
- •В.Б. Кульметьева, С.Е. Порозова
- •Керамические материалы: получение, свойства, применение
- •1. ВВЕДЕНИЕ
- •1.1. История, современное состояние и перспективы развития производства керамических материалов
- •1.3. Классификация керамических материалов
- •Список литературы
- •Список литературы
- •Использованная литература
- •Дополнительная литература
- •3. ИСХОДНЫЕ КОМПОНЕНТЫ
- •3.1. Оксидные системы
- •3.2. Бескислородные тугоплавкие соединения и сиалоны
- •Список литературы
- •Использованная литература
- •Дополнительная литература
- •4.1. Керамика на основе оксида алюминия
- •4.5. Другие виды керамик конструкционного назначения
- •4.6. Перспективы и области применения конструкционной керамики
- •Список литературы
- •Использованная литература
- •Дополнительная литература
- •5. КЕРАМИКА ФУНКЦИОНАЛЬНОГО НАЗНАЧЕНИЯ
- •Дополнительная литература
- •Керамические материалы: получение, свойства, применение
Выход BN по этой реакции составляет 26 %.
Запатентованы также способы получения BN путем обработки водой продуктов реакции азотирования боратов в присутствии до бавок алюминия и кремния. В этом случае силикаты и алюминаты переходят в раствор, a BN - в нерастворимый остаток.
Метод синтеза BN из газовой фазы В(ОСН3)3+ NH3, ВС13пар + + NH3 основан на взаимодействии галоидных и органических со единений бора с аммиаком при высоких температурах. Этим спо собом можно получать как порошки BN, так и покрытия.
Тугоплавкие соединения переходных металлов. Основу наи более жаропрочной керамики для эксплуатации в неокислитель ных агрессивных средах составляют бориды, карбиды и нитриды переходных металлов IV-V периодической системы. Для этих со единений характерны наиболее высокие величины температур плавления и твердости; металлоподобные соединения имеют более или менее широкую область гомогенности, в которой такие свой ства, как температура плавления, твердость и другие, изменяются монотонно, достигая максимума в области состава, отличающегося наибольшей термодинамической стабильностью, например, для TiCx и 7хСхпри х s 1, для NbC* при х - 0,96.. .0,98.
Список литературы
Использованная литература
1. Получение ультрадисперсных порошков методом сжига ния аэровзвесей частиц металлов / В.Н. Анциферов [и др.] // Кос мический вызов XXI века. Т. 2. Перспективные материалы и тех нологии: Нанокомпозиты / под ред. А.А. Берлина и И.Г. Оссовского. - М : ТОРУС ПРЕСС, 2005. - С. 47-58.
2. Получение субмикронных керамических порошков газо динамическими методами / В.Н. Анциферов и др. // Системные проблемы надежности, качества, информационных и электрон ных технологий (Инноватика-2004): междунар. науч.-техн. конф. и российская научная школа молодых ученых и специали стов, 2-13 октября 2004 г., г. Сочи, Россия.
3.Краснокутский Ю.И. Получение тугоплавких соедине ний в плазме / Ю.И. Краснокутский, В.Г. Верещак. - Киев: Вища школа, 1987. - 200 с.
4.Вассерман И.М. Химическое осаждение из растворов / И.М. Вассерман. - Л.: Химия, 1980. - 280 с.
5.Сравнительная оценка методов получения частично ста билизированного диоксида циркония / Т.И. Панова [и др.] // Журн. прикп. химии. - 1990. - Т . 63. - № 1. - С. 100-105.
Дополнительная литература
1.Шевченко В.Я. Техническая керамика / В.Я. Шевченко, С.М. Баринов. - М.: Наука, 1993. - 187 с.
2.Керамика для машиностроения / А.П. Гаршин [и др.]. - М.: ООО Издательство «Научтехлитиздат», 2003. - 384 с.
3.Химическая технология керамики: учеб, пособие для ву зов / под ред. проф. И.Я. Гузмана. - М.: ООО РИФ «Строймате риалы», 2003. - 496 с.
4.Гнесин Г.Г Бескислородные керамические материалы /
Г.Г.Гнесин. - Киев: Технжа, 1987. - 152 с.
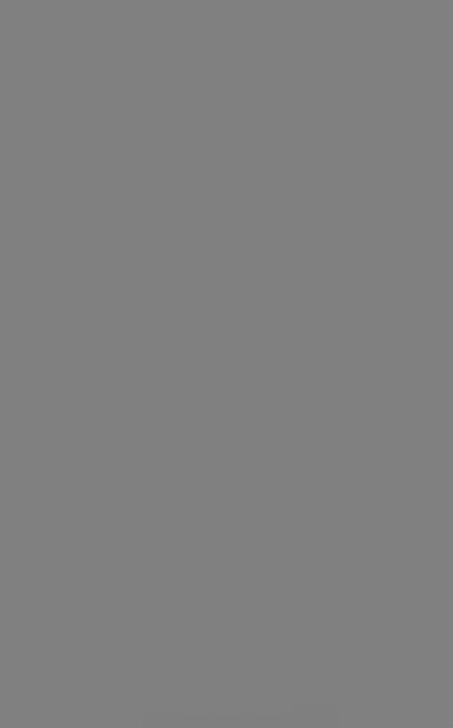
Кдругим преимуществам керамических материалов по сравнению с металлическими относятся: высокая твердость, из носостойкость, химическая инертность, меньший в 2-3 раза удельный вес, широкий диапазон электрических, теплофизиче ских и ядерных свойств, радио- и светопрозрачность.
Косновным керамическим материалам конструкционного
назначения относятся оксиды алюминия и циркония, карбид и нитрид кремния. Большое внимание ученых привлекают мате риалы в системах типа карбидов и боридов циркония, гафния, тантала, перспективные для создания тугоплавких материалов с рабочими температурами выше 1800 °С.
4.1. Керамика на основе оксида алюминия
Керамика на основе оксида алюминия остается наиболее широко применяемым керамическим материалом в самых раз нообразных областях техники, так как она имеет такое благо приятное сочетание свойств, какое не имеется ни у одного огне упорного оксида.
