
5595
.pdfРежущий механизм представляет собой комплект серповидных ножей, заточенных с одной стороны, и стальной гребёнки, которая очищает лезвия ножей от мяса. В соответствии с требованиями качества фарша куттер должен иметь не менее 2 скоростей (1500/3000 об./мин), а ножевая головка не менее 3 пар ножей. Частота вращения ножей до 100 об./сек. Нож куттера имеет режущую кромку в виде прямой линии с заточкой в виде клина с углом при вершине 15 – 30°. Толщина ножа принимается по условиям работы
3...7 мм.
Конструкцию ножей и ножевой головки (см. рисунок 27) выбирают такой, чтобы обеспечить их лёгкую балансировку и поддерживать минимальный зазор между внутренней поверхностью чаши и режущей кромкой ножа.
Ножи 1 укрепляют на вал 5 гайкой 8, и они удерживаются силой трения, их изготавливают с отверстиями в посадочной части 2. Отверстия 4 и 7 предназначены для входа исходного сырья и удаления измельчённого.
Привод ножевого вала (см. рисунок 27) – электродвигатель, клиноремённая передача.
Механизм выгрузки – тарелка. Привод включает червячный редуктор, к которому с одной стороны фланцем присоединён электродвигатель, с другой – труба выгружателя с проходящим через неё валом привода тарелки. В момент начала выгрузки продукта она получает вращение, а так как одновременно включается муфта червячной пары, то медленно опускается в чашу – фарш выгружается. При достижении тарелкой дна чаши муфта отключается, движение тарелки вниз прекращается. Она продолжает вращаться до полной выгрузки продукта, затем включается реверс и тарелка поднимается вверх.
Механизм загрузки – тележка для транспортирования продукта к куттеру и механизм её опрокидывания, смонтированный в чугунной станине.
Принцип работы заключается в следующем. В чашу загружают сырьё, предварительно измельчённое на волчке. Сырьё, медленно вращаясь с чашей, подаётся к быстровращающимся ножам. Происходит мелкое измельчение. Время куттерования зависит от вида продукта и степени его измельчения до поступления в куттер. Степень измельчения зависит от длительности куттерования, скорости резания, числа ножей и их заточки, расстояния между крайними ножами и чашей (минимальное 2 мм).
91
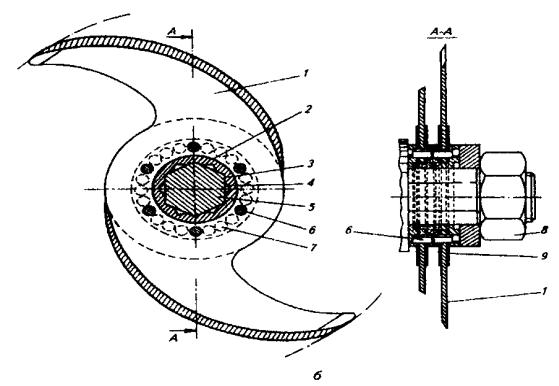
Рисунок 27 – Ножевая головка куттера: 1 – нож; 2 – посадочная часть; 3 – втулка; 4 – отверстие; 5 – вал; 6 – штифт; 7 – отверстие; 8 – гайка; 9 – диск
Измельчение продукта без добавления воды вызывает увеличение потребляемой мощности на 30 – 40%. В процессе измельчения в куттер добавляют воду или специальный чешуйчатый лёд. Этим достигается соблюдение рецептуры фарша, а также снижение его температуры, которая при куттеровании повышается на 1.. .4 °С. Технические характеристики куттера представлены в таблице 13.
