
2858.Оборудование литейных цехов учебное пособие
..pdf
M = π(R2 − r12 )bγ, g 106
сообщается при каждом обороте скорость, равная полусумме окружных скоростей на радиусе направляющей дуги R и радиусе диска r1, к которому крепится метательный ковш, т.е. сообщается скорость, м/с,
|
|
|
|
|
|
|
uср = |
|
πn R + r1 |
1 |
|
. |
|
|
|
|
|
|
|
|
|
|
|
|
|||||||||||
|
|
|
|
|
|
|
|
30 |
|
|
|
|
2 |
|
|
102 |
|
|
|
|
|
|
|
|
|
|
|
|
|||||||
Таким образом, |
|
|
|
|
|
|
|
|
|
|
|
|
|
|
|
|
|
|
|
|
|
|
|
|
|
|
|
|
|
|
|||||
Nвент = |
Muср2 |
|
n 1 |
|
= |
π(R2 |
− r12 )bγ 1 πn |
|
R + r1 |
2 |
|
1 n 1 |
|||||||||||||||||||||||
|
|
|
|
|
|
|
|
|
|
|
|
|
|
|
|
|
|
|
|
|
|
|
|
|
|
|
|
|
|
|
|
|
|||
2 |
60102 |
|
g |
10 |
6 |
|
|
|
|
2 |
10 |
4 |
60102 |
|
|||||||||||||||||||||
|
|
|
|
|
|
|
2 30 |
|
|
|
|||||||||||||||||||||||||
или, окончательно, |
|
|
|
|
|
|
|
|
|
|
|
|
|
|
|
|
|
|
|
|
|
|
|
|
|
|
|
|
|
|
|||||
|
Nвент = |
|
γb(R − r1) |
|
|
πn R + r1 |
|
3 |
|
|
|
|
(12.8) |
||||||||||||||||||||||
|
|
|
|
|
|
|
|
|
|
|
|
|
|
|
|
|
|
|
|
кВт, |
|
|
|
||||||||||||
|
2g 102 10 |
4 |
|
|
|
|
|
|
|
|
|
|
|
|
|||||||||||||||||||||
|
|
|
|
|
|
|
|
60 100 |
|
|
|
|
|
|
|
|
|
|
|
где γ – удельный вес воздуха, γ = 1,2 кгс/м3; g = 9,81 м/с2; R, r1 и b – размеры, см.
Полезная мощность Nпол (кВт) определяется как кинетическая энергия, сообщаемая пакетам смеси ротором:
Nпол = |
Lδ 1000 v2 |
1 |
, |
||||
|
|
|
|
|
|||
3600g 2 102 |
|||||||
|
|
||||||
или |
|
|
|
|
|
|
|
Nпол = |
Lδv2 |
|
, |
(12.9) |
|||
2g 3,6 102 |
где L – производительность пескомета по уплотненному объему, м3/ч; δ – степень уплотнения набивки формовочной смеси в опоке, г/см3; δ ≈ 1,6 г/см3; v – абсолютная скорость схода пакетов смеси с ротора пескомета, м/с; g = 9,81 м/с2.
При изменении подачи смеси или производительности данного пескомета полная мощность привода головки согласно
231

опытным данным [9] изменяется по закону прямой линии. Так, для головки с ротором диаметром 2R = 620 мм при n = 1460 об/мин изменение мощности в диапазоне производительности L0 = = 5…25 т/ч происходило по следующей эмпирической закономерности: N = 7,5 + 0,57L0 кВт.
Как показывают расчеты, в пескометах с головками обычной конструкции, имеющих подачу смеси на ротор в осевом направлении, средний расход мощности на трение пакетов смеси о направляющую дугу составляет 0,4–0,5 суммарной мощности привода ротора. Поэтому существенное значение имеет уменьшение работы трения смеси о дугу путем изменения места осевого ввода с сокращением центрального угла направляющей дуги либо путем применения подачи в других направлениях.
Общая теория ротора с прямой нерадиальной лопаткой.
Начиная с момента, когда вращающаяся лопатка ротора пескомета пройдет направляющую дугу кожуха головки, пакет формовочной смеси под действием центробежных сил будет скользить вдоль лопатки по направлению от центра к периферии и через некоторое время, дойдя до выходной кромки лопатки, будет ею выброшен с ротора.
