
диафрагмированные волноводные фильтры / d6bf6408-7314-4fe5-b273-bc209521f2c4
.pdf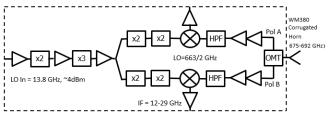
This article has been accepted for publication in a future issue of this journal, but has not been fully edited. Content may change prior to final publication. Citation information: DOI 10.1109/TTHZ.2018.2873114, IEEE Transactions on Terahertz Science and Technology
29th IEEE International Symposium on Space Terahertz Technology, Pasadena, California, USA, March 26-28, 2018
WM380 (675-700GHz) Band-Pass Filters in
Milled, Split-Block Construction
Daniel Koller*, Eric W. Bryerton, and Jeffrey Hesler
Virginia Diodes, Inc., Charlottesville, VA 22903, U.S.A.
*Contact: koller@vadiodes.com
Abstract—Filters play an invaluable role in RF analysis and communications hardware, blocking unwanted signals, limiting bandwidth, attenuating harmonic components, etc. In waveguide construction for mm-wave frequencies, where the powers are generally low, the iris-coupled-resonator band-pass filter has proven to be very practical and amenable to easy machining.
At Virginia Diodes, much of our technology has been constructed using standard "split-block" techniques, in which high-precision CNC milling machines are used to mill out the features from solid blocks of metal. Typical machining tolerances are on the order of +/-5-10 microns. Construction of such filters to ~200 GHz has been routine but pushing the operation into the Terahertz regime requires special considerations.
Described here is a WM380 (WR1.5) filter for the 500-750 GHz waveguide band having a pass-band of 675-700 GHz. The filter is proof of concept for a 640 GHz heterodyne polarimeter, designed as part of an SBIR to develop technology for NASA's planned Aerosol, Cloud and Ecosystems (ACE) mission. From the very beginning, filter design and optimizations were carried out assuming the structure would be milled, hence necessitating that all internal features accommodate the finite radii of available machine tools. Construction of this filter required careful attention to machining tolerances to be able to push the milling machines to their absolute limits of +/-2.5 microns or better.
Measured results of a batch of filters are shown and compared to simulations to illustrate just how well these filters can be made. Furthermore, the filters can be tuned by simple mechanical means and data are presented to illustrate how easily the filters can be adjusted.
Additional modifications to the filter topology to simplify machining, and allow other construction techniques to be utilized are also demonstrated. Ultimately it should be possible to push the split block technology to manufacture iris coupled resonator filters for use at frequencies of well over 1 THz.
I. INTRODUCTION
The specific motivation for the work described here was the development of a 640 GHz integrated-block heterodyne polarimeter, intended to serve as a proof-of-concept for future instruments in which many complex mm-wave components are integrated into a single machined part[1]. As shown in the block diagram in Figure 1 below, a pair of identical filters is required to pass only the upper sideband of an input signal, from 675-692 GHz. The two filters must be closely matched, and more importantly need to meet a tight, and absolute
frequency specification as determined by the science for which the instrument is designed.
Figure 1 Block diagram of an Integrated 640 GHz Heterodyne Polarimeter
The filters chosen for the project are of the iris-coupled resonator design, adapted to a split-block construction, which lends itself readily to CNC machining[2]. In such a device, thin inductive irises milled into the block divide the waveguide into a series of coupled resonators. A typical resonator length for the WM380 band in question is on the order of 250 microns, yet state-of-the-art CNC milling allows a machining tolerance of +/-2.5 microns[3]. In a worst-case scenario, the errors can be independent, yielding a length variation of the resonators of +/-2%. The corresponding variation in frequency for a 675 GHz filter is approximately +/-14 GHz, which is more than half of the target pass-band and will clearly not work for the instrument pictured above. A possible solution is to design the filters to operate at frequencies nominally higher than the desired pass band and to tune them down mechanically to the desired values. Several techniques for doing so are described below.
