
книги / Машины и оборудование нефтяных и газовых промыслов. Силовые приводы машин и оборудования нефтяных и газовых промыслов
.pdfизносостойкостью и сопротивлением ударным нагрузкам. От диаметра валика зависят прочность цепи и контактное давление в шарнире цепи. Изготовляют валики из стали марки 12ХН3А по ГОСТ 4543–71 либо из стали марки 25Н3, цементируют на глубину 0,05–0,08 от их диаметра, и после термообработки они имеют твердость поверхности 54–61 HRC и сердцевины 43–48 HRC. Концы валиков перед раскаткой подвергают отжигу.
Втулки цепи изготовляют из стали марки 12ХНЗА или 12ХН2 и подвергают цементации на глубину 0,3–0,7 мм для цепей с шагом 31,75 и 38,1 мм и 0,4–0,8 мм – с шагом 44,45–63,5 мм. Твердость после термообработки 54–61 HRC. Втулки входят в отверстия пластины с натягом, и для устранения среза металла торцы их по наружному диаметру скругляют. Часть поверхности втулки, контактирующая с отверстием пластины, желательно полировать.
Ролики цепи непосредственно контактируют с зубьями звездочек и подвергаются ударам и износу. Диаметр ролика выбирают в зависимости от шага цепи. Он является исходным параметром для построения профиля звездочки. Изготовляют их из стали марки 30ХНЗА и закаливают до твердости 45–52 HRC.
Соединения валик–пластина и втулка–пластина, собираемые с натягом, проверяют на проворачивание. Крутящие моменты, необходимые для проворачивания втулок и валиков относительно пластины, возрастают с увеличением шага цепи и должны быть в пределах, регламентированных техническими требованиями ГОСТ 21834–76.
Число деталей, используемых для сборки цепи, зависит от рядности и числа шагов (звеньев):
–наружных пластин zн = Lt;
–промежуточных пластин zп = (a – 1) Lt;
–внутренних пластин zвн = aLt;
–валиков zвал = Lt;
– втулок и роликов zвт = zp = aLt (Lt – длина цепи в шагах; а – число рядов цепи). Число шплинтов равно числу соединительных звеньев.
Роликовые цепи характеризуются следующими геометрическими параметрами (см. рис. 2.5): шаг t, диаметр ролика d, расстояние между внутренними пластинами bвн, ширина цепи В.
Шаг цепи измеряется расстоянием между осями двух роликов внутренних и наружных звеньев при натянутом состоянии цепи под нагрузкой, равной 0,01 от разрушающей нагрузки. Различают действительный шаг, измеряемый между смежными звеньями, и средний шаг, определяемый как частное от деления длины некоторого отрезка цепи на число звеньев, входящих в данный отрезок t = lц/mt.
Число звеньев в измеряемом отрезке зависит от шага: |
|
|
|||||
Шаг, мм |
25,4 |
31,75 |
38,1 |
44,45 |
50,8 |
51,15 |
63,5 |
Число звеньев |
49 |
47 |
39 |
33 |
29 |
25 |
23 |
В изношенной цепи шаг внутренних и наружных звеньев неодинаков, поэтому необходимо определять средний шаг tcp на отрезке цепи, содержащем не менее десяти четных чисел звеньев. Удлинение цепи (вытяжка) вследствие износа шарниров
|
tcp t |
100 %. |
(2.15) |
|
t |
||||
|
|
|
||
Диаметр ролика d определяет радиусы впадин сопряжения и |
головки зуба |
звездочек. Отношение шага к диаметру ролика принимается за геометрическую характеристику зацепления цепи λ = t/d. Расстояния между внутренними пластинами bвн и между осями рядов А цепи определяют размеры поперечного профиля звездочки.
31
Разрушающая нагрузка Рр цепи соответствует минимальной статической нагрузке, при которой начинается разрушение цепи, и определяется путем растяжения цепи на универсальных разрывных машинах.
Технические условия на приводные роликовые цепи буровых установок регламентируются ГОСТ 21834–76, которым также предусматривается изготовление цепей двух типов: нормальных Н и тяжелых Т (с утолщенными пластинами). Нормальные цепи легче тяжелых и могут работать при более высоких (на 10–15 %) скоростях движения цепи. Однако при малых и средних скоростях они имеют меньший срок службы (на 10–15 %).
