
Механическое оборудование предприятий по производству вяжущих строи
..pdf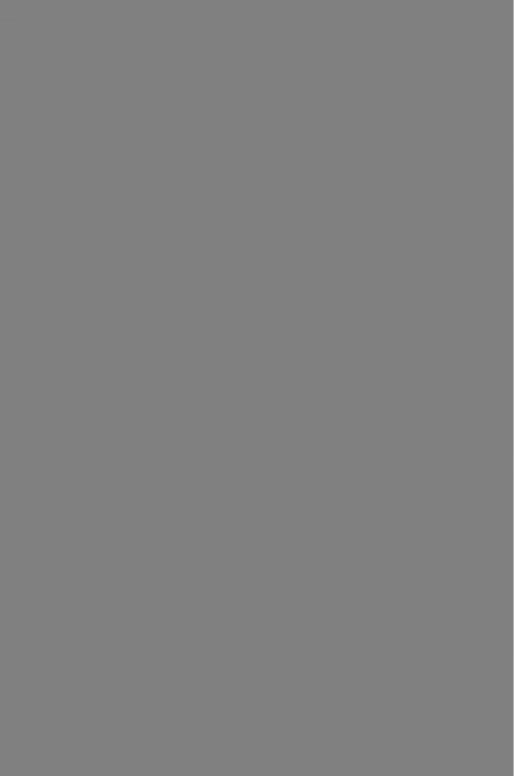
личаясь простотой изготовления, эти перегородки имеют неболь шую долговечность.
В настоящее время проводятся испытания наклонной междукамерной перегородки, принципиальное отличие которой в том, что она установлена под некоторым углом к оси вращения мельницы (обычно 42,5°). Особенностями наклонной перегородки являются: появление циклических изменений длины камеры, что вызывает дополнитель ное продольное движение мелющих тел и материала вдоль оси мель ницы; выполнение перегородкой функции встроенного классифика тора, отделение мелких частиц измельчаемого материала из камеры грубого помола и принудительное их перемещение в последующие камеры.
§ 54. Смазочная система и система гидроподпора
Для смазывания основных узлов трения трубных мель ниц применяют минеральные и пластичные смазочные материалы. При использовании минеральных масел применяют различные ме тоды смазывания — непрерывное, периодическое, циркуляционное, смазывание погружением и под давлением, смазывание масляным туманом и др. При использовании пластичных смазочных материа лов применяют ресурсное смазывание (одноразовое перед началом работы), смазывание набивкой, под давлением и др.
В зависимости от вида смазочные материалы бывают жидкие, пластичные и газообразные.
По характеру циркуляции смазочного материала смазочные си стемы бывают проточные и циркуляционные. В проточных системах смазочный материал подается к трущимся поверхностям периоди чески небольшими порциями, используется в работе один раз и в резервуар системы не возвращается. Все системы с использованием пластичного смазочного материала являются проточными. В цирку, ляционных системах применяют только жидкие смазочные матери алы, циркулирующие многократно между узлом трения и резерву, аром. При этом масло, сливающееся самотеком в резервуар, подвер. гается непрерывной очистке перед его повторной подачей к узду трения.
В смазочной системе мельницы 4,2x10 м (рис. 57) сочетает^ большинство перечисленных способов смазывания. Схемой преду. смотрено смазывание следующих узлов мельницы: цапфовых под. шипников (трубопроводы А подачи масла) — жидким смазочным материалом от циркуляционной системы (ЦСЖС-1) с подачу 125 л/мин под давлением до 0,4 МПа; подшипников качения вала под. венцовой шестерни (трубопроводы Б) и подшипников скольженця главного электродвигателя привода (трубопроводы В) — системой ЦСЖС-2 с подачей 50 л/мин под давлением до 0,4 МПа [слив масда из систем ЦСЖС-1 и ЦСЖС-2 показан штриховыми линиями (труб0_ проводы Д и £)]; открытое зацепление венцовой и подвенцовой шестерен (трубопровод Г) — пластичным смазочным материалом от
142
Рис. 57. Схема смазывания основных узлов трения мельницы 4,2Х 10 м
централизованной системы (ЦСПС) путем распыления форсунками смазочного материала струей сжатого воздуха на зубья венцовой ше стерни (графитовая смазка); редуктора вспомогательного привода и муфт зубчатых промежуточных соединений (на схеме не показаны)_ смазыванием погружением (КС); электродвигатель вспомогательного привода и опоры промежуточного вала (на схеме не показаны) — пластичными смазочными материалами от индивидуальной системы
смазывания (ИС).