II.FILTER DESIGN I
A filter, hereafter referred to as X1, was designed with a 3- dB pass-band of 670-710 GHz to allow for some initial compensation for machining tolerances and with the expectation, based on prior empirical evidence, that there would be some slight shifting down in frequency of the initial build. X1 is of a “conventional” design in which machined irises, each 1/10 the waveguide width in thickness, stand out from the waveguide sides. The irises are of different heights. Construction is of the split-block design in which half of the structure is located in part of a metal block with the other half in an identically machined block, and the structure is split down the middle along the E-symmetry plane of the waveguide. By pushing state-of-the-art milling machines to their limits, five blocks were delivered with mechanical
2156-342X (c) 2018 IEEE. Personal use is permitted, but republication/redistribution requires IEEE permission. See http://www.ieee.org/publications_standards/publications/rights/index.html for more information.

This article has been accepted for publication in a future issue of this journal, but has not been fully edited. Content may change prior to final publication. Citation information: DOI 10.1109/TTHZ.2018.2873114, IEEE Transactions on Terahertz Science and Technology
29th IEEE International Symposium on Space Terahertz Technology, Pasadena, California, USA, March 26-28, 2018
tolerances better than +/-2.5 microns in all dimensions. A |
simulation based on the dimensions of that same filter is |
micrograph of one of the X1 filters is shown in Figure 2. |
shown in Figure 4. |
|
|
|
|
Figure 2 Micrograph of the X1 filter looking in from the split-plane, showing the thin irises.
Figure 4 Typical filter performance compared to HFSS simulation based on measured physical dimensions of filter X1 #1-02.
RF performance of all five filters was measured on a Keysight Vector Network Analyzer with a pair of Virginia Diodes WM380 frequency extension heads, using an SOLT calibration. Results for all five units are shown in Figure 3 below. Note that two of the filters (#1-01 and #1-05) are shifted down in frequency relative to the others, presumably due to within-tolerance variations in the machining. Otherwise, the filters are very tightly grouped, indicating good control over the machining.
Figure 3 Measured performance of the X1 filter. Inset shows the asassembled filter geometry.
All of the filters are shifted down in frequency with respect to the design by about 10 GHz at the low end of the pass band, and slightly less at the upper end of the band. While the design is not optimal for use in the final 640 GHz polarimeter the goal of the present study was to see how closely the filters could be machined and subsequently tuned, rather than the exact target frequency.
Filter #1-02 was (arbitrarily) chosen as typical of the batch and all subsequent measurements of the band-pass shifts are with respect to the band edges of that filter. A comparison of the measured filter performance for #1-02 and an HFSS
Note that there is one free parameter in the HFSS simulation; the “gap” between the two halves of the filter, split along the E-plane of the waveguide, has been increased to 1 micron. The results are consistent with a residual gap between the block halves which does not go away when the two pieces are clamped together. A RMS surface roughness of ½ micron, due to residual machining marks is all that is required to produce such a gap, but note that the value is well below the expected ~2.5 micron machining tolerances, and yet easily explains the relative shift in the various filter responses.
Attempts to simulate all the filters using their “as machined” dimensions resulted in fits which compared poorly to the measured return loss. It is likely that uncertainties in measuring the dimensions of the machined parts are greater than the machining uncertainties. Better fits were obtained by assuming that the blocks were machined essentially as designed, with the exception of errors in the depth of the cut
(i.e. the “gap”) which are always multiplied by two when the blocks are assembled.
The expected behaviour of the X1 filter upon intentionally introducing various “gaps” between the block halves was simulated in HFSS and the results are shown in Figure 5. The lower edge of the pass band shifts linearly at the rate of -1.9 GHz per micron of introduced gap. The upper band edge shifts slightly less, at a rate of -0.9 GHz per micron so the overall pass-band of the filter increases as the filter response is shifted down. The return loss of the filter also worsens as the gap is increased, but the decay is well behaved. The simulations hint at an elegant way to “tune” the filter by introducing a gap between the block halves in a controlled manner.
Note that simulation of an actual narrow gap is difficult, requiring careful consideration of the morphology of the facing surfaces and radiation boundaries. The model was simplified by simply increasing the depth of the features on both sides of the waveguide. Because the filter is E-plane split, any RF leakage from the gap is expected to be small and will not deteriorate the insertion loss of the device. The
2156-342X (c) 2018 IEEE. Personal use is permitted, but republication/redistribution requires IEEE permission. See http://www.ieee.org/publications_standards/publications/rights/index.html for more information.