Цепи для буровых установок должны удовлетворять следующим техническим требованиям:
–крутящие моменты при испытании на проворачивание валика в пластине должны быть в пределах 18–160 Н·м и втулок в пластине – 11–100 Н·м в зависимости от шага и типа цепи; предельные отклонения длины измеряемого отрезка цепи, состоящего из 11 звеньев, от номинального значения должны быть только положительными и составлять 0,15 %;
–предельное отклонение действительного шага от его номинального значения по длине цепи, а также разность действительных шагов в каждом ряду по ширине цепи
должны строго соответствовать принятым нормам;
–разность посадочных размеров промежуточных пластин одного наружного звена не должна быть более 0,02 мм для цепей с шагом от 25,4 до 38,1 мм и не более 0,03 мм для цепей с шагом от 44,45 до 63,5 мм;
–предельная амплитуда напряжений промежуточных пластин должна быть не менее 50 МПа при базе испытаний 5·106 циклов, для чего рекомендуется упрочнять их путем дорнования и обжатия краев отверстий;
–каждая собранная цепь должна быть обтянута в течение не менее 1 мин на стенде при нагрузках 0,25–0,33 от соответствующей разрушающей нагрузки;
–ресурс цепи до списания должен быть не менее 3000 ч при коэффициенте запаса по сопротивлению усталости, равном 1,1;
–собранная цепь должна иметь легкую (без заедания) подвижность в шарнирных
соединениях, проверяемую поворотом звеньев цепи рукой на 90°;
–цепи не должны иметь пропеллерности и серповидности, препятствующих замыканию цепи в контур усилием руки;
–детали цепи не должны иметь окалины, трещины, заусенцев и коррозии;
–для защиты от коррозии пластины цепей подвергаются фосфатированию;
–длина цепи устанавливается по согласованию с потребителем.
Примеры условных обозначений. Цепь однорядная нормальная с шагом 38,1 мм: 1Н-38,1 ГОСТ 21834–76. Цепь трехрядная тяжелая с шагом 44,45 мм: ЗТ-44,45 ГОСТ 21834–76. Переходное звено однорядной цепи нормального типа с шагом 50,8 мм: П-1Н-50,8 ГОСТ 21834–76. Переходное звено двухрядной цепи тяжелого типа с шагом 50,8 мм: П-2Т-50,8 ГОСТ 21834–76 [1].
2.2.2. Звездочки к цепям
Колеса цепных передач в отличие от зубчатых называются звездочками. Долговечность и надежность цепной передачи значительно зависят от правильного выбора формы зуба, материала, термообработки и точности изготовления звездочек. Форма зуба определяется продольным профилем, являющимся основным поперечным профилем и профилем сечений зуба в плане. Для нормального взаимодействия с цепью форма зуба звездочек должна обеспечить плавное зацепление со звеньями цепи, минимальные значения контактного давления и устранить возможность соскакивания изношенной цепи со звездочки при увеличении шага цепи в пределах установленной нормы. Наряду с этим, форма зуба должна быть простой в изготовлении.
32
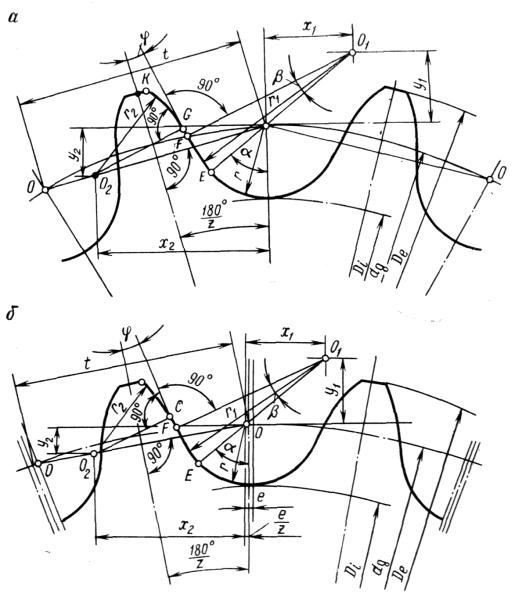
Наиболее полно указанным требованиям отвечает форма зуба с вогнуто-выпуклым основным профилем (рис. 2.6), параметры которого регламентируются ГОСТ 591–69. Стандарт устанавливает два профиля зубьев звездочек: без смещения центров дуг впадин и со смещением центров дуг впадин. Звездочки с профилем без смещения центров дуг впадин рекомендуется применять в особо точных передачах. В буровых установках применяются звездочки со смещенными центрами дуг впадин, отличающиеся тем, что впадина зуба очерчивается из двух центров, смещенных на величину e = 0,03t.
