
книги / Плавка цветных металлов
..pdf2)строгое соблюдение правил пожарной безопасности;
3)необходимость тщательного рафинирования расплава для удаления неметаллических включений;
4)применение особых формовочных и стержневых смесей со специальными добавками и присадками;
5)литье в защитной атмосфере сернистого или других газов;
6)необходимость антикоррозионной обработки отливок.
4.2. Технологические особенности плавки магниевых сплавов
Магниевые сплавы плавят в тигельных топливных печах, отражательных печах, футерованных магнезитом, и индукционных печах средней и промышленной частоты. При плавке магниевых сплавов важное значение приобретают вопросы пожаро- и взрывобезопасности. Особенно недопустим контакт расплава с водой. В связи с этим для плавки магниевых сплавов разработаны специальные индукционные печи с принудительным воздушным охлаждением индуктора.
В обычных индукционных печах металл может интенсивно перемешиваться под действием электродинамических сил. Такое перемешивание приводит к нарушению защитного флюсового покрова, что недопустимо при плавке магниевых сплавов. Специальные индукционные печи для плавки магниевых сплавов (рис. 18) состоят из тигля с крышкой, теплоизоляции, индуктора и магнитопровода.
Для плавки магниевых сплавов применяются литые и сварные стальные тигли (рис. 19). Железо существенно снижает коррозионную стойкость сплавов, однако при значениях температуры до 750 °С оно растворяется медленно, поэтому тигли и плавильный инструмент можно изготовлять из малоуглеродистой стали (чем больше углерода в стали, тем больше растворимость железа в сплаве). Недопустимо применение для этих целей нержавеющих и жаропрочных сталей, содержащих никель, который еще более резко снижает коррозионную стойкость.
81
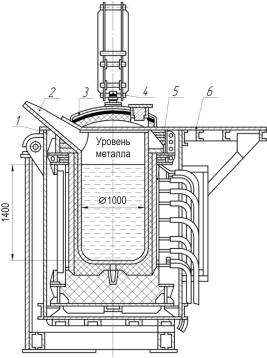
Рис. 18. Индукционная тигельная печь для плавки магниевых сплавов ИГТ-1,6: 1 – рама; 2 – стальной тигель; 3 – крышка; 4 – механизм подъема крышки; 5 – индуктор; 6 – рабочая площадка
Сварные тигли имеют емкость до 300 кг. Их изготовляют из листовой малоуглеродистой стали толщиной от 8 до 15 мм. Они бывают простые (см. рис. 19, б) и с дополнительной перегородкой для удержания шлака (см. рис. 19, в). Тигли имеют конусную форму. Днище тигля штампуется такой формы, чтобы сварной кольцевой шов работал на растяжение. Толщина днища больше, чем стенок, и доходит до 25 мм.
Литые тигли (см. рис. 19, а) получают из сталей 15Л или 20Л. Они имеют значительно больший срок службы и более безопасны в работе, чем сварные. Для печей большой емкости применяются толстостенные (20–25 мм) тигли (см. рис. 19, г).
82

а |
б |
в |
г
Рис. 19. Тигли для плавки магниевых сплавов: а – стальной литой тигель емкостью 250–300 кг; б и в – сварные тигли из листовой стали; г – стальной
тигель большой емкости
В печах с толстостенным литым тиглем теплота индуктируется в тигель, а затем передается к шихте. В этом случае металл экранируется тиглем от магнитного поля и находится в спокойном со-
83
стоянии. В печах с тонкостенными сварными тиглями часть магнитного поля проходит внутрь тигля, особенно при значениях температуры выше магнитного превращения, и металл приходит в движение. При рафинировании флюсами это можно рассматривать как положительное явление: отпадает необходимость ручного перемешивания. Однако последующее выстаивание расплава и разливку сплава надо проводить при выключенной печи.
Для защиты от насыщения железом тигли и плавильный инструмент покрывают краской следующего состава (мас. %): борная кислота – 3,5; графит – 7,0; мел – 25,5; вода – ост.
Из-за высокой химической активности расплавленного магния необходимо свести к минимуму операции с его переливом из тигля
втигель. В связи с этим разработано несколько вариантов плавки:
встационарных тиглях с забором металла разливочными ковшами;
ввыемных тиглях с заливкой форм из тигля и комбинированным способом. Литые стальные тигли используют как стационарные,
асварные тигли более пригодны для второго варианта плавки – в выемных тиглях.
