
- •FRACTURE 1977
- •МЕХАНИКА
- •ОТ РЕДАКТОРА ПЕРЕВОДА
- •СПИСОК ЛИТЕРАТУРЫ
- •1. ВВЕДЕНИЕ
- •4.1. Оценка методами механики разрушения
- •4.2. Количественное описание «пластического» роста усталостных трещин (тип I)
- •5. ЗАКЛЮЧЕНИЕ
- •СПИСОК ЛИТЕРАТУРЫ
- •НЕКОТОРЫЕ ОСОБЕННОСТИ РОСТА УСТАЛОСТНЫХ ТРЕЩИН В МЕТАЛЛАХ И СПЛАВАХ
- •ВВЕДЕНИЕ
- •НИЗКИЕ СКОРОСТИ РОСТА УСТАЛОСТНЫХ ТРЕЩИН
- •ПОРОГИ
- •ВВЕДЕНИЕ
- •ТЕОРЕТИЧЕСКАЯ ОСНОВА АНАЛИЗА ДИНАМИЧЕСКОГО РОСТА И ОСТАНОВКИ ТРЕЩИНЫ
- •ПАРАМЕТРЫ МАТЕРИАЛА
- •ПЕРСПЕКТИВЫ ПРИМЕНЕНИЯ ТЕОРИИ
- •РАСПРОСТРАНЕНИЕ ТРЕЩИН В ТРУБОПРОВОДАХ
- •ПРОЕКТИРОВАНИЕ С УЧЕТОМ ТОРМОЖЕНИЯ ТРЕЩИН
- •СПИСОК ЛИТЕРАТУРЫ
- •Разрушение при сварке
- •Трещиностойкость в зоне термического влияния (ЗТВ)
- •СПИСОК ЛИТЕРАТУРЫ
- •ЛОКАЛИЗАЦИЯ ПЛАСТИЧЕСКОГО ТЕЧЕНИЯ И ТРЕЩИНОСТОЙКОСТЬ ВЫСОКОПРОЧНЫХ МАТЕРИАЛОВ
- •СПИСОК ЛИТЕРАТУРЫ
- •ВВЕДЕНИЕ
- •Теория
- •Сравнение теории с экспериментальными данными
- •НЕКОТОРЫЕ НЕДАВНИЕ ТЕОРЕТИЧЕСКИЕ И ЭКСПЕРИМЕНТАЛЬНЫЕ ИССЛЕДОВАНИЯ ПО МЕХАНИКЕ РАЗРУШЕНИЯ
- •/^-кривая
- •Критерий COD
- •Метод /-интеграла
- •Обсуждение результатов испытаний пластин с центральной трещиной
- •Результаты и обсуждение испытаний компактных образцов на растяжение
- •IV. РАЗРУШЕНИЕ ТИПА II
- •Анализ
- •Испытания и результаты
- •СПИСОК ЛИТЕРАТУРЫ
- •РАЗРУШЕНИЕ
- •8. ОБСУЖДЕНИЕ
- •СПИСОК ЛИТЕРАТУРЫ
- •СПИСОК ЛИТЕРАТУРЫ
- •СОДЕРЖАНИЕ:
связано с диффузией водорода, и его влияние на дефекты в низкотемпературном превращении с изменением прочности происходит вблизи температур окружающей среды [5]. Раз рушение при термообработке после сварки [6] связано глав ным образом с механизмами образования новых фаз и выде лением примесей на границах зерен, вызывающими исчерпа ние пластичности при ползучести с ростом полостей.
Более подробно эти процессы разрушения описываются в следующих разделах.
Р и с . 1. Схематическая температурная зависимость вида растрескивания: растрескивания при затвердевании и при снижении пластичности (р — пла стичность, Т — температура, 1 — при нагреве, 2 — при охлаждении, 3 — сни жение пластичности, 4 — затвердевание и ликвация; ~ s — приблизительное положение солидуса).
Разрушение при сварке
Для образования трещин при затвердевании требуется на личие двух необходимых факторов:
1.Межзеренное выделение жидкой фазы, смачивающей границы зерен или твердой фазы, которая покрывает боль шую часть границ зерен, а не образует случайно разбросан ные включения. Такие выделения несколько вольно называют «пленками».
