
книги / Перспективные материалы и технологии порошковой металлургии
..pdfствия лазерного излучения, то говорят о лазерном синтезе. Единым эле- |
|
ментом для этих направлений является химически активная плазма, и, |
|
следовательно, проблемы, связанные с ней, также являются едиными |
|
как для лазерного синтеза, так и для плазмохимии. |
|
Ниже приведены порошковые материалы, полученные лазерным |
|
синтезом. |
|
Размер частиц (нм) нанодисперсного порошкадля различных веществ |
|
Si, SiC .................................................................................................... |
50 |
Cr2O3 ...................................................................................................... |
50 |
TiN ......................................................................................................... |
50 |
B4C ....................................................................................................... |
300 |
TiB2 ...................................................................................................... |
160 |
Mo .......................................................................................................... |
70 |
MoS2 ...................................................................................................... |
70 |
B ............................................................................................................... |
– |
Fe .......................................................................................................... |
7,6 |
ZrO2 ....................................................................................................... |
22 |
Преимущества газофазных методов очевидны: они дают возмож- |
|
ность селективно переводить исходный материал в газовую фазу, а затем |
|
переносить его к подложке, где он формируется в виде порошка либо |
|
пленки (все зависит от параметров процесса). Поскольку вещество осаж- |
|
дается из газовой фазы при температуре ниже точки плавления, в осадках |
|
можно зафиксировать структурные и композиционные эффекты. |
|
Несмотря на кажущуюся простоту процесса осаждения из газовой |
|
фазы, управление этим процессом с целью получения материалов задан- |
|
ной структуры и состава представляет собой сложную задачу. Процесс |
|
включает большое количество физических и химических стадий, которые |
|
часто рассматриваются как самостоятельные области науки и техники. |
Лазерное физическое газофазное осаждение
Процесс лазерного физического газофазного осаждения можно представить в виде двух этапов. Первый этап – это испарение мишеней под воздействием лазерного излучения и создание лазерной плазмы как источника синтезируемого материала, второй – это синтез нанодисперсного порошка из паровой фазы.
В последнее время, после открытия высокотемпературной сверхпроводимости, получило развитие изготовление высокотемпературных сверхпроводящих пленок с использованием лазерной технологии. Первый этап, т.е. испарение мишеней под воздействием лазерного излуче-
51
ния, является общим как для создания нанодисперсных порошков, так и для создания сверхпроводящих пленок, однако, варьируя условия испарения, можно получать либо пленки, либо порошки.
Наряду с парами испаряемого вещества в эрозионном факеле присутствует жидкокапельная фаза, которая может образоваться за счет объемного парообразования. В свою очередь, наличие капельной фазы приводит к созданию частиц достаточно больших размеров (50 нм и более).
Существует три типа лазерной плазмы, различающиеся механизмами образования: лазерная искра, эрозионная плазма и плазма оптического пробоя вблизи поверхности преграды. Возникновение лазерной плазмы – явление пороговое.
Лазерная плазма поглощает энергию, достаточную для нагрева до нескольких тысяч градусов. Нежелательно, чтобы часть энергии возвращалась обратно в активную среду лазера. В этом случае плазма играет роль одного из зеркал квантового генератора. Это приводит к автоколебательным процессам между активной средой лазера и плазмой оптического пробоя, когда часть отраженной энергии возвращается обратно в активную среду и способствует изменению КПД лазера.
Другим механизмом передачи энергии от плазмы оптического пробоя к поверхности является газовая теплопроводность. В обоих случаях отрыв оптического разряда от поверхности мишени, который может происходить при достаточно больших интенсивностях лазерного излучения, приводит к снижению эффективности лазерного воздействия на материал. Отсюда следует, что для повышения эффективности лазерного воздействия необходимо как можно быстрее создать приповерхностную плазму, а затем поддерживать ее в режиме медленного горения, не допуская экранировки поверхности.
