
Учебное пособие 1209
.pdf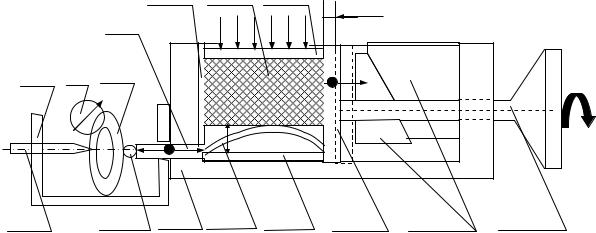
|
|
|
|
|
|
|
|
|
|
|
8 |
9 |
10 |
11 |
|
|
|
|
|
|
|
|
|
|||
12 |
14 |
7 |
|
|
|
|
|
|
|
|
|
|
f |
|
|
|
|
80 |
|
15 |
1 |
2 |
3 |
4 |
5 |
6 |
13 |
|
|||||||
|
|
|
|
|
|
Рис. 2.7 |
|
|

2.4.3. Техника испытания
Из листа в направлении прокатки вырезают 12 образцов на одноосное растяжение с расчетной длиной 80 мм и шириной 20 мм согласно международному стандарту ISO 6892-84. Образцы предварительно отжигают по режиму полного отжига.
Три образца из партии испытывают на одноосное растяжение для получения характеристик сопротивления пластическому деформированию и построения кривой течения в координатах истинное напряжение - логарифмическая пластическая деформация e. Экспериментальные кривые аппроксимируют по методике, описанной в лабораторной работе № 1, уравнением Свифта:
A(e 0 )n , |
(2.51) |
где A, 0,n- параметры аппроксимации.
Остальные образцы партии растягивают до различных степеней деформации в диапазоне от 0 до равномерной остаточной деформации e* .
Затем из рабочей части каждого растянутого образца, в которой реализуется однородное напряженное состояние, вырезают полосу размерами 160х20 мм. Каждая пластина помещается в контейнер и подвергается продольному изгибу до достижения предельной стрелы прогиба f * , превышение которой приводит к появлению пластических деформаций.
Пусть на i-м этапе нагружения длина образца в начале изгиба li-1, ход плунжера i. Обозначим высоту сечения hi , а
ширину bi. Гибкость пластины i |
удовлетворяет условию |
||||||
применимости формулы Эйлера |
|
|
|
|
|
|
|
120.5l |
|
|
|
|
|
|
|
i |
|
|
E |
(2.52) |
|||
i |
|
|
|
|
|||
hi |
|
|
e |
||||
|
|
|
|
|
|
для приближенной оценки минимального критического усилия P*, при котором изгибаемый образец теряет
81
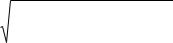
устойчивость. Через e |
в (2.52) обозначен предел |
пропорциональности сплава, |
приближенно равный 0.9 02(p) ; |
li – длина полосы после ее разглаживания в конце i-й стадии деформирования; Е – модуль Юнга материала образца.
Поскольку деформирование упругое, напряжения в поперечном сечении полосы изменяются по линейному закону.
Напряжения в сечении с прогибом f * не должны превышать предела пропорциональности. Выражая наибольшее сжимающее усилие через минимальную критическую силу, определённую решением задачи о продольном изгибе шарнирно опертой полосы, получим
f * |
2 |
l2 |
(1 2 ) |
|
|
|
e i 1 |
|
, |
(2.53) |
|
|
|
|
|||
i |
2Eh |
|
|||
|
|
|
i |
|
где - коэффициент Пуассона. Здесь и в последующем предел пропорциональности определяется приближённо с учётом эффекта Баушингера. Для сплава Д16, например, и принятых размеров полосы f * =4.5-5 мм.
Ход плунжера i определяют следующим образом. Усреднённый радиус кривизны изгибаемой полосы находится из геометрических соотношений:
r |
4f 2 |
(l |
i 1 |
|
)2 |
. |
(2.54) |
|
|
i |
|
i |
|
||||
|
|
|
|
|
||||
i |
|
|
8fi |
|
|
|
|
|
|
|
|
|
|
|
|
Используя закон Гука при изгибе и условие пропорционального упругого деформирования после подстановки в него (2.53), получим квадратное уравнение относительно i , в результате решения которого находим
|
|
l |
4( f |
*h ) |
E |
4 f *2 |
. (2.55) |
|
e(1 2) |
||||||
|
i |
i 1 |
i |
i |
i |
|
82
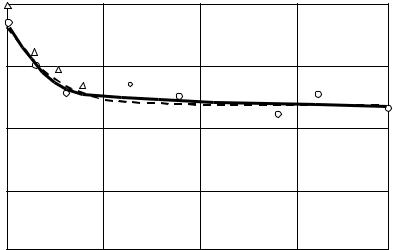
Из этого равенства следует, например, что для упругого деформирования полосы из Д16 ход плунжера на начальном этапе деформирования не должен превышать 10 мм. При дальнейшем сжатии величина хода уменьшается согласно (2.55). Во время испытаний ход плунжера контролируют по линейке, закрепленной на верхней поверхности продольной стенки контейнера (рис. 2.7).
