
диафрагмированные волноводные фильтры / aea536b1-9aba-4a97-816d-95c53ad32801
.pdfThis article has been accepted for inclusion in a future issue of this journal. Content is final as presented, with the exception of pagination.
IEEE TRANSACTIONS ON TERAHERTZ SCIENCE AND TECHNOLOGY |
1 |
Silicon Micromachined Terahertz Bandpass Filter
With Elliptic Cavities
Jian-xing Zhuang, Student Member, IEEE, Zhang-Cheng Hao, Member, IEEE, and Wei Hong, Fellow, IEEE
Abstract—In this paper, a 400-GHz silicon micromachined elliptic cavity waveguide filter with two transmission zeros on both sides of the passband is presented. The filter is cascaded by two elliptic cavities which are operating at quasi- mode. Each elliptic cavity can introduce a transmission zero near the passband of the filter. By adjusting the axial-ratio (AR) of the elliptic cavity, the position of the introduced transmission zero could be moved to the upper side or the lower side of the passband. The micromachining process of deep reactive ion etching (DRIE) is used for the fabrication. The measured 3-dB bandwidth of the filter is 7.52%, from 380.2 to 409.9 GHz, and the measured insertion loss is 2.84 dB, including extra waveguide of about 4.5 mm at the input and output ports.In addition, the insertion loss of straight waveguide is also measured and analyzed. Then, an analysis method for the loss property is summarized. According to the measurement, the unit length loss of the waveguide is about 0.144 dB/mm at 400 GHz.
Index Terms—Bandpass filter, deep reactive ion etching (DRIE), elliptic cavity, insertion loss, micromachining, transmission zero.
I. INTRODUCTION
WITH the development of measurement system and the fabrication process for the micro-electro-me- chanical systems (MEMS), submillimeter-wave and terahertz frequency bands have attracted more and more attention in recent years. The most commonly used micromachining process at millimeter-wave frequency is high-precision milling process. However, while the frequency increases to submil- limeter-wave or terahertz frequency band, the process becomes more time-consuming and expensive due to the decreasing of the dimensions. At the terahertz frequency band, micromachining processes with photolithographic technology [1]–[18] are widely used for the fabrication of components. These techniques can be roughly divided into three categories: SU-8 photoresist-based processes [1]–[3], LIGA and UV-LIGA processes [4], [5], and silicon etching process, such as KOH wet etching and deep reactive ion etching (DRIE) dry etching techniques [6]–[17]. Each technique has its own advantages and disadvantages [7]–[9] and will not be described here. Among
Manuscript received June 11, 2015; revised August 20, 2015; accepted September 14, 2015. This work was supported in part by Research Fund for the Doctoral Program of Higher Education of China under Grant 20120092110012 and the National Nature Science Foundation of China under Grant 61471118.
The authors are with the State Key Laboratory of Millimeter Wave, School of Information Science and Engineering, Southeast University, Nanjing 210096, China (e-mail: jxzhuang@emfield.org; zchao@seu.edu.cn; weihong@seu.edu. cn).
Color versions of one or more of the figures in this paper are available online at http://ieeexplore.ieee.org.
Digital Object Identifier 10.1109/TTHZ.2015.2480844
them, the most commonly used technique is the DRIE process, which mainly adopts the standard Bosch process.
Due to the advantages of low transmission loss, high power capacity, and suitability for fabrication by the micromachining process, rectangular waveguide structures are widely used for terahertz application. In [8], a hybrid coupler and a power divider are fabricated at the -band with DRIE process. In [18], an all-metallized micromachined waveguide coupler with outstanding accuracy is shown. In [10]–[15], terahertz filters are proposed from 120 to 750 GHz. All of the filters are designed with conventional structures, and the loss properties have not been analyzed in detail. Additionally, most of these filters are implemented with rectangular cavities.
In this paper, elliptic cavities are used for the filters. The general concept of the elliptic cavity includes the circular cavity while its major and minor axes are with the same length. Meanwhile, the unloaded quality factor of the elliptic cavity is higher than the rectangular cavity at the same frequency, which is beneficial for achieving the lower insertion loss. By adjusting the AR of the elliptic cavity, transmission zero could be moved to the upper or the lower side of the passband. According to this feature, a terahertz bandpass filter with two transmission zeros is designed by cascading two elliptic cavities with different AR. The filter is fabricated by the DRIE process. A straight waveguide is also fabricated and measured, and the source of the loss is analyzed in detail. On this basis, the filter is resimulated, and the simulated results match well with the measured results.
