
Учебное пособие 800232
.pdf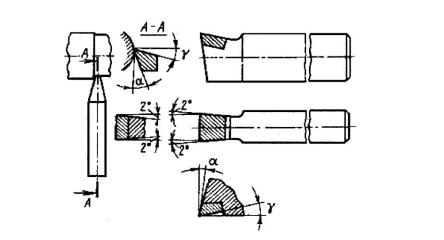
И. А. Чечета О. Н. Кириллов
РЕЗАНИЕ МАТЕРИАЛОВ
Часть 2 Курс лекций
Воронеж 2004
МИНИСТЕРСТВО ОБРАЗОВАНИЯ РОССИЙСКОЙ ФЕДЕРАЦИИ Воронежский государственный технический университет
И. А. Чечета О. Н. Кириллов
РЕЗАНИЕ МАТЕРИАЛОВ
Часть 2
Утверждено Редакционно-издательским советом университета в качестве курса лекций
Воронеж 2004
ВВЕДЕНИЕ
Любой из известных способов резания, целью которого является удаление определенного слоя материала посредством превращения его в стружку, реализуется за счет применения специального инструмента и соответствующего оборудования (станка). При этом имеется в виду, что инструмент располагает режущим лезвием, а станок обеспечивает те виды движения, при наличии которых режущее лезвие, внедряясь в обрабатываемую поверхность на заданную глубину и перемещаясь в соответствии с назначенной подачей, превращает срезаемый слой материала в стружку.
Основными конечными показателями процесса при имеющейся скорости резания являются уровень шероховатости обработанной поверхности, еѐ геометрическая точность и физико-механическая характеристика (например, упрочнение и глубина залегания изменившейся микротвердости). Так как исходные параметры резания, среди которых главенствуют глубина резения, подача, скорость резания, СОЖ, взаимно связаны между собой и совокупно влияют на результаты резания, то в практике машиностроения выработалась условная градация процессов резания. Сущность этой градации в том, что все процессы резания разделяют на черновые (предварительные), чистовые и доводочные. Кроме того, в каждом из способов резания существует своя дополнительная градация. Например, различают черновое (обдирочное), получистовое, чистовое и тонкое точение.
Подобная градация характерна и другим способам резания. |
|
||
В связи с тем, что для каждой градации способов |
резания сформированы |
||
диапазоны численных значений |
шероховатости, точности и других характеристик |
||
обработанных поверхностей, то совокупность этих |
показателей оценивают |
как |
|
технологические возможности способов резания, а |
необходимые для |
реализации |
резания станки, инструмент и выявляющаяся длительность процесса позволяют судить об экономичности того или иного способа резания.
С учетом изложенного во втором разделе конспекта по дисциплине "Резание материалов" представлены сведения, касающиеся особенностей резания конструкционных материалов как лезвийным, так и абразивным инструментом.
Материал учебного пособия соответствует программе подготовки дипломированных специалистов по направлению 651400 "Машиностроительные технологии и оборудование" специальности 120100-"Технология машиностроения", дисциплина "Резание материалов". Пособие может быть также использовано и при изучении курсов "Основы технологии машиностроения" и "Технология машиностроения" того же направления профессиональной подготовки. Практическая ценность пособия состоит в систематизации условий, необходимых для формирования технологических процессов, относящихся к обработке конструкционных материалов резанием.
1 ОСНОВНЫЕ СПОСОБЫ РЕЗАНИЯ МАТЕРИАЛОВ
1.1 Технические средства для резания
Основными средствами для реализации процесса резания являются:
технологическое оборудование, представляющее собой основное орудие производства, например, металлорежущие станки, в которых для процесса резания размещают заготовки и средства воздействия на эти заготовки (в том числе и источники энергии или соответствующие звенья для передачи энергии);
технологическая оснастка, представляющая собой дополнительное орудие производства, добавляемое к основному оборудованию для выполнения процесса резания.
К технологической оснастке относятся режущий инструмент, вспомогательный инструмент (в виде устройств, обеспечивающих режущему инструменту необходимую координацию в рабочей позиции), приспособление для крепления заготовки на период резания.
Подготовка (наладка) технологического оборудования и оснастки к реализации
процесса резания заключается в выполнении ряда действий, к которым относят
крепление на станке и выверку согласно заданным техническим требованиям
режущего инструмента, приспособления для заготовки, укладки самой заготовки в
приспособление, а также переключение органов управления станком с целью
обеспечить заданный режим резания.
