
1463
.pdf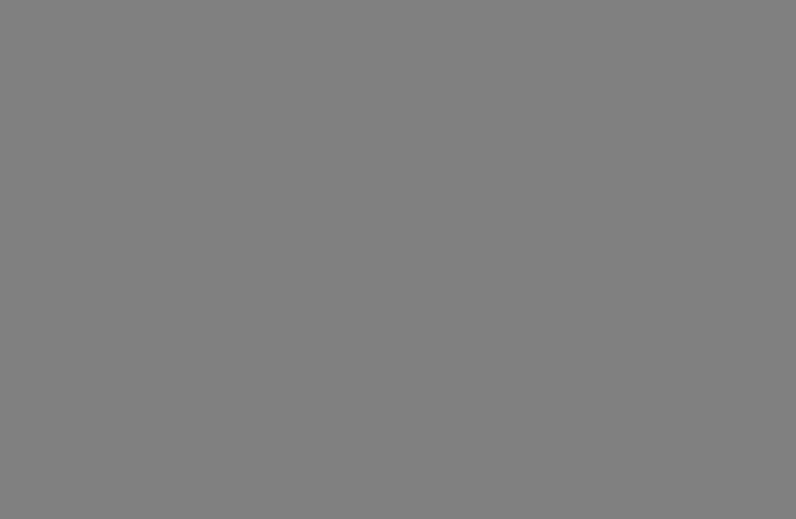
Во второй период плавки шлаки не сливают и подачу воз духа в конвертер не прекращают. После второго периода в кон вертере получается черновая медь, содержащая 98,5—99,5% Си* 0,03-0,8% S, 0,03—0,1% Fe, 0,3-0,5% Ni, 15-250 г/т Ag, 1,0— 350 г/т Аи, до 0 ,1 % 0 2. Шлаки второго периода содержат до 5,0% Си, их используют как оборотные материалы. Продолжи тельность плавки в конвертере емкостью 40 т составляет— 15 час.
Так как черновая медь содержит примеси, ухудшающие ка чество меди, ее рафинируют. Рафинирование меди ведут двумя способами: огневым и электролитическим.
Огневое рафинирование меди
Рафинирование черновой меди огневым способом ведут в тех случаях, когда в ней содержится малое количество благо родных металлов (золота и серебра), и когда в полученной ра финированной меди допустимо повышенное содержание неже лательных примесей. Процесс рафинирования ведут в пламен ных печах. Для этого черновую медь загружают в печь, расплав
ляют, |
затем металл |
продувают |
воздухом |
при |
давлении 1,5— |
2,0 ат. |
Воздух для |
продувания |
подают |
через |
металлические |
трубы сверху. Во время продувания кислород воздуха окисляет примеси Si, Al, Zn, Mn, Sn; Pb, Fe и др. Часть примесей окис ляется и переходит в шлак (FeO, Si02, А120з), а часть приме сей (ZnO, РЬО и др.) в парообразном состоянииудаляется с
печными газами. Одновременно |
с окислением примесей окис |
|
ляется и некоторое количество |
меди |
по реакции 4Си + 0 2 |
■-> 2Си2 0. После окончания окисления |
примесей подачу возду |
ха в печь прекращают и ведут восстановление окисленной ме ди. Восстановление меди производят методом «дразнения». Для этого в металл вводят березовые или сосновые бревна диамет ром 250—350 мм, длиной 7—10 м. При дразнении происходит процесс перемешивания металла, благодаря образующимся га зам и восстановление меди по реакциям:
CU2O -р С —>■2 Си -р СО,
CU2O -р СО —>2 Си -р С02-
В результате получают техническую медь с содержанием 99,5—99,7% Си. Готовую медь из печи выпускают в ковши и разливают на слитки или анодные плиты. Медные слитки в ос новном используют для получения сплавов бронзы или латуни при производстве фасонных отливок. Анодные плиты направ ляют на электролиз.