На основе корунда создано большое количество высококаче ственных материалов, из них наиболее известные и применяемые в промышленности: ВК-94-1, ВК-100-1, ЦМ-332 (микролит), картинит, сикор, корал-2 и ряд других. Свойства корундовой керамики зависят от содержания глинозема, состава зернограничных фаз, размера зерна, других характеристик микроструктуры.
Большинство изделий корундовой керамики изготавливают из технического глинозема, который подвергают предварительному обжигу при температуре 1300... 1400 °С для его перевода из у-А120 3 в a-форму. Длительность обжига в туннельных печах составляет обычно 15...30 ч, причем выдержка при максимальной температуре составляет 3.. .4 ч. После обжига глинозем измельчают.
В зависимости от конфигурации и размеров изделий для формования заготовок используют различные методы - прессо вание, в том числе изостатическое, шликерное литье в гипсовые формы, горячее литье под давлением в металлические формы, пленочное литье.
Прессование |
корундовых изделий большой сложности |
не представляет. |
Так как порошок А120 3 непластичен, в него |
вводят временную технологическую связку.
При литье под давлением горячих шликеров для придания им литейной способности вводят 15... 18 % технологической связки, содержащей парафин, олеиновую кислоту и воск. Коли чество связки зависит от степени обжига глинозема, его дис персности. Температура выжигания связки 1100... 1200 °С. В некоторых случаях практикуют частичное удаление парафина нагреванием до 240...260 °С. Остающиеся при этой температуре тяжелые фракции парафина придают изделию прочность, доста точную для дальнейших операций.
Обжиг корундовых изделий осуществляют в высокотемпе ратурных печах как в окислительной, так и в инертной среде.
Температура обжига изделий из корунда технической чистоты (А120 3- 99...99,5 %) и дисперсностью 1...2 мкм без введения до бавок находится в пределах 1710... 1750 °С. При этой температуре достигается относительная плотность 0,94...0,96. Дальнейшее уве личение температуры до 1800... 1850 °С в воздушной среде и дли тельная выдержка практически не приводят к дополнительному уплотнению. Этому препятствуют закрытые внутрикристаллические поры и процессы рекристаллизации, в результате чего растет зерно, и прочность корундовой керамики снижается. Пористость такого спеченного корунда в основном закрытая, внутрикристаплическая, форма пор округлая. Сравнительно низкая плотность изделий из чистого глинозема вынуждает применять добавки в ви де индивидуальных чистых оксидов или комбинированного соста ва, в том числе и стекловидных.
К первому виду относятся широко используемые в про мышленных массах оксиды - ТЮ2, MgO, Z r02, М п02 и др. Наи более эффективно температуру спекания снижает добавка ТЮ2. Введение 1 % ТЮ2 в глинозем позволяет снизить температуру обжига до 1550 °С благодаря образованию твердого раствора титана в А120 3. Добавка ТЮ2одновременно способствует интен сивному росту кристаллов а-А120 3, достигающих размера
200.. .350 мкм, благодаря чему такая керамика обладает более высокой термостойкостью, чем керамика без добавок, у которой размер зерен составляет 20...50 мкм. Однако прочность корунда с добавкой ТЮ2резко снижается.
Ряд добавок задерживает рост кристаллов корунда. Наибо лее сильно этот эффект проявляется при введении MgO и MgF2. Кроме этих добавок, к числу задерживающих кристаллизацию, но в меньшей степени, принадлежат Z r02, Si02, CaF2и ряд дру гих. При введении в массу 0,5—1 % MgO размер кристаллов
не превышает 2... 10 мкм при исходном |
размере зерен А120 3 |
|
1.. |
.2 мкм. Такое тормозящее рост кристаллов корунда действие |
|
объясняется образованием на поверхности корунда микронных |
||
прослоек магнезиальной шпинели MgO |
А120 3. При этом кри |
сталлы корунда приобретают более изометрическую форму. Снижения температуры спекания при введении MgO не наблю дается. Добавку MgO вводят в виде тонкодисперсного порошка оксида или в виде раствора солей магния.
Добавка Zr02в последнее время получает все большее приме нение благодаря новейшим достижениям в технологии оксидной
керамики Применение мелких неагрегированных монофракционных порошков а-А120 3 с размером частиц 0,5 мкм, полученных химическими методами осаждения при одновременном введении ZrOj, позволило получить керамику с очень мелкими кристаллами и очень высокими механическими свойствами.
Существенное снижение температуры спекания может быть достигнуто добавками, которые образуют жидкую фазу. Присутст вие жидкой фазы с высоким поверхностным натяжением и хоро шим смачиванием кристаллов корунда позволяет снизить темпера туру спекания на 300.. .400 °С при весьма небольшом содержании добавок (массовая доля 0,5...5,0 %). Подбирая добавки с целью образования в процессе обжига эвтектического расплава, можно достичь высокой степени уплотнения при температурах 1300.. .1500 °С при сохранении мелкокристаллической структуры с последующей кристаллизацией расплава, что обеспечивает полу чение керамики, практически не содержащей стеклофазу. Добав
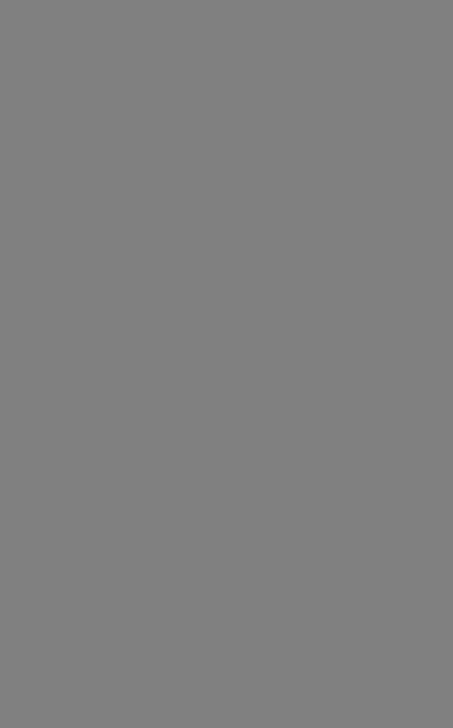
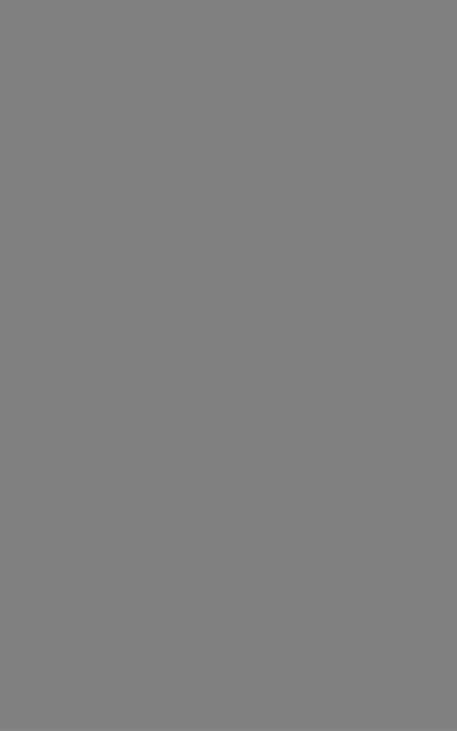
До недавнего времени в керамических материалах не исполь зовали чистый оксид циркония, потому что он обладает низкими техническими свойствами и плохой стойкостью к тепловому уда ру. Тем не менее еще в 1975 г. были созданы новые керамические материалы с диоксидом циркония с исключительной прочностью и вязкостью, повышенной твердостью, ударной вязкостью, низ кой теплопроводностью, малой теплоемкостью. Диоксид цирко ния характеризуется химической инертностью и сохраняет со противление эрозии и коррозии даже при повышенных темпера турах, а также имеет низкий коэффициент трения (0,17.. .0,2) при эксплуатации в паре с большинством металлов.
