
книги / Специальные плазменные технологии
..pdfПоэтому напылением можно наносить покрытия из многих неорганических материалов, которые могут быть расплавлены, т.е. не разлагаются или испаряются в твердом состоянии. В зависимости от конкретной пары материалов, покрытие – основа, температура подогрева основы Т2 может лежать как в области отрицательных температур (по стоградусной шкале), так и достигать 1000 °С и более.
Особенно удобны для напыления тугоплавкие металлы, образующие прочное покрытие при естественном подогреве основы, т. е. при комнатной температуре. Поэтому покрытия из тугоплавких металлов часто используют как подслои, которые наносят на изделие под основное покрытие и которые повышают прочность сцепления между ними.
На поверхности металлов обычно образуется тонкий устойчивый слой оксида толщиной 2–5 нм. При нагреве металла выше некоторой критической температуры (обычно 100–300 °С) слой оксида растет значительно быстрее. Толстые оксидные пленки препятствуют образованию прочного сцепления металлических частиц с основой, разделяя взаимодействующие металлы. Например, при напылении ванадия на полированный образец из никеля прочное сцепление возникает уже при 20 °С. Однако если образец предварительно выдержать в течение 1–3 мин на воздухе при 400–500 °С, а затем охладить до 20 °С, то при последующем напылении привариванию частиц мешает толстая пленка NiO. При напылении на медь толстая оксидная пленка появляется при нагреве выше 100–150 °С.
Увеличение прочности приваривания частиц к основе по мереповышения еетемпературыТ2 объясняется двумяпроцессами:
–расширением диаметра пятна химического взаимодействия Dх, на котором частица приваривалась к основе;
–повышением прочности в самом пятне Dх.
Предельным случаем для первого процесса является приваривание по всей площади Dх/D = 1 расплющенной частицы диаметром D (см. рис. 35), для второго – получение прочности
101

сцепления, соответствующей некоторой максимальной величине, близкой к прочности соединяемых металлов. Перегрев напыляемых частиц выше температуры плавления Тпл повышает прочность их соединения с основой (кривые 1 и 2, рис. 36) и увеличивает площадь пятна химического взаимодействия.
Рис. 36. Влияние перегрева серебряных частиц
искорости соударения v1 на прочность их сцепления P/Fx
ссеребряной основой: 1 – напыляемые частицы нагреты выше температуры плавления (v1≈40 м/с); 2 – частицы
расплавлены при температуре, близкой к плавлению (v1≈20…40 м/с); 3 – расплавленные частицы соударяются с основой при низкой скорости (v1<5 м/с); Р – усилие отрыва; σB – временное сопротивление серебра при растяжении
Рост прочности объясняется тем, что при перегреве частиц повышается контактная температура и процесс химического взаимодействия резко ускоряется.
Другим важным технологическим приемом повышения качества покрытий является увеличение скорости напыляемых частиц.
Существует предел скорости частиц. При напылении со скоростью частиц ниже этого предела прочность их сцепления резко снижается. «Медленные» частицы мало деформируются и почти не растекаются при ударе, в результате чего контактные процессы взаимодействия материалов частицы с основой нару-
102
шаются. Установлено, что при скорости частиц 5 м/с рост их прочности сцепления с основой замедляется (см. рис. 36, кривая 3), одновременно очень слабо увеличивается относительный диаметр пятна химического взаимодействия и по абсолютной величине не превышает 0,5 даже при очень сильном подогреве основы (см. рис. 35). В соединении покрытия с основой существенную роль играет механическое сцепление напыляемых частиц с выступами и впадинами на поверхности основы, образованными предварительной обработкой. Этот механизм адгезии покрытия называют анкерным эффектом. Кроме механического сцепления, соединение покрытия с основным материалом обеспечивается за счет диффузии компонентов покрытия в основной материал, сплавления и химического взаимодействия. При сцеплении частиц между собой внутри покрытия действуют те же механизмы, что и при взаимодействии покрытия с поверхностью основного металла. Эффективность взаимодействия значительно зависит от различия коэффициентов линейного расширения напыляемого металла и оксидов (нитридов). При охлаждении усадка металлических частиц происходит в большей степени, чем усадка оксидов, и чем значительней это различие, тем хуже условия образования прочного монолитного покрытия.
3.6. ОБОРУДОВАНИЕ ДЛЯ ПЛАЗМЕННОГО НАПЫЛЕНИЯ
Любая установка для газотермического напыления состоит из распылителя, механизма подачи распыляемого материала (проволоки или порошка); источника энергопитания; системы подачи распылительных газов; пульта управления. В некоторых установках предусмотрена система охлаждения. На рис. 37 приведена функциональная схема обобщенной установки для газотермического напыления.