This article has been accepted for publication in a future issue of this journal, but has not been fully edited. Content may change prior to final publication. Citation information: DOI 10.1109/TTHZ.2018.2873114, IEEE Transactions on Terahertz Science and Technology
29th IEEE International Symposium on Space Terahertz Technology, Pasadena, California, USA, March 26-28, 2018
validity of this assumption is confirmed by inspection of the measured data, described below.
Figure 5 HFSS simulations of X1 filter, "tuned" by separating the halves at the split-plane.
III.FILTER DESIGN II
A second series of filters was also designed and built. The X2 structure is intended to be more amenable to scaling to higher frequencies, where a two-level electroforming or etching technique might provide higher dimensional accuracy[4][5]. All the irises are of the same height, but the widths vary. The design was carried out by optimizing in FEST-3D but forcing the iris heights to be constant, while maintaining the same target performance as the X1 design[6]. A micrograph of half of an X2 filter is shown in Figure 6.
Figure 7 Measured performance of the X2 filter. Inset shows the asassembled filter geometry.
Figure 8 compares the measured response of filter 1-02 with the HFSS simulations. In this case, a larger value of 3.5 microns for the gap between the block halves was required to match the measured data. The value is consistent with the increased (but un-measured) surface roughness evident in Figure 6.
Note that the split plane of the block appears considerably rougher than the X1 filter (presumed to have ~ ½ micron surface roughness) and visual inspection reveals larger scale, periodic machine markings. The blocks were not lapped, so any residual tooling marks and surface errors are effectively doubled when the blocks are assembled. Nevertheless, the total “gap” of 3.5 microns is still less than the twice the individual block tolerance of ~2.5 microns. On this scale, even inconsistencies between the thickness of the gold plating on the surface and the bottom of the waveguide channel need to be considered as possible sources of error.
Figure 6 Micrograph of the X2 filter looking in from the split-plane. The irises are all the same height, but the "widths" vary.
All five units were measured on a VNA and the results are presented in Figure 7, which also includes an image of the unusual filter structure in the inset. Note that all five filter responses are relatively closely matched, and as with the X1 design, there is a net shift down in frequency from the design target.
As before, filter #1-02 was selected as “typical” and used as a reference point for the frequency shifts of the various tuning experiments.
Figure 8 Typical filter performance compared to HFSS simulation of Ideal X2 filter.
The simulated effect of tuning the filter by introducing a gap between the block halves is again explored in Figure 9 and some notable differences are evident. The lower and upper edges of the band shift downward at the rate of 2.6 and 2 GHz per micron respectively, a rate much greater than that of the X1 design. In addition the bandwidth increases by only 0.6 GHz per micron, vs. 0.95 GHz per micron for the X1 design.
2156-342X (c) 2018 IEEE. Personal use is permitted, but republication/redistribution requires IEEE permission. See http://www.ieee.org/publications_standards/publications/rights/index.html for more information.

This article has been accepted for publication in a future issue of this journal, but has not been fully edited. Content may change prior to final publication. Citation information: DOI 10.1109/TTHZ.2018.2873114, IEEE Transactions on Terahertz Science and Technology
29th IEEE International Symposium on Space Terahertz Technology, Pasadena, California, USA, March 26-28, 2018
Overall, the X2 design is much more sensitive to tuning by introduction of a gap between the block halves and the bandwidth changes more slowly.
Figure 9 HFSS simulations of X2 filter, "tuned" by separating the halves at the split-plane.
IV. FIXED TUNING WITH MYLAR AND ALUMINUM SHIMS
For the initial series of experiments, small Mylar squares, each 5 microns thick, were placed between the clamp screws of filter X1 #1-02 as shown in the inset to Figure 10[7]. The filter was clamped together, measured, and then another layer of squares was placed on top of the first to build the gap up to 10 microns, and the process continued up to 5 layers. Note however that the Mylar spacers lie between the clamp screws. The resulting frequency shifts shown in the figure are not as large as expected by simulation, and the response is nonlinear. It is likely that the block deformed under clamping, so the full effect of the spacers was not realized.