Высокая прочность и трещиностойкость такой керамики обусловлена полиморфным превращением диоксида циркония из метастабильной тетрагональной модификации в стабильную моноклинную. Такое превращение инициируется внешними ме ханическими нагрузками и приводит к необратимым затратам работы при деформировании и разрушении материала. В систе мах с дисперсными частицами диоксида циркония получены уникальные материалы, имеющие прочность при изгибе выше 1500 МПа и трещиностойкость более 30 М П ам 1/2
По микроструктурному признаку различают три типа кера мических материалов, трансформационно-упрочненных диокси дом циркония (рис. 4.2):
1) частично стабилизированный диоксид циркония (PSZ), микроструктура которого состоит из двух фаз: матрицы из ку бической фазы (с повышенным содержанием легирующих доба вок), в которой находятся дисперсные выделения тетрагональ ной фазы (с меньшим содержанием добавок). Характер структу ры можно регулировать, изменяя температуру спекания и режим охлаждения;
2) поликристаллический тетрагональный диоксид цирко ния (TZP), микроструктура которого представляет собой мелко зернистые кристаллы из одной тетрагональной фазы диоксида циркония;
3) композиционные материалы, содержащие диоксид цир кония в отличающейся по составу керамической матрице.
Рис. 4.2. Микроструктура транформационно-упрочненной керамики на основе Zr02
Материалы первого и второго типов отличаются, помимо структуры, содержанием стабилизирующих добавок (табл. 4.2).
|
|
Т а б л и ц а 4 . 2 |
||
|
Содержание стабилизирующих добавок |
|
||
|
в Zr02-KepaMHKe различного вида |
|
||
Материал |
|
Содержание добавки, мол. % |
Y,0, |
|
СаО |
MgO |
|||
|
||||
PSZ |
5...9 |
7...10 |
3...4 |
|
TZP |
До 2 |
До 2 |
До 3,5 |
Материалы на основе диоксида циркония, содержащие эти добавки, могут в зависимости от ее количества, условий изго товления и последующей термообработки иметь микрострукту ру, содержащую несколько различных кристаллических струк тур диоксида циркония.
4.2.1. Частично стабилизированный диоксид циркония
Эффект трансформационного упрочнения был открыт на 2г0 2-материалах, частично стабилизированных оксидом каль ция. Однако наибольшее значение для практического использо вания имеютPSZ-материалы, содержащие 8...9 мол. % MgO.
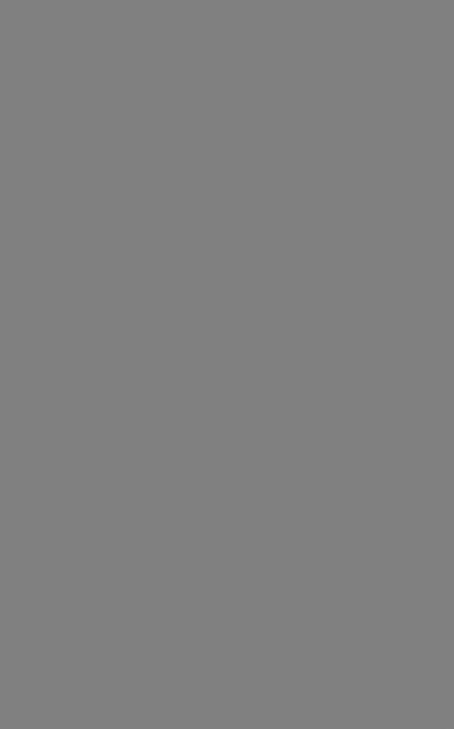
оси 30...60 нм. Значение температуры мартенситного превра щения для таких выделений всегда ниже комнатной температу ры, так что для достижения эффекта упрочнения необходима дополнительная термообработка, приводящая к укрупнению выделений T-Zr02до размера ~ 180 нм.
Термообработкой на старение PSZ в системе ZrO2-M g0 по лучают материалы, имеющие прочность 500...800 МПа и трехциностойкость 12... 15 МПа-м1/2. Такую термообработку прово дят при температуре около 1100 °С.
Другой, наиболее подробно изученной системой для получе ния высокопрочной PSZ-керамики является система Z rO r-Y ^ . Содержание стабилизирующей добавки составляет 3...6 мол. %. Термообработка для гомогенизации и обжиг обычно проводятся при температурах 1700 °С и выше. В результате спеченный Y-PSZ имеет структуру с размером зерна 50...70 мкм, в которой'присут ствуют выделения двух тетрагональных фаз: T-Zr02и T'-Zr02. Т - фаза отличается от метастабильной тетрагональной фазы (Т) высо ким содержанием иттрия и стойкостью к преобразованию в моно клинную фазу, также в литературе ее называют непревращаемой. Т'-фаза формируется в результате бездиффузионного превращения из кубической фазы при быстром охлаждении (1600 °С/ч) из облас ти стабильности высокотемпературных фаз. В случае медленного охлаждения (300 °С/ч) образуется Т-фаза.