Расчет и построение теоретического (исходного) профиля зубьев выполняются в соответствии с рис. 2.6. Диаметр окружности выступов следует вычислять с точностью до 0,1 мм, остальные линейные размеры – до 0,01 мм, а угловые – до 1'. Расчет и построение основных размеров зубьев и венцов однорядной, двухрядной и многорядной звездочек в поперечном сечении следует выполнять в соответствии с рис. 2.7.
Рис. 2.6. Профиль зубьев звездочек:
а – без смещения центров дуг впадин; б – со смещением центров дуг впадин
33

Рис. 2.7. Профиль зубьев и венцов звездочек в поперечном сечении: а – однорядные; б – двухрядные; в – трехрядные
Наиболее распространены звездочки, у которых сечение зуба в плане представляет собой прямоугольник (рис. 2.8, а). Для устранения перекосов при контакте роликов цепи с зубьями звездочки необходимо обеспечить перпендикулярность образующей зуба к торцу венца и параллельность с осью отверстия ступицы. Выпуклая форма сечений зуба (рис. 2.8, в), обеспечивающая нормальную работу передачи в случае относительного смещения звездочек, более сложная в изготовлении.
Рис. 2.8. Профиль зубьев звездочек в сечении (плане): а – прямолинейный; б – вогнутый; в – выпуклый
Искажение профиля зубьев звездочек ухудшает работу передач и приводит к преждевременным разрушениям цепи. Ввиду этого материал и термообработка должны обеспечить прочность и износостойкость зубьев. В цепных передачах буровых установок звездочки изготавливают из сталей марок 40Х, 40Г2, 50Г2, 35ГС, 40ХНЛ9Ф с поверхностной закалкой до твердости 42–52 HRC. Предельные отклонения и допуски на шаг, диаметр окружности выступов, впадин и другие конструктивные размеры зубьев в зависимости от шага и числа зубьев звездочки регламентируются ГОСТ 591–69 [1, 12].
2.2.3. Смазка цепных передач
Смазка благоприятно влияет на износостойкость и выносливость цепных передач, смягчает удары роликов о зубья цепи и отводит тепло, возникающее в результате трения в шарнирных соединениях. Благодаря смазке снижается крутящий момент, необходимый для огибания звездочек, и устраняется проворачивание валиков и втулок относительно проушин пластин. Способ смазки и марка масел, выбираемые с учетом условий и режима работы цепной передачи, должны обеспечивать поступление масла в шарниры цепи и охлаждение цепи до практически приемлемых температур. В табл. 2.2 приведены рекомендации по выбору способа смазки цепных передач буровых установок в зависимости от скорости цепи.
При ручном способе масло наносят на цепь с помощью кисти либо масленки через каждые 8–10 ч работы. Капельная смазка осуществляется с помощью масленоккапельниц. Масло закапывают в зазоры между внутренними и наружными пластинами цепей. В масляной ванне цепь погружается в масло так, чтобы в самой низкой точке глубина погружения не превышала высоты пластины цепи. Циркуляционная (струйная)
34
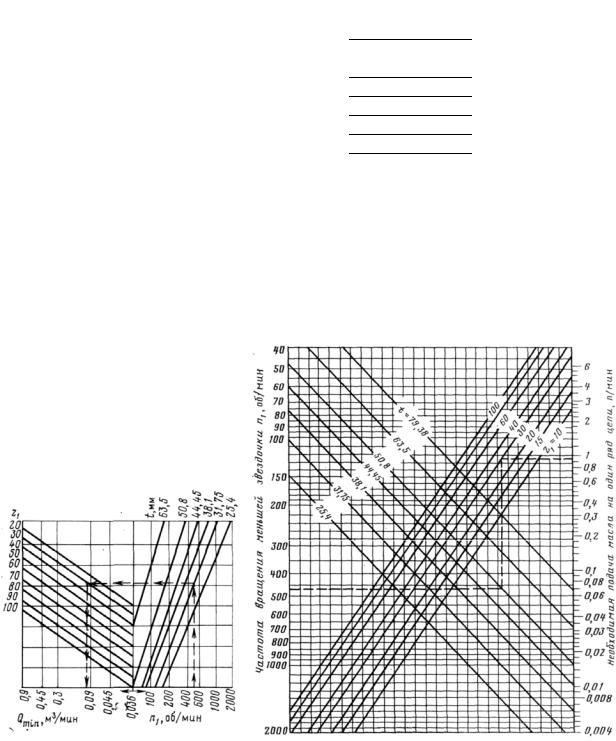
смазка осуществляется с помощью насоса, подающего масло по маслопроводу на ведомую ветвь цепи в месте выхода из зацепления с ведущей звездочкой.
