
1463
.pdf5) податливостью, т. е. способностью сжиматься при усадке металла во время его кристаллизации и охлаждения отливки. Это качество необходимо для предотвращения образования тре щин в отливке. Лучшей податливостью обладает смесь из круп ного песка и с содержанием каменного угля, древесных опилок или. торфа, различного рода органических связующих материа лов. Глина ухудшает податливость смеси;
6) практическим отсутствием гигроскопичности высушенных стержней и форм.
Перечисленные требования особенно строго должны выдер живаться для стержневых смесей, так как стержни находятся в более тяжелых условиях при заливке металлом, чем форма. Кроме этого, они должны обладать легкой выбиваемостью, т. е. легко удаляться из отливки после ее охлаждения. С уменьше-
|
|
|
|
|
|
|
|
|
Т а б л и ц а |
20 |
|||
|
Рекомендуемые составы стержневых смесей для цветного литья |
|
|
||||||||||
Состав смеси в весовых частях |
|
Свойства смеси |
|
|
|
|
|
|
|||||
|
|
|
|
|
|
|
прочность |
|
|
|
|
|
|
|
|
|
|
|
|
|
к г /с м 2 |
|
Назначение |
|
|||
квар |
связующие |
различные |
н |
газопро |
|
сухих |
|
|
|||||
|
|
|
смеси |
|
|||||||||
цевbiii |
|
|
|
Л |
ницае |
сырых |
|
|
|
|
|
|
|
материалы |
добавки |
о |
образ |
|
|
|
|
|
|||||
песок |
о |
мость |
образ |
|
|
|
|
|
|||||
|
|
|
* |
цов |
|
|
|
|
|
||||
|
|
|
|
|
|
цов |
при |
|
|
|
|
|
|
|
|
|
|
га |
|
|
при |
растя- |
|
|
|
|
|
|
|
|
|
§ |
|
|
сжатш1женни |
|
|
|
|
|
|
100 |
Крепи |
Сера |
3 - 4 |
Не |
ни 0,04—г |
9—10I |
Изготовление |
||||||
|
тель |
М |
(0,4—- |
|
же |
100 |
0,05 |
стержней |
|
1-го |
|||
|
(до 3,0) |
0,6), |
|
|
|
|
класса |
сложности |
|||||
|
|
|
уайт- |
|
|
|
|
для |
отливок |
из |
|||
|
|
|
спирит |
|
|
|
|
магниевых |
спла |
||||
|
|
|
(0,2) |
|
|
|
|
вов |
|
|
|
|
|
100 |
Крепи |
|
3 - 4 |
Не |
ни |
0,05— |
8—10 |
Изготовление |
|||||
|
тель М (до |
|
|
же 70 |
0,065 |
стержней |
1 -го |
и |
|||||
|
2,0), |
суль |
|
|
|
|
|
2-го классов слож |
|||||
|
фитная |
|
|
|
|
|
ности |
для |
отли |
||||
|
барда |
(до |
|
|
|
|
|
вок |
из |
алюминие |
|||
|
1,5) или |
|
|
|
|
|
вых |
сплавов |
|
||||
|
4ГУ (1—1,5) |
- |
3 - 4 |
Не ни |
0,05— 10—12 |
|
|
|
|
|
|||
|
и барда |
|
|
же 70 |
0,06 |
|
|
|
|
|
|
||
|
(2,5—3,5) |
|
|
|
|
|
|
|
|
|
|
|
|
98— |
КВС (1,5) |
Глина |
3—4 |
Не ни- (3,06 — 12—14 |
Изготовление |
|
|||||||
100 |
барда |
|
(0 -2 ) |
|
же 60 |
0,1 |
стержней 2-го |
и |
|||||
|
(2-2,5) |
|
|
|
|
|
3-го классов слож |
||||||
|
|
|
|
|
|
|
|
ности для отливок |
|||||
|
|
|
|
|
|
|
|
из |
|
алюминиевых |
|||
|
|
|
|
|
|
|
|
и медных сплавов |
нием глинистой составляющей в стержневых смесях выбивае-
мость их улучшается. |
с м е с и |
подразделяются на |
облицовоч |
Ф о р м о в о ч н ы е |
|||
ные, наполнительные и единые. |
засыпают |
||
При изготовлении |
формы |
облицовочной смесью |
модель слоем толщиной 20—30 мм. В процессе заливки облицо вочная смесь находится в непосредственном соприкосновении с металлом и должна обладать всеми вышеперечисленными свойствами.
Наполнительной смесью заполняют остальную часть формы. Наполнительные смеси могут быть менее высококачественными и более дешевыми. Такие смеси должны быть прочными и газо проницаемыми.
