
диафрагмированные волноводные фильтры / 8b47ca52-bcf8-42de-88d8-fd3900231a76
.pdf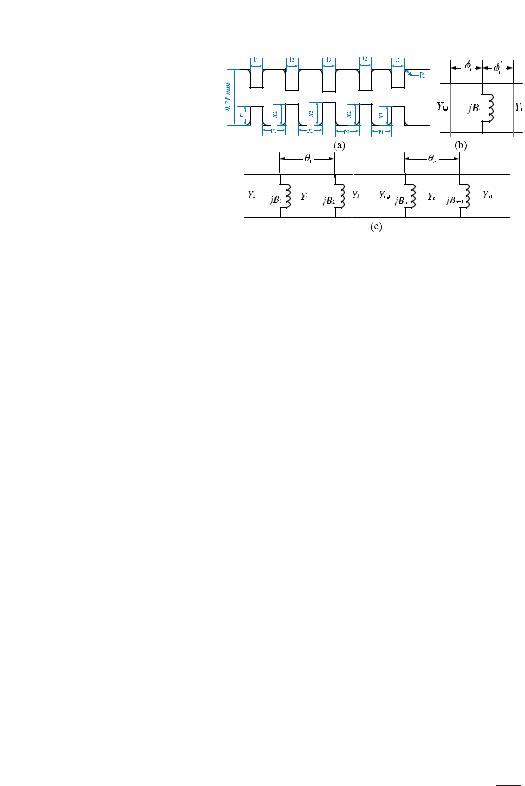
This article has been accepted for inclusion in a future issue of this journal. Content is final as presented, with the exception of pagination.
IEEE MICROWAVE AND WIRELESS COMPONENTS LETTERS |
1 |
A Low-Loss Design of Bandpass Filter
at the Terahertz Band
Naibo Zhang, Ruiliang Song, Mingjun Hu, Guangcun Shan, Chunting Wang, and Jun Yang
Abstract— This letter demonstrates a terahertz (THz) bandpass filter with a center frequency of 340 GHz, low insertion loss of−0.6 dB, and bandwidth of 5.3%. The diaphragm thickness is quantitatively analyzed to obtain accurate filter parameters based on equivalent circuit and diaphragm coupling in THz band for the first time, and the simulation results based on calculated filter parameters show that diaphragm thickness has great influence on the filter performance. The test results show a good agreement with the theoretical analysis and simulation results. Meanwhile, the relationship between fabrication error and insertion loss was discussed and a quantitative mathematical model is given. The filter also shows an excellent performance when compared with the performance of other filters from the current literature reports.
Index Terms— Bandpass filter, terahertz (THz) filter.
I. INTRODUCTION
THERE is a growing interest in terahertz (THz) components in the frequency from 300 GHz to 10 THz for potential applications in security scanning, medical imag-
ing, and ultrafast wireless communications [1]. In general, design and fabrication are widely studied for THz filters. In design methods, these techniques can be roughly divided into three categories: waveguide structure [1], [2], metamaterial structure, and frequency selected surface (FSS) [3]. Meta-material structure filter and FSS filters are a candidates of THz filter, which exhibits insertion loss <1 dB at 700 GHz under experimental measurement [3]. However, due to the simple resonant structure, the stopband rejection of mesh filter is imperfect, and hard to integrate with waveguide module and sensitive to installation and environment. Apart from the filter styles and fabrication methods, the parameters of filter structures are studied in [4]–[6], which are designed based on H-ladder rectangle waveguide. Compared with the general rectangular cavity filter design, the THz filter needs to consider the thickness of the filter diaphragm accurately, so that the thickness cannot be ignored like the filter design in the lowfrequency band. This is because the length of the resonator
Manuscript received February 6, 2018; revised March 18, 2018; accepted May 7, 2018. This work was supported in part by the National Natural Science Foundation of China under Grant 61504124 and in part by the National Defense Science and Technology Innovation Special Zone Fund under Grant 00402901. (Corresponding authors: Naibo Zhang and Mingjun Hu.)
N. Zhang, R. Song, and C. Wang are with the Beijing R&D Center, The 54th Research Institute, China Electronics Technology Group Corporation, Beijing 100070, China (e-mail: zhangnaibai@163.com).
M. Hu and G. Shan are with the College of Materials Science and Engineering, Beihang University, Beijing 100191, China (e-mail: mingjunhu@buaa.edu.cn).
J. Yang is with the Department of Mechanical and Materials Engineering, Western University, London, ON N6A 3K7, Canada.
Color versions of one or more of the figures in this paper are available online at http://ieeexplore.ieee.org.
