
книги / Плавка цветных металлов
..pdf
ниевых сплавов обычно выбирают более дешевый азот. При значениях температуры до 800 °С азот не вступает во взаимодействие с расплавленным алюминием, т.е. является нейтральным газом по отношению к алюминию. При более высоких значениях температуры образуются нитриды алюминия.
Механизм рафинирования продувкой инертными или нейтральными газами, в частности азотом, приведен на рис. 13. Газ можно подавать в расплав при помощи керамических (или футерованных металлических) трубок с пористыми наконечниками (см. рис. 13, а) в плавильный тигель или разливочный ковш, а также через пористые керамические вставки, смонтированные в дно ковша (см. рис. 13, б). Трубку с газом необходимо перемещать по всему объему расплава. Газ поступает из баллона через редуктор. Давление газа увеличивают постепенно до появления легкого бурления над расплавом. В систему подачи газа должен быть встроен осушитель, наполненный гранулами силикагеля.
а |
б |
Рис. 13. Способы продувки расплава азотом через трубку с пористым наконечником (а) и через пористую вставку (б): 1 – тигель (ковш); 2 – трубка; 3 – пористая вставка; 4 – кожух для подачи газа
На рис. 14 показано распределение парциального давления в поднимающемся пузырьке азота. Поскольку парциальное давление водорода во вновь образованном пузырьке равно нулю, начинается диффузия растворенного в расплаве водорода в этот пузырек, несмотря на то, что давление азота в нем больше атмосферного (иначе
61
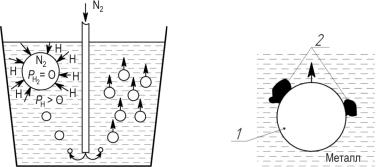
он не будет всплывать). Растворенный газ будет переходить из расплава в пузырек до тех пор, пока не наступит равновесие между газовой фазой и расплавом – раствором. Чем больше суммарная поверхность пузырьков инертного газа (меньше размер пузырьков), тем выше скорость дегазации. Этим объясняется использование при продувке пористых материалов с диаметромпор не более 0,1–0,5 мм [12].
Всплывающие газовые пузырьки всегда оказывают флотирующий эффект по отношению к неметаллическим включениям, которые плохо смачиваются расплавом (являются гидрофобными телами). Пузырьки «прилипают» к поверхности включений. Этот процесс энергетически выгоден. В результате в расплаве образуются целые агрегаты из пузырьков газа и неметаллических включений (рис. 15). В агрегате может быть один пузырек и одна или несколько частиц, а может быть несколько пузырьков и одна или несколько частиц. Как только суммарная плотность такого агрегата станет меньше плотности расплава, он поднимется на поверхность и перейдет в шлак.
Рис. |
14. Распределение |
Рис. 15. Агрегаты неметаллических |
|
парциального |
давления |
включений и газовых пузырьков: |
|
газов |
в |
всплывающем |
1 – пузырек газа; 2 – неметаллические |
|
пузырьке азота |
включения |
Высокие результаты достигаются при продувке активным хлором. Пузырьки хлора, введенного в расплав, в первую очередь взаимодействуют с алюминием по реакции
62
2Al + 3Cl2 = 2AlCl3.
Хлористый алюминий (температура кипения 180 °С) мгновенно превращается в пар и образует дополнительные газовые пузырьки. Часть хлора вступает в реакцию с растворенным водородом:
Cl2 + 2Н = 2НCl.
Хлористый водород также находится в парообразном состоянии. Пузырьки AlCl3 и НCl будут всплывать на поверхность. Поскольку парциальное давление водорода в них в начальный момент равно нулю, то водород, растворенный в металле, вследствие разности значений парциального давления будет диффундировать в пузырьки рафинирующих газов. Так же, как и при использовании инертного или нейтрального газа, этот процесс будет продолжаться до тех пор, пока не сравняются значения парциального давления водорода в расплаве и в газовом пузырьке.
Если на пути газовых пузырьков встретятся твердые частицы, смачиваемые газом, то они также будут всплывать на поверхность расплава.
