
Оборудование для подготовки материалов
..pdf3.Вентиляционное оборудование для сбора и удаления пыли: вентиляторы 1, циклоны 3, фильтры 2 и бункеры.
4.Оборудование для транспортирования регенерата на склад формовочных материалов: камерный питатель 11, материальный трубопровод 14, разгрузочное устройство 20.
Установка состоит из устройств, связанных между собой средствами непрерывного транспорта, управляемых автоматически.
Другие механические методы регенерации предусматривают применение различных приводных устройств для очистки поверхности зерен песка от пленок и сепарирующих устройств для восстановления зернового состава смеси. К таким устройствам можно отнести:
– виброрегенераторы, в которых используется энергия ко-
лебаний масс отдельных песчинок друг относительно друга,
врезультате чего они истираются и освобождаются от пленок;
–молотковые мельницы с воздушным сепаратором и вибрационным классификатором, приспособленные для дробления сростков, очистки поверхности зерен от пленок и восстановления зернового состава смеси.
1.2.4.4. Установка для сепарации мелкодисперсных материалов
В литейных цехах при подготовке исходных формовочных материалов значительное место занимает процесс сепарации, т. е. разделения мелкодисперсных материалов по фракциям. Например, при помоле глины или песка неотъемлема сепарация продукта помола; при переработке и подготовке отработанных смесей также широко используют сепарацию — удаление мелких фракций песка.
При сепарации отработанных формовочных смесей, в отличие от регенерации, не восстанавливается качество исходного материала (не удаляется инертная пленка с поверхности песчинок), а только обеспечивается их обеспыливание.
91
Наиболее распространены такие способы сепарации отработанных смесей, как пневматический и электрический.
В пневматическом сепараторе (рис. 1.49) мелкодисперсный материал вместе с воздухом по трубопроводу 1 вдувается со скоростью 18–20 м/с в пространство между наружным 2 и внутренним 3 конусом. Вследствие значительного увеличения проходного сечения скорость воздушного потока снижается до 4–6 м/с, и крупные частицы смеси выпадают из него и отводятся через патрубок 6. Мелкие частицы, продолжая движение в воздушном потоке, поступают внутрь конуса 3 и, проходя на своем пути тангенциально установленные лопатки 4, ударяются о них, переходя во вращательное движение. При этом возникают центробежные силы инерции, под действием которых происходит вторичное отделение крупных частиц, выпадающих в патрубок 6.
Тонкие частицы вместе с воздухом через патрубок 5 выходят из сепаратора и направляются либо в фильтр для очистки воздуха, либо во второй сепаратор для отделения второй, более мелкой фракции. Регулировать процесс сепарирования по размеру частиц можно путем изменения положения лопаток 4.
Один из главных недостатков пневматических сепараторов — потребность в фильтрах для очистки воздуха.
Электрический сепаратор обеспечивает более высокую эффективность. Сущность электрического способа сепарации заключается в изменении траектории движения частиц под действием электрического поля (рис. 1.50). Частица М, попадая в электрическое поле напряженностью Е между коронирующим электродом K и осадительным О, заряжается и под действием силы F движется по траектории, отклоненной от вертикали на угол α . Угол α зависит от отношения электрической силы Fe, действующей на частицу, к ее силе тяжести G и обратно пропорционален размеру частицы. Поэтому мелкие частицы отклоняются больше, а крупные — меньше. Если на пути отклоняемых частиц поставить перегородку П, то таким способом можно отделить зону I с мелкими частицами от зоны II с крупными частицами.
92

В целях повышения производительности и качества сепарации сепарационную установку выполняют многосекционной: секции располагаются одна над другой, через них просыпается поток частиц. Габаритные размеры этих секций напряженностью Е постоянного тока (до 50 кВ), подаваемого на электроды, зависят от физических свойств частиц материала (размер, плотность, диэлектрическая постоянная) и технологических требований к процессу сепарации (степень обеспыливания материала или частота заданной фракции по крупности частиц).
Рис. 1.49. Схема пневматического |
Рис. 1.50. Схема устройства и работы |
сепаратора |
электрического сепаратора |
Электронные сепараторы конструктивно просты. Например, коронирующий электрод K представляет собой профильный угольник с заостренными полками (материал — сталь Ст3). Такие угольники закрепляют к вертикальным стойкам из профильной стали на расстоянии 6–10 см друг от друга в количестве от
93
двух до шести. Осадительный электрод О представляет собой стальной лист толщиной 2–5 мм либо наклонно расположенные стальные полосы в виде жалюзи для улавливания крупных частиц. Все эти элементы собирают в секции шириной 0,5–0,7 м такой же длины и высотой 0,4–0,6 м.
1.3.Оборудование для приготовления формовочных
истержневых смесей
Процесс приготовления смесей для разовых форм и стержней из песчано-глинистых материалов заключается в смешивании твердых и жидких составляющих. При перемешивании составляющих на поверхности частиц песка образуются пленки, связывающие между собой смежные зерна. Связывание разрозненных зерен песка в единую систему (смесь) обусловлено возникновением сил сцепления между поверхностью зерен и пленкой связующего, а также наличием сил связи между частицами самого связующего вещества.