Используя для частичной стабилизации диоксида циркония набор добавок разной концентрации, видоизменяя структуру материала в результате варьирования режимов термической об работки, можно получить большое разнообразие его свойств (табл. 4.3).
При испытаниях PSZ-керамики, изготовленной методом го рячего прессования, получены значения прочности при изгибе 2400 МПа и трещиностойкости 10...15 МПа м1/2 Прогнозирует ся возможность достижения в будущем значений, равных соот ветственно 8000 МПа и 20 МПа-м1/2.
|
|
Т а б л и ц а |
4.3 |
Прочностные характеристики PSZ-керамики, |
|
||
|
выпускаемой в некоторых странах |
|
|
Страна |
Прочность при изгибе, |
Трещиностойкость, МПа м1/2 |
|
|
МПа |
2,3...6 |
|
США |
200...575 |
|
|
Япония |
900...980 |
4...9 |
|
Австралия |
700 |
8...15 |
|
ФРГ |
650 |
7...15 |
^ |
4.2.2. Поликристаллический диоксид циркония тетрагональной модификации
Температура мартенситного (Т -» М)-превращения в Zr02
может быть понижена до уровня комнатной температуры за счет формирования ультрадисперсной структуры. Такие материалы, практически полностью состоящие из T-ZrC>2 (TZP), обладают уникально высокими прочностными характеристиками. В каче стве стабилизаторов в этих материалах используют добавки Y20 3(Y-TZP) или C e02(Ce-TZP).
Одной из основных проблем при их изготовлении является ингибирование роста зерна при спекании или горячем прессова нии, чтобы предотвратить (Т -» М)-превращение при охлажде нии. Критический размер частиц, при котором метастабильный T-Zr02 спонтанно превращается в M -Zr02, зависит от содержа ния легирующих оксидов, их распределения, наличия стеклофазы и ее локализации. Керамику спекают при 1350... 1450 °С в области существования T-Zr02.
Значительное улучшение механических свойств этих мате риалов обусловлено мартенситным превращением зерен метастабильного T-Zr02 в M -Zr02 на вершине распространяющейся трещины с увеличением объема приблизительно на 5,3 % и раз витием сдвиговых деформаций, увеличивающих в свою очередь объем зоны, в которой происходит фазовый переход. Поэтому способность к превращению метастабильных зерен T-Zr02 в зо не распространяющейся трещины играет доминирующую роль
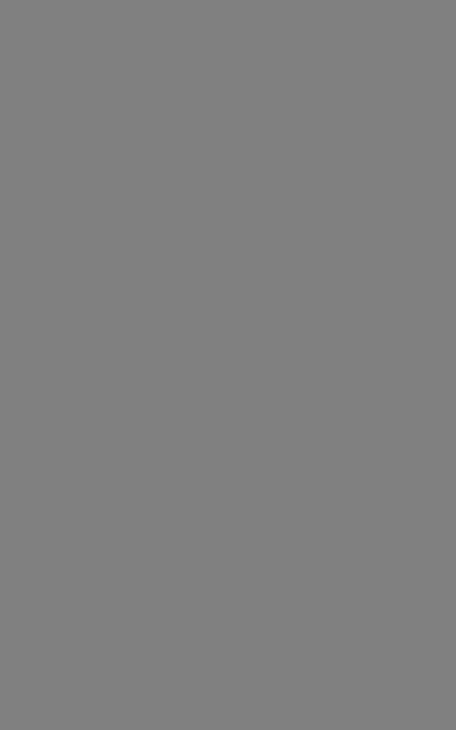


Введение частиц Zr02в А120 3-матрицу положительно влия ет и на другие свойства, снижая, например, скорость субкрити ческого распространения трещины. Однако износостойкость может быть пониженной вследствие образования микротрещин в зоне контактного воздействия.
Дисперсные частицы частично стабилизированного Zr02 были успешно использованы и для повышения механических свойств других оксидных матриц, таких как муллит или шпи нель (MgAl20 4).
Керамические материалы на основе оксида циркония при меняют для изготовления насадок для непрерывной разливки стали, тиглей для плавки металлов, вставок для экструдирования труб из хромоникелевых сталей и калибрования прецизион ных деталей, матриц для волочения, металлорежущих инстру ментов, вкладышей пресс-форм. Благодаря низкой теплопро водности оксид циркония используют для изготовления деталей дизельных адиабатических двигателей (гильзы цилиндров, го ловки поршней, клапаны и др.).
4.3. Карбид кремния
Карбид кремния нашел широкое применение в технике благо даря уникальному сочетанию физических свойств регулируемой электропроводности, высокой твердости и теплопроводности, ма лому температурному коэффициенту линейного расширения (ТКЛР), высокому сопротивлению окислению при температурах < 1500 °С. Эти свойства стимулируют разработку широкого класса материалов на основе SiC, включая материалы конструкционного назначения.
Преимущественно ковалентный тип химической связи в SiC не позволяет получать из него обычным спеканием изделия вы сокой плотности без введения добавок, активирующих процесс спекания.
В отсутствие активирующих добавок спекание порошков карбида кремния можно реализовать при температуре выше 2100 °С. При этом образуется поликристаллический материал
с высокой пористостью (22...40 %), так называемыйрекристаплизованный карбид кремния.
Достижение более высокой плотности рекристаллизованных материалов возможно путем введения активирующих доба вок. Параметры получения и реализуемые свойства спеченного SiC (рис. 4.5) в значительной степени зависят от вида и количе ства активирующих добавок, которые можно разделить на ки слородсодержащие и бескислородные. К первой группе отно сятся AI2O3, Y20 3, Се02, ВеО, их комбинации A120 3-Y 20 3, Al20 3-M g0. Ко второй группе относятся В, С, В4С, BN, BP, A1N и такие их комбинации, как В-С, Al-C, В-А1-С и др.
