
5679
.pdf11.Изготовление соломенной шляпы вручную.
12.Изготовление и установка пластикового окна 1,5м * 1,5м.
13.Переплетение (брошюровка) научного текста формат 24/1,50 см.
14.Химчистка мягкой мебели на дому.
15.Изготовление парика длиной до 25 см.
16.Отбивка и заточка косы вручную.
17.Установка 10 м бордюрного камня проездной части дороги.
18.Проведение профилактического осмотра напольных кабинетных часов с регулировкой механизма боя.
19.Машинная вязка детского платья 36 размер.
20.Настройка и регулировка рояля концертного.
21.Реставрация шубы женской.
22.Изготовление парашюта.
23.Установка опоры ЛЭП.
24.Валка леса вручную (диаметр до 30 см) при проведении санитарных рубок вдоль полотна железной дороги.
По согласованию с преподавателем содержание операции может быть определено бакалаврантом самостоятельно. Необходимо обосновать полученный результат и достоверность источника информации.
3.5. Расчёт норматива ОП (оперативной работы)
Содержание задания:
Составьте интервальный план проведения исследования операции, проведите расчёт ОП с использованием графоаналитического метода и метода наименьших квадратов. Сравните полученные результаты, сделайте выводы.
Операция: Заливка металлом форм высотой 0,32 м.
S(площадь опоки) м2 = 0,08 : 0,22 .
В результате проведённых хронометражных наблюдений получены следующие результаты (таблица 37):
Таблица 37 – Зависимость времени заливки форм от её площади
|
Площадь опоки,S,м2 |
0,08 |
0,10 |
0,12 |
0,14 |
0,16 |
0,18 |
0,20 |
0,22 |
|
|
|
|
|
|
|
|
|
|
|
|
|
Время заливки формы, мин |
5,0 |
6,6 |
7,6 |
9,3 |
8,2 |
9,8 |
15,0 |
12,6 |
|
|
|
|
|
|
|
|
|
|
|
|
|
|
|
|
|
|
|
|
|
|
|
61
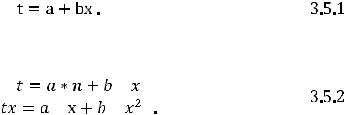
Зависимость времени выполнения операции от влияющего фактора описывается линейным уравнением:
Определение значений a и b в исследуемом уравнении при использовании метода наименьших квадратов производится на основе системы уравнений:
Метод графоаналитический предполагает обязательное построение графиков фактической зависимости нормативной прямой на основе полученных результатов, проведение анализа качества построения нормативной прямой, определение числовых значений параметров a и b.
3.6. Расчёт норматива ОТД (время отдыха)
Содержание задания
Используя метод экспертной оценки производственных факторов, определите норматив ОТД по шести произвольно выбранным видам работ из различных сфер деятельности (таблица 38).
Таблица 38 – Расчёт норматива времени на отдых в зависимости от влияющих производственных факторов
|
Нормативные значения Тотд по производственным |
Тотд, |
Тл.н. , |
||||||||||
Наименование |
|
факторам |
|||||||||||
|
мин в |
мин в |
|||||||||||
видов работ |
|
|
|
|
|
|
|
|
|
|
|
||
физич. |
нервная |
|
|
|
|
|
|
|
|
|
|||
|
|
|
|
|
|
|
|
|
смену |
смену |
|||
|
нагрузка |
нагрузка |
|
|
|
|
|
|
|
|
|
||
|
|
|
|
|
|
|
|
|
|
|
|
||
|
|
|
|
|
|
|
|
|
|
|
|
|
|
1. |
|
|
|
|
|
|
|
|
|
|
|
|
|
2. |
|
|
|
|
|
|
|
|
|
|
|
|
|
3. |
|
|
|
|
|
|
|
|
|
|
|
|
|
4. |
|
|
|
|
|
|
|
|
|
|
|
|
|
5. |
|
|
|
|
|
|
|
|
|
|
|
|
|
6. |
|
|
|
|
|
|
|
|
|
|
|
|
|
|
|
|
|
|
|
|
|
|
|
|
|
|
|
Сравните полученные результаты, сделайте выводы.
