
книги / Технология конструкционных материалов. Способы получения деталей (заготовок) и конструкций
.pdf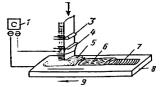
Рис. 68. Схема процесса наплавки лен- |
|
|
|
|
|
|
|
|
|
|
|
|
||
|
|
2 |
|
|
|
|
|
|
|
|
||||
точным электродом под флюсом: 1 |
|
|
|
|
|
|
|
|
|
|
||||
|
|
|
|
|
|
|
|
|
|
|
|
|||
|
|
|
|
3 |
|
|
|
|
|
|||||
источник питания; 2 ленточный элек- |
1 |
|
|
|
|
|
|
|
|
|||||
|
|
4 |
|
|
|
|
|
|||||||
трод; 3 ролики подачи электрода; 4 |
|
|
|
|
|
|
|
|
|
|
|
|||
|
|
|
|
|
5 |
|
|
|
7 |
|
||||
|
|
|
|
|
6 |
|
||||||||
мундштук (токоподвод); 5 флюс; 6 |
|
|
|
|
|
|
|
|
|
|
|
|
|
|
|
|
|
|
|
|
|
|
|
|
|
|
|||
шлак; 7 наплавленный металл; 8 ос- |
|
|
|
|
|
|
|
|
|
|
|
|
||
|
|
|
|
|
|
|
|
|
8 |
|||||
новнойметалл; 9 направлениенаплавки |
|
|
|
9 |
|
|
|
|
|
|
|
в процессе наплавки почти под прямым углом к основному металлу. При наплавке ленточным электродом образуется плоский валик наплавленного металла, примерно равный ширине ленточного электрода, что обеспечивается малой глубиной проплавления основного металла, незначительным влиянием его на состав наплавленного металла. Способ, высокопроизводительный за счет высокой скорости наплавки и при большой силе тока, применяется для наплавки корро- зионно-стойкой стали, сплава «инконель» и других коррози- онно-стойких наплавочных материалов.
Наплавка открытой дугой. Наплавка без защитной среды, в среде воздуха, осуществляется проволокой сплошного сечения или порошковой проволокой. При наплавке используют простое оборудование и технологию. Возможна наплавка в полевых условиях. Состав наплавленного металла можно регулировать в широких пределах.
Наплавка в среде углекислого газа обеспечивает защиту зоны дуги от окружающего воздуха.
При осуществлении износостойкой наплавки в СО2 используют проволоку сплошного сечения или порошковую проволоку. Недостаток этого способа связан с невозможностью работы на открытом воздухе.
Основное назначение способа: наплавка деталей, подвергаемых последующей механической обработке. Наплавка
131
порошковой проволокой применяется без последующей обработки.
Плазменная наплавка основана на возникновении между основным металлом и электродом горелки (катодом) электрической дуги, обеспечивающей переход в плазменное состояние рабочего газа, подаваемого в зону дуги. При этом из сопла горелки истекает высокотемпературная плазменная струя, обеспечивающая плавление наплавочного материала. Для образования плазмы используют смесь гелия (75 %) с аргоном (25 %), а в качестве защитного газа применяют аргон. В качестве наплавочного материала используют коррозионностойкую сталь, никель и его сплавы, сплавы меди и др. При наплавке проволокой диаметром 2,4 мм получают слой толщиной до 6,5 мм.
Наплавка в среде защитного (инертного газа аргона,
гелия и др.) осуществляется плавящимся и вольфрамовым электродами.
При наплавке плавящимся электродом дуга возникает между основным металлом и электродным наплавочным материалом, который подается автоматически в виде электродной проволоки.
При наплавке вольфрамовым электродом дуга, за счет теплоты которой происходит плавление наплавочного присадочного металла, возникает между основным металлом и вольфрамовым электродом.
Применение инертного газа исключает необходимость использования флюса, поэтому данный способ особенно эффективен при наплавке цветных металлов, высоколегированных сталей и других материалов, чувствительных к окислению и азотированию. Высокое качество наплавленного металла достигается большим выбором наплавочных материалов.
