
диафрагмированные волноводные фильтры / a5d44d37-3ab0-4f13-9e03-dc786e96dd82
.pdf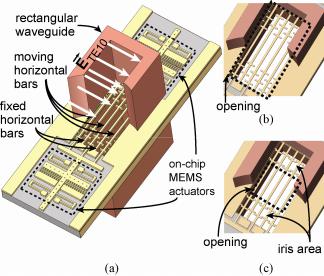
MEMS-RECONFIGURABLE WAVGUIDE IRIS FOR SWITCHABLE V-BAND CAVITY RESONATORS
Zargham Baghchehsaraei and Joachim Oberhammer
Micro and Nanosystems, KTH Royal Institute of Technology, Stockholm, Sweden
ABSTRACT
This paper presents for the first time a novel MEMSreconfigurable inductive iris based on a 30-µm thick reconfigurable transmissive surface and reports on its application to create a switchable cavity resonator in a WR12 rectangular waveguide (60-90 GHz). The reconfigurable surface incorporates 252 simultaneously switched contact points for activating (ON state) and deactivating (OFF state) the inductive iris by a 24 µm lateral displacement of two sets of distributed vertical cantilevers. In the ON state, these contact points are short-circuiting the electric field lines of the TE waveguide mode on the cross-sectional areas of a symmetric inductive waveguide iris, and are not interfering with the wave propagation in the OFF state. Thus, this novel concept allows for completely switching the inductive iris ON or OFF. The inductive iris has an insertion loss of better than 1.0 dB in the OFF state, of which 0.8 dB is attributed to the measurement setup alone. In the ON state the measured performance of the switchable iris is in good agreement with the simulation results. Furthermore, a novel, switchable cavity resonator was implemented based on such a MEMSreconfigurable iris, and was characterized to a Q-factor of 186.13 at the resonance frequency of 68.87 GHz with the iris switched ON, and an OFF-state insertion loss of less than 2 dB (including the measurement setup) without any resonance, which is for the first time reported in this paper.
INTRODUCTION
Cavity resonator filters are of interest for millimeterwave frequencies but also for lower frequencies when low insertion loss and high power handling capability are important. With the increasing complexity of wireless technology there is a desire to implement tunable/switchable components for frequency-agile and multi-frequency systems. The resonance frequency of a waveguide cavity is commonly tuned manually by using a screw, or by using either piezoelectric [1] or electrostatic radio frequency microelectromechanical systems (RF MEMS) actuators [2]. Resonators based on piezoelectric tuning mechanism are large and slow, while electrostatic RF MEMS actuators benefit from near-ideal signal handling behavior, ultra-low power consumption, faster tuning speed, and high Q-factor [3,4].
In this paper, we present a switchable inductive iris based on a MEMS-reconfigurable transmissive surface. The transmissive surface is integrated into a WR-12 rectangular waveguide (60-90 GHz, inner dimensions 3.1 mm × 1.55 mm) and can be switched between its activated (ON) state and deactivated (OFF) state by on-chip MEMS electrostatic comb-drive actuators. Previous attempts of MEMSreconfigurable waveguide elements only provide limited
tuning functionality [5,6], but the novel concept presented here allows for completely switching ON and OFF the irises and thus enables new possibilities for MEMSreconfigurable waveguide devices, such as resonators/filters which can be switched ON and OFF, as demonstrated by the very first results in this paper.
Figure 1: Simplified schematic view of presented MEMSreconfigurable inductive iris: (a) chip with reconfigurable iris surface and on-chip actuators integrated into a rectangular waveguide; (b) iris surface in the deactivated/OFF state; (c) iris surface in the activated/ON state.
CONCEPT
A simplified schematic view of the micromachined chip with the integrated MEMS-reconfigurable inductive-iris surface, inserted into the WR-12 waveguide cross-section, is shown in Figure 1. The MEMS-reconfigurable surface, placed perpendicularly to the wave propagation, consists of distributed fully-metallized vertical cantilever sections, similar to a MEMS waveguide switch recently presented by the authors [7]. The distributed vertical cantilevers are placed on the two areas of a conventional, fixed waveguide iris. Furthermore, the cantilever sections are grouped into movable and fixed cantilevers and mechanically suspended through horizontal suspension bars which are transparent to the wave propagation. In the deactivate-iris state, the movable set and the fixed set of vertical cantilever sections are not in contact with each other and the reconfigurable surface is totally transmissive allowing the electromagnetic wave of the TE mode (dominant rectangular waveguide mode) to propagate freely through the surface
978-1-4799-3509-3/14/$31.00 ©2014 IEEE |
206 |
MEMS 2014, San Francisco, CA, USA, January 26 - 30, 2014 |

(see Figure 1(b)). On-chip electrostatic comb-drive MEMS actuators, which are placed outside the narrow (E-plane) walls of the waveguide to avoid any disturbance of the wave propagation, can displace the movable set of vertical cantilevers laterally via the movable set of horizontal bars to bring them in contact with the fixed set to activate the iris (switched ON). As a result, the wave propagation will be partially blocked due to short-circuiting of the electric field lines of TE mode by vertical cantilevers in this configuration (see Figure 1(c)). The placement of vertical cantilevers toward the narrow wall of the waveguide results in localized short-circuiting of the field in that region similar to a symmetric inductive iris. Therefore, utilization of this novel reconfigurable iris in switchable waveguide components provides the possibility of completely deactivating (OFF state) or activating (ON state) the component.
