
Аэрокосмическая техника высокие технологии и инновации – 2014
..pdf–каталитическая изомеризация перекиси 4-изопропенил-фенола перекисью водорода в кислой среде до ГХ. Непрерывный способ крупнотоннажного производства ГХ реализован в США. Недостатки каталитической изомеризации в периодическом способе производства связаны с высокой скоростью полимеризации 4-изопропенилфенола (30–60 с), высоким экзоэффектом при образовании гидроперекиси и кислотной изомеризациипоследней вГХ [6].
Анализируя описанные выше методы синтеза ГХ, необходимо отметить, что наиболее приемлемым является окисление анилина двуокисью марганца или хромовой кислотой до хинона, который восстанавливают порошком железа в воде в присутствии бисульфита натрия. На стадии окисления требуется активная (не менее 85 %) двуокись марганца [7]. Активность двуокиси марганца зависит в основном от способа ее получения, условий и сроков хранения, содержания основного вещества [8]. К проблемам реализации данного метода синтеза ГХ относятся неудовлетворительное качество образцов окиси марганца (II) от различных поставщиков, а также потери хинона на стадиях выделения из реакционной среды непрореагировавшей двуокиси марганца, раствора сульфата марганца (2+), водного раствора серной кислоты. По этим причинам в качестве окислителя выбран бихромат натрия [9].
На стадии восстановления хинона за рубежом в основном ис-
пользуют железные порошки, ронгалит, SO2, N2H4, H2O. Ввиду того что российские предприятия порошковой металлургии не производят порошки железа, удовлетворяющие техническим требованиям технологического процесса восстановления хинона, при разработке технологического процесса ГХ выбран в качестве восстановителя гидразингидрат [10, 11].
Разработана двухстадийная периодическая схема производства ГХ, реализуемая по схеме:
–стадия окисления
2PhNH2 |
5H2SO4 4MnO2 2p-Qn 4MnSO4 |
|
(1) |
|
NH4 2 SO4 4H2O |
|
|
|
|
|
|
|
71 |
|
|
2PhNH2 6H2SO4 Na2Cr2O7 p-Qn NaHSO4 |
(2) |
||
Cr2 SO4 3 NH4 2 SO4 H2O |
|
||
|
|
||
– стадия восстановления: |
|
|
|
|
2 |
|
|
Mn |
|
H2O |
(3) |
p-Qn N2H4 H2O H2O H2Qn N2 |
|||
p-Qn SO2 2H2O H2Qn H2SO4 , |
|
(4) |
где H2Qn – гидрохинон; p-Qn-п – бензохинон, PhNH2 – анилин. Первую стадию технологического процесса проводят в два
этапа. На первом этапе получают раствор сернокислого анилина дозированием при перемешивании дистиллированной воды, серной кислоты и анилина, охлаждением раствора до температуры 0–2 С и при непрерывном перемешивании дозируют в течение 2,5–3,5 ч первую часть 20%-го водного раствора бихромата натрия.
На втором этапе после статической выдержки при перемешивании дозируют оставшуюся часть 20%-го водного раствора бихромата натрия при температуре 0–2 С в течение 2,5–3,5 ч и дают статическую выдержку.
Для улучшения санитарно-гигиенических условий ведения периодического технологического процесса фаза фильтрации хинона [9] заменена фазой экстракции его толуолом. Реакционную массу после статической выдержки трехкратно экстрагируют толуолом, отделяют экстракт хинона и направляют на стадию восстановления.
Восстановление толуольного экстракта хинона ведут дозированием раствора гидразингидрата в водный раствор 3–5,0%-го сернокислого марганца (II), используемого в качестве катализатора. Раствор сернокислого марганца используется один раз, так как при повторном использовании наблюдается образование нерастворимого комплекса, что требует увеличения времени выдержки и снижает выход и качество гидрохинона.
Экспериментально установлено, что оптимальное объемное соотношение толуольного экстракта к водному раствору сульфата марганца (II) составляет от 3 до 4, что обеспечивает качество гидрохинона, соответствующего требованиям ГОСТ 19627-74 (таблица).