|
Способы смазки цепных передач |
Таблица 2.2 |
|||
|
|
|
|||
|
|
|
|
|
|
|
|
Способ смазки |
|
|
|
Шаг цепи, |
Ручная |
Капельная |
Масляная |
Циркуляционная |
|
|
|
ванна |
|
|
|
мм |
|
|
|
|
|
|
Линейная скорость цепи, мм |
|
|
||
|
|
|
|
||
|
не более |
не более |
не более |
свыше |
|
25,40 |
0,86 |
3,30 |
7,62 |
7,62 |
|
31,75 |
0,76 |
2,64 |
6,60 |
6,60 |
|
38,10 |
0,66 |
2,18 |
6,10 |
6,10 |
|
44,45 |
0,58 |
1,88 |
5,59 |
5,59 |
|
50,80 |
0,51 |
1,68 |
5,08 |
5,08 |
|
57,15 |
0,48 |
1,52 |
4,83 |
4,83 |
|
63,50 |
0,43 |
1,32 |
4,57 |
4,57 |
|
Для более интенсивного отвода тепла используется дополнительная маслоотводная трубка с отверстиями, по которой масло подается на ведущую ветвь цепи в месте выхода из зацепления с ведомой звездочкой. Расход масла на один ряд цепи в зависимости от ее шага t, частоты вращения n1 и числа зубьев z1 меньшей звездочки определяют по номограмме (рис. 2.9).
Рис. 2.9. Графики для определения количества смазки Qmin, подаваемой на один ряд цепи, в зависимости от частоты вращения n1 и числа зубьев малой звездочки z1
35

36
Рис. 2.10. Система смазки цепного редуктора

Рекомендуемые марки масел для циркуляционной смазки при помощи насоса указаны ниже.
Температура окружающей среды, °С |
<5 |
5–30 |
>30 |
Марка масла по ГОСТ 20799–75 |
И-20А |
И-50А |
И-70А |
|
И-30А |
|
|
Масло заменяют через 6 мес. эксплуатации цепной передачи. Внеочередная замена проводится в случае изменения температуры окружающей среды, когда требуется увеличить или уменьшить вязкость используемого масла.
Цепные передачи предохраняют от грязи и пыли кожухами, которые одновременно служат резервуаром для масла, обеспечивают безопасность работы и гашение шума. При ручной и капельной смазках используются кожухи облегченной конструкции для сбора масла и обеспечения безопасности обслуживающего персонала. Кожухи цепных трансмиссий привода буровой установки, коробки перемены передач, снабженные циркуляционной смазкой, являются несущими конструкциями и должны обладать необходимой прочностью и жесткостью. Крышки кожухов изготовляются быстросъемными и имеют окна для осмотра и ремонта цепи. Смотровые окна располагаются над звездочками, а окна для ремонта – в средней части крышки.
Утечки масла предотвращаются уплотнениями, устанавливаемыми в разъемных соединениях и в подшипниках валов. Крышка и днище рассчитываются по сопротивлению ударным нагрузкам, возникающим при обрывах цепи. Между натянутыми ветвями цепи и выступающими деталями кожуха рекомендуется иметь зазор (мм)
h |
At (30 50) , |
(2.16) |
где А и t – межцентровое расстояние и шаг цепи, мм.
Площадь поверхности кожуха должна быть достаточной для отвода тепла.
