
книги / Специальные плазменные технологии
..pdfвисимости от силы тока дуги плавящегося электрода возможны два вида переноса электродного металла. При силе тока меньше некоторого критического значения столб дуги плавящегося электрода имеет цилиндрическую или слегка коническую форму, а перенос металла происходит каплями, движущимися вдоль оси дуги. Разбрызгивания нет, однако глубина проплавления основного металла значительна, так как тепловой поток дуги и капель сосредоточен на небольшой площади. При больших тепловых потоках капельный перенос переходит во вращатель- но-струйный. Для него характерны большая длина расплавленной части электрода, изгиб ее по спирали и вращение вокруг оси горелки. Электродный металл переходит в сварочную ванну в форме мелких капель, движущихся по спирали, разбрызгивание практически отсутствует. В результате вращения энергия дуги и наплавляемый металл распределяются по поверхности изделия, что приводит к получению широких плоских валиков с малым проплавлением основного металла. Кроме того, такие режимы отличаются большей производительностью. Ресурс работы плазмотронов зависит от токовых нагрузок: ток плазмы порядка 150 А, ток плавящегося электрода 300–500 А. С увеличением силы тока плазменной дуги увеличивается ширина наплавленного валика, глубина проплавления основного металла изменяется в меньшей степени. В промышленных условиях плазменную наплавку плавящимся электродом применяют для нанесения износостойких и антикоррозионных сталей и сплавов.
1.3.2. Плазменнаянаплавка понеподвижнойприсадке
Характерная особенность этой группы способов плазменной наплавки состоит в том, что в процессе наплавки присадка неподвижна относительно изделия, а плазменную дугу используют для расплавления этой присадки. Присадочный материал укладывают, насыпают, напыляют или каким-либо иным способом наносят заранее на подлежащую наплавке поверхность из-
21

делия или же подают на нее в процессе наплавки впереди дуги. В качестве присадки используют кольца или пластины, форма и размеры которых соответствуют разделке под наплавку, пасты, порошки и другие материалы.
Наплавка с применением компактной присадки в виде колец и пластин. Наплавку выполняют плазменной дугой прямого действия. Для каждого типоразмера наплавляемых деталей требуется изготовление соответствующей присадки определенной формы, что является технически и экономически оправданным только в условиях массового и серийного производства. Производительность наплавки зависит от мощности плазмотрона; глубина проплавления основного металла мала, несмотря на применение плазменной дуги прямого действия. Примером может служить плазменная наплавка выпускных клапанов автомобильных двигателей с применением компактной присадки в виде колец, изготовленных методом порошковой металлургии (рис. 8). Кольца укладывают в разделку на тарелке клапана и расплавляют плазменной дугой. В течение многих лет этот способ наплавки успешно применяется при изготовлении клапанов двигателей легковых и грузовых автомобилей.
Рис. 8. Схема плазменнойнаплавкиклапанадвигателя внутреннегосгоранияс применениемприсадкив видекольца: 1 – присадочноекольцо; 2 – клапан; 3 – плазмотрон;
4 – водоохлаждаемыйподпятник
22
Для клапанов автомобиля ЗИЛ применяют следующий режим наплавки: сила тока 200–220 А, напряжение 22–24 В, скорость наплавки 23 м/ч, расход плазмообразующего газа (аргон) 1 л/мин, расход защитного газа 5 л/мин.
