
2858.Оборудование литейных цехов учебное пособие
..pdf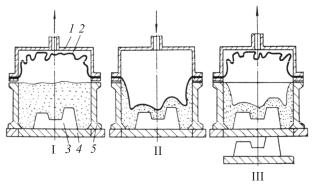
тейных форм гибкой диафрагмой позволяет устранить этот существенный технологический недостаток метода уплотнения прессованием плоской колодкой. Достигается это тем, что гибкая диафрагма (рис. 3.6) под действием сжатого воздуха, впускаемого в головку машины, давит на формовочную смесь в опоке, обжимая и уплотняя ее равномерно со всех сторон модели. Рабочая поверхность диафрагмы обычно превышает площадь опоки на 30–40 %. Давление диафрагмы на смесь, т.е. удельное давление прессования, будет равно давлению в заводской сети – 0,5–0,6 МПа (5–6 кг/см2). Стойкость резиновой диафрагмы толщиной 6 мм составляет ~23000 съемов (формовок).
Рис. 3.6. Уплотнение формовочной смеси резиновой диафрагмой: I – позицияпередначалом прессования; II – прессование; III – выхлоп, подъем диафрагмы, вытяжка модели; 1 – кожух; 2 – резиновая диафрагма; 3 – модель; 4 – подмодельная плита; 5 – опока
Для диафрагменного прессования созданы специальные формовочные автоматы проходного типа, встроенные в автоматическую формовочную линию. Вместе с тем диафрагменное прессование дает практически равномерное уплотнение форм смоделями только при условии больших зазоров между моделью и стенкой опокиимежду соседними моделями (не менее50 мм).
Для диафрагменного прессования применяются смеси как низкой прочности, так и высокой.
31
Широкого применения способ не получил из-за низкой стойкости материала диафрагмы. Кроме головок с эластичными диафрагмами применяют так называемые головки из гидропласта. Такая головка представляет собой конус, закрытый снизу сплошным элементом из пластичного материала (вакуумная резина, гидропаст и др.). Пространство между головками заполнено жидкостью. Напряжения в смеси при воздействии на нее такой колодки также будут одинаковы во всех точках прессующего элемента. Поскольку при прессовании гидропластмассовой колодкой напряжения не концентрируются над выпуклой частью диафрагмы, и жидкость, находящаяся в головке, легко перетекает в места, менее напряженные, то силы трения здесь способствуют перетеканию смеси, и равномерность уплотнения повышается. Эластичные гидропластмассовые головки обладают большей стойкостью по сравнению с диафрагменными.
3.6. Прессующий механизм с многоплунжерной головкой
Уплотнение литейных форм многоплунжерной головкой, так же как и гибкой диафрагмой, обеспечивает более равномерное распределение плотности смеси как вокруг модели, так и по всему объему формы.
Многоплунжерная прессовая головка (рис. 3.7) в зависимости от размеров формы может иметь от 30 до 100 плунжеров, на штоках которых закреплены башмаки – подвижные прессовые колодки, уплотняющие формовочную смесь в опоке. Каждый башмак под действием давления масла осуществляет прессование независимо от других и обжимает смесь как над моделью, так и вокруг нее. Объединяя плунжеры в несколько групп и подавая в каждую масло под различным давлением, можно производить поочередное (раздельное по времени) прессование отдельных полостей форм, обеспечивая тем самым лучшие условия перетекания смеси внутри формы и более равномерное ее уплотнение. Такие плунжерные головки называются активными(рис. 3.9).
32

Рис. 3.7. Уплотнениеформовочнойсмеси |
Рис. 3.8. Устройство |
многоплунжерной прессовой головкой: |
плунжера |
1 – смесь; 2 – модель; 3 – модельная |
|
плита; 4 – опока; 5 – колодка плунжера; |
|
6 – наполнительнаярамка; 7 – плунжер; |
|
8 – масло; 9 – корпус головки |
|
Устройство плунжера показано на рис. 3.8. При прессовании масло поступает по каналу в корпус головки 3 и давит на плунжер 2, перемещая его вместе с башмаками 1 вниз. При этом сжимается пружина 4, которая служит для возврата плунжера в исходное положение после снятия давления масла.
Общее усилие прессования P, передаваемое на смесь в опоке, будет определяться соотношением
P = pм Fплi,
где pм – давление масла в системе, Па; Fпл – активная площадь плунжера, м2; i – количество плунжеров в головке.
Удельное давление прессования под каждым башмаком плунжера
33
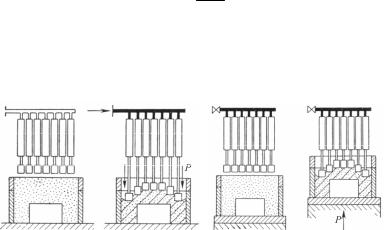
p = pм Fпл ,
Fбаш
где Fбаш — активная поверхность башмака, м2.
