
книги / Общая химическая технология. Лабораторный практикум
.pdf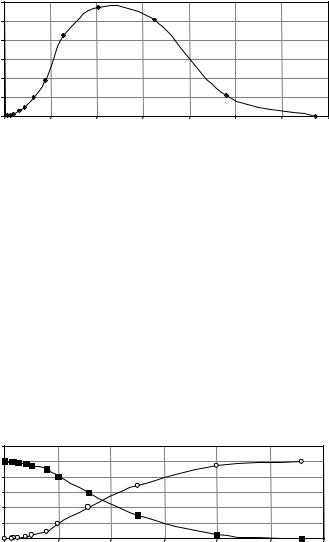
Содержание кристаллов |
|
30 |
|
|
|
|
|
|
|
|
25 |
|
|
|
|
|
|
|
|
во фракции, % |
20 |
|
|
|
|
|
|
|
|
15 |
|
|
|
|
|
|
|
||
10 |
|
|
|
|
|
|
|
||
5 |
|
|
|
|
|
|
|
||
0 |
|
|
|
|
|
|
|
||
|
|
0 |
0,4 |
0,8 |
1,2 |
1,6 |
2 |
2,4 |
2,8 |
|
|
|
|
Средний размер зерен, мм |
|
|
|
Рис. 1. Дифференциальная кривая распределения частиц по размерам
По виду дифференциальной кривой можно определить преобладающую фракцию зерен, соответствующую максимуму, а также долю этой фракции в общей массе материала. Чем однороднее по размерам частиц исследуемый материал, тем больше доля этой фракции. Сыпучие материалы, близкие к монодисперсным, дают острый и длинный пик. Гранулометрический состав неоднородных полидисперсных материалов обычно изображается на дифференциальных кривых в виде одного или нескольких широких пиков.
На рис. 2 представлены интегральные кривые распределения кристаллов по размерам.
мм, |
120 |
|
|
|
|
|
|
кристаллов, |
100 |
|
|
|
|
|
2 |
80 |
|
|
|
|
|
||
|
|
|
|
|
|
||
60 |
|
|
|
|
|
|
|
40 |
|
|
|
|
|
|
|
Содержание |
|
|
|
|
|
|
|
20 |
|
|
|
|
|
1 |
|
0 |
|
|
|
|
|
||
|
|
|
|
|
|
||
0 |
0,4 |
0,8 |
1,2 |
1,6 |
2 |
2,4 |
|
|
|
Размер отверстий сита, мм |
|
|
|||
Рис. 2. Интегральные кривые распределения кристаллов по размерам: |
|||||||
|
|
1 – кривая остатков, 2 – кривая проходов |
|
|
51

Две интегральные кривые являются зеркальным отражением друг друга и имеют S-образную форму. Первая кривая показывает, какая часть или доля от общей массы пробы остается на сите данного размера, вторая кривая показывает, какая доля от всей навески порошка проходит через сито данного размера.
По данным гранулометрического анализа можно определить величины, характеризующие среднюю крупность и однородность зернистого материала.
Для характеристики средней крупности пробы рассчитывают средневзвешенный размер D (мм), который можно определить методом аддитивности из соотношения
D – m1d1 + m2d2 + … + mndn = midi,
где m1, m2, …, mn – содержание каждой фракции в образце, мас. доли; d1, d2, …, dn – средний размер кристаллов этих фракций, мм.
Для характеристики однородности дисперсного образца используют так называемый коэффициент отклонения K0. Чем меньше коэффициент отклонения, тем однороднее продукт. Для расчета K0 используют интегральную кривую проходов. Для определения коэффициента отклонения K0 из общей массы исследуемого образца отбрасывается по 16 % наиболее мелких и наиболее крупных фракций и в расчет принимается только 2/3 материала. По графику, характеризующему кривую проходов, определяют размер отверстий, через которые проходит 16, 50 и 84 % проанализированной пробы, т.е. три величины d16, d50 и d84 (мм). Коэффициент отклонения определяют по формуле
K0 d84 d16 100%.
2d50
52
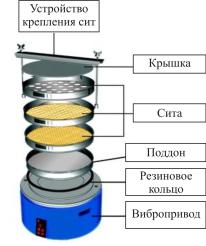
3. Экспериментальная часть
Химические реактивы
Для определения дисперсных характеристик могут быть использованы различные твердые сырьевые материалы, а также готовые кристаллические и гранулированные продукты. По указанию преподавателя для исследования могут быть взяты: гранулированные удобрения (суперфосфат, карбамид, хлорид калия), молотые природные руды (хромит, сильвинит, карналлит), различные химические продукты (отработанный электролит, флотационный и галургический хлорид калия и другие соли).