Вкачестве шихтовых материалов применяются чушковые первичные металлы (магний, алюминий и цинк), первичные магниевые сплавы в чушках, лигатуры, соли и возврат собственного производства.
Марганец вводят лигатурой Al–Мn или при помощи соли МnСl2. Марганец восстанавливается магнием и переходит в сплав,
аобразовавшийся хлористый магний во флюс. При использовании соли не требуется излишний перегрев сплава. Количество соли берут таким, чтобы содержание марганца в ней в 3 раза превышало содержание марганца в сплаве.
Цирконий вводят лигатурами Al–Zr (3–5 % Zr) или Mg–Zr
(до 15 % Zr), фторцирконатом калия (K2ZrF6) или шлак-лигатурой (40 % K2ZrF6, 40 % карналлита и 20 % магния). Расплав перед введением циркония перегревают до 850–900 °С. Восстановление циркония происходит по реакции
K2ZrF6 + 2Mg = 2KF + 2MgF2 + Zr.
84
Из-за неполноты протекания реакции в расплав переходит треть циркония, содержащегося в соли. Ориентировочно можно считать, что для введения 1 % Zr в сплав нужно израсходовать 3 % K2ZrF6. Для более полного восстановления циркония из фторцирконата калия предварительно готовят шлак-лигатуру. В расплавленный криолит порциями вводят фторцирконат калия при температуре 720–750 °С. В расплавленные соли приливают расплавленный магний.
Лантан, неодим и иттрий вводят в чистом виде или лигатурами с магнием, а бериллий лигатурами Al–Bе, Аl–Мg–Bе или фторбериллатом натрия (Na2BeF4). Лучшее усвоение бериллия наблюдается при введении его смесью солей (50 % карналлита и 50 % фторбериллата натрия) во время рафинирования при 720–750 °С.
Все шихтовые материалы должны быть очищены от продуктов коррозии, масла, эмульсии и т.п. Возвраты предварительно разделяют по сортам: 1-й сорт – бракованные отливки, крупные и мелкие чистые выпоры, чистые литники и коллекторы; 2-й сорт – мелкие отходы, сплески, стояки; 3-й сорт – стружка, опилки и металл, извлеченный из сплесков. Возврат 1-го сорта используется в шихте без переплава. Отходы 2-го и 3-го сортов вводятся в шихту в переплавленном виде.
Шихтовые первичные материалы загружают в следующей последовательности: магний, лигатуры и возврат, алюминий, затем цинк и кадмий. При использовании чушковых сплавов и переплавов сначала расплавляют их, а затем проводят подшихтовку чистыми металлами в приведенной последовательности.
При плавке магниевых сплавов недопустим контакт металла, флюсов, плавильного инструмента и материала форм с влагой. Это может вызвать воспламенение металла, выбросы его из печи или формы и ухудшение качества отливок. Весь плавильный инструмент рекомендуется хранить в специальной тигельной печи в расплавленном флюсе [1].
Плавку ведут под защитными флюсами или защитными атмосферами.
85
4.2.1. Защитные флюсы для магниевых сплавов
Для магниевых сплавов, как и для других цветных сплавов, применяют флюсы, состоящие из хлористых и фтористых солей, щелочных и щелочно-земельных металлов [4]. Плотный слой флюсов надежно защищает сплав от окисления. Общие требования к флюсам сформулированы ранее (см. подразд. 1.3).
Основные затруднения при подборе состава флюсов для плавки магниевых сплавов связаны с малой плотностью расплава и невысокой температурой плавления. Для рабочих значений температуры 680–720 °С флюсы должны иметь температуру плавления 620–650 °С, не более. Все соли, которые входят в состав покровнорафинирующих флюсов для цветных сплавов (см. табл. 8), имеют плотность, равную или большую, чем расплавленный магний или магниевые сплавы. В расплавленном состоянии плотность солей будет существенно ниже, но все равно только смеси KCl·LiCl и (МgСl2 KСl)LiCl, содержащие более 50 % LiCl, оказываются легче магниевого расплава. Они имеют малую вязкость и малое поверхностное натяжение, что затрудняет отделение флюса от расплава. Кроме того, эти флюсы гигроскопичны, дороги и химически активны к футеровке, поэтому не нашли применения в промышленности (флюсы, состоящие из хлористого и фтористого лития, используют при плавке магниево-литиевых сплавов).