2.Деформация увеличивается, когда сварочный расплав твердеет по площади пленки, пока она не распадается на
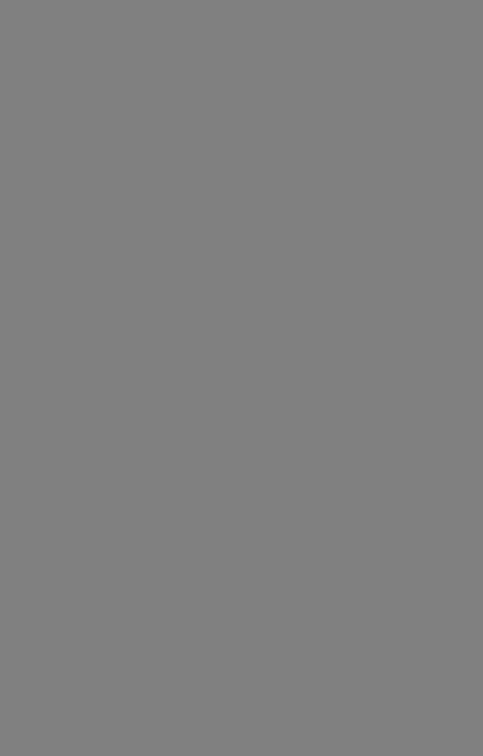
наличия сульфидов, карбидов и интерметаллических фаз мо гут образовываться полости, заполненные жидкостью. Если в сварном металле встречаются трещины ликвации, то это ог раничивается областью повторного нагрева. Если пленки встречаются как в областях повторного нагрева, так и в слоях осажденного металла, то более уместно именовать это
растрескиванием при затвердевании.
Растрескивание при снижении пластичности встречается на границах, свободных от пленок, и обычно связано с поло жением впадины на диаграмме «пластичность — температу ра». Оно наблюдалось во многих металлах и сплавах, но главным образом касается материалов с гранецентрирован ной кубической атомной решеткой, которые, как обычно счи тается, должны быть довольно пластичными при любых тем пературах. Однако в испытании на растяжение при повы шенной температуре обнаруживается, что фактически для всех материалов с таким строением имеет место сниже ние пластичности в температурном интервале между одной второй и двумя третями от температуры плавления (рис. 1). Для многих сплавов это представляет лишь академический интерес, но в некоторых аустенитных сплавах, содержащих 25% Сг, 20% Ni, такое охрупчивание может привести к рас трескиванию при сварке [9].
С помощью исследования поверхностей разрушения обна ружено, что трещины являются межзеренными, и раскрытие трещин изменяется постепенно геометрически упорядочен ным образом, в частности при наличии смещений за счет скольжения и растяжения. Эти межзеренные расщепления во многом сходны с клиновидными трещинами Стро — Мак-Ли на [10, 11], а полости подобны тем, которые встречаются при разрывах, обязанных ползучести [12]. Электронная фрактография в случае такого типа растрескивания демонстрирует термическую фасеточную структуру, декорированную иногда мелкодисперсными карбидами [2]. Из-за больших касатель ных напряжений в направлении скольжения, которые могут развиваться на границах зерен, в материалах с высоким разрушающим напряжением, увеличивающимся благодаря упрочнению и выпадению примесей, повышается опасность растрескивания.
Расслоение встречается в основном в конструкциях из прокатанного листа и вызывается температурными деформа циями. Сам разрыв всегда происходит в основном листе, за частую вне видимой зоны термического влияния, и обычно параллельно границе сплавления [3]. Для того чтобы проис
ходило расслоение, должны выполняться два основных ус ловия:

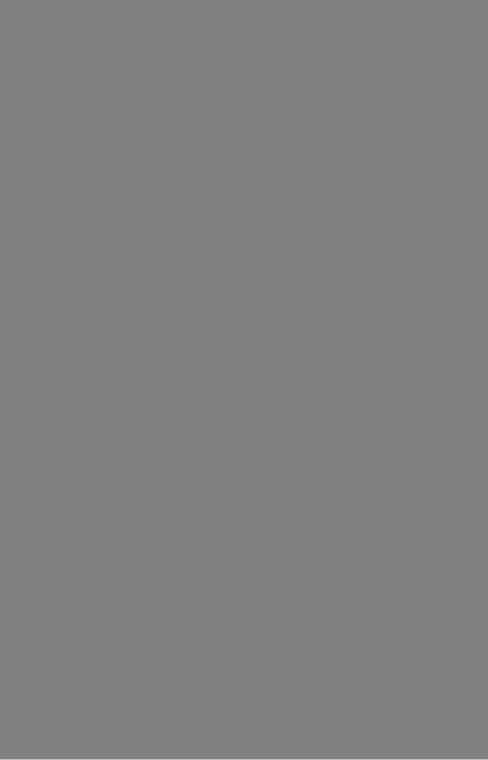
1.Согласно механизму давления, водородное растрески вание вызывается восстановлением (рекомбинацией) диффундирующего атомарного водорода до молекулярного во внутренних порах или на ступеньках дислокаций с последую щим значительным повышением давления.