С увеличением плотности мощности воздействующего излучения размеры частиц уменьшаются. Это объясняется тем, что с увеличением плотности мощности в зоне облучения перегрев расплавленного материала наступает быстрее и в более тонком слое и, как следствие этого, за счет объемного парообразования в эрозионный факел поступают более мелкие частицы. Двигаясь навстречу лазерному излучению, частицы интенсивно доиспаряются и, попадая в зону зондирования, становятся еще меньше. Таким образом, предполагается, что образование частиц происходит при интенсивном испарении мишени и дальнейшее уменьшение размера объясняется доиспарением частиц.
В большинстве работ по применению лазеров в качестве источника испарения отмечалось, что использовались импульсные оптические квантовые генераторы (ОКГ).
52
При использовании лазера непрерывного излучения облегчается регулирование скорости осаждения и создание условий испарения, близких к термодинамическому равновесию. В случае импульсных лазеров высокая скорость испарения приводит к выбросам частиц и жидких капель.
Сравнительный анализ возможности сохранения стехиометрии при испарении сложных полупроводниковых соединений показал, что конденсат обладает структурой, соответствующей исходному веществу – мишени.
Импульсные ОКГ используются, как правило, в режимах миллисекундного и наносекундного импульсов. Миллисекундные импульсы дают паровую фазу с разнообразным содержанием фрагментов – комплексов. В режиме наносекундных импульсов достигаются очень высокие температуры – до десятков тысяч градусов, что приводит к полной диссоциации пара и его интенсивной конденсации.
Таким образом, режим работы ОКГ является важнейшим физикохимическим параметром получения порошков, определяющим температуру и длительность испарения, состав и состояние испаренного вещества, а через них – скорость и механизм конденсации, структуру и свойства осажденного продукта.
Одной из важнейших характеристик лазерного испарения является ее эффективность. Эффективность испарения β определена как отношение испаренной за один импульс массы mi к энергии лазерного импульса при постоянной мощности, режиме, длине волны излучения ОКГ и частоте следования импульсов.
Эффективность испарения, как правило, в частотном периодическом импульсном режиме выше, чем в непрерывном. Эффективность испарения связана с температурой пара: с ростом β все большая часть импульса расходуется на испарение вещества и меньшая часть на разогрев пара, т.е. чем выше β, тем ниже температура пара.
Оценка удельной энергии испаряемого вещества дает величины порядка 0,1 и 1–100 эВ/атом. Таким образом, состояние испаряемого вещества может меняться от нейтрального пара, имеющего молекулярный состав даже при испарении органических соединений или слабоионизированного пара с большим количеством молекулярных фрагментов – комплексов, до сильно ионизованной, полностью диссоциированной на атомы высокотемпературной плазмы.
Многолетний опыт использования метода лазерного парофазного осаждения для синтеза нанодисперсных порошковых материалов, в том числе и в Научном центре порошкового материаловедения ПНИПУ, позволил оценить его основные достоинства:
53
–предельно чистые условия вакуумного препарирования – источник энергии для испарения вещества находится вне вакуумного объема;
–возможность получения порошков самых тугоплавких веществ и многокомпонентных соединений;
–высокая производительность и технологичность.
Требования к нанодисперсным порошкам
ипроблемы их синтеза
Впоследние годы уделяется большое внимание материалам, полученным из керамики. Керамика характеризуется твердостью, термостойкостью, эрозионной, окислительной и коррозионной стойкостью, низкой плотностью и в некоторых случаях особыми электрическими и оптическими свойствами. Однако использование керамических материалов в областях техники, где необходимы такие свойства, как высокое сопротивление разрушению, может стать реальным при условии повышения их надежности. Большой разброс по прочности, характерный для них, заставляет инженеров конструировать с таким запасом прочности, что керамика теряет свои преимущества посравнению с обычными материалами.
Дефекты, снижающие прочность, закладываются обычно на стадии предыстории образца – начиная от синтеза порошков и затем на всех этапах наработки вплоть до спекания в уплотненные материалы. Существует много причин появления дефектов, ограничивающих прочность, однако большинства из них можно избежать, если изготавливать керамику из порошков со следующими характеристиками:
–частицы порошка должны иметь малый размер, как правило, менее 0,5 мкм;
–частицы не должны слипаться;
–частицы должны иметь узкое распределение по размерам;
–частицы должны быть равноосными, т.е. приближенными по форме к шару;
–порошки должны характеризоваться высокой чистотой и отсутствием полиморфизма.
