
Kozlovski_Kobzev
.pdfются две единицы В для каждой единицы А, и F(2) означает, что требуются две единицы F
для каждой единицы С. |
|
|
|
Часть В: |
|
2 |
|
Часть С: |
|
3 |
|
Часть D: 2 х количество Вs + 2 x количество Fs = 2 х 2 + 2 х 6 = |
16 |
||
Часть Е: 3 х количество Вs + 1 x количество Сs = 3 х 2 + 1 х 3 |
= |
9 |
|
Часть F: 2 х количество Сs = |
2 х 3 = 6 |
||
Часть G: 1 x количество Fs = |
1 х 6 |
= 6 |
Пример 7.2. Расчет потребности на программу изделия. Спрос на изделие А состав-
ляет 50 единиц, что отражено в программе выпуска. Имея развернутую структуру изделия, можно определить количество штук каждой сборочной единицы, требующихся для удовлетворения потребности в заданном программой количестве изделий А:
Часть В: |
2 х количество Аs = |
(2)(50)= 100 |
Часть С: |
3 х количество Аs = |
(3)(50)= 150 |
Часть D: 2 х количество Вs + 2 x количество Fs = (2)(100)+(2)(300)= 800 |
||
Часть Е: |
3 х количество Вs + 1 x количество Сs = (3)(100)+(1)(150)= 450 |
|
Часть F: |
2 х количество Сs = |
(2)(150)= 300 |
Часть G: 1 x количество Fs = |
(1)(300)= 300 |
Пример 7.3. План полной потребности. Компания производит все элементы изделия А; время изготовления известно. Используя эту информацию, можно построить полный план потребности в материалах и расписание производства, охватывающее 50 изделий А, чтобы удовлетворить спрос в течение восьми недель, как это показано на рис.7.3 и в таблице.
План полной потребности в материалах для производства 50 изделий А
|
|
|
|
|
Недели |
|
|
|
Время |
|
|
|
1 |
2 |
3 |
4 |
5 |
6 |
7 |
8 |
изготовления |
A |
Дата потребности |
|
|
|
|
|
|
|
50 |
1 неделя |
|
Приказ на выпуск |
|
|
|
|
|
|
50 |
|
|
|
|
|
|
|
|
|
|
|
||
|
|
|
|
|
|
|
|
|
|
|
B |
Дата потребности |
|
|
|
|
|
|
100 |
|
2 недели |
|
Приказ на выпуск |
|
|
|
|
100 |
|
|
|
|
|
|
|
|
|
|
|
|
|
||
|
|
|
|
|
|
|
|
|
|
|
C |
Дата потребности |
|
|
|
|
|
|
150 |
|
1 неделя |
|
Приказ на выпуск |
|
|
|
|
|
150 |
|
|
|
|
|
|
|
|
|
|
|
|
||
|
|
|
|
|
|
|
|
|
|
|
D |
Дата потребности |
|
|
|
|
200 |
|
|
|
1 неделя |
|
Приказ на выпуск |
|
|
|
200 |
|
|
|
|
|
|
|
|
|
|
|
|
|
|
||
|
|
|
|
|
|
|
|
|
|
|
E |
Дата потребности |
|
|
|
|
300 |
150 |
|
|
2 недели |
|
Приказ на выпуск |
|
|
300 |
150 |
|
|
|
|
|
|
|
|
|
|
|
|
|
|||
|
|
|
|
|
|
|
|
|
|
|
F |
Дата потребности |
|
|
|
|
|
300 |
|
|
3 недели |
|
Приказ на выпуск |
|
|
300 |
|
|
|
|
|
|
|
|
|
|
|
|
|
|
|
||
|
|
|
|
|
|
|
|
|
|
|
D |
Дата потребности |
|
|
600 |
|
|
|
|
|
1 неделя |
|
Приказ на выпуск |
|
600 |
|
|
|
|
|
|
|
|
|
|
|
|
|
|
|
|
||
|
|
|
|
|
|
|
|
|
|
|
G |
Дата потребности |
|
|
300 |
|
|
|
|
|
2 недели |
|
Приказ на выпуск |
300 |
|
|
|
|
|
|
|
|
|
|
|
|
|
|
|
|
|
||
|
|
|
|
|
|
|
|
