
книги / Основы физики и механики разрушения
..pdf
Если реализуется разрушение от дислокационной СМТ, то RMC = 18(dф )−1/2 . Если же реализуется разрушение от цементитной
СМТ, такой зависимости не будет и необходимо искать зависимость
RMC = f (tц )−1/2 .
4.6.3. Сопротивление микросколу сталей эвтектоидного состава
В структуре перлита пластины феррита и цементита залегают параллельными рядами, образуя перлитную колонию, в которой все ферритные промежутки имеют одну общую кристаллографическую ориентировку.
Вследствие определенной кристаллографической ориентировки срез цементитных пластин (или стержней) в перлите происходит не по наименьшему размеру tц , а по сильно наклоненной плоскости скольже-
ния в ферритной матрице, увеличивающей длину среза почти в 5 раз
(рис. 4.6):
tср = 4,75tц.
∆Ф tц
Стр
tср
Рис. 4.6. Образование СМТ в результате скола пластинки эвтектоидного цементита. ∆Ф – толщина ферритной пластины
191
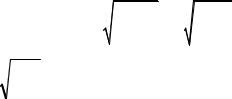
Удвоенную величину косого среза цементитной пластины в перлите можно рассматривать как максимальный размер СМТ, инициированной пластическим сдвигом в перлите:
ССМТ = 9,5tц ≈ 10tц.
Из этого выражения, используя концепцию Гриффитса, можно легко получить расчетную формулу для напряжения микроскола, источником которого является срез цементитной пластины в перлите:
σцМС = n |
4Eγ |
= n |
4Eλ |
= Kцtц−1/2 , |
πCСМТ |
|
|||
|
|
π10tц |
где Kц = n |
4Eγ |
, n – фактор ориентировки, равный 1,15. |
|||
10π |
|||||
|
|
|
|
||
Тогда Kц = 0,78 кГ/мм–3/2, и окончательно |
|||||
|
|
R |
= 0,78 t |
−1/2. |
|
|
|
MC |
|
ц |
Наряду с растрескиванием цементита в плоскостях скольжения существует и возможность зарождения СМТ по дислокационному механизму на границах перлитных колоний.
Поскольку существует возможность конкуренции двух механизмов зарождения СМТ, силовая характеристика разрушения σр = RМС будет
определяться тем, какой из двух конкурирующих факторов – размер перлитной колонии dп или толщина цементитной пластины tц – является источником появления СМТ бόльшего размера.
При двух возможных уровнях напряжения разрушение произойдет при напряжении, соответствующем СМТ бόльшего размера, т.е. при меньшем σСМТ . При этом меньшее из двух напряжений должно быть
равно напряжению течения σт, так как без макротекучести не может
возникнуть ни дислокационная, ни цементитная СМТ.
Таким образом, условием перехода от одного механизма зарождения СМТ к другому будет равенство двух напряжений: σр (dп ) = σр (tц ) ,
или 18dп−1/2 = 0,78tц−1/2 , отсюда dп ≈ 550tц.
Это означает, что если колонии перлита будут чрезмерно крупными, т.е. dп > 550tц , то в этом случае σр будет соответствовать σт фер-
рита с таким же размером зерна и RMC = 18dп−1/2 . Если же цементит бу-
192
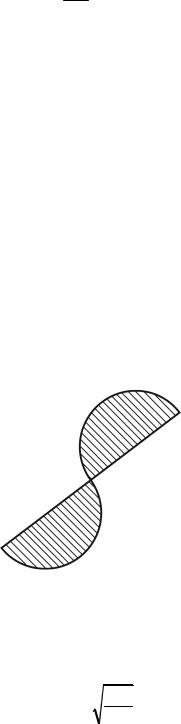
дет слишком грубым, т.е. tц > 1 dп , разрушающее напряжение ока550
жется ниже, чем RMC = 18dп−1/2 , и его уровень необходимо будет оценивать как RMC = 0,78(tц−1/2 ) .
4.6.4.Сопротивление микросколу сталей
сглобулярным цементитом
Возможен еще один источник гетерогенного зарождения СМТ – скол или срез хрупких частиц глобулярной формы. Такие глобулярные карбиды в большом количестве присутствуют в сталях, подвергнутых высокому отпуску или отжигу на зернистый перлит.
Известно, что прочность сталей со сферическими частицами определяется межчастичным расстоянием в соответствии с моделью Орована, однако напряжение разрушения σр определяется диаметром таких
карбидных глобулей.
Сдвиг половинок частицы образует дискообразную область разорванных межатомных связей в ферритной матрице, которую и рассматривают в качестве зародышевой СМТ с размером Сз = 2dц (рис. 4.7).