Рис. 12.5. Схема движения твердой частицы по лопатке ротора
232

Рассмотрим движение твердой частицы по лопатке вращающегося ротора (рис. 12.5). В исходном положении, в точке 1, в некоторый нулевой момент времени частица с массой m имеет начальную скорость w1 по лопатке ab и координату x1. Требуется найти текущую скорость частицы по лопатке w и текущую координату x частицы в некоторой точке 2, куда частица в течение t, с, переместится по вращающейся лопатке под действием центробежной силы.
Принимая во внимание геометрические соотношения
r = |
x2 + r 2 , |
|
|||||
|
|
|
|
|
|
н |
|
sin γ= |
rн |
= |
|
rн |
, |
||
|
r |
x2 + rн2 |
|||||
|
|
|
|
|
|||
cosγ= |
x |
|
= |
|
x |
, |
|
r |
|
x2 + rн2 |
|||||
|
|
|
|
|
можно написать выражения для действующих на частицу сил
втекущей точке 2:
1)центробежная сила
P = mω2r = mω2 |
x2 + r2 |
; |
ц |
н |
|
2) составляющая этой силы по лопатке
Pц cosγ= mω2 x;
3)составляющая центробежной силы, перпендикулярной
клопатке,
Pц sin γ= mω2rн;
4) силы Кориолиса
Pк = 2mωdxdt ;
233
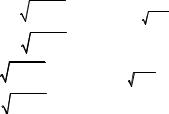
5) силы трения частицы о лопатку
P |
= f (P − P sin γ) = mf |
|
2ωdx |
− ω2r |
|
, |
тр |
к ц |
|
dt |
н |
|
|
|
|
|
|
|
|
где f – коэффициент трения частицы о лопатку.
Силой тяжести частицы пренебрегаем вследствие малой ее величины по сравнению с остальными действующими силами. Уравнение движения частицы по лопатке выглядит следующим образом:
|
m |
d 2 x |
= P cosγ− P |
|
||
|
|
|
dt2 |
ц |
тр |
|
|
|
|
|
|
|
|
или |
|
|
|
|
||
|
d 2 x |
+ 2 fωdx − ω2 x = fω2r . |
(12.10) |
|||
|
|
|||||
|
dt2 |
|
dt |
н |
|
|
|
|
|
|
Решение этого линейного дифференциального уравнения с постоянными коэффициентами и постоянной второй частью имеет вид
x = |
ω(x1 + frн )( |
f 2 + 1 + f )+ w1 |
e |
ωt( |
f |
2 +1− f ) |
+ |
|||||
2w |
f 2 + 1 |
|
|
|
|
|
|
|||||
|
|
|
|
|
|
|
|
|
(12.11) |
|||
|
ω(x1 + frн )( f 2 + 1 − f )− w1 |
|
− ωt( |
f 2 +1+ f ) |
|
|||||||
+ |
e |
− fr . |
||||||||||
|
|
|
|
|
|
|
|
|||||
|
|
2w f 2 |
+ 1 |
|
|
|
|
|
|
|
н |
|
|
|
|
|
|
|
|
|
|
|
Формула (12.11) представляет собой уравнение пути движения частицы по лопатке во времени. Продифференцировав это уравнение, найдем следующее уравнение скорости движения частицы по лопатке во времени:
234

w = |
ω(x1 + frн )+ w1 ( |
f 2 + 1 − f ) |
e |
ωt( |
f 2 +1− f ) |
− |
|||||
|
f 2 + 1 |
|
|
|
|||||||
2 |
|
|
|
|
|
(12.12) |
|||||
|
ω(x1 + frн )− w1 ( |
f 2 + 1 + f ) |
|
|
−ωt( |
f 2 +1+ f ) |
|||||
− |
e |
. |
|||||||||
|
f 2 + 1 |
|
|
|
|||||||
2 |
|
|
|
|
|
|
Формулы (12.11) и (12.12) дают возможность найти все параметры схода пакета формовочной смеси с лопатки ротора пескомета.
Так, имея исходное положение х1 центра тяжести пакета на лопатке и зная координату х выходной кромки лопатки, находим по уравнению (12.11) продолжительность t движения пакета от точки 1 до точки 2, т.е. от конца направляющей дуги до точки схода пакета с лопатки.
Далее по найденному значению t движения определяем, пользуясь уравнением (12.12), относительную скорость w движения пакета по лопатке в момент схода.