|
|
|
160
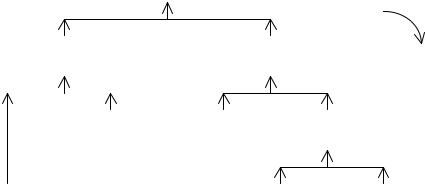
|
|
|
|
|
|
|
|
|
|
|
|
|
|
|
|
А |
|
|
|
|
|
|
|
|
|
|
|
|
|
|
|
|
|
|
|
|
|
|
|
|
|
|
|
|
|
|
|
|
|
|
|
|
|
|
|
|
|
|
|
|
|
|
|
|
|
|
|
|
|
90° |
|
||||
|
|
|
|
|
|
|
|
|
|
|
|
|
|
|
|
|
|
|
|
|
|
|
|
|
|
|
|
|
|
|
|
|
|||||
|
|
|
|
|
|
|
|
|
|
|
|
|
|
|
|
|
|
|
|
|
|
|
|
|
|
|
|
|
|
|
|
|
|
|
|
|
|
|
|
|
|
|
|
|
B |
|
|
|
|
|
|
|
|
|
|
|
|
C |
|
|
|
|
|
|
|
|
|
|
|
|
|
||||
|
|
|
|
|
|
|
|
|
|
|
|
|
|
|
|
|
|
|
|
|
|
|
|
|
|
|
|
|
|
|
|
|
|
|
|
|
|
|
|
|
|
|
|
|
|
|
|
|
|
|
|
|
|
|
|
|
|
|
|
|
|
|
|
|
|
|
|
|
|
|
|
|
|
|
|
|
|
|
|
|
|
|
|
|
|
|
|
|
|
|
|
|
|
|
|
|
|
|
|
|
|
|
|
|
|
|
|
|
|
|
|
|
|
|
|
|
|
|
|
|
|
|
|
|
E |
|
|
|
|
|
|
|
E |
|
|
|
|
F |
|
|
|
|
|
|
|
|
|||||
|
|
|
|
|
|
|
|
|
|
|
|
|
|
|
|
|
|
|
|
|
|
|
|
|
|
|
|
|
|
|
|
|
|
|
|
|
|
|
|
|
|
|
|
|
|
|
|
|
|
|
|
|
|
|
|
|
|
|
|
|
|
|
|
|
|
|
|
|
|
|
|
|
|
|
|
|
|
D |
|
|
|
|
|
|
|
|
|
|
|
|
|
|
|
|
|
|
|
G |
|
|
|
|
|
|
|
D |
|
|
|
|
|||
|
|
|
|
|
|
|
|
|
|
|
|
|
|
|
|
|
|
|
|
|
|
|
|
|
|
|
|
|
|
|
|
|
|
|
|
|
|
|
|
|
|
|
|
|
Длительность цикла частичных процессов |
|
|
|
|
|
|
|
|
||||||||||||||||||||||
|
|
|
|
|
|
|
|
|
|
|
|
|
|
|
|
|
|
|
|
|
|
|
|
|
|
|
|
|
|||||||||
|
|
Процесс |
|
|
|
|
A |
|
|
|
B |
|
C |
|
|
D |
|
E |
|
F |
|
G |
|
|
|||||||||||||
|
|
|
|
|
|
|
|
|
|
|
|
|
|
|
|
|
|
|
|
|
|
|
|
|
|
|
|
|
|
|
|
|
|
|
|
|
|
|
|
|
|
Тц, |
|
|
|
1 |
|
|
2 |
|
1 |
|
1 |
|
|
2 |
|
|
|
3 |
|
2 |
|
|
|
|
|||||||||
|
|
недель |
|
|
|
|
|
|
|
|
|
|
|
|
|
|
|
|
|||||||||||||||||||
|
|
|
|
|
|
|
|
|
|
|
|
|
|
|
|
|
|
|
|
|
|
|
|
|
|
|
|
|
|
|
|
|
|||||
|
|
|
|
Циклограмма сборки изделия и изготовления компонент |
|||||||||||||||||||||||||||||||||
|
|
|
|
|
|
|
|
|
|
|
|
|
|
|
|
|
|
|
|
|
|
|
|
|
|
|
|
|
|
|
|
|
|||||
|
|
|
|
|
|
|
|
|
|
|
|
|
|
|
|
|
|
|
|
|
|
|
|
|
|
|
|
|
|
|
Изготовление |
||||||
|
|
|
|
|
|
|
|
|
|
|
|
|
|
|
|
|
|
|
|
|
|
|
|
|
|
|
|
|
|
|
|
|
G |
||||
|
|
|
|
|
|
|
|
|
|
|
|
|
|
|
|
|
|
|
|
|
|
|
|
|
|
|
|
|
|
|
|
|
|||||
|
|
|
|
|
|
|
|
|
|
|
|
|
|
|
|
|
|
|
|
|
|
|
|
|
|
|
|
|
|
|
|
|
|||||
|
|
|
|
|
|
|
|
|
|
|
|
|
|
|
|
|
|
|
|
|
|
|
|
|
|
|
|
|
|
|
Изготовление |
||||||
|
|
|
|
|
|
|
|
|
|
|
|
|
|
|
|
|
|
|
|
|
|
|
|
|
|
|
|
|
|
|
|
|
F |
||||
|
|
|
|
|
|
|
|
|
|
|
|
|
|
|
|
|
|
|
|
|
|
|
|
|
|
|
|
|
|
|
Изготовление |
||||||
|
|
|
|
|
|
|
|
|
|
|
|
|
|
|
|
|
|
|
|
|
|
|
|
|
|
|
|
|
|
|
|||||||
|
|
|
|
|
|
|
|
|
|
|
|
|
|
|
|
|
|
|
|
|
|
|
|
|
|
|
|
|
|
|
|
|
E |
||||
|
|
|
|
|
|
|
|
|
|
|
|
|
|
|
|
|
|
|
|
|
|
|
|
|
|
|
|
|
|
|
|
|
|||||
|
|
|
|
|
|
|
|
|
|
|
|
|
|
|
|
|
|
|
|
|
|
|
|
|
|
|
|
|
|
|
Изготовление |
||||||
|
|
|
|
|
|
|
|
|
|
|
|
|
|
|
|
|
|
|
|
|
|
|
|
|
|
|
|
|
|
|
|||||||
|
|
|
|