2.Согласно гипотезе поверхностной энергии, охрупчива ние вызывается снижением поверхностной энергии адсорби рованным водородом. Исходя из этого, согласно критерию
Гриффитса Of ~ д/YS » видим, что адсорбция водорода ведет
кувеличению хрупкости.
3.В механизме, рассматривающем энергию сцепления, предполагается, что водород влияет на разрыв атомных свя зей в вершине трещины и, следовательно, может быть отне сен к воздействиям на межатомные силы сцепления.
4.В модели дислокационной подвижности утверждается,
что водород оказывает влияние на хрупкость при эксплуата ции оборудования, снижая локальное напряжение, необходи мое для движения дислокации, и приводя к разупрочнению твердого раствора, к более низкому локальному пределу те кучести и тем самым к более низкой интенсивности напряже ний, контролирующей распространение трещины.
Растрескивание при повторном нагреве — один из видов разрыва при ползучести — происходит в основном в сталях, сопротивляющихся ползучести и особенно содержащих Сг, Mo, V. Когда температура растет при циклическом снятии напряжений, релаксация остаточных напряжений, вызванная ползучестью, может исчерпать податливость материала в от ношении ползучести. Такая неспособность границ зерен вос принять деформацию ведет к растрескиванию при повторном нагреве (рис. 5). В этом случае в течение теплового цикла разгрузки от напряжения карбид ванадия повторно выпадает в виде мелкого осадка, сцепленного с матрицей, в пределах внутренности зерен крупнозернистой зоны термического влия ния и, таким образом, придает жесткость внутренности зер на. Вследствие этого любая полная деформация передает на грузку на границы зерен. Если приложенная деформация превосходит прочность сцепления границы зерна, то в конеч ном итоге происходит разрушение. Ситуация обостряется на личием примесных элементов на границе зерна, которые пре пятствуют скольжению и действуют как центры зарождения
полостей [16, 17].
В структурно-чувствительных материалах начало про цесса, вероятно, происходит на стадии прогрева. С помощью акустического излучения [17, 18] обнаружено много событий в температурном интервале 500—690°С. За пикоде излучения


от трещиностойкости частей сварного изделия. Большое зна чение для регулирования трещиностойкости имеет металлур гическое строение этих частей.
Трещиностойкость металла сварного шва
Трещиностойкость металла сварного шва для сталей микролегированных и с добавками С — Мп будет рассмотрена в зависимости от сопротивления сколу и пластического разру шения.
а) Микроструктурные особенности. Когда металл свар ного шва затвердевает и остывает, микроструктура может оказаться состоящей из некоторой смеси продуктов превра щения, включая эвтектоидный феррит, крупно- и мелкозерни стый бейнит и мартенсит. Тип и количество продукта превра щения зависят от химического состава металла сварного шва
искорости охлаждения.
Одругом продукте превращения, называемом игольчатым ферритом, сообщалось в основном для сварных изделий из
микролегированной стали с низким содержанием углерода (< 0 ,1 % ) [21]. Такую структуру трудно отличить от мелко зернистого бейнита, который образуется при превращении с более низкой температурой. Примеры различных продуктов превращения даны на рис. 8а — 8г.
Некоторая зона очищенных зерен обнаруживается внутри металла, подвергнутого многопроходной сварке. Очищенная зона образуется, когда температура от последующих сварок превышает критическую температуру нагрева стали Лез.
Неметаллические включения также представляют собой особенность микроструктуры металла сварного шва. Вклю чения являются частицами окислов и силикатов, которые обычно имеют сферическую форму (рис. 8г). Объемное со держание включений в сварном металле зависит от реакций металла со шлаками во время сварки. Сопротивление сколу в металле сварного шва определяется типом и количеством некоторых продуктов превращения, в то время как включе ния влияют на сопротивление пластическому разрушению.
б) Сопротивление сколу. Из-за смешения продуктов пре вращения в наплавленном металле сложную задачу пред ставляет собой необходимость определить идеальную струк туру с оптимальной трещиностойкостью и сопротивлением сколу. С помощью количественных металлографических ме тодов [22] удается связать эту задачу с вопросами о влия нии вида и количества микроструктурных составляющих в сварочном металле на сопротивление разрушению.