Рис. 4.7. Образование СМТ в результате скола карбидного глобуля
Для такой трещины решение уравнения Гриффитса было получено Заком:
σСМТ = πЕAγ .
193

Поскольку A = 2dц , то:
|
σСМТ |
= |
πЕγ |
= 2,5dц−1/2. |
|
|
|||
|
|
|
2dц |
|
Переходным |
условием |
от одного механизма зарождения СМТ |
||
к другому будет |
равенство |
двух напряжений: σр (dф ) = σр (dц ), или |
18dф−1/2 = 2,5dц−1/2 , отсюда dф = 52dц .
Следовательно, если зерно феррита слишком крупное, т.е. dф > 52dц ,
реализуется дислокационная СМТ, а если цементитные глобули грубые, т.е. dф < 52dц , источником разрушения будет служить цементитная СМТ.
Все случаи, описанные в подразд. 4.6.2–4.6.4, получили экспериментальное подтверждение. Покажем это на примере последнего случая, на
зависимостях RMC = f (dф )−1/2 (такие зависимости Ю.Я. Мешков [6] назы-
вает структурно-силовыми диаграммами разрушения – ССДР): начиная с определенного размера ферритного зерна экспериментальные точки перестают подчиняться зависимости RMC = 18dф−1/2 (рис. 4.8, а). Однако если
для этих точек построить зависимость RMC = 2,5dц−1/2 , то все они будут
подчиняться этойзависимости (рис. 4.8, б).
При термической обработке углеродистых сталей нередки случаи, когда в структуре наблюдается как глобулярный, так и пластинчатый цементит. Наличие сразу двух источников цементитной СМТ вызывает необходимость установить еще одно условие смены микромеханизма разрушения.
Критическое соотношение между размером глобуля и толщиной пластины цементита легко установить из равенства следующих напряжений:
RMC = 2,5dц−1/2 и RMC = 0,78 tц−1/2 .
Равенство этих выражений дает соотношение dц ≈ 10tц , т.е. только
в тех случаях, когда размер глобуля будет в 10 раз больше толщины пластины цементита, разрушение глобуля может оказаться источником микроскола.
194

Рис. 4.8. Структурно-силовые диаграммы разрушения, построенные в зависимости от размера зерна феррита (а)
и размера цементитного глобуля (б)
Таким образом, самое низкое критическое соотношение между размером элемента микроструктуры и хрупкой цементитной частицы наблюдается для равноосных частиц глобулярной формы. Это означает, что в сталях со сфероидизированным цементитом его охрупчивающее влияние наименее заметно, поскольку лишь относительно большие глобули могут служить источниками микроскола.
4.7. Связь основных параметров физики и механики разрушения
Несмотря на очевидную важность и полезность критерия вязкости разрушения KIС , приписать этой характеристике свойства фундамен-
тальной константы материала не представляется возможным.
В последние десятилетия многие ученые предпринимали попытки изучить микромеханизм процесса в области острия трещины и развить подходы к определению KIС через критическое локальное напряжение,
которое, как показывают результаты, по сути, является напряжением микроскола.
Еще одним серьезным обстоятельством является то, что исходный постулат механики разрушения, по которому KIС не зависит от длины
трещины и других геометрических параметров, является лишь некоторым приближением, справедливым только для достаточно длинных – макроскопических трещин.
195

Показано, что малые трещины, для которых С ≈ d, т.е. трещины длиной от 10 до 100 мкм, а при очень крупном зерне – до 1,0 мм, не могут начать свой рост в тот момент, когда коэффициент интенсивности напряжений у вершины такой малой трещины достигает уровня KIС , опреде-
ленного в экспериментах с наведенной усталостной макротрещиной. Образцы из сталей, заведомо имеющих микротрещины размером
С ≈ d, разрушаются при напряжениях микроскола RMC = σр = 18d
так, как будто никаких трещин в нем нет. Малым трещинам «не под силу» создать требуемый для своего старта критический уровень коэффициента интенсивности напряжений. Таким образом, KIС , определенный
по стандартным методикам, неприемлем для описания поведения малых трещин.
Поскольку KIС нельзя рассматривать как фундаментальную характеристику, имеет смысл поискать корреляционную связь между KIС
и другими, более фундаментальными параметрами механического поведения металлов и сплавов.
Проведя подробный анализ, Ю.Я. Мешков показал [3, 6], что такими характеристиками являются предел текучести, относительное сужение, сопротивление микросколу и некоторых случаях – ударная вязкость.
