
Учебное пособие 800232
.pdf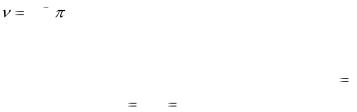
4.ФРЕЗЕРОВАНИЕ
4.1.Общие сведения о фрезеровании
Сущность процесса резания методом фрезерования состоит в том, что с обрабатываемой поверхности удаляется слой материала многолезвийным инструментом - фрезой. В соответствии со своей принципиальной конструктивной схемой фреза имеет конфигурацию цилиндра, у которого боковая поверхность оснащена зубьями с режущими лезвиями, расположенными вдоль образующей цилиндра (или по винтовой линии относительно оси цилиндра). Режущие зубья могут быть также радиально расположенными на рабочем торце цилиндра.
В процессе резания (фрезерования) реализуется сочетание двух одновременно выполняемых движений, а именно: вращательного и поступательного. Обычно вращается фреза, а поступательное движение выполняет заготовка, неподвижно закрепленная на столе, способном выполнять требуемое поступательное движение. В ряде конструкций фрезерных станков вращающуюся фрезу, установленную на блоке привода, вместе с блоком по программе (или по копиру) вдоль намеченной траектории перемещают относительно обрабатываемых поверхностей.
Режущие лезвия фрезы, взаимно расположенные на ее боковой поверхности и торце, обеспечивают эффективную обработку вертикально и горизонтально расположенных плоских поверхностей. Именно по этой причине из технологии обработки материалов резанием в своѐ время были вытеснены тихоходные строгальные работы.
После дальнейшего видоизменения и совершенствования конструкции фрез и фрезерных станков фрезерование превратилось в универсальный способ обработки резанием. В настоящее время фрезерованием обрабатывают самые разнообразные поверхности, в том числе тела вращения, резьбовые поверхности, прямые и винтовые поверхности зацепления зубчатых колѐс, шлицевые поверхности прямого и эвольвентного профиля, режут прутки и другой профильный прокат на мерные части.
4.2. Режимные параметры фрезерования
При фрезеровании ось вращения фрезы может быть расположенной вертикально (на вертикально-фрезерных станках), горизонтально (на горизонтально-фрезерных станках) или с некоторым наклоном (в зависимости от технологических возможностей фрезерного станка). Тем не менее, во всех случаях вращательное движение инструмента является главным. Поступательное движение является вспомогательным и обычно сообщается обрабатываемой заготовке.
Скорость точек наружного диаметра D фрезы является скоростью резания (фрезерования) - м/мин. Если диаметр исчисляется в миллиметрах, а частота вращения п - обороты в минуту, то
10 3 Dn ,(м/мин).
Вспомогательное движение подачи Ds , направленное перпендикулярно оси вращения фрезы, количественно задается значением подачи. При фрезеровании оно определяется величиной подачи на зуб S z , мм/зуб. Величина подачи за один оборот составляет So zSz (здесь z - число зубьев фрезы); минутная подача S мин S0 n S z zn (в мм/мин).

Значением подачи на зуб S z пользуются при теоретических исследованиях и расчете
режима резания для фрезерования. |
В производственных условиях (например, при |
||||
наладке |
фрезерных |
станков) |
пользуются |
минутной |
подачей S мин , если у |
фрезерного станка отсутствует кинематическая связь между вращающимся шпинделем и механизмом подачи, имеющим свой привод.
Режущие лезвия зубьев вращающейся фрезы за время одного оборота, как правило, находятся в контакте с обрабатываемой заготовкой только на некоторой части этого оборота, а оставшуюся часть оборота проходят, не совершая работы. Период времени, в течение которого режущие лезвия контактируют с обрабатываемой поверхностью, называется рабочим циклом, а угол поворота лезвия за время рабочего цикла - углом контакта и обозначается . Период, когда лезвие вне контакта с поверхностью,
называется холостым циклом.