|
|
|
|
|
|
|
|
|
|
|
|
|
|
|
|
|
|
|
|
|
|
|
|
|
|
|
|
|
D |
||||
|
|
|
|
|
|
|
|
|
|
|
|
|
|
|
|
|
|
|
|
|
|
|
|
|
|
|
|
|
|
|
|
|
|||||
|
|
|
|
|
|
|
|
|
|
|
|
|
|
|
|
|
|
|
|
|
|
|
|
|
|
|
|
|
|
|
Изготовление |
||||||
|
|
|
|
|
|
|
|
|
|
|
|
|
|
|
|
|
|
|
|
|
|
|
|
|
|
|
|
|
|
|
|||||||
|
|
|
|
|
|
|
|
|
|
|
|
|
|
|
|
|
|
|
|
|
|
|
|
|
|
|
|
|
|
|
|
|
С |
||||
|
|
|
|
|
|
|
|
|
|
|
|
|
|
|
|
|
|
|
|
|
|
|
|
|
|
|
|
|
|
|
Изготовление |
||||||
|
|
|
|
|
|
|
|
|
|
|
|
|
|
|
|
|
|
|
|
|
|
|
|
|
|
|
|
|
|
|
|||||||
|
|
|
|
|
|
|
|
|
|
|
|
|
|
|
|
|
|
|
|
|
|
|
|
|
|
|
|
|
|
|
|
|
В |
||||
|
|
|
|
|
|
|
|
|
|
|
|
|
|
|
|
|
|
|
|
|
|
|
|
|
|
|
|
|
|
|
|
Сборка |
|||||
|
|
|
|
|
|
|
|
|
|
|
|
|
|
|
|
|
|
|
|
|
|
|
|
|
|
|
|
|
|
|
|
|
А |
||||
1 |
|
2 |
|
|
3 |
|
4 |
|
5 |
|
6 |
|
7 |
|
|
8 |
|
|
|
|
|
Недели |
|
||||||||||||||
|
|
|
|
|
|
|
|
|
|
|
|
|
|
|
|
|
|
|
|
|
|
|
|
|
|
|
|
|
|
|
|
|
|
|
|
|
|
Рис.7.3. Составление графика производства изделия
Интерпретация полного плана потребности в материалах такова. Если нужно иметь 50 штук А на восьмой неделе, требуется начать узловую сборку А в начале седьмой недели. Отсюда следует, что необходимо иметь к седьмой неделе 100 штук В и 150 С. Эти два элемента требуют соответственно две и одну неделю на их изготовление. Производство В должно быть начато на пятой неделе и производство С должно быть начато на шестой неделе (время изготовления вычитается из даты потребности этих элементов). Работая в обратном направ-
161
лении, можно представить остальные компоненты для всех элементов. План потребности в материалах графически показывает, когда производство каждого элемента должно быть начато для того, чтобы иметь 50 штук А изготовленными на восьмой неделе.
Таким образом, рассмотрено покрытие полной потребности, но в предположении, что нет заделов (запасов) на руках. Многие элементы заделов на рабочих местах и складах состоят из сборочных единиц или деталей. Когда на рабочем месте имеется их запас, необходимо удовлетворять не полную, а только чистую потребность; это позволяет избежать излишних или сверхнормативных запасов. Если полная потребность в автомобилях 100 штук, и в запасе на складе готовой продукции находится 20, то чистая потребность составляет 80 (т.е. 100 - 20). Но каждый автомобиль имеет четыре колеса и один замок зажигания, в результате потребность в колесах падает на 80 колес (20 автомобилей на складе х 4 колеса) и потребность в замках зажигания падает на 20 (20 х 1).
Пример 7.4. План чистой потребности. В предыдущих примерах получены структура товара на основе ВОМ и полный план потребности. Располагая следующей информацией о запасах (заделах), можно построить план чистой потребности.