72
Физико-химические показатели гидрохинона по ГОСТ 19627-74
Наименование показателей |
Нормы для сортов |
||
высшего ОКП 24 |
первого ОКП 24 |
||
|
7212 0120 05 |
7212 0130 03 |
|
Массовая доля гидрохинона, % |
99–101 |
99–101 |
|
Цветность по бихроматной шкале, |
12 |
20 |
|
не более |
|||
|
|
||
Температура плавления, С |
171–175 |
170–175 |
|
Массовая доля потерь |
0,1 |
0,1 |
|
при высушивании, %, не более |
|||
|
|
||
Массовая доля остатка после |
0,03 |
0,08 |
|
прокаливания, %, не более |
|||
|
|
||
Массовая доля железа (Fe), %, |
0,002 |
0,010 |
|
не более |
|||
|
|
||
Массовая доля тяжелых металлов |
0,0005 |
0,002 |
|
(Pb), %, не более |
|||
|
|
||
Растворимость в разбавленной |
ГОСТ 19627-74 |
Не нормируется |
|
уксусной кислоте |
|||
|
|
При объемных соотношениях менее 3 гидрохинон по показателю цветности превышает 12 и требует проведения операции очистки бисульфитом натрия, а при более 4 уменьшается выход продукта.
Гидразингидрат дозируют в течение 30 мин при температуре 5–8 С и непрерывном перемешивании. Выдерживают 1 ч, затем раствор фильтруют и отделяют толуольный слой. Образовавшийся гидрохинон из водного раствора трехкратно экстрагируют этоксиэтаном, экстракт сушат безводным сернокислым магнием и отгоняют растворитель. Максимальный выход продукта составляет 74 %.
Новизной данного способа производства гидрохинона является применение операций экстракции толуолом и этоксиэтаном для передачи гидрохинона между фазами восстановления, очистки и выделения. Фаза восстановления хинона в гидрохинон раствором гидразингидрата выделена в отдельную фазу по сравнению с [12], что позволило повысить качество гидрохинона сырца до показателей высшего сорта по ГОСТ 19627-74. Все емкостные аппараты работают в атмосфере азота, а парогазовые выделения улавливают в адсорбционной установке счастичнымвозвратом толуола иэтоксиэтана в техпроцесс.
73
Утилизацию отработанных растворов стадии окисления сернокислого анилина бихроматом натрия проводят с помощью доведения рН сточных вод до 7 техническим карбонатом натрия и выделением осадка углекислого хрома в осадительной центрифуге. Осадок углекислого хрома упаковывают в полиэтиленовые мешки и хранят на накопительной площадке для последующей реализации на сторону. Водный раствор сульфатов натрия, аммония с органическими соединениями обрабатывают озоном в реакторе-утилизаторе до полного окисления органических примесей, разбавляют оборотной водой до требуемых концентраций и сбрасывают на биоочистку.
Отработанный раствор стадии восстановления хинона в гидрохинон направляют в реактор-утилизатор и озонируют до отсутствия Mn+2 в пробах водного раствора. Далее его подают на осадительную центрифугу и выделяют MnO2, который промывают, сушат и фасуют в полиэтиленовые мешки для последующей реализации или повторного использования. рН водного раствора после центрифуги доводят до 7 с помощью углекислого натрия, разбавляют оборотной водой и сбрасывают на биоочистку.
Список литературы
1.Отчет о НИР/НИИПМ; Руководитель работы: Г.В. Куценко.
Инв. № 24215. – Пермь, 2006. – 67 с.
2.Закономерности каталитического гидроксилирования фенола пероксидом водорода / А.И. Михайлюк, С.В. Тимофеев [и др.] // Катализ и каталитические процессы химфенилпроизводств: тез. докл. 2-й Всесоюз. конф. Ч. 1 / Всесоюзн. науч.-исслед. хим.-технол. ин-т мед. и микробиол. пром-сти. – М., 1989. – С. 234–236.