Дополнительное регулирование технологического оборудования и оснастки для
восстановления |
или |
коррекции |
параметров резания представляет собой подналадку. |
||
Необходимость подналадки технологического оборудования |
предопределена тем, что |
||||
конфигурация |
обрабатываемых поверхностей заготовки |
отличается от |
|||
конфигурации |
будущей |
детали наличием слоя (припуска на механическую |
|||
обработку), который |
в |
процессе |
резания подлежит |
удалению. |
Толщина этого припуска обусловлена способом получения заготовки и требованиями рабочего чертежа детали, касающимися конечной точности и чистоты поверхности. Поэтому в процессе обработки глубина резания, подача и скорость резания постоянно корректируется, то есть назначается с учетом ряда факторов, в числе которых требуемая шероховатость, физико-механические свойства обработанной поверхности, стойкость инструмента и др.
1.2.Влияние оборудования на результативность резания
Выбор режима резания в основном сводится к установлению рациональных значений главенствующих параметров резания, в числе которых, прежде всего, глубина резания, подача и скорость резания. Обоснование численных значений этих параметров проводят, опираясь на учение о резании материалов с учетом конкретных условий для резания. Дополнительное влияние на режим резания оказывают конструктивная форма заготовки, степень еѐ жесткости и уравновешенности (для случая, когда резание осуществляется с вращением заготовки). При всѐм этом установленный режим резания, ориентированный на требуемую точность и качество обработанной поверхности, должен соответствовать технологическим возможностям станка.
Вопросу о технологических возможностях металлорежущего оборудования постоянно уделяют пристальное внимание. Наблюдавшийся как в нашей стране, так и за рубежом всплеск в индустриальном развитии (в течение первых двадцати лет после Отечественной войны) во многом обусловлен бурной реконструкцией и новыми разработками в области станкостроения. Это выразилось в резком повышении производительности при резании. Общие показатели по группам станков за эти 20 лет свелись к следующему.
Токарно-расточные станки. Коренные конструктивные изменения станков сопровождались улучшением технических характеристик. Станочная система получила программное управление, повысилась точность резания, мощность привода увеличилась в 2,5 раза, диапазон допустимой скорости резания и подачи заметно сместился в сторону численного увеличения этих параметров, введена быстрая (и автоматическая) смена инструмента. В целом производительность повысилась в 3 раза
Фрезерные станки. Производительность фрезерных станков возросла в основном за счет изменения технических характеристик и введения целого ряда конструктивных усовершенствований. Увеличено количество двигателей и их мощность, расширен диапазон подач до 9,5 ÷2280 мм/мин (по сравнению с ранее имевшимся 3,175÷1020 мм/мин) и частота вращения до 16÷1600 об/мин (ранее было 18÷1300 об/мин). Скорость продольных и поперечных перемещений изменилась с 2540 до 3800 мм/мин, а вертикального - с 1900 до 2020 мм/мин. В целом производительность фрезерования повысилась на 40 %, а в отдельных случаях - на 75 %.
В числе конструктивных изменений следует отметить введение механизма выборки люфта в винтовой паре для обеспечения попутного фрезерования.
Сверлильные станки. На протяжении ряда лет не отмечается существенного сдвига в производительности мелких вертикально-сверлильных и радиально-сверлильных станков, жесткость которых повышалась в пределах, достаточных для работы сверлами из
быстрорежущих сталей. |
|
|
Несколько возросла производительность многошпиндельных сверлильных |
||
станков в |
связи с постоянным |
совершенствованием их конструкции и ростом |
мощности |
привода. Основные |
усовершенствования конструкции коснулись |
управления |
и системы смазки, введения блокировки, исключающей возможность |
работы станка при неисправностях в системе смазки или при притуплении инструмента. Повышены скорости подачи и автоматизирован
Заметный рост производительности наблюдается у сверлильных станков с револьверными головками, взявшими на себя работу, ранее выполняемую на обычных сверлильных станках с помощью кондукторов. Это привело к повышению производительности в 3÷4 раза.
Существенно повысило производительность введение программного управления. Протяжные станки. Протягивание - один из наиболее производительных
современных видов холодной обработки резанием. Скорость протягивания на современном протяжном станке порядка 90 м/мин (вместо 7,5 м/мин). Протяжные станки часто оснащают программным управлением.
Для протягивания характерна большая потеря времени на смену заготовки. Например, при обработке инструментальных пластин на станке фирмы Sundstrand (США), развивающим силу резания 100 КН (10 т) при длине хода 1675 мм, смена заготовок занимает 15 мин. Поэтому большую роль в повышении производительности занимает оснастка.
