
книги / Фосфогипс и его использование
..pdfтеле или на прирельсовом складе и этими же разбрасывателя ми ее вносят на поля, подлежащие известкованию в соответст вии с утвержденными требованиями. Прямоточная технология работ при использовании тракторных агрегатов типа РУМ-5, РУМ-8, МВУ-16 экономически целесообразна в радиусах пере
возок смеси 10—20 км. Автомобильные |
разбрасыватели типа |
МХА-7 эффективны в радиусах доставки |
смеси соответствен |
но до 25 и 40 км. |
|
При перевалочной технологии смесь к месту известкования перевозят на автосамосвалах или тракторных и автомобильных прицепах. Ее укладывают в бурты согласно схеме размещения буртов, прилагаемой к проектно-сметной документации. Из буртов смесь загружают в разбрасыватели тракторными по грузчиками.
Перегрузочная технологическая схема предусматривает ис пользование при перевозке смеси автомобилей-самосвалов типа САЗ-3502 или автопогрузчиков типа АП-7.
Смеси пылевидных известковых материалов с фосфогипсом можно хранить (в период от доставки до внесения в почву) в прирельсовых складах павильонного типа. Допускается кратко временное хранение (до 3 мес.) на открытых площадках с твер дым покрытием в буртах, укрытых полимерной пленкой [1 1 1 J.
При работе по перевалочной технологии, когда смесь неко торое время хранится на краю поля в буртах под открытым небом, возможно ее переувлажнение атмосферными осадками. Вносить такую смесь возможно только после высыхания на воздухе до влажности не более 18%. Сроки и дозы внесения такой смеси корректируют по данным определения влаги.
2.3.6. Перспективные районы и эффективность использования смесей на кислых почвах
Предполагаемые примерные объемы производства описанных выше смесей для химической мелиорации кислых почв даны в табл. 2,9. Перспективные районы-потребители смесей для хи мической мелиорации почв, расположенные в радиусе наибо лее рациональных перевозок химических мелиорантов, приво дятся в работах [113, 111]. Вопросы, связанные с организаци ей и технологией производства смесей, излагаются в специаль ных методических рекомендациях [128].
Состав для химической мелиорации кислых почв (смесь пылевидных известковых материалов с фосфогипсом) содержит кальций в двух основных формах: карбонатной (СаСОз) и сульфатной (CaS04). Внесение смеси указанных соединений кальция способствует лучшему проявлению потенциального плодородия почв в результате его мобилизации под действием входящего в смесь фосфогипса.
Основным преимуществом смесей фосфогипса с пылевидны ми известковыми материалами перед исходными компонентами
является то, что они обладают благоприятными физико-механи ческими и мелиорирующими свойствами. Смесь не теряет сы пучести при хранении в поле без укрытия; дает возможность использовать такие отходы, как фосфогипс и сланцевая зола, обладающие плохими физическими свойствами каждый в от дельности и удовлетворительными в смеси; содержит фосфор, серу и ряд микроэлементов, являясь дополнительным источни ком элементов минерального питания растений [86, 105—109, 111, 113].
Растворимость в воде CaS04 на два порядка выше, чем СаСОз. Растворенная часть CaS04 повышает концентрацию ионов кальция в почвенном растворе.
При внесении смеси извести с фосфогипсом наряду с нейт рализацией почвенной кислотности создаются более благопри ятные условия для питания растений и коагуляции почвенных кол лоидных структур в результате повышения концентрации ионов кальция в почвенном растворе. При этом улучшается структу ра почвы, уменьшается вымывание гумусовых веществ из па хотного слоя, увеличивается водопроницаемость почвы, умень шаются средняя плотность, коркообразование и необходимое тяговое усилие при обработке почвы. Полевыми испытаниями, проведенными в Московской, Ленинградской, Липецкой облас тях, Латвийской ССР (1981—1985 гг.), установлена высокая эффективность смесей на кислых почвах. Положительный эф фект от совместного внесения доломитовой муки и других карбонатных форм кальция с фосфогипсом получен на кислых почвах Украины и Белоруссии [ПО, 113, 141, 142].