Применительно к условиям приготовления формовочных смесей процесс смесеобразования может быть условно разделен на собственно перемешивание и обволакивание, которые в зависимости от режима совершаются последовательно или одновременно. Смесеобразованию обычно сопутствуют весьма важные в технологическом отношении физико-химические явления.
Так, при смешивании песка с водой ее молекулы ориентируются определенным образом по отношению к ионам, расположенным на поверхности зерен кварца, покрывая их слоем «жесткой» воды. При сближении увлажненных зерен песка водные оболочки вступают в электростатическое взаимодействие, связывая между собой эти зерна.
Однако прочность такой смеси незначительна, так как площадь контакта зерен чрезвычайно мала. Повысить прочность смеси можно путем создания вокруг зерен песка деформируемых оболочек из глины или другого вещества. Глинистые частицы, покрываясь слоем воды с несколько иной ориентацией
94
молекул, чем на поверхности зерен кварца, при сближении с этими зернами прочно связывают их. При этом глинистые частицы располагаются как на поверхности зерен, так и частично в порах между песчинками.
Очевидно, что для прочного связывания зерен между собой необходимо распределить глинистые частицы по всей их поверхности, что возможно при сближении зерен и перемещении их в контакте с глинистым веществом. В идеальном случае при смешивании каждое зерно песка должно быть окружено оболочкой связующего вещества. Этого можно достигнуть различными методами, в том числе и перетиранием смеси.
Интенсивность покрытия (обволакивания) определяется фи- зико-химическими свойствами компонентов, конструкцией рабочих органов смесителя и числом уплотнений и разрыхлений каждого элемента смеси в единицу времени.
Основным узлом в каждой смесеприготовительной установке является смеситель.
Существует множество типов литейных смесителей, которые по характеру работы можно разделить на две большие группы: 1) смесители циклического (периодического) действия;
2)смесители непрерывного действия.
Всмесителях циклического действия материал перемеши-
вается отдельными порциями (замесами). Каждая новая порция может быть загружена в смеситель лишь после выгрузки из него предыдущего замеса. Это позволяет регулировать длительность цикла перемешивания в зависимости от состава и назначения приготовляемой смеси.
Всмесителях непрерывного действия загрузка, перемеши-
вание и выгрузка готовой смеси ведутся одновременно и непрерывно. Машины этого типа более экономичны и легче автоматизируются.
Смесители циклического действия, в основу которых положена жесткая программа, определяющая последовательность, характер и продолжительность отдельных операций, требуют применения различного рода дозаторов и других устройств, обеспечиваю-
95
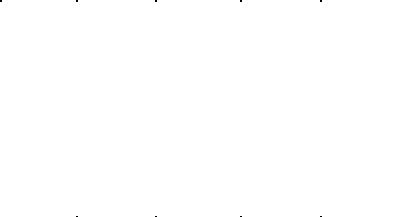
щих получение заданного состава смеси и периодическую выдачу готового замеса. Автоматика таких смесителей включает большое количество исполнительных механизмов, различных приборов, пневмо- и электроаппаратов идругихустройств.
Осуществление принципа непрерывности в смесеприготовительных установках (непрерывность загрузки материалов, их смешивания, получения информации о ходе процесса и качества смешивания, непрерывность регулирования влажности смеси, непрерывность ее выдачи в готовом состоянии) является основным условием, надежной и полной автоматизации процесса приготовления смеси.
Таблица 1 . 2
Литейные смесители
Тип |
Объем замеса, |
Диаметр чаши, |
Максимальная |
Мощность двигате- |
3 |
мм |
производитель- |
ля, кВт |
|
|
м |
ность, м3/ч |
||
|
|
Циклического действия |
|
|
|
смешивающие литейные бегуны |
|
||
1А11 |
0,25 |
1670 |
5,0 |
10 |
1А12М |
0,60 |
2200 |
12,0 |
30 |
114М |
1,0 |
2800 |
25,0 |
40 |
15126 |
3,0 |
2840 |
70,0 |
162 |
|
центробежные смешивающие бегуны |
|
||
115М |
0,4 |
1925 |
25,0 |
89 |
116М2 |
0,63 |
2300 |
50,0 |
114 |
15328 |
1,60 |
2500 |
50,0 |
160 |
|
|
Непрерывного действия |
|
|
|
смешивающие литейные бегуны (сдвоенные) |
|
||
1524 |
1,25 × 2 |
– |
80,0 |
200 |
15207 |
2 × 2 |
– |
100,0 |
160 |
По конструктивным признакам машины для приготовления формовочных и стержневых смесей можно подразделить на смешивающие бегуны одинарные и сдвоенные, центробежные, лопастные и барабанные, а также смесители других типов. Некоторые типы выпускаемых в нашей стране смесителей и их характеристики приведены в табл. 1.2.
96

1.3.1. Смешивающие бегуны
Нормальные смешивающие бегуны системы Симпсона (рис. 1.51) имеют неподвижную чашу и два гладких катка, которые катятся по слою смешиваемого материала, загруженного в чашу, описывая круги вокруг центрального вертикального вала и в то же время вращаясь вокруг собственной оси. При помощи плужков смешиваемый материал направляется под катки.