Все проблемы синтеза нанодисперсных порошков в той или иной степени связаны с трудностями, которые можно отнести к указанным характеристикам. На практике редко удается преодолеть все трудности
иполучить порошок с идеальными характеристиками.
Как правило, многие виды керамики характеризуются полиморфизмом, что создает иногда непреодолимые трудности для получения нанодисперсных порошков с нужными свойствами. Если удается полу-
54
чить порошки нужных размеров и формы, то не удается добиться узкого распределения частиц по размерам либо стабилизировать нужную фазу. А если удается получить нанодисперсные порошки с требуемым фазовым составом и малым размером частиц, то не удается получить сферическую форму и избежать агломерирования частиц.
В связи с этим наиболее эффективным способом получения нанодисперсных порошков представляется лазерный синтез, и прежде всего использование излучения CO2-лазера, которому свойственно наиболее эффективное преобразование электромагнитной энергии в тепловую.
Всю проблему лазерного синтеза нанодисперсных порошков можно разбить на три задачи.
Прежде всего необходимо провести термодинамическое моделирование процесса испарения и конденсации с целью определения теоретического размера частиц нанодисперсных порошков. Следует провести также термодинамический расчет состава газовой фазы над мишенью, произвести оценку теплоты и температуры испарения при различном давлении и изучить механизм и кинетику физико-химических процессов при конденсации паров материала мишени.
Следующая задача – это спектральные исследования эрозионного факела, образующегося при взаимодействии лазерного излучения с материалом мишени, в результате чего происходит испарение вещества с последующей конденсацией. Учитывая особенности взаимодействия вещества и поля, можно сказать, что этот процесс не всегда определяется рамками классической физики.
Проведение спектральных исследований позволяет определить условия формирования частиц в эрозионном факеле, что в сочетании с термодинамическими исследованиями, в свою очередь, позволяет получить более полную картину формирования нанодисперсных систем.
И наконец, последняя задача – исследование процесса синтеза нанодисперсных порошков из выбранного материала.
Термодинамические расчеты равновесных составов паров оксида алюминия в присутствии воздуха
Теоретическое описание процессов, происходящих при синтезе нанодисперсных порошков, требует многостороннего подхода к данной проблеме, в частности изучения:
1) термодинамического равновесия твердой и газовой фаз при протекании процессов испарения и конденсации оксида алюминия. Полученная информация позволяет оценивать степень пересыщения при кинетическом подходе, теплоты испарения и конденсации при разных ус-
55
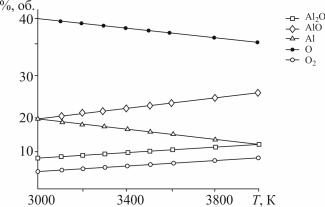
ловиях, выявить молекулы, атомы и ионы – удобные объекты для спектроскопического исследования и наблюдения за процессом, позволяющим провести диагностику состава и температуры, а также степень их отклонения от равновесных;
2) кинетики процессов испарения и конденсации. Кинетика испарения связана с процессами передачи энергии лазера поверхности образца, теплопередачи и лучистого теплообмена, а также формирования приповерхностной плазмы и плазменного факела.
Параметры факела – размер, температура, скорость, режим движения – зависят от интенсивности поглощаемой энергии и давления в реакторе. Эксперименты по испарению показали, что оксид алюминия дает ровный ламинарный факел, перпендикулярный поверхности жидкой капли в точке касания луча лазера.
Для получения термодинамических характеристик процесса испарения и конденсации оксида алюминия были проведены расчеты по разработанной программе на ЭВМ с применением средств табличного процессора «Суперкалк». В расчете использованы значения констант равновесия. С помощью средств «Суперкалк-4» на основе полученных данных построены графики зависимостей (рис. 18–20).
На рис. 18 представлена зависимость состава газовой фазы оксида алюминия от температуры в отсутствие воздуха. Из рисунка видно, что основными компонентами паров над Al2O3 являются AlO, Al2O, Al, O, O2.