Digital Object Identifier 10.1109/LMWC.2018.2835650
Fig. 1. (a) Top view of bandpass filter. (b) Reactance coupled circuit diagram.
(c) Equivalent circuit of H-ladder waveguide bandpass filter (n = 4).
and the thickness of the diaphragm are at the same order of magnitude. In [6], it is inaccurate to calculate the length of the resonator, which calculated the half of diaphragm thickness as the resonator length directly, but the parameters obtained by such algorithm are unable to achieve a good performance.
The filter insertion loss is mainly caused by two aspects: 1) the surface metal loss (the Q value) and 2) the matching of each structural parameter. Compared with [2]–[7], this letter mainly considers the matching of filter structure parameters, especially about diaphragm thickness, so as to get low insertion loss, and the metal loss did not be reduced in this letter. The matching among parameters is the key to obtain low insertion loss, and the accurate calculation of diaphragm thickness is an important way to obtain the parameters and their matching. In this letter, a special parameter was introduced for the diaphragm thickness calculation, and the results show a good performance.
II. DESIGN
The transmission line theory was used for analyzing and calculating the filter structure parameters: diaphragm thickness (t ), diaphragm width (x ), and resonator length (P).
A. Theoretical Analysis
Fig. 1(a) shows the top view of the rectangle waveguide filter. Fig. 1(b) shows the reactance coupled circuit diagram, and Fig. 1(c) shows the equivalent circuit of H-ladder waveguide bandpass filter (n = 4), which was used for analyzing the rectangle waveguide filter. The electrical length (θi ) is as follows:
θi |
= |
π |
+ |
φi |
+ |
φi 1 |
= |
π |
+ |
1 |
arc tan |
ui |
+ |
arc tan |
ui+1 |
|
2 |
2 |
2 |
|
|
||||||||||||
|
|
+ |
2 |
2 |
|
(1)
1531-1309 © 2018 IEEE. Personal use is permitted, but republication/redistribution requires IEEE permission. See http://www.ieee.org/publications_standards/publications/rights/index.html for more information.

This article has been accepted for inclusion in a future issue of this journal. Content is final as presented, with the exception of pagination.
2 |
IEEE MICROWAVE AND WIRELESS COMPONENTS LETTERS |
where ui = Bi+1/Yi , Bi is the junction susceptance, Yi is the characteristic wave admittances, and ϕi is the electrical length of filter unit cavity. In this letter, the relative bandwidth (BW) is designed as 5.3%, the attenuation is 35 dB when the frequency is equal to f0 · (1 ± 10%), where f0 is the center frequency, the voltage standing-wave ratio ρ in passband is designed as 1.02, and four-order resonators were used for the filter. The order impedances (Zi ) of every diaphragm (ti ) in Fig. 1(a) are Z0 = 1 (input), Z1 = 5.613, Z2 = 0.0875, Z3 = 27.2, Z4 = 0.1817, and Z5 = 1.02 (output), respectively. And then, the voltage standing-wave ratio (ρi ) of every order diaphragm were
ρ1 |
= ρ5 |
= Z1/Z0 |
= 5.613 |
|
ρ2 |
= ρ4 |
= Z1/Z2 |
= 64.15, and ρ3 = Z3/Z2 = 310.86. |
(2) |
Bi /Y0 can be expressed as |
|
|||
|
B1/Y0 = B5/Y0 = 1.95 |
|
||
|
B2/Y0 = B4/Y0 = 7.88, and B3/Y0 = 17.57. |
(3) |
According to (1), the electrical length (θi ) and length of resonators (li ) can be calculated as
θ1 = 150.015(l1 = 0.53 mm) and θ2 = 169.63(l2 = 0.598 mm).
(4)
However, l1 and l2 are different from conventional resonator length; in this letter, the thickness of diaphragm (t ) needs to be considered for resonator length, since diaphragm (t ) is about (1/20) · li (1/5) · li (30–100 μm) and cannot be ignored [5], and l1 and l2 are expressed as
l1 = P1 + 1 · t1/2 + 2 · t2/2
and
l2 = P2 + 2 · t2/2 + 3 · t3/2 |
(5) |
where 1, 2, and 3 are correction factors. In this letter, t1, t2, and t3 are defined as 40, 60, and 40 μm, respectively.