Усилие сжатия образца Pic в процессе его прессования
резиной измеряют электронным датчиком усилия S-5000.
В результате поэтапного сжатия полосы получают начальный участок кривой течения при сжатии. Экстраполяцией этой кривой до пересечения с осью ординат по параболическому закону находят условный предел текучести при сжатии 02(c) . На рис. 2.8 приведены как экспериментальные значения параметра Баушингера, так и кривая зависимости (2.48) (штриховая).
|
|
|
|
|
0.75 |
|
|
|
|
0.5 |
|
|
|
|
0.25 |
|
|
|
|
0.0 |
6.0 |
9.0 |
e, |
% |
3.0 |
||||
|
Рис. 2.8 |
|
|
|
|
83 |
|
|
|
2.5. Лабораторная работа № 13 Определение диаграммы предельных деформаций
испытанием образцов NAKAZIMA
Цель работы. Построение экспериментальной диаграммы предельных деформаций листовых материалов.
2.5.1. Теоретическая справка
Одним из доминирующих технологических дефектов (отказов) операций листовой штамповки является потеря устойчивости в виде местных утонений, по которым затем происходит разрыв материала. Для прогнозирования потери устойчивости листовой заготовки в процессе пластического формообразования используют диаграмму предельных деформаций (ДПД).
Диаграмму строят в координатах: наибольшая главная деформация e1* в плоскости листа – параметр вида
деформированного состояния e2 /e1*, где e2 - наименьшая главная деформация в плоскости листа. На рис. 2.9 приведена типичная ДПД алюминиевого сплава Д16АМ.
Для оценки предельных возможностей заготовки при штамповке на каждом этапе формообразования определяют наибольшие главные деформации e1, e2 в плоскости листа и рассчитывают . Если точка на координатной плоскости ДПД, соответствующая деформированному состоянию заготовки, лежит ниже диаграммы, считают, что в рассматриваемый момент времени процесс ведется бездефектно.
Как видно из рис. 2.9, минимальная предельная деформация наблюдается при плоской деформации, когда e2 0, 0 . Для построения левой ветви ДПД проводят два вида испытаний: на одноосное растяжение, рассмотренное в лабораторной работе № 1, и на растяжение в условиях плоской деформации.
84
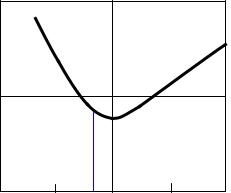
e1*,%
1
e1 e1*
e1 ,
-0.5 |
0 |
1 |
Рис. 2.9
Один из методов построения этих диаграмм основывается на комплексной методике, применяемой для построения ДПД. Методика была разработана специалистами голландской фирмы “Хуговенс груп” (Hoogovens Groep BV). Для построения диаграммы испытывают образцы с прямоугольной рабочей частью (рис. 2.10), известные в литературе как полосы Накасима (Nakazima strips).
Семь партий образцов (по пять образцов в партии) вырезают из одного листа на удалении от краев не менее 100 мм.
Пять партий образцов отличаются друг от друга шириной рабочей части h, равной соответственно 40, 70, 95, 100 и 105 мм. Образцы двух других партий изготавливают круглыми с диаметром 166 мм.
На каждый образец методом фотохимического травления наносят делительную сетку с круглыми, пересекающимися ячейками диаметром 2 3 мм (рис. 2.10). Образец укладывают на матрицу и жестко фиксируют по периметру прижимом по схеме перетяжного порога усилием в 75 кН.
85
Вытяжку образца цилиндрическим пунсоном с полусферическим наконечником диаметром 75 мм производят на прессе со скоростью 40 мм/мин (рис. 2.11). Для уменьшения трения в области контакта между пуансоном и образцом помещают две тефлоновые прокладки толщиной до 1 мм со смазанными машинным маслом поверхностями. Нагружение прекращают при появлении трещины.