____________________________
Единица: A B C D E F G В запасе: 10 15 20 10 10 5 0
Представленная ниже карта является планом чистой потребности для изделия А. План чистой потребности включает полную потребность, запасы в заделах (на складах), чистую потребность, планируемые сроки начала изготовления и планируемые сроки окончания изготовления для каждого элемента. Конструкция плана чистой потребности является аналогичной конструкции плана полной потребности. Начинаем с А и движемся в направлении, обратном ходу изготовления изделия, рассматривая все компоненты и определяя чистую потребность для всех единиц. Чтобы сделать эти расчеты, берем из структуры товара данные о компонентах, запасах в заделах и время изготовления (в данном случае в неделях). Полная потребность изделия А равна 50 штукам к концу восьмой недели. Учитывая затем число единиц в запасе, отмечаем чистую потребность и планируемое к изготовлению количество к концу восьмой недели в размере 40 единиц в обоих случаях. Затем определяем плановые сроки изготовления заданного количества единиц, равного 40 штукам. Время общей сборки А равно одной неделе, т.е. она должна начаться на седьмой неделе. Рассматривая график и структуру изделия, можем увидеть, что требуются 8 (2 х 40) единиц В и 120 (3 х 40) единиц С в конце седьмой недели, чтобы в итоге получить 50 единиц А в конце восьмой недели. Индекс А справа от большой цифры у единиц В и С указывает, что эти объемы необходимы, чтобы удовлетворить потребность в производстве родителя А. Аналогично продолжая анализ, узнаем чистую потребность для D, E, F, G. Обратим внимание на задел для позиции Е на шестой неделе. Он равен нулю, потому что запас (10 штук) был использован, чтобы изготовить В в колонке 5. Точно такие же рассуждения справедливы и для запаса D, который был израсходован, чтобы изготовить F.
162

Полный план чистой потребности в материалах для производства 50 изделий А
Еди- |
Нижний уровень |
Время изго- |
Показатели |
|
|
|
Недели |
|
|
|
|
ница |
входимости |
товления, нед. |
планирования |
1 |
2 |
3 |
4 |
5 |
6 |
7 |
8 |
А |
0 |
1 |
Полная потребность |
|
|
|
|
|
|
|
50 |
|
|
|
Ожидаемое получение от- |
|
|
|
|
|
|
|
|
|
|
|
крытых ранее заказов |
|
|
|
|
|
|
|
|
|
|
|
Текущий запас |
10 |
10 |
10 |
10 |
10 |
10 |
10 |
0 |
|
|
|
Чистая потребность |
|
|
|
|
|
|
|
40 |
|
|
|
Планируемое получение |
|
|
|
|
|
|
|
|
|
|
|
заказываемой партии |
|
|
|
|
|
|
|
40 |
|
|
|
Планируемое открытие |
|
|
|
|
|
|
|
|
|
|
|
нового заказа партии |
|
|
|
|
|
|
40 |
|
В |
1 |
2 |
Полная потребность |
|
|
|
|
|
|
80А |
|
|
|
|
Ожидаемое получение от- |
|
|
|
|
|
|
|
|
|
|
|
крытых ранее заказов |
|
|
|
|
|
|
|
|
|
|
|
Текущий запас |
15 |
15 |
15 |
15 |
15 |
15 |
0 |
0 |
|
|
|
Чистая потребность |
|
|
|
|
|
|
65 |
|
|
|
|
Планируемое получение |
|
|
|
|
|
|
|
|
|
|
|
заказываемой партии Пла- |
|
|
|
|
|
|
65 |
|
|
|
|
нируемое открытие нового |
|
|
|
|
|
|
|
|
|
|
|
заказа партии |
|
|
|
|
65 |
|
|
|
С |
1 |
1 |
Полная потребность |
|
|
|
|
|
|
120А |
|
|
|
|
Ожидаемое получение от- |
|
|
|
|
|
|
|
|
|
|
|
крытых ранее заказов |
|
|
|
|
|
|
|
|
|
|
|
Текущий запас |
20 |
20 |
20 |
20 |
20 |
20 |
0 |
0 |
|
|
|
Чистая потребность |
|
|
|
|
|
|
100 |
|
|
|
|
Планируемое получение |
|
|
|
|
|
|
|
|
|
|
|
заказываемой партии Пла- |
|
|
|
|
|
|
100 |
|
|
|
|