На рис. 2.10 показана система смазки цепного редуктора. Масляные насосы 5, 6 приводятся в действие цепной передачей от крайних валов цепного редуктора. Из картера редуктора масло подается в маслопроводы 1, 2, 3, 4 и через распылители 8, 9 и 12 поступает на цепи. По маслопроводу 11 масло направляется в фильтр 10, из которого после очистки поступает по наружным трубам к подшипникам валов редуктора. Уровень масла в редукторе проверяется щупом 13. Масло сливается через вентиль 7 и отверстия на дне редуктора, которые закрываются резьбовыми пробками [1].
2.3.Муфты
2.3.1.Общие сведения
Муфты передают вращение с одного вала на другой или с вала на свободно сидящую на нем деталь (например, цепную звездочку, зубчатое колесо). Характерная особенность муфт заключается в том, что они не изменяют величину и направление передаваемого вращающего момента. Муфты выбирают по передаваемому вращающему моменту и диаметру соединяемых валов. В буровых машинах и механизмах используются муфты различных конструкций и видов, отвечающие определенным монтажным и эксплуатационным требованиям.
Муфты делятся на механические, гидравлические и электромагнитные. Механические муфты по назначению подразделяются на постоянные и сцепные. Постоянные муфты не допускают разъединения валов в процессе работы машины. Для разъединения валов, соединенных постоянными муфтами, требуется их разборка,
37
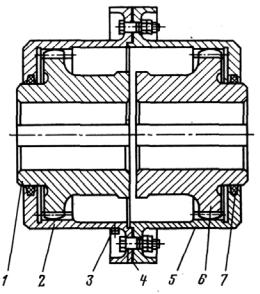
которая производится при ремонте и демонтаже. Сцепные муфты служат для соединения и разъединения валов на ходу или при кратковременных остановках [1].
2.3.2. Постоянные муфты
Для постоянного соединения валов применяются неподвижные (глухие) и подвижные муфты. Наиболее просты по конструкции глухие муфты, выпускаемые трех видов: втулочные со штифтами и со шпонками, фланцевые (поперечно-свертные) и продольно-свертные. Глухие муфты могут быть использованы при строгой соосности валов. В буровых машинах трудно обеспечить необходимую для установки глухих муфт соосность валов. Высокая точность, достигнутая при изготовлении и сборке, в процессе эксплуатации может быть нарушена вследствие деформации валов и вибрации оснований буровых машин, осадки фундамента, температурных изменений и других причин. Ввиду этого в машинах и агрегатах бурового комплекса для постоянных соединений преимущественно используются подвижные муфты, допускающие взаимное смещение валов за счет подвижных элементов муфты. К подвижным муфтам относятся жесткие компенсирующие, шарнирные и упругие. Все три типа применяются в буровых машинах.
Из жестких компенсирующих муфт наиболее распространены зубчатые, способные компенсировать незначительные осевые, радиальные и угловые смещения соединяемых валов. На рис. 2.11 показана зубчатая муфта, соединяющая тихоходный вал редуктора с трансмиссионным валом регулятора подачи долота. Муфта состоит из обойм 2 и 5 с внутренними зубьями, находящимися в зацеплении с наружными зубьями втулок 1 и 6. Для снижения потерь на трение и увеличения долговечности зубчатое зацепление работает в масляной ванне, герметизированной прокладкой 4 и войлочными кольцами 7. Отверстие для масла закрывается пробкой 3. Аналогичная муфта применяется во вспомогательных лебедках.
Рис. 2.11. Зубчатая муфта
Шарнирные муфты применяют для соединения валов, оси которых расположены под большим углом друг к другу, причем в процессе работы величина угла наклона может изменяться. Шарнирная муфта состоит из двух валов и шарнирно соединенной с ними крестовины. Недостаток шарнирной муфты – неравномерность вращения ведомого вала при равномерном вращении ведущего, если валы установлены несоосно. Для устранения этого недостатка применяют сдвоенные шарнирные муфты с промежуточным валом, образующие в этой комбинации карданную передачу, которую
38
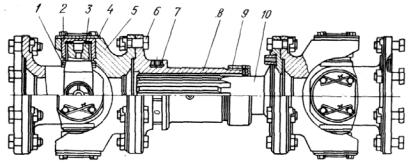
принято называть карданным валом. Карданные валы применяют в приводе буровых установок для передачи вращающего момента от гидротрансформатора к суммирующему редуктору, буровым насосам и ротору в тех случаях, когда они располагаются на разных отметках по высоте. Для равномерного вращения ведомого звена необходимо обеспечить параллельность валов, соединяемых карданным валом. В буровых машинах применяется шесть типоразмеров карданных валов.