По тому же значению t движения находим угол поворота ротора υ = ωt между положениями 1 и 2, т.е. угловую координату точки схода.
В частном случае при w1 = 0 и f = 0 уравнения (12.11) и (12.12) принимают следующий вид:
уравнение пути
x = x1ch ωt;
уравнение скорости
w = ωx1 sh ωt,
где гиперболические функции
chωt = |
eωt + e− ωt |
и shωt = |
eωt − e− ωt |
. |
|
2 |
2 |
||||
|
|
|
235
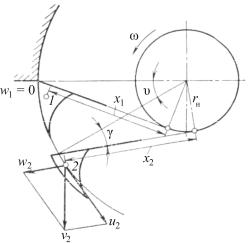
Сход пакета смеси с лопатки ротора. Пакет уплотненной,
связанной формовочной смеси на лопатке ротора метательной головки пескомета можно рассматривать как одно целое твердое тело. Если считать, что пакет смеси сходит с лопатки ротора как одно целое, то этот процесс можно представить, как изображено на рис. 12.6. Пакет начинает скользить вдоль лопатки в точке 1, соответствующей моменту прохождения кромкой лопатки конца направляющей дуги. Через некоторое время (при соответствующем ему угле поворота ротора υ в точке 2) центр тяжести пакета дойдет до радиуса r выходной кромки лопатки, и пакет смеси в этот момент сойдет с лопатки.
Рис. 12.6. Схема схода пакета смеси
слопатки ротора
Вмомент выхода пакет будет иметь абсолютную скорость
выхода v2, равную геометрической сумме векторов u2 окружной скорости на радиусе r и относительной скорости w2 по лопатке.
Пакет сходит с лопатки ротора пескомета практически как одно целое тело, что и подтверждается непосредственными наблюдениями с помощью стробоскопа и киносъемки [20, 48].
236

Влияние расстояния от метательной головки до плоско-
сти набивки. Пакет уплотненной формовочной смеси, летящий из головки пескомета в набиваемую форму, испытывает сопротивление воздуха, вследствие чего скорость его с расстоянием постепенно уменьшается. Кроме того, в результате аэрации летящего пакета некоторая часть смеси из него выдувается и двигается самостоятельно, падая в форму уже с малыми скоростями, что также уменьшает степень уплотнения формы. Рассчитаем уменьшение скорости движения пакета смеси при полете вследствие сопротивления воздуха [8]. При этом будем учитывать силу тяжести пакета, так как при большом расстоянии от головки до опоки влияние ее на изменение скорости пакета становится уже вполне ощутимым.
Уравнение движения пакета в воздухе
G dv = G − Q, g dt
где G – вес пакета; g – ускорение силы тяжести; v – текущая скорость движения пакета; t – время; Q – сила сопротивления воздуха,
Q = cx SM γ2vg2 ,
где сх – коэффициент лобового сопротивления пакета, SM – площадь лобового сопротивления пакета; γ – удельный вес воздуха.
Приняв во внимание, что v = dx/dt, где х – текущее расстояние пакета от головки, и вводя скорость витания пакета
vв = 2Gg , cx γSM
записываем уравнение в виде
|
dv |
|
|
v |
2 |
|
||
v |
|
= g 1 |
− |
|
|
|
. |
(12.13) |
dx |
v |
|
||||||
|
|
|
в |
|
|
|||
|
|
|
|
|
|
|||
|
|
|
|
|
|
|
|
237 |

Решение уравнения (12.13) при начальном условии v = v2 при х = 0 имеет вид
2gx |
|
v = vв2 + (v22 − vв2 )e− vв2 . |
(12.14) |
Коэффициент лобового сопротивления сх, |
отнесенный |
к площади лобового сопротивления, может быть принят следующим в зависимости от соотношения между сторонами а и b прямоугольного сечения пакета, перпендикулярного к направлению полета:
a/b |
1 |
2 |
4 |
10 |
18 |
∞ |
cx |
1,10 |
1,15 |
1,19 |
1,29 |
1,40 |
2,01 |
|
Скорость полета пакета близка к окружной скорости ковша |
на радиусе направляющей дуги и составляет в зависимости от типа пескомета 24–60 м/с при частоте вращения ротора пескометной головки 1000–1500 об/мин.