нируемое открытие нового |
|
|
|
|
|
|
|
|
|
|
|
заказа партии |
|
|
|
|
|
100 |
|
|
Е |
2 |
2 |
Полная потребность |
|
|
|
|
195В |
100С |
|
|
|
|
|
Ожидаемое получение от- |
|
|
|
|
|
|
|
|
|
|
|
крытых ранее заказов |
|
|
|
|
|
|
|
|
163
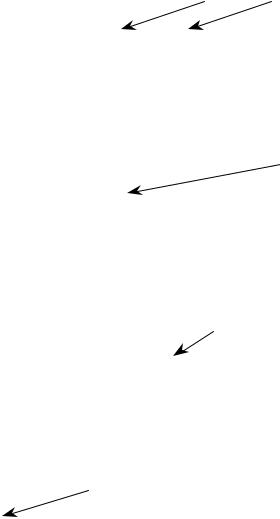
|
|
|
Текущий запас |
10 |
10 |
10 |
10 |
15 |
115 |
115 |
115 |
|
|
|
Чистая потребность |
|
|
|
|
185 |
85 |
|
|
|
|
|
Планируемое получение |
|
|
|
|
|
|
|
|
|
|
|
заказываемой партии Пла- |
|
|
|
|
200 |
200 |
|
|
|
|
|
нируемое открытие нового |
|
|
|
|
|
|
|
|
|
|
|
заказа партии |
|
|
200 |
200 |
|
|
|
|
F |
2 |
3 |
Полная потребность |
|
|
|
|
|
200С |
|
|
|
|
|
Ожидаемое получение от- |
|
|
|
|
|
|
|
|
|
|
|
крытых ранее заказов |
|
5 |
|
|
|
|
|
|
|
|
|
Текущий запас |
0 |
5 |
5 |
5 |
5 |
0 |
0 |
0 |
|
|
|
Чистая потребность |
|
|
|
|
|
195 |
|
|
|
|
|
Планируемое получение |
|
|
|
|
|
|
|
|
|
|
|
заказываемой партии Пла- |
|
|
|
|
|
195 |
|
|
|
|
|
нируемое открытие нового |
|
|
|
|
|
|
|
|
|
|
|
заказа партии |
|
|
195 |
|
|
|
|
|
D |
3 |
1 |
Полная потребность |
|
|
390F |
|
130В |
|
|
|
|
|
|
Ожидаемое получение от- |
|
|
|
|
|
|
|
|
|
|
|
крытых ранее заказов |
|
|
|
|
|
|
|
|
|
|
|
Текущий запас |
400 |
400 |
10 |
10 |
0 |
0 |
0 |
0 |
|
|
|
Чистая потребность |
|
|
0 |
|
120 |
|
|
|
|
|
|
Планируемое получение |
|
|
|
|
|
|
|
|
|
|
|
заказываемой партии Пла- |
|
|
|
|
120 |
|
|
|
|
|
|
нируемое открытие нового |
|
|
|
|
|
|
|
|
|
|
|
заказа партии |
|
|
|
120 |
|
|
|
|
G |
3 |
2 |
Полная потребность |
|
|
195F |
|
|
|
|
|
|
|
|
Ожидаемое получение от- |
|
|
|
|
|
|
|
|
|
|
|
крытых ранее заказов |
|
|
|
|
|
|
|
|
|
|
|
Текущий запас |
0 |
0 |
0 |
0 |
0 |
0 |
0 |
0 |
|
|
|
Чистая потребность |
|
|
195 |
|
|
|
|
|
|
|
|
Планируемое получение |
|
|
|
|
|
|
|
|
|
|
|
заказываемой партии Пла- |
|
|
195 |
|
|
|
|
|
|
|
|
нируемое открытие нового |
|
|
|
|
|
|
|
|
|
|
|
заказа партии |
195 |
|
|
|
|
|
|
|
164
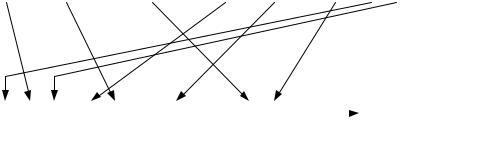
Пример 7.5. Сводный график производства. В предыдущих примерах рассматривалось изготовление изделия только одного наименования; 50 штук А требовались к концу восьмой недели. Обычно же в течение этого времени существует спрос на изделия многих наименований; для каждого из них нужно подготовить график производства. Составляя расписание производства каждого отдельного изделия в общем производственном плане-графике, в конечном итоге составляют план чистой потребности в материалах. Расписание производства нескольких изделий, входящих в один производственный план-график и соответственно единый план потребности в материалах для их производства, показано ниже.
|
A |
|
S |
___________|____________ |
|
___________|_________ |
|
| |
| |
| |
| |
B |
C |
B |
C |
Время изготовления = 4 для А |
Время изготовления = 6 для S |
Несколько расписаний входят в полный график потребности в В: одно В в каждом А и одно В в каждом S; кроме того, как запчасти 10 В продаются в первую неделю, еще 10 продаются во вторую неделю. Большинство систем запасов записывают количество штук в запасе, которые предписываются для специального использования в производстве будущего, но сейчас не используются. Такие единицы часто рассматриваются как зарезервированные единицы. Зарезервированные единицы могут затем быть включены в планирование MRP и представлены на листе расписаний.
