
книги / Механика материалов. Методы и средства экспериментальных исследований
.pdf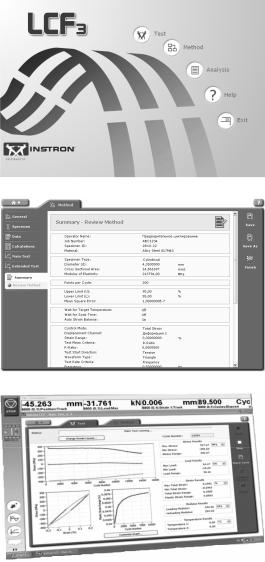
а
б
в
Рис. 5.18. Программа LCF3 для проведения испытаний
на малоцикловую усталость: основное меню (а), окно настройки метода испытаний (б), окно испытания (в)
141

показаны основное меню и экраны настройки метода эксперимента и испытания программы LCF3.
Эксперименты на малоцикловую усталость необходимо осуществлять в режиме «жёсткого» нагружения, при котором в процессе испытания средние и амплитудные значения циклических деформаций сохраняют свои исходные значения. На рис. 5.19 отражена схема «жёсткого» нагружения, которую необходимо задать в методе испытания.
Рис. 5.19. Схема нагружения при испытаниях на МЦУ: εа – амплитуда деформации, εр – размах деформации
Во всех экспериментах на МЦУ используется отнулевой положительный цикл деформации с коэффициентом асимметрии R = εmin /εmax = 0 . Форму волны циклов необходимо выбирать в виде
треугольника (как показано на рис. 5.19), что обеспечивает постоянную скорость деформации на этапах нагрузки и разгрузки. Зависимость деформации от времени должна сохраняться в течение всей программы испытаний. Частота циклирования поддерживается постоянной для каждого испытания изадаетсяравной0,5 Гц.
При разработке метода испытания необходимо указать используемый тип образца, размеры его поперечного сечения (минимальный диаметр dmin ), размах деформации εp = εmax – εmin ,
142
критерий остановки опыта (например, падение нагрузки на 30–50 %) и схему сохранения данных по циклам нагружения (желательно с логарифмическим приростом).
III. Проведение испытания
Для проведения испытаний при нормальной температуре на малоцикловую усталость при постоянных параметрах цикла рекомендуется использовать партию, состоящую не менее чем из 13 образцов. Управление по деформации в процессе эксперимента осуществляется при помощи датчика осевых деформаций. С целью проверки закрепления датчика и образца необходимо провести предварительное циклическое воздействие с малой амплитудой деформации в пределах зоны упругости. На каждом цикле следует проверить значение модуля Юнга на этапах нагрузки Eн и разгрузки Eр. Разница между полученными значениями модулей упругости должна составлять не более 10 %. Впротивном случае необходимо произвести разборку оснастки, снова установить образец в испытательнуюмашинуиприкрепитькнемудатчикосевыхдеформаций.
Циклическое нагружение образцов необходимо продолжать до тех пор, пока максимальная нагрузка в цикле не уменьшится на 50 % по сравнению с первыми циклами или образец не разделится на две части, что соответствует полному разрушению.
По результатам испытаний заполняется протокол, в котором содержится информация о величине амплитуды задаваемой осевой деформации и о предельном числе циклов до разрушения. Пример протокола приведён в табл. 5.10.
Таблица 5 . 1 0
Протокол испытаний на малоцикловую усталость цилиндрических образцов
Номер |
Максимальная |
Минимальная |
Амплитуда |
Числоциклов |
образца |
деформация |
деформация |
деформации |
доразрушения, |
|
вцикле, εmax, % |
вцикле, εmin, % |
вцикле, εa, % |
N |
|
|
|
|
|
|
|
|
|
|
|
|
|
|
|
143
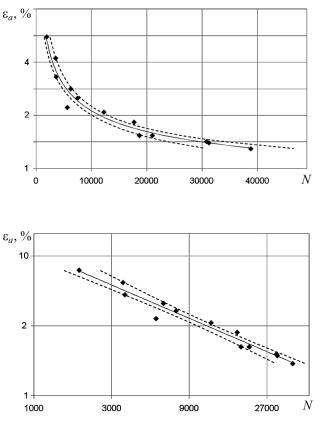
IV. Обработка результатов и подготовка отчёта
По результатам испытаний строится кривая малоцикловой усталости в обычных и логарифмических координатах.