This paper is organized as follows. In Section II, several layer structures of the waveguide components are shown along with their advantages and disadvantages. On this basis, a proper layer structure is chosen. And the processing procedure of the fabrication and the measurement setup are introduced. In Section III, the insertion loss of waveguide is measured and the loss property of the waveguide is analyzed in detail. In Section IV, the proposed elliptic cavity bandpass filter is presented. The conclusion is discussed in Section V.
II.FABRICATION AND MEASUREMENT SETUP
A. Layer Structure
For ease of the peripheral connection and the measurement, waveguide with standard size is usually required. By using DRIE process, a certain depth needs to be etched on the silicon wafers. Due to the difference in etching depth and the way wafers stack, there are several different structures to form the waveguides, as shown in Fig. 1. In [8] and [10], waveguide components are combined by two identical halves in the H-plane, as shown in Fig. 1(a). These two halves are formed by
2156-342X © 2015 IEEE. Personal use is permitted, but republication/redistribution requires IEEE permission. See http://www.ieee.org/publications_standards/publications/rights/index.html for more information.

This article has been accepted for inclusion in a future issue of this journal. Content is final as presented, with the exception of pagination.
2 |
|
|
|
|
|
|
|
IEEE TRANSACTIONS ON TERAHERTZ SCIENCE AND TECHNOLOGY |
|
|
|
|
|
|
|
|
|
|
|
|
|
|
|
|
|
|
|
|
|
|
|
|
|
|
|
|
|
|
|
|
|
|
|
|
|
|
|
|
|
|
|
|
|
|
|
|
|
|
|
|
|
|
Fig. 2. Processing steps.
Fig. 1. Four different layer structures of the silicon based rectangular waveguides.
etching the half height of the standard waveguide. Thus both the top and the bottom surfaces of the waveguide are rough, which will increase the insertion loss. In addition, a small misalignment of these two halves also increases the loss. In [12]–[14], the height of the standard waveguide is etched in one silicon wafer. After bonded with another wafer, waveguide will be formed, as shown in Fig. 1(b). In this way, no misalignment exists, and the top surface of the waveguide is a smooth surface. The measured insertion loss is 0.4 dB/mm in the frequency band of 325 GHz–440 GHz in [13] and 0.15 dB/mm @ 600 GHz in [14]. In [9] and [11], both H-plane and E-plane waveguides are implemented in two halves, as shown in Fig. 1(a) and (c), respectively. The measured insertion loss is very good with the well-designed silicon pegs and bosses, which is lower than 0.1 dB/mm across the WR-1.5 band for both of the H- and E- plane split waveguides. In [15], the structure consists of three layers, while the waveguide is etched in the middle layer. The height of the middle layer is the standard waveguide height. The top and the bottom layers are glass or silicon layers. In this way, the roughness in the top and the bottom surfaces is eliminated. Meanwhile, the misalignment error could be avoided. Two filters operating at D-band are proposed by this structure in [15]. However, since the measurement is carried out by the local oscillation signal source with frequency source module and RF power meter, the return loss of the filters and the loss characteristic of the straight waveguide are not given.
In this paper, the structure in Fig. 1(d) is chosen for the fabrication of the waveguide and filter at WR-2.2 band, and the loss characteristic of the waveguide is analyzed in detail, which will be discussed in Section III.
B. Processing Steps and Measurement Setup
Since the cross section of WR-2.2 waveguide is 560 m
280
m, the high-resistivity silicon with a thickness of 280
m is chosen as the middle layer. Thetop and bottom layers are both glass with the thickness of 550
m. The silicon and glass wafers are all double side polished. As shown in Fig. 2, the general
Fig. 3. (a) Photograph of the silicon pieces. (b) Photograph of the test fixture.