Анализ принципиальных кинематических схем резания и траектории результирующего движения при резании показывает, что при неизменном направлении главного движения подачи Ds главное движение резания Dr меняет своѐ направление. Соответственно,
выработалось понятие о встречном фрезеровании, когда направление подачи и главного движения встречные, и попутном фрезеровании, когда эти направления совпадают (рисунок 4.1).
Для встречного фрезерования характерно, что нагрузка на зуб по мере резания увеличивается постепенно, так как толщина среза изменяется от нуля при входе зуба до максимума при выходе зуба из обрабатываемого материала. Параллельно с увеличением толщины срезаемого слоя возрастает величина силы, под действием которой фреза «отрывает» заготовку от стола. При недостаточной жесткости элементов конструкции, предназначенных для фиксации установочного положения обрабатываемой заготовки, возникает вибрация, ухудшающая качество обработанной поверхности (возрастает шероховатость).
При попутном фрезеровании заготовка силой резания дополнительно прижимается к столу. Но зуб фрезы начинает работать с первого момента резания с наибольшей толщиной срезаемого слоя, то есть сразу подвергается максимальной нагрузке . Тем не менее, при наличии достаточной жесткости станочной системы попутное фрезерование располагает возможностью для работы с более высокой скоростью резания (повышение производительности) при более высоком качестве обработанной поверхности.

Рисунок 4.1 Схемы встречного (а) и попутного (б) фрезерования плоскостей
Глубина фрезерования всегда измеряется в плоскости вращения фрезы, то есть в плоскости, перпендикулярной оси вращения фрезы.
Обычно глубина фрезерования при обработке одной заготовки бывает постоянной. Но при врезании и выходе фрезы, при обработке угловых переходов, обработки заготовок с неравномерным припуском на обработку глубина резания во время фрезерования может возрастать или уменьшаться.
Ширина фрезерования всегда измеряется вдоль оси фрезы (перпендикулярно глубине фрезерования).
Шероховатость обработанной поверхности предопределяется диаметром D фрезы и величиной подачи на зуб S z . Анализ геометрических построений профиля обработанной поверхности позволяет получать расчетное значение высоты шероховатости h :
h 0,5[D (D2 S z2 )].
Нагрев при фрезеровании. В процессе резания около 95 % затраченной энергии переходит в тепло, расходуемое на нагрев стружки, обрабатываемой заготовки вблизи зоны резания, лезвия инструмента и частично отводится в окружающую среду. Периодичностью смены рабочих и холостых циклов каждого из зубьев фрезы предопределено отличие тепловых явлений фрезерования от тепловых явлений, сопровождающих, например, точение, сверление, зенкерование и развертывание.
Лезвие каждого зуба фрезы в период рабочего цикла успевает нагреться до температуры около 400 °С, что почти в 2 раза ниже, чем на резцах и сверлах. В период холостого хода это тепло частично уходит в окружающую среду и в массу фрезы. Но в целом уровень этого нагрева фрезы не оказывает существенного влияния на ее стойкость. Поэтому применение смазывающе-охлаждающей жидкости (СОЖ) диктуется только видом обрабатываемого и инструментального материалов. Например, обработку стальных заготовок фрезами из быстрорежущих сталей ведут, применяя СОЖ, так как быстрорежущие стали практически не чувствительны к температурным циклическим нагрузкам. В отличие от этого обработка стальных заготовок фрезами, оснащенными режущими твердосплавными пластинками, ведется всухую, так как пластинки не

выдерживают циклической температурной нагрузки: лезвия склонны к растрескиванию и выкрашиванию.
Основное технологическое время, затрачиваемое на обработку одной заготовки, составляет
t0 (l1 l l2 ) / S мин ,
где l1 - длина пути врезания фрезы в заготовку;
l - длина обрабатываемой заготовки;
l2 - перебег фрезы в конце фрезерования.