Размеры деформированных ячеек измеряют на микроскопе с точностью не менее 0.001 мм с обеих сторон трещины (рис. 2.10). Измерения производят только на образцах, разрушенных в вершине. С каждой стороны трещины выбирают ближайшие к трещине целые ячейки (на рис. 2.10 они заштрихованы) в вершине образца, у которых измеряют наибольшую l1 и наименьшую l2 длины ячеек.
Наибольшую e1 и наименьшую e2 главные деформации образца в каждой ячейке, а также параметр вида деформированного состояния вычисляют с учетом кривизны поверхности по формулам:
|
|
|
|
2 R arcsin |
|
l1 |
|
|
|
|
|
|
|
|
|
|
|
|
|
|
|
|
|
||
e1 |
2 R |
|
|
|
|
|||||||
|
|
|
|
|
|
|
|
|
||||
ln[ |
|
|
|
|
]; |
|
||||||
|
l0 |
|
|
|
|
|||||||
|
|
|
|
|
|
|
|
|
|
|
|
|
|
|
|
|
|
2 R arcsin |
|
l2 |
|
|
|
|
|
|
|
|
|
|
|
|
|
|
|
|
||
|
|
|
|
|
|
|
|
|
||||
e2 |
|
|
|
|
|
|
2 R |
|
|
|
|
(2.56) |
ln[ |
|
|
|
|
|
]; |
||||||
l0 |
|
|
|
|
|
|||||||
|
|
|
|
|
|
|
|
|
|
|
|
|
|
|
e2 |
, |
|
|
|
|
|
|
|
||
|
|
|
|
|
|
|
||||||
|
|
|
|
|
|
|
||||||
|
|
e1 |
|
|
|
|
|
|
|
где R – радиус кривизны, включающий радиус пуансона и толщину образца.
86
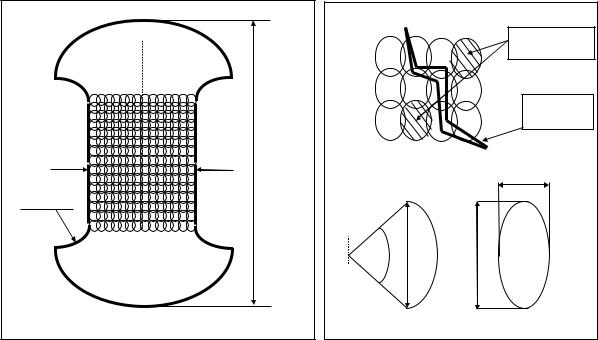
87
|
|
Измерение |
|
|
Трещина |
|
h |
l2 |
|
|
|
R20 |
|
166 |
|
R |
|
|
|
|
|
|
l1 |
|
|
l1 |
|
|
2 |
|
|
Рис. 2.10 |
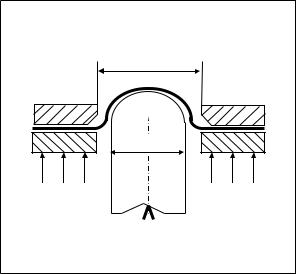
85
75
88
P
Рис. 2.11
Одну из партий круглых образцов испытывают со специальным прижимом, в котором имеется продольный паз шириной 75 мм и глубиной 1 мм со стороны контакта образца с инструментом. В паз вставляют дополнительную тефлоновую прокладку, обеспечивающую условия прижима, при которых реализуется деформированное состояние
=0,4 0,6.
На рис. 2.12 приведена ДПД углеродистой стали. Экспериментальные данные, соответствующие одной партии образцов, помечены на диаграмме одинаковыми значками. Как видно из рисунка, экспериментальные значения деформаций разрушения расположены в широком диапазоне параметра вида деформированного состояния, что позволяет описывать предельные деформационные свойства материала для большинства операций листовой штамповки: вытяжки, формовки ( =0.6 1.0), отбортовки, гибки ( = – 0.5 0.2),
обтяжки ( = – 0.4 – 0.1) и т.д.
Основным достоинствами этой методики являются в первую очередь возможность создания одинаковых условий деформирования во всей области изменения деформированного состояния материала, характерного для большинства операций листовой штамповки, а также возможность использования одного и того же оборудования.
Поскольку предельные деформации разрушения и потери устойчивости листовых материалов зависят от условий прокатки, режимов и сочетаний исходной термообработки, скорости и температуры деформации, а также от дефектов листа структурного и геометрического характера, данный вид комплексных испытаний позволяет свести к минимуму влияние этих факторов во всем диапазоне изменения и повысить тем самым стабильность построения ДПД.
89