Циркуляционные системы различных мельниц одинаковы и раз личаются лишь подачей, типом насосов и фильтров. В состав систем (рис. 58) входит следующее оборудование: резервуар 7 для масла; два насоса 5 с электродвигателями, один из которых рабочий, а вто рой резервный; два фильтра 4 с приводом; теплообменник (масло
охладитель) |
1 (при |
необходимости); |
трубопроводы напорный |
13 |
||
и сливной 11 |
и запорная |
арматура (вентили, задвижки, |
клапаны); |
|||
перепускной |
клапан |
2 ; |
аппаратура |
управления — один |
или |
два |
(в зависимости от наличия маслоохладителя) электроконтактных термометра 15 и 16; реле 8 уровня масла в резервуаре; два электро контактных манометра /7; технический манометр 18; технический дифференциальный манометр 19 для контроля перепада давления на фильтрах; командный электроприбор для автоматической очистки
фильтров.
При работе системы масло рабочим насосом 5 через плавающую всасывающую трубу подается из резервуара 7 в пластинчатые филь тры 4 , в которых происходит очистка масла от механических приме сей. Отсюда через маслоохладитель 1 (при его наличии) по напорному
трубопроводу 13 масло поступает к узлам трения 12. После смазы-
--------------лпялсамотеком-ГО!,'! по сливному трубопроводу 11 Вания всех узлов масло
возвращается в резервуар. В нем оно отстаивается, освобождается
от механических примесей и частично — от воды. Периодическая очистка масла в резервуаре осуществляется с помощью центробеж ного сепаратора 6 . Для улучшения отстоя, а также в холодное время года масло в резервуаре подогревается паром, подаваемым по паро проводу 9 с помощью мембранного вентиля с электромагнитным при водом. Вентиль включается при минимально допустимой температуре масла в резервуаре, а выключается при повышении температуры масла до нормальной. Команду на включение и выключение вентиля дает электроконтактный термометр /5, датчик которого 10 установлен на резервуаре и контролирует температуру масла.
Температура масла контролируется также после маслоохладителя с помощью датчика 14 и электроконтактного термометра 16.
При повышении температуры выше допустимого значения На пульт управления системой подается предупреждающий сигнал. Для непрерывного измерения давления масла до и после фильтров 4 применяют дифференциальный манометр 19. При нормальном пере паде давления на фильтрах замкнут минимальный контакт этого ма нометра и на пульте управления смазочной системой горит зеленая лампа. При загрязнении фильтров и увеличении перепада давления свыше допустимого замыкается максимальный контакт манометра и загорается сигнальная красная лампа.
Очистка фильтров 4 выполняется автоматически посредством включения их приводов от командного прибора КЭП или с помшцью датчика-реле разности давлений. Периодичность включения устанав ливается в зависимости от условий работы системы и смазываемых узлов трения и составляет 6—12 ч. Продолжительность включения соответствует двум-трем оборотам патрона фильтра. В аварийных ситуациях, когда фильтры засорены и их приводы не включаютея
срабатывает перепускной клапан 2 и масло поступает к узлам тре
ния, минуя фильтры.
Для измерения давления масла в напорном трубопроводе за теплообменником установлен технический показывающий манометр 18 общего назначения. Для контроля давления масла в системе и авто матического включения резервного насоса на станции жидкого смазывания установлены два электроконтактных манометра
Уровень масла в резервуаре контролируют с помощью датчика 8 уровня поплавкового типа. К узлам трения 12 от напорного трубо провода 13 масло подается с помощью дроссельных распредели телей, снабженных регуляторами и указателями расхода масла. В системе смонтирован резервуар 3 давления (пресс-бак), давление воздуха в котором равно давлению в напорном трубопроводе.
Рассмотренные установки и различные способы смазывания в зна чительной мере используют также в схемах смазывания другого
оборудования для производства цемента.
В мельницах диаметром более 3 м предусматривают гидроподпор, заключающийся в подводе к цапфам мельницы в момент ее пуска и остановки масла под высоким давлением. В результате этого под цапфой появляется масляный клин и наблюдается незначительное «всплытие» (подъем) цапфы, что резко уменьшает силы трения между цапфой и вкладышем подшипника, снижая пусковые нагрузки на
двигатель и уменьшая износ пар трения.
Система гидроподпора (рис. 59) состоит из насосной установки, входящей в комплект мельницы и включающей в себя гидронасос 4, создающий давление 10 МПа, предохранительный клапан 5, масляный бак и фильтры для очистки масла, электроконтактные манометры 2 с электроаппаратурой, запорную аппаратуру 3 и трубопроводы 1 . Питание системы гидроподпора маслом, а также его очистка и подо грев при необходимости осуществляются от циркуляционной системы
жидкого смазывания мельницы (ЦСЖС).
