
книги / Развитие усталостных трещин в материалах и конструкциях
..pdf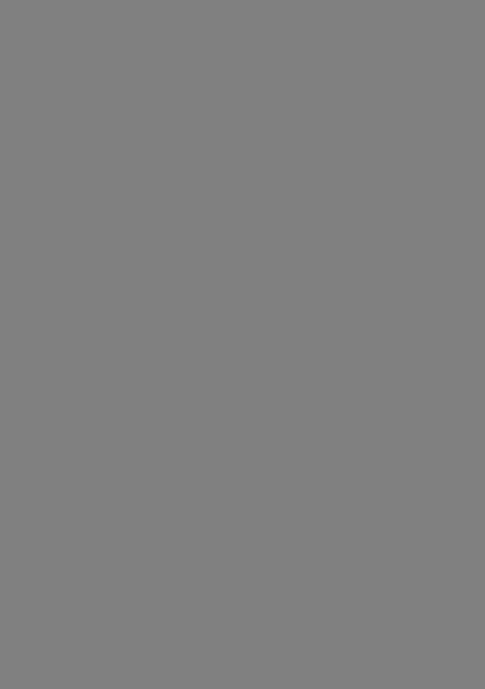

В настоящее время много внимания уделяется вопросам обеспече ния безопасности эксплуатации и прогнозирования остающегося ресурса ответст венных динамически нагруженных конструкций, ослабленных трещиной усталос ти, т. е. работающих в условиях начавшегося усталостного разрушения. В ряде случаев критерии линейной и нелинейной механики разрушения дают возмож ность с некоторой степенью точности определить скорость развития возникшей трещины, оценить способность материала сопротивляться дальнейшему ее разви тию и прогнозировать долговечность поврежденной конструкции.
Вместе с тем следует иметь в виду, что результаты аналитических подходов- к изучению кинетики роста трещин усталости пока не могут дать исчерпывающих ответов на многие важные для практики вопросы, так как эти подходы всегда базируются на тех или иных модельных представлениях, схематизирующих и упрощающих описание весьма сложного процесса усталостного разрушения кон струкционных материалов. В связи с этим большое значение приобретают экспе риментальные методы соответствующих исследований, которым доступно накопле ние опытных данных, позволяющих при описании закономерностей развитияусталостного разрушения охарактеризовать влияние многочисленных эксплуата ционных, технологических и конструкционных факторов, не улавливаемое ана литическими методами расчета.
В предлагаемой монографии систематизированы полученные в Институте ме ханики АН УССР результаты методических разработок и экспериментальных исследований кинетики роста усталостных трещин и накопления повреждений- в некоторых металлических и композиционных материалах и в натурных конст рукциях. В связи с существенным различием в характере разрушения металлов и< композитов, а также в подходах к изучению кинетики их разрушения эксперимен тальные данные, относящиеся к этим двум группам конструкционных материалов, рассматриваются в монографии раздельно.
Г л а в а 1
МЕТОДЫ И СРЕДСТВА ИССЛЕДОВАНИЯ ЗАКОНОМЕРНОСТЕЙ р а з в и т и я УСТАЛОСТНЫХ ТРЕЩИН
§ 1. МАШИНЫ ДЛЯ ИЗУЧЕНИЯ КИНЕТИКИ УСТАЛОСТНОГО РАЗРУШЕНИЯ МАТЕРИАЛОВ И ДЕТАЛЕЙ
Требования, предъявляемые к научному оборудованию при изучении кинетики усталостного разрушения материалов и конструкций, не могут быть общими для всех случаев и должны определяться конкретными задачами, которые ставятся перед каж дым планируемым исследованием. Актуальность экспериментального изучения закономерностей развития уже возникших трещин уста лости в металлах и полимерах обусловлена тем, что основными для большинства конструкций являются динамические нестационарные нагрузки, в связи с чем у наиболее напряженных деталей всегда существует вероятность возникновения трещин усталости, кото рые, развиваясь с той или иной скоростью в условиях продолжаю щейся эксплуатации, могут еще до исчерпания расчетного ресурса достичь критических размеров, т. е. начала стадии спонтанного распространения, и вызвать хрупкое разрушение.
