
книги / Перспективные материалы и технологии порошковой металлургии
..pdf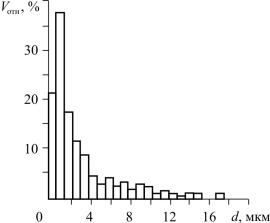
Рис. 4. Дифференциальное распределение по размерам частиц порошка TiC, подвергнутого обработке в планетарноцентробежном аппарате в режимах ускорения 600 м/с2
в течение 15 мин (Sуд = 14,4 м2/г)
Из результатов исследования кинетики измельчения карбида титана следует, что к процессу измельчения, реализуемому в чистом виде на начальном этапе обработки до 5 мин, с увеличением продолжительности измельчения добавляется процесс агрегатообразования, приводящий к замедлению роста наблюдаемой удельной площади поверхности.
Таким образом, диспергирование порошкообразного карбида титана в планетарно-центробежном аппарате позволяет получать порошок карбида с частицами размером 1–2 мкм и удельной площадью поверхности 14,4 м2/г вместо 2–30 мкм и (0,41±0,1) м2/г соответственно в случае заводской поставки. Однако дальнейшее применение диспергированных порошков карбида титана в качестве покрытий требует их гранулирования.
Рентгенограммы гранул TiC, полученных гранулированием со связующим на роторно-лопастном грануляторе при 25 °С с последующей конвективной сушкой гранулята, представлены на рис. 5. В качестве пластификаторов-смазок использовались поливиниловый спирт высшей категории (СН2=СНОН), парафин первой категории, жидкое натриевое стекло (nNa2O×kН2О). Количество связующего в гранулах составляло 5– 10 % от их массы.
Термодинамический расчет показал, что в температурном интервале 600–1200 °С наиболее вероятны следующие реакции:
(1/2)TiC + О2 ↔ (1/2)ТiО2 + (1/2)СО2↑
11

(2/3)TiC + О2 ↔ (2/3)ТiО2 + (2/3)СО↑ TiC + СО2 ↔ ТiО2 + С
Рис. 5. Рентгенограммы порошка карбида титана: 1 – исходное состояние; 2 – режимпомола 400 м/с в течение 5 мин
Исследована кинетика окисления частиц и гранул карбида титана в токе очищенного кислорода в реакторе термогравиметрической установки с одновременным автоматическим контролем изменения массы образца m (масса навески М = 10 г) с помощью микровесов и фиксированием на потенциометре «ЭПП-09» температуры испытаний от 600 до 1200 °С и давления реакционного газа 1,33 кПа. Продолжительность температурного воздействия (время окисления) составляла от 0,5 до 5 мин, что связано с быстротечностьюпроцессов, происходящих при окислении.
Результаты окисления порошка TiC представлены на рис. 6. Кинетика окисления TiC описывается зависимостями, близкими к
линейным, а наибольшая скорость окисления наблюдается при 800 °С. При температурах выше 800 °С наблюдается область с отрицательным температурным коэффициентом.
При исследовании компактных образцов обнаружено, что в процессе окисления карбида титана на его поверхности образуется оксидная фаза TiО2 с температурой плавления 1850 °С.
Спекание оксидных систем обычно наблюдается при температурах выше (0,5±0,7)Тпл. В этом случае скорость процесса окисления начинает определяться диффузией катионов титана по междоузлиям кристаллической решетки рутила к фазовой границе оксид–газ. В отличие от горячепрессованных образцов при окислении мелкодисперсных порошков TiC, за счет развитой поверхности, процессы спекания наблюдаются при более низких температурах, что ведетк снижению скорости окисления.
12

Рис. 6. Кинетические кривые окисления (а) и температурные зависимости скорости окисления (б) зернистого TiC при PO2 = 1,33 кПа в интервале температур 873–1473 °С:
а: 1 – 800 °С; 2 – 700 °С; 3 – 600 °С; 4 – 900 °С; 5 – 1000 °С; 6 – 1100 °С; 7 – 1200 °С; б: 1 – 5 мин, 2 – 4 мин, 3 – 3 мин, 4 – 2 мин, 5 – 1 мин, 6 – 0,5 мин
Рентгенофазовый анализ показал, что в конденсированных продуктах окисления зернистого карбида титана обнаруживается оксикарбид TiC0,95O, присутствующий во всем интервале температур. Кроме оксикарбида титана в конденсированных продуктах реакции регистрируются TiC и ТiO2. Сравнение интенсивностей линий (002) углерода, измеряемых методом съемки «по точкам», показало отсутствие его во всем исследованном температурном интервале.