Описание установки и методика проведения работы
Схема лабораторной установки для определения гранулометрического состава дисперсных материалов приведена на рис. 3.
Рис. 3. Лабораторная установка для определения гранулометрического состава дисперсных материалов
53
Чтобы анализ достоверно отражал дисперсный состав порошкообразного материала, отобранная для анализа проба должна правильно представлять материал. Представительность пробы обеспечивается соответствующим отбором ее из массы материала и надлежащей подготовкой к анализу. При колебаниях характеристик порошкообразных материалов необходимо провести анализ нескольких образцов. Иногда ограничиваются средней пробой.
Исследуемый материал осторожно, избегая потерь, высыпают конусом на гладкий лист. Если проба имеет высокую дисперсность, то ее высыпают на лист с помощью воронки, конец которой находится вблизи поверхности листа, а при нарастании конуса плавно поднимается без сдвига в сторону. Для перемешивания материал набирают шпателем снизу конуса и высыпают на вершину так, чтобы он распределялся равномерно по всем сторонам. После многократного перемешивания по всей окружности основания конуса пробу квартуют. Конус делят на четыре части крестообразным делителем. Две противоположные четверти удаляются, а оставшиеся две перемешиваются между собой. Перемешивание, квартование и удаление части пробы повторяют до тех пор, пока оставшаяся масса не достигнет желаемой величины.
Для рассева брали твердый сырьевой материал в виде гранулированного удобрения (суперфосфат, карбамид, хлорид калия), молотой природной руды (хромит, сильвинит, карналлит), различных химических продуктов (отработанный электролит, флотационный и галургический хлорид калия и другие соли), определяли его массу. Навеска пробы для определения гранулометрического состава берется на технических весах с точностью 0,01 г. Затем этот материал помещали на верхнее сито, все закрепляли и включали виброгрохот. После окончания рассева определяли массу каждой фракции с точностью до трех знаков после запятой на аналитических весах. Материал маленького размера, при-
54

липший к ситу, с помощью кисточки собирали и добавляли к соответствующей фракции. Затем, после определения массы всех фракций, рассчитывали процентное содержание каждой фракции в грануляте.
4. Обработка результатов
Рассчитав суммарную массу всех фракций, определяют долю каждой фракции в общей массе и потери материала при рассеве по отношению к исходной навеске, взятой на анализ.
Гранулометрический состав в процентах выражают отношением массы каждой фракции к суммарной массе всех фракций. Допустим, на сите 2 мм выделена фракция зерен, прошедших через сито размером 3 мм. Значит, размер зерен этой фракции меньше 3 мм и больше 2 мм, т.е. средний диаметр частиц 2,5 мм. Обозначим массу указанной выше фракции через g2,5 (г), а общую массу всех фракций – G (г), тогда массовая доля этой фракции (в %)
m2,5 gG2,5 100%.
Точность ситового анализа определяется тщательным соблюдением правил отбора средней пробы, условий просеивания, исключением потерь, а также физическими свойствами материала и размерами фракций.
Результаты ситового анализа целесообразно представить в виде табл. 2.
Результаты расчетов процентного содержания отдельных фракций зерен в исследуемом материале являются дифференциальной характеристикой гранулометрического состава образца. Их заносят в табл. 2 и используют для расчета интегральных характеристик гранулометрического состава.
55
Таблица 2
Результаты ситового анализа
Номер |
Размер |
Размер |
Масса |
Масса |
Масса |
Содер- |
Средний |
отвер- |
фрак- |
тары, |
тарыс |
фрак- |
жание |
размер |
|
тары |
стий |
ции,мм |
г |
навеской, |
ции, |
фрак- |
зерен, мм |
|
сита,мм |
|
|
г |
г |
ции,% |
|
1 |
|
|
|
|
|
|
|
2 |
|
|
|
|
|
|
|
3 |
|
|
|
|
|
|
|
… |
|
|
|
|
|
|
|
Для расчета доли частиц, оставшихся на каком-либо сите определенного размера, суммируют процентное содержание всех фракций со средним размером зерен более размера ячейки данного сита. При этом доля частиц, прошедших через это же сито, определяют как разность между 100 % и долей оставшихся частиц.
Полученные данные используют для построения дифференциальных и интегральных кривых распределения частиц по размерам.
На основе результатов анализа определяют преобладающий размер зерен, средний размер частиц и однородность дисперсного материала, которая характеризуется коэффициентом отклонения.
По результатам ситового анализа делают выводы о гранулометрической характеристике исследованного дисперсного материала.
Контрольные вопросы
1.Что такое обогащение сырья и для чего его проводят на производстве?
2.Каковы методы обогащения сырья?
56
3.В чем суть ситового анализа?
4.Что показывают интегральные и дифференциальные кривые распределения частиц?