Расход хлора 0,3–0,5 м3 на тонну сплава, длительность продувки при 710–730 °С может составлять 10–12 мин. Давление хлора поддерживают на уровне 0,11–0,12 МПа, при котором наблюдается легкое бурление на поверхности расплава. Обработку хлором проводят в герметичных камерах или в ковшах с крышкой, соединенной с вентиляционной системой.
Хлор – токсичный газ, поэтому необходимо тщательно соблюдать меры по охране труда. По этой причине продувка хлором в настоящее время практически не применяется на производстве.
Продувку азотом или аргоном ведут при 720–730 °С в течение 5–20 мин. Расход этих газов составляет 0,5–1,0 м3 на тонну сплава. Эффективность метода возрастает, если продувку вести через пористые керамические вставки. Чем меньше размеры пузырьков продуваемого газа и равномернее распределение по объему расплава, тем чище расплав.
Продувку расплава газами целесообразнее проводить при плавке в тигельных печах. В отражательных печах глубина ванны мала и пузырьки всплывают очень быстро.
63
Обработка хлористыми слоями сопровождается протеканием обменных реакций с расплавом. Применяют хлористые цинк и марганец (0,05–0,2 % при температуре 700–730 °С), гексахлорэтан С2Cl6 (0,3–0,7 % при температуре 740–750 °С), а также TiCl4 и другие хлориды. При протекании реакций
3TiCl4 + 4Al = 4AlCl3 + 3Ti; 3ZnCl2 + 2Al = 2AlCl3 + 3Zn; 3MnCl2 + 2Al = 2AlCl3 + 3Mn
образуются газообразные продукты реакции (AlCl3), которые оказывают рафинирующее действие, как при продувке газами.
Хлористые неорганические соли обладают высокой гигроскопичностью. Для удаления влаги соли подвергают сушке (МnС12) или переплавляют (ZnСl2) и вводят в расплав при помощи колокольчика в несколько приемов. После обработки расплав выстаивают 10–15 мин. Подготовленные соли после переплава или сушки необходимо хранить в термостате при 120–150 °С. Металлы, восстановленные из солей, остаются в расплаве. Некоторые из них полезны и могут играть роль модификаторов, но для ряда сплавов могут оказаться вредными примесями.
Органические хлориды, в первую очередь гексахлорэтан, отличаются пониженной гигроскопичностью, недефицитны и обладают хорошей дегазирующей способностью. Гексахлорэтан С2Cl6 (бесцветное кристаллическое вещество с температурой возгонки 187 °С и плотностью 2,1 г/см3) постепенно вытесняет другие соли. При взаимодействии с расплавленным алюминием образуется два газообразных продукта:
3C2Cl6 + 2Al = 3C2Cl4 + 2AlCl3.
Тетрахлорэтилен (C2Cl4) вскипает при 121 °С и вместе с AlCl3 оказывает рафинирующее действие. Если в сплаве содержится магний, то рафинирующее действие солейснижается из-запротеканияреакции
3Mg + 2AlCl3 = 2Al + 3MgCl2
и образования жидкого хлористого магния.
64
Внастоящее время на основе гексахлорэтана производится препарат «Дегазер» в виде таблеток в вакуумной упаковке. Для увеличения плотности в препарат добавлен хлористый барий (10 %), поэтому таблетки опускаются на дно, увеличивая объем обрабатываемого расплава.
Общим недостатком всех адсорбционных методов рафинирования является то, что они не могут охватить весь объем расплава и очищают только теучасткирасплава, через которыепроходит адсорбент.
Обработка рафинирующими флюсами является более универ-
сальным и эффективным методом рафинирования алюминиевых сплавов, чем продувка газами и обработка солями.
Воснову этого метода рафинирования положено физикохимическое взаимодействие между флюсом и примесями, а именно способность флюса адсорбировать и растворять неметаллические примеси или химически связывать их в прочные соединения, которые легче удаляются из расплава в виде шлака. Главную роль играют поверхностные явления. Включения переходят во флюс под действием межфазных сил. Такими свойствами обладают флюсы на основе хлористых и фтористых солей с содержанием не менее 10 %
фторидов (NaF, CaF2, Na3AlF6, Na2SiF6 и др.). Состав основных рафинирующих флюсов приведен в табл. 11.