Figure 10 Filter X1 #1-02 "tuned" by adding small squares of 5 micron thick Mylar, one layer at a time.
The distortion of the block due to the uneven distribution of the spacers has implications for the “differential tuner” described below. It also eliminates concerns about flatness of the blocks as long as the filter structure is placed between pairs of clamp screws; The block will deform under pressure to ensure that the split plane surfaces are in good contact. Surface features with length scales smaller than a few mm will however still keep the blocks apart.
In the next series of tests, larger sheets of Mylar were used that cover the full length of the block and the results for multiple filters with differing gaps are presented in Figure 11. Note that the filters were not identical so the resulting frequency shifts appear to be non-linear and curves for filters with the same gap are not coincident. What is immediately apparent is that the shifts are much larger than when using small Mylar squares. When the frequency shifts relative to the un-gapped filter are determined, and the offset from the “reference filter” #1-02 subtracted, the response is indeed linear as will be further summarized below.
Figure 11 Multiple X1 filters tuned by adding longer pieces of Mylar between the block halves.
Finally, a 14 micron thick sheet of aluminum foil was used as shim material. One, and later two pieces of foil were laid down across the entire central section of the block straddling the position of the filter to ensure a uniform gap. The results are shown in Figure 12 along with the positioning of the foil as illustrated in the inset. The resulting filter tuning was linear and as predicted by the HFSS simulations.
Figure 12 Filter X1 #1-02 tuned by adding layers of rolled aluminum foil.
The filters were constructed in the centers of 1” (2.54 cm) long waveguides which are expected to have a loss of 0.57 dB per cm [8]. All of the filters measured have a worst case insertion loss at mid-band of ~2.1 dB, giving an excess loss of only ~0.26 dB per cm. Despite introducing gaps between the blocks of up to 25 microns, none of the filters showed any
2156-342X (c) 2018 IEEE. Personal use is permitted, but republication/redistribution requires IEEE permission. See http://www.ieee.org/publications_standards/publications/rights/index.html for more information.

This article has been accepted for publication in a future issue of this journal, but has not been fully edited. Content may change prior to final publication. Citation information: DOI 10.1109/TTHZ.2018.2873114, IEEE Transactions on Terahertz Science and Technology
29th IEEE International Symposium on Space Terahertz Technology, Pasadena, California, USA, March 26-28, 2018
increase in the mid-band insertion loss, supporting the validity of the HFSS simulations and the assertion that the E-plane split construction precludes leakage from the waveguide.
V. FREQUENCY SHIFT SUMMARY
The performance of the shimmed X1 filters is summarized in Figures 13 and 14 below, with linear fits to the data for comparison. The non-linearity of the tuning with small Mylar squares is evident, and it also apparent that the larger Mylar sheets (not shown, but roughly the size and shape of the aluminum foil pieces shown Figure 12) are indeed effective.
The 5 micron Mylar shims present an anomaly. Note that there are TWO data points, from different filters, corresponding to the relatively un-shifted 5 micron-gapped filter. A plausible explanation is that the initial Mylar sheet contributes more to a smoothing of some surface roughness at the block surface. In other words, it fills in the ~1 micron gap assumed to be present between the block halves as shown in the HFSS simulations of Figure 4. The same effect however is NOT seen in Filter X2.
Aluminum shims appear to be the most robust, and shift the frequency response of the filter by nearly the same amount as expected from the simulations. Corresponding plots for Filter X2 are provided in Figures 15 and 16.
Figure 13 Frequency shifts vs. gap for X1 filter using various spacers.