При выполнении задания можно использовать отраслевые нормативы времени на отдых по отдельным элементам условий труда или в качестве аналога, предполагаемые нормативы ОАО «Российские железные дороги» (приложение Б).
62
Нормативное значение времени на личные надобности персонала определите по одному из рассматриваемых видов работ. Результат обоснуйте.
3.7. Расчёт величины оперативного времени с использованием Базовой системы микроэлементных нормативов времени (БСМ–1)
Сущность микроэлементного нормирования сводится к тому, что самые сложные и многообразные по своему характеру трудовые действия работников являются комбинациями простых или первичных элементов, таких, например, как «переместить», «взять», «повернуть» и т. д., которые названы микроэлементами. Если выделить и изучить эти первичные элементы операций (микроэлементы), определить для них нормативы времени в зависимости от факторов, влияющих на их продолжительность, т. е. создать микроэлементные нормативы, появится возможность ещё до начала трудового процесса проектировать и нормировать самые разнообразные трудовые процессы, кроме тех, время выполнения которых предопределяется характеристиками используемого оборудования и режимами его работы.
Под микроэлементом понимается такой элемент трудового процесса, который дальше расчленять нецелесообразно. Микроэлементы состоят из одного или нескольких движений, выполняемых непрерывно. Например, микроэлемент «переместить» состоит из одного движения, микроэлемент «взять» состоит из нескольких мелких движений пальцев.
Микроэлементные нормативы представляют собой величины времени, полученные в результате статистической обработки затрат времени, изученных с применением киносъёмки, и установления наиболее вероятного времени, необходимого для большинства исполнителей по выполнению микроэлемента.
Основное преимущество микроэлементных нормативов в их аналитической и синтетической сущности, которая позволяет тщательно анализировать процесс, а также проектировать, обосновывать спроектированный рациональный вариант, улучшать метод работы.
Микроэлементные нормативы времени наряду с режимами работы оборудования и дифференцированными нормативами основного времени на машинноручные и машинные работы должны являться исходными данными для расчёта
63
межотраслевых и отраслевых нормативов времени различной степени укрупнения, в том числе укрупнённых нормативов и типовых норм времени.
Использование микроэлементных нормативов времени при расчёте межотраслевых и отраслевых норм и нормативов обеспечит их единую напряжённость.
Система микроэлементных нормативов времени БСМ–1 создана на базе исследований, проведённых на предприятиях и в организациях разных отраслей экономики: автомобилестроения, приборостроения, тракторного и сельскохозяйственного машиностроения, текстильной, швейной, обувной, мясной и полиграфической промышленности, а также в организациях связи.
Изучению подвергались различные виды работ:
–заготовительные, механическая обработка и сборка в машиностроении;
–изготовление обуви, пошив верхней одежды, ткачество в лёгкой промышленности;
–обработка письменной корреспонденции, посылок, пачек и мешков с печатью (газеты, журналы и т. д.) в организациях связи;
–обвалка говядины, съём шкур, вязка варёных колбас, обработка туш крупного рогатого скота в мясной промышленности.
Система содержит нормативы времени на 19 групп микроэлементов, в том числе на 10 групп микроэлементов, выполняемых руками, 7 групп микроэлементов, выполняемых ногами и туловищем, и 2 группы микроэлементов, выполняемых глазами. В зависимости от способа выполнения микроэлементы подразделяются на виды. Всего системой предусмотрено 36 видов
Содержание задания
Используя нормативные значения БСМ–1 (приложение В), исследуйте и спроектируйте трудовую операцию, содержание которой определите в соответствии с заданием №1 раздела «Нормирование труда» данного учебного пособия.
Результаты представьте в виде нормативной карты (таблица 39). Сравните со значениями, полученными при использовании методики МОДАПС.