Наплавка по слою пасты. Этот способ плазменной наплавки, как и пасты ЦИС 218 и ЦИС 770В, которые используются в качестве присадочного материала, был разработан в Центральном институте сварочной техники (г. Галле). Основой паст служит смесь порошков металлов, ферросплавов, карбидов и т.п., при расплавлении которых образуется износостойкий Fe-Cr-C- и Fe-Cr-V-Ni-C-сплав. При приготовлении паст используют органическую связку или растворимые в воде связующие вещества, например карбоксиметилцеллюлозу C6H7O2(OH3)3. Пасту готовят непосредственно перед употреблением и наносят шпателем на очищенную от ржавчины и оксидов поверхность изделия. Толщина слоя пасты 5–8 мм. После нанесения пасту сушат на воздухе в течение 5–12 ч. Процесс сушки можно ускорить за счет нагрева пламенем или инфракрасными лучами. При наплавке больших поверхностей применяют следующий способ нанесения пасты: путем экструдирования из нее получают полоски нужных размеров, которые затем укладывают впритык друг к другу на наплавляемую поверхность. После сушки пасту расплавляют плазменной дугой. Режим наплавки: сила тока 500–550 А, напряжение 40–45 В, скорость колебательного движения плазмотрона 48 м/ч, скорость продольного перемещения аппарата 1,25 м/ч, расход плазмообразующего газа (аргон) 6 л/мин. Так как в состав пасты вводят небольшое количество флюса, то защитный газ не применяют.
Наплавка по слою гранулированной присадки (крупки).
Присадочный материал в виде гранул неправильной формы размером 0,5–3,0 мм в поперечном сечении заранее насыпают равномерным слоем на наплавляемую поверхность изделия или же подают на нее из специального питателя в процессе наплавки (рис. 9). Расплавление слоя осуществляют плазмотроном, кото-
23

рый перемещается вслед за наконечником питателя и совершает поперечные колебания с размахом, равным ширине насыпанного слоя. Тяжелые крупные гранулы не раздуваются дугой и защитным газом.
Рис. 9. Схема наплавки по слою гранулированной присадки: 1 – источник питания; 2 – ограничительное сопротивление;
3 – электрод; 4 – ввод защитного газа; 5 – ввод плазмообразующего газа; 6 – сопло плазмотрона; 7 – питатель подачи крупки;
8 – крупка; 9 – наплавленный металл
Недостатки процесса – сложность наплавки криволинейных или цилиндрических поверхностей (при малом радиусе кривизны наплавка практически невозможна), необходимость применения формирующих приспособлений при наплавке кромок, невозможность наплавки тонких слоев металла. Производительность наплавки по слою крупки составляет 6–8 кг/ч при силе тока 250–300 А и может быть значительно повышена при использовании более мощных плазмотронов.
Центробежная плазменная наплавка. Этот способ явля-
ется разновидностью плазменной наплавки по слою порошковой или гранулированной присадки применительно к наплавке внутренних поверхностей гильз, втулок и подобных деталей цилиндрической формы (рис. 10). Сущность его заключается в сле-
24

дующем: во вращающуюся с большой скоростью деталь цилиндрической формы при помощи загрузочного устройства, например поворотного лотка, равного по длине наплавляемому участку детали, засыпают необходимое для получения наплавленного слоя заданной толщины количество порошка (крупки). Под действием центробежных сил порошок равномерно распределяется по внутренней поверхности детали. Затем в нее на длинной жесткой штанге, внутри которой проложены коммуникации для подвода тока, воды и газа, вводят плазмотрон и возбуждают дугу прямого действия. После образования кольцевой ванны расплавленного присадочного металла включают продольное перемещение плазмотрона. Для наплавки детали с внутренним диаметром свыше 150 мм можно применять несколько плазмотронов, расположенных по периметру кольцевой ванны.
Рис. 10. Схема центробежной плазменной наплавки: 1 – источник питания плазменной дуги; 2 – плазмотрон; 3 – кольцевая сварочная ванна; 4 – присадочный порошок; 5 – деталь; 6 – патрон
С увеличением числа оборотов детали поверхность наплавленного металла становится более ровной. При достаточно большой скорости вращения исключается раздувание присадочного порошка дугой, уменьшается влияние давления дуги на проплавление основного металла, обеспечивается отличное формирование наплавленного металла. Центробежным способом можно
25
наплавлять слои толщиной от 0,5 до 4 мм с хорошим качеством поверхности и минимальными припусками на обработку. При силе тока дуги 400–450 А производительность наплавки достигает 12 кг/ч; скорость вращения цилиндрической детали –
1000–1250 об/мин.