По данным хроматографического анализа, отходящий газ содержал одновременно и оксид, и двуоксид углерода. Установлено, что отношение СО/СО2 в отходящих газах возрастает при увеличении продолжительности и температуры взаимодействия в соответствии с рис. 7.
Результаты окисления гранулированного TiC представлены на рис. 8 в виде температурных и кинетических зависимостей скорости окисления.
Процесс окисления включает поверхностное и диффузионное окисление, а также химическое взаимодействие карбида титана с продуктами высокотемпературного разложения и возгонки связующих компонентов. Большое влияние на характер кинетики окисления оказывают физикохимические свойства связующего. Так, при использовании в качестве связующего жидкого стекла при температурах исследования кинетические
13

кривые (рис. 8, а) находятся в области отрицательного увеличения массы. С ростом температуры от 900 до 1200 °С они переходят в область с положительным увеличением массы. В дальнейшем кинетические кривые изменяются практически по линейному закону и отличаются от кинетических кривых дисперсного TiC меньшим углом наклона, характеризующим скорость окисления. Наибольшая скорость окисления наблюдается при 1100 °С, при дальнейшем росте температуры кинетические кривые переходят в область с отрицательным температурным коэффициентом.
Рис. 7. Зависимость отношения СО/СО2 в отходящих газах при окислении от времени и температуры при PO2 = 1,33 кПа:
1 – 1200 °С; 2 – 1000 °С; 3 – 800 °С; 4 – 600 °С
Рис. 8. Кинетические кривые окисления (а) и температурные зависимости скорости окисления (б) гранулированного TiC при PO2 = 1,33 кПа (фракция гранул 0,24–0,34 мм, связую-
щее – жидкое натриевое стекло): а: 1 – 1100 °С; 2 – 1000 °С;
3 – 1200 °С; 4 – 900 °С; 5 – 800 °С; 6 – 700 °С; 7 – 600 °С; б:
1 – 5 мин; 2 – 4 мин; 3 – 3 мин; 4 – 2 мин; 5 – 1 мин
14

Резкая потеря массы навесок гранулированного TiC в начальный момент окисления объясняется испарением влаги, находящейся в значительном количестве в жидком стекле. В дальнейшем пары влаги, являясь, в свою очередь, окислителем, могут выступать в роли некоторого барьера реакции окисления кислородом. Отсутствие термодинамических данных не позволяет провести оценку возможности протекания реакции с образованием сложного комплекса SiO2×ТiO2.
Рентгенофазовый анализ продуктов окисления TiC, гранулированного на жидком стекле, показал, что при температурах 800, 1000, 1200 °С они состоят из TiC, Тi2С3 иω-фазы (рис. 9).
Рис. 9. Дифрактограммы продуктов окисления гранулированного TiC, окисленного при температурах 800 (а), 1000 (б) и 1200 °С (в) (кобальтовое излучение, связующее – жидкое стекло)
Использование в качестве связующего органических соединений (поливинилового спирта и парафина) показало, что характер кинетических кривых близок к окислению гранул на жидком стекле, но возгонка и испарение связующих протекают более интенсивно. Угол наклона, ха-
15
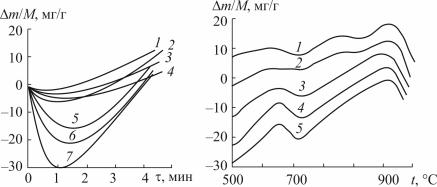
рактеризующий скорость реакции окисления, близок к углу наклона для зернистого TiC. Кинетические кривые окисления гранулированного TiC (рис. 10, а) свидетельствуют о том, что с увеличением времени процесса окисления повышается скорость увеличения массы продуктов окисления. Максимальный уровень увеличения массы достигается при температуре 1100 °С, в то время как для зернистого TiC – при 800 °С. Дальнейшее повышение температуры приводит к скачкообразной потере массы. В диапазоне температур 600–800 °С существенное влияние на ход реакции окисления оказывает время протекания реакции (рис. 10, б).