Устройство карданного вала показано на рис. 2.12.
Рис. 2.12. Карданный вал:
1 – уплотнение; 2 – обойма с игольчатыми подшипниками; 3 – крестовина; 4 – крышка; 5 – вилка; 6 – болт; 7 – балансир; 8 – шлицевая муфта; 9 – гайка;
10 – шлицевой вал
Упругие подвижные муфты характеризуются наличием упругого элемента, за счет деформации которого происходит взаимное перемещение деталей муфты, необходимое для компенсации смещения осей соединяемых валов. Наряду с этим, упругие муфты смягчают толчки и удары и служат средством защиты от резонансных крутильных колебаний, возникающих вследствие неравномерности вращения. Упругие муфты изготовляются с металлическими и неметаллическими, преимущественно резиновыми, упругими элементами. В буровых машинах и агрегатах применяются муфты с резиновыми упругими элементами благодаря сравнительной простоте конструкции, низкой стоимости, отсутствию особых требований по уходу, высоким компенсационным свойствам и хорошей демпфирующей способности. При работе с электродвигателями важное значение приобретает электроизолирующая способность муфт с резиновыми упругими элементами.
Для соединения тяжело нагруженных валов буровых машин и агрегатов, а также для соединения вала электродвигателя с трансмиссионным валом бурового насоса и промежуточным валом лебедки применяют упругие (эластичные) муфты, конструкция которых показана на рис. 2.13. Полумуфта 1 с конусной расточкой устанавливается на консоль вала и крепится гайкой 2, предохраняемой от самоотвинчивания специальной шайбой. Вторая полумуфта состоит из ступицы 8 и стакана 6, соединяющихся болтами 7. Ступица имеет цилиндрическую расточку и крепится на консоли вала шпонкой. В утолщенных ободах стакана 6 и диска ступицы 3 имеются отверстия для резиновых валиков 4. Последние предохраняются от выпадания пружинным кольцом 5, установленным в кольцевом пазе обода стакана.
39

Рис. 2.13. Упругая эластичная муфта |
Рис. 2.14. Упругая муфта дизеля |
На рис. 2.14 показана упругая муфта для соединения коленчатого вала дизеля с валом редуктора. Диск 2 с зубчатым венцом 3 для запуска дизеля стартером устанавливается на шлицы вала дизеля и центрируется на нем конусами 1 и 7. Конусы затягиваются при помощи разрезной пробки 8, ввинченной в вал дизеля и надежно закрепленной конической пробкой 13, гайкой 11 и шайбой 12. Ведомый стакан 6 закреплен на коническом конце быстроходного вала 9 понизительного редуктора и застопорен гайкой 10. В ведущем и ведомом дисках установлено по девять пальцев 5 и 14, которые попарно соединяются пластинами 4 из прорезиненной ткани [1].
2.3.3. Сцепные муфты
Сцепные муфты используются при частых пусках и остановках, при необходимости изменения режима работы и реверсировании. Вращающий момент передается зацеплением (сцепные кулачковые и зубчатые муфты) либо силами трения (фрикционные сцепные муфты).
Сцепные кулачковые и зубчатые муфты состоят из двух полумуфт, одна из которых крепится на ведущем валу, а другая перемещается на шпонках или шлицах ведомого вала с помощью вилки и сухарей.
В тяжело нагруженных реверсируемых соединениях применяются кулачковые муфты с прямыми кулачками, число которых выбирают в зависимости от передаваемого вращающего момента (при данном диаметре муфты число кулачков тем меньше, чем больше вращающий момент). Подвижную муфту обычно располагают на ведомом валу, что позволяет уменьшить износ деталей управления муфтой. Для нереверсивных соединений применяют муфты с тремя или шестью косыми кулачками. Кулачковые муфты очень чувствительны к перекосам и несоосности валов и применяются в основном для соединения свободно вращающихся цепных звездочек с валом в коробках перемены передач буровой лебедки и цепных редукторах. Реже, например для соединения регулятора подачи долота и гидродинамического тормоза с
40