103

Рис. 37. Функциональная схема установки для газотермического напыления
Общие требования, предъявляемые к установкам (аппаратам) для газотермического напыления, следующие:
–получение стабильного потока напыляемых частиц заданнойформы;
–возможность регулирования потока напыляемых частиц по производительности, скорости; обеспечение высоких значений энергетических коэффициентов распыления и напыления;
–возможность механизации и автоматизации процесса;
–высокая долговечность и надежность;
–безопасность и удобство в эксплуатации;
–экологическая приемлемость;
–минимальная материалоемкость и небольшая стоимость. Установки для плазменного напыления можно классифи-
цировать по способу получения плазмы, способу защиты процесса, давлению в камере и регенерации газа.
По способу получения плазмы различают установки с дуговыми плазменными распылителями и высокочастотными индукционными распылителями.
По способу защиты процесса большинство установок выпускается для ведения процесса на воздухе. Для напыления с местной защитой используют различные насадки на плазмотрон, местные негерметичные камеры и другие устройства. Большое распространение получают установки для плазменного напыления с общей защитой процесса в герметичных жестких камерах.
104
По давлению в камере различают установки для напыления в камерах при давлении плазмообразующего газа, близком к атмосферному (Рк ≈ 0,1 МПа); в низком вакууме (Рк = 133 Па и выше) и при повышенном давлении (Рк > 0,1 МПа). В настоящее время широко применяют установки первых двух типов. Особенно перспективны установки для напыления в низком динамическом вакууме.
По регенерации газа процесс можно производить с полным сбросом плазмообразующего газа в атмосферу и с его регенерацией по замкнутому циклу. В последнем случае установки становятся более сложными. Однако при этом в ряде случаев экономится дорогой и дефицитный газ.
Плазменные распылители предназначены для создания потока дисперсных частиц с заданной плотностью, температурой и скоростью. Требования, предъявляемые к распылителям, следующие: малая масса, особенно для ручных распылителей (до 2,5 кг), и удобство в работе, отсутствие перегрева при длительном напылении, высокие значения теплового КПД, возможность быстрой замены изношенных деталей, легкость ввода распыляемого материала.
Для плазменного напыления используют в основном дуговые плазменные распылители, ВЧ- и СВЧ-плазмотроны.
В настоящее время разработано большое количество плазменных распылителей. Простейшая конструктивная схема, отражающая принцип его работы, приведена на рис. 38. Корпус распылителя 1 состоит из трех частей. Нижняя часть связана с соплом 2 плазмотрона. При питании дуги прямой полярности (минус на электроде) – это анодный узел распылителя. Верхняя часть является стержневым электродным узлом. При прямой полярности – это катодный узел плазмотрона. В его центральной части располагается электрод 4. Сопловой и электродный узлы горелки связаны между собой электроизоляционнойпроставкой 3.
Для герметизации при интенсивном охлаждении плазмотрона водой предусмотрены прокладки 5 и крепежные винты 6.
105
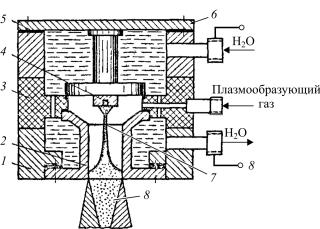
Токопровод совмещен с каналом подвода воды. Дуга 7 возбуждается и горит между стержневым электродом и соплом. Плазмообразующий газ подается в дуговую камеру распылителя через отверстие в проставке. Плазменная струя 8, вытекающая из сопла, является источником нагрева, распыления и ускорения частиц.
Рис. 38. Конструктивная схема плазменного распылителя
Подача распыляемого материала на схеме не показана. Проволока подается на срез сопла. Порошок вводят либо в различные участки плазменной струи, либо в дуговую камеру сопла. Наряду с однодуговыми плазмотронами (рис. 39, а) для напыления покрытий могут быть использованы и более сложные схемы: двухструйные (рис. 39, б), трехфазные (рис. 39, в) и др. Наиболее ответственным элементом плазменного распылителя является сопло. Именно конструкция сопла определяет длину дуги и ее стабильность, скорость и характер истечения струи, а следовательно, в значительной мере тепловой КПД распылителя и эффективный КПД процесса нагрева распыляемого материала. В плазмотронах с самоустанавливающейся дугой канал
106

сопла гладкий и имеет небольшую длину (10–30 мм). Для некоторой фиксации дуги разрядный канал выполняется с уступом.
а |
б |
в |
Рис. 39. Схемы плазменного напыления: а – однодуговыми; б – двухструйными; в – трехфазными плазмотронами; I – подача распыляемого материала; II – подача плазмообразующего газа
В плазменных горелках с фиксированной дугой применяют секционированные сопла. Наличие секций (5–10) позволяет сначала растянуть дугу, а затем фиксировать активное пятно на выходе канала. Для получения ламинарных и сверхзвуковых плазменных струй сопла профилируют. На рис. 40, а приведены конструкции сопел различного назначения.
