
книги / Переработка углеводородных газов
..pdfПри каталитической очистке серосодержащие соединения выделить из газа не удается, так как они превращаются в другие химическиесоединения, которыеболее легко извлекаются изгаза.
Существует три типа каталитической очистки от меркаптанов: гидрирование, гидролиз и окисление.
Гидрирование – это процесс селективного замещения атома серы в сероорганических соединениях водородом в присутствии катализатора с образованием H2S и веществ, не содержащих серу:
C2H5SH + H2 C2H6 + H2S;
COS + H2 CO + H2S.
По убыванию реакционной способности сероорганические соединения можно расположить в следующий ряд: серооксид углерода – меркаптаны – тиофен. Процесс проводят при 300–400 С в присутствии кобальтили никель-молибденового катализатора.
Гидролиз – это процесс конверсии сероорганических соединений при взаимодействии их с водяным паром при высоких температурах:
COS +H2O CO2 + H2S;
СS2 + H2O CO2 + 2H2S.
Окисление идет в присутствии катализатора при температуре 300–350 С с образованием SO2, который в последующем выделяют из газа. Для демеркаптанизации сжиженных газов и ШФЛУ используют абсорбционно-каталитический процесс «Мерокс». Сущность процесса состоит в том, что сначала в абсорбере меркаптаны поглощаются щелочным раствором, содержащим катализатор (органические соли кобальта), а далее насыщенный меркаптанами раствор направляют на окисление кислородом воздуха, при этом меркаптиды разлагаются на меркаптаны и щелочь, а меркаптаны окисляются в дисульфиды, которые абсорбируют углеводородной фазой и выводят:
2C3H7SH + O2 C3H7-S-S-C3H7 + 2H2O.
51
Достоинство каталитических методов очистки – это высокая степеньудалениясероорганическихсоединений(до0,5–1 мг/м3 газа).
4.13. Осушка углеводородного газа
Нефтяные и природные газы, как правило, насыщены водяным паром, что связано с контактом газа и воды в пластовых условиях, а также с условиями их последующей обработки.
Обычно содержание паров воды определяется температурой, давлением и составом газа. Тяжелые углеводородные газы при тех же условиях содержат меньше воды, чем легкие. Присутствие Н2S и СО2 увеличивает влагосодержание, а азота – уменьшает.
Влагосодержание газа – это количество паров воды в состоянии их насыщения в газе (г/м3) при данных температуре и давлении.
Абсолютной влажностью газа называют фактическое содержание паров воды (г/м3).
Относительная влажность газа – это отношение абсолютной влажности к влагосодержанию.
Для удаления паров воды из углеводородного газа проводят его осушку. Качество осушки оценивают по точке росы – температуре, при которой при данном давлении пары воды переходят в состояние насыщения – выпадает конденсат – роса. Чем выше степень осушки, тем ниже точка росы.
Содержание водяных паров в углеводородных газах строго регламентируется, так как при изменении температуры и давления пары могут конденсироваться в аппаратах и трубопроводах и создавать условия для образования твердых кристаллических веществ – гидратов. Последние могут закупоривать рабочее пространство технологических систем и нарушать нормальные условия их эксплуатации.
Кроме того, при наличии воды, а также Н2S и СО2 усиливается коррозия металлических частей аппаратуры.
Гидраты – это кристаллические соединения, существующие в стабильном состоянии. Они не являются химическими соедине-
52
ниями, а по существу представляют собой твердые растворы, растворителем в которых являются молекулы воды, образующие с помощью водородных связей объемный каркас. В полостях этого каркаса находятся молекулы газов, способных к образованию
гидратов (С1–С3, i-С4, Н2S, СО2, N2 и др.).
Для предотвращения гидратообразования широко применяется ингибирование – подача в газовый поток веществ, понижающих температуру гидратообразования (метанол, гликоли и др.), а также осушка углеводородных газов различными методами. В промышленности получили применение три метода осушки: осушка охлаждением, абсорбционнаяиадсорбционная осушки.