Кроме того, важнейшим параметром материала Ю.Я. Мешков считает отношение сопротивления микросколу к пределу текучести,
Kв = RMC . Он называет этот параметр коэффициентом вязкости.
σ0,2
При RMC = σ0,2 Kв = 1, материал становится хрупким, и реализую-
щийся на пределе текучести микроскол приводит к разрушению.
Если RMC σ0,2 , то в материале сначала реализуется текучесть, он
упрочняется, и только затем, на какой-то стадии деформационного упрочнения, произойдет разрушение.
Если же RMC < σ0,2 , то материал переохрупчен.
Таким образом, наиболее интересным представляется установление связи KIС с RMC и Kв .
Для отыскания такой связи необходимо перевести механику разрушения, которая, в сущности, является макронаукой, на микроуровень.
196
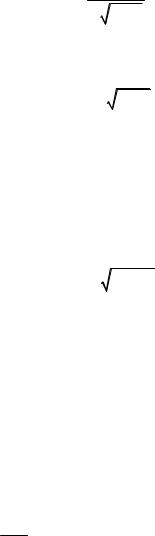
Подробный обзор работ по микромеханическому моделированию вязкости разрушения KIС , представлен в монографии О.М. Ро-
манива [10]. Здесь мы используем только некоторые из представленных в этой книге подходов.
Согласно деформационному критерию Краффта [11], разрушение тела с трещиной произойдет тогда, когда на некотором расстоянии от вершины трещины dт будет достигнута критическая деформация
екр = KIС .
Е 2πdт
Краффт приближенно полагает, что eкр численно равна коэффициенту деформационного упрочнения n , тогда
KIС = nE 2πdт .
Как показал Ю.Я. Мешков [3], eкр ≈ n действительно может иметь
место лишь при небольших значениях коэффициента деформационного упрочнения n ≤ 0, 25.
Это означает, что критическая ситуация возникает недалеко от границы упругопластической зоны, что позволяет считать dт приблизительно
равным эффективному радиусу вершины трещины ρэфф , итогда
KIС = nE 2πρэфф .
Хан [12] получил эмпирическую зависимость, позволяющую оценивать KIС по критерию критического напряжения скола σС :
2 |
|
1 |
3 |
KIСσт |
= |
|
σC . |
|
|||
|
2,35 |
|
Это напряжение является не чем иным, как RMC . В этом случае можно записать
2 |
|
1 |
3 |
KIСσт |
= |
|
RMC . |
|
|||
|
2,35 |
|
Поскольку Kв = RMC , это то выражение можно переписать в сле-
σ0,2
дующем виде:
197
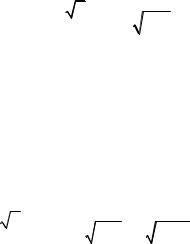
|
|
= |
1 |
|
|
R |
|
3 |
= 0,08R K 2. |
||
K |
|
|
|
|
MC |
|
|||||
|
|
|
|
σт |
|
|
|||||
|
IС |
|
13 |
|
2 |
|
MC |
в |
Данная зависимость удовлетворительно выполняется лишь в случае хрупкого транскристаллитного разрушения исходно высокопластичных сталей при низкотемпературных испытаниях: t < −80 °С.
Ю.Я. Мешков [6] получил аналитическое выражение, связывающее
KIС, RMC и Kв : |
|
|
|
|
|
|
|
|
|
K |
|
= |
π |
R |
K |
|
ρ |
|
. |
IС |
|
в |
эфф |
||||||
|
|
2 |
MC |
|
|
|
|||
|
|
|
|
|
|
|
|
|
Для расчетов эту формулу в таком виде использовать неудобно изза неопределенности величины ρэфф . Тем не менее, понимая под ρэфф
расстояние от вершины трещины до микрообъема, в котором реализуется микроскол, а реализуется он на границе упругопластической зоны,
можно принять, что ρэфф ≈ rЗПД . |
|
|
|
|
|
|
|||||||
Принимая ρ |
эфф |
≈ r |
|
и R = 18d −1/2 , можно окончательно записать |
|||||||||
|
|
ЗПД |
|
MC |
|
|
|
|
|
|
|||
K |
|
= |
|
π |
18d |
−1/2 K |
|
r |
= 9 πr |
K |
d −1/2. |
(4.9) |
|
IС |
|
|
в |
||||||||||
|
|
|
|
2 |
|
|
ЗПД |
ЗПД |
в |
|
|
||
|
|
|
|
|
|
|
|
|
|
|
|
|
Поскольку в последнем выражении появился размер зерна, имеет смысл проанализировать имеющиеся данные по влиянию размера зерна на вязкость разрушения. На рис. 4.9 [10] представлены зависимости вязкости разрушения для низкоуглеродистой стали от размера зерна (рис. 4.9, а) и параметра Холла – Петча (рис. 4.9, б). Очевидно, что в случае достаточно мелкого зерна, d < 40 мкм, вязкость разрушения практически линейно возрастает по мере измельчения зерна, тогда как при наличии в структуре крупных зерен, d < 40 мкм, вязкость разрушения не зависит от размера зерна.