Рис. 18. Зависимость состава пара над окисью алюминия от температуры
На рис. 19 представлены зависимости логарифма давления паров продуктов испарения оксидов от температуры в среде воздуха при различном давлении. Из графика следует, что при наличии воздуха давле-
56

ние паров оксидов снижается, или при одинаковом давлении паров оксидов в присутствии воздуха необходима несколько более высокая температура.
Результаты расчета использованы для спектроскопической диагностики процесса лазерного испарения оксидов. Для этих целей наиболее удобны двухатомные молекулы, атомы и ионы – AlO, Al, Al+.
Особенностью паровой фазы над окисью алюминия является высокая концентрация атомарного алюминия во всем диапазоне температур(см. рис. 18).
Для оценки исследования влияния избытка кислорода на стехиометрию продуктов в газовой фазе проведен расчет термодинамики испарения оксида алюминия в присутствии кислорода воздуха.
Из рис. 20 видно, что в присутствии кислорода воздуха количество кислорода в оксидах алюминия, находящихся в газовой фазе при низких температурах (3000 К), почти в 2 раза выше, чем при температуре 4000 К. Однако при повышении температуры вследствие повышения общего давления продуктов испарения оксидов над
твердой поверхностью (см. рис. 19) состав газа в присутствии воздуха и, соответственно, содержание кислорода в оксидах газа уменьшается и приближается к значениям в отсутствие воздуха (нижняя кривая на рис. 20).
Для определения теплоты фазового перехода при испарении оксида алюминия из жидкой фазы воспользуемся уравнением Гельмгольца– Гиббса, которое связывает логарифм давления паров над поверхностью
57
с обратной температурой линейной зависимостью, наклон которой равен теплоте фазового перехода:
δ (lńP) = ∆Hисп/(R · δ (1/T)). (9)
На рис. 19 представлена зависимость давления паров оксидов над поверхностью окиси алюминия от обратной температуры. Зависимость выражается почти прямой линией, по формуле (9) находим теплоту фазового перехода (испарения) – 597,0 кДж/моль. С учетом этой величины зависимость давления паров от температуры (см. рис. 19) в аналитическом виде имеет следующий вид:
lnP = –31173,8/T + 7,85308. |
(10) |
Таблица 1 6
Температура кипения оксида алюминия при равном давлении по данным термодинамических расчетов
Давление, кПа |
Ткип, К |
101 |
3970±50 |
50 |
3823 |
10 |
3521 |
Рассчитанная по уравнению (10) температура кипения оксида алюминия при различном давлении приведена в табл. 16.
Расчет теплоты испарения и экспериментальное определение скорости испарения оксида алюминия
Из рассчитанных составов паров оксида алюминия можно определить теплоту испарения, включающую тепло нагрева и расплавления оксида. Для Al2O3 получена формула
Q1 |
= αi (HT − Ho ) |
− (HT − Ho ) |
298.i |
+ |
H f .298.i |
− |
H f .298.Al |
2 |
O |
3 |
(11) |
||
|
i |
|
T .i |
|
|
|
|
|
|
|
|||
|
|
|
|
|
|
|
|
|
|
|
|
|
где αi – стехиометрические коэффициенты уравнений соответствующих
реакций для i-го компонента; (HT – Ho)T.i, (HT – Ho)298.i – энтальпии i-го компонента при температуре Т и 298 К соответственно; ∆Hf.298.i – стандартная теплота образования i-го компонента из элементов при темпе-
ратуре 298 К.