64
Таблица 39 – Исследование и проектирование трудовой операции
КАРТА 6. Исследования и проектирования трудового процесса |
|
|
Лист 3 |
|
|||||||
|
|
|
|
|
|
|
|
|
|
||
III. Метод выполнения операции (существующий) |
|
|
|
|
|
||||||
|
|
|
|
|
|
|
|
|
|||
№ |
Содержа- |
№ п/п мик- |
Левая рука |
|
|
Правая рука, туловище, ноги |
|
||||
п/ |
ние трудо- |
роэлемента |
|
|
|
|
|
|
|||
Наименова- |
Код микро- |
Время |
Код микро- |
Наименова- |
|||||||
п |
вого |
про- |
|
ние |
микро- |
элемента |
по БСМ, |
элемента |
ние микро- |
||
|
цессапо |
|
элемента |
|
тыс.доли |
|
элемента |
||||
|
приёмам |
|
|
|
|
мин |
|
|
|
|
|
|
|
|
|
|
|
|
|
|
|||
1. |
Взять |
1 |
Протянуть |
ПР1 (S 400) |
8,7 |
7,2 |
ПР1 (S 300) |
Протянуть |
|||
|
детали |
|
руку |
|
(ОС1;К3) |
|
|
(ОС1; К3) |
руку |
|
|
|
для |
пер- |
2 |
|
|
|
|
6,8 |
В1 (З0,5) |
Взять |
про- |
|
вой |
ман- |
|
|
|
|
|
|
(ОС2;К3) |
кладку |
из |
|
жеты |
|
|
|
|
|
|
|
пачки |
|
|
|
|
|
3 |
Взять манже- |
В1 (З 0,5) |
6,8 |
|
|
|
|
|
|
|
|
|
ту из пачки |
(ОС2; К3) |
|
|
|
|
|
|
|
|
|
|
|
|
|
|
|
|
||
2. |
Сложить |
4 |
Переме- |
П1 (S 400) |
8,7 |
7,2 |
ПР1 (S 300) |
Переме- |
|
||
|
детали |
|
стить к про- |
(ОС1; К3) |
|
|
(ОС1; К3) |
стить |
к |
||
|
|
|
|
кладке |
|
|
|
|
манжете |
||
|
|
|
5 |
Установить |
УП2 (l 260) |
– |
7,6 |
УП2 (l 260) |
Установить |
||
|
|
|
|
(совместить |
(ОС1; ОР3) |
|
|
(ОС1; ОР3) |
(совместить |
||
|
|
|
|
по контуру) |
|
|
|
|
по контуру) |
||
|
|
|
6 |
Переме- |
П2 (S 200; l |
– |
6,6 |
П2 (S 200; l |
Переме- |
|
|
|
|
|
|
стить на пол |
260) |
|
|
260) |
стить к сто- |
||
|
|
|
|
|
|
(ОС1; К2) |
|
|
(ОС1; К2) |
лу |
|
|
|
|
|
|
|
|
|
|
|
|
|
|
|
|
7 |
Отпустить |
ОТ1 |
1,2 |
|
|
|
|
|
|
|
|
8 |
Протянуть |
ПР1 (S 150) |
4,9 |
|
|
|
|
|
|
|
|
|
руку к дру- |
(ОС1; К2) |
|
|
|
|
|
|
|
|
|
|
гому |
участ- |
|
|
|
|
|
|
|
|
|
|
ку детали |
|
|
|
|
|
|
|
|
|
|
9 |
Взять |
де- |
В1 (З 0,5) |
4,2 |
|
|
|
|
|
|
|
|
таль |
|
(ОС1; К2) |
5 |
|
|
|
|
|
|
|
10 |
Перегнуть |
УП2 (l 260) |
3,3 |
3,3 |
УП2 (l 260) |
Перегнуть |
||
|
|
|
|
край детали |
(ОС1; ОР2) |
5 |
5 |
(ОС1; ОР2) |
край детали |
||
|
|
|
|
|
|
|
|
|
|
|
|
65

3.8. Методические основы расчёта нормы времени на работы, выполненные на токарном станке
Обработку деталей с применением токарных станков принято называть токарными работами. Расчёт нормы времени на эти виды работ производится по методике расчёта норм и нормативов для станочных работ с использованием типовых общемашиностроительных нормативных таблиц. Выбор и обоснование параметров режимов резания производится исходя из конкретных производственных условий и технологической карты производственного задания:
(3.8.1)
где tпз, tобс, tотпопределяется по нормативным таблицам, непосредственно учитывая содержание производственного задания:
,
где l – геометрические размеры обрабатываемой поверхности (мм); l1 – величина врезания и перебега резца (мм);
l2 – величина взятия пробной стружки (мм);
n – скорость вращения обрабатываемой детали (об/мин);
S – подача режущего инструмента в мм на один оборот детали; i – число проходов (шт).