Электролитическое рафинирование меди
Электролитическому рафинированию подвергают до 9 5 % черновой меди. Процесс рафинирования ведут в электролизных
ваннах (рис. 20). Ванны изготовляют |
из дерева или |
бетона. |
|
Внутри ее покрывают свинцовыми листами толщиной |
от |
2 до |
|
4 мм. Ванна имеет размеры: ширину 1 , 2 |
м, длину от 2 , 5 |
до |
3 , 0 м |
Р и с. 20. |
В ан н а |
д л я |
эл ек т р о л и ти ч еск о го |
р а ф и н и р о |
||
|
|
вани я м еди : |
|
|
||
1 — корпус |
ванны; |
2 — листовой |
свинец; |
3 — изоляторы; |
||
4 — отверстие для |
спуска |
шлама; |
5 — шлам; |
6 |
— анод; 7 —» |
|
|
|
катод; |
8 — электролит |
|
|
и глубину до 1,0 м. |
Перед электролизом в ванну заливают элек |
|
тролит, состоящий |
из 10—16% раствора медного купороса с |
|
добавкой |
1 0 —1 6 % |
серной кислоты. После заливки электролита |
в ванну |
опускают |
анодные плиты и катоды. Катодами явля |
ются медные листы толщиной от 0,5 до 0,7 мм, полученные элек тролитическим способом в специальных матрицах. В ванне раз мещают 20—40 анодных плит, число размещенных катодов на единицу больше числа анодов. К анодам подводят шинами электрический ток с положительным полюсом, а к катодам — с отрицательным полюсом. Ток пропускают силой до 10 000 а при напряжении Ю0 — 2 2 0 в.
При пропускании тока в ванне протекают электролитические процессы. В растворе под воздействием тока сернокислая медь, диссоциирует на катионы Си2+ и анионы S0 4 ++. Катионы осаж даются на катоде, в то же время на аноде отрываются элек троны
Си + 2е -9- Си2+
и переходят в раствор. В результате протекания этого процесса в течение 10—12 суток на каждом катоде осаждается до 90 кг меди с содержанием 99,95% Си.
Примеси, содержащиеся в анодной меди, частью растворя ются, а частью осаждаются на дно ванны (шлам). При высоком содержании благородных металлов количество шлама состав
ляет до |
1,0%. |
Он содержит 18% Си,— 0,65% Аи,— 3,5% Ag, |
- 0,7% |
Pb, ~ |
3,5% Sb, ~ 3,0% As , ~ 0,7% Se и ~ 1,0% Fe. |
Шлам из ванны спускают и извлекают из него благородные ме таллы. При электролизе меди расход электроэнергии составляет 250—300 квт-ч/т катодной меди.
Электролитическую медь используют для изготовления элек троматериалов— проволоки, шин, кабелей, а также при произ водстве труб и различных медных сплавов.
Гидрометаллургический способ получения меди
Гидрометаллургическую переработку медных руд ведут дву мя способами: сернокислотным и аммиачным. Сернокислотный способ имеет большое распространение. Для этого бедную по содержанию меди руду в измельченном состоянии растворяют в деревянных или бетонных чанах. В качестве растворителей ис пользуют H2 S04 и Fe2 (S0 4 )3 .
Сернокислотный способ переработки медных руд основан на том, что серная кислота в водном растворе реагирует с карбо натами и окислами двухвалентной меди:
СиС03 |
. Си (ОН) 2 |
+ 2H2S04 |
= 2CuS04 |
+ |
3 Н20 + С02; |
|
2 СиС03 |
• Си (ОН) 2 |
+ 3H2S04 |
= 3CuS04 |
+ |
4 |
Н20 + 2С02; |
|
СиО |
H2 S04 = CuS04 -|- Н20. |
|
Полусернистую медь и высшие сульфиды меди из руд пе реводят в сульфаты действием сульфата окиси железа
Cu2S + 2Fe2 (S04 ) 3 -> 2 CuS04 + 4 FeS04 + S02.
Растворы, содержащие CuS04, Fe30 4, и примеси отделяют от нерастворимого остатка отстаиванием и фильтрованием.
Богатые растворы по содержанию сернокислых солей меди
подвергают |
электролизу. |
Так как медь находится |
в растворе, |
|
используют |
нерастворимые аноды, изготовляемые |
из свинца. |
||
Катоды применяют также из электролитической меди. |
|
|||
Из бедных растворов медь извлекают методом цементации. |
||||
Для этого в раствор загружают куски железа |
(обрезки листов, |
|||
проволоки). Загруженное |
железо, растворяясь, |
замещает медь |
||
в сернокислом соединении |
|
|
|
CuS04 -f- Fe —>FeS04 -f- Cu.
Медь выделяется в виде порошка и осаждается на дне чана. В осадке содержание меди доходит до 70%.