§ 55. Расчет основных параметров трубной мельницы
и режимов ее работы]
Основными параметрами и режимами работы трубных мельниц являются: производительность, тонина (тонкость) помола, масса мелющих тел, коэффициент заполнения мельницы мелющими телами, частота вращения мельницы, мощность привода.
Тонкость помола материала зависит т>т твердости размалывае мого материала. Размолоспособность различных сырьевых матери алов по сравнению с размолоспособностью клинкера, принимаемой за единицу, характеризуется следующими значениями: известняк —
1,2—1,8, опока — 1,3—1,4, гранулированный доменный |
шлак — |
|
0,8— 1, 1. |
размолоспособность материала |
|
Тонкость помола оценивают и |
||
сравнивают по остатку на ситах № |
02 (с-размером ячейки |
0,2 мм) |
и № 008 (с размером ячейки 0,08 мм) в процентах по массе или удель ной поверхности, определяемой по методу воздухопроницаемости.
(в |
Производительность |
трубной |
мельницы по сухому материалу |
|
т/ч) |
|
|
|
|
|
П = 6A5V у ~D0 (-£-)°’8 |
(76) |
||
где |
V — внутренний объем |
мельницы, |
м3; D0 — внутренний диаметр |
мельницы |
в свету, т. е. с учетом толщины футеровки, м; G — вес мелющих тел, Н; b — удельная производительность мельницы при заданной тонкости помола, т/(кВт-ч), для квар цевого песка b = 0,026 т/(кВт-ч), для клинкера и гранулированного шлама b = = 0,04 т/(кВт-ч), для известняка b = 0,042 т/(кВт-ч), для опоки b = 0,054 т/(кВт-ч);
6 — поправочный коэффициент на тонкость |
помола; г) — коэффициент, зависящий |
от схемы помола, для открытого цикла r| = |
1 (для замкнутого цикла г| — 1,2-т-1,2). |
Поправочный |
коэффициент |
б |
1 при |
помоле с остатком 10 % |
|
на сите № 008, |
б = 0,9-=-Э,8 |
с |
остатком 8—6 %. |
||
|
D0 |
- (0,94-^0,95) D, |
(77) |
||
где D — внутренний |
диаметр |
барабана |
мельницы, |
м. |
Массу мелющих тел (в т) ориентировочно определяют из уравне
ния |
|
|
|
|
т = 0,785DoLcpmK, |
(78) |
|
где L — длина барабана, м; |
ф — коэффициент заполнения |
мелющими телами, |
|
для шаровой загрузки в первой камере Ф |
0,29-:-0,32, для цильпебсных камер ф |
||
= 0,25-н0,3; mv — средняя |
плотность |
мелющих тел, т/м3, |
ту — 4,6. |
Частота вращения мельницы, строго определенная для каждого типоразмера мельницы, зависит от ее диаметра. Каждому диаметру барабана мельницы свойственна так называемая критическая ча стота вращения, при достижении которой за счет действия центро бежных сил мелющие тела будут вращаться, не отрываясь от его внутренней поверхности.
Критическая частота вращения барабана мельницы (в об/мин)
пкр = 42,3/17 Д,. |
(79) |
Рабочая частота вращения, когда мелющие тела падают на слой размалываемого материала, определяется коэффициентом запаса \р — 0,75:
п = фякр = 0,75 • 42,3/т/ Д) = 31,7/]/ D0. |
(80) |
При подборе параметров электродвигателя и редуктора привода мельницы частота вращения ее не должна превышать ±1 % частоты, рассчитанной по формуле (80).
Расчет мощности привода мельницы теоретически представля ет определенные трудности, связанные с хаотическим движением загружаемых в мельницу материала и мелющих тел при вращении барабана, различием физико-механических свойств размалываемого материала и соответствующего подбора размеров и массы мелющих тел. В связи с этим для определения мощности электродвигателя ис пользуют различные эмпирические зависимости.
В соответствии с исследованиями В. В. Товарова мощность, не обходимая для помола твердых пород в трубной мельнице (в кВт),
Na = 6,55V /D o ( А ) 0’7 |
(81) |
С учетом потерь на трение в приводе и запаса мощности при пуске загруженной мельницы мощность электродвигателя принимают на 30 % больше.
Пример 23. Рассчитать основные параметры и режимы работы двухкамерной
трубной мельницы производительностью 100 т/ч для помола по открытому циклу опоки средней прочности с остатком до 10 % на сите N° 008.