The wavelength of rectangular waveguide (λ0) equals to 1.27mm [8], the wavelength of desired center frequency (λ0 340 GHz) is 0.882 mm, and a = 710 μm. According to
(3) and (6), (Bi /Y0) · (a/λg ) is about 1.09, 4.41, and 9.84, where i = 1, 2, and 3. And then checked form in [5], di /a is 0.51, 0.38, and 0.32, respectively. So, d1 = d5 = 0.36 mm,
d2 = d4 = 0.27 mm, and d3 = 0.23 mm, where di = a−2xi . When i ·ti decreases, the coupling between resonators
decreases, and then di is increased to balance the coupling coefficient. In other word, i · ti and di are inverse relations
1 · t1 · d1 = C1, 2 · t2d2 = C2, and 3 · t3 · d3 = C3. (6)
To ensure the determined band signals pass without reflections, it is defined that C1, C2, and C3 equals to a constant and are all equal, then defined that P1 = 0.44 mm, R value in Fig. 1(a) is 50 μm. According to (5) and (6), the parameters can be calculated as 1 = 1.77, 2 = 1.48, 3 = 2.77, P2 = 0.492 mm, x1 = 0.17 mm, x2 = 0.22 mm, and x3 = 0.24 mm.
B. Simulation
The filter is design as: center frequency f0 = 340 GHz, BW = 18 GHz, return loss < −20 dB, rejection loss (at 300 GHz) RL = 45 dB, and four-pole Chebyshev. When t2 = 0.06 mm, P1 = 0.44 mm, and P2 = 0.5 mm (optimized
Fig. 2. (a) RF performances of filter when t1 and t3 change from 0.04 to 0.06 mm. (b) RF performances of filter when t2 changes from 0.04 to 0.06 mm.
Fig. 3. 340-GHz filter appearance structure. (a) Magnifying diagram of the filter structure. (b) Fabricated filter structure.
by HFSS), t1(= t3) changes from 0.04 to 0.06 mm; the performances are shown in Fig. 2(a). In Fig. 2(a), when t1 and t3 increased, the return loss decreases (the performance changes worse), and the center frequency f0 and BW keep constant.
When t1 = 0.04 mm, P1 = 0.44 mm, and P2 = 0.5 mm, t2 changes from 0.04 to 0.06 mm, the performances are shown
in Fig. 2(b). When t2 increased, the return loss increases (changes better), and the center frequency and BW keep constant. The reason of return loss changes is that the structures t1, t2, and t3 affected the coupling coefficient of the filter, but resonator length was changed little. This shows that t mainly affects the return loss and insertion loss.
III. MEASUREMENT AND DISCUSSION
In this letter, the waveguide (WR-2.8) components are combined by two identical halves in E-plane. The bulk material is copper and the surface material is gold. The measurement is carried out by Agilent vector network analyzer av3672b, and control module av3640a with two frequency extenders av3649. The through-reflect-line calibration is used during the measurement. The flanges (WR-2.2 UG-387/UM) on the extenders were used to connect the test fixture and fixed by screws.
A. Measurement
The fabricated THz filters are shown in Fig. 3, the length of the filter structure is 2.12 mm, and the length of the filter after encapsulation is 22.12 mm. The measurement setup connector is WR-2.2 waveguide; Fig. 4(a) shows the comparison between simulated and measured results. Because the measurement setup connector is WR-2.2 and the filter connector is WR-2.8, the return loss above and below the passband has a large ripple component that passes through 0 several times. The fabrication error is 5 μm tested by metallurgical microscope. Fig. 4(b) shows the expanded view of S21 in Fig. 4(a), which shows−0.6 dB of measured result in passband.
B. Discussion
There are two main factors determining insertion loss, quality factor (Q), and the structure parameters matching, and the quality factor (Q) is determined by surface roughness.

This article has been accepted for inclusion in a future issue of this journal. Content is final as presented, with the exception of pagination.
ZHANG et al.: LOW-LOSS DESIGN OF BANDPASS FILTER AT THz BAND |
3 |
TABLE I
COMPARISON OF DIFFERENT TYPES THZ FILTERS
Fig. 4. S-parameters tested by connector WR-2.2. (a) Measurement results in 5-μm fabrication accuracy. (b) Expanded view of S21.
Fig. 5. Relationship between fabrication error and filter insertion loss in passband.
The insertion loss IL can be expressed as |
|
|||||
IL |
= |
f (Qu , k) |
= |
k · f0 |
gi |
(7) |
|
||||||
|
|
B W · Qu |
|
where Qu is the quality factor with no load, k is the correction factor, BW is the bandwidth, and gi is the resonator numbers. Qu is determined by roughness of metal surface, and k is determined by the structure parameters matching, when all parameters matched perfectly, k = 4.343.
