
книги / Научные основы технологической подготовки группового производства
..pdfПрессовая установка ПФ-200 предназначена для изготовления крупно габаритных литейных форм методом прессования в опоке 2100 X 1500 х X 750 мм для индивидуального и мелкосерийного производства чугунного литья (рис. II. 16).
Она состоит из специального гидравлического пресса 1 усилием 200 Т, подвижного стола 2, двух гидравлических цилиндров 3 привода стола, двух гидравлических съемников 4 для протяжки форм, двух электро тележек для фигурного и плоского пуансонов 5, бункера 6 для формо вочной земли (рис. II. 17), пластинчатого питателя 7 и несущей металло конструкции 8 тележек пуансонов.
Прессовая установка ПФ-200 работает следующим образом.. На под вижной стол 2 устанавливается два модельных агрегата — один низа формы и один верха формы. После установки модельных агрегатов и опок стол 2 гидроцилиндром 3 подается под пресс 1 и опока низа из бункера 6 пластинчатым питателем 7 через отверстие в верхней части пресса 1 запол няется формовочной смесью до уровня наполнительной рамки. Для прес сования деталей сложной конфигурации используется электротележка с фасонным пуансоном, которая выезжает и устанавливается над опокой; перемещением подвижной траверсы пресса осуществляется прессование. После обжатия формы фасонным пуансоном производится досыпка формо вочной земли и форма окончательно допрессовывается плоским пуансоном второй электротележки. Запрессованная форма низа подается подвижным столом 2 на позицию протяжки, где происходит протяжка формы, съем ее с гидравлического съемника 4 краном, кантовка формы на траверсе крана и подача ее на сборку. После изготовления формы низа точно по такому же технологическому процессу изготовляется и форма верха. Формы для деталей простой конфигурации прессуются только плоским
.пуансоном.
Производительность установки для максимальной опоки — 15 полуформ в час. Установку обслуживает один человек. Установка дистанционно управляется с одного пульта, но может работать и по автоматическому циклу. Занимаемая площадь 11 X 10 м (без насосной). Высота установки над уровнем пола 5,5 м.
Применение метода прессования форм под высоким давлением в соче тании с групповым методом открывает большие возможности автоматиза ции всего производственного цикла получения литых заготовок в условиях индивидуального и серийного производства.
Теоретические разработки и практика работы показали, что применение группового метода при литье в песчаные формы в условиях мелкосерий ного производства позволяет:
1) механизировать приготовление формовочной смеси, транспорти ровку ее к формовочным машинам, подачу горелой земли к бегунам;
2)отказаться от ручной формовки и широко использовать машинную формовку;
3)внедрить конвейерную заливку; при отсутствии конвейера установить линию приводных рольгангов для транспортировки опок на заливку и вы бивку;
4)производить заливку в непосредственной близости от плавильных агрегатов, что способствует решению задачи транспортировки жидкого металла к формам;
