменников, жаростойких труб, сопел различного назначения. Такие материалы на основе карбида кремния сохраняют высокие механические свойства при температурах до 1250 °С.
Керамические композитные материалы широко используются в конструкции гиперзвуковых летательных аппаратов (орбитальный БПЛА X37, ракета X51A WaveRider). При полeте на высокой скорости температура поверхностей передних кромок плоскостей может достигать 2700 °С, а температура в камере сгорания прямоточного воздушнореактивного двигателя со сверхзвуковой камерой сгорания (scramjet) – 3000 °С. Для обеспечения тепловой защиты и высоких прочностных характеристик конструкции при аэродинамическом нагреве используются многослойные сэндвич-структуры Ceramic Matrix Composite/Foam Core (рис. 5.15).
Рис. 5.15. Керамический матричный композит с внутренним слоем из пористой керамики
176
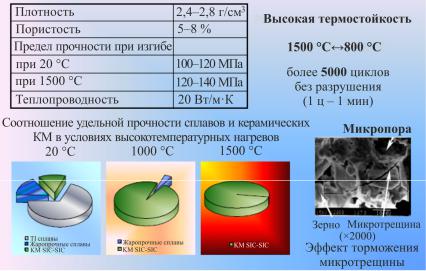
Основным преимуществом таких материалов по сравнению с теплозащитными плитками, используемыми в конструкции Space Shuttle или «Буран», является высокая прочность, позволяющая встроить теплозащиту в несущую конструкцию. Композитная сэндвич-панель, имеющая плотность порядка 1,06 г/cм3, обладает высокой прочностью и жесткостью. Коэффициент теплового расширения, керамического композитного материала обшивки и пористого керамического материала сердцевины подобраны таким образом, чтобы обеспечить градиент температур на наружной и внутренней поверхности сэндвич–панели около 1000 °С без расслоений и растрескивания.
В камере сгорания scramjet используются керамические композиты на основе высокотемпературной керамики. Такая керамика, состоящая из диборида циркония и карбида кремния, спекается с помощью электроискровых разрядов высокой частоты (так называемый метод Sparc Plasma Sintering). По сравнению с методом горячего изостатического прессования Sparc Plasma Sintering позволяет получить более плотную структуру.
Рис. 5.16. Характеристика керамического композиционного материала SiC-SiC (ВМК-3)
Во Всероссийском институте авиационных материалов (ВИАМ) разработан керамический композиционный материал на основе SiC-SiC (ВМК-3), предназначенный для изготовления теплонагруженных узлов
177
и деталей конструкционного назначения с рабочей температурой до 1550 °С в окислительной среде. Обладает низкой удельной массой (в 2–3 раза легче сталей), повышенной эрозионной, химической и коррозионной стойкостью в агрессивных средах; при эксплуатационных температурах обладает эффектом самозалечивания микродефектов и восстановления до 100 % исходных механических характеристик. Отличительной особенностью керамического композиционного материала SiC-SiC (ВМК-3) является сверхвысокая стойкость при термоциклических нагрузках в продуктах сгорания топлива: 1550–800 °С более 7000 циклов (1 цикл – 1 мин) без разрушения (рис. 5.16).
5.2. Углерод-углеродные композиционные материалы
Углерод-углеродные композиционные материалы (УУКМ) – одни из наиболее известных современных композитов. Одинаковая природа и близкие физико-химические свойства обеспечивают прочную связь волокон с матрицей и уникальные свойства этим КМ. Материалы этого типа часто считают самыми перспективными для изготовления конструкций, работающих при высоких температурах. Они используются для изготовления носовых обтекателей ракет, сопловых блоков, лопаток турбин, деталей тормозных устройств самолетов, высокотемпературных подшипников ядерныхсиловыхустановок, других важных деталей.
УУКМ состоят из углеродной (графитовой) матрицы, упрочненной углеродным (графитовым) волокном. Углеродные волокна используются не только как упрочняющие элементы, они препятствуют распространению трещин. Основные достоинства УУКМ, определяющие их широкое применение, заключаются в высокой прочности, малой плотности, высокой теплостойкости, стойкости к тепловому удару и облучению. В кислой среде углеродные материалы сохраняют работоспособность до 773 К, в инертной среде и в вакууме – до 3273 К. Они способны выдерживать перепад температур, достигающий 1000 К/см. В зависимости от структуры предел прочности на растяжение углеродуглеродных композитов изменяется в диапазоне 100...1000 МПа. Механические свойства УУКМ в большей степени зависят от схемы армирования. Наиболее предпочтительные является многоосное армирование, при котором армирующие волокна расположены в трех и более направлениях.