Р е ш е н и е . Для определения требуемой массы мелющих тел в соответствии с фор мулой (78) и с учетом физико-механических свойств опоки предварительно при нимаем минимальное значение коэффициента заполнения ср.
Среднее значение коэффициента заполнения мелющих тел для двух камер мель ницы
0,29 + 0,25 Ф= — . — 0,27.
При плотности мелющих тел т,у = 4,6 т/м3 их масса
т = 0,7851)2Ь0,27.4,6 = 0,975D%L т.
Подставив полученное значение в формулу (76), получим
П = 6,45К ]/"D0 ( 0,975P0Ly .8 ^ т/ц
С учетом заданных( условий принимаем значения коэффициентов 6 = 1 т] .-= 1
иb — 0,042 т/(кВт-н). Тогда
П= 6,45К \f~D 0 ( ° ’97^ У ’8 !. j .0|042 = 0.265К |^D0 ( - ^ - ) ° ’8
Параметры V, D |
и L |
взаимосвязаны уравнением |
V = ^Dg/(j)L). Тогда |
|
Я = |
0,265 |
4 |
L V D 0 ( 4 § | г ) М = |
° ’252D^ L* |
|
|
|
|
|
|
|
|
D8" i - O l l 2 “ 39M' |
(82) |
|||||
|
|
|
|
|
||||||
= |
4 |
Предварительно принимаем отношение длины корпуса к его диаметру L : D = |
||||||||
1. Откуда L = |
4D 0. Тогда |
|
|
|
|
|
||||
|
|
' |
Dg’5.4D0 = |
396,8 |
или |
Д, = 3,72 м. |
|
|||
|
|
Исходя из формулы (77), получим внутренний диаметр барабана мельницы |
||||||||
|
|
£> : |
Р 0 |
|
|
3,72 |
|
|
||
|
|
0,94 н- 0,95 |
0,94 -- 0,95 = 3,95 -ь 3,91 м. |
|||||||
|
|
С учетом существующего типажа на параметры мельниц (см. табл. 29) принимаем |
||||||||
D |
= |
4 м. |
|
|
|
|
|
|
|
|
|
|
Уточненный диаметр мельницы в свету по формуле (77) |
|
|||||||
|
|
|
D о = |
(0,94-^0,95)D |
= |
3,76^3,8 м. |
|
|||
|
|
Принимаем D 0 = |
3,8 м. |
|
|
в |
уравнение (82), |
получим |
||
|
|
Подставив полученное значение D0 |
||||||||
|
|
|
3,82-5/. = 396,8, откуда |
L = 1 4 , 1 M. |
|
|||||
|
|
Принимаем L = |
14 м. |
|
|
|
|
|
|
|
|
|
Внутренний объем мельницы |
|
|
|
|
|
|||
|
|
|
V = |
nDl |
3,14• 3,82 |
14= 158,7 м3. |
||||
|
|
|
|
4 |
|
|
4 |
|
|
|
|
|
По формуле (78) определяем необходимую массу мелющих тел: |
||||||||
|
|
|
т = |
0,785-3,82-14-0,27-4,6 = 197,1 т. |
|
|||||
|
|
Уточненная производительность мельницы по формуле (76) |
||||||||
|
|
П = 6,45-158,7 J /M ( Щ |
4 ) ° |
* 1 ‘ 1■°’054 = |
127,5 т> |
|||||
|
|
Рабочую частоту |
вращения мельницы определяем по формуле (80): |
|||||||
|
|
|
п = |
31,7/(/"3,8 = |
16,26 об/мин. |
|
||||
|
|
Для выбора привода допустимый диапазон рабочей частоты вращения мельницы |
||||||||
|
|
п ' = 16,26 ± |
16,26 ^ |
= |
16,26 ± |
0,1626 = 16,09 |
16,42 об/мин. |
|||
|
|
Мощность, необходимая для |
помола, |
в соответствии с |
формулой (81) |
|||||
|
|
N a = 6,55-158,8 / О |
( ]Т ^ 4 )0’7 = 2347,3 кВт. |
|||||||
|
|
Мощность электродвигателя должна быть не менее |
|
N = 1,ЗМП= 1,3-2347,3 = 3051,5 кВт.