Для алюминиевых сплавов применяют преимущественно верхнее флюсование и флюсование по всему объему. Предварительно переплавленные и высушенные флюсы в количестве 0,5–1,0 % от массы металла засыпают на поверхность и энергично замешивают в расплав при температуре 700–750 °С в течение 3–5 мин. Затем шлак снимают и дают сплаву отстояться 10–15 мин [8]. После повторного снятия шлака металл готов к разливке. Целесообразнее вводить флюсы при помощи «колокольчика», который перемещают по всему объему тигля до полного расплавления флюсов и прекращения взаимодействия с расплавом (прекращения бурления металла).
Флюс № 1 используют для рафинирования деформируемых сплавов, а флюсы № 2 и 13 для рафинирования литейных силуминов. Для сплавов системы Al–Mg применяют рафинирующие флюсы № 3–9 на основе карналлита.
65
|
|
Таблица 11 |
|
|
Состав рафинирующих и универсальных флюсов |
||
|
для плавки алюминиевых сплавов |
||
|
|
|
|
Номер |
Содержание компонентов, % |
Область применения |
|
флюса |
|||
|
|
||
1 |
47KCl; 30NaCl; 23Na3AlF6 |
Рафинирующие флюсы для |
|
2 |
35KCl; 50NaCl; 15Na2SiF6 |
всех сплавов без магния |
|
3 |
60MgCl2KCl; 40KF |
|
|
4 |
80MgCl2·KCl; 12–15 KCl; 5–8 BaCl2 |
|
|
5 |
80MgCl2KCl; 20CaF2 |
Рафинирующие флюсы для |
|
6 |
85MgCl2KCl; 15MgF2 |
алюминиево-магниевых |
|
7 |
90MgCl2KCl; 10K3AlF6 |
сплавов |
|
8 |
90MgCl2KCl; 10KF |
|
|
9 |
90MgCl2KCl; 10AlF3 |
|
|
10 |
11,5KCl; 56,5NaCl; 25NaF; 7Na3AlF6 |
Универсальные (рафини- |
|
11 |
10KCl; 50NaCl; 10Na3AlF6; 30NaF |
рующие и модифицирую- |
|
12 |
45NaCl; 15Na3AlF6; 40NaF |
щие) флюсы для силуми- |
|
13 |
40KCl; 35NaCl; 10NaF |
нов |
Для ускорения процесса рафинирования и повышения его эффективности флюсы лучше использовать в жидком виде. С этой целью их расплавляют в отдельной флюсовой печи.
Вакуумирование является одним из наиболее надежных способов дегазации металлических расплавов. Ковш с расплавом помещают в вакуумную камеру и выдерживают при остаточном давлении 13,3–133 Па в течение 10–15 мин. Схема процесса вакуумирования представлена на рис. 16. В вакуумной камере 1 установлена печь 3 с газовым обогревом, в которую устанавливается тигель 2 с расплавленным металлом. Расплав перегревают на 40–50 °С, убирают газовую горелку 5 и закрывают камеру крышкой. Герметичное прилегание крышки обеспечено прокладкой из вакуумной резины 4. При помощи ресивера 8 в камере быстро (1–2 мин) создается необходимое разрежение. Из ресивера воздух предварительно откачивают вакуумным насосом 6. Остаточное давление в ресивере, а потом и в камере контролируют при помощи вакуумметров 7.
66

Рис. 16. Схема установки для вакуумирования алюминиевых расплавов
Фильтрация расплавов в настоящее время стала неотъемлемой частью технологического процесса плавки и разливки алюминиевых сплавов на всех предприятиях. Применяют сетчатые, зернистые и пористые керамические фильтры.
Сетчатые фильтры изготовляют из стеклоткани или металлосетки с размером ячеек от 0,5×0,5 до 1,5×1,5 мм. Фильтры отделяют те включения, размер которых больше ячейки сетки. Их применение позволяет в 1,5–2 раза снизить содержание крупных включений и пленок. Но они не оказывают влияния на содержание мелкодисперсных включений и водорода. Обычно их устанавливают по разъему формы под стояком.
