
книги / Основы физики и механики разрушения
..pdf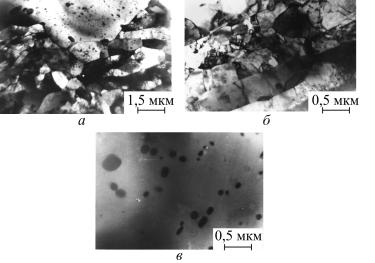
ластях, а также в сорбите, полученном при отпуске, низкая (рис. 3.2, б). В результате коагуляции карбидов они укрупняются и округляются
(рис. 3.2, в).
Рис. 3.2. Тонкая структура стали 09Г2С. Закалка 920 °С, вода + отпуск 650 °С: а – общий вид; б – дисперсный сорбит отпуска; в – сорбит отпуска
Необходимо различать два вида сорбита при отпуске закаленной стали:
–дисперсный сорбит отпуска, в котором еще сохраняется созданная закалкой субструктура (рис. 3.2, б);
–сорбит отпуска, в котором в результате сильно развитых рекристаллизационных процессов субструктура исчезает (рис. 3.2, в).
Среднеуглеродистая сталь 35 (С = 0,32…0,40 %). Основной структурой закаленной стали 35 является также реечный мартенсит.
Наблюдается не более 8–10 % частично двойникованного мартенсита (рис. 3.3, а). При отпуске в температурном интервале 200–400 оС субграницы, полученные в процессе закалки, полностью сохраняются, что подтверждается постоянным средним размером мартенситных кристаллов (см. табл. 3.1).
Изменение характеристик механических свойств в данном интервале температур отпуска связано с процессами, протекающими внутри реечных кристаллов α-фазы. Эти процессы состоят в перераспределении и аннигиляции дислокаций, в результате чего уменьшается плотность дислокаций, а также в выделении цементитных карбидов в теле мартенситных кристаллов.
141
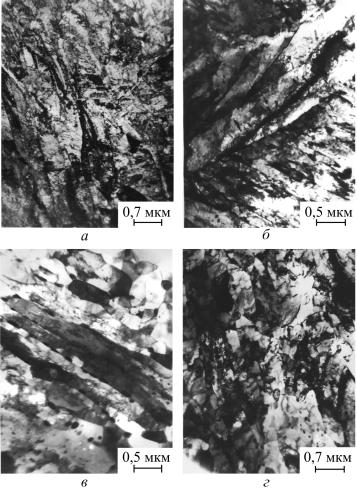
Рис. 3.3. Тонкая структура стали 35. Закалка 860 °С, вода: а – отпуск 200 °С; б – отпуск 500 °С; в, г – отпуск 650 °С
При отпуске до 500 °С реечная структура мартенсита сохраняется, но плотность дислокаций заметно уменьшается. Продолжается выделение цементитных карбидов, причем при этой температуре они образуются преимущественно по границам реек. В отдельных случаях могут наблюдаться зародыши рекристаллизации (рис. 3.3, б).
При отпуске до 650 °С протекают процессы полигонизации и формируется структура дисперсного сорбита отпуска – относительно удлиненные ферритные ячейки с небольшой плотностью дислокаций внутри них и цементитные карбиды, основная часть которых располагается по границам ферритных ячеек. В этой части микрообъе-
142
мов, где по границам наблюдается непрерывная цепочка карбидов, сохраняется реечная субструктура. Относительно реже могут наблюдаться небольшие области сорбита отпуска (не более 10 % от объема), в которых прошла рекристаллизация и реечно-ячеистая субструктура отсутствует (рис. 3.3, в и г). Таким образом, электронно-микроскопи- ческие исследования показывают, что среднеуглеродистая сталь 35 менее склонна к рекристаллизации по сравнению с низкоуглеродистой сталью 09Г2С. Причиной этого прежде всего является барьерный эффект, который вызывает появление цементитных карбидов, которые выделяются в большом количестве по субграницам и препятствуют их миграции.
Высокоуглеродистая сталь 80 (С = 0,77…0,85 %). При закалке стали 80 образуется главным образом пластинчатый мартенсит, частично или полностью двойникованный. Он составляет 60–70 % общего объема (рис. 3.4, а). Этот тип мартенсита характеризуется повышенной склонностью к хрупкому разрушению не только из-за упрочнения твердого раствора (большие деформации решетки и полное закрепление дислокаций атмосферами Котрелла), но и в результате особенностей его формирования. В этом случае максимальное перемещение атомов в решетке при образовании мартенсита создает участки с высоким уровнем микронапряжений на конце (вверху) мартенситной пластины при завершении ее роста. К объемному эффекту добавляется динамический, вызванный высокой скоростью, с которой образуются мартенситные пластины [5]. Максимальные пиковые напряжения будут возникать при образовании крупной пластины мартенсита, которая прорезает целиком тело аустенитного зерна и останавливается на его границе. Эти напряжения могут достигнуть таких высоких значений, в результате которых возникают приграничные микротрещины. Если они добавятся к напряжениям, которые возникают в кончике созданной магистральной трещины, то они могут вызвать транскристаллитное или интеркристаллитное разрушение.