5)сосредоточить выбивку в одном месте на выбивной решетке.
Все это обеспечивает организацию механизированных литейных цехов в условиях мелкосерийного производства.
На рис. II. 18 показана схема механизированного участка сборки, заливки и выбивки форм. Сборка форм производится на рольгангах /,
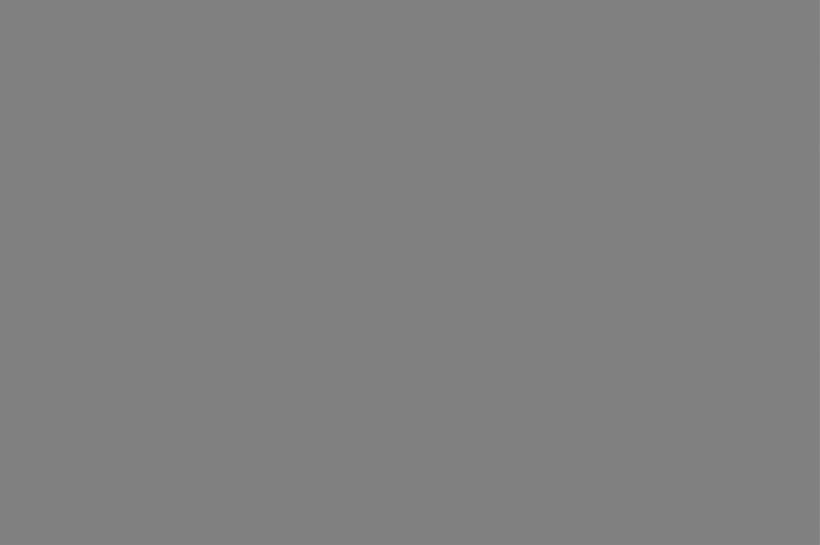
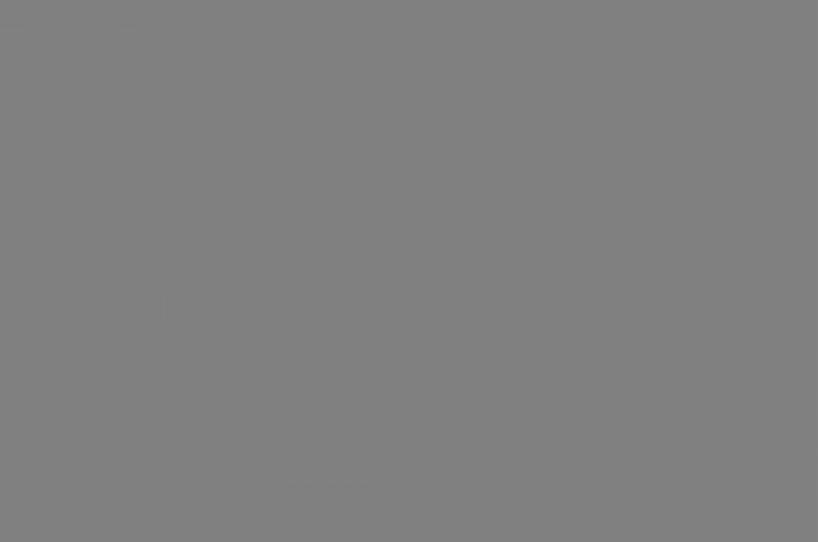
идущих от формовочных машин, на которых производится формовка раз личных групп деталей. Собранные формы поступают на площадки 2 кон вейера и передвигаются к месту заливки 3. Залитые формы охлаждаются в охладительном тоннеле 4 и пневматическим подъемником подаются на выбивную решетку 5. После выбивки пустые опоки тем же подъемником устанавливаются на площадках конвейера и возвращаются к формовочным машинам.
Дальнейшие операции обрубки и очистки литья также механизируются. Однако внедрение автоматизированных процессов формовки, заливки, выбивки и очистки, изготовления смесей и стержней требует выполнения
ряда условий.
Например, одним из условий автоматизации формовки является приме нение одного размера опок на всей автоматической линии, так как при раз личных размерах опок автоматизировать формовку очень трудно. Решение этой первой задачи требует специализации производства литья — по раз весу и конфигурации. И только применение метода групповой формовки позволяет в опоках одного размера формовать детали широкой номенкла туры.
Вторая задача — это автоматизация заливки. Даже в лучших механи зированных и автоматизированных литейных цехах заливка чугуна и стали производится вручную. Для того чтобы не останавливать опоки в момент заливки, ковш с металлом и сам заливщик перемещаются со скоростью движения опок, но тем не менее заливка производится вручную.
Одним из интереснейших путей решения этой задачи является приме нение метода групповой заливки. Опоки должны быть разбиты на несколько групп по весу заливаемого металла, например по 50, 70 и 90 кг. В соответ ствии с этим должны быть предусмотрены подвижные ковши, в которые на весовом дозаторе наливается заданное количество металла.
На автоматической линии металл из ковша полностью выливается в опоку. Если не удается подобрать группу отливок, суммарный вес кото рых соответствовал бы емкости ковша, то формуется небольшая дополни тельная прибыль для избыточного металла. Этот пример хорошо иллюстри рует возможности использования группового метода при решении такой сложной технической задачи, как автоматизация заливки.
Третья задача — применение группового метода при автоматизации процесса остывания форм. Обычно на конвейер для остывания ставятся все опоки, причем приходится подбирать скорость конвейера по наиболее медленно остывающей детали. Например, если такая деталь требует на остывание 2 ч, то весь конвейер двигается с такой скоростью, чтобы каждая из опок находилась на нем 2 ч. Это увеличивает длину конвейера и площадь, занимаемую им в цехе. При этом отливки сходят с конвейера с различной температурой.