Значительно эффективнее зернистые фильтры. Их получают из крошки шамота, магнезита, алунда, кремнезема, сплавов хлористых и фтористых солей (рафинирующих флюсов) и других материалов. Полнота удаления взвешенных неметаллических включений зависит от природы материала фильтра, диаметра и длины межзеренных каналов. Очистка обусловлена механическими и адгезионными процессами. Фильтры из крошки переплавленных флюсов называют активными. За счет адгезионных процессов они позволяют отделить до
67
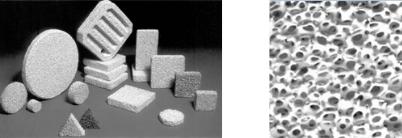
40 % тонкодисперсных взвесей и на 10–20 % снизить содержание водорода в сплавах, прошедших рафинирование флюсами.
Зернистые фильтры, как и сетчатые, устанавливают на пути заливаемого в форму металла. Средний размер зерен фильтрующего материала от 4 до 15 мм в поперечнике, а высота слоя 100–150 мм. Располагают зернистые фильтры в раздаточном тигле, в стояке или в литниковой чаше. Заливку ведут таким образом, чтобы фильтр был закрыт слоем расплава 10–15 мм. Зернистые фильтры рекомендуется нагревать до 700–720 °С. Это позволяет удалить адсорбированную влагу и предотвратить замораживание металла в тонких каналах. Существенное влияние на полноту отделения включений и плен оказывает скорость течения расплава по межзеренным каналам фильтров. При большой скорости течения уменьшается возможность осаждения включений и увеличивается вероятность смыва уже осевших частиц [12].
Насыпные зернистые фильтры не всегда обеспечивают стабильность процесса очистки расплава. При случайном расположении между крупными зернами могут образоваться каналы большого сечения. Этих недостатков лишены современные объемные пористые керамические фильтры любой формы (рис. 17) с любым заданным сечением каналов. Их изготовляют из Al2O3, SiO2, ZrO2 и других материалов. Фильтры могут поставляться в виде крупных блоков или фасонных изделий любой формы по требованию заказчика.
а |
б |
Рис. 17. Пенокерамические фильтры для фильтрации металлических расплавов: а – форма фильтров; б – структура фильтра [7]
68
Пенокерамические фильтры можно установить в любой части литниковой системы.
Фильтры из муллитокорундовой керамики производства Минского института порошковой металлургии имеют следующие харак-
теристики: |
|
открытая пористость........................................................ |
75–85 %; |
предел прочности при изгибе......................................... |
1–5 МПа; |
максимальная рабочая температура................................ |
1550 °C; |
средний размер пор............................................................ |
1–5 мм; |
вязкостный коэффициент проницаемости............... |
10–9–10–8 м2; |
максимальный линейный размер...................................... |
180 мм; |
толщина........................................................................... |
10–25 мм. |
Эффективность их использования рассмотрим на примере фильтрации эвтектического поршневого сплаваАК12ММгН(табл. 12).
|
|
Таблица 12 |
Характеристики образцов сплава АК12ММгН |
|
|
без очистки и с очисткой |
|
|
|
|
|
Характеристики сплава |
Без очистки |
С очисткой |
Предел прочности при растяжении, МПа |
140–145 |
165–170 |
Содержание неметаллических включений, |
0,20–0,25 |
0,05–0,06 |
мм2/см2 |
||
Балл пористости |
3 |
1 |
3.2.5. Модифицирование алюминиевых сплавов
Из всех групп алюминиевых литейных сплавов модифицирования требуют в первую очередь силумины. Доэвтектические и эвтектические сплавы (АК12, АК9, АК7, АК12ММгН и др.) для измельчения выделений эвтектического кремния модифицируют натрием, стронцием, иттрием, сурьмой. Для заэвтектических силуминов (≥13 % Si) применяют фосфор. Большинство деформируемых сплавов и литейные сплавы системы Al–Mg модифицируют тугоплавкими элементами (Тi, B, Zr, Y и др.). Состав некоторых модификаторов и режимы обработки приведены в табл. 13.