Основу большинства флюсов составляет карналлит (МgСl2 KСl). Плотность карналлита несколько больше, чем магниевого расплава. Для лучшего отделения флюсов от сплава в них вводят утяжелители (BaCl2, CaCl2) и сгустители (MgO, CaF2). Такие флюсы, хотя и более тяжелые, чем расплав, удерживаются на поверхности за счет сил поверхностного натяжения и постепенно стекают на дно по стенкам тигля. Таким образом, плавка магниевых сплавов протекает в своеобразном флюсовом мешке (рис. 20). Отдельные частицы флюса, попавшие в металл, опускаются на дно и увлекают за собой неметаллические частицы. Ввиду этого в дополнение к общим требованиям, предъявляемым к флюсам, флюсы для магниевых сплавов должны смачивать стенки тигля и под печи.
86
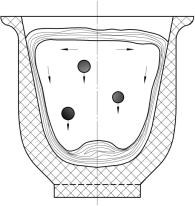
Рис. 20. Схема плавки магниевых сплавов под флюсами
При плавке сплавов, содержащих РЗМ (Ce, Y, Nd, La, а также Ca), могут протекать обменные реакции, которые приведут к потере этих ценных металлов:
3MgCl2 + 2Cе = 2CeCl3 + 3Mg; 3MgCl2 + 2Y = 2YCl3 + 3Mg; MgCl2 + Ca = CaCl2 + Mg.
Для таких сплавов необходимо применять бесхлоридные флюсы, состоящие из более дорогих фтористых солей. Если таких флюсов нет, то РЗМ для уменьшения потери необходимо вводить за 2–3 мин до разливки сплава.
Состав некоторых флюсов, применяемых при плавке магниевых сплавов, приведен в табл. 14.
Флюсы № 2, ВИ2 и ВИ3 на основе карналлита были первыми, рекомендованными для плавки магниевых сплавов. Они содержат некоторое количество нерастворимого осадка (н.о.) и влаги. Флюс № 2 представляет собой переплавленный карналлит с добавкой BaCl2 для уменьшения вязкости. ВИ2 и ВИ3 получены на базе этого флюса.
87
|
|
Таблица 14 |
|
Состав некоторых флюсов для плавки магниевых сплавов |
|||
|
|
|
|
Марка |
Состав, мас. % |
Назначение |
|
флюса |
|||
|
|
||
№ 2 |
≥40 MgCl2; 34–40 KCl; ≤8 NaCl + CaCl2; |
Для промывки пла- |
|
|
5–8 BCl2; ≤1,5MgO; ≤1,5 н.о.; ≤ 2Н2О |
вильного инструмента |
|
ВИ2 |
38–46 MgCl2; 32–40 KCl; 5–8 BCl2; |
Для плавки в стацио- |
|
|
≤8 NaCl + CaCl2; ≤1,5MgO; ≤1,5 н.о.; ≤3Н2О |
нарных тиглях |
|
|
34–40 MgCl2; 25–36 KCl; 15–20 СаF2; |
Универсальный флюс |
|
ВИ3 |
≤8 NaCl + CaCl2; 7–10 MgO; ≤1,5 н.о.; |
для плавки в выемных |
|
|
≤3Н2О |
тиглях |
|
ФЛ5 |
25–42 MgCl2; 20–36 KCl; 4–8 BCl2; |
Единый флюс |
|
|
< СаF23–11MgF2; 3–14 AlF3; 1,8B2O3 |
|
|
ФЛ10 |
20–35 MgCl2; 16–29 KCl; 8–12 BCl2; |
Универсальный флюс |
|
|
14–23 СаF2; 14–23 MgF2; 0,5–8 B2O3 |
|
|
ФЛ1 |
13CaF2; 32MgF2; 40AlF3; 15B2O |
Бесхлоридный флюс |
|
ВАМИ1 |
3,5CaF2; 23,5AlF3; 40B2O3; 33Na3AlF6 |
|
|
ВАМИ5 |
17,5CaF2; 17,5MgF2; 15AlF3; 50B2O3 |
|
Флюс ВИ2 для плавки в стационарных тиглях обладает достаточно высокой вязкостью для отделения флюса во время зачерпывания и заливки металла и образует эластичный покров без образования корки во время выстаивания.