На рис. 5.20 представлены экспериментальные данные зависимости амплитуды задаваемой деформации εа от числа циклов в испытании N.
а
б
Рис. 5.20. Кривая малоцикловой усталости в обычных (а)
и логарифмических (б) координатах (штриховые линии – граница 95%-ной доверительной области, точками отмечены результаты проведенных испытаний)
144

Необходимо провести статистическую обработку полученных экспериментальных данных, по результатам которой следует определить эмпирическую формулу линии регрессии в виде степенной функции N (εa ) = C εαa с определением вели-
чин C и α, а также рассчитать границы 95%-ной доверительной области (пунктирные линии на рис. 5.20) [21].
В состав отчёта по испытаниям на малоцикловую усталость должны входить следующие пункты:
1)результаты замеров образцов (табл. 5.9);
2)результаты испытаний (табл. 5.10);
3)график кривой малоцикловой усталости с границами 95%-ной доверительной области, построенный в обычных и логарифмических координатах;
4)эмпирическая формула линии регрессии;
5)графики зависимостей напряжения от полной деформации, зафиксированные в начале, середине и конце (перед разрушением) испытания (пример типичных петель гистерезиса приведён на рис. 5.21);
Рис. 5.21. Петли гистерезиса при малоцикловой усталости
145
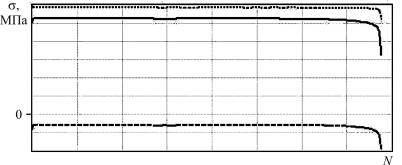
Рис. 5.22. Тренды пиковых нагрузок в испытаниях на МЦУ:
σmax – сплошная линия, σmin – штриховая линия,
σr – пунктирная линия
6)графики-тренды зависимостей пиковых нагрузок σmax ,
σmin и размаха напряжений σr = σmax – σmin в цикле от их общего
числа (рис. 5.22).
5.6. ИССЛЕДОВАНИЕ СКОРОСТИ РОСТА УСТАЛОСТНОЙ ТРЕЩИНЫ
Цель работы
Знакомство с методикой проведения испытаний на циклическую трещиностойкость.
Объект исследования
При проведении испытаний на циклическую трещиностойкость используются металлические образцы, чертёж и внешний вид которых приведены на рис. 5.23 и 5.24 соответственно. Стандартом ASTM [30] накладываются ограничения на размеры образцов. В частности, минимальный размер W должен быть не менее 25 мм, а толщина выбирается из диапа-
зона |
W |
≤ B≤ |
|
W |
. |
|
4 |
||||
20 |
|
|
|||
146 |
|
|
|
|
|
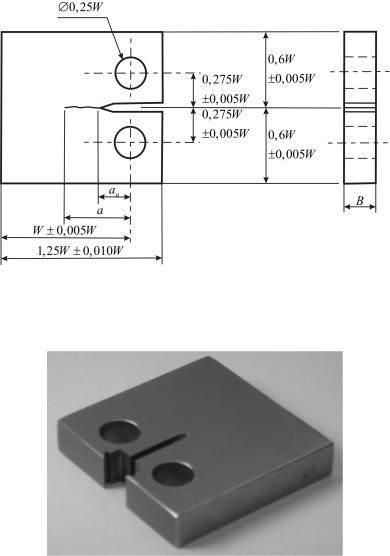
Рис. 5.23. Чертёж образца для испытаний на циклическую трещиностойкость
Рис. 5.24. Внешний вид образца для испытаний на циклическую трещиностойкость
147
Перед началом экспериментов следует произвести определение размеров образца W и B с точностью до 0,01 мм и занести полученные данные в приведённую ниже табл. 5.11.
Таблица 5 . 1 1
Размеры образцов для испытаний на циклическую трещиностойкость
Номер |
Маркировка |
Длина рабочей части |
Толщина рабочей |
|
образца |
части образца |
|||
образца |
образца |
|||
W, мм |
B, мм |
|||
|
|
|||
1 |
|
|
|
|
2 |
|
|
|
|
3 |
|
|
|
Испытательная установка
Испытания на малоцикловую усталость проводятся на сервогидравлической испытательной системе Instron 8801 с использованием датчика раскрытия трещины COD.