В цехе остывания, использующем групповой метод, все детали разбиты на восемь групп по срокам остывания — от 2 ч до 15 мин. В соответствии с этим в цехе имеется восемь конвейеров остывания со скоростью пере мещения опок от 2 ч до 15 мин. В зависимости от группы деталей опокам задается адрес конвейера остывания, куда они автоматически передаются. Такая система позволяет более чем в 62 раза уменьшить площадь цеха осты вания и получать отливки, остывшие примерно до одинаковой темпера туры.
Таким образом, практика работы показывает, что групповой метод изго товления отливок создает все условия не только для организации механи зированных, но и полностью автоматизированных литейных участков и цехов.

оказывается большей, чем наверху. Машины с вертикальной осью враще ния обычно применяются и для получения мелких фасонных отливок в пес чаных формах.
При изготовлении фасонных отливок применяются два способа. Пер вый способ (рис. II. 19, в) используется при получении сравнительно круп ных отливок, когда ось отливки совпадает с осью вращения машины. При втором способе (рис. II. 19, г) оси отливок не совпадают с осью враще ния машины, но заполнение полостей комплекта форм 4 происходит от центрального питания под действием центробежной силы.
При необходимости изготовления фасонных отливок используются песчаные стержни, устанавливаемые в формы.
Наиболее эффективное применение способа центробежного литья в ус ловиях индивидуального и мелкосерийного производства возможно только на основе группового метода с широким использованием нормализованной технологической оснастки.
В данном случае все датели классифицируются на группы в зависимо сти от технических характеристик центробежных машин, габаритных раз меров и веса деталей.
Необходимо, чтобы за каждым типом машины была закреплена вполне определенная группа деталей, так как в этом случае переналадка машины с одного размера отливки на другой внутри группы не требует больших затрат времени.
В качестве примера может быть рассмотрен опыт использования груп пового метода при отливке центробежным способом деталей на Коломен ском заводе тяжелого станкостроения.
Отливки, получаемые на заводе центробежным способом, имеют сле дующие размеры (в мм):
по D наружному |
от 60 |
до550 |
по Dj внутреннему |
от 30 |
до500 |
по длине L |
от 40 |
до600 |
Т а б л и ц а II. 7
Конструкции и мощности машин для центробежного литья, в соответствии с которыми проведена классификация отливок по габаритным размерам
|
|
Характеристика |
|
|
Тип центробежной машины |
наибольшие |
максимальная |
мощность |
габарит |
размеры |
скорость |
|||
|
отливки |
вращения |
двигателя |
машины |
|
в мм |
вала |
в кет |
в м |
|
|
в об!мин |
|
|
Пятишпиндельная пневмати ческая машина с вертикальным валом
Машина с горизонтальным ва лом
Машина с горизонтальным ва лом двухконсольного типа .
Машина с пневматическим тол кателем
Машина с изложницей, сво бодно покоящейся на опорных роликах
'■§х ш |
2000 |
2.8 |
1.8x0,55 |
|
|
|
|
ï*» |
1100 |
2,8 |
1.6x0,8 |
1000 |
4,5 |
3,0x0,1 |
|
S*» |
900 |
4,5 |
3,0x1,5 |
S*» |
360 |
4,5 |
3,0x2,4 |
В зависимости от мощности и конструкции имеющихся на заводе машин (табл. II. 7) весь диапазон размеров отливок разбит на семь групп и для каждой группы размеров изготовлены специальные изложницы.
Первая группа скомплектована из деталей типа втулок с внутренним диаметром от 30 до 100лш, высотой от 40до 100 мм. Отливка деталей произ водится на центробежной машине с вертикальной осью вращения. Излож ница (рис. И. 20) состоит из стального корпуса 1, на дно которого поме щается графитовый вкладыш 2, устраняющий приваривание отливки к кор пусу, чугунной гильзы 4 и крышки 5 с различными диаметрами централь ного отверстия. Для регулирования высоты отливки применяются чугун
ные сменные вкладыши 3. Закрепление |
|
||
крышки 5 обеспечивается центробежными |
|
||
замками 6. |
|
|
|
На рис. И. 21 показана другая конст |
|
||
рукция изложницы со сменными стаканами |
|
||
2, устанавливаемыми на корпусе 1 и за |
|
||
крепляемыми |
с помощью центробежных |
|
|
замков 3. |
второй, третьей и четвертой |
|
|
Отливки |
|
||
групп имеют наружный диаметр доЗООлш; |
|
||
изготовляются они на машинах с горизон |
|
||
тальной осью вращения в изложницах, |
|
||
одна из конструкций которых показана |
|
||
на рис. II. 22. Изложница состоит из |
|
||
стального корпуса 3, имеющего с одной |
|
||
стороны хвостовик с резьбой и направ |
£ис*Ч* 20*Изложннца АЛЯ центР°- |
||
ляющей расточкой, |
обеспечивающей креп- |
||
ление изложницы |
на валу центробежной |
бежнои маш"7алосн "еРтикалы,ым |
машины. В корпус вставляется чугунная гильза 2, в которую для регулирования длины получаемой отливки
помещается чугунный вкладыш 1. Гильза в корпусе закрывается чугун ной крышкой 4, закрепляемой клиньями 5, которые обеспечивают про
стое и надежное крепление крышки. |
(пятая и |
шестая группы) |
||
Для |
отливки втулок больших диаметров |
|||
применяются сборные изложницы (рис. II. 23), которые состоят из |
||||
корпуса 5 и планшайбы 3, соединенных |
между |
собой |
болтами. |
|
Такая |
конструкция позволяет многократно |
использовать |
планшайбу |
вслучае износа и смены корпуса и упрощает изготовление изложницы.