178
Уникальной особенностью углерод-углеродных КМ является увеличение прочности в 1,5–2,0 раза и модуля упругости при повышении температуры. К их недостаткам относят склонность к окислению при нагреве до температур выше 500 °С в окислительной среде. В инертной среде и вакууме изделия изуглерод-углеродных КМ работают до 3000 °С.
5.2.1. Углеродные волокна
Уникальным видом упрочняющих элементов являются углеродные волокна (УВ). Композиционные материалы, матрица которых армирована УВ, в настоящее время применяются в машиностроении, авиастроении, космической технике и ряде других областей.
Хотя первые УВ были получены в конце ХIХ века, основной интерес к ним проявился 60-е гг. ХХ в. Объем применения УВ при изготовлении КМ постоянно возрастает, что объясняется высоким уровнем их механических свойств, которые перекрывают широкий диапазон значений модуля (200–700 ГПа) и прочности (2000–4000 МПа). УВ имеют высокую теплостойкость, они разнообразны по электрофизическим свойствам (от полупроводников до проводников с проводимостью, характерной для металлов) и могут иметь сильно развитую поверхность (1000–2000 м2/г). Они отличаются высокой жаропрочностью до 2500 °С
винертной среде, но требуют специальной защиты от окисления для работы на воздухе при температурах выше 400 °С.
Широкий спектр существующих типов углеродных волокон позволяет получать материалы с уникальным набором теплофизических, химических, механических характеристик в сочетании с возможностью управления анизотропией перечисленных свойств. Каждый тип волокна обладает индивидуальными свойствами, влияющими на технологические параметры изготовления композита.
Классификация углеродных волокон. В зависимости от условий об-
работки углеродные волокна делятся на частично карбонизованные, карбонизованные и графитированные. Температура термической обработки частично карбонизованных волокон составляет до 500 °С, содержание углерода до 90 мас.%. У карбонизованных волокон температура термической обработки составляет 900...1500 °С, содержание углерода
вних 91...98 мас.%. Температура термической обработки графитированных выше 1500 °С и достигает 3000 °С. Углерода в них содержится более 99 %.
179
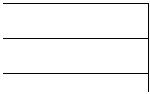
Для проведения графитизации, как правило, используют карбонизованные волокна. Карбонизация и графитизация проводятся в вакууме, различных контролируемых средах (метан, азот, аргон и др.), а также в угольной, коксовой и графитовой засыпках.
По уровню механических характеристик УВ подразделяются на высокопрочные, низкомодульные и высокомодульные волокна (табл. 5.9). Механические и физико-химические свойства УВ в большой степени зависят от типа исходного сырья и технологии их изготовления.
Таблица 5.9
Классификация углеродных волокон, основанная на физико-механических свойствах
Классификация |
Прочность на разрыв, МПа |
Модуль Юнга, ГПа |
Высокопрочные |
3000–7000 |
200–300 |
Высокомодульные |
2000–3000 |
350–700 |
Низкомодульные |
500–1000 |
30–50 |
Средней прочности |
1000–2000 |
50–150 |
5.2.2. Изготовление углеродных волокон
Производство углеродных волокон основано на термической деструкции органических полимеров в инертной среде. Во время разложения полимеров образуются летучие продукты, и остается твердый коксовый остаток. Преобразование органических волокон в углеродные волокна связано с протеканием сложных реакций, кардинальным изменением структуры при сохранении элементов первоначального полимерного скелета. Структура исходных волокон – линейно-кристалли- ческие образования (фибриллы), ориентированные по оси волокна. Диаметр фибрилл из вискозы составляет 300–500 Å, из полиакрилонит-
рила – 73–150 Å.
Для получения УВ используют только волокнистые полимеры, которые должны отвечать ряду требований:
•исходные волокна должны сохраняться как единое целое на всех стадиях производства УВ;
•они не должны образовывать «расплава» ни на одной из стадий производства;
180