5. РЕЗАНИЕ АБРАЗИВНЫМ ИНСТРУМЕНТОМ
5.1.Специфика резания абразивом
В перечне способов обработки материалов резанием видное место занимает обработка абразивным инструментом. Режущим элементом здесь являются абразивные зерна, обладающие очень высокой твердостью (22 - 31 кН/мм2), теплоустойчивостью и имеющие острые кромки, которые и являются режущими лезвиями.
Абразивные зерна используют:
-в виде порошка, подаваемого вдоль обрабатываемой поверхности сильной струей воздуха или воды;
-в виде мелкозернистого порошка (размером 0,02 мм и меньше), наносимого на поверхность неабразивного твердого тела (например, методом вдавливания абразива в поверхность этого твердого тела) для выполнения притирочных работ;
-в виде пасты, состоящей из 70 85 % очень мелкого абразивного порошка и 15 30 % связующего вещества, в составе которого воск, стеариновая и олеиновая кислоты и другие вещества;
-в виде смеси абразивных зерен, соединенных со связующими веществами в единое геометрическое тело определенной формы, которое после специальной силовой и термомеханической обработки представляет собой абразивный инструмент, употребляемый в виде шлифовальных кругов, сегментов, головок, брусков и шкурок.
Выступающие острые кромки абразивного материала |
(рисунок 5.1), прочно |
|
закрепленного на связке, в |
совокупности составляют набор определенным образом |
|
взаимно расположенных режущих лезвий. Этот набор |
режущих лезвий |
|
применительно, например, к шлифованию представляется |
в виде как торцевой |
рабочей поверхности шлифовального круга, так и его цилиндрической поверхности. При взаимодействии рабочей поверхности круга с обрабатываемой поверхностью заготовки режущие лезвия зерен срезают слой материала, превращая его в очень
Рисунок 5.1 Работа абразивных зерен
мелкую стружку. Большое число стружек и их малая толщина обусловливаются малыми размерами самих режущих зерен-резцов и большим количеством зерен, одновременно участвующих в резании.
Вследствие малого сечения среза и большой скорости резания обеспечивается высокая точность обработанной поверхности при очень малом уровне шероховатости. Поэтому процесс резания абразивным инструментом чаще всего является окончательной

(отделочной) операцией. В свою очередь, по результативности резания, оцениваемой достижимой точностью и качеством обработанной поверхности, а также областью предпочтительного применения, выделились такие группы операций как шлифование, хонингование, суперфиниш, притирка.
5.2.Абразивные материалы и связующие вещества
Абразивные материалы, применяющиеся в виде режущих зерен, по своему происхождению делятся на две группы: естественные и искусственные.
К естественным |
относятся |
минералы |
- алмаз, корунд и наждак. Основной |
составляющей частью |
корунда и |
наждака |
37 |
является окись алюминия (глинозем); они |
содержат также посторонние примеси, снижающие их качество, а потому в современном машиностроении почти не применяются.
К искусственным абразивам относятся электрокорунд, карбид кремния, карбид бора, боразон, искусственный алмаз (получают из обычного графита за счет воздействия на него высокими давлениями и температурой).
Электрокорунд является кристаллической окисью алюминия ( Al2O3 ), получаемой
путем электроплавки бокситов, которые состоят в основном из окиси алюминия и некоторых примесей. При плавке (температура плавки 2200 2400 °С) из бокситов выделяются примеси, а окись алюминия кристаллизуется. Электрокорунд уступает по твердости карбиду кремния, карбиду бора и алмазу.
Карбид кремния (карборунд) является химическим соединением кремния и углерода ( SiC ). Он получается из кварцевого песка при плавлении его с углеродом (коксовым порошком). По твердости уступает карбиду бора и алмазу, но при дроблении дает более острые режущие кромки.
Карбид бора (В4С) является химическим соединением бора с углеродом. По твердости приближается к алмазу, но более хрупок. Применяется для доводки поверхностей деталей из твердых сплавов, при притирочных работах, для резки драгоценных камней.