Вкорпус вставляется сменная гильза 4, опирающаяся на поддон 2, на который при удалении отливки передается действие пневматического толкателя. Гильза в корпусе закрывается крышкой 3, закрепляемой
клиньями 7. Длина отливки регулируется сменным вкладышем 1. Излож ница крепится на валу центробежной машины с пневматическим тол
кателем. |
|
по размерам разбиты на семь групп, |
В связи с тем, что отливки |
||
для каждой |
из них спроектирован стандартный набор гильз и |
|
крышек. Для |
уменьшения веса |
отливок и улучшения их охлаждения |
гильзы для больших отливок имеют ребристую поверхность. Материалом для изготовления гильз, крышек и вкладышей служит чу
гун марки СЧ15-32.
Пользуясь перечисленной выше оснасткой, можно получить отливку в пределах диаметра от 60 до 550 мм, кратного пяти.
Для получения отливки, длина которой больше длины стандартной оснастки, необходимо изготовить специальную крышку (рис. II. 24, де таль 7), в которой выполняется часть отливки. Если по наружному
|
Р а з м е р ы о т л и в к н |
|
Т и п с т а к а н а |
|
|
|
D |
Н |
I |
51— 65 |
4 0 -1 2 0 |
II |
6 6 - 8 0 |
40— 120 |
I I I |
81— 95 |
3 0 - 1 2 0 |
IV |
9 6 - 1 1 0 |
30— 120 |
V |
111— 120 |
20— 120 |
V I |
121 -1 3 0 |
20— 120 |
Рнс. II. 21. Изложница для центробежной машины
5 Ц 3 2 1
№ и з л о ж |
D |
D i |
|
н и ц ы |
|||
|
|
||
2 |
152 |
280 |
|
3 |
202 |
330 |
|
4 |
302 |
430 |
Рис. II. 22. Изложница для центробежной машины с го ризонтальным валом
7 6 5 4
№ и з л о ж |
D |
D i |
|
н и ц ы |
|||
|
|
||
5 |
357 |
490 |
|
6 |
402 |
540 |
Рис. II. 23. Изложница для центробежной машины с пневматическим толкателем
контуру отливка является нецилиндрической или имеет ступенчатую форму, то делается специальная гильза (рис. II. 24, деталь 2), воспроиз водящая контур отливки.
Отливка втулок больших диаметров производится на центробежных машинах с изложницей, свободно покоящейся на опорных роликах. Изложница (рис. II. 25) состоит из корпуса 4, имеющего два кольцевых
Рис. II. 25. Изложница для роликовой центробежной машины
пояска, которыми она опирается на ролики 7, передающие ей враще ние. Сменные гильзы 3, имеющие ребристую поверхность, опираются на поддон 5. Длина отливки регулируется посредством вкладыша 6. Крышка 1 крепится тремя клиньями 2. В донной части корпуса имеется отверстие для вывода газов, через которое также осуществляется выбивка,отливки.
3. ЛИТЬЕ ПОД ДАВЛЕНИЕМ
Литье под давлением позволяет значительно сократить продолжитель ность производственного цикла, получить дешевые и сложные отливки с повышенной точностью размеров и чистотой поверхности, большую эко номию металла.
Современная техника литья под давлением дает возможность получать отливки весьма сложной конфигурации с тонкими стенками, которые