Трактовать эти результаты можно следующим образом: пока размер зоны пластической деформации rЗПД существенно больше размера зерна,
т.е. пока в объеме ЗПД размещается много произвольно ориентированных зерен, зарождение очага разрушения происходит в соответствии с моделью микроскола, поэтому выражение (4.9) корректно описывает струк-
198
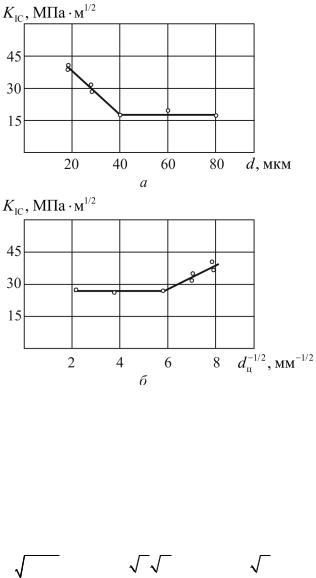
турную зависимость вязкости разрушения (см. рис. 4.10, а). Если же в объем ЗПД помещается лишь часть одного зерна (рис. 4.10, б), для зарождения СМТ критического размера и реализации микроскола из-за резко неоднородного распределения напряжений в объеме зерна потребуется значительно большее внешнее напряжение.
Рис. 4.9. Зависимость вязкости разрушения стали 08кп от размера зерна (а) и параметра Холла – Петча (б)
Из схемы на рис. 4.10, б видно, что в этом случае дислокации могут свободно выходить за пределы ЗПД и скользить вплоть до границ крупного зерна. Таким образом, можно принять, что в этом случае
= d, и тогда
K |
IС |
= 9 πr K |
d |
−1/2 = 9 π d K |
d −1/2 |
= 9 π K |
в |
≈ 16K |
. |
|
ЗПД в |
|
в |
|
|
в |
|
Таким образом, в случае крупного зерна вязкость разрушения действительно не зависит от размера зерна.
199
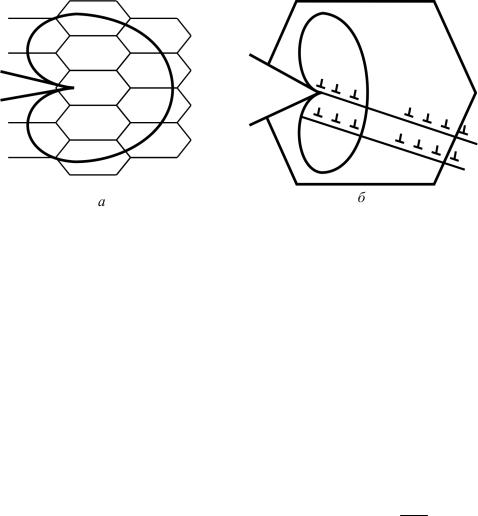
Рис. 4.10. Различные соотношения между размером зерна и размером ЗПД: а – rЗПД >> d ; б – rЗПД << d
4.8. Оптимизация параметров прочности конструкционных сталей с точки зрения физики разрушения
Физическая теория хрупкости стали позволяет сформулировать критерий надежности металлических материалов, т.е. нечувствительности металлического материала к дефектам на основе требований
кструктуре и традиционным свойствам.
Вданном случае имеется в виду чисто силовая часть понятия «надежность», не охватывающая специальные виды отказов: износ, усталость, коррозия и т.п.
По Ю.Я. Мешкову [3, 6], запас вязкости металла Kв = RMC должен
σ0,2
быть не менее 2,5, чтобы металл оказался полностью нечувствителен к концентраторам напряжений.
Попытаемся найти соотношение между основными прочностными параметрами металла, обеспечивающими такой запас Kв . Распишем
подробнее условие Kв = |
RMC |
= 2,5 : |
|
|
|||||
|
|
|
|
||||||
|
|
|
σ0,2 |
|
|
|
|||
K |
в |
= |
RMC |
= |
|
Kрd −1/2 |
= 2,5. |
||
|
σ0 |
+ Ky d −1/2 |
|||||||
|
|
|
σ0,2 |
|
200