Производство алюминия
Для получения алюминия используют руды, содержащие А12 0 3. К таким рудам относят бокситы, нефелины, алуниты и каолины. Б о к с и т ы в своем составе содерн^ат: 30—57% А12 0 3, 17—35% Fe20 3, 3—13% Si02, 2,0—4,0%; ТЮ2, до 3,0% СаО и 1 0 - 18% Н2 0. Бокситы залегают в Тихвинском районе, на Урале, в Сибири и в других районах. В боксите алюминий нахо
дится в составе гидратов окиси алюминия. |
Н е ф е л и н ы полу |
чают в виде отходов после обогащения |
апатито-нефелиновой |
породы, содержащей около 30% А120 3, 20%(Na2O + К2 0), 40—
45% Si02, 2,0—4,0% СаО |
и 2,0—4,0%; F2 0 3. Апатито-нефели |
|
новые руды залегают на Севере и Урале. А л у н и т ы |
содержат |
|
20-21% А12 0 3, 4,5—5,0% |
(Na20 + К20 ), 22—23% |
S 03, 41— |
42%. Si02, 4,0—5,0% Fe2 0 3 |
и 6,0—7,0% Н2 0. |
|
Основными рудами для получения алюминия являются бок ситы и нефелины. При использовании нефелинов для производ ства алюминия получают ценные побочные продукты — поташ и соду.
Технологический процесс получения алюминия разделяется в основном на две стадии: получение глинозема из руды и по лучение алюминия из глинозема.
Получение глинозема
Для получения глинозема из руд существует несколько спо собов. Для получения глинозема из руд, содержащих не более
5 % S i0 2y наиболее |
рентабельным является щелочной |
способ. |
При получении |
глинозема по этому способу боксит |
подвер |
гают дроблению и размолу. Затем в автоклавах производят вы щелачивание глинозема, содержащегося в боксите. Для этого в автоклав заливают раствор едкого натра, загружают размо лотый боксит и вводят пар для поддержания рабочего давления до 12 ат и температуры 160—170° С.
Глинозем, содержащийся в боксите в форме гидратов окис
лов алюминия, в автоклаве взаимодействует |
с |
едким натром |
и переходит в раствор в виде алюмината натрия: |
|
|
2А1 (ОН)з + 2 NaOH = Na20 - А120 3 + |
4 |
Н20. |
Окислы железа, находящиеся в бокситах, при выщелачивании не переходят в раствор, а остаются в шламе, придавая ему кир пично-красный цвет.
Кремнезем, содержащийся в бокситах, реагирует с едким натром и переходит в раствор в виде силиката натрия:
Si02 + 2 NaOH = Na20 • Si02 + H20.
Силикат натрия, взаимодействуя в растворе с алюминатом натрия, образует нерастворимый натриевый алюмосиликат:
Na20 • А120 3 |
-р 2 (Na20 |
Si02) -f- 4Н20 = |
= Na20 • А12 |
0 3 - 2 Si02 |
2 Н20 + 4 NaOH. |
В результате этой реакции раствор очищается от кремнезема, но при этом переходит в шлам глинозем и требуется повышен ный расход едкого натра.
Полученный алюминат натрия в виде пульпы из автоклава поступает в специальный аппарат — самоиспаритель. Передача пульпы осуществляется за счет разности давления в автоклаве и самоиспарителе. В самоиспарителе производят гидролиз алю мината натрия и выделение кристаллической гидроокиси алю миния по реакции
Na20 А1о03 + 4 Н20 в NaOH + ф 2 А1 (ОН)3.
Для ускорения разложения пульпа перед операцией охлажда ется до 60° С и по мере хода процесса ее температура снижается до 40° С. Кроме этого, вводится затравка в виде кристаллов гидроокиси алюминия.
Выделившаяся гидроокись алюминия отфильтровывается и направляется для обезвоживания. Обезвоживание производят в трубчатых вращающихся печах путем прокаливания при тем пературе до 1200° С. В процессе прокаливания получают чистый глинозем по реакции
А1 (ОН) 3 А120 3 + Н20.
Выход глинозема из руды по этому способу составляет око ло 85 %.
Для получения глинозема из руд с высоким содержанием кремнезема руды прокаливают, размалывают, смешивают с со дой (Na2 C03) и мелом (СаС03). Смесь при температуре 1 1 0 0 ° С спекают, в результате получают алюминат натрия в твердом
виде |
— |
А120 3 |
-р Na2C0 3 -> Na20 • А120 3 -р С0 2, |
а также двукальциевый силикат
2СаС03 + SiO* -* 2 СаО • Si02 + 2 С02
и феррит натрия
2 Fe20 3 + Na2C03 -> 2 Fe20 3 Na20 + С02.
После спекания массу размалывают и подвергают выщела чиванию, в процессе которого в раствор переходят алюминат натрия (Al20 3 -Na20) и феррит натрия (2Fe2 0 3 • N20 ) . В осадке остаются двукальциевый силикат (2СаО • Si02) и другие не-
растворимые примеси. Феррит натрия из раствора осаждают путем гидролиза:
Fe20 3 Na20 + 4H 2 0 -> 2F e(0H ) 3 + 2Na0H.