В результате отпуска при 400 °С структура, полученная после закалки, сохраняется. Наблюдается выделение дисперсных карбидов как по границам, так и в теле α-пластин. Плотность дислокаций внутри пластин уменьшается, при этом начинает исчезать контраст от двойни-
ков (рис. 3.4, б).
143
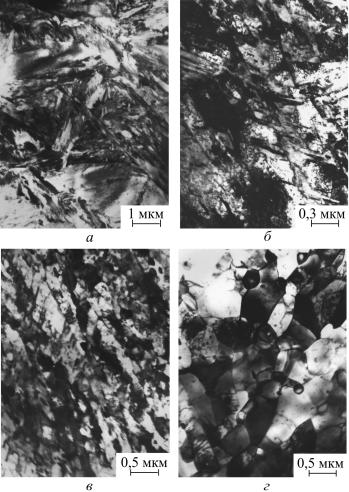
Рис. 3.4. Тонкая структура стали 80. Закалка 820 °С, вода: а – без отпуска; б – отпуск 400 °С; в – отпуск 500 °С; г – отпуск 650 °С
При отпуске до 500 °С границы пластин α-фазы прослеживаются еще отчетливее. Во внутренних объемах пластин активно протекает полигонизация, которая формирует ячеистую субструктуру (рис. 3.4, в). Наибольшие ячейки ограничены от окружающей их матрицы высокоугловыми границами и превращаются в рекристаллизационные зародыши. Одновременно наблюдается рост и изменение формы цементитных карбидов: если при отпуске до 400 °С карбиды имели пластинчатую форму, то при отпуске при 500 оС они приобретают форму эллипсоидов. Структура, которая формируется при отпуске при 650 °С, может классифицироваться как дисперсный сорбит отпуска (рис. 3.4, г).
144
На основе статистического анализа, результаты которого приведены в табл. 3.1, можно сделать следующие выводы. В закаленном состоянии и после отпуска при низких температурах размеры микроструктурных элементов (размер аустенитного зерна, размер пакетов
всталях 09Г2С и 35, поперечный размер мартенситных кристаллов) имеют близкие значения. Наиболее существенная разница наблюдается
вувеличении части объема, занятого пластинчатым мартенситом, –
встали 09Г2С 0 %, в стали 35 около 10 % и в стали 80 до 70 %.
После отпуска при высоких температурах средний размер ферритных ячеек и карбидных частиц для трех исследованных сталей имеет очень близкие значения (см. табл. 3.1). Разница в плотности дислокаций внутри ячеек также незначительна. Следовательно, разница в структуре сталей 09Г2С, 35 и 80 после высокотемпературного отпуска состоит в различной доле карбидов, которая увеличивается при повышении содержания углерода (1,0–1,2 % в стали 09Г2С, 4,5–4,7 % в стали 35 и 9,5–10,0 % в стали 80) и в количестве сорбита, полученного в результате отпуска (часть рекристаллизованной α-фазы), которая уменьшается с увеличением содержания углерода (50 % в стали 09Г2С, 10 %
встали 35 и практически 0 % в стали 80).
3.2.Микромеханизмы разрушения при однократном нагружении углеродистых и низколегированных сталей с различным содержанием углерода, закаленных и отпущенных
вшироком температурном интервале
Мы исследовали ряд низколегированных сталей с различным содержанием углерода после закалки и отпуска в широком температурном интервале. Наряду с традиционными механическими свойствами определяли предел трещиностойкости IC при статическом нагружении
и трещиностойкость КСТ при ударном трехточечном изгибе
(ГОСТ 9454–78).
На основании результатов, полученных при ударных испытаниях, определяли критическую температуру ТKар12 при значении ар ≡ КСТ =
= 12 Дж/см2. Результаты, полученные при изучении механических свойств, представлены в табл. 3.2 и на рис. 3.5.