VI. |
CONTINUOUS DIFFERENTIAL SCREW TUNER |
Encouraged by the success of the Mylar and aluminum shims, an additional filter tuning scheme was designed. Sets of “differential screws” were constructed as depicted in Figure 17. Each pair of screws consists of a commonly available 2- 56 set screw, to be threaded into the top half of the block, and a 2-64 set screw, to be threaded into the bottom half. The two are locked together by a short bit of hex key, pressed into the 2-56 screw. The resulting mechanisms replace the two clamp screws on either side of the filter structure in the block. When the blocks are assembled, the 2-56 screw engages the 2-64 screw so that they turn together. For each turn, the upper screw advances 1/56”, but the screw in the lower half of the block only advances 1/64”. The net result is that the screws compress the short hex key bit between them producing a
Figure 14 Bandwidth vs. gap for X1 filter using various spacers.
Figure 15 Frequency shifts vs. gap for X2 filter using various spacers.
Figure 16 Bandwidth vs. gap for X2 filter using various spacers.
separation of the block halves of only 57 microns per turn. The expected resolution is twice that of a precision 0.1 mm pitch micrometer and the device is many times more compact.
2156-342X (c) 2018 IEEE. Personal use is permitted, but republication/redistribution requires IEEE permission. See http://www.ieee.org/publications_standards/publications/rights/index.html for more information.

This article has been accepted for publication in a future issue of this journal, but has not been fully edited. Content may change prior to final publication. Citation information: DOI 10.1109/TTHZ.2018.2873114, IEEE Transactions on Terahertz Science and Technology
29th IEEE International Symposium on Space Terahertz Technology, Pasadena, California, USA, March 26-28, 2018
stress limit of the mechanism. Any additional turning of the device resulted in stripping out the hex of the 2-56 screw.
Figure 17 "Differential Screw" mechanisms were constructed by joining pairs of common 2-56 and 2-64 set screws.
Mounted between a pair of VNA extender heads, the filter is shown ready for measurement in Figure 18. To keep track of the separation of the block halves, the hex keys were turned in increments of ¼ turn each. The filter is expected to see a gap which is an average of the separations produced by the two screws so a net increment of ~7 microns was expected.
Figure 19 Frequency shifts of "differentially tuned" filter X1.
Figure 20 Summary of frequency shifts for "differentially tuned" X1 filter.
Figure 18 "Differentially Tuned" filter mounted between VNA extenders.
The results, shown in Figure 19 tell a different story. While the frequency shifts are linear, they are not nearly as large as expected from the HFSS simulations. Note that the block is clamped by pairs of screws on either end. There is a large amount of force on the block. The differential screws must work against the compressive forces of the adjacent clamping screws so there is a deformation of the block, and the net effect is to reduce the separation obtained from the differential mechanism alone.
Results for both filter designs are summarized in Figures 20 and 21. The fits shown exclude the first three data points where it appears that the two halves of the differential mechanism were not fully engaged. It takes up to 1 full turn to ensure that the hex bit is in contact with the 2-64 set screw
so that the spacing becomes proportional to the number of Figure 21 Summary of frequency shifts for "differentially tuned" X2 filter. turns. The last point was also ignored because it nearing the
2156-342X (c) 2018 IEEE. Personal use is permitted, but republication/redistribution requires IEEE permission. See http://www.ieee.org/publications_standards/publications/rights/index.html for more information.

This article has been accepted for publication in a future issue of this journal, but has not been fully edited. Content may change prior to final publication. Citation information: DOI 10.1109/TTHZ.2018.2873114, IEEE Transactions on Terahertz Science and Technology
29th IEEE International Symposium on Space Terahertz Technology, Pasadena, California, USA, March 26-28, 2018
The large forces required to separate the block halves have an additional benefit; the filter tuning is repeatable. The X2 filter was tuned by turning both screws by 1 turn, then going back to 0 turns, and repeating several times, measuring the response each time. The initial frequency shift was greater than the others, and could not be repeated, but all subsequent shifts were within ~1 GHz of each other. In all likelihood, the initial turn compressed the threads of the screws, the block and the mating surfaces of the hex bit. Once so worn, the tuning was repeatable. The very high compressive forces in the block ensured that the shifts returned to zero each time the differential screws were backed off; the elastic limit of the block was not reached.
VII. STABILITY
Mylar is an established material for space-qualification, but stability of the filters remains a concern. Two X1 filters, each with 2 layers of 5 micron thick Mylar, were baked in an oven at 110C for 50 hours. Additionally two X2 filters, one with only one 5 micron layer, and one with 15 microns of Mylar, were similarly baked. There was no measurable change in the filter response of any of the filters.