При ударе пакета о слой, не ограниченный стенками формы и опоки, напряжения в слое быстро уменьшаются по мере удаления от плоскости удара; происходит релаксация напряжений. Однако сам процесс уплотнения верхнего слоя формы и пакета протекает аналогично под действием сил инерции, которые создают сжимающие напряжения до 0,3–0,4 МПа в верхних слоях пакета, в средних ~ 1,5 МПа, в верхних слоях формы напряжения достигают 4 МПа. Весь процесс удара пакета длится ~ 0,0007 с [2]. Плотность формы достигает 1,5–1,57 г/см3.
Величину сил инерции можно определить из уравнения
движения пакета в момент внедрения его в смесь: |
|
|||||
M |
|
d 2 x |
− Cx = 0, |
(12.15) |
||
п dt |
2 |
|||||
|
|
|
где Мп – масса пакета, кг; С – жесткость пакета смеси, Н/м; х – деформация смеси.
238
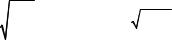
Из уравнения (12.15) следует, что ускорение инерции j и сила инерции Рmax пропорциональны скорости vп пакета в момент его соприкосновения со слоями смеси, лежащими в опоке.
j |
|
= v |
|
C |
, м/с2; P |
= v |
CM |
|
, Н |
(12.16) |
|
|
|
|
|||||||
|
max |
п M п |
max |
п |
|
п |
|
|
||
где C = KHo F / H ( KHo |
– модуль упругости смеси, Па; F, H – |
площадь и высота опоки).
Процесс пескометной формовки предъявляет дополнительные требования к формовочной смеси: формовочная смесь перед подачей на пескомет должна подвергаться дополнительной очистке, в частности, с применением установки вибросит с ячейкой сита 16–20 мм.
Из анализа уравнений (12.15) и (12.16) видно, что качество уплотнения смеси пескометом определяется технологическими параметрами: скоростью полета пакета vп, массой – Мп.у (масса, приходящаяся на единицу длины ковша) и жесткостью смеси С (параметр, характеризующий ее физико-механические и реологические свойства). Кроме того, на качество уплотнения существенно влияет величина относительного смещения пакетов α, определяемая отношением смещения двух смежных пакетов при укладке к их размеру в направлении смещения, т.е. относительной скоростью перемещения головки пескомета относительно набиваемой опоки.
Величина относительного смещения характеризует совершенство процесса. Чем ближе α к 1, тем большая часть энергии будет затрачиваться на уплотнение. При использовании обычных пескометов α = 0,2…0,4 при vп = 48…60 м/с, ширококовшо-
вых пескометов – α = 0,5…0,7, vп = 24…30 м/с.
При пескометной формовке степень уплотнения смеси по всей высоте формы, как показывает опыт, практически одинаковая. Однако в местах пересечения крестовин и непосредственно под ребрами крестовин имеет место снижение плотности. Осо-
239
бенно существенное уменьшение плотности наблюдается при ширине ребер 30 мм и более. Не рекомендуется применять толщину ребер более 16–20 мм. Целесообразно, чтобы ребра крестовин не имели острых углов. Углы желательно выполнять скругленными, чтобы падающий пакет меньше разрушался. Расстояние от нижней кромки ребра до выступающей части модели должно быть не менее 100–120 мм.
Пакет уплотняемой формовочной смеси, выброшенный пескометом, достигая формы, во-первых, трамбует смесь, о которую он ударяется, вовторых, дополнительно уплотняется сам под действием собственной силы инерции, которая погашается при ударе, и, в-третьих, внедряется в набивку.
Эффективность процесса уплотнения пескометом и качество формы зависит от абсолютной скорости падения пакета в момент удара и от скорости перемещения головки пескомета над опокой.
При слишком медленном перемещении головки движущиеся последовательно пакеты падают друг на друга, смесь образует конус в месте падения, растекается по нему в стороны и частично разрыхляется. При слишком быстром перемещении головки пакеты не будут образовывать сплошности набивки.
12.2. Конструктивные типы пескометов
По конструкции пескометы разделяют на консольные
имостовые, по ширине ковша – на узкоковшовые и ширококовшовые, по функциональному назначению – на стационарные
ипередвижные. Последние снабжены механизмом для перемещения по рельсовым путям и предназначены для набивки крупных форми стержней, атакже для формовки наплацу и в кессонах.
Подвесные пескометы мод. 290 (рис. 12.7) применяют для набивки небольших опок в условиях мелкосерийного производства. Их размещают непосредственно над карусельной установкой или пульсирующим конвейером. Рабочим органом пескомета
240