Единые формовочные смеси применяют главным образом при массовом механизированном производстве отливок и изго товлении форм на машинах. К ним предъявляют те же требова ния, что и к облицовочным смесям.
В зависимости от способа использования форм различают следующие смеси: для заливки по-сырому, по-сухому, быстро твердеющие и самозатвердевающие. Составы рекомендуемых формовочных и стержневых смесей представлены в табл. 16—20.
^Приготовление формовочных и стержневых смесей
Приготовление формовочных и ст.ержневых смесей состоит из двух стадий: 1) подготовки исходных формовочных материа лов; 2) смешивания их в необходимой пропорции и разрыхле нии смеси.
Подготовка исходных материалов состоит из следующих операций:, магнитной сепарации и просеивания отработанной смеси, сушка песка, глины и каменного угля при 100—110° С для удаления влаги, размола глины и угля, просеивания песка, глины и угля.
Магнитную сепарацию отработанной смеси производят при помощи магнитных шкивов (рис. 80) с целью отделения частиц металла. Для просеивания смеси используют конусообразные барабанные сита (рис. 81), стенки которых представляют собой сетки с отверстиями определенного размера. При вращении си та крупные частицы отделяются от мелких и скатываются в сто рону, противоположную загрузке. Песок, глину и каменный уголь сушат в горизонтально вращающихся сушилах (рис. 82) и мно гоподовых печах (см. главу I). Глину и уголь размалывают в размалывающих бегунах (рис. 83) и шаровых мельницах.
На ряде заводов взамен сухой глины в состав смеси вводят глинистую суспензию с удельным весом 1,4. Применение глини стой суспензии сокращает расход глины в среднем на 30% и при-
Рис. |
80. |
Схема шкивного магнитного сепаратора: |
|
I — вал; |
2 — |
сердечники; |
3 — катушки; 4 — транспортерная лен |
та; 5 — немагнитный |
материал; 6 — магнитный материал |
/
Рис. 82. Схема горизонтального барабанного сушила:
1 — загрузка исходного материала; 2 — выход высушенного ма териала; 3 — топка; 4 — барабан; 5 — дымовая труба
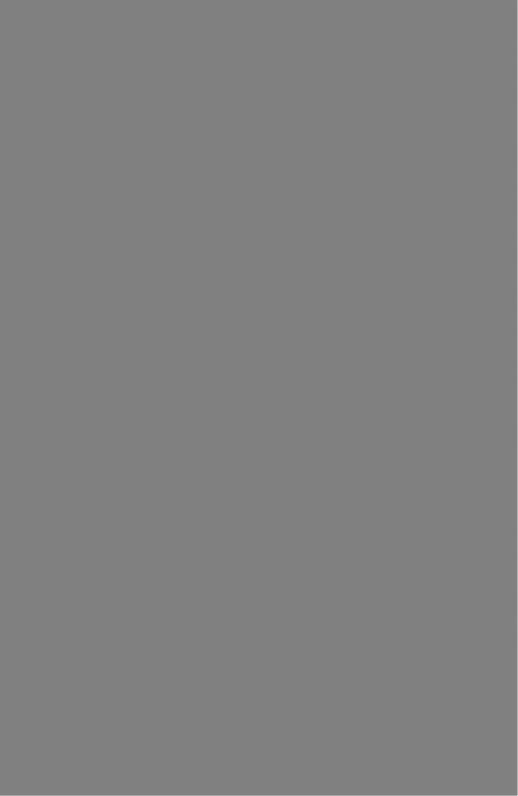
дает смеси большую пластичность, прочность и газопроницае мость. Приготовляют глинистую суспензию в горизонтальных мешалках.
Смешивают исходные формовочные материалы для изготов ления смеси в смешивающих бегунах (рис. 84). В последнее время применяют бегуны центробежные модели 115 и 116 с го ризонтально вращающимися катками.
Характеристика бегунов
Емкость эамеса, ж3 |
0,45 |
Диаметр чаши, мм |
1925 |
Производительность при полной механизации загрузки и вы грузки смеси, т!час:
Наполнительной смеси для отли
вок из чугуна и стали |
40,5 |
Облицовочной смеси для отливок |
|
из стали и чугуна |
25 |
Стержневой смеси |
35 |
Применение этих бегунов сокращает |
время перемешивания |
и повышает качество смеси. По выходе из смешивающих бегу нов готовая смесь подвергается разрыхлению.