Боразон (кубический нитрид бора) - синтетический материал, по физико-механическим свойствам близкий к алмазу, но обладает большей теплостойкостью.
Связующие вещества (связки) служат для соединения |
зерен в одно целое - |
|||
абразивный |
инструмент. От |
связок |
зависит |
прочность удерживания зерна в |
абразивном |
инструменте |
и способность |
самого инструмента противостоять своему |
|
разрушению |
в процессе |
эксплуатации например, |
под действием центробежных сил |
при шлифовании инструментом в виде быстро вращающегося круга. Связки делятся на органические и неорганические.
К органическим связкам относятся вулканитовая В и бакелитовая Б.
Вулканитовая связка состоит из резины и серы (30 %). Абразивный инструмент с вулканитовой связкой обладает высокой прочностью, эластичность и не боится влаги; может иметь малую толщину (0,5 мм) при большом диаметре (до 150 мм). Шлифовальные круги на вулканитовой связке допускают большие окружные скорости (до 75 м/с) и обладают высоким полирующим действием. Производительность сдерживается быстрым засаливанием круга.

Бакелитовая связка состоит из бакелита – искусственной смолы, приготовленной из карболовой кислоты и формалина.
Абразивный инструмент на этой связке прочный и эластичный; допускает большие окружные скорости вращения, но разрушается под действием щелочной охлаждающей жидкости и поэтому нуждается в дополнительной пропитке парафином. Бакелитовая связка также теряет свою прочность при нагреве свыше 180°С.
К неорганическим связкам относятся керамическая К, магнезиальная М и силикатная С связки.
Керамическая связка приготавливается из огнеупорной глины, полевого шпата, кварца, талька, мела и жидкого стекла. Основными составляющими являются первые три вещества. Абразивный инструмент на керамической связке получил наибольшее распространение, так как эта связка огнеупорная, химически стойкая, не боится влаги, хорошо сохраняется профиль рабочей кромки.
Магнезиальная (магнезит и хлористый магний) и силикатная (смесь глины, кремневой пыли и жидкого стекла) связки дают мягкий абразивный инструмент, малопрочный, а потому применяются редко.
5.3. Особенности шлифования
Шлифование осуществляется абразивным инструментом в виде круга, который, вращаясь относительно своей оси, взаимодействует рабочей поверхностью (боковой или торцовой) с обрабатываемой поверхностью заготовки и срезает назначенный слой материала.
Схема процесса стружкообразования при шлифовании больше всего приближается к схеме резания, осуществляемого зубьями фрезы.
Несмотря на малые размеры срезаемого слоя, получаемая при шлифовании стружка имеет то же строение и вид, что и стружка, получаемая при фрезеровании. Здесь также имеют место упругое и пластическое деформирование, тепловыделение, упрочнение, износ. Но так как не все зерна одинаково участвуют в работе, то наряду с нормальной (мелкой) стружкой при шлифовании получается ещѐ и металлическая пыль, которая при возникающей высокой температуре спекается.
Высокая температура при шлифовании (порядка 1000 1500 °С) возникает из-за наличия у зерен разнообразной, неправильной геометрии режущей части (отрицательного переднего угла ) и большой скорости резания.
Температура при шлифовании повышается с увеличением износа зерен. По мере износа зерен притупляются их режущие кромки (рисунок 5.2) и возрастают силы трения притупившихся зерен с обработанной поверхностью заготовки. Это может вызывать деформацию поверхности, прижоги, структурные изменения и трещины в обработанной поверхности. Во избежание перечисленных недостатков предпринимают:
1)выбирают абразивный инструмент с такой связкой, которая оказывается неспособной удерживать на рабочей поверхности инструмента притупившееся зерно, то есть возросшие силы трения способствуют его выкрошиванию;
2)шлифование, например сталей, ведут при обильном (10-60 л/мин) охлаждении.