3.Пат. 4578521, США. Shape-selection catalytic oxidation of phenol. Chang Clarence D., Hellurg Stuart D., Mobil Oil Corp., заяв. 4.02.85;
№697804; опубл. 25.03.86.
4.Заявка 55-59124 Япония. Способ получения гидрохинона.
кл. С 07 С 39/08, С 07 С 37/60, заявл. 27.10.78, №53-131710; опубл. 2.05.80; РЖХ 16Н125П, 1981 г.
5.Пат. 4258219, США. Способ получения гидрохинона. НКИ кл. С07 С37/01, заявл. 19.10.1979; опубл24.03.81; РЖХ, 23Н145П, 1981 г.
74
6.Новые пути синтеза дигидроперикисей диалкилбензолов В.К. Цысковский, И.В. Цысковская [и др.] // Хим. промышлен-
ность. – 1976. – № 7. – С. 13–15.
7.Пат. 870698 ФРГ, НКИ В 73 Ivc/12q/ Verfahren zur Herstellung von Hydrochinonen / Badische Anilin und Sod-Fabrik, 1G Farbenindustrie; заявл. 8.07.1949; опубл. 16.03.1953.
8.Регенерация соединений марганца в производстве гидрохинона / С.М. Соколова, Н.Н. Иванова, Б.А. Пономарев, В.А. Якоби // Изв. высш. учеб. заведений. – 1977. – Т. 20, № 4. – С. 478.
9.Карякин Ю.В., Ангелов И.И. Чистые химические вещества. –
М.: Химия, 1974.
10.Пат. 67030 СРР. Способ и установка для получения гидрохинона из анилина., МКИ С 07 С 39/08; заявл. 3.07.75, №82741,
опубл. 15.01.80.; РЖХ 11Н145П, 1981 г.
11.Прянишников Н.О. Практикум по органической химии. – М.: Гос. наука, 1956.
12.Пат. 116276 ПНР. Способ выделения гидрохинона; заявл. 21.10.78, №210429, опубл. 30.11.82, МКИ С 07 С 39/08, РЖХ. 20Н152П, 1983 г.
РАЗРАБОТКА ТЕХНОЛОГИИ ПО УСТРАНЕНИЮ ПОВРЕЖДЕНИЙ НА ЛОПАТКАХ МОНОКОЛЕС ГТД С ПРИМЕНЕНИЕМ ИМПУЛЬСНОЙ ЛАЗЕРНОЙ НАПЛАВКИ (LMD)
Е.В. Кондрашов1, А.С. Ермолаев2, А.М. Иванов2
1Пермский национальный исследовательский политехнический университет, Пермь, Россия
2ОАО «Авиадвигатель», Пермь, Россия
e-mail: tukachev-dv@avid.ru, ermolaev-as@avid.ru, ivanov-am@avid.ru
Представлена технология восстановления лопаток компрессора авиационного двигателя посредством газопорошковой лазерной наплавки. Описана актуальность применения данной
75
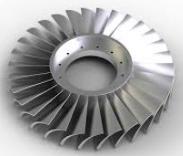
технологии, а также ее преимущества перед электродуговыми способами восстановления. Даны теоретические сведения по LMD-обработке. Приведены краткие сведения по применяемому оборудованию, которое используется для проведения наплавки, и основные параметры технологического процесса.
Внастоящее время при проектировании ГТД предполагается использование современных конструктивных решений. Для улучшения газодинамических характеристик компрессора в его конструкции используют моноколеса (рис. 1.) – ступени, изготовленные по технологии blisk.
Однако в процессе эксплуатации в составе авиационного двигателя лопатки моноколеса испытывают вибрации и удары, подвергаются абразивному износу, воздействию высоких температур и прочих негативных факторов. Это, в свою очередь, приводит к образованию трещин, забоин, изменению прочностных характеристик
иискажению геометрии профиля каждой лопатки.