Микроплазменное оплавление предварительно напы-
ленного покрытия. Для восстановления и защиты от изнашивания деталей, у которых по условиям эксплуатации допускается небольшой линейный износ, широко применяется термическое напыление самофлюсующимися сплавами с последующим оплавлением напыленного слоя для придания ему плотности и повышения прочности сцепления с основным металлом. Оплавление можно выполнять различными способами, но во всех случаях не только покрытие, но и саму деталь нагревают до высокой температуры. Микроплазменную дугу можно применять для наплавки тонких (0,2–1,0 мм) слоев путем расплавления напыленного покрытия. Этим способом можно наносить не только самофлюсующиеся, но и другие наплавочные сплавы независимо от температуры их плавления. Однако необходимо, чтобы температура плавления покрытия была ниже, чем у основного металла. Типичные режимы механизированной наплавки: сила тока дуги 15 А, напряжение 25 В, скорость наплавки 3,5 м/ч, частота колебаний 52 мин–1, размах колебаний 6,5 мм, расход плазмообразующего газа (аргон) 0,2 л/мин, защитного (аргон +азот) 2 л/мин. На практике процесс применяется для повышения эрозионной стойкости лопаток судовых турбин.
1.3.3. Плазменно-порошковая наплавка
Плазменная наплавка с присадкой порошка в наибольшей степени отличается от других способов плазменной наплавки применяемыми материалами, оборудованием и технологическими возможностями.
26
Порошки могут быть получены практически из любого пригодного для наплавки сплава независимо от его твердости, пластичности, степени легирования и других свойств, поэтому с этой точки зрения являются универсальным присадочным материалом. В качестве присадки для плазменной наплавки применяют как собственно порошки (под порошком обычно понимают тонко измельченное твердое тело с размерами частиц до 0,1 мм, в сварочной технике – до 0,5 мм), так и более крупнозернистые сыпучие материалы с размерами частиц до
2,5–3,0 мм.
Наплавку с присадкой порошка выполняют плазменной дугой прямого действия или двумя плазменными дугами – прямого и косвенного действия с общим электродом. При этом используют различные схемы ввода порошка в дугу, которые можно разделить на две группы, отличающиеся тем, что в одной группе порошок вводят в дугу внутри плазмотрона (рис. 11), а в другой – вне его (рис. 12). В плазмотронах с внутренним вводом порошка в дугу создаются, как правило, более благоприятные условия для его нагрева плазмой. При внешней подаче порошка его нагрев менее эффективен, зато надежность работы плазмотрона несколько выше.
Запатентованные схемы ввода порошка в дугу через электродную камеру плазмотрона (рис. 11, а, б) не нашли практического применения, так как вследствие попадания порошка на электрод последний быстро выходит из строя.
Плазмотроны с подачей порошка через осевое отверстие в катоде также пока не нашли широкого применения из-за трудностей изготовления электродов с отверстием и сложностями, связанными с подачей порошка через отверстие относительно малого диаметра. Радиальный ввод порошка через боковое отверстие в канале сопла (рис. 11, в) типичен для напыления, но для наплавки используется редко. При такой схеме ввода порошка стабильная работа плазмотрона возможна лишь при сравнительно больших расходах плазмообразующего газа и ма-
27
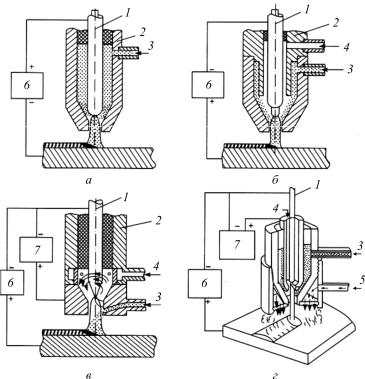
лых транспортирующего. Большой расход плазмообразующего газа нежелателен, так как ведет к увеличению глубины проплавления основного металла.