Полученная гидроокись железа переходит в осадок, а щелочь переходит в раствор.
Полученный раствор, содержащий алюминат натрия, отде ляют и направляют на обескремнивание и карбонизацию. Целью обескремнивания является более полное удаление кремнезема. Сущность этой операции состоит в связывании растворенного кремнезема в нерастворимые соединения и выделение их в оса док натриевым или кальциевым алюмосиликатом.
Обескремненный алюмосиликатный раствор после отделения от него шлама подвергается карбонизации пропусканием газа, содержащего С02. Эту операцию проводят для выделения из раствора гидрата окиси алюминия по реакции
А120 3 • Na20 С02 ЗН20 —>2А1 (ОН) 3 -f- Na2C03.
Гидрат окиси алюминия А1(ОН) 3 выпадает в осадок, а сода (Na2C03) остается в растворе. Выпавший осадок отфильтровы вают, промывают и прокаливают. При прокаливании получают чистый глинозем1.
Получение алюминия из глинозема
Безводная окись алюминия имеет температуру плавления 2050° С, температуру кипения 2980° С и представляет собой прочное химическое соединение алюминия с кислородом. Полу чение металлического алюминия из глинозема восстановлением углеродом или окисью углерода невозможно, так как этот про цесс приводит к образованию карбидов (А14С3). Также не удает ся получить алюминий и электролизом из водного раствора со лей, так как на катоде выделяется только водород. Поэтому алю миний получают электролизом из глинозема, растворенного в расплавленном криолите. Криолит представляет собой фторит алюминия и натрия Na3AlF6. В качестве сырья для производст ва криолита используют плавиковый шпат (CaF2), гидрат окиси алюминия, соду и серную кислоту.
Для электролиза глинозема применяют электролизные ван ны (рис. 2 1 ).
Ванна имеет железный корпус, внутри выложенный тепло изоляционным кирпичом, а затем угольными блоками. В поди ну ванны вставлены катодные шины. Сверху в ванну опущены угольные электроды, представляющие собой аноды. Электриче ский постоянный ток к анодам подводится от шин, расположен ных над ванной. Ток применяют с напряжением от 5 до 10 в, сила тока на одну ванну от 40 000 до 100 000 ат. Электрический
ток используется как для электрохимического процесса, так и для нагрева электролита до 950—1000° С. По современным тео ретическим представлениям кинетика электролиза глинозема протекает следующим образом. Под действием электрического тока в расплавленном криолите протекает диссоциация на ионы:
Na3 AlF0 3Na+ + AlFg-
|
Р н с. |
21. |
Э л ек тр ол и тн ая ванн а |
д л я эл ек т р о л и за гл и н о зем а : |
|
|||||||
/ — угольный |
анод; |
2 — угольная футеровка; |
3 — жидкий алюминий; |
-/ — расплавлен |
||||||||
ный |
электролит; 5 — корка электролита; |
6 — глинозем; 7 — катодные |
шины; |
8 — бун |
||||||||
кера |
для загрузки |
глинозема |
в ванну; |
9 — анодная |
шина; 10 — контакты (стержни) |
|||||||
для |
подвода |
тока |
к аноду; 11 — анододержатель; 12 — механизм |
опускания |
и подъ |
|||||||
ема |
анода; |
13 — кожух |
из алюминиевого |
листа для. непрерывного |
анода; /-/ — корпус |
|||||||
ванны; 15 — труба |
для |
отбора |
алюминия из |
ванны; |
16 — вакуумный |
ковш; |
17 — тру |
|||||
|
|
ба к вакуумному |
насосу; 18 — анодная |
углеродистая |
м-асса |
|
Растворенный в криолите глинозем также диссоциирует на ионы
А120 3 ^ Al3+ + А103-.
Ток к катоду переносится ионами А13+ и 3Na+ в соответствии с положенным их ряду напряжением. Ион А13+ обладает менее отрицательным потенциалом выделения, чем ион 3Na+. Поэтому только алюминий А13+ получает разряд и переходит в метал лический алюминий
A F + + Зе -> А 1
и осаждается на дно ванны. Ионы же натрия с анионами А103~ образует алюминат натрия
3Na+ + АЮ3- -►Na3 A103.
К аноду движутся анионы A1F3- и АЮ3-, на аноде разря жаются только более отрицательные ионы
2А103- — 6е А120 3 + з/20 2.