Для сталей с низким содержанием углерода (С < 0,2 %) увеличение температуры отпуска от 200 до 650 °С снижает статическую трещиностойкость IC , в то время как трещиностойкость при ударном нагруже-
145
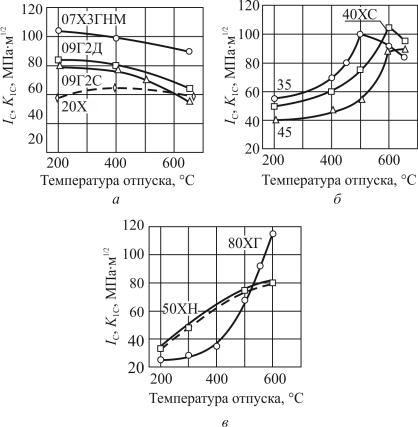
нии КСТ непрерывно растет. Фрактографический анализ (рис. 3.6, а и рис. 3.7, а) свидетельствует, что доминирующей рельефной составляющей в изломах после отпуска при низких температурах являются ямки (Я). При повышении температуры отпуска появляются значительные по размеру, бесструктурные по характеру, гладкие, с низкой энергоемкостью плоские ямки (рис. 3.7, б, в), называемые плато (П) [6]. В литературе этот рельеф известен еще как площадки расслоения по плоскостям скольжения [7].
Рис. 3.5. Влияние температуры отпуска на изменение характеристик статической трещиностойкости для углеродистых и низколегированных сталей (сплошная линия – IC, пунктирная линия – KIС): а – низкоуглеродистые стали;
б– среднеуглеродистые стали; в – высокоуглеродистые стали
Сповышением температуры отпуска до 650 °С средний размер плато достигает 15–25 мкм, в то время как их площадь занимает 45–50 % от общей поверхности излома (рис. 3.7, в).
146
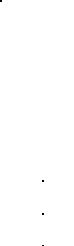
Таблица 3 . 2 Характеристики механических свойств сталей 09Г2С, 35 и 80
Марка |
Режим |
|
Механические свойства |
|
||||
σв |
σ0,2 |
δ |
ψ |
КСТ, |
TKар12 , |
IC , |
||
стали |
термообработки |
|
|
|
|
Дж/см2 |
оС |
МПа·м1/2 |
МПа |
% |
|||||||
09Г2С |
Закалка 920оС, вода |
1260 |
1060 |
9,0 |
33 |
14 |
–64 |
78 |
|
Закалка + отпуск |
1270 |
1080 |
9,0 |
35 |
16 |
–70 |
80 |
|
200 оС |
|
|
|
|
|
|
|
|
Закалка + отпуск |
1170 |
1030 |
7,0 |
36 |
14 |
–40 |
– |
|
300 оС |
|
|
|
|
|
|
|
|
Закалка + отпуск |
1010 |
960 |
7,0 |
38 |
16 |
–78 |
78 |
|
400 оС |
|
|
|
|
|
|
|
|
Закалка + отпуск |
820 |
780 |
11,0 |
41 |
25 |
–82 |
71 |
|
500 оС |
|
|
|
|
|
|
|
|
Закалка + отпуск |
700 |
600 |
19,0 |
53 |
36 |
–91 |
57 |
|
650 оС |
|
|
|
|
|
|
|
Сталь |
Закалка 880 оС, |
710 |
710 |
0 |
0 |
– |
– |
– |
35 |
вода |
|
|
|
|
|
|
|
|
Закалка + отпуск |
1590 |
1460 |
3,0 |
19 |
10 |
+119 |
56 |
|
200 оС |
|
|
|
|
|
|
|
|
Закалка + отпуск |
1340 |
1250 |
6,5 |
23 |
10 |
– |
60 |
|
300 оС |
|
|
|
|
|
|
|
|
Закалка + отпуск |
1100 |
1020 |
10,0 |
38 |
19 |
+30 |
69 |
|
400 оС |
|
|
|
|
|
|
|
|
Закалка + отпуск |
950 |
880 |
12,5 |
42 |
30 |
–20 |
100 |
|
500 оС |
|
|
|
|
|
|
|
|
Закалка + отпуск |
710 |
680 |
30,0 |
56 |
54 |
–54 |
84 |
|
650 оС |
|
|
|
|
|
|
|
Сталь |
Закалка 820 оС, вода |
– |
– |
– |
– |
– |
– |
21 |
80 |
+ отпуск 200 оС |
|
|
|
|
|
|
|
|
Закалка + отпуск |
1560 |
1450 |
2,5 |
6,5 |
– |
– |
32 |
|
400 оС |
|
|
|
|
|
|
|
|
Закалка + отпуск |
1190 |
1050 |
6,0 |
13,5 |
– |
– |
62 |
|
500 оС |
|
|
|
|
|
|
|
|
Закалка + отпуск |
960 |
855 |
12,0 |
28,0 |
– |
– |
98 |
|
650 оС |
|
|
|
|
|
|
|
Для среднеуглеродистых сталей (С = 0,3…0,5 %) предел трещиностойкости IC имеет максимальные значения после закалки и отпуска
в интервале 500–600 °С. Дополнительное повышение температуры отпуска приводит к известному снижению IC . При этом чем выше со-
держание углерода, тем при более высокой температуре отпуска наблюдается этот максимум.