(c) The enlarged view of the assembled silicon piece.
processing steps are as follows. First, photoresist is used as the mask layer and the shallow step is etched on the silicon wafer. Then thermal oxidation mask layer thicker than 3 m on the middle silicon wafer is formed, and ICP etching process is used to etch the depth of 280
m for the designed structures. After etching, the bottom layer is bonded with the silicon layer by anodic bonding technology. For metallization, the inner surfaces of the etched structures are sputtered with 0.3-
m gold, then a 2.5-
m gold layer is electroplated for the further metallization, while the skin depth for gold is 0.124
m at 400 GHz. The bonding interfaces of the top glass wafer and the silicon wafer are partly electroplated with gold in the same way as the etched structures. Next, the top glass wafer is bonded with the middle silicon wafer by the anodic bonding and thermocompression bonding to form the waveguides or cavities. In the area without gold, glass and silicon are bonded by anodic bonding, while the other areas electroplated with gold are bonded by thermocompression bonding. Then the wafer is divided into pieces by dicing saw. At last, in case the energy leaks into the silicon [16], [17], every side surface of the single piece is metalized by sputtering with 0.3
m gold. After fabrication, the size of the pieces are 6 mm
6 mm
1.38 mm or 6 mm
8 mm
1.38 mm, as shown in Fig. 3(a).
The test fixture is shown in Fig. 3(b), which is fabricated by CNC milling process. It consists of two metal blocks. A recess

This article has been accepted for inclusion in a future issue of this journal. Content is final as presented, with the exception of pagination.
ZHUANG et al.: SILICON MICROMACHINED TERAHERTZ BANDPASS FILTER WITH ELLIPTIC CAVITIES |
3 |
Fig. 4. Photograph of the measurement setup of the WR-2.2 waveguide.
is implemented in one of the blocks and is suitable for the silicon piece. The precision of our CNC machine is 5
m. In the actual fabrication process, initialdimension of the thickness and the width of the recess is slightly smaller than the silicon piece, then we enlarge the dimension of the recess with the increment of 5
m. Thus, after modification for several times, the silicon piece and the recess will match up with each other. The length of the silicon piece should just match up with the block or be longer than 5
m at most, because exact matching is very difficult. However, if the length of the silicon piece is shorter than the block, leakage will exit.
These two metal blocks can be connected by alignment pins and screws. Some small edges are left on the divided pieces, shown in Fig. 3(c). Therefore, two symmetrical incisions are cut in the recess.
The measurement is carried out by Agilent vector network analyzer (VNA) N5245A with two OML WR-2.2 frequency extenders, as shown in Fig. 4. The trough-reflect-line (TRL) calibration is used during the measurement. The flanges (UG-387) on the extenders are used to connect the test fixture and will be fixed by screws.
III. WAVEGUIDE MEASUREMENT AND LOSS ANALYSIS
In order to obtain the loss property of the components fabricated by DRIE process, a straight waveguide is fabricated, measured, and analyzed. Fig. 5 shows the measured results of the straight waveguide with a length of 8 mm. As can be seen, the insertion loss is approximately changing monotonically, and the return loss is better than 13 dB. The ripple of the return loss is caused by the mismatch between the flange interface and the proposed waveguide [4], [9]. The measured insertion loss is 1.86–0.92 dB from 325–500 GHz. The approximately unit length loss can be achieved using the insertion loss divided by the length of the waveguide. As a result, the unit length loss of the waveguide at 400 GHz is about 0.144 dB/mm.
Although the 2.5-m gold layer is electroplated for the metallization, surface roughness still exits inside of the waveguide and has an impact on the insertion loss. For surface roughness, a lot of models have been designed for the different structures. In this paper, we choose the Huray model to simulate the roughness of the gold layer [22]. Fig. 7 shows the effectof Hall–Huray surface ratio to the insertion loss. Nodule radius and layer thickness are set to 0.5 [13] and 2.5
m, respectively. The length of the waveguide is 8 mm in the simulation. With the increasing of Hall–Huray surface ratio, insertion loss will increase and
Fig. 5. Measured results of the 8-mm straight waveguide.
Fig. 6. Expanded view of the in Fig. 5.
Fig. 7. Effect of the Hall–Huray surface ratio to the insertion loss. Nodule radius and layer thickness are set to 0.5 and 2.5 m, respectively. The length of the waveguide is 8 mm.
present a rising tendency. And this change is almost linear to the increasing of surface ratio. The work in [13] also uses this model to analyze the loss. Another approach to analyze the surface roughness is using the equivalent conductivity which includes the effect of roughness [11], [14].
Another source of the loss is dimension error, which consists of two factors. One is the lateral walls of the waveguides which

This article has been accepted for inclusion in a future issue of this journal. Content is final as presented, with the exception of pagination.