Данные многочисленных наблюдений за техническим состоянием ответственных деталей машин в пределах запланированных сроков службы свидетельствуют, что примером конструкций, вероятность длительной эксплуатации которых с развивающимися усталостными трещинами достаточно велика, могут служить такие сложные дета ли, как коленчатые валы двигателей внутреннего сгорания, транс миссионные валы и поворотные кулаки автомобилей, элементы обшивки самолетов, сварные соединения несущих систем самоход ных машин, оси железнодорожного подвижного состава и многие другие. Поэтому нами использованы результаты исследования уста лостного разрушения материалов и натурных деталей машин массового производства автотракторной, транспортной, сельскохо зяйственной, авиационной, энергетической и других ведущих от раслей промышленности. Таким образом, в данном случае требова ния к испытательному оборудованию, к его динамическим и метро логическим свойствам определялись вполне конкретной областью экспериментальных исследований, ограниченной изучением законо мерностей развития усталостных трещин в материалах и деталях
широкого класса машин в связи с их конструкцией, технологией изготовления и условиями эксплуатации.
Следует иметь в виду, что закономерности развития трещин ус талости в лабораторных образцах и натурных деталях могут быть существенно различными в связи с влиянием многочисленных факто ров, например абсолютных размеров деталей, остаточных напряже ний в них, специфики геометрии, состояния поверхностных слоев и т. д. Воспроизведение всех свойств деталей в образцах или даже в моделях не может быть достаточно точным, поэтому в накоплении наиболее, достоверной и полной информации о живучести готовой конструкции и особенностях развития в ней усталостных трещин на турные испытания самой конструкции приобретают самостоятельное значение.
Наряду с изучением исходных закономерностей развития трещин усталости возможна также постановка сравнительных испытаний на турных деталей на стадии их проектирования с целью эксперимен тального обоснования оптимальных вариантов, обеспечивающих наи большую живучесть. В этом случае планируются испытания не скольких серий деталей, одинаковых по назначению, но разных по конструкции или технологии изготовления. В качестве критерия оп тимальности принимаются такие характеристики, как продолжитель
ность процесса развития трещины от момента |
ее зарождения до |
достижения критических размеров, скорость |
развития трещины |
с учетом стадийности этого процесса или |
другие, получаемые |
при испытании данные, характеризующие сопротивляемость дета лей начавшемуся разрушению. Результаты таких испытаний ис пользуются для оптимизации конструкций, поэтому исследуемые варианты различаются только исполнением, а условия нагружения
?для всех вариантов остаются одинаковыми. Вместе с тем часто возни кает необходимость в сравнительных испытаниях, цель которых — изучение процесса усталостного разрушения в связи с влиянием эксплуатационных факторов, относящихся не к конструкции или ее изготовлению, а к условиям ее работы. Такими факторами могут быть, например, форма спектра эксплуатационных напряжений, высокочастотные составляющие основного процесса циклического нагружения, кратковременные перегрузки и т. д. В сравнительных испытаниях такого типа объекты исследования остаются одинаковы ми, а сами исследования различаются только условиями нагруже ния. В качестве базы сравнения могут быть использованы те же экспе риментальные данные, что и при сравнительных испытаниях кон структивных вариантов.
Сравнительные испытания натурных деталей предъявляют к ис пытательному оборудованию ряд дополнительных требований, обусловленных разнообразием конструкций этих деталей и диапа
зоном их деформационных характеристик, исключающих полную унификацию динамометрических узлов, зажимных устройств и при способлений для наблюдения за ростом трещин.