Применение смесей на кислых почвах позволяет резко со кратить потери химических мелиорантов и загрязнение окру жающей среды, расширить агросроки их внесения.
Экономический эффект от применения смесей образуется в результате действия следующих основных факторов:
снижение капитальных вложений на строительство складов и себестоимости хранения смесей в складах павильонного типа
ТАБЛИЦА 2,9. Предполагаемые объемы производства смесей для химической мелиорации кислых почв в 1990—2000 гг.
Регион |
Годы |
Всего, млн. т |
В том числе марки |
||
А |
Б |
||||
|
|
|
|||
СССР — всего |
1990 |
1,5 |
1,0 |
0 ,5 |
|
|
1995 |
25,9 |
18,4 |
7,5 |
|
РСФСР |
2000 |
32,2 |
12,2 |
20,0 |
|
1990 |
1.5 |
1,0 |
0 ,5 |
||
|
1995 |
22,1 |
14,6 |
7 ,5 |
|
Украинская ССР |
2000 |
28,4 |
8,4 |
20,0 |
|
1995 |
1,5 |
1,5 |
— |
||
|
2000 |
1,5 |
1,5 |
___ |
|
Белорусская ССР |
1995 |
2,3 |
2,3 |
— |
|
|
2000 |
2,3 |
2,3 |
— |
или под полиэтиленовой пленкой вместо дорогостоящих скла дов силосного типа для пылевидных известковых материалов; снижение себестоимости транспортирования и внесения сме сей машинами общего назначения вместо дефицитных специ альных машин с пневмоустройствами типа АРУП-8 для пыле
видных известковых материалов; повышение прибавки урожаев сельскохозяйственных куль
тур по сравнению с применением чистой известняковой муки в среднем на 1,5 ц/га зерновых единиц и по сравнению со слан цевой золой — на 1,0 ц/га;
снижение потерь химического мелиоранта в виде непылящей смеси по сравнению с пылевидными известковыми материала ми [381].
2.4. СУШКА И ОТГРУЗКА ФОСФОГИПСА НА ЗАВОДЕ
Фосфогипс по ТУ 6-08-418—80 (см. табл. 2,2) поставляется сельскому хозяйству двух сортов.
Продукт I сорта получают сушкой фосфогипса текущей вы работки до конечной влажности 5±1%. В результате получа ется монодисперсный (частиц размером более 5 мм не более 1 %, более 1 мм — не более 6%), сыпучий, неслеживающийся и практически не смерзающийся фосфогипс, который можно пе ревозить в любое время года. Однако перевозить его следует в крытых вагонах и хранить в закрытых складах.
В СССР построена установка сушки фосфогипса мощностью 650 тыс. т/год в расчете на сухой дигидрат (проект и оборудо вание поставлены фирмой «Babkoc-BSH», ФРГ). Сущность про цесса заключается в том, что часть фосфогипса высушивают до содержания кристаллизационной влаги («14% ), а затем сме шивают ее с исходным влажным фосфогипсом для получения продукта необходимой влажности (рис. 2-6).
На установку сушки из производства фосфорной кислоты фосфогипс по дается в виде пульпы. Большая часть отфильтрованного на барабанном ва куум-фильтре 3 кека поступает в забрасыватель трубы-сушилки 10, меньшая часть — в смеситель 12. Высушенный фосфогипс отделяют от потока горячего газа в циклоне 11 и электрофильтре 14. Уловленный продукт поступает в сме ситель 12 или в силосный склад (в этом случае смешение производится при погрузке в вагоны или автотранспорт).
Выходящие из электрофильтра газы очищаются от соединений фтора в промывной башне 15, орошаемой известковым молоком.
Проектные расходные коэффициенты (на 1 т готового продукта в пересчете на сухой дигидрат): 53 кг условного топлива; 26,3 кВт-ч электроэнергии; 5,2 кг известкового молока (100% СаО).