Figure 3 shows a scanning electron microscope (SEM) image of the reconfigurable surface of a chip. The vertical cantilevers have 5 μm width with 5 μm overlap between the movable and the fixed pair. The horizontal suspension bar has 25 μm thickness. The gap between the edge of the movable cantilever (longer cantilevers) and the horizontal bar is 5 μm.
FABRICATION
An overview of the two-mask micromachining fabrication flow of the chips is shown in Figure 2. The process starts with an silicon-on-insulator (SOI) wafer with device layer thickness of 30 µm, buried oxide (BOX) layer thickness of 2 µm and handle wafer thickness of 500 µm. Bosch deep reactive ion etching (DRIE) technique was used to etch the backside of the chip with a pocket as large as the waveguide inner dimensions to have only the device layer interacting with the wave propagation. Then, the MEMS structure is patterned on the device layer by DRIE. Afterwards, the moving elements of the MEMS structure were release-etched in hydrofluoric acid. Finally, 50-nm layer of titanium tungsten adhesion layer and 1-µm layer of gold is deposited on both sides of the chip by sputtering. The skin depth is 290 nm at 60 GHz and this metallization step (with the thickness equal to more than three time the skin depth) eliminates the metal losses due to skin depth. Furthermore, complete metallization of the chip eliminates any requirement of using a high resistivity SOI wafer to lower the substrate loss, thus an SOI wafer with resistivity of 1-20 Ω-cm is used here.
Figure 2: Two-mask fabrication flow of the MEMSreconfigurable iris chips: (a) SOI wafer; (b) Deep reactive ion etching of the handle wafer followed by the device layer;
(c)Release etching of the device layer in hydrofluoric acid;
(d)Double side gold sputtering.
Figure 3: SEM image of the MEMS-reconfigurable surface of a switchable inductive iris.
ON-CHIP MEMS ACTUATORS
The on-chip electrostatic MEMS actuator is designed as a standard push-pull comb-drive actuator with folded-beam springs with the dimensions shown in Figure 4.
Figure 4: Dimensions of on-chip electrostatic comb-drive MEMS actuators.
The 24-μm displacement of the reconfigurable surface is achieved by engaging four comb-drive actuators for 12 μm active pushing or active pulling in opposite directions around the central rest position. The actuator shown in Figure 4, with 106 fingers on each actuator and with spring
207

constant of 1.97 N/m, is mirrored along the E-plane and H- plane of the waveguide resulting in total eight comb-drive actuators. The average actuation voltage for full displacement in one direction was measured to 40.0 V with a reproducibility of 0.1 V.
As all structural elements are fabricated by bulk micromachining in silicon, all moving parts have a monocrystalline silicon core which is metal-cladded for RF purpose. Furthermore, the design comprises an all-metal design, i.e. no dielectric isolation layers are used which could be prone to reliability impact.
dummy chip with an ideal reference iris with completely filled metal areas. The measurements fit the simulations very well except for a higher insertion loss of 0.4-1.0 dB in the deactivated-iris (OFF) state, of which the majority of 0.3-0.8 dB is attributed to the flange assembly of the measurement setup, which could be demonstrated by the measurement of a reference chip. The reference chip is fabricated in the same process flow as the MEMSreconfigurable chips but contains no MEMS elements; its device layer and handle wafer is etched through completely with pockets as large as the waveguide inner dimensions.
MEASUREMENT SETUP AND RESULTS
Reconfigurable inductive iris
The MEMS-reconfigurable chip is integrated into a WR-12 (60-90 GHz, inner dimensions 3.1 mm × 1.55 mm) rectangular waveguide by placing it in a recess of tailormade waveguide flanges and by applying conductive polymer interposers between the top surface of the chip and wide walls of the waveguide [8]. The compliant conductive polymer layer, with a nominal resistivity of 8 mΩ-cm, avoids any discontinuity in the surface currents on the wide walls of the waveguide by filling the gap between the waveguide and the chip. The conductive polymer is only applied on the wide waveguide walls (H-plane) to allow the mechanical feed-throughs (horizontal suspension bars of the moving cantilevers) to be connected to on-chip MEMS actuators through the narrow walls (E-plane). The narrow walls are nearly current-free so that the mechanical feedthroughs are not disturbing the RF performance [8]. A schematic cross-section of the integration is shown in Figure 5.
Figure 5: Cross-sectional view of integration of a chip with a MEMS-reconfigurable iris into WR-12 rectangular waveguide.