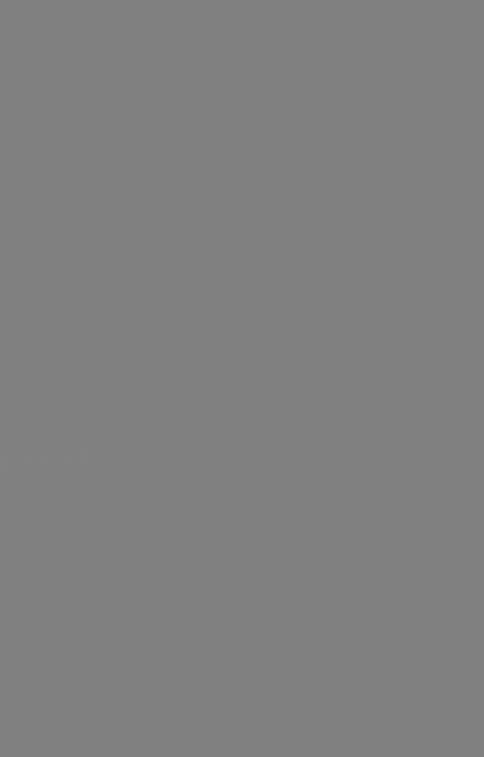
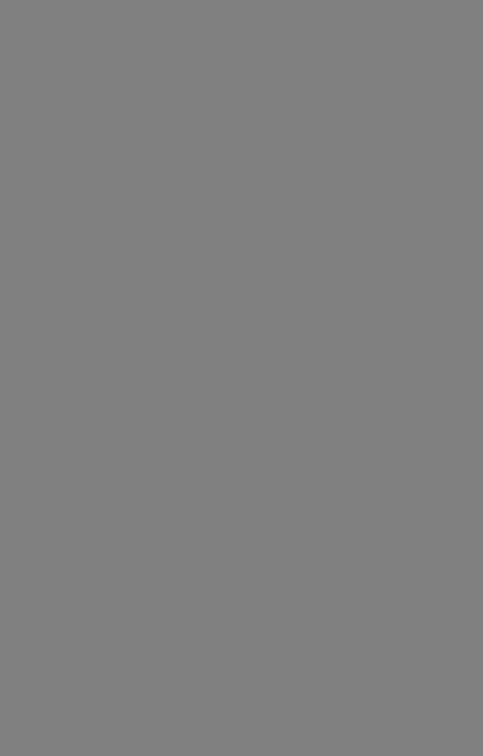
Таблица 1
Влияние микроструктуры наплавленного металла на трещиностойкость (энергия удара 68 Дж) [23]
Сварка |
Эвтектоидный |
Мелкозерни |
|
Верхний |
Другие струк |
Температура |
феррит, % |
стый бейнит, |
|
бейнит, % |
туры. % |
перехода, *С |
|
|
|
% |
|
|
|
|
1 |
13 |
76 |
| |
10 |
1 |
- 4 8 |
2 |
1 |
5 |
|
91 |
3 |
27 |
3 |
4 |
— |
|
96 |
— |
27 |
4 |
38 |
43 |
|
15 |
4 |
- 3 2 |
5 |
1 |
98 |
|
1 |
1 |
- 6 0 |
структурой сварного шва и тем самым трещиностойкостью достигается контролем состава сварного шва и скорости охлаждения.
Уместно теперь обратиться к обсуждению роли состава металла сварного шва. Основными легирующими элементами в углеродисто-марганцовистой стали, применяемой для сварки, являются Si, Мп, Мо, .Сг и Ni. В сварных изделиях из микролегированной стали необходимо учитывать влияние эле ментов Nb, Ti и V. Благодаря довольно быстрому охлажде нию имеющему место в сварочных процессах, большинство легирующих элементов, включая такие составляющие твердого карбида, как Nb, Ti и V, должны, вероятно, остаться в наплавленном металле в виде твердого раствора.
Работа [25] была одним из первых исследований по оцен ке влияния отдельных легирующих элементов на трещино стойкость наплавляемого металла при однопроходной сварке погруженной дугой и использовании в качестве основного металла углеродисто-марганцовистой стали типа А201. На
рис. 9 видно, что малые концентрации |
таких добавок, как |
Si Сг, Мп и Ni, не влияют или слабо |
повышают трещино |
стойкость. Однако с увеличением количества этих элементов может произойти снижение трещиностойкости. Элементы С и V оказывают вредное влияние на трещиностойкость даже при относительно низком уровне концентрации добавок. Хотя анализ микроструктуры был ограниченным, установлено, что измельчение ферритных зерен [не выяснено, какого типа, эвтектоидного или бейнитного) соответствует увеличению трещиностойкости. Уменьшение трещиностойкости было свя зано с образованием крупнозернистого бейнита и увеличи вающейся доли карбидных включений.