Хотя себестоимость фосфогипса I сорта выше отгружаемого из отвала фосфогипса II сорта, а значит, должна быть выше и оптовая цена, но только высушенный продукт может обеспе чить равномерное распределение его по поверхности почвы и более полный контакт с ней. Мы полагаем, что для достижения одинакового эффекта фосфогипса I сорта потребуется значи-
Рис. 2-6.
Схема производства фосфогипса I сорта для химической мелиорации солонцо вых почв:
/ —сборник; 2 — насосы; 3 — барабанный вакуум-фильтр; 4 — вакуум-приемник; 5 — брызгостделитель; 6 —ленточный конвейер; 7 — вакуум-насос; 8 — вентилятор; 9 — топка; 10 — труба-сушилка; 11 — циклон; 12 — смеситель; 13 — пневможелоб; 14 — электрофильтр; 15 — промывная башня
тельно меньше, чем фосфогипса II сорта. Кроме того, фосфогипс I сорта можно транспортировать в течение всего года.
Фосфогипс II сорта подвергается естественной подсушке до содержания не более 20% гигроскопической влаги. Крупность частиц ТУ не ограничивается.
Узел отгрузки фосфогипса II сорта из отвала (рис. 2-7) располагается возможно ближе к последнему.
Для формирования штабеля, в котором фосфогипс несколько подсуши вается и из которого производится его погрузка в полувагоны и автомашины, используются бульдозеры типа ДЗ-110А, а для рыхления слежавшегося фос фогипса — рыхлители-бульдозеры типа ДЗ-116В. Погрузка фосфогипса из шта беля в полувагоны и автомашины производится экскаваторами с электропри водом типа Э-2503В с прямой лопатой емкостью 2,5 м3. Во время погрузки экскаваторы могут перемещаться вдоль фронта штабеля на длину 15 м по мере отбора из него фосфогипса.
На площадке узла погрузки располагаются весы и помещение для обслу
живающего персонала и электропункта. |
|
При мощности узла отгрузки 250 тыс. т |
фосфогипса в год в натуре |
(200 тыс. т/год в пересчете на сухой дигидрат) |
узел отгрузки обслуживают по |
2 агрегата указанных выше типов. |
|
В эксплуатации находится также узел отгрузки фосфогипса текущей выработки с интенсифицированной естественной под сушкой до влажности не более 20% проектной мощностью 650 тыс. т/ год (в пересчете на сухой дигидрат).
Фосфогипс после вакуум-фильтра производства ЭФК подают в крытый склад, оборудованный тремя мостовыми грейферными кранами грузоподъем ностью 15 т с грейфером емкостью 5 м3 (аналогичен складу, где производится
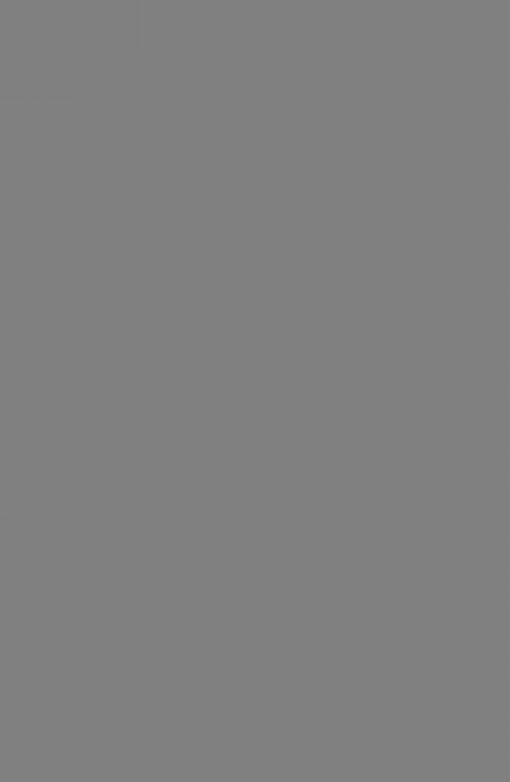
Глава 3
ИСПОЛЬЗОВАНИЕ ФОСФОГИПСА ДЛЯ ПРОИЗВОДСТВА ГИПСОВЫХ ВЯЖУЩИХ И ИЗДЕЛИЙ
Для |
использования |
фосфогипса* необходима их технологичес |
кая |
переработка с |
целью получения гипсовых, ангидритовых |
или |
композиционных вяжущих — порошкообразных продуктов, |
которые при смешении с водой образуют формовочные массы, способные превращаться в камневидное тело. В формовочные массы могут вводиться заполнители (наполнители), армирую щие материалы и химические добавки.