Всравнении срабочими колесами сборнойконструкции восстановление поврежденных лопатокмоноколес осложнено невозможностью
заменить поврежденные лопатки. Требуется крайне дорогостоящая замена моноколеса целиком, поэтому восстановление моноколес сегодня является актуальной задачей. К тому же в процессе анализа повреждаемости рабочих лопатокустановлено, чтооколо70 % их общего числа составляют повреждения глубиной 0,4–2,0 мм [1]. В мировой
Рис. 1. Моноколесо практике восстановление лопаток с подобными дефектамиосуществляется
лазерной наплавкой (LMD). Следует также отметить, что стоимость восстановления таких деталей в разы дешевле, чем создание новых, к тому жеремонтосуществляется в самые короткие сроки.
Поскольку реальная геометрия каждой лопатки моноколеса отличается от номинальной геометрии CAD модели, для осуществ-
76
ления ремонта лопаток необходимо применять адаптивные методы обработки, в частности метод адаптивной наплавки. Такие методы обработки отличаются от стандартных тем, что созданные по номинальной геометрии модели ЧПУ программы обработки проходят индивидуальную адаптацию к геометрии каждой лопатки.
LМD (Laser Metal Deposition) – это разновидность лазерной наплавки, при которой металл послойно наносится на поверхность восстанавливаемых деталей. Под действием лазерного луча на поверхности обрабатываемого изделия формируется ванна расплава, в которую из специального сопла подается металлический порошок. В ванне порошок плавится и прочно связывается с поверхностью основного металла, образуя покрытие. Это покрытие формируется в виде «дорожки». Несколько «дорожек», уложенных с перекрытием, образуют слой. Слои поочередно укладываются друг на друга для получения требуемой высоты наплавки [2]. Для предотвращения окисления расплавленного металла зону наплавки защищают инертными газами (Ar, He) . После лазерной наплавки требуется механическая обработка для придания поверхности необходимой геометрической формы, размеров и шероховатости [1].
Кроме того, метод лазерной наплавки имеет следующие преимущества в сравнении с электродуговыми методами обработки:
–минимальное термическое воздействие наосновнойматериал;
–минимальные остаточные деформации;
–восстановление тонких поверхностей со сложным профилем геометрии;
–локальность обработки;
–минимальные припуски под механическую обработку;
–высокая точность воспроизводимости.
Также следует отметить, что при использовании импульсной лазерной наплавки достигается высокая скорость охлаждения жидкой фазы расплава, в результате чего реализуется режим автозакалки, обеспечивающий формирование мелкодисперсной структуры с высокой износостойкостью [2].
На ОАО «Авиадвигатель» разрабатывается технология газопорошковой лазерной наплавки для ремонта торца пера, а также вход-
77
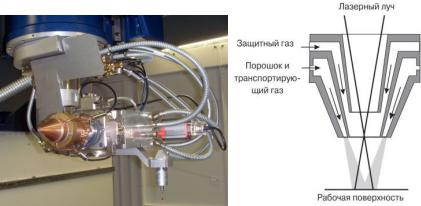
ной и выходной кромок лопаток в составе моноколеса КВД, поскольку эти области наиболее подвержены повреждениям. Работы ведутся на установке TruLaser Cell 7020 фирмы TRUMPF (Германия), которая оснащена твердотельным 2 кВт дисковым лазером TruDisk 2001, оптическим устройством с фокусным расстоянием 200 мм, коаксиальным соплом (рис. 2.) с системой видеонаблюдения. Адаптивность процесса наплавки обеспечивается применением программного паке-
та «OpenArms» фирмыBCT.