Выделившийся на аноде кислород взаимодействует с угле родом анодов и образует СО и С02, которые отводятся из ван ны. Собравшийся жидкий алюминий на дне ванны периодически выпускают в ковш или выбирают при помощи сифона. При элек тролизе для получения 1 т алюминия расходуется до 2 г глино зема, 100 кг криолита, до 600 кг угольных электродов и 16 500— 18 500 кот-ч электроэнергии.
Рафинирование алюминия
Получаемый электролизом алюминий в своем составе содер жит различные примеси, которые ухудшают его свойства. Для получения чистого алюминия его подвергают рафинированию методом хлорирования или электролитическим способом. Способ хлорирования состоит в продувке алюминия хлором в ковшах емкостью 1200—1300 кг при температуре 750—770° С в течение 10—15 мин. Во время продувки примеси (глинозем, криолит, га зы и др.) из алюминия выделяются; одновременно с этими про дуктами теряется часть алюминия (до 1,0%). Рафинированный хлором алюминий разливают в чушки.
Электролитический способ рафинирования применяют для по лучения алюминия высокой чистоты. При этом способе рафини рования первичный алюминий подвергают анодному растворе нию, а чистый алюминий служит катодом. Между анодным и чистым алюминием в качестве электролита используют хлори стые и фтористые соли. По этому способу получают чистый алю миний (99,85—99,9% А1).
Производство магния
В современном машиностроении магний находит широкое применение главным образом как основа легких сплавов. Для получения металлического магния применяют два способа — электролитический и термический. В качестве исходных мате риалов используют магнезит, доломит, карналлит и бишофит. М а г н е з и т является карбонатом магния (MgC03), содержа щий 28,8% Mg. В природном магнезите, кроме MgC03, обычно содержатся окислы кремния, железа, алюминия и кальция. В нашей стране имеются большие залежи магнезита на Урале (Саткинское и Халиловское месторождения).
Д о л о м и т представляет |
собой двойной карбонат магния |
и кальция (MgC03 *СаСОз), |
содержащий 13,2% Mg. Доломит |
содержит примеси в виде кварца, кальцита, гипса и др. Наибо лее крупные промышленные месторождения доломита находят ся в Московской области, на Урале и на Украине.
К а р н а л л и т является природным хлоридом магния и |
ка |
лия (MgCl2КС1 -6Н2 0), в зависимости* от содержания тех |
или |
иных примесей имеет розовый, желтый или серый цвет. Карнал лит является гигроскопическим материалом, активно поглощаю
щим влагу. В карналлите содержится 8 ,8 % |
Mg. Крупнейшие |
|||
залежи карналлита |
находятся |
на Урале (Соликамское |
место |
|
рождение). |
|
собой хлорид магния |
(MgCl2 • |
|
Б и ш о ф и т представляет |
||||
*6Н2 0 ), в природе |
содержится в морской |
воде, около 0,3% |
в воде соляных озер. В некоторых озерах нашей страны, напри мер озера Перекопской группы, к концу лета содержание MgCl2 достигает 15%. Бишофит также получают при переработке при родного карналлита.
Получение магния электролитическим способом
Электролитическим способом получают магний из хлоридов магния.
Для этой цели доагнезит или доломит подвергают обжигу при температурах 700—800° С. Во время обжига магнезит диссо циирует
MgC03 -> MgO + С02,
а доломит диссоциирует
MgC03 • СаС03 -> MgO + СаО + 2С02.
Полученную окись магния хлорируют при температуре 800— 900° С в присутствии углерода. Во время хлорирования проте кает реакция
MgO -j- С -|- Cl2 —>- MgCl2 -j- с о .
Хлорирование окиси магния осуществляют в шахтных элек трических печах, футерованных шамотным кирпичом. Во вре мя хлорирования в печь, кроме окиси магния, загружают уголь ные цилиндрики, а через фурмы, расположенные внизу печи, подают хлор. Электроды в печи располагают друг к другу под углом 120°. При работе печи развивается максимальная темпе ратура до 1000° С. В печи образовавшийся хлористый магний расплавляется и периодически, через 3—4 часа, выпускается б ковш с плотно закрывающейся крышкой и в последнем транс портируется в цех электролиза.
Карналлит подвергают обезвоживанию и расплавлению. Обезвоживание обычно производят в трубчатых вращающихся печах при температуре газов на входе до 450° С и на выходе до 220° С. Плавление ведут в трехфазных электропечах при тем пературе 750—800° С. Во время выдержки из расплава оседает