Содержание работы
Выполнение эксперимента включает в себя пять основных этапов:
1)подготовка к работе испытательного оборудования,
2)выращивание предварительной усталостной трещины,
3)создание метода испытания на циклическую трещиностойкость,
4)проведение испытания,
5)обработка результатов и подготовка отчёта.
Подготовка и проведение испытаний выполняются толь-
ко в присутствии инженера, обслуживающего испытательную систему.
I. Подготовка к работе испытательного оборудования Для подготовки к работе необходимо включить компью-
тер и контроллер испытательной машины, запустить программу управления Console и убедиться, что все датчики системы (дат-
148

чики силы, экстензометр) подключены и откалиброваны. Затем включить маслостанцию и прогреть испытательную машину в течение одного часа.
Перед проведением серии циклических испытаний для минимизации изгибных деформаций (изгибная деформация не должна превышать 5 % амплитуды минимальной деформации) захваты необходимо выровнять с помощью устройства AlignPRO, рисунок которого и схема установки в испытательную машину
приведены в параграфе 5.5. |
|
|
Образцы для испытаний |
|
|
необходимо устанавливать в за- |
|
|
хваты согласно рис. 5.25 в сле- |
|
|
дующем порядке: образец 4 ус- |
|
|
танавливается в вилки 2 и фик- |
|
|
сируется с помощью пальцев 3; |
|
|
на вилки накручиваются адапте- |
|
|
ры 6; полученная сборка фикси- |
|
|
руется с |
помощью накидной |
|
гайки 5 на тяге 1; пальцы фик- |
|
|
сируются шпильками 7. |
|
|
В экспериментах на цик- |
|
|
лическую |
трещиностойкость |
|
в качестве параметра управле- |
|
|
ния испытательной машиной |
|
|
используется полная амплиту- |
|
|
да осевой силы. Перед испы- |
|
|
таниями необходимо произве- |
|
|
сти настройку обратной свя- |
|
|
зи (PID-параметров) машины. |
Рис. 5.25. Схема установки |
|
С этой целью проводятся проб- |
образца в захватах: 1 – тяга, |
|
ные циклические нагружения |
2 – вилка, 3 – палец, 4 – компакт- |
|
с формой волны в виде синуса, |
ный образец, 5 – накидная гайка, |
|
в процессе которых подбира- |
6 – адаптер, 7 – шпилька |
|
|
ется коэффициент пропорцио-
149
нальности для обеспечения соответствия величины заданной и реализуемой на испытательной машине амплитуды осевого усилия.
II. Выращивание предварительной усталостной трещины Перед проведением испытаний на циклическую трещиностойкость необходимо прорастить в образцах предварительную трещину до длины a0 ≈ 14,5 мм (при длине надреза 12 мм).
При этом частота циклического нагружения должна составлять 20 Гц, а отношение минимальной и максимальной нагрузки в цикле Pmin / Pmax = 0,1.
Предварительное проращивание трещины осуществляется в несколько этапов. Амплитуда циклического нагружения на каждом последующем шаге должна уменьшаться на 20 % по сравнению с предыдущим [30]. Продолжительность каждого этапа определяется приращением трещины не менее чем на величину
∆ a= |
3 |
Kmax′ |
2 |
|
|
|
|
|
, |
(5.11) |
|
π |
|
||||
|
σв |
|
|
||
где Kmax′ – конечное значение Kmax предыдущего шага. |
|
||||
Процесс циклического нагружения прекращается |
в мо- |
мент, когда длина проращиваемой трещины достигает заданного значения a0 . На рис. 5.26 показана схематизация процедуры проращивания трещины. Максимальный коэффициент интенсивности напряжений Kmax в конце предварительной процедуры проращивания равнялся Kmax в начале испытания.
После проращивания трещины производится измерение ее длины при помощи переносного микроскопа с рекомендуемым увеличением х56. Размер трещины необходимо измерять с двух сторон компактного образца. Если разница между измеренными значениями не превышает 0, 25 B (для используемого в данной
лабораторной работе образца – 2,5 мм), образец признается при-
150