Таблица 13 – Технические характеристики куттера
Характеристика |
|
Значение |
|
|
|
Производительность, кг/ч |
|
1200 |
|
|
|
Вместимость чаши, м3 |
|
0,125 |
|
|
|
Коэффициент загрузки чаши |
|
0,4…0,6 |
|
|
|
Число ножей |
|
2 |
|
|
|
Длительность цикла, мин |
|
3…5 |
|
|
|
Скорость резания ножей, м/с |
|
65 |
|
|
|
Установленная мощность, кВт |
|
30,6 |
|
|
|
Занимаемая площадь, м2 |
|
5,5 |
|
|
|
Масса, кг |
|
2200 |
|
|
|
|
92 |
|
Для безопасной разборки режущего механизма при санитарной обработке машины применяют приспособление для отвинчивания зажимной гайки и специальный крючок, прилагаемые в комплекте поставки. Зона вращения ножей куттера и передаточные механизмы должны быть закрыты крышками, сблокированными с пусковым устройством. При открытой любой из крышек куттера должна быть исключена возможность пуска куттера в работу. Для удобной и безопасной выгрузки из чаши переработанного фарша куттер следует обеспечивать тарельчатым выгружателем, сблокированным с пусковым устройством. При подъёме тарелки выгружателя должно прекращаться вращение самой тарелки и чаши куттера. Дежа куттера – мешалки должна иметь предохранительную планку, сблокированную с приводом, обеспечивающую отключение машины при касании рамки дежи.
После каждого цикла работы необходимо разбирать ножи, чистить и промывать, проверять состояние остроты. Также необходимо промывать чашу от мясных остатков.
Некоторые виды неисправностей куттера представлены в таблице 14.
Таблица 14 – Характерные неисправности куттера
Неисправность |
Вероятная причина |
Способ устранения |
|
|
|
Не обеспечивается |
Затупились ножи |
Снять ножи – заточить |
нужное качество |
Слабо затянута гайка |
Затянуть гайку, |
измельчения сырья |
фиксации ножей |
отрегулировать зазор между |
|
|
ножом и чашей |
|
|
|
При пуске |
Слабое натяжение ремней |
Отрегулировать натяжение |
установки ощутимы |
привода ножевого вала |
ремней привода ножевого |
вибрации |
|
вала |
|
|
|
Шумы в редукторе |
Грязное масло. Износились |
Промыть и заменить масло |
при работе машины |
подшипники |
Разобрать редуктор, заменить |
|
Небольшой уровень масла |
подшипники Долить масло |
|
|
|
Производительность куттера зависит от величины загрузки, характера измельчаемого сырья и продолжительности обработки и рассчитывается по формуле
Q |
V |
|
, |
(34) |
|||
|
|
|
0 |
|
|||
|
|
|
|
||||
|
1 |
|
|
|
|
|
|
|
|
|
|
||||
|
|
|
|
|
|
93
где Q – производительность куттера (м/с);
τ – длительность процесса измельчения (сек); τ0 – длительность вспомогательных операций (сек); V – геометрическая вместимость чаши (м)3;
α – коэффициент загрузки чаши (0,5... 0,65) – для открытых и (0,7 – 0,8) – для вакуумных;
ρ – плотность сырья (кг/м3).
Мощность привода куттера, кВт
N N 1 N 2 N 3 |
|
(35) |
||||
|
|
|
|
|
||
где N1 – мощность, необходимая для привода режущего механизма, кВт: |
|
|||||
N |
|
|
a F z n a |
, |
(36) |
|
1 |
3,6 пр |
|||||
|
|
|
|
|||
|
|
|
|
|
где а – удельный расход энергии на перерезывание слоя фарша одним ножом за один оборот, кДж/м2 (а = 2,7... 3,1 кДж/м2);
z – число ножей;
F – площадь сечения слоя фарша в чаше куттера (м2) ( F = 0,1 ...0,3 м2); n – частота вращения ножевого вала (с-1) ( n = 20...50 с-1);
ηa – коэффициент запаса мощности двигателя (ηa = 1,3... 1,4); ηпр – КПД привода ножевого вала (ηпр = 0,8... 0,9).
N2 – мощность, расходуемая на привод вращения чаши (кВт) (N2 = 1...3 кВт – в зависимости от вместимости чаши);
N3 – мощность , расходуемая на выгрузку сырья (кВт) (N3 = 0,6... 1,0 кВт – при n до 30 с-1).
Вопросы для самоконтроля
1.Из каких основных частей состоит куттер?
2.Какое количество ножей может иметь куттер?
3.В чём состоит преимущество вакуумных куттеров перед обычными?
4.От каких параметров зависит степень измельчения?
5.Как определить производительность и мощность куттера?
94
15. ИЗУЧЕНИЕ РАБОТЫ, УСТРОЙСТВА И ПРАВИЛ ЭКСПЛУАТАЦИИ ВОЛЧКА К6-ФВП
ЦЕЛЬ ЗАНЯТИЯ
1.Изучение устройства и принципа работы волчка, требования безопасной эксплуатации волчка.