Плотная керамика на основе SiC имеет модуль упругости 380...480 ГПа; прочность при изгибе 700... 1000 МПа; KiC = 3...
4 М Пам|/2; коэффициент теплопроводности 65...320 Вт/(мК); ТКЛР = (3,5...4) • 10"6К-1 в интервале 20. ..1000 °С. Значение К1С можно повысить до 7...8 МПа-м1/2 введением дисперсной фазы TiB2. При высоких температурах керамика сохраняет высокие прочностные свойства: при 1500 °С прочность при изгибе дости гает 500 МПа.
Добавка оксида алюминия, как правило, позволяет умень шить размер кристаллов до 1...2 мкм, что позволяет достичь прочности 750 МПа. В то же время образование алюмосиликатов по границам кристаллов SiC при нагревании приводит к тому, что горячая прочность при температурах выше 1000 °С у керамики
сдобавкой А120 3ниже, чем с добавкой бора и углерода.
Вкачестве исходного вещества для использования в техно логии спеченного карбида кремния применяются микропорошки SiC с размером частиц 0,6... 1,5 мкм и высокой степени чистоты, примеси металлов не должны превышать 0,1 %, содержание ки слорода должно быть менее 1%.
Вводимые добавки при спекании инициируют фазовый пе
реход P-SiC -> а -SiC, что способствует процессу спекания кар бида кремния. Например, добавка бора при температуре выше 2000 °С приводит практически к полному переходу P-SiC —> a-SiC с образованием крупных неизометричных пластинчатых
кристаллов SiC политипа 6Н. При введении добавки алюминия и оксида бериллия происходит частичный переход p-SiC -» ос-SiC с преимущественным образованием политипа 4Н и фор мированием структуры из изометричной формы кристаллов.
Рис. 4.5. Принципиальная схема получения спеченного карбида кремния
Использование оксидных активаторов позволяет получать плотные материалы из SiC при температурах до 2000 °С, боруглеродных - до 2200 “С. Наиболее предпочтительной для спе кания является среда аргона.
Остаточная пористость материала влияет на основные фи зико-механические характеристики. Так, твердость спеченного карбида кремния 26...28 ГПа при нулевой пористости падает до 20 ГПа при пористости 5.. .6 %.
При горячем прессовании (ГП) порошков карбида кремния без добавок также получаются изделия с высокой пористостью. Так, при давлении 58,84 МПа и температуре 2350 °С максималь ная относительная плотность горячепрессованного SiC-мате- риала не превышает 84 %.
При введении в прессуемые порошки карбида кремния до бавки аморфного бора были получены изделия с пористостью до 4 % при удельном давлении прессования порядка 9,8 МПа. ГП получило широкое развитие при изготовлении мелкосерийных ответственных деталей простой формы, не требующих механи ческой обработки. Технология ГП карбида кремния по сравне нию с обычным спеканием позволяет снизить количество доба вок, сохранить исходную мелкодисперсную структуру, исполь зовать более грубодисперсные порошки, достичь практически беспористого состояния.
При использовании порошка a-SiC (средний размер частиц 0,26 мкм) с добавками 6 % Al, 1 % В и 1 % С увеличение удель ного давления прессования от 20 до 60 МПа при температуре 1650 °С приводит к увеличению плотности горячепрессованных образцов от 2,6 до 3,1 г/см3, а прочность при изгибе возрастает при этом от 340 до 550 МПа. Анализ микроструктуры горячепрессованного SiC-материала показал наличие областей, вытя нутых перпендикулярно направлению прессования, что свиде тельствует о жидкофазном механизме спекания в условиях го рячего прессования SiC.
Для получения изделий сложной формы применяют метод изостатического горячего прессования (ГИП). При этом могут осуществляться два варианта применения технологии ГИП: 1) доуплотнение без капсулирования предварительно спеченно го полуфабриката до относительной плотности 93...95 % 2) обработка порошкообразных полуфабрикатов, капсулирован ных в газонепроницаемую оболочку из молибдена, вольфрама или тантала. Температура процесса составляет 1950 °С при дав лении 200 МПа, а выдержка 2...3 ч. Наибольшее уплотнение при горячем прессовании (2000 °С) порошков SiC достигается с использованием добавок бора и углерода.
Горячепрессованные SiC-материалы имеют более высокий уровень механических свойств по сравнению с рекристаллизованным карбидом кремния. Однако реализация метода горячего прес сования в промышленных масштабах связана с чрезвычайно боль шими трудностями по причине низкой стойкости графита, исполь зуемого для пресс-форм и способного работать при температурах выше 2000 °С, а применение метода горячего изоетатического прессования связано со значительными усложнениями технологии.
Приведенных выше недостатков, отмеченных для получения SiC-материалов методами рекристаллизационного спекания и го рячего прессования, лишена технология получения поликристаллического SiC-материала методом реакционного спекания, при ко тором заготовка, прессованная из смеси порошков первичного кар бида кремния и углеродистого материала, пропитывается распла вом или парами кремния. При использовании этого метода имеется широкий выбор способов формования заготовок изделий (полусу хое, гидростатическое прессование, шликерное литье, экструзия, инжекция), а получаемые при этом после реакционного спекания материалы обладают свойствами, близкими к свойствам материа лов, получаемых горячим прессованием.
Впервые SiC-изделия методом реакционного спекания были получены в 1950-х гг. При этом в качестве углеродистой добав ки использовались графит, смесь древесного угля и пекового кокса, нефтяной кокс, сажа. Временной связкой в таких издели ях служили резольно-формальдегидная смола, параформальде гид, декстрин, пульвербакелит и жидкий бакелит. Пропитка за готовок кремнием проводилась в среде его расплава и паров при температуре 2050 °С и атмосферном давлении, либо при 1500... 1600 °С в вакууме.
В композиционной системе SiC-Si и в системе SiC-Si-C при наличии углерода и избытка несвязанного кремния в про цессе пропитки прессованной заготовки жидким кремнием на блюдается процесс перекристаллизации исходного карбида кремния (SiC„) через жидкий кремний (путем растворения наи более мелких зерен SiC в кремнии и осаждения их на более крупных) и формирование кристаллов SiC правильной огранки или близкой к ней (рис. 4.6).