В недавних исследованиях, особенно сварных изделий из микролегированной стали, более широко изучена роль микроструктурных изменений, вызванных легирующими элемен тами в наплавленном металле. Наибольшее внимание было уделено видам сварки с большим подводом тепла, благо даря которому растворение Nb в наплавленном металле мо жет достигать 60%. Данные Соухилла [26] и Ханнерца [27], приведенные на рис. 10, указывают на увеличение темпера туры перехода в испытаниях по Шарли с увеличением содер жания Nb в наплавленном металле. Соухилл сообщил, что
Р и с . 9. Влияние легирующих элементов на температуру перехода в ис пытаниях Шарпи в наплавленном металле в случае сварки погруженной дугой [25] (Т — температура в градусах Цельсия, С — весовая концентрация добавок).
при заданной скорости охлаждения микроструктура измени лась от мелкозернистого бейнита к крупнозернистому с уве личением содержания Nb на 0,05%. Увеличение доли круп нозернистого бейнита сопровождалось ухудшением трещиностойкости. Добавление в отдельности титана Ti [28] и вана дия V [29] в наплавленный металл может вызвать аналогич ное уменьшение трещиностойкости. Во всех исследованиях имеется мало информации о том, как микроскопические до бавки веществ влияют на кинетику распада аустенита.
Чтобы устранить потерю в трещиностойкости за счет мик ролегирования, в металл сварного шва добавляют и другие элементы. Например, Соухилл [30] увеличивал трещиностойкость наплавленного металла, содержащего 0,05% Nb, путем
добавления V, Ti, Сг и Мо как по отдельности, так и вме сте. Это улучшение трещиностойкости было связано с из мельчением бейнитной микроструктуры.
Чтобы достичь оптимальности сопротивления сколу, не обходимо больше знать о кинетике распада аустенита на другие продукты при понижении температуры. Чувствуется отсутствие диаграмм превращений при непрерывном охлаж дении для составляющих наплавленного металла, в частно сти для сварных узлов из микролегированной стали. Такая
Р и с. 10. Зависимость температуры |
перехода в испытаниях Шарли от |
||
концентрации Nb. |
(Т — температура |
перехода в |
градусах Цельсия, |
С — концентрация |
Nb в %, • . при энергии удара |
68 Дж [20], X . при |
|
|
энергии удара |
22 Дж [21].) |
|
информация позволила бы инженеру по сварке выбрать сва рочные электроды и методику, которые приводили бы к со ставу сварного шва и скорости охлаждения, необходимым Для получения желательных продуктов превращения.
в) Сопротивление пластическому разрушению. Энергия, необходимая для пластического разрушения наплавленного металла, непосредственно связана с объемным содержанием
включений Vfi
v ^ vf ~ T ‘
Здесь С — размер частицы, Л — расстояние между частицами. Эта энергия может быть выражена через значение энергии на верхней полочке температурной кривой для ударных ис пытаний по Шарли, или через величину COD, соответствую щую плато на диаграмме зависимости COD от температуры.
Один из механизмов разрушения [31] состоит в образова нии пустот за счет нарушения сцепления на поверхности раздела между включениями и матрицей, сопровождаемого пластической деформацией и сдвиговым разрушением в об ласти между частицами.
Р и с . 11. Влияние содержания |
кислорода в металле сварного |
шва на |
||
предельную энергию в испытании |
Шарпи [32] (U — верхний предел энер |
|||
гии |
в Дж, С — концентрация кислорода в частях на |
106 частей металла). |
||
ся |
Поскольку включениями в наплавленном металле являют |
|||
главным образом окислы и силикаты, |
объемная |
доля |
включений может быть непосредственно связана с содержа нием кислорода. Тейлор и Фаррар [32] собрали данные о связи верхнего предела энергии в испытании по Шарпи с содержанием кислорода для металла, наплавленного при сварке погруженной дугой. Как продемонстрировано на рис. 11, предельная энергия уменьшается с увеличением со держания кислорода, и наиболее резкое изменение происхо дит в области концентраций от 300 до 600 частей кислорода на 106 частей сплава.
Регулирование содержания включений или кислорода в металле сварного шва оказывает влияние на реакции между шлаком и металлом, которые происходят во время сварки.