
книги / Получение модифицированной порошковой целлюлозы
..pdf6. Технология получения порошковой
имикрокристаллической целлюлозы
6.1.Стадии переработки волокнистого сырья
Наиболее распространенным способом получения порошковой и микрокристаллической целлюлозы является кислотный гетерогенный гидролиз. Ниже приведены традиционные стадии получения порошковой целлюлозы (в качестве примера принято производство ПЦ на заводе им. С.М. Кирова).
Процесс получения порошковой целлюлозы методом кислотного гидролиза состоит из следующих стадий:
–гидролиз волокнистой целлюлозы с получением целлюлозного порошка;
–промывка порошковой целлюлозы и ее сгущение;
–измельчение сгущенных крупных фрагментов (комков) целлюлозы на отдельные мелкие фракции (протирка целлюлозы);
–сушка порошковой целлюлозы;
–сортирование;
–переработка отходов сортирования;
–упаковка.
В данном случае порошковая целлюлоза предназначена для использования в фармацевтической, пищевой и медицинской промышленности, поэтому всё оборудование для производства порошковой целлюлозы должно быть выполнено из пищевой нержавеющей стали марки 08Х18Н10.
Сырье для получения целлюлозного порошка. При получе-
нии порошковой целлюлозы, которая будет использоваться для медицинских, фармацевтических и пищевых целей, в качестве сырья должна быть химически чистая целлюлоза с минимальным содержанием нецеллюлозных примесей. К таким видам исходного волокнистого сырья относятся хлопковая и древесная целлюлоза для химической переработки.
В настоящее время производство древесной целлюлозы для химической переработки в России приостановлено, а хлопковая цел-
41
люлоза является импортным сырьем и часто поставляется на российский рынок неудовлетворительного качества. В этом случае исходным волокнистым сырьем для получения порошковой целлюлозы является древесная целлюлоза для химической переработки, гидролизующим агентом – азотная кислота.
Гидролиз древесной целлюлозы. Кислотный гетерогенный гидролиз целлюлозы заключается во взаимодействии волокнистого сырья с водными растворами минеральных кислот (серной, азотной, соляной) при повышенной температуре. При этом разрушаются гликозидные связи в аморфных участках микрофибрилл целлюлозы, в результате чего снижается степень полимеризации целлюлозы, и они приобретает порошкообразную форму.
Гидролиз целлюлозы проводится в химическом реакторе с паровой рубашкой, снабженном вертикальным перемешивающим устройством.
К настоящему времени разработано множество режимов гидролиза целлюлозы.
В рассматриваемом примере условия получения порошковой целлюлозы: температура 95 °С, продолжительность 90 мин, гидромодуль 15:1, концентрация азотной кислоты 6 %.
Полученная в результате гидролиза порошковая целлюлоза направляется на промывку. В процессе промывки целлюлозного порошка образуется значительное количество кислых стоков, так как процесс получения порошковой целлюлозы осуществляется растворами минеральных кислот.
Процесс промывки целлюлозного порошка преимущественно осуществляется по методу «отжим – разбавление – отжим» с противоточным использованием оборотного раствора.
Для отжима порошковой целлюлозы часто используются шнековые центрифуги, которые характеризуются высокой производительностью, продолжительным сроком службы, исключительной эксплуатационной надежностью, возможностью быстрой и точной настройки в случае изменения технологических условий. На центрифугах порошок сгущается до влажности 40–45 %, разбавление сгу-
42
щенной порошковой целлюлозы с получением суспензии осуществляется (в промежуточных емкостях с перемешивающим устройством) до концентрации 3–4 % и суспензия вновь подается на сгущение.
Протирка влажной порошковой целлюлозы после центрифуг необходима для разрушения крупных комков влажного материала, поступающего на сушку, что способствует обеспечению оптимального режима сушки данного продукта. В результате протирки агломераты из частиц порошковой целлюлозы разрушаются до размеров не более 1 мм.