Рисунок 5.2 Рельеф режущей поверхности абразивного инструмента: 1 - плоскость, в которой лежат поверхности износа абразивных зерен
Смазочно-охлаждающие жидкости наряду со снижением температуры способствуют удалению абразивной и металлической пыли и очищению пор, образующихся в местах, из которых удалены притупившиеся абразивные зерна. СОЖ так-же способствует улучшению чистоты обработанной поверхности и замедляет вызываемое температурой размягчение связки.
При шлифовании сталей наибольшее распространение имеют следующие СОЖ:
1)1 %-ный раствор кальцинированной соды и 0,15 %-ный раствор нитрита натрия;
2)2 %-ный водный раствор мыльного порошка;
3)(5 7) %-ный водный раствор эмульсола
4)3,5 %-ный водный раствор нейтрального эмульсола на основе олеиновой кислоты.
При шлифовании алюминия применяют керосин или керосин с добавкой минеральных масел. Чугун и медь часто шлифуют без охлаждения, но при этом желательно наличие пылеотсосов.
Наряду с общими явлениями, присущими и другим видам обработки металлов резанием, процесс обработки абразивным инструментом (в том числе и шлифование) имеет и свои специфические особенности:
1) в отличие, например от фрезы, у шлифовального круга не сплошная, а прерывистая режущая кромка, поскольку зѐрна удалены друг от друга на некоторое расстояние;
2)абразивные зерна имеют неправильную, пирамидальную округленную в вершинах геометрическую форму и произвольно расположены в инструменте (бруске, круге), этим обусловлено непостоянное и отрицательное значение переднего угла;
3)в процессе работы шлифовальный круг может самозатачиваться, то есть под действием повышающейся силы трения на притупляющемся зерне это зерно крошится и выпадает, обнажаются новые острые зерна, которые затем продолжают резание;
4)из-за округления вершины зерна и нулевой толщины среза в момент, предшествующий срезанию (то есть при врезании), имеет место сильное скольжение - трение зерен о поверхность резания, образованную впереди идущими зернами резца; это одна из причин появляющихся прижогов при шлифовании;
5)абразивное зерно снимает стружку за очень короткий срок (0,0001 0,00005 с), практически мгновенно.
Все эти особенности делают процесс резания абразивным инструментом более сложным, чем при других видах резания, и создают большие трудности как при теоретическом, так и при экспериментальном его исследовании.
5.4.Основные приемы шлифования
Многообразие конструктивных форм создаваемых деталей при очень широком диапазоне требований, диктуемых условиями эксплуатации, предопределило требования к геометрическим формам абразивного инструмента. В свою очередь, современные станки, созданные специально для шлифовальных работ, характеризуются многообразием кинематических схем резания. Хотя сам механизм резания всегда сохраняется, особенности и специфика выбора основных режимных параметров шлифования может быть выявлена только на основе анализа вариантов обработки конкретных типовых поверхностей и элементов конструкции будущих деталей.
Наружное круглое шлифование в центрах (рисунок 5.3а) имеет три разновидности:
шлифование с продольной подачей, глубинное шлифование и шлифование с поперечной подачей (методом врезания).
При шлифовании с продольной подачей шлифовальный круг имеет два движения: вращательное - вокруг оси и поступательное - в глубину обрабатываемой заготовки (то есть поперечная подача), а заготовка имеет вращательное движение вокруг оси и поступательное движение - вдоль оси (продольная подача с целью обработки по всей длине заготовки). Поперечная подача круга на определенную величину осуществляется в конце одного продольного хода заготовки или после двойного хода (вперед-назад). Если заготовки представляют собой длинные валы, то под действием силы резания возможен их упругий прогиб. В этом случае практикуют резание по методу «выхаживания», то есть увеличивают число двойных проходов без дополнительной радиальной подачи. В период выхаживания резание идет исключительно за счет действия упругих сил, обеспечивающих силовой контакт рабочей поверхности круга с обрабатываемой поверхностью заготовки. Этим повышается точность обработанной поверхности (удаляется бочкообразность).