В механизированных литейных цехах формовочные смеси приготовляют в земледельных системах по следующей схеме: с разливочного конвейера залитые и охлажденные формы пода ются на выбивание решетки, где производится выбивка смеси. Выбитая (отработанная) смесь через конусообразный бункер, расположенный под выбивной решеткой, поступает на ленточ ный транспортер, который передает смесь на другой, перпенди кулярно расположенный ленточный транспортер. Во время осы пания смеси с первого транспортера на второй происходит отде ление металлической части при помощи магнитного шкива, установленного в конусе первого транспортера. Со второго транс портера смесь, освобожденная от металлических частиц, ссыпает ся в конусообразное барабанного типа сито, в котором отделяются крупные спекшиеся куски смеси и куски стержней, попадающих в смесь во время выбивки форм. Из сита крупные куски идут в отвал, а смесь требуемой формы поступает на распределительную ленту, с которой распределяется по бункерам, расположенным над смешивающими бегунами. В смешивающие бегуны отработан ная смесь из бункера засыпается порциями. Кроме отработанной смеси, в бегуны загружают свежие формовочные материалы (пе сок, глину, порошкообразный каменный уголь) и добавляют воду. Перемешивание смеси в обычных смешивающих бегунах длится 3—5 мин., в бегунах автоматического действия 1,5—3 мин. Из бегунов через отверстие в днище приготовленная смесь ссыпается на ленточный транспортер и подается в разрыхлитель, установ ленный над одним (отстойным) бункером, а затем в отстойный
15 Н. А. Баринов и др.
бункер, всегда имеющий запас смеси. При помощи питателя и транспортера смесь из этого бункера подается во второй разрых литель, а из «его на ленточный распределительный транспортер» с которого распределяется по расходным бункерам, установлен ным над формовочными машина-ми. Из расходных бункеров смесь периодически засыпают в опоки при открывании затвора.
Внемеханизированных литейных цехах при индивидуальном
имелкосерийном производстве отливок выбитую из формы смесь загружают в землеразрыхлительную ленточную машину, на ко торой происходит разрыхление смеси и отделение крупных кус ков смеси и металла. Отработанную смесь, отделенную от круп ных кусков, вместе со свежими формовочными материалами загружают в смешивающие бегуны, подают воду и приготовля ют формовочную смесь для изготовления форм.
Приготовление стержневых смесей включает в себя те же стадии, что и приготовление формовочной смеси. Смешивание исходных формовочных материалов производится в смешиваю щих бегунках.
Изготовление форм
При индивидуальном и мелкосерийном производстве отливок формы изготовляют ручным способом, а при крупносерийном и массовом производстве — на формовочных машинах или песко метом. Обычно их изготовляют в опоках. Это специальные рам ки, в которые набивается формовочная смесь (рис. 85). В зави симости от размера и сложности отливки форму изготовляют в двух или нескольких опаках, соединенных штырями. В процессе изготовления формы опока устанавливается на подмодельную плиту и наполняется формовочной смесью.
Опоки бывают разъемные и неразъемные. Разъемные опоки применяют при массовом производстве отливок небольшого веса
иназывают жакетами. В жакетах производится формовка и сборка форм. С собранных форм такие опоки снимают и залива ют формы металлом.
Внеразъемных опоках изготовляют формы и заливают их ме таллом. Они применяются при производстве отливок небольшого
ибольшого веса.
Изготовление форм на формовочных машинах и пескомета ми производится в парных опоках. Применяют опоки таких раз меров, чтобы между опокой и моделью был зазор, обеспечиваю щий форме необходимую прочность при заливке ее металлом и минимальный расход формовочной смеси.
При ручной формовке формы могут быть изготовлены в поч ве на полу цеха, покрытом слоем формовочной смеси, в двух или нескольких опоках. Применяют несколько различных приемов
ручной формовки: шаблонную формовку, формовку по скелетным моделям и др., позволяющие изготовлять формы с помощью уп рощенного модельного инвентаря.
Ручная формовка. И з г о т о в л е н и е фо р м в д в у х о п о к а х по н е р а з ъ е м н о й м о д е л и с о с т о и т из с л е д у ющ и х о п е р а ц и й : на подмодельную доску У (рис. 86) ставят модель 2 и накрывают опокой 3. Затем модель в опоке засыпа ют облицовочной формовочной смесью слоем 15—20 мм и запол няют опоку наполнительной смесью, уплотняя сначала острым,
а затем |
плоским концом трам |
По Я-ft |
||||
бовки. Лишнюю формовочную |
||||||
з / |
||||||
смесь спребают линейкой. Изго |
||||||
|
||||||
товленную полуформу перево |
|
|||||
рачивают и устанавливают на |
|
|||||
нее вторую опоку 4 и модель |
|
|||||
стояка. Операцию наполнения |
|
|||||
опоки и |
уплотнения |
смеси по |
|
|||
вторяют, |
после чего вырезают |
|
||||
литниковую |
чашу, |
вынимают |
|
|||
модель стояка и снимают верх |
|
|||||
нюю полуформу. На плоскости |
|
|||||
разъема |
в нижней полуформе |
|
||||
прорезают каналы, |
соединяю |
|
||||
щие стояк с полостью формы. |
|
|||||
Края формы |
вокруг |
модели |
|
|||
слепка |
увлажняют, |
|
модель |
|
||
расшатывают |
и вынимают из |
Рис. 85. Опоки: |
||||
формы. |
Поврежденные |
места |
1 — верхняя опока: 2 — нижняя опока; |
|||
исправляют, |
затем |
верхнюю |
3 |
|||
•полуформу устанавливают на |
|
нижнюю, скрепляют и форму заливают металлом.