Во многих случаях различные виды холодной обработки резанием заменяют протягиванием. По данным фирмы Lapointe после внедрения протягивания время обработки сложной детали клапана было снижено с 13 часов до 15 минут. В другом случае один протяжной станок заменил 15 фрезерных. Метод протягивания успешно заменяет зуборезание (разумеется, при наличии свободного выхода инструмента из зоны резания). Например, вместо 5 минут обработки шестерни с 30-ю зубьями на зуборезном станке, тратится 20 секунд на протягивание. При этом точность поверхности зубьев, обработанных протягиванием, в ряде случаев дает возможность отказаться от шевингования.
Шлифовальные станки. Совершенствование круглошлифо-вальных станков обеспечивалось решением комплекса вопросов. В частности, разрабатывались устройства, автоматически компенсировавшие колебания размера детали из-за температурных изменений и износа абразивного круга, Это создавало условия для повышения скорости резания до 40 м/с. Попутно выполнены разработки, позволившие повысить скорость вращения керамических шлифовальных кругов.
Усовершенствована конструкция системы гидроуправления подачей и скоростью, усовершенствован механизм автоматической правки круга и введена система активного контроля обрабатываемой поверхности.
Конструкция плоскошлифовальных станков развивалась по двум направлениям:
а) разработка новых конструкций для высокоточного (прецизионного) шлифования;
б) разработка новых конструкций для грубого, но производительного обдирочного шлифования.
Станки высокоточного шлифования оснащены шкалами тонкой вертикальной и поперечной подачи (шкалы с ценой деления 1,2 мкм), беззазорной передачей в системе «винт-гайка», бесступенчатым регулированием скорости вращения круга в пределах
1200÷6000 об/мин.
Производительность станков, работающих методом врезания, повышена в основном за счет возросшей мощности привода и скорости резания, а также за счет увеличения ширины круга.
По группе внутришлифовальных станков производительность возросла преимущественно за счет автоматизации станков. Производительность заточных станков,
работающих без охлаждения, выросла благодаря введенной новой конструкции шпинделя, повышения точности перемещения стола и улучшения системы управления.
2.РЕЗАНИЕ МАТЕРИАЛОВ ТОЧЕНИЕМ
2.1.Общие положения
Точение представляет собой обработку резанием наружных и внутренних осисимметричных поверхностей геометрических тел вращения, а также плоских поверхностей, расположенных перпендикулярно к оси вращения. Реализуется точение на станках токарной группы. Принципиальная кинематическая схема точения в прямоугольной (декартовой) системе координат имеет вид, показанный на рисунке 2.1. В соответствии с этой схемой заготовка вращается относительно оси X (движение Dr), а продольную подачу осуществляют вдоль оси X (движение Ds). Сочетание этих двух движений предопределяет траекторию результирующего движения, которое совершают точки лезвия проходного резца. Движение имеет вид винтовой линии.
Точение вдоль оси X называют проходным. За каждый оборот заготовки лезвие проходного токарного резца перемещается на размер подачи S и удаляет один виток слоя материала. Толщина слоя представляет собой глубину резания t. Этот слой превращается в стружку (рисунок 2.2).
Исходя из технологических назначений, различают предварительное точение (обдирка - с целью удалить избыточный припуск, обусловленный способом получения заготовки), межоперационное формообразующее точение, чистовое формообразующее точение и окончательное (доводочное) точение.
Для перечисленных видов точения практикой машиностроения выработаны следующие ориентировочные соотношения между глубиной резания t(мм) и подачей S
(мм/об).
Предварительное точение
t 4,0 5,0 6,0 7,0 8,0 S 0,8 0,7 0,6 0,5 0,4
Межоперационное точение
t 1,0 |
1,5 |
2,0 |
3,0 4,0 |
S 0,2 |
0,25 0,3 |
0,35 0,4 |
|
Чистовое точение |
|
|
|
t 0,1 |
0,2 |
0,3 |
0,4 0,5 |
S 0,02 |
0,04 0,06 0,08 0,10 |
Окончательное (доводочное) точение t 0,06 0,07 0,08 0,09 0,10 S 0,006 0,007 0,008 0,009 0,01

Рисунок 2.1 Принципиальная кинематическая схема точения
Рисунок 2.2 Схема последовательного срезания припуска проходным токарным резцом
В каждом конкретном случае токарной обработки при выборе параметров резания следует учитывать то обстоятельство, что режущий инструмент (резец) имеет всего лишь одно главное лезвие, причем, его активная длина ограничена шириной срезаемого слоя и находится в условиях большой динамической и температурной напряженности. В свою очередь, геометрия режущей части оказывает существенное влияние как на качество обработанной поверхности (уровень шероховатости), так и на еѐ состояние (наклѐп поверхностного слоя).