147
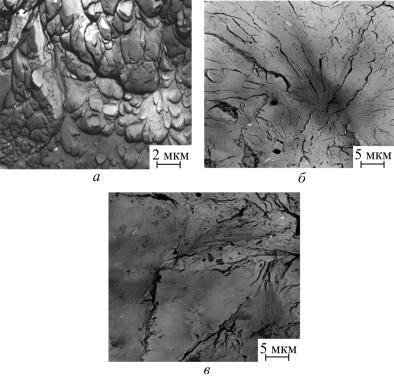
Рис. 3.6. Рельеф поверхности изломов низкоотпущенных сталей после испытаний на статическую трещиностойкость:
а– сталь 09Г2С; б – сталь 35; в – сталь 80
Сповышением температуры отпуска во всем температурном интервале от 200 до 650 °С динамическая трещиностойкость КСТ непрерывно растет. Кроме того, как следует из литературных данных [8], температура отпуска, при которой реализуются максимальные значения статической трещиностойкости, существенно зависит и от легирования стали. При наличии сильных карбидообразующих элементов, таких как ванадий и титан, этот максимум перемещается в область более высоких температур отпуска. Другими словами, такая экстремальная зависимость статической трещиностойкости характерна для углеродистых низколегированных сталей со средним содержанием углерода, в состав которых не входят элементы-карбидообразователи.
Исследование микромеханизма разрушения среднеуглеродистых сталей после закалки и низкотемпературного отпуска показывает, что основ-
ными рельефными составляющими являются субтранскристаллитные итранскристаллитные фасетки (рис. 3.6, б и рис. 3.8, а). С повышением
148
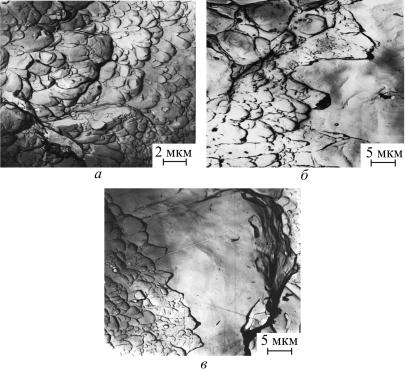
температуры отпуска этот хрупкий механизм развития трещины сменяется более вязким, и при достижении максимальных значений статической трещиностойкости вместо хрупких фасеток появляются энергоемкие ямки (рис. 3.8, б). Снижение трещиностойкости при еще более высоких температурах отпуска (см. рис. 3.5, б) связано с образованием известного количества площадей, занятых плато (рис. 3.8, в).
Рис. 3.7. Рельеф поверхности изломов стали 09Г2С после испытаний на статическую трещиностойкость: а – отпуск 200 °С;
б– отпуск 400 °С; в – отпуск 650 °С
Всталях с высоким содержанием углерода (С > 0,5 %) с повышением температуры отпуска статическая трещиностойкость увеличивается (рис. 3.5, в). Фрактографически (см. рис. 3.6, в) этот процесс выражается
вобразовании при низких температурах отпуска очень хрупких транскристаллитных и интеркристаллитных фасеток. С повышением температуры отпуска до средних температур начинают образовываться относительно более энергоемкие субтранскристаллитные фасетки. При высоких температурах образуется характерный энергоемкий ямочный рельеф.
149

Рис. 3.8. Рельеф поверхности изломов стали 35 после испытаний на статическую трещиностойкость. КС – квазискол, Я – ямки, П – плато:
а – отпуск 200 °С; б – отпуск 500 °С; в – отпуск 650 °С
Изломы исследованных материалов, полученные при динамическом нагружении, имеют фрактографические особенности, аналогичные полученным при статическом нагружении.
3.3. Закономерности изменения трещиностойкости при статическом нагружении закаленных и отпущенных углеродистых
и низколегированных сталей
Диаграмма максимальной трещиностойкости [8] (рис. 3.9).
На диаграмме в зависимости от содержания углерода в стали показано, при каких температурах отпуска реализуется максимальное значение статической трещиностойкости. При построении диаграммы, кроме собственных, использованы данные и других авторов [8, 9–12].
Диаграмма предельной трещиностойкости. На рис 3.10 получен-
ные результаты исследований обобщены в виде диаграммы предельной трещиностойкости [13, 14]. Значения предела трещиностойкости IC пред-
ставлены в зависимости от предела текучести σ0,2. Из представленных
150