2.Определение производительности волчка и мощности его привода.
3.Обработка результатов.
ПОРЯДОК ВЫПОЛНЕНИЯ РАБОТЫ
1. Изучить теоретический материал.
2. Вычертить принципиальную схему машины в масштабе 1,5:1, используя миллиметровую бумагу формата А4.
3.Определить основные технические характеристики волчка.
4.Заполнить журнал №4.
5.Ответить на контрольные и дополнительные вопросы.
КРАТКИЙ ТЕОРЕТИЧЕСКИЙ МАТЕРИАЛ
Волчок предназначен для среднего и мелкого измельчения. Волчок установлен на станине 1 сварной конструкции и включает в себя механизм подачи сырья, режущий механизм 5, привод 2 и загрузочную чашу 8 (см. рисунок 28). В верхней части машины имеется загрузочный бункер сварной конструкции для приёма измельчаемого сырья. В механизм подачи сырья входят рабочий шнек 4, вспомогательный шнек 3 и рабочий цилиндр 7. Рабочий цилиндр имеет рёбра. Их расположение продольное, что предотвращает проворачивание мяса вместе со шнеком и возврат его в зону загрузки. Принудительная подача сырья в рабочую часть осуществляется вспомогательным шнеком – это обеспечивает постоянную загрузку режущего механизма и высокую удельную производительность. Рабочий шнек имеет витки, уменьшающиеся в сторону выгрузки продукта. Чем длиннее рабочий шнек, тем меньше мяса вытесняется обратно в загрузочную часть и выше производительность волчка. Чем больше витков, тем образуется как бы лабиринт, что снижает возможность передавливания фарша из зоны давления в зону загрузки.
95
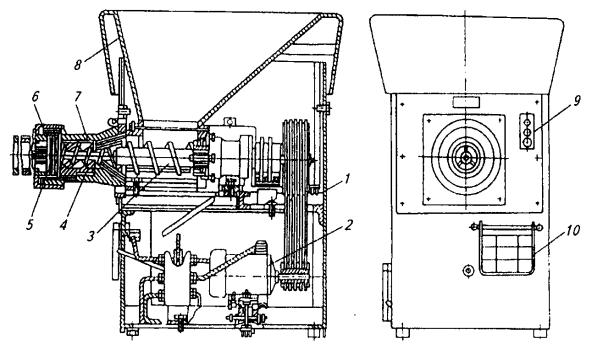
Рисунок 28 – Волчок К6-ФВП-120: 1 – станина; 2 – привод; 3 – подающий шнек; 4 – рабочий шнек; 5 – режущий механизм; 6 – прижимное устройство; 7 – цилиндр; 8 – бункер; 9 – кнопки управления; 10 – откидная площадка
Важнейшая часть волчка – режущий механизм (см. рисунок 29). Волчок имеет плоскую форму и представляет собой последовательное чередование неподвижных решёток и вращающихся ножей. Самый распространённый механизм измельчения состоит из приёмной, выходной и промежуточной решёток, двусторонних и односторонних многозубых ножей. Особенности конструкции решёток – это форма и размеры отверстий, представляющие собой кольцевые режущие кромки. Диаметр отверстий определяет скорость истечения сырья и степень его измельчения. Форма отверстий – круглая без скосов, диаметр отверстий 3,5,12,16.