Экспериментальные исследования, а также анализ напряжен ности исследуемых конструкций в условиях их эксплуатации поз воляют считать, что испытательное оборудование для изучения кинетики усталостного разрушения в указанном выше аспекте должно обеспечивать возможность доводить до окончательного разру шения разнообразные в конструктивном отношении объекты испы таний (включая натурные детали), моделировать наиболее типич ные режимы эксплуатационного нагружения и регистрировать процесс развития трещин усталости с возможно большей точностью.
В настоящее время наша промышленность не выпускает испы тательные машины, которые наилучшим образом удовлетворяли бы всем перечисленным требованиям, поэтому ниже рассмотрен во прос о перспективности применения для исследования развития трещин усталости программных машин испытательного комплекса, конструкция и общая композиция которого достаточно подробно описаны в работах [21, 61]. В данной работе обращается внимание только на те его свойства, которые дают представление о его возможностях применительно к изучению кинетики усталостного разрушения. Очевидно, основным таким свойством является уни версальность машин комплекса, позволяющая воспроизводить все виды нагрузок (изгиб, кручение, растяжение — сжатие) и с доста точной точностью моделировать эксплуатационные режимы меха нической напряженности при испытании на усталость как лабо раторных образцов, так и натурных деталей различных размеров..
Универсальность комплекса в значительной степени обеспе чивается его общей структурой, предусматривающей компоновку испытательных машин различного назначения из отдельных, взаи мозаменяемых узлов, а также разработанными средствами силовозбуждения и моделирования режима испытаний.
Анализ существующих способов силовозбуждения показывает, что при достигнутом в настоящее время уровне развития средств автоматизации процессов управления каждый из них может быть использован для моделирования режима испытаний в определенном диапазоне усилий и частот. В машинах испытательного комплекса применено кинематическое силовозбуждение при помощи шатуннокривошипного механизма, которое по основным своим характеристи кам и возможностям является вполне приемлемым и для планируемых исследований кинетики усталостного разрушения, так как большин ство конструкций указанных выше отраслей машиностроения работает с частотой не более 100 Гц, а усилия, достаточные для их раз рушения при растяжении — сжатии, обычно не превышают 20 000 кг
Следует, однако, отметить, что, по сравнению с другими способа ми, кинематическое силовозбуждение имеет ряд существенных недо статков, обычно затрудняющих его применение в испытательных ма шинах вообще и в машинах для изучения процессов усталостного разрушения в частности. Одним из таких недостатков является не постоянство амплитуды задаваемой нагрузки, которая в период развития трещины усталости или при испытании полимеров может существенно изменяться в соответствии с изменением жесткости объекта исследований и влиять на скорость развития усталостного разрушения. В конструктивном отношении кривошипные возбуди тели характеризуются громоздкостью механизма регулирования воз мущающих динамических перемещений и значительной нагруженностыо основных деталей в связи с неизбежным участием подшипни кового узла в передаче усилия на образец. Эти особенности кине матического силовозбуждения затрудняют варьирование режима испытаний в соответствии со спектрами эксплуатационных нагрузок и создание надежно работающих систем управления.
Успешное использование машин с кривошипным приводом для программных испытаний на усталость оказалось возможным благодаря теоретической проработке некоторых вопросов его динамики с уче том требований моделирования эксплуатационных режимов нагру жения. В результате этой проработки были получены аналитические зависимости, позволяющие выбирать параметры динамических схем испытательных машин с учетом жесткости образца и обеспечивать оптимальный режим испытаний по основным показателям, т. е. по величине развиваемой нагрузки, по чувствительности ее амплитуды к изменению жесткости образца в период его постепенного разруше ния и по частоте возбуждения. Подшипниковый узел и детали воз будителя колебаний при этом практически полностью освобождаются от воздействия реактивных усилий со стороны деформируемой систе мы, что позволяет реализовать важные для изучения процесса уста лостного разрушения преимущества кинематического привода, например, такие, как возможность варьирования асимметрии цикла нагружения, проведения испытаний в широком диапазоне частот и возбуждения значительных динамических перемещений, свобод ных от частотной зависимости.