Структуру реакционноспеченного SiC-материала, получае мого при одном и том же режиме силицирования, можно регу лировать изменением содержания углерода в шихте, плотности прессованных заготовок, а также крупностью частиц состав ляющих шихту компонентов. На рис. 4.7 представлена техноло гическая схема получения изделий из реакционноспеченного карбида кремния.
Рис. 4.7. Технологическая схема производства изделий из реакционного карбида кремния
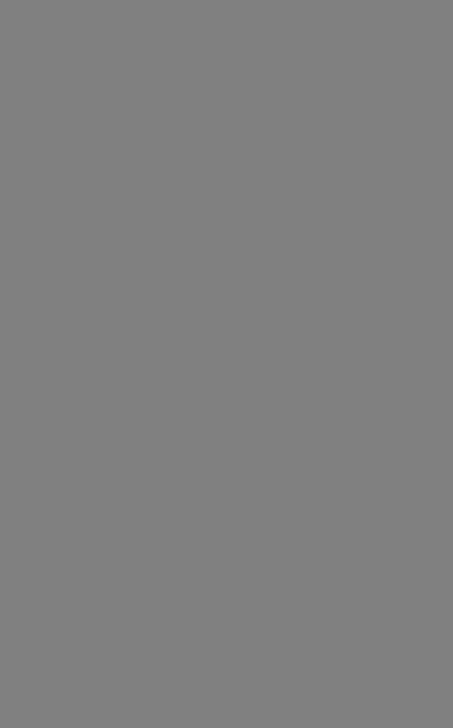
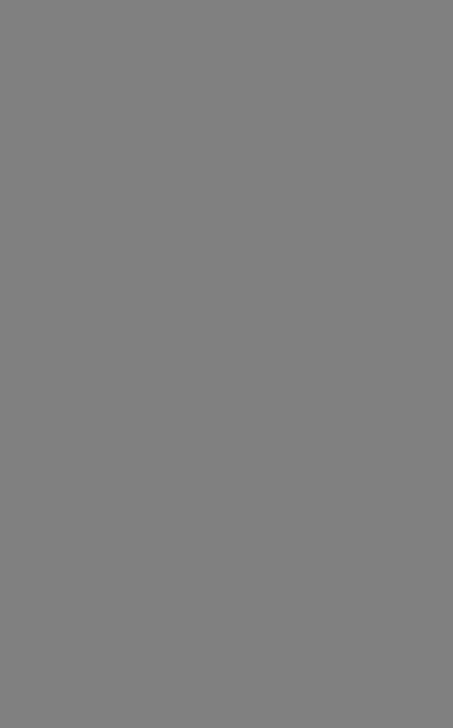
4. Нитрид кремния, который образуется в условиях горячего изостатического прессования (ГИПНК) из порошков Si3N4с ак тивирующими добавками.
Основные проблемы получения плотного нитрида кремния возникают при осуществлении процесса спекания, которое за труднено из-за сильных ковалентных связей в кристаллической решетке и осложняется диссоциацией соединения при нагрева нии до высоких температур. Уплотнение нитрида кремния мо жет быть эффективным только при жидкофазном механизме спекания.
Регулирование количества жидкой фазы и температуры ее образования при спекании нитрида кремния достигается введе нием специальных добавок, как правило оксидных. Эти активи зирующие спекание добавки участвуют в фазообразовании
иформировании микроструктуры нитридкремниевой керамики, оказывая таким образом существенное влияние на эксплуатаци онные свойства спеченного материала. Можно выделить не сколько основных видов добавок:
1.Введение MgO в качестве добавки. Жидкая фаза форми руется благодаря взаимодействию оксида магния с Si02, кото рый всегда присутствует в виде поверхностной пленки на час тицах Si3N4. При охлаждении эта жидкая фаза состава Mg-Si- O-N формирует на границах зерен Si3N4 стеклофазу, отличаю щуюся низкой температурой размягчения (~ 1000 °С) и опреде ляющую невысокие значения высокотемпературной прочности
исопротивление ползучести данного материала.
2.При добавлении к нитриду кремния У20 3в процессе спе кания или горячего прессования при относительно низких тем пературах образуется жидкая фаза, способствующая спеканию. При более высокой температуре, когда происходит окончатель ное уплотнение, эта фаза реагирует с нитридом кремния, обра зуя более жаропрочную связующую фазу. В зависимости от ко личества Y20 3 и присутствующего в порошке нитрида кремния поверхностного Si02 в данной системе возможно образование четырех различных кристаллических оксинитридных фаз, кото
рые располагаются по границам зерен Si3N4 и, с одной стороны, обеспечивают повышенную жаропрочность материала, а с дру гой - снижают его устойчивость к окислению.
3. Наилучшие результаты по спеканию нитрида кремния получены с использованием комплексной добавки Y2O3-AI2O3, обеспечивающей образование жидкой фазы Y -Si-A l-0-N , в присутствии которой уплотнение нитрида кремния происхо дит наиболее эффективно. При термообработке образующаяся на границе зерен фаза полностью кристаллизуется, и таким об разом получают спеченные изделия с величиной предела проч ности при изгибе > 1000 МПа при 1200 °С.
4.Введение оксидов редкоземельных элементов - Ьа20 3, Sm203, Се02 и других - приводит к получению жаропрочной межзеренной фазы в структуре керамики благодаря образова нию сложных оксинитридов.
5.Благодаря наличию на частицах Si3N4 поверхностной пленки Si02 жидкофазное спекание нитридкремниевой керами ки можно осуществлять, применяя нитридные добавки (A1N, BeSiN4, YN и др.). Неоксидные добавки используют также при горячем прессовании. В частности, для улучшения эксплуатаци онных свойств инструментальной керамики на основе Si3N4
вводят добавки карбидов (TiC, WC), нитридов (TiN, BN), сили цидов (WSi2). Чаще всего для этих целей применяют карбид ти тана, существенно повышающий стойкость резцов, а также нит рид и карбонитрид титана.
При спекании Si3N4, в связи с тем что температура обжига близка к температуре разложения Si3N4, легко выделяется крем ний, поэтому необходимо точное управление температурой спе кания и средой. Способом горячего прессования можно полу чить плотное спеченное изделие, несмотря на небольшую вели чину вводимых добавок. Поэтому количество образующейся при спекании жидкой фазы небольшое, и невелико снижение прочности при высокой температуре по сравнению с изделиями, спеченными при обычном спекании.