При уплотнении форм чистым прессованием с помощью многоплунжерных головок обычно применяют активные прессовые головки.
а |
б |
а |
б |
Рис. 3.9. Принцип работы |
Рис. 3.10. Принцип работы |
||
«активной» многоплунжерной |
«пассивной» многоплунжерной |
||
прессовой головки: Р – сила |
прессовой головки: Р – сила |
||
прессования: а – исходное |
прессования: а – исходное |
||
положение; б – уплотнение |
положение; б – уплотнение |
||
|
смеси |
|
смеси |
Пассивными (рис. 3.10) называются такие прессовые колодки, которые сами не создают усилий прессования, а только передают их смеси. Рабочие полости плунжеров соединены между собой, и масло может перетекать из полости одних плунжеров в полости других. При прессовании в зависимости от степени сопротивления смеси на отдельных участках формы плунжеры изменяют свое положение по высоте, что и обеспечивает равномерность уплотнения.
При разработке конструкций пневматических прессовых машин необходимо предусматривать оснащение их аппаратурой для подготовки воздуха на входе (водоотделителями, маслораспылителями); аппаратурой для стабилизации заданного давления сжатого воздуха (регуляторами давления, редукционными
34

клапанами, реле давления); аппаратурой для защиты механизмов и обслуживающего персонала (обратными клапанами, блокировочными устройствами и др.).
3.7.Рычажно-прессовый механизм
Врычажно-прессовых машинах усилие прессования создается механизмом, представляющим собой сочетание пневматического цилиндра с механическим усилителем рычажного типа
(рис. 3.11).
Рис. 3.11. Схемы работы рычажного прессового механизма: а – перед прессованием; б – в конце прессования; в – механизм рычагов Эйлера; г – механизм рычажного параллелограмма: 1 – прессовый цилиндр; 2 – рычажный механизм; 3 – прессовая плита; 4 – формовочная смесь
Этот механизм (рычаги Эйлера) обеспечивает прогрессирующее увеличение силы прессования по ходу прессовой колодки при постоянном давлении воздуха в прессовом цилиндре. Кроме того, давление прессования здесь увеличивается по сравнению сдавлением воздухав прессовомцилиндрев8–10 раз.
Примером может служить прессовый пневморычажный автомат модели 5833Г (конструкции НИИтракторосельхозмаша), устройство которого приведено на рис. 3.12.
35

Этот формовочный однопозиционный автомат, предназначенный для изготовления литейных форм из песчано-глинистых смесей в опоках 600×900 мм и высотой 175–250 мм методом верхнего прессования с давлением 4 МПа. Усилие, развиваемое прессом, равно 1980 кН, производительность 180 полуформ вчас.
Рис. 3.12. Схема устройства и работы формовочно-прессового автомата
На нижней плите 1 пресса установлены четыре квадратные колонны 9, на которых сверху смонтирована плита 11. На верхней плите крепится пневматический цилиндр 13, шток 14 поршня которого соединен с рычажным механизмом 10. Нижние
36
концы рычагов механизма 10 шарнирно соединены с подвижной плитой 8. На круглых колоннах 6, движущихся в направляющих верхней и нижней плит, укреплена наполнительная рамка 5. Механизм перемещения наполнительной рамки, расположенный в верхней плите, состоит из двух рабочих цилиндров 12 и двух цилиндров обратного хода (на схеме не показаны), штоки поршней которых через зубчатую передачу (на схеме не показаны) связаны кинематически с колоннами 6. В нижней плите 1 размещены механизмы протяжки 2, обдува и опрыскивания модели. С нижней плитой 1 пресса стыкуется основание 21, на котором установлен бункер 15. Под бункером расположен коробчатый дозатор 16, который перемещается горизонтально по опоре 17 пневматическим цилиндром 19. На основании расположен ресивер 22 для питания сжатым воздухом главного цилиндра прессования 13. Под цилиндром 19 привода установлен цилиндр 20, служащий для выкатывания из автомата модельной плиты при ее замене.
При работе автомата опока 4 проталкивается толкателем по полозьям наполнительной рамки 5. Одновременно модельная плита 3 обдувается и опрыскивается. Рабочие цилиндры 12 опускают колонны 6 с наполнительной рамкой 5, и опока ложится на модельную плиту 3, центрируясь по штырям (схема II). Верхний уровень наполнительной рамки 5 оказывается ниже дозатора 16. Дозатор, заполненный смесью, штоком поршня цилиндра 19 перемещается в положение над наполнительной рамкой. При этом шибер 18, соединенный с дозатором 16, закрывает бункер. Смесь из дозатора пересыпается в опоку и наполнительную рамку, а дозатор с остатком смеси возвращается в исходное положение. Сжатый воздух направляется в верхнюю полость прессового цилиндра 13, и шток его поршня рычажным механизмом 10 опускает подвижную плиту 8. Прессовая плита 7 входит в наполнительную рамку и уплотняет смесь (схема III).