132

Наплавка токами высокой частоты (ТВЧ) (рис. 69).
Наплавку ТВЧ выполняют с помощью индукционного нагрева с присадочным материалом, который предварительно наносят на поверхность изделия в виде смеси порошка, литого кольца или прессованного брикета либо расплавляют в огнеупорной воронке, расположенной над наплавляемой деталью.
Возникающие индукционные токи нагревают до плавления поверхностный слой детали и легирующую шихту, которая образует на детали ровную поверхность. Способ характеризуется незначительной глубиной проплавления основного металла и высокой производительностью.
2 –
1 3
4 5
Сжатый воздух или газ
Рис. 69. Схема распыления проволоки высокочастотным индукционным способом: 1 проволока; 2 индуктор; 3 концентратор; 4 покрытие; 5 изделие
Наплавку токами высокой частоты применяют для получения износостойкого слоя на деталях, подвергающихся быстрому износу (ножи дорожных машин, детали землеройного оборудования и т.п.). Недостатком способа является высокая стоимость генераторов высокой частоты.
Электрошлаковую наплавку применяют для получе-
ния наплавленного слоя толщиной не менее 10…12 мм. Наплавка этим способом протекает при непрерывной
подаче электродной проволоки (или ленты) внутри слоя расплавленного шлака, а плавление их происходит за счет теп-
133
лоты электросопротивления при пропускании тока между основным металлом и электродом.
Электрошлаковая наплавка обеспечивает наплавку слоя большой толщины; меньший расход шлака, чем при дуговой наплавке под флюсом; возможность наплавки высокоуглеродистых и других материалов; высокую производительность; высокое качество поверхности наплавки.
4.2. Напыление покрытий
Для восстановления изношенных деталей и для нанесения на детали защитных и упрочняющих покрытий наряду
снаплавкой используют различные способы напыления. Они основаны на нагреве мелких частиц напыляемого материала и переносе их на поверхность изделия-подложки. Соударяясь
сподложкой, нагретые частицы закрепляются на ней и формируют покрытие. Чем больше скорость частиц, тем выше
качество покрытия его плотность и прочность сцепления с основой. Материалом покрытия могут быть металлы, керамика, полимеры; материалом подложки металл, стекло, ткани и др. Можно создавать многослойные покрытия из слоев различного состава. Расход материалов при напылении невелик, так как подложка обычно не плавится и не разбавляет материал покрытия. Используемое оборудование относительно простое и производительное.
Применение напыленных покрытий снижает затраты металла, повышает срок службы и надежность деталей в жестких условиях эксплуатации (интенсивный износ, высокие скорости и температура, коррозионные среды и т.п.). Напылением можно получать тепло- и электроизоляционные покрытия. Напыление разных материалов можно производить на одном и том же оборудовании. Размеры напыляемых подложек не ограничены.
Напылением сравнительно просто наносить покрытия на любом ограниченном участке поверхности изделия из самых
134
разнообразных материалов, надежно защищать эти участки и получать желаемые свойства покрытия.
Основные области применения технологии напыления это защита поверхностей деталей и узлов машин от абразивного, эрозионного, коррозионного и других видов воздействия рабочей среды.
К основным способам напыления относятся газопламенное и плазменное напыление, электродуговая металлизация, детонационное и вакуумное напыление.
Процесс газопламенного напыления (рис. 70) основан на использовании кислородно-ацетиленового или кислороднопропанового пламени 2. В него подают проволоку 1 или порошок, конец проволоки 3 оплавляется, и расплавленные частицы 5 уносятся газовым потоком 4 на подложку 7, образуя покрытие 6. Скорость частиц порошка в серийных газопламенных установках составляет 50…100 м/с.
Температура нагрева напыляемого материала относительно невелика. Поэтому способ целесообразно применять для нанесения пластмасс, цинка, алюминия, медных сплавов, сталей. Можно наносить также оксид алюминия и карбидсодержащие композиции.