Возможность получения высокоплотных нитридкремниевых материалов и параметры технологических процессов определяются не только выбором композиции, но и в значительной степени ха рактеристиками исходных порошков. Общими требованиями, предъявляемыми к порошкам Si3N4, являются следующие:
■высокая дисперсность и однородность частиц. Для боль шинства технологий требуются порошки субмикронных размеров
судельной поверхностью 10...25 м2/г, позволяющие получать высокоплотные материалы с мелкозернистой структурой;
■высокое содержание a -фазы, так как процессы уплотне ния и структурообразования нитридкремниевой керамики свя заны с сопутствующим фазовым превращением a-Si3N4 -> P-Si3N4, которое происходит по механизму перекристаллизации через жидкую фазу;
■контролируемое содержание кислорода. Кислород как
основная примесь присутствует в порошке нитрида кремния
в адсорбированном виде, а также в виде Si02. Содержание ки слорода определяет количество жидкой фазы при спекании, влияет на фазовый состав, структуру и свойства материала;
■ минимальное содержание металлических примесей и уг лерода. Наличие в порошке нитрида кремния железа, кальция и магния приводит к снижению вязкости жидкой фазы при спе кании, повышает конечную плотность на 1...5 %, но способст вует росту зерен Si3N4 и образованию более грубой зернистой структуры керамики, определяет уменьшение высокотемпера турной прочности и увеличение скорости деформации при воз действии механических напряжений. Присутствие углерода уменьшает количество жидкой фазы и изменяет ее состав, по давляет уплотнение и способствует укрупнению структуры.
Характеристики порошка нитрида кремния определяются методом его синтеза и качеством исходных реагентов.
Формование порошков нитридкремниевых композиций производят различными методами, используемыми в керамиче ской технологии. Выбор метода формования и соответствующая подготовка порошков зависят от формы и размеров изделия и предъявляемых к нему требований.
Керамику на основе S13N4 спекают различными методами: обычным спеканием, реакционным спеканием, горячим прессо ванием, их комбинацией.
В среде азота без избыточного давления спекают материалы на основе нитрида кремния с использованием различных спе кающих добавок. Необходимым требованием при этом является применение активных высокочистых исходных порошков SijN4
субмикронных |
размеров. |
Наилучшие результаты получены |
с использованием комплексной добавки Y2O3-AI2O3. Такой ма |
||
териал имеет |
следующие |
свойства: фазовый состав (3-Si3N4 |
и стеклофаза; предел прочности при изгибе 800... 1000 МПа при 20 °С, 400...550 МПа при 1200 °С; температура падения прочно сти 1000 °С; вязкость разрушения 7,0 МПа м1/2; твердость HV 16... 18 ГПа.
При реакционном спекании Si3N4после формования порош ка Si его азотируют в среде NH3или N2- При этом под влиянием реакции 3Si + 2N2-> Si3N4 происходит упрочнение формуемого изделия. В результате реакционного спекания Si3N4 образуется с закрытием пустот, остающихся от частиц Si, поэтому измене ния размеров до и после реакции крайне незначительны. Порис тость спеченных изделий получается не ниже 20 %. Этим обу словлена их низкая прочность, составляющая ~ 250 МПа, но она остается такой же и при температуре ~ 1400 °С; вязкость разру шения 1,8... 2,0 МПа-мш; твердость HV 9... 10 ГПа.
Спеканием можно получить плотный нитрид кремния, ис пользуя в качестве исходного материала реакционносвязанный Si3N4. РСНК дополнительно спекают при 1800...2000 °С в среде азота при нормальном или повышенном давлении (0,1...
10 МПа). Плотность материала достигает более 98 % от теоре тической, но усадка составляет всего 5...7 %, что позволяет по лучать изделия достаточно точных размеров. Нитрид кремния марки ОТМ-907 (ОНПП «Технология») имеет следующие свой ства: фазовый состав p-SisN4 и стеклофаза; предел прочности
при изгибе 500 МПа при 20 °С, 400...550 МПа при 1000 °С; вяз-
I/O
кость разрушения 5,5 МПа-м
Для уплотнения нитрида кремния широко используются мето ды с применением давления: горячее прессование, горячее изостатическое прессование и спекание при повышенном давлении азота.
Использование повышенного давления азота позволяет про водить спекание нитрида кремния при более высоких темпера турах без разложения материала и, следовательно, активизиро вать уплотнение. При этом имеются широкие возможности воз действовать на свойства материала, изменяя параметры процес са. Горячим прессованием были получены первые материалы с высокой прочностью на основе нитрида кремния. Нитрид кремния марки ОТМ-914 (ОНПП «Технология») имеет следую щие свойства: фазовый состав P-Si3N4 и стеклофаза; предел прочности при изгибе 830 МПа при 20 °С, 700 МПа при 1400 °С; вязкость разрушения 7,9 МПа-мш; рабочая температура 1300 °С.
Особенности реализуемой в нитридкремниевой керамике микроструктуры (рис. 4.9) оказывают сильное влияние на ее способность сопротивляться распространению трещин. При го рячем прессовании керамики на основе a-Si3N4 в результате фа зового перехода a —* р реализуется эффект самоармирования благодаря образованию зерен P-Si3N4 удлиненной формы в мат рице из равноосных зерен a-Si3N4, что приводит к значительно му росту критического коэффициента интенсивности разруше ния керамики. Чем больше содержание a -фазы в исходном по рошке, тем выше прочность горячепрессованного материала. Наиболее эффективны для повышения трещиностойкости спе ченной керамики из P-Si3N4 зерна размером более 1 мкм. При определенной популяции таких зерен в матрице с ультрадисперсной структурой удается достичь уровня трещиностойкости 9,7 МПа-м1/2 (при прочности 900 МПа).
Однако применение горячего прессования ограничивается серьезными недостатками, наиболее существенными из которых являются возможность получения только простых форм, необ ходимость дорогостоящей конечной обработки, низкая произво дительность.