69
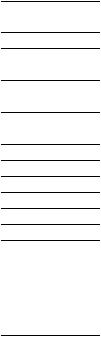
70
|
|
|
|
|
|
|
|
|
|
|
Таблица 13 |
|
Модификаторы для алюминиевых сплавов |
|
|
||||||||
|
|
|
|
|
|
|
|
|
|
|
|
Но- |
|
|
|
|
|
|
|
Количество, мас. % |
Темпера- |
Область |
|
Состав модификатора, мас. % |
|
|
|
|
тура про- |
примене- |
|||||
мер |
|
|
модифи- |
модифицирую- |
|||||||
|
|
|
|
|
|
|
катора |
щего элемента |
цесса, °С |
ния |
|
|
|
|
|
|
|
|
|
||||
|
|
|
|
|
|
|
|
|
0,05–0,15 Ti |
|
|
1 |
Лигатура Al–Ti (2,5Ti) |
|
|
|
|
|
|
1–3 |
|
Для чисто- |
|
|
|
|
|
|
|
|
|
|
0,05–0,15 Ti |
|
го алюми- |
2 |
Лигатура Al–Ti В (5Ti, 1В) |
|
|
|
|
|
|
1–2 |
|
||
|
|
|
|
|
|
0,01–0,02 B |
|
ния и де- |
|||
|
|
|
|
|
|
|
|
|
|
||
|
|
|
|
|
|
|
0,01–0,02 B |
720–750 |
формируе- |
||
3 |
Препарат «Зернолит» (55K |
TiF |
, 27KBF |
4 |
, 15C Cl , |
0,2–0,5 |
|||||
2 |
6 |
|
|
2 |
6 |
|
|
мых |
|||
3K2SiF6) |
|
|
|
|
|
|
0,05–0,1 Ti |
|
|||
|
|
|
|
|
|
|
|
|
|||
|
|
|
|
|
|
|
|
|
0,01–0,02 B |
|
сплавов |
4 |
Флюс (35NaCl, 35KCl, 20K2TiF6, 10KBF4) |
|
|
0,5–1,0 |
|
||||||
|
|
0,05–0,10 Ti |
|
|
|||||||
|
|
|
|
|
|
|
|
|
0,05–0,10 Na |
|
|
5 |
Металлический натрий |
|
|
|
|
|
|
0,05–0,10 |
750–780 |
Для доэв- |
|
|
|
|
|
|
|
|
|
|
0,05–0,10 Na |
|
тектиче- |
6 |
Флюс (67NaF, 33NaCl) |
|
|
|
|
|
|
1,0–2,0 |
780–810 |
||
|
|
|
|
|
|
|
0,05–0,10 Na |
|
ских силу- |
||
7 |
Флюс (62,5NaCl, 25NaF, 12,5KCl) |
|
|
|
|
1,0–2,0 |
730–750 |
||||
|
|
|
|
|
0,05–0,10 Na |
|
минов |
||||
8 |
Флюс (50NaCl, 30NaF, 10KCl, 10Na AlF ) |
|
|
0,5–1,0 |
720–750 |
||||||
|
|
|
3 |
6 |
|
|
|
0,05–0,10 Na |
|
|
|
9 |
Флюс (35NaCl, 40KCl, 10NaF, 15Na3AlF6) |
|
|
1,0–1,5 |
740–760 |
|
|||||
|
|
|
|
|
|
|
|
|
0,06–0,08 Sr |
|
|
10 |
Лигатура Al–Sr (10Sr) |
|
|
|
|
|
|
0,60–0,80 |
750–780 |
|
|
11 |
Лигатура Cu–P |
|
|
|
|
|
|
0,5–1,0 |
|
790–820 |
Для заэв- |
|
|
|
|
|
|
тектиче- |
|||||
12 |
Смесь (20 красного фосфора, 10K2ZrF6, 70KCl) |
|
1,5–2,0 |
|
790–825 |
||||||
|
|
|
|
|
ских силу- |
||||||
13 |
Смесь (58K2ZrF6, 34 порошка алюминия, 8 красного |
0,3–0,4 |
0,05–0,10 Р |
790–825 |
|||||||
фосфора) |
|
|
|
|
|
|
минов |
||||
14 |
Фосфорорганические вещества (трифенилфосфат, |
0,4–0,6 |
|
760–780 |
|
||||||
хлорофос) |
|
|
|
|
|
|
|
|
|||
|
|
|
|
|
|
|
|
|
|
|
|
70