Осушка охлаждением. Метод основан на охлаждении углеводородного газа при постоянном давлении. Избыточная влага при этом конденсируется, а точка росы, соответственно, снижается. Нижний предел охлаждения ограничивается условиями образования гидратов. Метод применяется для предварительного удаления основногоколичествавлагивкомбинациисдругимиметодамиосушки.
Абсорбционная осушка. Этот метод осушки основан на селективном поглощении паров воды жидкими абсорбентами, в качестве которых используются простые ди- и триэфиры двухатомных спиртов, например, ди- (ДЭГ) и триэтиленгликоль (ТЭГ).
В общем случае количество влаги, которое можно извлечь данным методом, зависит от гигроскопичности абсорбента, температуры, давления, эффективности применяемых контактных устройств, массы абсорбента и его вязкости.
Рассмотрим технологическую схему процесса абсорбционной осушки газа ДЭГ или ТЭГ (рис. 4.12). Согласно схеме исходный влажный газ поступает в абсорбер 1, где контактирует с гликолем (t = 30…40 С, Р = 10…12 МПа). С верха абсорбера уходит осушенный газ, а насыщенный абсорбент – через дегазатор 2, в котором происходит отдув поглощенных УГ, и через теплообменник 6 поступает в десорбер 3, где при t = 160 С (для ДЭГ) или t = 190 С (для ТЭГ) и Р = 0,2…0,3 МПа вода испаряется и выводится с верха десорбера 3. Регенерированный гликоль (кон-
53

центрация 95–97 %) после охлаждения в теплообменнике 6 и в холодильнике 5 направляется вновь в абсорбер 1.
Рис. 4.12. Технологическая схема абсорбционной осушки газа ДЭГ или ТЭГ: 1 – абсорбер; 2 – дегазатор; 3 – десорбер; 4 – дожимной компрессор; 5 – холодильники; 6 – теплообменник; 7 – кипятильник; I – исходный влажный газ; II – сухой газ; III – регенерированный гликоль; IV – вода; V – насыщенный абсорбент
Глубина осушки газа существенно зависит от концентрации гликоля на входе в абсорбер. Однако термическая десорбция воды не позволяет достичь концентрации гликоля выше 97 % из-за того, что при соответственно 164 и 206 С ДЭГ и ТЭГ разлагаются. При данной концентрации гликоля точка росы газа после осушки снижается не более чем на 30 С (депрессия точки росы). Если концентрация гликоля на входе в абсорбер будет достигать 99 %, то депрессия точки росы составит 40 С. Применение гликоля такой концентрации обеспечивает точку росы от –5 до –25 С. Для углубления осушки газа используют регенерацию гликоля под вакуумом, что позволяет достичь осушки до –40 С (точка росы) – концентрация гликоля 99,8–99,9 %.
Максимально возможной точки росы можно достичь при использовании двухступенчатой абсорбционной осушки: на первой ступени применение абсорбента концентрации 95–97 %,
54
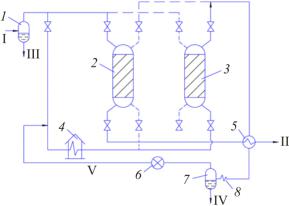
а на второй ступени применения гликоля с концентрацией
99,5–99,7 % (доосушка).
Адсорбционная осушка. Сущность метода состоит в избирательной адсорбции молекул воды поверхностью твердых тел определенной структуры, с последующей десорбцией воды при повышенной температуре и пониженном давлении.