5.На какие показатели влияет гранулометрический состав?
6.Что такое монодисперсный и полидисперсный продукт? Как, пользуясь рис. 1, можно определить монодисперсный или полидисперсный продукт?
Список литературы
1.Коузов П.А. Основы анализа дисперсного состава промышленных пылей и измельченных материалов. – Л.: Химия, 1974. – 278 с.
2.Кутепов А.М., Бондарева Т.И., Беренгартен М.Г. Общая химическая технология: учеб. для вузов. – 3-е изд., перераб. – М.: Академкнига, 2007. – 527 с.
57
Лабораторная работа № 6
ПОЛУЧЕНИЕ ГИДРОКСИДА НАТРИЯ КАУСТИФИКАЦИЕЙ СОДОВОГО РАСТВОРА
1. Цель работы
Исследование зависимости степени каустификации содового раствора от времени процесса, концентрации исходного содового раствора и температуры. Определение констант скорости процесса и энергии активации.
2. Теоретические основы процесса
Гидроксид натрия, или каустическая сода (каустик), широко применяется в производстве искусственных волокон, моющих средств, органических красителей, в бумажном и текстильном производствах, в технологии оксида алюминия, синтетического фенола и др.
Получают гидроксид натрия электрохимическим и химическим способами.
Электрохимический способ осуществляют электролизом водных растворов хлорида натрия. В результате образуется раствор гидроксида натрия, упариванием которого получают раствор либо твердый гидроксид натрия. Побочные продукты – газообразные хлор и водород.
Химические методы – ферритный и известковый, предпочтение отдают известковому способу.
Ферритный способ заключается в смешении сухой соды с измельченным оксидом железа в соотношении 1:3 и прокаливании смеси при температуре 1000 °С. При этом образуется плав – феррит натрия:
58
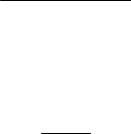
Na2CO3 Fe2O3 Na2O Fe2O3 CO2.
Плав разлагают горячей водой с образованием раствора гидроксида натрия и оксида железа:
Na2O Fe2O3 H2O 2NaOH Fe2O3.
Известковый способ получения NaOH заключается в смешении водных растворов соды и извести (реакция каустификации):
Na2CO3 Ca(OH)2 CaCO3 2NaOH.
Эта реакция является обратимой и при определенных условиях (концентрации, температуре) наступает состояние равновесия, реакция превращения Nа2СО3 в NaOH не доходит до конца. Равновесие реакции определяется соотношением между растворимостями гидроксида и карбоната кальция или значе-
ниями концентраций ионов ОН– и CO32 в растворе. Константа равновесия Kс определяется из следующего соотношения:
|
CaCO3 NaOH 2 |
Kc |
Ca(OH)2 Na2CO3 . |
Поскольку концентрации [СаСО3] и [Са(ОН)2] можно принять постоянными, то константа равновесия будет опреде-
ляться отношением концентраций ионов ОН– и CO32 , т.е.
OH– 2 Kc CO32– .
Степень каустификации, т.е. доля соды, превратившейся в гидроксид, увеличивается с уменьшением концентрации соды в исходном растворе.
При повышении температуры значение константы равновесия уменьшается, так как реакция каустификации являет-
59
ся экзотермической. Следовательно, более полное превращение Nа2СОЗ в NaOH будет наблюдаться в интервале температур 15–20 °С. На практике процесс ведут при температуре 80–100 °С. Повышение температуры способствует увеличению скорости процесса, получению хорошо фильтрующегося осадка.
Скорость процесса зависит от свойств и количества применяемой извести, т.е. размеров частиц, наличия примесей. В качестве примесей известь содержит SiО2, Al2O3, Fе2O3, MgO. Каждая примесь по-разному влияет на процесс, замедляя процесс гашения, уменьшая скорость осаждения шлама. Уменьшение количества примесей улучшает технологический процесс. Интенсивное перемешивание суспензии способствует ускорению процесса растворения гидроксида кальция, что приводит к увеличению скорости процесса.
Таким образом, оптимальными условиями каустификации являются: концентрация соды 250 г/л, температура 80 °С, интенсивное перемешивание. При этом степень каустификации, т.е. отношение количества соды, перешедшей в гидроксид натрия, ко всему ее количеству, участвующему в реакции, дости-
гает 90–95 %.
Технологический процесс производства гидроксида натрия состоит из следующих стадий:
•приготовление известкового молока;
•приготовление содового раствора;
•каустификация содового раствора;
•отделение СаСО3 от раствора;
•упаривание раствора;
•фильтрация щелока и отделение выпавших солей
Nа2СО3 и Na2SО4;
• окончательное упаривание раствора до получения плава
NaOH.
60