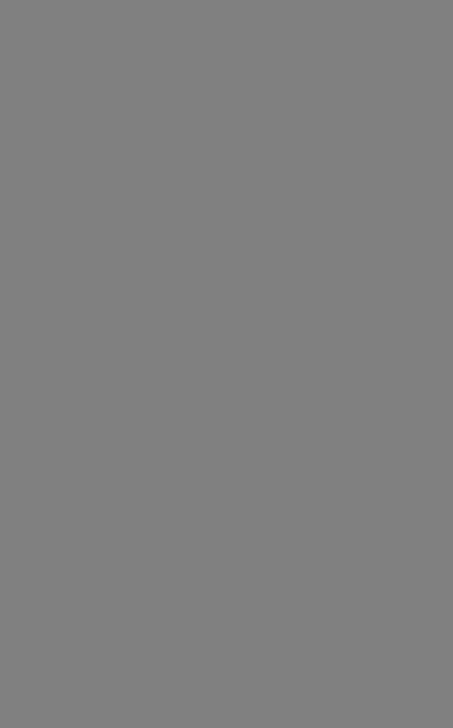
ность материала выше 93 % от теоретической и при газостатировании выполнены условия сохранения термодинамической стабильности нитрида кремния. Примерный цикл ГИП состоит из следующих этапов: сначала повышают температуру до раз мягчения капсулы, затем увеличивают давление и температуру, при 1700..Л 900 °С и давлении 100...200 МПа проводят ГИП в течение 1 ч и более.
При использовании в качестве добавок оксидов РЗЭ методом ГИП получена нитридкремниевая керамика со следующими свой ствами: фазовый состав (3-Si3N4 и кристаллические фазы; предел прочности при изгибе 800... 1000 МПа при 20 °С, 600...800 МПа
при 1200 °С; температура падения прочности 1300... 1400 °С.
Использование перехода a-Si3N4 -» p-Si3N4 в сочетании
с ГИП (1900 °С, 150 МПа, 2 ч) позволяет изготовить высоко плотную керамику без применения добавок. Полученная кера мика имеет при 1400 °С прочность при изгибе 750 МПа, что значительно превосходит прочность керамики с добавками.
Для повышения трещиностойкости Si3N4 могут быть ис пользованы различные добавки. Например, введение в керамику на основе Si3N4 некоторых металлоподобных тугоплавких со единений, имеющих более высокий, чем основная фаза, ТКЛР, создает в материале поле структурных напряжений, приводящих к образованию системы микротрещин, препятствующих разви
тию магистральной трещины.
Высокая трещиностойкость обеспечивается введением в Si3N4 частично стабилизированного диоксида циркония, опти мальное содержание которого в керамике для получения наи большего эффекта составляет 20 об. %. Прочность такого мате риала достигает 800... 1250 МПа, а трещиностойкость более 7,5 МПа-м1/2.
Трещиностойкость Si3N4 при высоких температурах, как и прочность, зависит от состава и структуры зернограничных фаз. Повышение тугоплавкости и вязкости зернограничной фазы приводит к увеличению трещиностойкости.
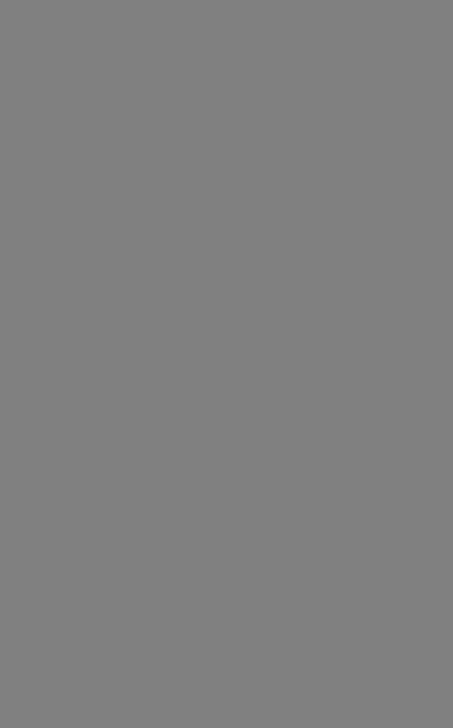
Исходные компоненты, условия синтеза и спекания подбирают таким образом, чтобы временно образующейся жидкой фазы было достаточно для получения беспористой керамики.
Беспористая керамика на основе Р-сиалона имеет плотность 3.. .3Д г/см3; твердость по Виккерсу 13...15 ГПа; модуль Юнга
200.. .280 ГПа; в интервале 20... 1200 °С ТКЛР (2,4...3,2) • КГ6КГ1
Изделия на основе Р-сиапона имеют более низкую теплопровод ность, чем керамика на основе Si3N4, что дает им определенное преимущество при использовании в качестве теплозащиты.
Керамика на основе р-сиапона обычно имеет примерно на 30 % меньшую прочность при изгибе, чем керамика на основе Si3N4, но на порядок более высокую стойкость к окислению. За щитный слой состоит не из чистого Si02, как у Si3N4, и не испы тывает опасных полиморфных превращений, поскольку его со став приближается к муллиту. Отсутствие добавок, образующих при нагревании жидкую фазу, приводит к тому, что высокие Прочностные свойства керамики на основе Р-сиалона сохраня ются до 1200 °С.
Помимо р-сиапона находит применение и а-сиалон. Кера мика на основе а-сиалона, полученная горячим прессованием, обладает плотностью 3,2 г/см3и при 20 и 1200 °С прочность при изгибе составляет 700 и 500 МПа соответственно.
В системе Si3N4-AlN -Y 20 3 имеется область, где а-сиалон сосуществует с p-Si3N4. В этой области составов без использо вания давления получена керамика с прочностью при изгибе 900 МПа, твердостью 20 ГПа, К1С 6 МПа м1/2 Трещиностойкость сиалонов может быть повышена до уровня ~ 7,6 МПа м1/2за счет формирования композиционных структур, в частности с удли ненными зернами P-Si3N4.
Керамику на основе сиалонов, особенно р-сиалона, исполь зуют в двигателестроении, производстве режущих инструмен тов, подшипников, насадок на горелки и т.д. Благодаря меньшей теплопроводности и большей стойкости к окислению сиалоны считают бблее подходящими для использования в адиабатиче
ских двигателях, чем нитрид кремния.