|
План-график для А |
|
|
|
План-график для S |
|
План-график для В |
||||||||||||
|
|
|
|
|
|
|
|
|
|
|
|
|
|
|
(прямые продажи) |
||||
Периоды |
|
|
|
|
|
|
|
|
|
|
|
|
|
|
|
|
|
|
|
5 |
6 |
7 |
8 |
9 |
10 |
11 |
8 |
9 |
10 |
11 |
12 |
13 |
1 |
2 |
3 |
||||
|
|
40 |
|
50 |
|
|
15 |
|
|
40 |
|
20 |
|
30 |
|
10 |
10 |
|
|
Периоды |
1 |
2 |
3 |
4 |
5 |
6 |
7 |
8 |
|
|
Следовательно, |
|
|
|
это полная по- |
||||||||||
|
|
10 |
50 |
40 |
50 |
20 |
|
45 |
|
|
|
|
|
|
|
|
|
|
требность |
||||||
|
|
|
|
|
|
|
|
|
|
для В
7.4. Размер партии поставки
Целью систем MRP является производство такого числа единиц, которое необходимо для удовлетворения потребностей без хранения на складе. Такая система организации опирается на небольшие объемы, частые заказы, небольшие уровни заделов (по принципу “точно в срок” - JIT) и зависимый спрос. Однако в тех случаях, когда затраты переналадки значительны, или когда условия производства не позволяют применить JIT, возникает объемноразмерная задача: определить оптимальный размер партии. Многие коммерчески доступные системы MRP включают набор большого числа методов определения размеров партий. Рассмотрим основные из них.
165
1) Партия за партией. Рассматриваемое объемно-размерное решение использует технику последовательного запуска партии за партией, размер которых принимается равным текущей потребности. Затраты хранения запасов равны нулю, но последовательность отдельных переналадок приводит к образованию суммарных затрат, равных затратам переналадки.
Пример 7.6. Партия за партией. Компания ставит задачу рассчитать для одного из выпускаемых изделий затраты на заказы и текущие запасы при использовании техники “партия за партией”. Компания определила, что для 1 изделия затраты переналадки составляют $100, на заделы тратится $1 за период. Производственный график, отражающий чистую потребность в изделиях, представлен ниже.
Техника: партия за партией
Недели |
1 |
2 |
3 |
4 |
5 |
6 |
7 |
8 |
9 |
10 |
Полная потребность |
35 |
30 |
40 |
0 |
10 |
40 |
30 |
0 |
30 |
55 |
График прихода |
|
|
|
|
|
|
|
|
|
|
Планируемый задел 35 |
35 |
0 |
0 |
0 |
0 |
0 |
0 |
0 |
0 |
0 |
Чистая потребность |
0 |
30 |
40 |
0 |
10 |
40 |
30 |
0 |
30 |
55 |
Плановые сроки окончания |
|
30 |
40 |
|
10 |
40 |
30 |
|
30 |
55 |
Плановые сроки начала |
30 |
40 |
|
10 |
40 |
30 |
|
30 |
55 |
|
|
|
|
|
|
|
|
|
|
|
|
Затраты хранения: $1 на штуку в неделю; затраты переналадки: $100; полная потребность в неделю: 27; время изготовления: 1 неделя.
Рассматриваемое объемно-размерное решение использует технику партия за партией. Затраты хранения запасов равны нулю, но семь отдельных переналадок представляют суммарные затраты, равные $700.
2)Размер экономичного заказа. Модель EOQ, рассмотренная ранее, может использоваться в объемно-размерной технике, как правило, там, где существует относительно постоянный независимый спрос, который не требует изучения. В процедуре же MRP исходят из предположения, что существует зависимый спрос. Можно использовать информацию о зависимом спросе и не предполагать, что спрос постоянен. EOQ-формула усредняет спрос на протяжении рассматриваемого периода. EOQмодель:
Q* = sqr (2DS/H),
где D - годовое использование; S - затраты переналадки; Н - текущие затраты хранения на годовой базе за единицу.
Количество переналадок за год определяется как отношение годового объема к Q*. Затраты на все переналадки представляют произведение S и количества переналадок за год. Затраты хранения = Q* /2 x (H x количество недель в году). Общие затраты = затраты переналадки + затраты хранения. Затраты за плановое число недель = общие затраты x (плановое число недель/ число недель в году).
Расчетные затраты хранения будут отличаться от действительных, зависящих от скорости действительного использования. Поскольку использование, как правило, не бывает постоянным, действительные затраты будут фактически больше рассчитанных на базе EOQ. Если произойдет любое уменьшение запасов, например, продажа готовых изделий, то возникающие при этом затраты необходимо будет добавить к рассчитанному EOQ.
166
Пример 7.7. Размер экономичного заказа. Компания, имеющая затраты переналадки $100 и недельные затраты хранения $1, анализирует свои общие затраты при использовании техники определения размера партии EOQ. Чистая потребность и размеры обрабатываемых партий подчиняются тем же требованиям, что и в предыдущем примере.