Рис. 4.13. Принципиальная схема адсорбционной осушки газа: 1, 7 – сепараторы; 2, 3 – адсорберы (десорберы); 4 – печь; 5 – теплообменник; 6 – компрессор; 8 – холодильники; I и II – исходный и осушенный газ; III – углеводороды и влага; IV – вода; V – рециркулирующий десорбцирующий газ
Принципиальная схема установки представлена на рис. 4.13. Согласно схеме исходный газ поступает в сепаратор 1, где освобождается от конденсата воды и углеводородов, и далее идет в адсорбер 2, где осушается и выходит с установки через теплообменник 5. Процесс адсорбции идет при t = 35…50 С и Р = 8…12 МПа, длительность контакта газа с адсорбентом не менее 10 с (скорость газа в аппарате 0,15–0,30 м/с). Десорбция воды с поверхности адсорбента идет за счет нагрева его до 200–250 С (силикагель) или 300–350 С (цеолит) частью потока горячего газа, после прохождения им печи 4. Далее горячий газ с парами воды из ад-
55
сорбера 3 поступает в теплообменник 5, холодильник 8, сепаратор 7, где отделяется конденсат воды, и далее через компрессор 6 возвращается в газовый поток. После регенерации адсорбент охлаждается потоком исходного газа.
В качестве адсорбентов нашли применение бокситы, активированные бокситы, силикагель, цеолиты.
Использование адсорбционной осушки целесообразно, если требуется высокая степень осушки: точка росы –85…–100 С.
Данная схема работает по варианту с открытым циклом регенерации адсорбента – регенерация и охлаждения адсорбента идет частью потока исходного газа.
В схемах с закрытым циклом регенерации адсорбента применяют десорбцию сухим газом, циркулирующим по замкнутому циклу, а охлаждение адсорбента ведут сухим газом, покидающим установку.
При наличии большого количества водяных паров в газе используют двухступенчатую осушку: сначала поглощение воды гликолями(первая ступень), азатем адсорбентом(вторая ступень).
56
5.МЕТОДЫ ПЕРЕРАБОТКИ УГЛЕВОДОРОДНЫХ ГАЗОВ
Всоставе природного газа присутствуют углеводороды от С1 до С5, причем углеводороды от С3 и выше в составе газа не желательны, хотя являются ценными компонентами и могут быть использованы по другим направлениям. В связи с этим до подачи природного газа в магистральные трубопроводы из него должны быть
удалены углеводороды от С2 (частично) до С5. Эта смесь называется газовым бензином и разделяется на установке газофракционирования наотдельныеуглеводородыи стабильный газовый бензин.
К основным технологическим методам извлечения тяжелых углеводородов из газа относятся низкотемпературная сепарация (НТС), низкотемпературная конденсация (НТК) и масляная абсорбция (высокое давление и низкая температура). Значительно реже для этих целей применяют адсорбцию.
5.1. Извлечение тяжелых углеводородов из газа методом низкотемпературной сепарации
Сущность процесса низкотемпературной сепарации состоит в однократной конденсации углеводородов при пониженной температуре газа (–25…–30 С) за счет его дросселирования через клапан (изоэнтальпийный процесс). Может быть использовано расширение газа в турбодетандере(изоэнтропийный процесс).
Степень конденсации каждого углеводорода зависит от температуры и давления. Рассмотрим схему НТС газа (рис. 5.1).
Согласно схеме исходный газ под давлением (до 8–12 МПа) поступает в сепаратор 1-й ступени (1), где от него отделяется тяжелый конденсат. Далее газ через теплообменники (8), охлаждаемые газом и конденсатом 2-й ступени сепарации поступает в дроссельное устройство (4), где давление снижается до 4–5 МПа, температура снижается, и высококипящие углеводороды конденсируются. Конденсат отделяется в конденсаторе 2-й ступени (2), а отсепарированный газ идет потребителю. Конденсат дополнительно разделяется в сепараторе (3) иидетв блокстабилизации конденсата (6).
57

Рис. 5.1. Принципиальная схема процесса низкотемпературной сепарации (НТС): 1, 2 – сепараторы 1-й и 2-й ступеней; 3 – сепараторы сырого конденсата; 4 – дроссельные клапаны (детандеры); 5 – холодильная машина; 6 – блок стабилизации конденсата; 7 – блок регенерации ингибитора гидратообразования; 8 – теплообменники; I и II – исходный и отсепарированный газ; III – газовый бензин; IV – конденсат сырого
газа; V – раствор ингибитора гидратообразования
Степень конденсации каждого углеводорода зависит от температуры и давления. Так, при –40 С достигается почти полная конденсация бутанов и пентана, а этан и пропан конденсируются только на 50 и 79 % соответственно (Р = 3,5 МПа).