4
Fig. 8. Measurement of the size of the input/output port of the waveguide.
Fig.9. Effectofthe shiftin -direction(airgap)tothe insertionloss.Thelength of the waveguide is 8 mm, the Hall–Huray surface ratio is set to 4, the Nodule radius and layer thickness are set to 0.5 and 2.5
m, respectively.
IEEE TRANSACTIONS ON TERAHERTZ SCIENCE AND TECHNOLOGY
Fig. 10. Effect of the shift in -direction to the insertion loss. The length of the waveguide is 8 mm, the Hall–Huray surface ratio is set to 4, the Nodule radius and layer thickness are set to 0.5 and 2.5
m, respectively.
are not perfectly vertical. As shown in Fig. 8, the bottom side of the waveguide port is wider than the top side. The taper angle in our process is about 1.46, similar to 1.65
in [13] and smaller than 3
in [11]. This factor comes from the DRIE process and can be improved by optimizing theetching parameters [15]. Another factor comes from the etching deviation. By the measurement of a microscope, the deviation is less than 2
m in our process, which has little impact on the results of the waveguide.
Misalignment between the test fixture and the flanges on the extenders is the third source of the loss. Misalignment will take place in three directions. In Fig. 9, a small inserted picture with two waveguide ports is used to show the shift directions in the measurement. In order to simplify the simulation process, the input/output ports on the both sides of the waveguide will shift in synchrony. The shift in the -direction will cause an air gap between two ports. The shifts in the
- or
-direction will cause H- or E- plane leakage, respectively. In the
-direction, the farther away from the center of the waveguide, the weaker the E-field. Therefore, the results will be less affected if the offset is only in the
-direction. As shown in Fig. 9, the gap or the shift in the
-direction has a great impact on insertion loss. With the effect of the air gap, the loss at the higher frequency band is larger than the middle and the lower frequency band. In the
-direc- tion, the shift mainly affects the lower frequency band, while
Fig. 11. Comparison of the resimulated results and the measured results of the straight waveguide.
the middle and the higher frequency change a little, as shown in Fig. 10. In addition, the ripple will become larger with the increasing of any kinds of these shifts.
All of the simulation analyses of the waveguide are carried out by the High Frequency Structure Simulator (HFSS). Based on the analyses mentioned above, we can achieve the simulated results shown in Fig. 11. The shifts in the - and
-direction are set to 0 and 10
m, respectively, and the Hall–Huray surface ratio is set to 4. The simulated and measured insertion losses are in good agreement with each other. The small rising tendency of the measured return loss is due to the abrasion of the flanges and the ports on extenders. The unit length loss is smaller than the 0.4 dB/mm in [13] and similar to 0.15 dB/mm in [14], but larger than the results in [9], due to the better surface roughness and the well-designed silicon pegs and bosses in [9].
Based on the above-mentioned analysis, a simulation analysis method for the loss property including the factors of surface roughness, dimension errors, and the misalignment could be summarized. This analysis method will be used in the next section for the simulation of filter.

This article has been accepted for inclusion in a future issue of this journal. Content is final as presented, with the exception of pagination.
ZHUANG et al.: SILICON MICROMACHINED TERAHERTZ BANDPASS FILTER WITH ELLIPTIC CAVITIES |
5 |
TABLE I
COMPARISON OF THE UNLOADED QUALITY FACTOR
Fig. 12. Schematic topology and the structure of the single cavity.
The quality factors are obtained by simulation.
IV. FILTER DESIGN AND RESULTS
A. Filter Design
At terahertz frequency, a better tolerance can be achieved if a relative larger dimension is used at the fixed frequency. Meanwhile, the unloaded quality factor is related to the insertion loss of the filter directly. The higher the
, the lower the insertion loss. Table I shows the comparison of the
of different cavities with different modes at about 400 GHz. The square cavity with fundamental mode has the lowest
and the smallest size. To the dual-mode cavities, the circular and the elliptic cavities have the higher
than the square and the rectangular cavities. And size of the dual-mode cavities are larger than single mode cavity at the same frequency. Therefore, the better tolerance and insertion loss will be achieved if the dual-mode circular or elliptic cavities are used for the terahertz components. The two different values for elliptic cavity represents the two quasi-
modes in different directions. The quality factors shown in Table I are obtained by HFSS. The conductivity is set to 3.3e7 S/m [4].