Так как токарная обработка предполагает снятие в результате обработки заготовки излишнего припуска до получения детали определённых параметров, то необходимо учитывать, что слой материала, который может быть срезан за один проход, может быть меньше, чем весь припуск на резание. Глубина резания за один проход обозначают – «t», а весь припуск на резание обозначается буквой «h».
Для того чтобы определить количество проходов, необходимых для снятия всего припуска, пользуются формулой
причём i всегда целое число. Если в расчете i получается числом дробным, необходимо округлить результат до ближайшего большего целого числа.
Например: если i = 2,3 , принимаем i = 3, но глубина резания для двух прохо-
дов будет равна t, а для третьего – .
66
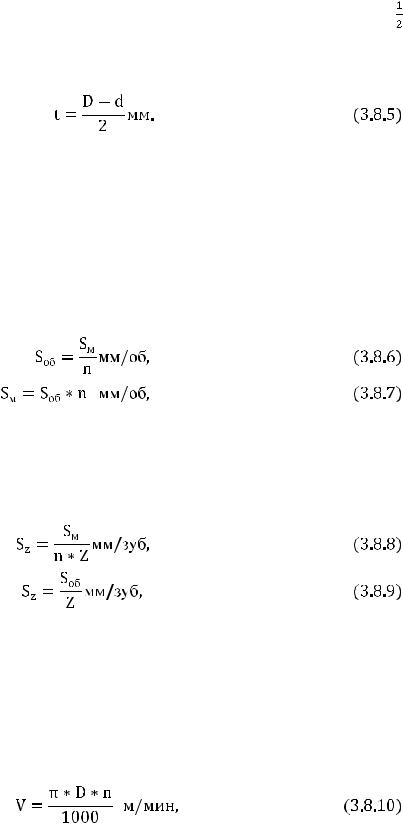
При обработке цилиндрических поверхностей (обтачивание, растачивание,
рассверливание, внешнее и внутреннее шлифование) глубина резания равна
разности диаметров заготовки до обработки (D) и детали после обработки за данный проход (d):
Подача – величина перемещения режущего инструмента относительно обрабатываемой детали, пройденная за определённый отрезок времени. Подача обозначается буквой «S».
При работе на обрабатывающих станках различают три вида подачи – минутная, за один оборот, на один зуб режущего инструмента.
Между минутной подачей (Sм) и подачей на один оборот (Sоб) имеется следующая зависимость:
где n – число оборотов обрабатываемой детали или режущего инструмента в 1 мин.
Между подачей на один зуб (Sz) и подачами Sм и Sоб имеется следующая зависимость:
где Z – число зубьев режущего инструмента.
Скорость резания (V) – это перемещение режущей кромки инструмента относительно обрабатываемой поверхности детали в направлении главного движения в единицу времени. При обработке на станках с вращательным главным движением (токарные, фрезерные, сверлильные и др.) скорость резания измеряется по окружности вращения, поэтому называется окружной и определяется по формуле
где D – начальный диаметр обрабатываемой поверхности детали или диаметр режущего инструмента, мм;
67

n –число оборотов обрабатываемой детали или режущего инструмента в
1 мин;
– отношение длины окружности к диаметру, равное 3,14.