а |
б |
Рис. 10. Кинетические кривые окисления (а) и температурные зависимости скорости окисления (б) гранулированного TiC при РО2= 1,33 кПа (фракция гранул 0,24–0,34 мм, связующее – поливиниловый спирт): а: 1 – 1100 °С; 2 – 900 °С;
3 – 700 °С; 4 – 1200 С; 5 – 1000 °С; 6 – 800 °С; 7 – 600 °С; б: 1 – 5 мин; 2 –4 мин; 3 – 3 мин; 4 – 1 мин; 5 – 1 мин
С увеличением времени наблюдается увеличение массы продуктов окисления, что объясняется присоединением кислорода к бензольным группам по свободным связям. С повышением температуры происходит разрушение бензольных групп. В дальнейшем процесс окисления имеет характер, сходный с кинетикой окисления карбида титана, гранулированного с применением жидкого натриевого стекла.
Рентгенофазовый анализ продуктов окисления карбида титана, гранулированного на поливиниловом спирте, показал, что при температурах выше 800 °С обнаруживается только карбид титана. Это подтверждает присоединение кислорода к бензольным группам. Поливиниловый спирт, разлагаясь, препятствует окислению TiC, упакованного в гранулы, скорость окисления его в большей степени зависит от размера
16
гранул, что прослеживается при использовании в качестве связующего всех трех веществ (жидкого натриевого стекла, поливинилового спирта, парафина). Наибольшее замедление скорости окисления TiC наблюдается в гранулах размером 0,25–0,63 мм. Характер кинетических кривых свидетельствует о том, что их угол наклона меньше угла наклона кинетических кривых окисления дисперсного TiC во всем исследованном временном интервале (см. рис. 6, а и рис. 10, а), т.е. реакция окисления переходит в кинетическую область.
Изменение характера кинетики окисления карбида титана (см. рис. 8, а и рис. 10, а), упакованного в гранулы, по сравнению с порошковым (см. рис. 6) определяется влиянием связующих компонентов на механизм окисления. Любая химическая реакция может протекать по двум механизмам: диффузионному и кинетическому. Диффузионный механизм действует, когда скорость диффузии реагента, определяющего реакцию,
меньше скорости протекания реакции (Vдиф < Vреакц), при Vдиф > Vреакц действует кинетический механизм. Условие Vдиф > Vреакц свидетельствует о
том, что имеется барьер для протекания реакции с возможной скоростью в бинарной системе TiC–O2. В данном случае наличие в гранулах веществ, имеющих низкую температуру испарения и возгонки, определяет переход начальной стадии реакции окисления TiC в диффузионную область.
Показано, что возможно диспергирование карбида титана до размеров частиц 1–2 мкм и гранулирование данных частиц до размеров гранул 250, 250–340 и 630–1250 мкм. Скорость окисления гранул TiC зависит от вида связующего вещества и размера гранул, причем наибольшее замедление скорости окисления наблюдается вгранулах размером 0,25–0,63 мм.
Таким образом, получены гранулированные материалы, содержащие диспергированный карбид титана.
Композиционные порошки для плазменного напыления TiC, TiO2 – Al2O3 были получены конгломерированием в грануляторе.
Для определения влияния количества связующего на пористость конгломерированного порошка фракции 60–100 мкм приготовлено несколько смесей с различным содержанием связующего (табл. 3).
|
|
|
Таблица 3 |
|
Влияние связующего на пористость смеси |
||
|
|
|
|
Номер смеси |
|
Количество связующего, % |
Пористость смеси, % |
I |
|
10 |
17 |
II |
|
16 |
12 |
III |
|
20 |
30 (рыхлая смесь) |
17
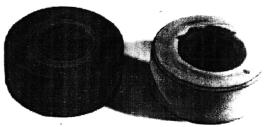
Из табл. 3 видно, что наименьшей пористостью обладают композиционные конгломерированные порошки с содержанием 16 % связующего, которые и были использованы в качестве материалов для нанесения плазменных покрытий на изделия. Покрытия наносили на установке плазменного нанесения покрытий «УПУ–ЗД» при следующих параметрах режима напыления: J = 400 A, U = 70, Q = 40 дел/шк., L = 80 мм.
