
Аэрокосмическая техника высокие технологии и инновации – 2014
..pdf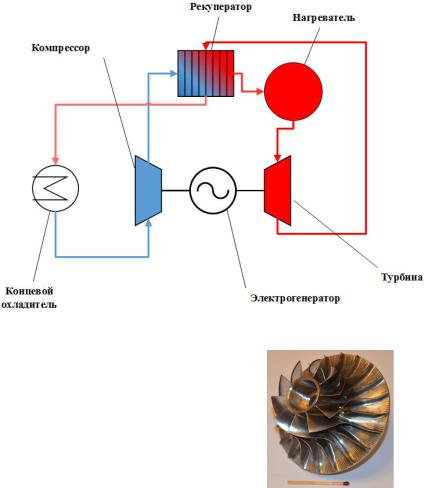
Рис. 1. Принципиальная схема замкнутой газотурбинной установки
Последний узел является ключевым элементом, определяющим работоспособность и эффективность установки. Данная работа посвящена исследованию характеристик малоразмерного центробежного компрессора на различных рабочих телах. Описание замкнутого стенда, методика обработки эксперимента и результаты тестовых экспериментов на воздухе изложены в работе [5].
Сравнение характеристик компрессора на различных рабочих телах, имеющих одинаковую молярную массу, представлено на рис. 3. При проведении эксперимента дроссельная заслонка была полностью открыта, частота вращения варьировалась от 23 700 до
21

30 300 мин–1. Как видно из графика, характеристика гелиексеноновой смеси лежит ниже, чем характеристика на аргоне. Вязкость аргона меньше вязкости гелий-ксеноновой смеси в 1,17 раза, следовательно, в проточной части центробежного компрессора потери на трение при работе на аргоне ниже, а к.п.д. выше, что и подтверждают экспериментальные данные. Влияние свойств рабочего тела на расчетные характеристики ступени ЦБК в рабочей точкепредставлено в таблице.
Рис. 3. Экспериментальные характеристики центробежного компрессора: 1 – степень повышения давления на гелиексеноне; 2 – степень повышения давлениянааргоне; 3 – к.п.д. нааргоне; 4 – к.п.д. нагелиексеноновойсмеси
Характеристика ступени ЦБК на различных рабочих телах
Наименование |
Обозначение |
Размерность |
Рабочее тело |
|
||
параметра |
Криптон |
Аргон |
|
Воздух |
||
Показатель адиабаты |
k |
– |
5/3 |
5/3 |
|
7/5 |
|
|
|
|
|
|
|
Молярная масса |
m |
кг/кмоль |
83,800 |
39,944 |
|
28,960 |
Газовая постоянная |
R |
Дж/(кг·К) |
99,210 |
208,153 |
|
287,200 |
22