Основное технологическое время t0 проходного точения составляет t0=l/n S, где l - длина обрабатываемой поверхности вдоль направления подачи S, n - частота вращения (об/мин).
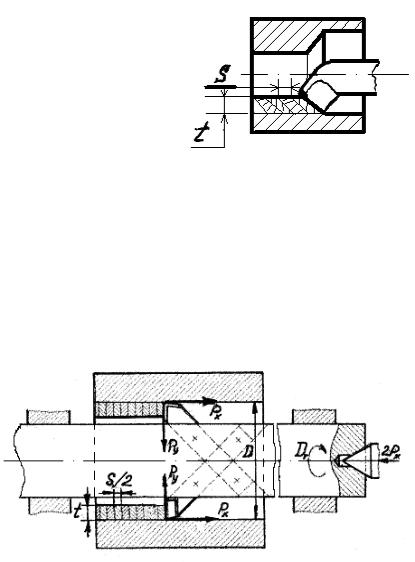
2.2. Разновидности токарной обработки
В перечень разновидностей токарной обработки входят: расточка отверстий (расточными резцами), подрезка торцовых поверхностей (подрезными резцами), отрезка обработанных деталей (отрезными резцами). Естественно, в каждом случае резцы имеют вполне конкретные конструктивные отличия.
2.2.1 Расточка отверстий. Этот вид токарной обработки внутренних поверхностей имеет ту же принципиальную кинематическую схему, что и наружное проходное точение. Из рисунка 2.3 видно, что последовательное срезание припуска представляет собой зеркальную картину проходного наружного точения.
Основные особенности внутренней расточки:
а) ограниченный обзор зоны резания (при глубоких отверстиях обзор полностью отсутствует);
б) малая жесткость расточного резца, так как размеры обрабатываемого отверстия диктуют ему уменьшенное поперечное сечение.
Рисунок 2.3 Схема удаления припуска расточным резцом
Рисунок 2.4 Схема удаления припуска расточной оправкой с двумя резцами
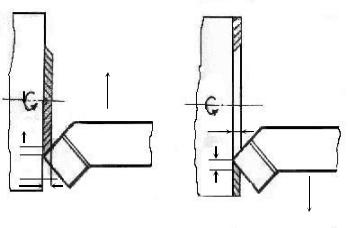
Из-за этого возникает упругое отжатие резца от обрабатываемой поверхности. В результате обработанная поверхность получает неточность в виде конусности. Чем выше твердость и механическая прочность обрабатываемого материала, тем больше упругое отжатие резца (при равных прочих условиях резания).
В ряде случаев малоразмерный резец устанавливают на более жесткой державке, которую, в свою очередь, крепят на суппорте станка. При расточке отверстий более крупных диаметров практикуют работу одновременно двумя резцами (рисунок 2.4) с диаметрально противоположным расположением зон резания. При этом опорные (установочные) поверхности резцов повернуты друг к другу. Естественно, что взаимное расположение резцов должно быть предварительно настроенным на размер диаметра растачиваемого отверстия. В результате точность резания предопределяется точностью настройки инструмента на размер.
2.2.2 Подрезка торцовых поверхностей. Торцовые поверхности в общем случае обрабатывают проходными отогнутыми резцами по схемам, показанным на рисунке 2.5. Припуск удаляют, перемещая резец как от оси вращения заготовки к периферии заготовки, так и от периферии заготовки к еѐ оси вращения, то есть главная и вспомогательная режущие кромки меняются местами в зависимости от направления главного движения в процессе резания.
При токарной обработке ступенчатых деталей возникает необходимость подрезать переходные торцовые поверхности. В ряде случаев для повышения производительности труда переходные торцы подрезают тем же проходным резцом, но с соответствующей предварительно спроектированной геометрией режущей части резца, чтобы не повредить примыкающую к торцу цилиндрическую поверхность (рисунок 2.6).
растачиваемого отверстия. В результате точность резания предопределяется точностью настройки инструмента на размер.
Dr |
|
|
DS |
Dr |
|
|
|||||
|
|
|
|
t |
|
S |
|
||||
|
S |
|
|||
t |
|
|
|||
|
|
|
|||
|
|
|
|
|
DS |
a) |
|
б) |
Рисунок 2.5 Схема обработки торца отогнутым проходным резцом при движении резца к оси (а) и от оси (б) вращения