Шток прессового поршня жестко соединен с системой рычагов типа двойного рычага Эйлера. При движении штока вниз
37
рычаги 10 расходятся в стороны, а рычаги, соединенные с плитами 8 и 11, поворачиваются, занимая вертикальное положение. Соответственно увеличивается усилие, передаваемое на прессовую плиту, т.е. передаточное отношение, которое в конце хода достигает значения 1:10.
Давление прессования можно уменьшать путем повышения давления в штоковой полости цилиндра 13 в момент прессования. Для плавной остановки прессового поршня в крышках его цилиндра установлены дроссельные клапаны 23 и 24.
При обратном ходе прессового поршня плита 8 поднимается, штыри протяжного механизма 2, двигая вверх полумуфту, вытягивают модель. Специальные цилиндры, расположенные на верхней плите (на схеме не показаны), поднимают наполнительную рамку 5, вместе с ней полуформа перемещается в исходное положение.
Автомат широко применяют для изготовления литейных форм в массовом производстве.
Автомат с рычажно-усилительным механизмом работает надежно и бесшумно. Однако наряду с преимуществом он обладает недостатками. Один из них – невозможность получения форм деталей со значительным перепадом высот. Другим недостатком этих механизмов является их быстрый износ и существенная потеря мощности на трение. Третий существенный недостаток – высокая чувствительность к колебанию влажности смеси: при повышенной влажности имеет место недоуплотнение формы, а при пониженной – переуплотнение. Это объясняется тем, что данная рычажная система имеет всегда один постоянный ход колодки, установленный при наладке (жесткая кинематическая схема рычажного механизма).
Автомат работает в составе автоматической формовочной линии (для отливок массой до 50 кг), успешно эксплуатируемой на многих заводах нашей страны.
38
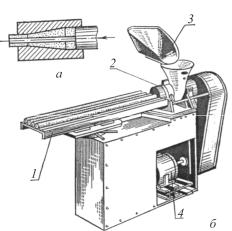
3.8. Мундштучные прессовые машины
Мундштучные прессовые машины (рис. 3.13) предназначаются для формовки цилиндрических и призматических стержней с поперечными размерами 20–100 мм.
Особенностью мундштучных машин является то, что для изготовления стержней не требуется стержневых ящиков. Принцип работы этих машин основан на выдавливании стержневой массы через специальные сменные насадки – мундштуки. Стержни, изготовленные на таких машинах, обладают равномерной плотностью, хорошей газопроницаемостью, высокой прочностью и высококачественной поверхностью.
Рабочим органом у мундштучных машин является плунжер или шнек. В мундштуке устанавливается пруток для создания в стержне вентиляционного канала. После сушки стержни разрезаются на куски требуемой длины.
Мундштучные машины выпускаются одноручьевыми имногоручьевыми.
Рис. 3.13. Мундштучная прессовая машина: а – схема мундштука; б– общийвидмашины; 1 – сушильнаяплита; 2 – сменныймундштук; 3 – лоток; 4 – электродвигатель привода машины
39
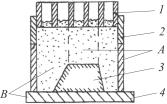
3.9. Прессование решетчатым элементом
На рис. 3.14 представлена схема процесса прессования решетчатой прессовой плитой. Плита-решетка состоит из достаточно прочных стальных пластин, связанных в единую рамку.
При прессовании смесь из наиболее уплотненной области А перетекает в зазоры между пластинами. Решетка тем самым более свободно перемещается в менее уплотненную область В, и плотность смеси по всему объему формы выравнивается. Конечная величина плотности, равномерность ее распределения определяются толщиной ребер, зазорами между ребрами, давлением прессования и свойствами
смеси. Конструкция решетки может быть самой различной: плоская плита с перфорированными отверстиями, плита с вертикальными стержнями, напоминающая многоплунжерную головку без башмаков, и т.д.
Решетчатый прессовый элемент можно применять как при верхнем, так и при нижнем прессовании.
При прессовании решеткой смесь, находящаяся непосредственно под решетками, имеет наибольшую плотность. Снижение плотности и рассеивание напряжений происходит так же, как и под плунжерами многоплунжерной головки в виде усеченных конусов, которые перекрываются конусами (пирамидами) от действия соседних ребер. Таким образом, на некоторой глубине от решетки напряжение и твердость в пределах одного слоя практически заравниваются.
Толщина ребра решетки существенно не влияет на ход процесса. Однако с увеличением толщины ребра неравномер-
40