Выбор режима резания (глубины, подачи, скорости) производится с учётом частоты вращения шпинделя станка, сил резания, крутящего момента и мощности, потребной на резание. Эти понятия являются дополнительными характеристиками режима резания.
Число оборотов детали измеряется в об./мин.
От выбранной скорости резания зависит частота вращения шпинделя станка. Зная скорость резания, можно определить число оборотов детали, инструмента или шпинделя станка в минуту. Из вышеприведённой формулы (п.3.6.10) получаем:
В практике технического нормирования принято параметры режимов резания выбирать исходя из показателей обрабатываемости материала, режущих свойств инструментального материала, геометрических параметров и стойкости инструмента, требований к чистоте и точности обработки.
Порядок выбора режима резания
Назначению режима резания предшествует разработка технологического процесса, в котором должны содержаться следующие данные:
а) исполнительные размеры, допуски и шероховатости (чистота обработанной поверхности);
б) припуск на обработку; в) конструкции, геометрические параметры и материал режущей части
инструмента; г) механические свойства обрабатываемого материала (предел прочности σв
кг/мм2 или твёрдость по Бринелю НВ); д) размеры заготовки и способ её крепления в приспособлении; е) тип и модель станка.
Выбор режима резания рассмотрим на конкретном примере для токарных работ.
68

Назначение режима резания и определение основного машинного времени осуществляется отдельно для черновой и чистовой токарной обработки в следующей последовательности;
1.Выбирается максимально возможная глубина резания.
2.Устанавливается максимально допустимая величина подачи.
3.Определяется норматив скорости резания и соответствующее ему число оборотов шпинделя в минуту.
4.Определяются силы резания P и мощность, потребная для резания.
5.Найденные параметры режима резания проверяются по возможности их осуществления и корректируются в соответствии с паспортными данными.
6.Рассчитывается время: основное, оперативное, штучное штучнокалькуляционное.
Характеристика технологического процесса
I |
2 |
3 |
|
|
71,5 |
|
|
|
61,5 |
|
|
|
|
|
|
81,5
515
725
80 70
725
Рисунок 4 – Чертёж вала
69

Наименование операции – обточка |
Изделие – вал (рисунок 4). |
|
по диаметру и шеек черновая. |
Наименование детали – вал. |
|
Разряд работы – 4. |
№ детали. |
|
Станок: токарно-винторезный. |
№ чертежа. |
|
Модель – 1К62, N= 10 кВт. |
Количество деталей на одно изделие. |
|
Инвентарный № 157. |
|
|
Число |
станков, обслуживаемых |
Род и размер заготовки – горячая |
рабочим – 1. |
штамповка. |
|
Число |
одновременно устанавливае- |
90 725 мм с припуском по шейкам ва- |
мых деталей –1. |
ла 5 мм на сторону, сталь 40Х, σв= 72 |
|
|
|
кг/мм2. |
|
|
Вал черновой – 30 кг. |
|
|
Размер партии – 200 шт. |
|
|
|
Исходные данные к примеру
Деталь – вал.
Операция – обточка по диаметру и шейке с одной стороны, черновая. Обрабатываемый материал – сталь хромистая 40Х, σв = 72 кг/мм2. Характер заготовки – горячая штамповка 90*75 мм.
Вес заготовки – 30 кг.
Станок – токарно-винторезный 1К62.
Инструмент – резец проходной, γ = 45˚, Т5К10, 1 шт.; резец проходной, γ = 90˚; Т5К10, 1 шт.
Приспособление – центра, хомутик.
Выбор глубины резания
Исходя из припуска на обработку устанавливается максимально возможная глубина резания «t», т.к. она оказывает меньшее влияние на стойкость резца и скорость резания, чем подача.
Надо стремиться, чтобы припуск на черновую обработку снять сразу. Сумма припуска на черновую обработку (hчерн) и чистовую обработку (hчист) представляет собой припуск на сторону при токарной обработке цилиндрических поверхностей.
По величине общего припуска на обработку 5,0 мм (на сторону) с учётом необходимости оставления припуска на чистовую обработку 0,75 мм устанавли-
70