In [19], elliptic cavities are used to form a narrowband filter. In [20], substrate-integrated-waveguide elliptic and circular cavities are used for duplex. The length of the major and minor axes of the elliptic cavity is different, therefore it has some characteristics that the circular cavity does not has. Actually, the circular cavity is a special case of elliptic cavity when the length of major and minor axes is the same. In [21], the position of the transmission zero for the fundamental mode circular cavity can be adjusted by changing the angle between the input and output ports. However, we will adjust the position of the transmission zero by changing the ratio of the major and minor axes.
The transmission zeros are generated due to the fact that the input and output ports are all coupled to the quasi- modes in the cavity. By simultaneously exciting the two modes, a different sign will be presented at a certain frequency. Therefore, a node will be generated at the output port, and the transmission zero will appear [23], [24]. With the changing of the ratio of major and minor axes, the fields in the cavity are squashed and stretched. The node will appear at the different positions while the frequency is fixed. Therefore, we have to change the frequency to ensure the node still exist at the output port, while the axial-ratio is changed.
Fig. 13. Varying of the transmission zeros with respect to the Ratio.
TABLE II
COMPARISON OF THE DIMENSIONS OF DIFFERENT CASES
Related TO Fig. 12.
Fig. 12 shows the structure and parameters of the single dualmode cavity. ,
are the length of minor axis and major axis, respectively. Ratio is the ratio of the major axis and minor axis.
is the angle between the input and output ports.
and
are the width and the length of coupling aperture.
is set to 140
and the center frequency
is set to 400 GHz. The three subfigures shown in Fig. 13 could be achieved by adjusting the Ratio. Their dimensions are listed in Table II. The transmission zero shifts from the lower sideband to the upper sideband as the Ratio is decreasing monotonously. Meanwhile,
and
need to be fine-tuned to ensure that the center frequency is 400 GHz.
For more details of the elliptic cavity, the plot of the position of transmission zeros against the Ratio is shown in Fig. 13. Three curves represent the different angles , 120
, 140
, and 160
, respectively. The transmission zeros are almost unchanged while the Ratio is 1. Meanwhile, the positions of the transmission zeros change slowly while the Ratio is larger than 1.3. With the increasing of the angle
, the slope of the curves are decreasing. And the bandwidth of the filter is getting larger and the stopband rejection is getting worse while the

This article has been accepted for inclusion in a future issue of this journal. Content is final as presented, with the exception of pagination.
6 |
|
|
|
IEEE TRANSACTIONS ON TERAHERTZ SCIENCE AND TECHNOLOGY |
||
|
|
|
|
|
|
|
|
|
|
|
|
|
|
|
|
|
|
|
|
|
|
|
|
|
|
|
|
|
|
|
|
|
|
|
Fig. 14. Structure and the parameters of the bandpass filter.
TABLE III
PARAMETERS OF THE PROPOSED FILTER
Fig. 15. X-ray photograph of the proposed bandpass filter.
Related to Fig. 14.
is increasing. On the other hand, too small will result in the difficulty of the fabrication because the input and the output ports are too close to each other. It should be emphasized that all the points in Fig. 13 have been optimized and the center frequencies are 400 GHz.
With this feature of the elliptic cavity, a dual-mode bandpass filter cascaded by two cavities are shown in Fig. 14. The two ellipticcavitieshavedifferentAR,therefore,atransmissionzero on each side of the passband could be obtained, as shown in Fig. 16. The other transmission zeros at the upper frequency band are caused by the higher modes in the elliptic cavities. The full-wave simulation is carried out by the HFSS. The center frequency is around 400 GHz, and the optimized dimensions are listed in Table III. The bended waveguides on both sides of the cavities are used to make sure that the input and output ports are on the same axis. This can simplify the structure of the test fixture and facilitate the measurement. Fig. 15 is the X-ray photograph of the proposed bandpass filter.