Продолжительность работы сопла невелика и составляет 10–50 ч, поэтому конструкция распылителя должна обеспечивать легкую и быструю смену его. Сопла изготавливают в основном из меди, рассчитывают на максимальное охлаждение водой, лучше дистиллированной, по замкнутому циклу. Для уменьшения эрозии канала сопла применяют вставки из вольфрама. Это особенно необходимо при работе плазмотрона в режиме обратной полярности («минус» на сопле).
Другим ответственным элементом плазменного распылителя является стержневой электрод. Чаще всего его изготавли-
107

вают из вольфрама в виде вставки с интенсивным охлаждением водой 1 (рис. 40, б). При использовании окислительных газов вольфрам заменяют цирконием или гафнием. Образующаяся на поверхности такого электрода тугоплавкая оксидная пленка препятствует его разрушению. При работе плазмотрона в режиме обратной полярности стержневой электрод (анод) изготавливают из меди.
а |
б |
Рис. 40. Конструктивные схемы электродных узлов в плазменных распылителях: а – сопловые узлы: 1 – цилиндрическое гладкое сопло; 2 – цилиндрическое сопло с уступом; 3 – сопло с межэлектродными вставками; 4 – профилированное сопло; б – электродные узлы:
1 – вольфрамовая вставка; 2 – держатель электрода; 3 – охлаждение
В настоящее время выпускаются установки для плазменного напыления типа УМП-6, УПУ-3Д, УПУ-5 и др.
3.7. МАТЕРИАЛЫ ДЛЯ НАПЫЛЕНИЯ
Напыляемые материалы применяют в виде проволоки, прутков и порошка. Проволоку и прутки используют при газовом, дуговом, плазменном и электроимпульсном напылении, а порошки – при плазменном, детонационном и газопламенном напылении.
108
3.7.1. Напыляемые материалы в виде проволоки
Преимущество напыления материалов в виде проволоки связано с возможностью непрерывной и равномерной ее подачи в высокотемпературную зону распылителя. Для напыления применяют электродные проволоки разных марок, чаще всего износостойкие.
Алюминиевое покрытие используют для защиты черных металлов от коррозии, а в случае последующего диффузионного отжига покрытия происходит диффузия алюминия в основной металл, что позволяет получать слой, обладающий стойкостью к высокотемпературному окислению.
Цинк – используют для защиты черных металлов от коррозии.
Молибден – обладает хорошей адгезией к черным металлам. Его часто используют для нанесения подслоя, на который затем напыляют слой требуемого материала. Само молибденовое покрытие используют как средство повышения жаростойкости. Молибден является единственным промышленным металлом, обладающим стойкостью к горячей концентрированной соляной кислоте.
Медь и ее сплавы. Для напыления используют проволоку из следующих сплавов:
–чистая медь (не менее 99,9 % Си) используется для нанесения электропроводных и декоративных покрытий;
–алюминиевая бронза (5–12 % А1) с добавлением небольшого количества железа, никеля и марганца обладает высокой коррозионной стойкостью, особенно в морской воде;
–латунь защищает поверхность деталей от коррозии. Также применяются никель и его сплавы для повышения
срока службы изделий в агрессивных коррозионных средах. Углеродистую и низколегированную сталь наиболее широ-
ко используют для повышения износостойкости деталей машин, а также для реставрации изношенных деталей.
109
3.7.2. Порошковые материалы для напыления
Плазменное, детонационное и газоплазменное напыление некоторыми материалами может быть осуществлено только путем использования порошковых материалов. Для напыления применяют порошки из металлов: алюминия, цинка и их сплавов, меди, вольфрама, коррозионно-стойких сплавов. Для восстановления изношенных поверхностей напылением и напылением с оплавлением широкое применение получили порошковые самофлюсующиеся сплавы системы Ni – Cr – B – Si, в которые могут добавляться карбиды, бориды, тугоплавкие металлы (вольфрам, ванадий, хром, молибден) для образования композиционных сплавов с более высокими физико-механическими свойствами. Расширяется выпуск биметаллических термореагирующих порошковых сплавов, обладающих экзотермическими свойствами, повышающими прочность сцепления покрытия с основой и фи- зико-механические свойства покрытия в целом. Они состоят из частиц сферической или близкой к ней формы. Каждая частица такого порошка состоит из никелевого ядра, покрытого тонким слоем мелкодисперсного алюминия. Представленные в табл. 6 порошки используются не только как износостойкие покрытия, но и как жаро-, тепло-, коррозионно-стойкие покрытия для деталей, работающих при повышенных температурах, в условиях агрессивных сред.
Порошки ПГ-10Н-01, ПГ-12Н-01 составлены на основе системы Ni – Cr – B – Si – C – Fe. Твердость регулируется содержанием С, В, Cr. Напыленные соединения имеют низкий коэффициент трения, высокую допустимую рабочую температуру (до 800 °С). Их применяют при восстановлении деталей из углеродистых, коррозионно-стойких сталей, чугунов типа «вал», поршневых насосов, фасок клапанов, шеек коленчатых валов, толкателей и проч. При твердости до HRC 40 покрытия обрабатывают резаньем, свыше – шлифованием.
110