Вяжущие применяют для заводского изготовления гипсовых
изделий |
и приготовления сухих |
смесей, которые |
используют |
||||||
для различных, |
в основном |
отделочных, |
работ |
в |
стро |
||||
ительстве и |
других |
отраслях |
промышленности. |
В |
зави |
||||
симости |
от |
области |
применения вяжущие |
должны |
об |
||||
ладать определенными показателями свойств. Эти |
пока |
||||||||
затели |
(скорость |
твердения, |
прочность, |
водостойкость и |
др.) зависят от вида используемого отхода промышленности и технологии его переработки в процессе производства вяжуще го. Выбор вида вяжущего и объемов его производства опреде ляется направлениями его использования (см. разд. 1.6) и тех нико-экономическими показателями в конкретных условиях региона, где' образуются отходы и должны использоваться вя жущие (см. гл. 6) [382].
3.1. ОБЩИЕ СВЕДЕНИЯ
3.1.1. Классификация и основные свойства вяжущих на основе сульфата кальция
Вяжущие на основе сульфата кальция подразделяют на гипсо вые вяжущие, в основном состоящие из полугидрата сульфата кальция (CaSO4*0,5 Н20), и ангидритовые вяжущие, в основ ном состоящие из ангидрита (CaS04); возможны их смеси. В зависимости от условий получения и свойств гипсовые вяжу щие подразделяют на обжиговые и автоклавные.
Обжиговые (низкомарочные) гипсовые |
вяжущие |
(не точ |
но— [J-гипс, p-полугидрат, строительный гипс и др.) |
получают |
|
тепловой обработкой сырья преимущественно при |
110—170 °С |
|
при атмосферном давлении с выделением |
кристаллизационной |
* И других отходов химических производств, СОСТОЯЩИХ В ОСНОВНОМ ИЗ различных модификаций сульфата кальция и содержащих примеси, соответ ствующие этим производствам.
воды в парообразном состоянии. Они содержат в основном полугидрат сульфата кальция р-формы.
Автоклавные (высокопрочные) гипсовые вяжущие |
(не точ |
но — а-гипс, а-полугидрат, высокопрочный гипс и др.) |
изготав- |
ляют тепловой обработкой сырья при 120—150 °С под избыточ ным давлением 0,13—0,4 МПа в паровой или водной среде с выделением кристаллизационной воды из гипса в жидком со стоянии, поэтому они состоят преимущественно из полугидрата сульфата кальция а-формы.
Ангидритовые вяжущие можно получить помолом ангидрит содержащего сырья (фторангидрит^Г или природного ангидри тового камня) или обжигом при 600—850 °С гипсо- и полугидратсодержащего сырья (фосфогипса, фосфополугидрата, борогипса, природного гипсового камня и др.) с последующим помолом продуктов обжига. В процессе обжига или помола мо гут вводиться добавки — катализаторы твердения (гидратации) ангидрита.