Для мельницы 4X14 м, рассчитанной в данном примере, подходит серийный привод мельницы размером 4Х 13,5 м обеспечивающий частоту вращения мель
ницы 16,2 об/мин и мощностью 3200 кВт (см. табл. 29). 148
Г л а в а 12
ОБОРУДОВАНИЕ ДЛЯ УСРЕДНЕНИЯ И ХРАНЕНИЯ СЫРЬЕВЫХ СМЕСЕЙ
§ 56. Оборудование усреднительных складов
Усреднение сырья на складах применяют в основном при сухом способе производства. Сущность этого метода заключается в складировании сырья послойно в крупные гряды и срезании слоя определенным образом, добиваясь смешивания всех слоев гряды и усреднения состава смеси. Для усреднения сырья в смесительных грядах применяют открытые площадки или крытые складские по мещения.
Смесительная гряда является одновременно промежуточным скла дом и установкой для предварительного усреднения. Большая вместимость смесительных гряд (20—35 тыс. т) в сочетании с отно сительно легким доступом к ним дает возможность синхронизиро вать работу карьера (передела периодического действия) с непреры вно действующей технологической линией. Обеспечивается рацио нальная разработка карьера путем перехода к односменной работе, а создание больших запасов материала в грядах гарантирует не прерывною работу мощных печей.
Смесительная гряда имеет особые значения для складирования пластичных материалов, которые трудно перемешивать другим путем, например, в силосах. Во избежание расслоения материала в гряде его обязательно предварительно дробят.
Системы смесительных гряд делятся на два типа: интегрирующие (многокомпонентные) гряды и однокомпонентные штабеля. При использовании интегрирующих гряд отдельные сырьевые компо ненты после дозирования укладывают слоями один на другой так, чтобы их соотношение в поперечном сечении штабеля соответство вало заданному составу сырьевой смеси. Чтобы обеспечить эффект усреднения, отдельные компоненты во время отсыпки анализируют. После укладки последнего слоя на основании результатов анализов проводят корректирование.
В однокомпонентных штабелях производят предварительное ус реднение сырьевых материалов с последующим их дозированием. Как правило, штабель формируют в направлении продольной оси, а затем отбирают материал в поперечном направлении.
Существуют несколько способов укладки материалов в штабеля: шевронный, отсыпки полосами, навалки тонкими горизонтальными слоями и др.
При шевронном способе (рис. 60, а) материал подается ц штабель над его серединой так, что отдельные слои накладываются друг на друга как бы в виде крыш.
При способе отсыпки полосами (рис. 60, б) слои материала имеют форму продольных полос, расположенных рядом или одна над дру гой, что почти исключает возможность отделения крупных кусков.
Н И И 1 Н
•)
Рис. 60. Схемы укладки штабелей
Однако такой способ штабелирования требует применения сложных и дорогих ленточных сбрасывателей, которые во время отсыпки дол жны в каждом поперечном сечении занимать различные рабочие по зиции.
При способе навалки тонкими горизонтальными слоями (рис. 60, б), слои лежат один на другом и покрывают всю площадь штабелирования.
Имеются и другие способы укладки, однако они по ряду причин не нашли достаточно широкого применения.
Основным оборудованием усреднительных складов являются установки для формирования штабелей — штабелеукладчики и для выемки усредненного сырья — штабелеразборщики.
Наиболее широко применяются штабелеукладчики с разгру зочной тележкой (рис. 61, а). Сырьевые материалы ленточным тран спортером 5, расположенным перпендикулярно к оси штабеля, через бункер 4 с питателем подаются на бесконечную ленту 1 штабелеук ладчика. С ленты с помощью сбрасывающего механизма материалы поступают в приемное устройство разгрузочной тележки 6 и далее через ленточный транспортер 5 укладываются в штабель 2, обычно шевронным способом. Разгрузочная тележка перемещается вдоль штабеля по рельсам. Привод основных узлов штабелеукладчика электромеханический. Транспортер 5 с помощью специальных уст ройств может подниматься и опускаться. В некоторых конструкциях штабелеукладчиков имеется возможность поворота его вокруг верти кальной оси разгрузочной тележки на поворотной платформе, чт0 позволяет формировать два параллельных штабеля (в то время, когда один формируется, другой разбирается).
Для укладки в штабель применяют штабелеукладчики других типов: скребковые (портальные, двухрельсовые с боковой отсыпкой и др.); телескопические ленточные транспортеры для формирования штабелей при отсыпке полосами; поворотные ленточные, вращав, щиеся вокруг своей оси, для отсыпки кольцевых штабелей (преиму. щественно в крытых складах) и др.
Выемку материала производят в основном с помощью штабеле разборщиков скребкового или роторного типа. Обычно штабели раз. рабатывают с торцов и выбирают плоскими слоями. Каждый из них по качеству в среднем соответствует смеси в штабеле.
Скребковый штабелеразборщик (рис. 61, б) представляет собой конструкцию, состоящую из собственно скребкового транспортера у
150