Плазменное напыление отличается более высокими температурой и скоростью газовой струи. В плазмотроне формируется поток низкотемпературной плазмы. Напыляемый материал (проволока, порошок) вводится в него, разгоняется до 100…400 м/с и переносится на подложку (рис. 71).
Между катодом 3 (из чистого вольфрама или с добавлением 2 % тория) и медным водоохлаждаемым соплом анодом 4, возникает дуга, нагревающая поступающий в сопло горелки рабочий газ 1 (аргон или азот), который истекает из сопла в виде плазменной струи. Порошковый наплавочный материал 2 подается в сопло струей транспортирующего газа, нагревается плазмой и с ускорением переносится на поверхность 5 основного материала для образования покрытия.
135
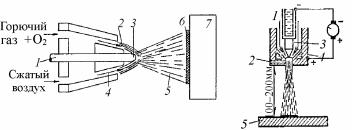
|
|
|
|
|
Рис. 70. Схема установки для газопла- |
Рис. 71. Схема плаз- |
|||
менного распыления проволоки (прутка) |
||||
менного напыления |
||||
|
из напыляемого материала |
|||
|
|
|
Высокая температура плазмы позволяет проводить напыление тугоплавких материалов. Можно регулировать температуру и скорость плазменной струи.
Покрытия, полученные плазменным напылением, обладают высокой плотностью и хорошим сцеплением с основой.
Дуговая металлизация
Металлизация – это нанесение металлического покрытия на поверхность методом осаждения на ней жидкого металла, распыляемого газовой струей. Металлическая проволока подается к источнику нагрева, расплавляется и под давлением газовой струи вылетает с большой скоростью из сопла металлизатора в виде распыленных капель, которые ударяются о поверхность детали и, соединяясь с ней, образуют слои покрытия.
В зависимости от используемого источника теплоты различают металлизацию дуговую, газовую, плазменную
и ТВЧ. При дуговой металлизации скорость переноса капель составляет 60…250 м/с.
Для металлизации применяют проволоки медные, алюминиевые, стальные и цинковые, а также неметаллические материалы в виде порошков (стекла, эмали, пластмасс).
136
Поверхность подложки перед металлизацией должна быть тщательно очищена и предпочтительно опескоструена.
Металлизацию применяют для защиты от изнашивания, коррозии, а также в декоративных целях для таких изделий, как цистерны, бензобаки, мосты, изнашивающиеся части валов, деталей машин и т.п.
Детонационное напыление
Способ основан на разгоне частиц порошка при взрыве (детонации) кислородно-ацетиленовой смеси в стволе специальной установки. Скорость частиц порошка составляет 600…4000 м/с. Сталкиваясь с поверхностью подложки, порошок разогревается. Высокая скорость частиц и их разогрев при ударе о подложку обеспечивают получение плотных и прочно сцепленных с основой покрытий. Состав покрытия тот же, что и порошка, в отличие от газотермических процессов состав частиц при напылении не изменяется. Температура основного металла остается низкой, он не деформируется, что позволяет использовать процесс при изготовлении прецизионных деталей. Толщина однослойного покрытия мала примерно 5…25 мкм, поэтому покрытия делают многослойными, наращивая 0,25…0,3 мм. Ударные волны, возникающие при детонационном напылении, частично очищают поверхность подложки.
Детонационное напыление применяют для повышения жаро- и теплостойкости деталей, получения износостойких и коррозионно-стойких покрытий, создания промежуточных слоев при пайке разнообразных материалов, замены цельноспеченных деталей из тугоплавких соединений на металлические с тугоплавким покрытием.
137
Вакуумное напыление
При термическом напылении металл нагревают в вакууме 10 2…10 3 Па до температуры, при которой давление его паров около 1 Па. На пути потока паров помещают подложку, и пары конденсируются на ней. Этим способом получают коррозионно-стойкие покрытия толщиной до 100 мкм с хорошей адгезией с основой. Способ отличается высокой производительностью, покрытия наносятся на непрерывно движущуюся ленту и получаются однородными с высокой степенью чистоты.