Оптимальная влажность целлюлозного порошка, поступающего в протирочную машину, составляет 55–70 %. При влажности продукта, загружаемого на сушку, более 70 % увеличиваются продолжительность процесса сушки и расход энергии на сушку. Понижение влажности целлюлозы менее 55 % вызывает уменьшение производительности протирочной машины, закупоривание отверстий перфорированной поверхности продуктом.
В процессе сушки формируются эксплуатационные характеристики готового продукта: плотность порошковой целлюлозы, пористость целлюлозного порошка, водоудерживающая и сорбционная способности. Возможные способы сушки порошковой целлюлозы: сушка вымораживанием, распылением в конвективных сушилках, сушка в вакууме, сушка в печи и весьма перспективный способ – аэрофонтанная (пневмотранспортная) сушка.
Последний способ сушки имеет следующие преимущества перед другими видами сушки:
–сушка порошковой целлюлозы в потоке воздуха при транспортировке ее через сушильную установку позволяет сохранить свойства целлюлозы благодаря отсутствию ороговения поверхности
еечастиц;
–низкая металлоемкость и простота эксплуатации;
–высокий уровень автоматизации процесса транспортировки;
–создание удовлетворительных гигиенических условий в помещениях из-за герметичности и бесшумности системы.
Сушить порошковую целлюлозу рационально при температуре
90–95 °С.
43

Следующей стадией получения порошковой целлюлозы является сортирование высушенного целлюлозного порошка. Сортирование проводится с целью отделения частиц размером более 315 мкм от фракции с требуемым размером. Для сортирования порошковой целлюлозы используется вибрационная сортировка.
Достоинства вибрационной сортировки: оптимальная эффективность рассева; высокая надежность; работа в непрерывном режиме; низкая энергоемкость; низкие динамические нагрузки на основание.
Отходы сортирования вновь возвращаются на гидролиз. Готовый продукт затаривается в мешки, отправляется на склад
и далее потребителю.
6.2. Варианты технологических схем
На рис. 7 и 8 приведены варианты технологических схем получения порошковой и микрокристаллической целлюлозы.
Рис. 7. Вариант производства МКЦ, используемой в качестве наполнителя в бумажном производстве: 1 – автоклавы; 2 – накопитель; 3 – центрифуга; 4 – промывочная емкость; 5 – водоотжимный агрегат; 6 – рыхлитель; 7 – транспортер (элеватор, пневмотранспорт); 8 – циклонные сушилки; 9 – циклон; 10 – размалывающееустройство; 11 – фракционатор; 12 – газодувка,
13 – теплообменник, 14 – скруббер
44
Технологический процесс получения МКЦ, представленный на рис. 7, состоит из следующих стадий:
–подготовка сырья (беленой облагороженной древесной или хлопковой целлюлозы), состоящая из предварительного разрыхления и подачи на гидролиз;
–приготовление кислотной смеси необходимой концентрации;
–загрузка емкостей (автоклавов) для гидролиза: сначала за-
ливают в автоклав 1/2 требуемого объема раствора кислоты, затем при работающей мешалке загружают порциями навеску целлюлозы
идоливают в автоклав оставшийся объем кислоты;
–гидролиз целлюлозы в автоклавах по приведенному вари-
анту схемы осуществляется по следующему режиму:
• масса целлюлозы, загружаемой в автоклав, кг |
............... 220–300 |
• гидромодуль ванны ............................................................ |
15…20 |
• температура гидролиза, °С ............................................ |
115…140 |
• избыточное давление, МПа .............................................. |
0…0,29 |
• массовая доля азотной кислоты, мас.% ........................... |
0,5–3,5 |
• продолжительность гидролиза, мин .................................... |
2…8; |
–отжим порошковой целлюлозы после гидролиза – отделение от гидролизата на центрифуге;
–промывка целлюлозы до значений рН 5–7 для удаления из МКЦ оставшейся кислоты проводится путем разбавления целлюлозной массы водой в промывочной емкости с последующим сифонированием промывных вод после отстаивания порошковой суспензии
втечение 3–4 ч;
–отжим целлюлозы до влажности 50 % проводится на барабанном или ленточном вакуум-фильтре;
–рыхление влажной целлюлозы на частицы 2–4 мм в рыхли-
теле;
–сушка порошка на пневмосушильной установке с сушильными камерами циклонного типа;
–измельчение МКЦ на различных типах мельниц – шестеренчатой, роторно-пульсационной или шаровой;
45
–рассев измельченной целлюлозы на специальных рассевах-
фракционаторах, позволяющих получать МКЦ соответствующего фракционного состава;
–фасовка, упаковка, маркировка.