Окончание таблицы
Наименование |
Обозначение |
Размерность |
Рабочее тело |
|
||
параметра |
Криптон |
Аргон |
|
Воздух |
||
Вязкостьприн.у. (273 К) |
µ |
1·10-5 Па·с |
2,510 |
2,220 |
|
1,71 |
|
|
|
(2,387)* |
(2,600)* |
|
|
Частота вращения |
n |
мин–1 |
40000 |
57939 |
|
66906 |
Расход |
G |
кг/с |
0,322 |
0,222 |
|
0,186 |
|
|
|
|
|
|
|
Мощность |
N |
кВт |
7,839 |
11,355 |
|
12,740 |
Окружная скорость |
U2 |
м/с |
188,50 |
272,99 |
|
315,29 |
Число Рейнольдса |
Re |
1·105 |
1,495 |
1,167 |
|
1,1269 |
|
|
|
(1,572)* |
(0,997)* |
|
|
* для гелиексеноновой смеси
Выводы
В малоразмерных лопаточных машинах на режимах частичной мощности на к.п.д. оказывает влияние вязкость рабочего тела.
Экспериментально получены характеристики ЦБК на аргоне
игелиексеноне (с молярной массой аргона) при полностью открытой дроссельной заслонке на модернизированном стенде при варьировании частоты вращения от 23 700 до 30 300 1/мин. Степень повышения давления составила 1,108 и к.п.д. 0,407.
Необходимо провести испытания центробежного компрессора с прикрытой дроссельной заслонкой и оценить тепловой поток от электродвигателя к улитке компрессора.
Работа выполнена при частичной поддержке Минобрнауки РФ (госзадание № 2014/104, код проекта 2092).
Список литературы
1.Ядерные газотурбинные и комбинированные установки / Э.А. Манушин, В.С. Бекнев, М.И. Осипов, И.Г. Суровцев. – М.: Энергоатомиздат, 1993. – 272 с.
2.Теория проектирования газотурбинных и комбинированных установок/ Ю.С. Елисеев, Э.А. Манушин, В.Е. Михальцев, М.И. Осипов, И.Г. Суровцев. – М.: Изд-во МГТУ им. Н.Э. Баумана, 2000. – 640 с.
23
3.Арбеков А.Н., Леонтьев А.И. Развитие космических газотурбинных установок в работах В.Л. Самсонова // Труды МАИ. – 2011. – Вып. 43.
4.Арбеков А.Н. Выбор рабочего тела для замкнутых газотурбинных установок мощностью от 6 до 12 кВт, работающих на органическом топливе // Теплофизика высоких температур. – 2014. –
Т. 52, №1. – С. 131.
5.Арбеков А.Н., Новицкий Б. Б. Экспериментальное исследование характеристик ступени малоразмерного центробежного компрессора [Электронный ресурс] // Наука и образование. – 2012. –
№8. – URL: http://technomag.edu.ru/doc/432308.html (дата обращения: 18.05.2014).
РАСЧЕТ ОТНОСИТЕЛЬНОГО РАСХОДА МАСЛА ЧЕРЕЗ МАСЛОЗАХВАТ
И.В. Ардашкин
Пермский национальный исследовательский политехнический университет, Пермь, Россия
e-mail: ilyaardashkin@gmail.com
Разработана упрощенная методика проведения расчета относительного расхода масла в роликоподшипник турбины высокого давления через маслозахват. Данная методика основана на определении траектории масла в относительном движении. Проведено сравнение результатов расчетов относительного расхода масла через маслозахваты различной конструкции с экспериментальными данными. Определены пути усовершенствования методики расчетаотносительногорасходамаслачерезмаслозахват.
Надежная работа подшипников газотурбинных двигателей зависит от организации подачи масла на подшипники. Масло, подаваемое на подшипники, предназначено как для смазки тел и дорожек качения подшипников, так и для отвода тепла (большая часть масла) [1]. Поэтому элементы (например, маслозахват), обеспечивающие подвод
24
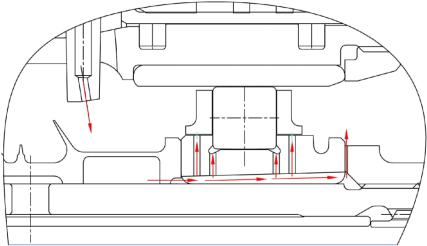
масла к подшипникам, должны обладать высокой эффективностью. В разрабатываемой конструкции элементом, обеспечивающим подвод масла к роликоподшипнику, являетсямаслозахват (рис. 1–3).
В разрабатываемой конструкции турбины высокого давления коэффициент быстроходности роликоподшипника (dm·n = 2,47·106 мм·об/мин)
больше, чем 2,2 106 мм об/мин, поэтому подача масла с помощью
струйных форсунок (жиклеров) не эффективна [2]. В разрабатываемой конструкции сепаратор центрируется по внутреннему кольцу, что мешает прямой подаче масла на роликоподшипник с помощью жиклеров в зазор между внутренним кольцом подшипника и сепаратором [1].
Рис. 1. Схема подачи масла под р/п ТВД с маслозахватом
Цель исследования – обеспечить максимальную эффективность маслозахвата. Эффективность маслозахвата определяется отношением расхода масла, поданного в роликоподшипник, к общему расходу масла. Эффективность зависит как от конструкции маслозахвата, так и от параметров струи масла (скорость, направление). Это было установлено экспериментально. Следует разработать способ определения эффективности маслозахвата на этапе проектирования.
25

Математическое моделирование двухфазной среды (масло и воздух) и ее взаимодействие с твердыми телами в нестационарной постановке является сложной комплексной задачей, поэтому на начальном этапе исследования решено разработать упрощенную методику расчета относительного расхода масла через маслозахват.
Разработанная методика основана на определении траектории движения капли масла, выделенной из общего потока, т.е. движения материальной точки в относительном движении. В методике приняты следующие упрощения: капли масла – абсолютно упругие сферические тела, отсутствует влияние течения воздуха.
Определить положение капли в относительном движении в полярных координатах можно с помощью системы уравнений (1), задаваясь углом, на который повернулся маслозахват, можно следующим образом:
r |
L2 R2 2LR cos , |
(1) |
||
|
V |
|
|
|
|
, |
|
||
arcsin |
sin |
|
||
|
nr |
|
|
|
где L – путь, пройденный маслом в абсолютном движении, м; r – расстояние от капли масла до центра маслозахвата в данный момент времени, м; R – радиус маслозахвата, м; α – угол, под которым масло входит в маслозахват, град; φ – угловое положение капли в относительном движении; γ – угол, на который повернулся маслозахват за время t; V – скорость движения масла в абсолютном движении; n – частота вращения маслозахвата, град/с.
С учетом данных допущений были построены траектории движения масла в маслозахватах для различных перепадов давлений и точек входа масла в маслозахват, пример построенных траекторий представлен на рис. 2 и 3.
Относительный расход масла в данном расчете определялся по формуле
G N 100 %, |
(2) |
отн |
360 |
|
|
|
26 |

где θ – угол между точками входа масла в маслозахват, при которых масло попадает в канавку, подающую масло под внутреннее кольцо подшипника; N – количество захватов.
Рис. 2. Траектории движения масла в маслозахвате № 1 при различных точках входа в маслозахват
Рис. 3. Траектории движения масла в маслозахвате № 2 при различных точках входа в маслозахват
По результатам расчетов и экспериментов для различных перепадов давлений на жиклере были построены графики зависимости относительного расхода масла через маслозахват от перепада давления на жиклере (рис. 4).
27