Освобождение возбудителя от действия реактивных усилий об легчило аппаратурное управление его исполнительными механиз мами при помощи команд, поступающих по каналам обратной связи от нагружаемой системы, и обеспечило возможность моделирования эксплуатационных режимов нагружения путем автоматического варьирования величины нагрузки и времени ее действия. Програм ма варьирования представляется в виде ступенчатых блоков в ко ординатах напряжение — число циклов, которые формируются
в соответствии со спектрами эксплуатационных нагрузок: Математи ческая запись программ, реализуемых машинами испытательного комплекса, может быть представлена в общем виде:
|
а (/) = |
аст (/) + A (t) sin at, |
|
где |
— статическая составляющая, |
||
|
(Тот (/) = |
(o CT) i , |
(сгсх)2, (сгст) 3, |
А (0 — амплитуда переменной |
составляющей, A (t) = Аи А2> |
||
А$, ... |
|
|
|
Электронное программирующее устройство испытательного комп лекса обеспечивает любую последовательность чередования уровней
напряжений в пределах каждого программного блока. |
Число уров |
ней в блоке устанавливается в зависимости от характера |
статистиче |
ского распределения эксплуатационных нагрузок и для более точного их моделирования может достигать двенадцати. Емкость блоков, выраженная в числе циклов, варьируется в широких пределах и ус танавливается с таким расчетом, чтобы достигалось необходимое осреднение влияния выбранной последовательности чередования уровней напряжений.
В машинах комплекса предусмотрена дублированная система силоизмерения — оптическая и электрическая. Электрические си лоизмерительные устройства (датчики) и нагружающие устройства посредством электронной аппаратуры объединены в замкнутую систему регулирования. Разработанные средства амплитудной ста билизации заданного режима нагружения позволяют проводить на машинах испытательного комплекса исследования закономер ностей развития трещин усталости при программировании как нагруженности образца (мягкое нагружение), так и его деформаций (жесткое нагружение). В первом случае электрические сигналы, управляющие работой возбудителя, инициируются датчиком дина мометра, во втором случае — датчиком активного захвата. Оба эти случая являются предельными случаями, которым соответству ет наибольшая и наименьшая скорости развития усталостных трещин. Вместе с тем в практике достаточно часто встречаются промежуточ ные случаи, когда в процессе развития повреждения конструкции (например, в статически неопределимых системах) происходит пере распределение и нагрузок и деформаций, в связи с чем условия роста усталостных трещин не соответствуют указанным выше предельным случаям.
Чтобы оценить возможность использования машин испытатель ного комплекса для исследования роли промежуточных режимов нагружения в развитии усталостного разрушения, следует учесть, что в унифицированную динамическую схему каждой такой машины
входят последовательно соединенные образец и сменный динамометр. Если их жесткости обозначить соответственно через сг и с2, то общая
жесткость нагружаемой системы будет с = С\-е с2.