Перечисленные вяжущие, а также их смеси относятся к группе воздушных вяжущих, прочность изделий из которых при длительном нахождении в воде снижается. Это объясняет ся высокой растворимостью и способностью к перекристалли зации во влажных условиях гипса (CaS0 4-2H20), который яв ляется конечным продуктом твердения гипсовых и ангидрито вых вяжущих:
|
CaS04-0,5H20+/zH20 |
—>- CaS04-2H20+(/z — 1,5)Н20, |
|
||
|
CaS04+/iH20 — |
CaS04-2H20 -f (я — 2)Н20. |
|
||
Полная гидратация полугидрата длится от 15—20 мин |
до |
||||
нескольких" часов, |
ангидрида — от нескольких |
часов до |
не |
||
скольких |
суток, а |
иногда |
и месяцев. Создание условий |
для |
|
неполной |
гидратации и повышение средней |
плотности изго- |
тавляемых изделий являются мерами, обеспечивающими лишь временное сохранение прочности изделий при их нахождении в воде. В конечном счете свойства и области использования из делий определяются низкой водостойкостью гипса.
Из большого числа предложенных мер по повышению водо
стойкости |
гипсовых |
и ангидритовых вяжущих |
заслуживает |
внимание |
(с практической точки зрения) создание компози |
||
ционных |
вяжущих, |
содержащих в своем составе |
кроме полу |
гидрата и ангидрита гидравлические компоненты. К последним относятся цементы, шлаки, золы, нефелиновый (белитовый) шлам, содержащие силикаты, алюминаты и алюмоферриты кальция и другие минералы, продукты гидратации которых, а также продукты их взаимодействия с сульфатом кальция яв ляются водостойкими.
В связи с этим в особую группу следует выделить компози ционные вяжущие (повышенной водостойкости. Из-за многооб разия и отсутствия апробированной классификации такие вя жущие в настоящее время подразделяют только по составу
(другие виды классификации недостаточно опробированы): гипсоцементнопуццолановое, гипсоизвестковошлаковое, гипсобелитопуццолановое, гипсоцементношлакопуццолановое, ангидритоцементнопуццолановое и т. п. Обязательным при подборе состава указанных вяжущих является создание условий, пре дотвращающих образование в затвердевшей системе высокоос новного гидросульфоалюмината кальция (ЗСаО- АЬОз-ЗСаБО^ •31Н20), или эттрингита, называемого иногда «цементной ба циллой». В противном случае происходит разрушение изделий и конструкций, так как объем твердой фазы эттрингита в не сколько раз больше абсолютного объема исходных твердых фаз [154—156].
Ниже рассмотрены основные свойства вяжущих и образцов на их основе.
Т о н и н а ( с т е п е н ь ) п о м о л а характеризуется остатком при просеива нии на сите с ячейками (в свету) определенного размера и выражается в про центах к массе просеиваемого вяжущего. Наиболее распространенным ситом является сито с размером ячеек 0,2 мм (сито № 02). В соответствии с требо ваниями ГОСТ 125—79 по степени помола гипсовые вяжущие подразделяют на грубого (14—23% остатка на таком сите), среднего (2— 14%) и тонкого (менее 20%) помола. Основная доля выпускаемых вяжущих относится к про дуктам среднего помола. В ряде случаев дополнительно определяют остаток на ситах с меньшим размером ячеек, а также удельную поверхность — по ме
тодам |
воздухопроницаемости, адсорбции |
различных веществ |
и др. |
У д е л ь |
н а я |
п о в е р х н о с т ь обжиговых гипсовых вяжущих составляет |
5—8 тыс. |
||
см2/г, |
автоклавных — 3,5 тыс. см2/г. |
воды, необходимой |
для |
получения |
В о д о п о т р е б н о с т ь — количество |
теста с консистенцией, определяемой по ГОСТ 125—79 на вискозиметре Суттарда и соответствующей диаметру расплыва 180 ± 5 мм. Водопотребность — основной фактор, определяющий прочность и плотность образцов. В зависимо
сти от технологии и используемого сырья |
она может |
изменяться от 25 до |
75-90% . |
основной |
характеристикой ско |
С р о к и с х в а т ы в а н и я я в л я ю т с я |
рости твердения гипсовых и композиционных вяжущих. Гипсовые вяжущие по срокам схватывания подразделяют на быстро-, нормально- и медленнотвердеющие. У быстротвердеющих начало схватывания должно наступать не ранее 2 мин, конец— не позднее 15 мин, у нормальнотвердеющих — соответственно 6 и 30, у медленнотвердеющих начало — не ранее 20 мин, а конец схватывания не регламентируется.