За основную техническую характеристику волчка принимают диаметр решётки. Рекомендуемая толщина решётки 8 – 18 мм. При толщине меньше 8
мм может произойти выдавливание решётки, т.к. в волчке создаётся давление порядка 3-6 МПа. В режущий механизм входят крестовидные двусторонние ножи. Ножи имеют криволинейные зубья, между которыми расположены проходные каналы для продукта. Режущая кромка ножа должна быть не менее 0,5 мм, иначе образуется стружка. Приёмный нож выполняется толщиной 18 – 20 мм, толщина кромки 0,5 – 2 мм (очень быстро вырабатывается). Режущий механизм необходимо собирать гак, чтобы
96
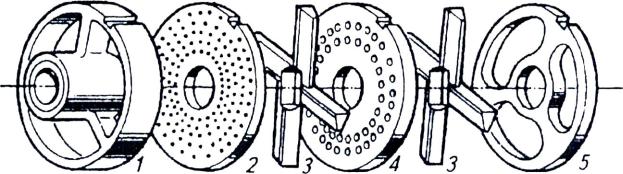
измельчение было вначале более грубым, затем мелким. Это обеспечивает меньшие затраты энергии и соответственно продукт меньше нагревается. В ножевом механизме с 4 режущими плоскостями на палец шнека надевают приёмную решётку, двусторонний нож, промежуточную решётку с диаметром отверстия 16 мм, второй двусторонний нож, выходную решётку с диаметром 5 мм и прижимное кольцо. Ножи и решётки умеренно затягивают зажимной гайкой. Одним из основных факторов, влияющих на качество работы волчка, является усилие, с которым режущие кромки ножей прижимаются к плоскостям решёток. Чрезмерное усилие ведёт к увеличению силы трения в паре и как следствие к нагреву, износу, увеличению энергозатрат, перегреву продукта. Недостаточное усилие способствует появлению зазора в паре, что приводит к нарушению процесса резания и выделения влаги. Для регулирования прижатия ножей к решётке применяют прижимные устройства, выполненные в виде гайка-маховик.
Рисунок 29 – Режущий механизм волчка: 1 – кольцо-подпора; 2 – выходная решётка; 3 – четырёхзубый нож; 4 – промежуточная решётка; 5 – приёмная решётка
Привод волчка выполнен в виде электродвигателя с клиноремённой передачей. Защитно-пусковая аппаратура расположена в электрошкафу.
Принцип работы: мясо весом 0,5 кг и температурой 0...+2°С подаётся в загрузочный бункер и шнеками направляется к режущему механизму.
Конструкция загрузочной горловины волчка должна предотвращать образование «сводов» и зависания обрабатываемого продукта. В случае необходимости для проталкивания сырья предусматриваются толкатели, обеспечивающие безопасность и удобство в работе. Привод к исполнительным органам волчка должен располагаться внутри станины и
97
иметь сплошное ограждение. Ограждения и щитки на монтажные окна должны иметь крепления, исключающие их снятие или открывание без инструмента, специальных ключей и приспособлений.
Волчки следует оборудовать откидным столом и подножкой, обеспечивающими удобство санитарной обработки и разборки режущего инструмента. Откидной стол и подножка блокируются с пусковым устройством, предотвращающим пуск в работу волчка при откинутой площадке или подножке. Для безопасной разборки режущего механизма при санитарной обработке машины применяют приспособление для отвинчивания зажимной гайки и специальный крючок, прилагаемый в комплекте поставки. Технические характеристики волчка К6-ФВП-120 представлены в таблице 15. Виды неисправностей волчка представлены в таблице 16.
Таблица 15 – Технические характеристики волчка К6-ФВП-120
Характеристика |
Значение |
Производительность, кг/ч |
2500 |
Диаметр, мм: |
|
отверстий решётки |
3, 5, 12, 16 |
режущего механизма |
120 |
Частота вращения шнека, об./мин |
150 |
Мощность электродвигателя, кВт |
12,5 |
Габаритные размеры, мм |
1600x1680x3000 |
Масса, кг |
800 |
Таблица 16 – Характерные неисправности волчка
Неисправность |
Вероятная причина |
Способ устранения |
|
|
|
Волчок не режет, а мнёт |
Неправильная |
Выключить |
мясо |
регулировка нажима гайки |
электродвигатель, вынуть |
|
|
решётки, ножи и шнек |
|
|
очистить их от жил и плёнок, |
|
|
установить на место и |
|
|
отрегулировать нажимную |
|
|
гайку |
Повышенный шум в |
Нож и решётки чрезмерно |
Ослабить нажим гайки |
редукторе или остановка |
зажаты гайкой |
|
двигателя |
|
|
|
|
|
Перерабатываемый |
Затупились ножи и |
Заточить и притереть ножи и |
продукт нагревается, а |
решётки. Неплотное |
решётки |
плёнки и жилы |
прилегание ножей и |
|
наматываются на ножи |
решёток |
|
При включении волчка |
Отсутствует одна фаза |
Проверить электропроводку |
электродвигатель гудит |
статорной цепи |
и контакты магнитного |
|
|
пускателя. Устранить дефект |
|
|
|
98
Задание. Дать описание волчка типа К6-ФВП-120, рассчитать производительность и мощность электродвигателя для его привода. Варианты исходных данных приведены в таблице 16: D – наружный диаметр винта шнека равен; d — диаметр вала в зоне загрузки, S — шаг винта в зоне загрузки, м; δ — толщина витка, м; n — частота вращения, об./мин. В расчётах учесть КПД передачи от электродвигателя 0,68 и плотности мяса
900 кг/м3.