Поскольку процесс НТС протекает при низких температурах, в поток газа вводят ингибитор гидратообразования. В качестве последнего используют метанол или гликоли, которые связывают влагу из газа после регенерации (дегидратации) в блоке 6 и возвращаются в процесс.
Важнейший параметр НТС – исходное давление газа из скважины, которое со временем (по мере выработки месторождения) снижается, при этом одновременно снижается содержание в газе тяжелых углеводородов и падает потенциал природной энергии для реализации процесса НТС. В этом случае перед сепаратором первой
58
ступени устанавливают дожимной компрессор или в точке дросселирования газа помещаютхолодильную машину (5).
Извлечение углеводородов из газа методом НТС в значительной мере определяется составом исходного газа. Для обеспечения нужного уровня извлечения жидких углеводородов необходимо поддерживать высокое давление и низкую температуру, что не всегда удается из-за сильного снижения давления газа в системе. В этом состоит основной недостаток процесса НТС, поэтому схемы НТС заменяют на схемы низкотемпературной конденсации (НТК), отличающиеся более низкими температурами охлаждения газа (–90…–120 С).
5.2. Извлечение тяжелых углеводородов из газа методом низкотемпературной конденсации
Процесс НТК получал развитие, когда повысился спрос на этан как сырье для нефтехимии. Это потребовало перейти на низкие температуры охлаждения газа. Это в свою очередь потребовало наряду с эффектом дросселирования применять искусственное охлаждение с использованием пропанового (до –70 С) холода или каскадного холодильного пропан-этанового цикла, с помощью которого стало возможно извлекать из газа 85–87 % этана, 99 % пропана и 100 % всех остальных углеводородов.
Для получения искусственного холода используют обычно компрессорные холодильные машины, хладагентом в которых выступает пропан, этан или фреон, а также турбодетандеры, в которых энергия расширяющегося газа рекуперируется для производства холода. Рассмотрим схему НТК (рис. 5.2).
Согласно схеме предварительно осушенный газ охлаждается
врекуперативных теплообменниках (8) и после отделения от него
всепараторе (2) сконденсированных углеводородов через детандер (3) поступает в колонну (4). В нее же из теплообменника (8)
поступает смесь сконденсированных углеводородов (от С2 и выше), а деэтанизированный газ с верха колонны (4), пройдя тепло-
59
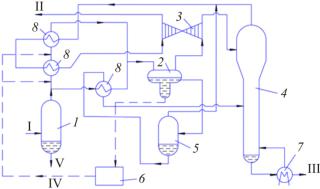
обменник (8), сжимается в турбодетандере (3) и идет к потребителю. ШФЛУ направляется на ректификацию, где отделяется С2 (87–90 %) и остальные углеводороды.
Рис. 5.2. Принципиальная схема процесса низкотемпературной конденсации (НТК): 1, 2 – сепараторы 1-й и 2-й ступеней; 3 – турбодетандер; 4 – ректификационная колонна; 5 – выветриватель конденсата; 6 – блок регенерации ингибитора гидратообразования; 7 – ребойлер; 8 – теплообменники; I и II – исходный и очищенный газ; III – ШФЛУ; IV – ингибитор
гидратообразования; V – конденсатсырогогаза
5.3. Маслоабсорбционное извлечение тяжелых углеводородов из газа
Это один из массовых процессов извлечения из газа тяжелых углеводородов. Сущность его состоит в поглощении тяжелых углеводородов абсорбентом (маслом) с последующей их десорбцией путем отпарки из абсорбента. В качестве абсорбента используют обычно керосиновую или дизельную фракцию нефти со средней молекулярной массой 140–200.
Типичная принципиальная схема масляной абсорбции приведена на рис. 5.3.
Согласно схеме исходный газ охлаждается в охладителях (1, 2), разделяется в сепараторе (3) и поступает в абсорбер (4), где извлекается основная масса тяжелых углеводородов. Насыщенный абсор-
60