Флюс ВИ3 для плавки в выемных тиглях содержит больше сгустителей (CaF2) для образования плотной корки, которая сдвигается во время разливки от носка тигля.
Другие флюсы, приведенные в табл. 14, представляют собой более современные композиции на основе тех же хлоридов и фторидов, а также бесхлоридые флюсы, предназначенные для плавки магниевых сплавов с РЗМ.
Технология плавки под защитными флюсами имеет существенные недостатки. Частицы хлористых флюсов при попадании в отливку быстро становятся очагами коррозии. Некоторые соли могут вступать в химические реакции с магнием, увеличивать потери сплава, менять его состав и загрязнять неметаллическими включениями. За состоянием поверхности флюса необходим постоянный
88
контроль, чтобы не допустить нарушения сплошности покрова. Во флюсе могут запутываться корольки металла, что увеличивает потери сплава. Испарения хлористых солей приводят к коррозии всех металлических конструкций цеха.
4.2.2. Защитные атмосферы для магниевых сплавов
На ряде отечественных и зарубежных заводов успешно внедрена технология бесфлюсовой плавки магниевых сплавов с использованием защитных атмосфер из аргона, азота, углекислого и сернистого газов в герметичных закрытых печах. Из них только аргон не реагирует с магнием. Углекислый и сернистый газы (CO2, SO2) являются окислителями, но менее активными, чем кислород. Так, например, при использовании SO2 на поверхности сплава протекают следующие реакции:
3Mg + SO2 → 2MgO + MgS′;
MgS′ + SO2 → MgSO4 + S2;
MgSO4 + MgO ↔ SO2 + O;
Mg + O ↔ MgO;
4Мg + 2SO2 ↔ 4MgO + S2.
Вторая и третья реакции протекают не полностью. В результате на поверхности спокойной ванны образуется плотная пленка, содержащая MgS′ и MgSO4 и защищающая сплав от интенсивного горения. Однако такая атмосфера не предотвращает образование шлаков на поверхности ванны. При их удалении происходят вспышки магния. Кроме того, применение требует надежной вытяжной вентиляции.
Двуокись углерода CO2 дает неплохие результаты, если ее
концентрация в атмосфере превышает 90 %.
Азот технической чистоты частично взаимодействует с магнием и примесями в сплаве. Происходит засорениерасплава нитридами.
Аргон обеспечивает более полную защиту, чем другие газы, но требуется герметизация печи, чтобы уменьшить его потери, к тому же он не исключает испарения магния.
89
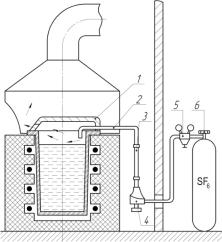
Удовлетворительные результаты принесло введение малых добавок SO2, BF3 и SF6 к защитным газам или непосредственно в воздух. Ввод до 0,1 % этих веществ в атмосферу CO2 повышает выход годного до 96–99 %. Аналогичные добавки к аргону уменьшают испарение магния. Особо эффективно применение шестифтористой серы (элегаза). Она в 5 раз тяжелее воздуха, поэтому равномерно распределяется над ванной и создает надежный защитный слой, содержащий фториды магния. Расход SF6 составляет 1 л/ч, что соответствует концентрации в воздухе 0,1 %. Элегаз – это нетоксичный газ без запаха и цвета. Молекулярное строение близко к инертным газам, чем и объясняются высокие защитные свойства. На поверхности магниевого расплава элегаз вступает с ним в химическое взаимодействие по реакции
5Mg + SF6 = Mg2S + 3MgF2,
продукты которой образуют плотную пленку, предохраняющую жидкий металл от окисления.
Схема подачи элегаза к печи СМТ-0,1 приведена на рис. 21. Печь должна иметь герметичную крышку.
Рис. 21. Схема подачи элегаза: 1 – крышка тигля; 2 – подводящая трубка; 3 – ротаметр; 4 – игольчатый вентиль; 5 – редуктор; 6 – баллон
90