The results for measured performance and HFSS simulation of a reconfigurable inductive iris are shown in Figure 6. The reconfigurable surface of the iris, consisting of 252 simultaneously switched contact points, has 21 horizontal suspension bars and seven vertical cantilever columns on each side, resulting in an iris opening of 1.075 mm in the waveguide H-plane. In the activated-iris (ON) state, the simulation result is also compared to a
Figure 6: Measured and HFSS-simulated performance of a chip with MEMS-reconfigurable inductive iris compared to a block iris and a reference chip: (a) Inductive iris in the activated/ON state; (b) Inductive iris in the deactivated/OFF state; (c) Schematic cross-sectional view of the reconfigurable iris, the block iris, and the reference chip.
208

Switchable cavity resonator
A switchable cavity resonator was created by placing a MEMS-reconfigurable surface half a wavelength away from the back-shorted end of a WR-12 waveguide as shown in Figure 7. When the inductive iris is deactivated, i.e. configured as a complete transmissive surface, the configuration is similar to a standard back-shorted waveguide.
assembly, and the ON-state measurements agree very well to idealized irises. Furthermore, the application of switchable inductive iris was shown by implementing a cavity resonator by integrating a MEMS-reconfigurable inductive iris half-wavelength from a back-short end of a waveguide. The switched resonator (ON-state) showed Q-factor of 186.13 at the resonance frequency of 68.87 GHz, and its OFF-state isolation is better than 2 dB (including the measurement setup).
Figure 7: Cross-sectional view of integration of a chip with a MEMS-reconfigurable iris into a back-shorted WR-12 rectangular waveguide to implement a switchable cavity resonator.
The measurement results of the switchable cavity resonator, shown in Figure 8, confirm that the resonator can clearly be switched ON and OFF. The ON-state reflection coefficient is 14.5 dB at the sharp resonance frequency of 68.87 GHz with a Q-factor of 186.13. In contrast to that, the OFF-state configuration does not show any resonance behavior and has an insertion loss of less than 2 dB in the frequency range of interest. Also here, the OFF-state insertion loss is to a major extent contributed by the measurement setup.
Figure 8: Measured cavity resonator (as in Figure 7) based on a single MEMS-switchable iris in ON and OFF states.
CONCLUSIONS
This paper reported on a switchable inductive waveguide iris with only 30-μm thick MEMSreconfigurable surface for V-band (50-75 GHz) application. The measurement results of such an iris integrated into a WR-12 rectangular waveguide demonstrated the insertion loss is better than 1.0 dB for the iris in the deactivated (OFF) state, to the major part up to 0.8 dB attributed to the
ACKNOWLEDGEMENTS
The authors wish to thank Alan Cheshire and Gabriel Roupillard from Applied Materials for their help with the Centura Etch. The authors would also like to thank Jan Åberg from MicroComp Nordic AB for the fabrication of the customized flanges for the measurement setup.
REFERENCES
[1]H. Joshi, H. H. Sigmarsson, S. Moon, D. Peroulis, W. J. Chappell, “High-Q fully reconfigurable tunable bandpass filters”, IEEE Trans. Microw. Theory Tech., vol. 57, no. 12, pp. 3525-3533, Dec. 2009.
[2]S.-J. Park, I. Reines, C. Patel, G. M. Rebeiz, “High-Q RF-MEMS 4–6 GHz tunable evanescent-mode cavity filter”, IEEE Trans. Microw. Theory Tech., vol. 58, no. 2, pp. 381-389, Feb. 2010.
[3]J. Small, M.S. Arif, A. Fruehling, D. Peroulis, “A Tunable Miniaturized RF MEMS Resonator With Simultaneous High Q (500–735) and Fast Response Speed (< 10–60µs)”, J .Microelectromech. Syst., vol. 22, no. 2, pp. 395-405, April 2013.
[4]G. M. Rebeiz, RF MEMS theory, design, and technology, Wiley, 2003.
[5]P. Blondy, D. Peroulis, “Handling RF Power: The Latest Advances in RF-MEMS Tunable Filters”, IEEE Microwave Magazine, vol. 14, no. 1, pp. 24-38, Jan.- Feb. 2013.
[6]D. Dancila, P. Ekkels, X. Rottenberg, I. Huynen, W. De Raedt, H. A. C. Tilmans, “A MEMS variable faraday
cage as tuning element for integrated silicon micromachined cavity resonators”, in IEEE 23rd
International Conference on Micro Electro Mechanical Systems, Wanchai, Hong Kong, Jan. 24-28, 2010, pp. 723-726.
[7]Z. Baghchehsaraei, U. Shah, J. Aberg, G. Stemme, J. Oberhammer, “Millimeter-wave SPST waveguide switch based on reconfigurable MEMS surface”, in
IEEE MTT-S Int. Microw. Symp. Dig., June 2-7, 2013, pp. 1–3.
[8]Z. Baghchehsaraei, M. Sterner, J. Aberg, J. Oberhammer, “Integration of microwave MEMS devices into rectangular waveguide with conductive polymer interposers”, Journal of Micromechanics and Microengineering, vol. 23, no. 12, pp. 1-10, 2013.
CONTACT
*Z. Baghchehsaraei, tel: +46-762315809; zargham@kth.se
209