Техника EOQ
Недели |
1 |
2 |
3 |
4 |
5 |
6 |
7 |
8 |
9 |
10 |
Полная потребность |
35 |
30 |
40 |
0 |
10 |
40 |
30 |
0 |
30 |
55 |
График прихода |
|
|
|
|
|
|
|
|
|
|
Задел 35 |
35 |
0 |
43 |
3 |
3 |
66 |
26 |
69 |
69 |
39 |
Чистая потребность |
0 |
30 |
0 |
0 |
7 |
26 |
4 |
0 |
0 |
16 |
Плановые сроки окончания |
|
73 |
|
|
73 |
|
73 |
|
|
73 |
Плановые сроки начала |
73 |
|
|
73 |
|
73 |
|
|
73 |
|
|
|
|
|
|
|
|
|
|
|
|
Затраты хранения: $1 штука/неделя; затраты переналадки: $100; полная средняя потребность в неделю: 27; время изготовления: 1 неделя.
Десятинедельное использование равно 270 штукам, поэтому недельное использование равно 27 штукам и 52-недельное (годовое) использование - 1,404 штукам.
EOQ-модель: Q* = sqr (2DS/H),
где D - годовое использование, D = 1,404; S - затраты переналадки, S = $100; Н - текущие затраты хранения на годовой базе за единицу, Н=$1 x 52 недели=$52; Q* = 73 штуки.
Количество переналадок: 1,404 /73 = 19 за год. Затраты на все переналадки: 19 х $100= $1,900. Затраты хранения: 73/2 x ($1 x 52 недели) = $1,898.
Затраты переналадки + Затраты хранения: $ 1,900 + 1,898 = $3,798.
EOQ-решение позволяет рассчитать затраты на десять недель: $ 3,789 x (10 недель/52
недели) = $730.
Действительные затраты хранения компании будут отличаться от рассчитанных $730, зависящих от скорости действительного использования. Из таблицы выше можно видеть, что в 10-недельном примере реальные затраты равны $400 на переналадки плюс затраты на текущее хранение 375 штук по $1 за неделю, равные $775. Поскольку использование не было постоянным, действительные рассчитанные затраты были фактически больше рассчитанных теоретических на базе EOQ ($730), и больше, чем по правилу партия за партией ($700). Если случится любое уменьшение запасов, например, продажа готовых изделий, то возникающие при этом затраты необходимо будет добавить к рассчитанному EOQ, равному $775.
3) Последовательное балансирование по отдельным периодам (РРВ). Представляет бо-
лее динамичный подход к выравниванию затрат переналадки и хранения. РРВ использует дополнительную информацию, чтобы изменить размер партии на основе данных о спросе стараясь сбалансировать затраты переналадки. Последовательное балансирование по отдельным периодам использует представления об отдельном экономичном периоде (ЕРР), который измеряется отношением затрат переналадки к затратам хранения. Для примера, при S = 100 д.е. и H = 1 д.е. ЕРР = 100/1 = 100 штук. Поэтому хранение 100 штук изделий в течение одного периода потребует затрат 100 д.е., что точно соответствует затратам одной пере-
167

наладки. Аналогично, хранение 50 штук в течение двух периодов также потребует затрат 100 д.е. (2 периода х 1 д.е. x 50 штук). РРВ, следуя этой логике, будет стремиться к некоторому увеличению потребности так, чтобы число отдельных периодов аппроксимировало ЕРР, в данном случае - в пределах 100 штук.
Пример 7.8. Последовательное балансирование по отдельным периодам (РРВ). Ком-
пания ведет расчет затрат, связанных с размером партии, исходя из затрат переналадки $100 и затрат хранения $1. Используется техника последовательного балансирования по отдельным периодам. Исходные данные сведены в таблицу.