И з г о т о в л е н и е фо р м в д в у х о п о к а х по р а з ъ е м ным м о д е л я м со с т е р жн е м . Под подмодельный щиток ставят нижнюю половину модели плоскостью разъема и накры вают нижней опокой. Процесс формовки в данном случае подо бен процессу формовки при изготовлении нижней полуформы по неразъемной модели. Когда нижняя полуформа готова, ее пово рачивают, посыпают поверхность формы разделительным песком и накладывают верхнюю половину на нижнюю половину модели, накрывают верхней опокой, устанавливают модели литникового канала шлакоуловителя, стояка и выпоров и производят процесс формовки в верхней полуформе. Когда верхняя полуформа заформована, на ней вырезают литниковую чашу, вынимают мо дели стояка и выпоров. Полуформу снимают и переворачивают. Выпоры по своей форме представляют подобие стояка. Их при меняют при отливке деталей из чугуна для того, чтобы образо-
15*

мощи чертилки проводят бороздки, соответствующие осям спиц. По каждой бороздке устанавливают рамку, вокруг которой очер чивают параллельные линии. Надевают на ось модель ступицы, устанавливают опоку, стояк и выпор и набивают верхнюю полуформу. Вынимают стояк и выпор, полуформу снимают и перево рачивают.
По отпечатанным бороздкам в верхней и нижней полуформе специальным гребком при помощи рамки делают контуры спиц и вынимают модель ступицы. Затем верхнюю полуформу устанав ливают на нижнюю, накладывают груз и форма готова для за
ливки металлом.
Машинная формовка. Процесс изготовления форм машинным способом по сравнению с ручным имеет ряд преимуществ:
1) механизацию уплотнения формовочной смеси и извлече
ния моделей из формы; 2) получение форм с более равномерным уплотнением и боль
шей прочностью; 3) получение отливок с меньшими припусками на обработку;
4)более рациональное использование труда формовщиков, которые освобождаются от ряда операций (установки моделей, набивки форм, прорезки литников и т. п.);
5)более быстрое освоение приемов формовки.
Формовочные машины по способу уплотнения в основном де лятся на следующие типы: прессовые, встряхивающие, встряхи вающие с подпрессовкой, пескометы.
Н а п р е с с о в ы х м а ш и н а х формы изготовляются по од носторонним модельным плитам. Машины приводятся в действие сжатым воздухом давлением 5—7 атм и подразделяются на ма-
Рис. 88. Схема верхнего |
Рис. 89. |
Схема нижнего |
|||
прессования: |
прессования: |
|
|||
1 — колодка; |
2 — наполни |
I — колодка; 2 — опока; |
3 — |
||
тельная |
рамка; |
3 — опока; |
наполнительная рамка; |
4 — |
|
4 — крепление модели к пли |
модель; |
5 — подмодельная |
|||
те; |
5 — модель |
|
плита |
|
чения формы на подмодельную плиту, укрепленную на столе ма шины, ставят опоку, которую из бункера заполняют формовоч ной смесью. Затем поворачивают траверсу с верхней плитой в рабочее положение и включают воздух.
Сжатый воздух поднимает стол и прижимает форму к верх ней плите траверсы. Дают небольшую выдержку, включают воз дух, опускают стол с формой и выводят его из под траверсы. Форму снимают и на стол ставят следующую опоку. Прессовую машину применяют для изготовления форм в опоках небольшой высоты, так как уплотнение формовочной смеси происходит не равномерно. Поверхность формы, непосредственно испытыва ющая давление, уплотняется больше, чем поверхность, прилега ющая к подмодельной плите и модели.
Примером этого типа машин является машина модели ПФ-4 с нижним прессованием. Размеры опоки в свету 756 X 676 мм, высота ее 100 мм. Часовая производительность (при полной ме