Очевидно, увеличивая или уменьшая жесткость динамометра с2при заданной амплитуде возмущающих колебаний (или при задан
ной программе ееизменения) и варьируя |
таким образом |
соотно |
||||||||
шение жесткостей элементов в системе |
машина — образец, |
можно |
||||||||
приближать нагружение образца соответственно к жесткому |
или |
|||||||||
мягкому режиму (рис. 1). Необходимо, |
однако, иметь в виду, что |
|||||||||
|
для возбуждения в образце на |
|||||||||
|
пряжений |
заданной |
|
величины |
||||||
|
изменение жесткости динамомет |
|||||||||
|
ра должно быть компенсировано |
|||||||||
|
соответствующим |
|
изменен нем |
|||||||
|
амплитуды возмущающих |
коле |
||||||||
|
баний /. Изменяется |
при этом и |
||||||||
|
амплитуда |
колебаний s массы т |
||||||||
|
пассивного захвата, |
которая |
мо |
|||||||
|
жет быть вычислена по формуле |
|||||||||
|
s = |
|
1С\ |
|
|
|
|
|
|
|
|
—j— |
1---- о »где со — часто- |
||||||||
|
|
С1+ |
сг |
— пш* |
[107]. |
|
|
|
||
|
та возбуждения |
|
|
и s |
||||||
|
Возрастание |
амплитуд I |
||||||||
Рис. 1. Зависимость амплитуды возму |
при |
уменьшении |
жесткости |
ди |
||||||
намометра сг иллюстрируют кри |
||||||||||
щающих колебаний и перемещений пас |
вые на |
рис. 1, построенные |
без |
|||||||
сивного захвата от жесткости динамо |
||||||||||
метра. |
учета динамического |
усиления, |
||||||||
|
которое |
при |
обычном соотноше |
|||||||
нии параметров нагружаемой системы невелико. |
Кривые построены |
в относительных координатах, где через /0 и s0 обозначены амплитуды соответственно возмущающих колебаний и колебаний массы т при ча> то реализуемом в испытательных машинах соотношении жесткостей с2/сг = 10. Амплитуды возмущающих колебаний I вычислялись при соблюдении постоянства напряжений в образце для всех исследован ных значений жесткости динамометра. Сопоставление кривых сви детельствует о том, что существует обширная область значений с21съ в пределах которой уменьшение жесткости динамометра не вы зывает существенного увеличения амплитуды возмущающих коле баний. Значительно быстрее возрастает амплитуда колебаний массы т. Эта масса сосредоточена между образцом и динамометром, поэто му влияние ее сил инерции на точность силоизмерения должно исклю чаться динамической тарировкой машины или вычислением соот ветствующей динамической поправки [107].
Таким образом, следует считать, что машины испытательного комплекса могут быть использованы для исследования усталостного разрушения, развивающегося не только в условиях предельных, но и промежуточных режимов нагружения.
В практике достаточно часто встречаются случаи, когда моделью эксплуатационной нестационарной нагруженности конструкций может служить бигармонический колебательный процесс (например, в элементах корпусов кораблей). Для исследования закономерностей развития трещин усталости в этих случаях также могут использо ваться машины испытательного комплекса, структура которых допускает одновременно нагружение объекта испытаний от двух унифицированных возбудителей — низкой и высокой частот. Для независимой регулировки в широких пределах и фиксации за данного соотношения всех параметров каждой гармонической со ставляющей (фазы, амплитуды и частоты) служит редуктор, соеди няющий кинематические цепи обоих возбудителей. Реализуемая
при этом программа |
испытаний записывается в следующем виде: |
|||
|
а (*) = А (/) sin Ы + В (f) sin kat> |
|||
где k = 1, 2, 3, |
...» |
a амплитуды низкочастотной и высокочастот |
||
ной составляющих |
могут |
принимать |
соответственно значения |
|
А (£) = A it Л2, J43, |
и |
В (/) = Bit |
> Я8. |
|
Выше были |
рассмотрены некоторые вопросы использования ма |
шин испытательного комплекса применительно к задачам моделиро вания механической напряженности конструкций при изучении зако номерностей развития трещин усталости. Однако значительный научный и инженерный интерес представляют аналогичные исследова ния при наложении влияния и других, обычно сопутствующих меха нической напряженности, эксплуатационных факторов, например температур, вакуума, агрессивных сред и т. д. Если изучению влия ния этих факторов на сопротивление усталости уделяется сравни тельно много внимания, о чем свидетельствуют многочисленные публикации, то их влияние на скорость развития усталостных тре щин и на характер протекания процесса разрушения изучено меньше.
Оценивая возможности машин испытательного комплекса при воспроизведении сопутствующих эксплуатационных факторов, сле дует иметь в виду, что для проведения таких исследований необхо димы специальные устройства в виде печей для нагревания образ цов или натурных деталей, камер для формирования и дозирования рабочих сред, приборов криогенной техники и т. д. Такими уст ройствами испытательные машины в обычном исполнении не оснаща ются, однако место для их установки общей композицией преду сматривается. Некоторый опыт таких исследований на машинах комплекса, уже накоплен, например при высокотемпературных