Стехиометрические коэффициенты αi получаются из табл. 16–17 путем деления парциального давления компонента на удвоенное суммарное количество атома металла (просчитанное для каждого столбца табл. 17). Эти коэффициенты соответствуют суммарной реакции
58
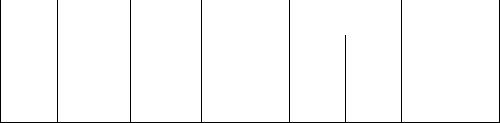
Al2O3(TB) →α1Al2O3(r) + α2Al2O3 + α3Al2O + … + αnO2 + αn+1O + |
(12) |
В результате расчета теплоты нагрева и испарения получены сле- |
|
дующие величины: |
|
– при 4000 К: Qисп.4000К = 2367 кДж/моль = 23,2 кДж/г, |
(13) |
– при 3300 К: Qисп.3300К = 1947 кДж/моль = 19,4 кДж/г. |
(14) |
Истинную теплоту испарения находим путем вычитания из полученных величин теплоты нагрева до температуры кипения и теплоты плавления:
L = 2367 – (651,38 – 10,02) = 1726 кДж/моль = 16,9 кДж/г. (15)
Большая полученная величина теплоты испарения связана с диссоциацией оксида с образованием атомарного Al и других радикалов при испарении Al2O3. Из табл. 16–17 видно, что соотношение O:Al в продуктах в 2,5 раза ниже, чем в оксиде Al, так как из оксида алюминия образуется много атомарного кислорода, что увеличивает потребности в энергии на испарение.
Экспериментальное определение поверхностного натяжения оксида алюминия
Экспериментальное определение поверхностного натяжения проводили с целью получения данных для расчета кинетики конденсации. Результаты измерений и расчетные величины приведены в табл. 17.
Таблица 1 7
Результаты экспериментов по измерению поверхностного натяжения оксида алюминия
Номер |
Состав |
Диаметр × |
Масса |
Плотность капли, Поверхностное |
||||
образца, |
кг/м3 |
натяжение σ, |
||||||
образца |
мас. % |
× 103, м |
капли·103, кг |
|
|
н/м |
2 |
|
ρ1 |
ρ2 |
|||||||
1 |
Al2O3 |
– 100 |
7,90 |
1,00 |
– |
– |
– |
|
2 |
Al2O3 |
– 100 |
7,10 |
0,84 |
– |
– |
– |
|
3 |
Al2O3 |
– 100 |
7,90 |
0,83 |
– |
– |
– |
|
|
Среднее: |
6,15±0,05 |
0,89±0,04 |
3960 |
4030 |
0,70±0,07 |
Примечание. ρ2 = 6m/(πd3) – экспериментально определенная плотность плавленой керамики (капли).
Капли оксида алюминия по внешнему виду серебристого цвета, повидимому, из-за присутствия металлического алюминия. Исходные образцы алюминиевой керамики – белого цвета.
Получено значение поверхностного натяжения (σ) жидкого оксида алюминия при температуре плавления (см. табл. 17).
59
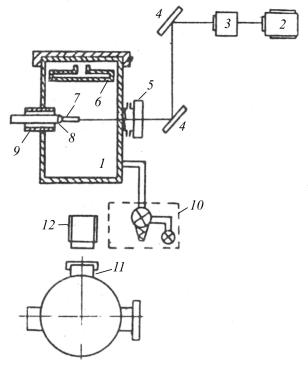
Закономерности формирования структуры и свойств нанокристаллических порошковых материалов
Для экспериментов по синтезу оксида алюминия была выбрана схема, представленная на рис. 21.
Излучение CO2-лазера 2 транспортировалось через измеритель мощности 3, систему поворотных зеркал 4, входное окно из КСI 5 и попадало на испаряемую мишень 7, расположенную в вакуумируемом реакторе 1. Мишень 7 крепилась в коническом медном держателе 8, а испаряемый порошок собирался на охлаждаемом медном диске 6. Собственное излучение лазерной плазмы регистрировалось спектрографом 12 через объектив 11. Вакуумный пост 10 давал возможность регулировать давление в реакторе от 10 до 100 кПа и позволял работать в режиме прокачки с целью обдува оптики поступающим в камеру газом.
Рис. 21. Схема установки синтеза нанодисперсных порошков: 1 – реактор; 2 – лазерная установка ЛТУ-0501; 3 – измеритель мощности РСИ-105-5; 4 – поворотные зеркала; 5 – входное окно из КСI; 6 – медный охлажденный диск для осаждения порошка; 7 – мишень; 8 – конический держатель; 10 – вакуумный
пост AV-63; 11 – объектив; 12 – спектрограф ДФС-458С
60