1) Surface Roughness: Gold layer ( 2.5 μm) is electroplated for the filter surface. In this letter, the Huray model is chosen to simulate the roughness of the gold layer [3]. The conductivity of electroplated gold film (3.96 × 107 S/m) is less than that of bulk gold, and the surface roughness of electroplated gold film also results in less conductive sidewalls. The height between peak and valley in the surface
is hpeak−valley, and the max distance between adjacent peaks is dpeak. In this letter, dpeak is set as 9.4 μm, hpeak−valley is 200 nm tested by step tester, and the insertion loss is
0.3 dB [7]. The insertion loss mainly caused by the surface metal resistance (22 mm) is 0.3 dB, and then the waveguide loss is 0.013 dB/mm.
2) Structure Parameter Matching: When fabrication errors are reconsidered in design, which is adjusting each parameter individually, the insertion loss will increase when fabrication error increases. For instance, the original parameter values of the filter were obtained by (1)–(6), when P2 = 0.492 mm,
x1 = 0.17 mm, x2 = 0.22 mm, x3 = 0.24 mm, d1 = d5 = 0.36 mm, d2 = d4 = 0.27 mm, d3 = 0.23 mm, and R = 50 μm, respectively, all parameters increase by z μm
(z = 1, 2, 3, 4, 5, 6, …), and the insertion loss is obtained by simulation, which are shown in Fig. 5. The function between fabrication error and filter insertion loss in passband is fit as (7)
IL |
1 |
= |
Ae f (x ) |
+ |
B, f (x ) |
= − |
(x + 0.09)2 |
|
(8) |
|
243.7 |
||||||||||
|
|
|
|
|
||||||
where IL1 |
is |
the filter insertion loss in bandpass, x is |
||||||||
the fabrication |
error, A |
= −2.92, and B = 3.06. |
From |
Fig. 5 and (8), the relationship between IL1 and x is an exponential form. The insertion loss is 0.3 dB when fabrication error is 5 μm, and k is equal to 4.8 according to (8).
Table I shows recently published THz waveguide filters, FFS filters, and meta-material filters. It is observed that the previously published filters could not provide such filter with low insertion loss and high return loss. Compared with the bandpass filters with the same center frequency, rectangle waveguide, and CNC milling in [2], the filter in this letter shows a much better performances than the performances in [2]. When compared with [3] with almost the same center frequency and BW, the differences are fabrication and filter structures; the proposed filter in this letter shows a lower insertion loss and a higher return loss in passband.
IV. CONCLUSION
This letter presents a bandpass filter with a center frequency of 340 GHz and 0.6-dB insertion loss, which is cascaded by rectangle cavities at WR-2.8 band. The fabrication and measurement setups are presented, and the parameters of the filter are analyzed to obtain a good filter performance. The measured results with a 5-μm fabrication error show a good agreement with simulation results, and the performances show a center frequency of 340 GHz, insertion loss of 0.6 dB, return loss of 20 dB, and BW of 18 GHz.
REFERENCES
[1]X. Shang, M. Ke, Y. Wang, and M. J. Lancaster, “WR-3 band waveguides and filters fabricated using SU8 photoresist micromachining technology,” IEEE Trans. THz Sci. Technol., vol. 2, no. 6, pp. 629–637, Nov. 2012.
[2]C. Wang et al., “0.34-THz wireless link based on high-order modulation for future wireless local area network applications,” IEEE Trans. THz Sci. Technol., vol. 4, no. 1, pp. 75–85, Jan. 2014.
[3]J.-X. Zhuang, Z.-C. Hao, and W. Hong, “Silicon micromachined terahertz bandpass filter with elliptic cavities,” IEEE Trans. THz Sci. Technol., vol. 5, no. 6, pp. 1040–1047, Nov. 2015.
[4]M. Vahidpour and K. Sarabandi, “Micromachined J-band rectangular waveguide filter,” in Proc. Gen. Assem. Sci. Symp., Aug. 2011, pp. 1–4.
[5]G. L. Matthaei, L. Young, and E. M. T. Jones, Microwave Filters, Impedance-Matching Networks, and Coupling Structures. New York, NY, USA: McGraw-Hill, 1964.
[6]W. Cheng, L. Bin, L. Jie, and D. Xianjin, “140 GHz waveguide H ladder bandpass filter,” in Proc. Int. Conf. Microw. Millim. Wave Technol., May 2012, pp. 1–4.
[7]S. Hall et al., “Multigigahertz causal transmission line modeling methodology using a 3-D hemispherical surface roughness approach,”
IEEE Trans. Microw. Theory Techn., vol. 55, no. 12, pp. 2614–2624, Dec. 2007.