Рис. 4. Зависимости относительного расхода масла через маслозахват от перепада давления на жиклёре
При увеличении перепада давления на жиклере относительный расход масла через маслозахват увеличивается до определенного оптимального значения, Кроме того, как эксперимент, так и расчет показали, что маслозахват №1 обеспечивает больший относительный расход масла (рис. 4).
Результаты расчетов и эксперимента имеют количественные различия. Для исключенияэтого следует доработатьметодику расчета:
–учесть влияние движения воздуха вокруг маслозахвата;
–ввести достоверную математическую модель столкновения масла с элементами маслозахвата.
Список литературы
1.Иноземцев А.А., Нихамкин М.А., Сандарцкий В.Л. Основы конструирования авиационных двигателей и энергетических установок – М.: Машиностроение, 2008. – Т 1. – 207 с.
2.Новиков Д.К., Фалалеев С.В. Опоры и уплотнения авиационных двигателей и энергетических установок: учеб. пособие. – Самара: Изд-во Самар. гос. аэрокосм. ун-та, 2011. – 124 с.
28
ОСОБЕННОСТИ ТЕПЛОФИЗИЧЕСКИХ ПРОЦЕССОВ ПРИ РЕЗАНИИ ИНСТРУМЕНТОМ С МНОГОСЛОЙНЫМИ ПОКРЫТИЯМИ
Р.И. Ахметшин, М.С. Дементьева, С.М. Каримова
Уфимский государственный авиационный технический университет, Уфа, Россия
e-mail: ahmetshin@bk.ru, masha_dem@mail.ru, ariya.08@mail.ru
Приведены результаты моделирования теплофизических явлений при лезвийной обработке резанием с использованием инструмента с композиционными покрытиями. В зависимости от обрабатываемого и инструментального материалов, режимов и условий резания проявляются различные виды износа. В зависимости от скорости (температуры) резания может измениться вклад каждого вида износа в общую интенсивность изнашивания. Рассмотрено воздействие тепловых факторов на износ инструмента. Установлена зависимость температурных параметров от типа покрытия режущего инструмента.
Ограничивающим фактором производительности операций, связанных с процессом резания, является снижение стойкости режущего инструмента (РИ). Поэтому важно изучить факторы, влияющие на изнашивание РИ, чтобы создать условия, при которых эти факторы наименьшим образом воздействовали бы на изнашивание РИ. Одним из таких факторов является тепловое воздействие [1].
На интенсивность изнашивания оказывает существенное влияние характер распределения температуры резания на контактных поверхностях режущего клина и теплообмен между заготовкой, режущим клином, стружкой и окружающей средой. Если, например, какимлибо образом удалось осуществить целесообразный теплообмен между этими элементами стружкообразования, то это дало бы возможность управлять качеством поверхностного слоя детали или скоростью изнашивания инструмента. Таким образом, возникает проблема управления тепловыми потоками изконтактных зон резания.
29
При компьютерном моделировании процесса резания появляется возможность варьировать теплофизическими и трибологическими характеристиками приконтактной зоны [2], имитируя параметры износостойких покрытий (теплопроводность и коэффициент трения), а также исследовать их влияние натемпературу резания [3,4].
Для моделирования резания использовали программный пакет «DEFORM – 3D». Используя эталонную обработку, задавали основные условия резания: режимы обработки, геометрию инструмента и заготовки, параметры покрытий инструмента. Геометрию заготовки задавали в виде цилиндра с диаметром 120 мм, а геометрия режущей части инструмента соответствовала следующим параметрам: = 10 ; = 0; = 1 = 45 . Режимы резания соответствовали следующим параметрам: V = 450 м/мин, S = 0,11 мм/об, t = 0,5 мм. Материал инструмента – ТТ8К6.
Моделирование процесса резания в среде DEFORM – 3D производили с использованием режущего инструмента:
1)без покрытия;
2)с покрытием TiN толщиной 5 мкм;
3)с двойным покрытием: 1-й слой – TiN (5 мкм), 2-й слой –
Al2O3 (5 мкм);
4)с двойным покрытием: 1-й слой – Al2O3 (5 мкм), 2-й слой –
TiN (5 мкм).
На рис. 1 приведены результаты, полученные в программном
пакете DEFORM – 3D для инструментов без покрытия (рис. 1, а) и с покрытием TiN, толщиной 5 мкм (рис. 1, б).
Установлено, что наибольшая температура резания соответствует обработке инструментом без покрытия. Максимальное снижение интенсивности тепловых потоков в системе «инструмент–заготовка» обеспечивают покрытия, имеющие многослойную архитектуру, причем интенсивность теплового потока заметно зависит от последовательности составляющихслоев многослойного покрытия.
На рис. 2 показаны результаты расчета для инструмента с двухслойной системой покрытия «твердосплавный субстрат – TiN (5мкм) – Al2O3 (5 мкм)» (рис. 2, а) в сравнении с двухслойной системой «твердосплавныйсубстрат– Al2O3 (5 мкм) – TiN (5мкм)» (рис. 2, б).
30