B. Filter Results
The simulated and measured results of the proposed filter are shown in Fig. 16. The simulation is carried out with smooth gold, and the conductivity is set to 3.3e7 S/m [4]. The simulated 3 dB bandwidth is 8.05%, from 383.9 to 416.1 GHz, while the measured 3-dB bandwidth is 7.52%, from 380.2 to 409.9 GHz. A small frequency offset happens due to the taper angle of the lateral wall. The insertion loss is 0.39 dB and 2.84 dB for the simulated and the measured results, respectively. According to the above-mentioned analysis, adding the surface roughness, taper angle 1.46 of the lateral walls and the shifts to the simulation model and re-simulate it. The surface ratio and nodule radius are set to 4 and 0.5
m, respectively, and the shift in
-di- rection is set to 5
m. The resimulated and measured results are shown in Fig. 17. Two curves match very well with each other, which shows that our simulation analysis method is accurate. The measured results have been averaged for 20 times, therefore it is much smoother than [11]. Moreover, the insertion loss
Fig. 16. Comparison of the simulated results and the measured results of the bandpass filter.
Fig. 17. Comparison of the resimulated results and the measured results of the bandpass filter.
of the filterincludes the loss coming from the bended waveguide at both sides of the cavities.
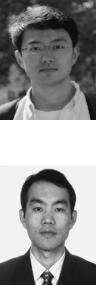
This article has been accepted for inclusion in a future issue of this journal. Content is final as presented, with the exception of pagination.
ZHUANG et al.: SILICON MICROMACHINED TERAHERTZ BANDPASS FILTER WITH ELLIPTIC CAVITIES |
7 |
V. CONCLUSION
This paper presents the design of a bandpass filter cascaded by ellipticcavitiesatWR-2.2bandand thelosspropertyanalysis of the fabricated waveguide and filter. The DRIE dry etching technique and a three layers structure are used for the fabrication. The obtained taper angle of the lateral walls is about 1.46. An 8-mm straight waveguide is fabricated and measured. The approximate unit length loss is 0.144 dB/mm@400 GHz, and the loss of the waveguide is analyzed in detail. Then a simulation analysis method for the loss property including the factors of surface roughness, dimension errors and the misalignment of the connecting ports is summarized. The proposed filter is cascaded by two elliptic cavities which transmission zero could be adjusted by changing the ratio of the major and minor axes. The measured 3 dB bandwidth of the filter is 7.52%, from 380.2 to 409.9 GHz, and the measured insertion loss is 2.84 dB, including extra waveguide of about 4.5 mm at the input and output ports. Using the summarized analysis method, the re-simulated and the measured results of the filters could match very well with each other.
The presented results shows that the DRIE process is suitable for the WR-2.2 band with the proper layer structure. The future work will focus on the design of the MEMS antennas and the integration of the passive components and the terahertz chips.
REFERENCES
[1]Y. Wang, M. L. Ke, M. J. Lancaster, and J. Chen, “Micromachined 300 GHz SU8 based slotted waveguide antenna,” IEEE Antennas Wireless Propag. Lett., vol. 10, pp. 573–576, 2011.
[2]X. Shang, M. J. Lancaster, M. Ke, and Y. Wang, “Measurements of micromachined submillimter waveguide circuits,” in Proc. 76th ARFTG Microw. Meas. Conf., 2010, pp. 1–4.
[3]X. Shang, M. Ke, Y. Wang, and M. J. Lancaster, “WR-3 band waveguides and filters fabricated using SU8 photoresist micromachining technology,” IEEE Trans. THz Sci. Technol., vol. 2, no. 6, pp. 477–487, Nov. 2012.
[4]L. Chen, A. Arsenovic, J. R. Stanec, T. J. Reck, A. W. Lichtenberger, R. M. Weikle, II, and N. S. Barker, “A micromachined terahertz waveguide 90 twist,” IEEE Microw. Wireless Compon. Lett., vol. 21, no. 5, pp. 234–236, May 2011.
[5]J. R. Stanec and N. S. Barker, “Fabrication and integration of micromachined millimeter-wave circuits,” IEEE Microw. Wireless Compon. Lett., vol. 21, no. 8, pp. 409–411, Aug. 2011.
[6]S. Biber et al., “Design and measurement of a 600 GHz micromachined Horn antenna manufactured by combined DRIE and KOH-etching of silicon,” in Proc. 16th Int. Symp. Space THz Technol., Goteborg, Sweden, 2005, pp. 507–512.
[7]Y. Li, P. Kirby, and J. Papapolymerou, “Silicon micromachined W band folded and straight waveguides using DRIE technique,” in IEEE MTT-S Int. Microw. Symp. Dig., Jun. 2006, pp. 1915–1918.