Калькулирование по методу РРВ
Объеди- |
Оцениваемый объем |
|
Затраты |
|
|
нение пе- |
(совокупная чистая |
Частичные периоды |
на |
на |
сумма |
риодов |
потребность) |
|
переналадку |
хранение |
|
|
|
|
|
|
|
2 |
30 |
0 |
100 |
70 |
170 |
2,3 |
70 |
40=40*1 |
|
|
|
2,3,4 |
70 |
40 |
|
|
|
2,3,4,5 |
80 |
70=40*1+10*3 |
|
|
|
2,3,4,5,6 |
120 |
230=40*1+10*3+40*4 |
|
|
|
|
|
|
|
|
|
Объединяются периоды от 2 до 5; 70 ближе всего к ЕРР, равному 100, что является целью
6 |
40 |
0 |
100 |
120 |
220 |
6,7 |
70 |
30 |
|
|
|
6,7,8 |
70 |
30 |
|
|
|
6,7,8,9 |
100 |
120=30*1+30*3 |
|
|
|
|
|
|
|
|
|
Объединяются периоды от 6 до 9; 120 ближе всего к ЕРР равному 100, что является целью
10 |
|
55 |
|
0 |
|
|
|
10 |
|
|
0 |
|
100 |
|||
|
|
|
|
|
|
|
|
300+190=490 |
|
|
|
|
|
|||
|
|
|
|
|
|
|
|
|
|
|
|
|
|
|
|
|
|
|
|
|
|
РРВ-техника |
|
|
|
|
|
|
|
|
|
||
|
|
|
|
|
|
|
|
|
|
|
|
|
|
|
|
|
|
Наименование |
|
|
|
|
|
Недели |
|
|
|
|
|
|
|||
|
1 |
|
2 |
3 |
4 |
5 |
6 |
7 |
|
8 |
9 |
|
10 |
|||
|
|
|
|
|
|
|||||||||||
|
|
|
|
|
|
|
|
|
|
|
|
|
|
|||
Полная потребность |
35 |
|
30 |
40 |
0 |
10 |
40 |
30 |
|
0 |
30 |
|
55 |
|||
График прихода |
|
|
|
|
|
|
|
|
|
|
|
|
|
|
||
Планируемый задел 35 |
35 |
|
0 |
50 |
10 |
10 |
0 |
60 |
|
30 |
30 |
|
0 |
|||
Чистая потребность |
0 |
|
30 |
0 |
0 |
0 |
40 |
0 |
|
0 |
0 |
|
55 |
|||
Плановые сроки окончания |
|
|
80 |
|
|
|
|
100 |
|
|
|
|
|
55 |
||
Плановые сроки начала |
80 |
|
|
|
|
|
|
|
|
|
|
55 |
|
|
||
|
|
|
|
|
|
|
|
|
|
|
|
|
|
|
|
|
Затраты хранения: $1 на штуку в неделю; затраты переналадки: $100; средняя за неделю полная потребность: 27; время изготовления: 1 неделя.
ЕРР составляет 100 (затраты переналадки делятся на затраты хранения: $100 / $1). Первая партия покрывает периоды первый, второй, третий, четвертый, пятый и равна 80. Суммарные затраты составляют $490 и включают суммарные затраты переналадки $300, суммарные затраты хранения $190.
168
4) Алгоритм Вагнера-Витина. Данная процедура является моделью динамического программирования, которая повышает точность, а, следовательно, и сложность размернообъемных расчетов. Она предполагает наличие временного горизонта, за которым отсутствует дополнительная чистая потребность. Эта техника запатентована и часто используется на практике. Реализована в виде программного продукта для коммерческого использования. В связи с этим анализ ее методического обеспечения затруднен.
Результаты сравнительного анализа не позволяют сделать однозначного вывода относительно предпочтительной размерно-объемной техники. В трех примерах по размернообъемным расчетам получены следующие значения затрат:
партия за партией |
$700; |
ЕОQ |
$775; |
последовательное |
|
балансирование по периодам |
$490. |
Однако на основании этих результатов не нужно делать поспешных выводов о предпочтительности размерно-объемной техники РРВ. Во-первых, затраты могут измениться вследствие изменения расписания потребности, и могут вести себя не совсем так, как в примерах. Во-вторых, в соответствии с требованиями теории новый размер партии должен пересчитываться с каждым изменением, возникающим в иерархии MRP; на практике это ведет к нестабильности в порядке, устанавливаемом расписанием, и потому нежелательно. Окончательный вывод: все рассчитываемые любым методом размеры партий лишь в какой-то степени отражают реальное положение дел, поскольку реальная система не в состоянии реагировать на частые изменения, которые только вносят “нервозность” в процесс ее функционирования.
Обычно использование метода партия за партией рассматривается как техника, обеспечивающая наиболее приемлемые результаты. Размер партии может быть изменен так, как это необходимо в соответствии с множеством различных ограничений, в т.ч. определяемых условиями протекания процессов (например, термические процессы могут потребовать вполне определенных размеров партий, загружаемых одновременно в печь или размер контейнеров определяет размер загружаемой в них партии материалов).
Однако необходимо проявлять осторожность и предварительно тщательно проверять любое намечаемое изменение размера партии, т.к. это может нарушить тот минимально необходимый уровень хранимых запасов, на котором строится вся иерархия в системе MRP. Там, где затраты переналадки значительны и спрос более или менее постоянен, последовательное балансирование по периодам (РРВ), алгоритм Вагнера-Витина или EOQ-техника обеспечивают удовлетворительные результаты. Правильный размер партии может быть установлен лишь в случае, если он базируется на действительных данных о затратах и представлен в терминах потребности.
Вопросы для самопроверки
1.Каковы содержание и задачи планирования потребностей/ ресурсов (RP)?
2.Как взаимосвязаны планирование поставок и планирование запасов?
3.Какие исходные данные требуются для планирования потребностей?
169