Рис. 1.52. Кинематическая схема нормальных смешивающих бегунов: 1 — электродвигатель; 2 — редуктор; 3 — конические шестерни; 4 — катки; 5 и 6 — плужки; 7 — кривошип; 8 — кронштейн кривошипа; 9 — регулирующий винт; 10 — разгрузочные дверки днища чаши
97
Катки смешивающих бегунов смонтированы на кривошипах, что дает каткам возможность приподниматься при попадании под них случайных твердых комьев и пропускать их. Кривошипы катков имеют кронштейны с упорными регулирующими винтами, упирающимися в траверсу. Эти винты ограничивают перемещение катков вниз и тем самым устанавливают величину минимального зазора а между катками и дном чаши, что предотвращает дробление зерен песка.
Нормальные смешивающие бегуны являются смесителями периодического действия. В непрерывной смесеприготовительной системе перед ними устанавливают бункеры с дозаторами для загрузки составных частей замеса. После перемешивания замес выдается из бегунов через открываемые для этого в днище чаши разгрузочные отверстия. Загрузку составных частей замеса и выдачу готового замеса производят, не останавливая вращения бегунов.
Продолжительность смешивания одного замеса в нормальных бегунах, включая время загрузки дозаторами и разгрузки замеса, составляет для единой формовочной смеси 3–5 мин, для облицовочной смеси 6–9 мин и для стержневых смесей 6– 12 мин.
Нормальные смешивающие бегуны дают высокое качество перемешивания составных частей формовочных и стержневых смесей. Они равномерно распределяют составные части в массе смеси и обеспечивают хорошее обволакивание песчаных зерен оболочками влажной глины или другого связующего. Смешивающее действие бегунов сводится к давлению катков на смесь, скольжению катков относительно днища чаши и дополнительному перемешиванию смеси плужками.
Наезжая на смесь, находящуюся на дне чаши бегунов, катки своим весом давят на нее — смесь деформируется и частично выжимается из-под катков вперед и в стороны. При этом происходит взаимное перемещение зерен, и распределение составных частей в смеси становится более равномерным.
98

Для увеличения силы воздействия катков на смесь в чаше часто применяют конструкции с дополнительной нагрузкой их с помощью пружины. Сами катки при этом могут быть сделаны более легкими. Известна также конструкция бегунов с автоматически регулируемой силой воздействия на смесь в процессе перемешивания замеса, например с увеличенной силой в начале цикла или же с поддерживанием постоянной силы прижима в течение всего цикла.
Скольжение катков бегунов относительно днища чаши происходит вследствие разности переносной скорости движения
точек на |
поверхности катка ( u = Ω R= |
var) |
и относительной |
скорости |
( w = ω r= const) (рис. 1.52). |
Как |
видно из схем |
рис. 52, а, б и в, для точек, лежащих на образующей катка, соприкасающейся с дном чаши (или слоем материала в чаше), скорости u и w имеют противоположные направления. Поэтому абсолютные скорости указанных точек катка (относительно неподвижной чаши) будут равны геометрическим суммам, или, в
данном случае, арифметическим разностям скоростей u и w:
υ = u+ w= u− w.
Скорость υ представляет собой скорость скольжения катка относительно чаши. Как показано на рисунке, без скольжения по чаше будет катиться только одна какая-то окружность 2 катка. Наибольшее скольжение будет наблюдаться на крайних окружностях катка. Из них окружность 1 будет иметь скольжение, направленное назад (буксование), а окружность 3 — скольжение, направленное вперед.
Скольжение катков бегунов относительно чаши может быть весьма полезным при смешивании формовочных и стержневых смесей, в особенности глинистых. При скольжении каток оказывает растирающее действие на смешиваемый материал, если только он имеет достаточное сцепление с этим материалом.
Высокое качество смешивания возможно только в том случае, если материалы, загруженные в чашу смесителя, неодно-
99
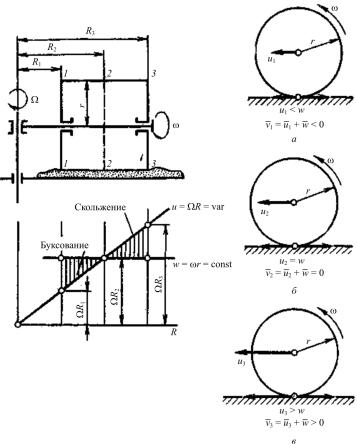
кратно подвергаются действию плужков и катков, распределяющих, уплотняющих и разрыхляющих смесь. Такое действие станет возможным, если под катки будет затягиваться определенный по высоте слой смеси. Чтобы частицы смеси захватывались катками, угол захвата α между касательной Т–Т. (рис. 53) и горизонтальной осью не должен превышать некоторой величины, соответствующей конструктивным параметрам смесителя.
Рис. 1.52. Кинематика катка бегунов: а, б и в — скорости на окружностях 1–1, 2–2 и 3–3 катка
100