[8]Y. Li, P. L. Kirby, O. Offranc, and J. Papapolymerou, “Silicon micromachined -band hybrid coupler and power divider using DRIE technique,” IEEE Microw. Wireless Compon. Lett., vol. 18, no. 1, pp. 22–24, Jan. 2008.
[9]T. J. Reck, C. Jung-Kubiak, J. Gill, and G. Chattopadhyay, “Measurement of silicon micromachined waveguide components at 500 to 750 GHz,” IEEE Trans. THz Sci. Technol., vol. 4, no. 1, pp. 33–38, Jan. 2014.
[10]H. J. Tang, W. Hong, G. Q. Yang, and J. X. Chen, “Silicon based THz antenna and filter with MEMS process,” in Proc. Int. Workshop Antenna Technol, Mar. 2011, pp. 148–151.
[11]L. Sevillano, T. J. Reck, C. Jung-Kubiak, G. Chattopadhyay, J. A. RuizCruz, J. Montejo-Garai, and J. Rebollar, “Silicon micromachined canonical E-plane and H -plane bandpass filters at the terahertz band,”
IEEE Microw. Wireless Compon. Lett., vol. 23, no. 6, pp. 288–290, Jun. 2013.
[12]M. Vahidpour and K. Sarabandi, “Micromachined J-band rectangular waveguide filter,” in Proc. XXXth URSI General Assembly Scientific Symp., Aug. 2011, pp. 1–4.
[13]J. Hu, S. Xie, and Y. Zhang, “Micromachined terahertz rectangular waveguide band pass filter on silicon-substrate,” IEEE Microw. Wireless Compon. Lett., vol. 22, no. 12, pp. 636–638, Dec. 2012.
[14]K. Leong, K. Hennig, C. Zhang, R. Elmadjian, Z. Zhou, B. Gorospe, P. Chang-Chien, V. Radisic, and W. Deal, “WR-1.5 silicon micromachined waveguide components and active circuit integration methodology,” IEEE Trans. Microw. Theory Techn., vol. 60, no. 4, pp. 998–1005, Apr. 2012.
[15]X. H. Zhao, J. F. Bao, G. C. Shan, Y. J. Du, Y. B. Zheng, Y. Wen, and C. H. Shek, “D-band micromachined silicon rectangular waveguide filter,” IEEE Microw. Wireless Compon. Lett., vol. 22, no. 5, pp. 230–232, May 2011.
[16]P. L. Kirby, D. Pukala, H. Manohara, I. Mehdi, and J. Papapolymerou, “A micromachined 400 GHz rectangular waveguide and 3-pole bandpass filter on a silicon substrate,” in IEEE MTT-S Int. Dig., Jun. 2004, pp. 1185–1188.
[17]P. Kirby, D. Pukala, H. Manohara, I. Mehdi, and J. Papapolymerou, “Characterization of micromachined silicon rectangular waveguide at 400 GHz,” IEEE Microw. Wireless Compon. Lett., vol. 16, no. 6, pp. 366–368, Jun. 2006.
[18]D. Meledin et al., “A 1.3-THz balanced waveguide HEB mixer for the APEX telescope,” IEEE Trans. Microw, Theory Techn., vol. 57, no. 1, pp. 89–98, Jan. 2009.
[19]L. Accatino, G. Bertin, and M. Mongiardo, “Elliptic cavity resonators for dual-mode narrowband filters,” IEEE Trans. Microw. Theory Techn., vol. 45, no. 12, pp. 2393–2401, Dec. 1997.
[20]H. Tang, W. Hong, J. Chen, G. Q. Luo, and K. Wu, “Development of millimeter-wave planar diplexers based on complementary characters of dual-mode substrate integrated waveguide filters with circular and elliptic cavities,” IEEE Trans. Microw. Theory Techn., vol. 55, no. 4, pp. 776–782, Apr. 2007.
[21]H. J. Tang, W. Hong, Z. C. Hao, J. X. Chen, and K. Wu, “Optimal design of compact millimetre-wave SIW circular cavity filters,” Electron. Lett., vol. 41, no. 19, pp. 1068–1069, Sep. 2005.