На рис. 8 приведена схема получения порошковой целлюлозы для пищевой, фармацевтической и медицинской промышленности, технология которой реализована на заводе им. С.М. Кирова. Технология и условия всех процессов разработаны на кафедре ТЦБП ПНИПУ.
Волокнистая целлюлоза кипами через загрузочный бункер подается в шредер (1) для измельчения и разрыхления кип целлюлозной папки. Далее по ленточному транспортеру (2) целлюлоза подается в установку «Диспергатор», где происходит роспуск разрыхленной целлюлозной папки на отдельные волокна. Затем распущенная целлюлоза уносится потоком воздуха, создаваемым вентилятором (4), и выбрасывается в циклон (5). Для более полного улавливания волокна, уносимого с потоком воздуха, дополнительно установлен циклон (5'). Из циклонов 5, 5' целлюлоза поступает в бункер для распущенной целлюлозы (6) и шнековым транспортером, расположенным на дне бункера, подается в реактор для гидролиза (9).
В качестве деструктирующего агента в процессе гидролиза используется водный раствор азотной кислоты. Концентрированная азотная кислота с помощью дозатора (8) подается из мерника кислоты вбак для приготовления разбавленного раствора кислоты (7), откуда готовыйрастворнасосом(35) подаетсявреактордлягидролиза(9).
Для поддержания необходимой температуры в реакторе предусмотрена подача пара в паровую рубашку (10).
Условия гидролиза целлюлозы (температура, продолжительность) принимаются на основании требований к готовому продукту. Гидромодуль процесса (15–20):1.
Обозначения к технологической схеме получения порошковой целлюлозы
1– шредер;
2– ленточный транспортер;
3– диспергатор;
46
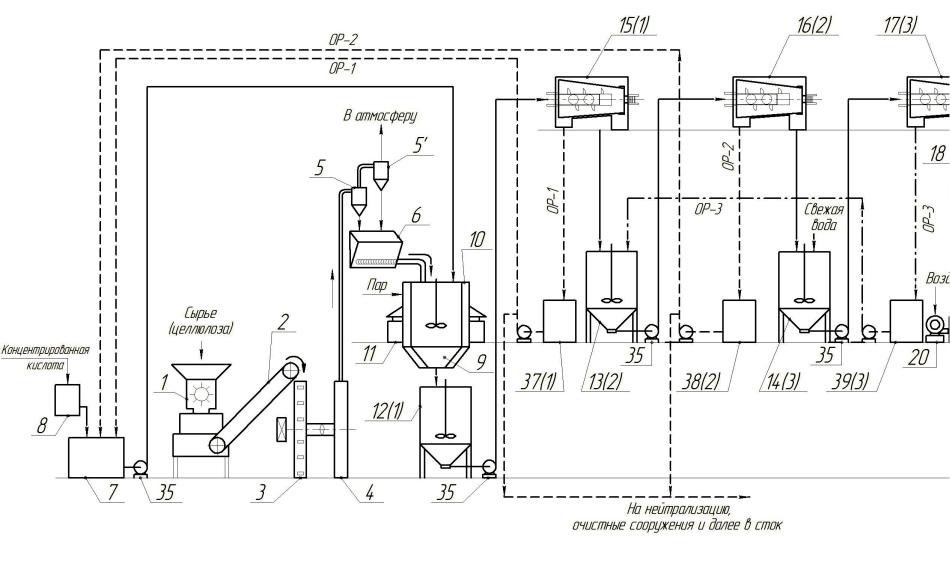
Рис. 8. Технологическая схема получения порошковой целлюлозы

4 – вентилятор;
5, 5ʹ – циклон;
6– бункер для распушенной целлюлозы;
7– бак для раствора кислоты;
8– дозатор концентрированной кислоты;
9– реактор;
10– паровая рубашка;
11– весомер;
12(1) – промежуточная емкость после реактора ;
13(2) – промежуточная емкость после первой ступени отжима;
14(3) – промежуточная емкость после второй ступени отжима;
15(1) – шнековая центрифуга первой ступени;
16(2) – шнековая центрифуга второй ступени;
17(3) – шнековая центрифуга третьей ступени;
18– протирочный барабан;
19– питательный рукав;
20– вентилятор;
20ʹ – вентилятор холодного воздуха;
21– воздухоподогреватель;
22– сушильная труба 1 ступени;
23– перепускная труба;
24– сушильная труба 2 ступени;