Рис. 11. Схемы плазменной наплавки с вводом присадочного порошка в дугу внутри плазмотрона: а – вместе с плазмообразующим газом; б – через электродную камеру; в – через боковое отверстие в канале сопла; г – через воронкообразуную щель между соплами; 1 – вольфрамовый или медный водоохлаждаемый электрод;
2 – сопло; 3 – ввод присадочного порошка с транспортирующим газом; 4 – ввод плазмообразующего газа; 5 – ввод защитного газа; 6 – источник питания дуги прямого действия; 7 – источник питания косвенной дуги
28
Для наплавки эффективной оказалась схема ввода порошка в дугу под углом 25–80° через воронкообразную щель, образуемую сопрягаемыми коническими поверхностями внутреннего и наружного сопел плазмотрона (рис. 11, г). В этом случае двухфазный поток транспортирующего газа и порошка концентричен дуге, поэтому не только не снижает, но и повышает его стабильность. Дуга косвенного действия горит между электродом и внутренним соплом и служит в основном для обеспечения устойчивой работы плазмотрона. Роль ее в нагреве порошка незначительна. Более мощная дуга прямого действия обеспечивает необходимый нагрев поверхности изделия, плавление присадочного металла и образование сварочной ванны.
При плазменной наплавке с внешней подачей присадочного порошка (рис. 12) последний подают в зону наплавки через отверстия в торце сопла плазмотрона (их может быть от одного до трех) или по трубке, расположенной сбоку сопла. При наплавке сплавов на основе никеля, кобальта или железа угол наклона этих отверстий (трубки), их сечение, расход транспортирующего газа
идругие параметры режима выбирают такими, чтобы порошок вводился в дугу на небольшом расстоянии от поверхности изделия и попадал в сварочную ванну под дугой (рис. 12, а, б).
При этом порошок можно подавать в дугу спереди, сзади
исбоку одновременно с нескольких сторон. При наплавке композиционных сплавов дополнительный канал для подачи упрочняющих частиц карбида вольфрама чаще всего расположен сзади дуги и имеет угол наклона, чтобы зерна карбида попадали в сварочную ванну, минуя дугу (рис. 12, в). Это позволяет устранить или, по крайней мере, уменьшить их растворение в расплаве. Сварочная ванна образуется за счет расплавления основного металла, защитного покрытия, нанесенного на зерна карбида вольфрама, или порошка сплава-связки, который подают вместе с карбидом либо отдельно от него по боковым каналам. В любом случае наплавленный металл имеет гетерогенную структуру, состоящую из относительно легкоплавкой матрицы
ине расплавившихся зерен карбида вольфрама.
29
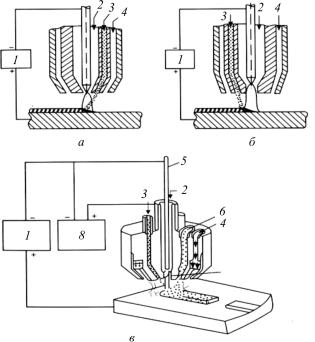
Рис. 12. Схема плазменной наплавки с внешней подачей присадочного порошка через отверстие в торце сопла: а – «углом назад»; б – «углом вперед»; в – по каналам в сопле плазмотрона; 1 – источник питания дуги прямого действия; 2 – ввод плазмообразующего газа; 3 – ввод присадочного порошка транспортирующим газом; 4 – ввод защитного газа; 5 – электрод; 6 – ввод дополнительного присадочного порошка;
7 – плазменная дуга; 8 – источник питания косвенной дуги
Очевидно, что с изменением режима работы плазмотрона и условий ввода присадочного порошка в дугу изменяются как интенсивность, так и продолжительность нагрева его частиц плазмой. Экспериментальных данных о температуре нагрева порошка в дуге при наплавке нет. Предполагается, что при подаче порошка по схеме на рис. 12 его частицы в момент соприкосновения с по-
30