а |
б |
Рис. 2. Оптическое устройство (а) и функциональная схема его коаксиального сопла (б)
Наплавка предусматривает восстановление входной и выходной кромок лопатки (7 мм), а также торца пера (5 мм) с обеспечением припуска в пределах 0,4–1,0 мм на сторону под механическую обработку. Перед наплавкой восстанавливаемые области предварительно отфрезерованы. Изначально работа проводилась в непрерывном режиме в связи с тем, что толщина наплавляемой поверхности на входной и выходной кромках составляют менее 1 мм, постоянный режим не позволил подобрать оптимальные параметры, обеспечивающие сплавление присадочного порошка и материала лопатки без подреза в месте выхода на тонкую кромку с радиусом 0,3 мм. Переход с режима наплавки непрерывным лазерным излучением на
78
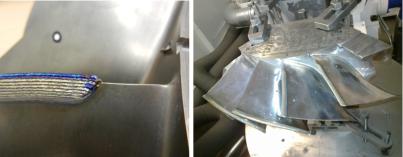
импульсно-периодическое лазерное излучение позволил решить проблему с подрезом. Программы наплавки создавались по CADмодели с использованием срединного сечения лопатки. Все пятикоординатные ЧПУ-программы наплавки адаптировались в ПО OpenArms. В ходе работ были получены оптимальные режимы наплавки титанового порошка Ti6Al4V (отечественный аналог ВТ6), разработаны основные стратегии создания ЧПУ-программ, выполнена наплавка входной, выходной кромок и торца сектора моноколеса 1-й ступени КВД сначала на постоянном, а затем и в импульсном режиме (рис. 3). Была также произведена наплавка выходных кромок лопаток полноразмерного моноколеса, поврежденного в ходе испытанийдвигателя.
а |
б |
Рис. 3. Наплавленная выходная кромка (а); входная кромка и торец лопатки (б) сектора 1-й ступени КВД двигателя ПД-14
После наплавки лопатки подвергаются визуальному и ЛЮМ- 10В-контролю на наличие недопустимых дефектов наплавки, таких как поры и несплавления, горячие трещины, оценивается величина припуска под механическую обработку.
Список литературы
1.Сварка и диагностика. – 2009. – № 5. – С. 41–46.
2.Гибридные технологии лазерной наплавки: учеб. пособие / А.М. Забелин, И.Н. Шиганов, А.М. Чирков, Ю.А. Хрусталев. – М., 2006. – 19–34 с.
79
ЭКСПЕРИМЕНТАЛЬНАЯ ОЦЕНКА ВЛИЯНИЯ НАПРАВЛЕНИЯ ВЫРЕЗКИ ОБРАЗЦОВ ИЗ ЗАГОТОВКИ НА ПРЕДЕЛ ВЫНОСЛИВОСТИ ТИТАНОВОГО СПЛАВА ПРИ ИСПЫТАНИЯХ НА МНОГОЦИКЛОВУЮ УСТАЛОСТЬ ПРИ РАЗЛИЧНЫХ ЦИКЛАХ НАГРУЖЕНИЯ
А.Н. Котельников
Пермский национальный исследовательский политехнический университет, Пермь, Россия
ОАО «Авиадвигатель», Пермь, Россия e-mail: kotelnikov@avid.ru
Предпринята попытка проверить влияние направления проката титановой плиты на характеристики сопротивления многоцикловой усталости образцов, вырезанных из нее. Испытания образцов проводились при коэффициентах асимметрии цикла R = 0; –1. Приведены краткие сведения о применяемом оборудовании, которое используется для определения характеристик МнЦУ. Были выполнены комплекс экспериментальных исследований образцов, статистический анализ экспериментальных данных и определены коэффициенты уравнений кривых усталости (вдоль и поперек проката и обобщенных кривых для каждой асимметрии цикла), а также значения пределов выносливости для каждого направления при каждойасимметриицикла.
На этапе проектирования деталей авиационных двигателей для определения их эксплуатационного ресурса используются характеристики усталости материала. Эти характеристики определяют путем испытания партии образцов с последующим построением кривой усталости (кривая Веллера).
Эксплуатационный ресурс деталей авиационного двигателя определяется ее циклической долговечностью, т.е. способностью материала воспринимать знакопеременную нагрузку. Одной из основных характеристик циклической долговечности является сопротивление многоцикловой усталости (МнЦУ).
80