П р о ч н о с т ь и з д е л и й — важный, но в ряде случаев не решающий показатель свойств вяжущих. Для гипсовых вяжущих нормативными доку ментами предусматривается определение прочности только в первоначальные
сроки твердения |
(2 ч), для некоторых видов композиционных — в более позд |
ние сроки (4 ч, |
1 сут.), ангидритовых — через несколько суток, а также после |
высушивания образцов после их предварительной выдержки в течение опре деленного времени во влажных условиях. Марка гипсовых вяжущих опре деляется пределом прочности при сжатии через 2 ч (в МПа), а композицион ных и ангидритовых — пределом прочности сухих образцов (обычно в кгс/см2) . Стандартными размерами образцов для определения прочности являются балочки размером 4X4X16 см, которые вначале испытывают на изгиб, а затем
их половники — на сжатие.
Гипсовые вяжущие могут иметь марку от Г-2 до Г-25, т. е. иметь проч ность при сжатии (через 2 ч после их изготовления) от 2 до 25 МПа. Для композиционных вяжущих установлены марки от 100 до 450, т. е. эти вяжущие имеют предел прочности в сухом состоянии от 10 до 45 МПа.
Соотношение прочностей гипсовых вяжущих |
при сжатии и изгибе через |
2 ч после изготовления и сухих образцов можно |
ориентировочно оценить по |
Рис. 3-1. |
|
R, МПа |
|
|
1700Я , |
Зависимость предела прочности при 70 |
|
|
|
||
сжатии и изгибе {R) образцов на ос- |
|
|
|
|
|
нове гипсового вяжущего из химичс- 60 |
|
|
|
||
ски чистого гипса от средней плотно |
|
|
|
|
|
сти (рСр) при различном расходе вя- 50 |
|
|
|
||
жущего |
(С?ВНП() 1 |
|
|
|
|
/ — через |
2 ч после изготовления; 2 — по* |
^ |
|
|
|
еле высушивания до постоянной массы |
30 |
|
|
|
|
|
|
|
|
|
|
данным рис. 3-1, где приведена экспе |
|
|
|
|
|
риментально полученная зависимость |
|
|
|
|
|
предела прочности от расхода вяжу |
|
|
|
|
|
щего и средней плотности образцов |
|
|
|
|
|
при использовании вяжущих, получен |
800 |
1000 |
1200 |
1400 £бят,кг/м3 |
|
ных тщательной переработкой хими- |
чески чистого гипса [168]. Такую прочность предложено принимать за потен
циальную |
(Япотеиц). Для оценки качества сырья, эффективности технологий |
и добавок |
(заполнителей) предложен так называемый коэффициент использо |
вания потенциальной прочности (/Си.п.п):
/Сн.п.п — /?факт/^потенЦ|
где Яфакт — фактическая прочность, полученная прямым испытанием образцов, МПа; Япотенц — потенциальная прочность при том же расходе вяжущего или при той же средней плотности образцов, МПа.
В о д о с т о й к о с т ь имеет значение только при применении гипсовых ма териалов и изделий в помещениях с влажным и мокрым режимом и характе ризуется коэффициентами размягчения и гидравличности, а также деформа циями влажных изделий под нагрузкой.
К о э ф ф и ц и е н т р а з м я г ч е н и я (/Сразм) — отношение прочности во донасыщенных образцов к прочности сухих образцов. Он является основным показателем свойств композиционных вяжущих и показывает величину потери прочности гипсовых изделий при увлажнении. Для вяжущих обычной водо стойкости он составляет преимущественно 0,2—0,35, а при высокой средней плотности может достичь 0,45—0,5; для композиционных — 0,5—0,8, в зависи мости от состава и плотности. Перед определением /Сразм образцы выдержива ют определенное время (преимущественно 1 сут.) в комнатных условиях, за тем сушат. Одну половину образцов испытывают в сухом состоянии, а дру гую — после насыщения водой.