Испытание износостойкости покрытий проводили на машине трения «СМЦ-1». Контртело было выполнено из СтХ13 в виде ролика диаметром 50 мм с твердостью 60–63 HRC. Скорость скольжения по поверхности трения составляла 0,785 м/с, продолжительность испытания – 8 ч при осевой нагрузке на пару трения 40, 50, 60 и 70 кг. Результаты исследований приведены в табл. 4.
|
|
|
|
|
|
Таблица 4 |
|
Зависимость износа от нагрузки на пару трения |
|
||||||
|
|
|
|
|
|
|
|
Количество |
|
|
Нагрузка на пару трения, кг |
|
|||
связующего |
40 |
|
50 |
|
60 |
|
70 |
|
|
Износ, мкм/км |
|
|
|
||
16 |
0,66 |
|
0,673 |
|
0,696 |
|
0,854 |
Рис. 11. Тяговый ролик с износостойким покрытием
Разработанные покрытия были испытаны в качестве износостойких на тяговых роликах (рис. 11), которые показали удовлетворительную работоспособность.
1.2. Карбидостали
Создание композиций карбид–сталь Гатфильда, хотя в них и заложена идея использования метастабильного состояния стали 110Г13, по аналогии с мартенситным ГЦК→ГПУ-превращением в кобальтовой матрице, не во всем подходят для композиций с относительно невысоким содержанием карбидов, так как связка обладает высокой износостойкостью лишь при весьма значительной пластической деформации.
18
Вместе с тем экспериментально доказана перспективность частичной замены марганца на ванадий или хром, а если материал содержит еще и никель, то оптимальная концентрация марганца не превышает десятых долей процента. Такую концентрацию марганца обеспечивает в спеченных сталях применение порошков технического железа, где всегда есть марганец в качестве сопутствующей примеси.
Важнейшей особенностью высокомарганцевых сталей является повышенная концентрационная неоднородность (ее, однако, не считали необходимым условием формирования метастабильного аустенита), поэтому одной из задач исследований было создание концентрационно-неод- нородной метастабильной матрицы, в которой наряду с заданным химическим составом необходимо было обеспечить определенный уровень неоднородности распределения легирующего элемента (в данном случае никеля). Исходя из этого продолжительность спекания определяли по величине коэффициента вариации концентрации V. Уровень V ≈ 0,10–0,08 выбирали на основе опыта изучения никелевых метастабильных сталей. После отсева точек, имеющих интенсивность рентгеновского излучения ниже фона или выше эталона, а также не укладывающихся в логарифмический нормальный закон распределения концентраций (31 точка из 302) для режима спекания при температуре 1360 °С в течение 4 ч, коэффициент вариации концентрации равен 0,09±0,01. Такое значение концентрационной неоднородности обеспечивало наилучшее сочетание свойств при любых испытаниях, сокращение спекания только на 1 ч 1360 °С, 3 ч приводило к падению абразивостойкости в 1,2–1,5 раза (ПК50Н12 + + 10 мас. % TiC). Отметим также, что знание закона распределения и коэффициента вариации дает полное статическое описание распределения никеля в стали. Высокое содержание никеля стало возможно в том числе благодаря действию TiC как α-стабилизатора. В процессе исследований установлено слабое влияние TiC в интервале 10–20 мас. % на абразивостойкость (рис. 12), но падение механических свойств по мере роста содержания TiC весьма значительно (рис. 13).
С увеличением концентрации добавок карбидной фазы твердость монотонно возрастает от 50 до 62 HRC. Менее всего рост содержания карбидной фазы отражается на пределе прочности при испытании на изгиб (σизг) композитов, содержащих 10 мас. % карбида титана (3500 МПа) и 20 мас. % карбида титана (2300 МПа). Несмотря на резкое падение значений σв и K1с с ростом концентрации TiC при содержании карбидной фазы 10 мас. % (14 об. %), конструкционная прочность остается на уровне ком-
19

пактных литых сталей, что связано с большим вкладом в улучшение свойств фазовых превращений в зоне разрушения.
Рис. 12. Абразивный износ сталей. TiC, %: 1 – 10, 2 – 20, 3 – 8; 4 – TD (литая сталь)
Рис. 13. Влияние содержания упрочняющей фазы на предел прочности при растяжении (1), трещиностойкость (2)
и ударную вязкость (3) карбидосталей
Необычное поведение данных материалов наблюдали и при других видах контактного взаимодействия. Так, при изнашивании в консистентной смазке с частицами (5 %) корунда интенсивность износа пары ПА – ПК100Д15 – ПК50Н12 + 10 % TiC, которую измеряли по изменению диаметров наружной (ступицы) и внутренней втулки, оказалась более чем в 30 раз лучше, чем при трении инструментальной стали Х12Ф1 (514 НВ) по
20