Ионное осаждение отличается от термического напыления тем, что пары осаждаемого металла или сплава ионизируются в плазме тлеющего разряда, в котором катодом служит испаряемый материал, а анодом подложка. Пары металла попадают в плазму инертного газа под давлением 0,1…1 Па. При этом происходит ионизация паров, ионы ускоряются электрическим полем, и поток ионов осаждается на подложке. Качество покрытия улучшается пропорционально степени ионизации напыляемого вещества.
Способ дает возможность ионной очистки поверхности перед напылением, обеспечивает плотность и однородность толщины покрытия, хорошую адгезию покрытия без нагрева подложки, универсальность по напыляемым материалам.
5. Пайка металлов
Пайкой называется процесс соединения частей изделия, обеспечиваемый за счет кристаллизации расплавленного промежуточного металла припоя, температура плавления которого всегда более низкая, чем температура плавления соединяемых металлов.
138
Пайку можно рассматривать как сочетание трех одновременно протекающих процессов: нагревание паяемого металла до температуры расплавления припоя, плавление припоя, взаимодействие припоя с паяемым металлом и возникновение межкристаллитных связей. Свойства паяного соединения определяются свойствами литого припоя, промежуточного слоя и основного металла, подвергнутого термическому воздействию при пайке. В технике применяют большое количество разнообразных припоев в зависимости от соединяемых металлов и назначения паяных соединений.
Важнейшей характеристикой припоев является температура плавления.
Различают два основных вида пайки: высоко- и низкотемпературную. Температура плавления припоев для высокотемпературной пайки составляет свыше 550 С, для низкотемпературной ниже 550 С.
В основу припоев с высокой температурой плавления входят Cd, Cu, Zn и Ag, а в основу припоев с низкой температурой Sn, Pb и Sb. Пайку широко применяют в различных отраслях народного хозяйства при изготовлении изделий из чугуна и цветных металлов.
6. Резка металлов
Термическую резку металлов и сплавов можно класси-
фицировать по способу нагрева разрезаемого металла газовая или электрическая резка и по способу механизации ручная или механизированная.
Резка начинается с нагрева металла в начале реза подогревающим пламенем резака до температуры воспламенения металла в струе кислорода. Металл сгорает с выделением тепла, которое передается через образовавшийся шлак нижележащим слоям; происходит сгорание металла по всей толщине разрезаемого листа с образованием узкой щели (реза).
139
Образующиеся в процессе резки оксиды и шлаки удаляются из реза струей кислорода, а также под действием собственной массы.
По характеру применяемого подогрева резка подразделяется на кислородную, кислородно-флюсовую, кислороднодуговую, плазменно-кислородную и др. Различают поверхностную (срезается поверхностный слой металла), разделительную (металл разделяется на части) и копьевую (в металле прожигается глубокое отверстие) кислородную резку.
Разделительная кислородная резка широко применяется при раскрое листов и резке профильного материала. В настоящее время получила значительное распространение машинная разделительная кислородная резка, которую выполняют на стационарных и переносных машинах. Основное применение поверхностной кислородной резки исправление брака на литье и прокатке. Копьевая резка широко применяется при обработке неметаллических материалов, например бетона.
Резку плазменной струей, плазменной дугой и лазерную можно применять практически для всех материалов.
При разделительной резке плазменной струей сопло плазмотрона располагают в непосредственной близости (1,5…2 мм) от поверхности заготовки и производят локальное выплавление или сжигание материала. Ширина реза при этом весьма незначительна 1…2 мм. Шероховатость Rz может составлять 30…40. Плазменной струей, полученной в столбе дугового разряда независимой дуги, разрезают неэлектропроводящие материалы (например, керамику), тонкие стальные листы, алюминиевые и медные сплавы, жаропрочные сплавы и т.д. При плазменной резке используют аргон, его смесь с водородом, воздух и другие газы.
140