A more stringent test is the so-called “Bellcore” cycle, in which parts are subjected to a 70C bake followed by a -40C soak in a 1 hour period, for 1000 hours[9]. As before, two X1 filters, each with 10 micron Mylar spacers, and two X2 filters, one with a 5 micron spacer, the other with 15 microns, were put through the Bellcore cycling. As before, no filter experienced any measurable change in performance, indicating that the Mylar and the clamping are stable under the tested conditions.
Stability tests on the differentially tuned filters were not attempted. In principle, the screws can be locked down with a thread-binding epoxy and the devices are expected to remain stable, though vibration testing might be warranted.
VIII. CONCLUSIONS
A WM380 675-700 GHz band-pass filter, with an inductive shunt, iris-coupled-resonator structure has been made in splitblock construction. The filter design is “routine”, well understood and has been in the literature for decades. What is unique is its frequency of operation. At 675 GHz, construction required pushing to the absolute limits of machining tolerances to make a repeatable filter capable of hitting absolute frequency targets. Despite the demonstrated reproducibility of the pass-band, the push towards even higher frequency, and smaller dimensions will require some sort of “adjustment” or tuning of the filters. A predictable, stable means of shifting the pass band of the as-designed filter down in discrete steps with Mylar or aluminum shims has been demonstrated.
A second design, with a much simpler mechanical structure has been similarly proven. Rather than utilizing thin irises milled into the waveguide, the simplified design has features milled to only two depths. The intention is that the filter could be made more easily with CNC milling, but also by electroforming or etching techniques where an “etch to a depth” or “deposit to a height” fabrication method would benefit from having only two steps in the structure. While there is no theoretical design paradigm for developing the
filter, a structure is easily obtained by optimizing a model, with constraints, using commercially available simulation software.
Finally, both designs, can be tuned continuously using a novel approach. A “differential screw” tuning mechanism allows for arbitrarily small increments. In principle the design could be improved by integrating stress-relief cutouts in the block to reduce the clamping force around the differential screws. As long as careful attention is paid to the design so that the elastic limit of the metal is not reached, a large and reproducible tuning range can be expected.
IX. ACKNOWLEDGMENT
This research was carried out during the development of a 640 GHz Heterodyne Polarimeter, built in support of a NASA Goddard Space Flight Center SBIR Phase II Contract, #NNX17CG06C.
X.REFERENCES
[1]Eric W. Bryerton, Jeffrey L. Hesler, Daniel Koller, Yiwei N. Duan, and Thomas W. Crowe, “A Compact Integrated 675-693 GHz Polarimeter”, accepted for publication in the Proceedings of the 43st International Conference on Infrared, Millimeter, and Terahertz waves (IRMMWTHz), 2018.
[2]G. Matthaei, L. Young, and E.M.T. Jones, Microwave Filters, Impedance Matching Networks and Coupling Structures, New York: McGraw Hill, 1964, first ed.,pp. 450-464.
[3]X. Shang, H. Yang, D. Glynn and M. J. Lancaster, "Submillimeter-wave waveguide filters fabricated by SU-8 process and laser micromachining," in IET Microwaves, Antennas & Propagation, vol. 11, no. 14, pp. 2027-2034, 19 11 2017. doi: 10.1049/iet-map.2016.0951.
[4]C. A. Leal-Sevillano et al., "Silicon Micromachined Canonical E-Plane and H-Plane Bandpass Filters at the Terahertz Band," in IEEE Microwave and Wireless Components Letters, vol. 23, no. 6, pp. 288290, June 2013. doi: 10.1109/LMWC.2013.2258097
[5]C. Jung-Kubiak et al., "A Multistep DRIE Process for Complex Terahertz Waveguide Components," in IEEE Transactions on Terahertz Science and Technology, vol. 6, no. 5, pp. 690-695, Sept. 2016.
doi: 10.1109/TTHZ.2016.2593793
[6]FEST, www.fest3d.com, Aurora Software and Testing S.L.U. (CST/3DS).