Таблица 17 – Варианты исходных данных
Исходные |
|
|
|
|
Вариант |
|
|
|
|
|
|
|
|
|
|
|
|
|
|
|
|
данные |
|
|
|
|
|
|
|
|
|
|
1 |
2 |
3 |
4 |
5 |
6 |
7 |
8 |
9 |
10 |
|
|
|
|
|
|
|
|
|
|
|
|
D, м |
0,16 |
0,12 |
0,14 |
0,1 |
0,12 |
0,16 |
0,14 |
0,12 |
0,1 |
0,14 |
|
|
|
|
|
|
|
|
|
|
|
d, м |
0,1 |
0,08 |
0,09 |
0,08 |
0,1 |
0,12 |
0,1 |
0,08 |
0,08 |
0,1 |
|
|
|
|
|
|
|
|
|
|
|
S, м |
0,1 |
0,09 |
0,1 |
0,08 |
0,09 |
0,1 |
0,08 |
0,07 |
0,07 |
0,08 |
|
|
|
|
|
|
|
|
|
|
|
δ, м |
0,01 |
0,008 |
0,009 |
0,01 |
0,008 |
0,008 |
0,007 |
0,006 |
0,005 |
0,006 |
|
|
|
|
|
|
|
|
|
|
|
п, мин-1 |
150 |
140 |
130 |
120 |
110 |
100 |
90 |
120 |
140 |
110 |
|
|
|
|
|
|
|
|
|
|
|
Порядок вычислений производится в следующей последовательности: Производительность волчка по режущей способности измельчающего механизма Q, кг/с определяется по формуле
Q F0 |
V0 |
, |
(37) |
||
|
|
|
|
||
где F0 – суммарная площадь отверстий в ножевой решётке (м2); |
|
||||
F |
d02 |
Z |
0 , |
|
|
0 |
4 |
|
|
(38) |
|
где d0 – диаметр одного отверстия (м); |
|
||||
Z0 – число отверстий ножевой решётки; |
|
||||
V0 n rH rB tg H KВ , |
(39) |
||||
где V0 – скорость продвижения продукта через отверстие решётки; |
|
||||
n – частота вращения шнека (об./сек); |
|
rН и rB – наружный и внутренний радиусы последнего витка шнека (м);
βH – угол между плоскостями последнего витка шнека и ножевой решётки;
99
КB – коэффициент проворачивания продукта относительно оси шнека (КB
=0,35-0,4);
φ– коэффициент использования площади отверстия решётки (φ = 0,7-0,8). р – плотность продукта (кг/м3), р=1000 кг/м3.
Производительность волчка по пропускной способности шнека.
Производительность волчка определяем по формуле
G 60 |
|
D2 |
d2 n s |
|
4 |
|
(40) |
где G – производительность волчка, кг/ч,
β – коэффициент использования шнека (практически (β = 0,25 ... 0,35); D – диаметр шнека (м);
d – диаметр вала шнека (м);
n – частота вращения шнека (мин-1); s – средний шаг шнека (м);
φ – коэффициент, учитывающий неравномерность загрузки сырья (φ = 0,2);
ρ – плотность продукта (кг/м3).
Мощность электродвигателя для привода волчка:
N |
G |
|
|
|
|
1000 |
(41) |
|
|
|
где N – мощност электродвигателя для привода волчка (кВт), G – производительность волчка (кг/ч);
α – удельный расход энергии при измельчении (кВт) (для сырого мяса значения приведены далее, а для варёного мяса они уменьшаются примерно в
2раза);
η– КПД привода (η = 0,85 ... 0,90).
Диаметр отверстий решётки волчка, мм |
1,8 |
2 |
3 |
Удельный расход энергии α, кВт |
0,35...0,45 |
0,2...0,3 |
0,15...0,20 |
100