25– сушильная труба 3 ступени;
26– циклон;
26ʹ – рукавный фильтр;
27, 27' – циклоны охладительной системы;
28 – сортировка;
29 – накопитель отходов;
30– бункер сортированной порошковой целлюлозы;
31– весы-дозатор;
32– мешок с порошковой целлюлозой на упаковку; 33, 36 – ленточные транспортеры;
34– мешкозашивочная машина;
35– центробежный насос;
37(1) – сборник оборотной воды после первой ступени отжима;
48
38 (2) – сборник оборотной воды после второй ступени отжима; 39 (3) – сборникоборотнойводыпослетретьейступениотжима; ОР-1 – крепкий оборотный раствор с центрифуги № 1; ОР-2 – слабый оборотный раствор с центрифуги № 2; ОР-3 – очень слабый оборотный раствор с центрифуги № 3.
Реактор снабжен весомером (11) для контроля количества подаваемой на гидролиз целлюлозы.
После окончания процесса гидролиза порошковая целлюлоза в виде суспензии порошка с концентрацией 5–6 % через промежуточную емкость 12 (1) насосом (35) подается на промывку. Промывка осуществляется в две ступени по принципу отжим – разбавление – отжим. Для этого суспензия подается на шнековую центрифугу 15 (1) для отжима до концентрации ~ 40–45 % и отделения от целлюлозы отработанного гидролизующего раствора. Далее сгущенный порошок поступает в промежуточную емкость 13(2), где разбавляется до концентрации 3–4 % оборотным раствором – ОР-3 из бака оборотной воды 39 (3). Из сборника водная суспензия порошка насосом (35) перекачивается в шнековую центрифугу 16 (2) для отжима до концентрации 40–45 %. Сгущенный порошок направляется в промежуточную емкость 14 (3), где разбавление осуществляется свежей водой до концентрации 3–4 %. Оборотный раствор – ОР-2 из бака оборотной воды 38 (2) поступает частично на приготовление кислоты для гидролиза, а остаток – на нейтрализацию и далее на очистные сооружения.
Оборотный раствор – 1 (ОР-1) из бака оборотной воды 37 (1) направляется в бак (7) на приготовление раствора кислоты для гидролиза (90–95 % от общего объема ОР-1), а остаток (5–10 %) – на нейтрализацию и очистные сооружения.
Из промежуточной емкости 14 (3) порошковая суспензия насосом (35) подается для отжима на шнековую центрифугу 17 (3), откуда с концентрацией 40–45 % поступает в протирочный барабан (18), а затем по питательному рукаву (19) целлюлозный порошок поступает в трубу, по которой воздухом, подаваемым вентилятором (20) и подогреваемым в воздухоподогревателе (21) свежим паром, подается на сушку.
49