[7]E.g. 5 micrometer thick clear Mylar, 7.0g /m2, available from http://www.homefly.com/products.asp?id=31 [as of 17 September 2018].
[8]https://standards.ieee.org/findstds/standard/1785.2-2016.html See also http://vadiodes.com/images/AppNotes/VDI_Waveguide_Designations_2 015.01.pdf, recovered 17 September 2018.
[9]Bellcore (Bell Communications Research, Morristown, N.J.) Document TA-NWT-000765 and GR-765
XI. AUTHORS
Daniel Koller (M ’12) is a native of the State of New
Jersey. He received the B.A. in physics from Columbia University in 1987. Concentrating in condensed matter physics and the study of superconducting doped Carbon60, he received the M. A. and Ph. D. degrees in physics from the State University of New York in Stonybrook in 1990 and 1995 respectively. As an engineer at the National Radio Astronomy Observatory (NRAO), Central Development Laboratory (CDL), Charlottesville, VA,
from 1999 to 2009 he designed large, low loss dielectric vacuum windows, Dewar systems and IF chains in support of the Band 6 cartridge tests for the Atacama Large Millimeter Array (ALMA), now deployed in Chile. He has been on the staff of Virginia Diodes, Inc., Charlottesville VA for 8 years, where he specializes in the design of passive mm-wave and THz components.
2156-342X (c) 2018 IEEE. Personal use is permitted, but republication/redistribution requires IEEE permission. See http://www.ieee.org/publications_standards/publications/rights/index.html for more information.

This article has been accepted for publication in a future issue of this journal, but has not been fully edited. Content may change prior to final publication. Citation information: DOI 10.1109/TTHZ.2018.2873114, IEEE Transactions on Terahertz Science and Technology
29th IEEE International Symposium on Space Terahertz Technology, Pasadena, California, USA, March 26-28, 2018
|
|
Dr. Eric W. Bryerton |
(S’95–M’99–SM’06) received his |
Jeffrey L. Hesler received the B.S.E.E. degree from |
||
|
|
BSEE from the University of Illinois in Urbana- |
Virginia Tech, Blacksburg, USA, in 1989, and the |
|||
|
|
Champaign and his PhD in EE from the University of |
M.S.E.E. and Ph.D. degrees from the University of |
|||
|
|
Colorado at Boulder. From 1999-2013, he was a research |
Virginia, Charlottesville, USA, in 1991 and 1996, |
|||
|
|
engineer at the National Radio Astronomy Observatory |
respectively. He is the Chief Technology Officer of |
|||
|
|
(NRAO) where he was responsible for the design, |
Virginia Diodes and a Visiting Research Assistant |
|||
|
|
development, and construction of the 30-950 GHz local |
Professor at the University of Virginia. His career is |
|||
|
|
oscillator system for ALMA (Atacama Large Millimeter |
focused on the creation of new technologies that are |
|||
|
|
Array), an array consisting of 66 twelve-meter antennas |
making possible the full exploitation of the Terahertz |
|||
with nearly quantum-noise limited cryogenic SIS receivers located on the |
frequency band for scientific, defense and industrial applications. He has |
|||||
Atacama plateau in northern Chile. Since joining VDI, Eric is enjoying |
published over 150 technical papers in refereed international conferences and |
|||||
applying the development of highly integrated sub-millimeter and THz |
journals, given talks at THz-focused workshops and conferences such as IMS |
|||||
modules to many other research areas besides radio astronomy, including sub- |
& EuMW, is a member of IEEE TC MTT-4 on THz Technology and |
|||||
millimeter test equipment extender modules, CubeSat atmospheric studies, |
Applications and serves as a reviewer for a variety of IEEE & IEE journals. |
|||||
ITER |
plasma |
diagnostics, |
and |
high-data-rate |
millimeter-wave |
Terahertz systems based on Dr. Hesler’s innovative designs are now used in |
communications. |
|
|
|
|
hundreds of research laboratories throughout the world. |
2156-342X (c) 2018 IEEE. Personal use is permitted, but republication/redistribution requires IEEE permission. See http://www.ieee.org/publications_standards/publications/rights/index.html for more information.