[22]S. H. Hall, S. G. Pytel, P. G. Huray, D. Hua, A. Moonshiram, G. Brist, and E. Sijercic, “Multi-GHz, causal transmission line modeling methodology with a hemispherical surface roughness approach,” IEEE Trans. Microw. Theory Techn., vol. 55, no. 12, pp. 2614–2624, Dec. 2007.
[23]U. Rosenberg and S. Amari, “Novel design possibilities for dual-mode filters without intracavity couplings,” IEEE Microw. Wireless Compon. Lett., vol. 12, no. 8, pp. 296–298, Aug. 2002.
[24]M. Guglielmi, P. Jarry, E. Kerherve, O. Roquebrun, and D. Schmitt, “A new family of all-inductive dual-mode filters,” IEEE Trans. Microw. Theory Techn., vol. 49, no. 10, pp. 1764–1769, Oct. 2001.
Jian-xing Zhuang (S'13) was born in Hubei Province, China, in 1988. He received the B.S. degree from XiDian University, Xi'an, China, in 2011. He is currently working toward the Ph.D. degree at Southeast University, Nanjing, China.
His research interests include material characterization, millimeter-wave, and terahertz passive devices and antennas.
Zhang-Cheng Hao (M'08) received the B.S. degree in microwave engineering from XiDian University, Xi'an, China, in 1997, and the M.S. degree and Ph.D. degree in radio engineering from Southeast University, Nanjing, China, in 2002 and 2006, respectively.
In 2006, he was a Postdoctoral Researcher with the Laboratory of Electronics and Systems for Telecommunications, École Nationale Supérieure des Télécommunications de Bretagne, Bretagne, France, where he was involved with developing millimeter-wave antennas. In 2007, he joined the
Department of Electrical, Electronic and Computer Engineering, Heriot-Watt University, Edinburgh, U.K., as a Research Associate, where he was involved

This article has been accepted for inclusion in a future issue of this journal. Content is final as presented, with the exception of pagination.
8
with developing multilayer integrated circuits and ultra-wide-band components. In 2011, he joined the School of Information Science and Engineering, Southeast University, Nanjing China as a professor. He holds 20 granted patents and has authored or coauthored over 80 referred journal and conference papers. His current research interests involve microwave and millimeter-wave systems, submillimeter-wave and terahertz components and passive circuits, including filters, antenna arrays, couplers and multiplexers.
Dr. Hao has served as the reviewer for many technique journals, including
the IEEE TRANSACTIONS ON MICROWAVE THEORY AND TECHNIQUES and the IEEE MICROWAVE WIRELESS COMPONENTS LETTERS. He was the recipient of the Thousands of Young Talents presented by China government in 2011 and the High Level Innovative and Entrepreneurial Talent presented by Jiangsu Province, China in 2012.
IEEE TRANSACTIONS ON TERAHERTZ SCIENCE AND TECHNOLOGY
Wei Hong (M'92–SM'07–F'12) received the B.S. degree from the University of Information Engineering, Zhengzhou, China, in 1982, and the M.S. and Ph.D. degrees from Southeast University, Nanjing, China, in 1985 and 1988, respectively, all in radio engineering.
Since 1988, he has been with the State Key Laboratory of Millimeter Waves where he has served as Director of the lab since 2003, and is currently a Professor and Vice-Dean of the School of Information Science and Engineering, Southeast University. In
1993 and 1995–1998, he was a short-term Visiting Scholar with the University of California at Berkeley and at Santa Cruz, respectively. He has been engaged in numerical methods for electromagnetic problems, millimeter-wave theory and technology, antennas, RF technology for wireless communications, etc. He has authored and coauthored over 300 technical publications and two books.
Dr. Hong is a Fellow of CIE and an AdCom Member of the IEEE Microwave Theory and Techniques Society (MTT-S), Vice-President of the CIE Microwave Society and CIE Antenna Society, and Chairperson of IEEE MTT-S/APS/EMC-S Joint Nanjing Chapter. He served as an associate editor for the IEEE TRANSACTIONS ON MICROWAVE THEORY TECHNIQUES during 2007–2010 and served as the editorial board member for IJAP, China Communications, and Chinese Science Bulletin. He was a three-time recipient of the first-class Science and Technology Progress Prizes issued by the Ministry of Education of China and Jiangsu Province Government and was a recipient of the Foundations for China Distinguished Young Investigators and for the “Innovation Group” issued by the National Science Foundation of China.