Для более полной характеристики композиционных вяжущих используют к о э ф ф и ц и е н т г и д р а в л и ч н о с т и (/СгнДР) — отношение прочности об
разцов, хранящихся в воде, к прочности образцов, хранящихся в сухом состоя |
||
нии. Он показывает способность материала изменять прочность при длительном |
||
хранении в воде. Для гипсовых вяжущих с небольшой средней плотностью его |
||
значение |
приближается |
к нулю через 6— 15 мес., ангидритовых— через 1— |
2 года, |
а образцы на |
основе композиционных вяжущих сохраняют /Сшдр= |
=0,8— 1,2 в течение 5— 10 и более лет. |
|
||
В л а ж н о с т ь |
изделий |
существенно сказывается |
на технико-экономиче |
ских показателях |
процесса |
сушки (расход топлива, |
капитальные вложения |
иамортизационные затраты). Для полной гидратации гипсовых, ангидритовых
икомпозиционных вяжущих требуется 160—250 кг воды на 1 т вяжущего;
практически для изготовления изделий литьевым способом вводят до 800— 900 кг воды с целью придать формуемой смеси требуемую консистенцию. Соот ветственно даже после полной гидратации изделия содержат до 500 кг воды на 1 м3, которую необходимо частично или полностью удалить при сушке. Вместе с тем чем ниже водопотребиость вяжущего и влажность изделий, тем больше расход вяжущего, средняя плотность и масса изделий. Поэтому в каж дом конкретном случае в зависимости от свойств вяжущего и требований
оо
о
ТАБЛИЦА 3,1. Преимущественные показатели свойств различных вяжущих*
Вяжущие
Гипсовые:
обжиговые
автоклавные
Ангидритовые
Композиционные на основе:
гипсовых
Обжиговых
гипсовых
автоклавных
ангидритовых
Сроки схватывания, мин
Вод©потреб ность, %
начало конец
60—75 |
4—9 |
7—20 |
26—45 |
5—20 |
10—40 |
30-40 |
15—120 |
Несколько |
|
|
часов |
слсл - о |
|
|
о |
5—15 |
10—25 |
1 |
|
|
25—45 |
6 -4 5 |
12—90 |
30—40 |
15—120 |
Несколько |
|
|
часов |
Предел прочности при сжатии (над чертой) и изгибе (под чертой), МПа
через |
через |
сухих |
2—4 ч |
сутки |
образцов |
2 - 7 |
2—7 |
8—18 |
1.5—3.5 |
1,2—3.5 |
4—9 |
10-25 |
10—25 |
20—70 |
4,5—8,0 |
4,5—8,0 |
8—20 |
0 |
0—10 |
15—50 |
0 |
0—3 |
5—15 |
2—6 |
3—7 |
8—20 |
1—3 |
1,5—3,0 |
3—9 |
8—20 |
10—22 |
15—55 |
3—7 |
4—9 |
6—15 |
0 |
0—10 |
15—50 |
0 |
0—3 |
5—12 |
Относитель |
Средняя |
Коэффици |
|
ная влаж |
|||
ность образ |
плотность |
ент размяг |
|
цов после |
сухих образ |
чения Кразм |
|
распалубки, |
цов, кг/м3 |
||
'% |
|
|
|
27—34 |
1000—1200 |
0,2—0,35 |
|
8—20 |
1400—1850 |
0,25—0,45 |
|
10—22 |
1400—1850 |
0,25—0,5 |
|
24—34 |
1050—1250 |
0,5—0,7 |
|
11—21 |
1400—1850 |
0.5—0,8 |
|
10—23 |
1400—1850 |
О сл |
о 00 |
|
|
|
1 |
* Испытание всех видов вяжущих проводили при стандартной консистенции (с добавлением соответствующего количества воды) по ГОСТ 23789—79, характеризуемой диаметром расплыва теста 180±5 мм.