
Контрольная_Работа_990241_Кириленко
.pdfМинистерство образования Республики Беларусь
Учреждение образования БЕЛОРУССКИЙ ГОСУДАРСТВЕННЫЙ УНИВЕРСИТЕТ
ИНФОРМАТИКИ И РАДИОЭЛЕКТРОНИКИ
Факультет компьютерного проектирования Кафедра электронной техники и технологии
Дисциплина «Проектирование и производство изделий интегральной электроники»
КОНТРОЛЬНАЯ РАБОТА
Студент: Кириленко Г. Б.
ст. гр. 990241
Руководитель: старший преподаватель кафедры Телеш Е. В.
2023
Содержание
1.Технология осаждения боросиликатного стекла…………………………3
2.Маршрутный процесс формирования КМДП-структуры…………….….6
3.Список использованных источников…………………………………….18
2
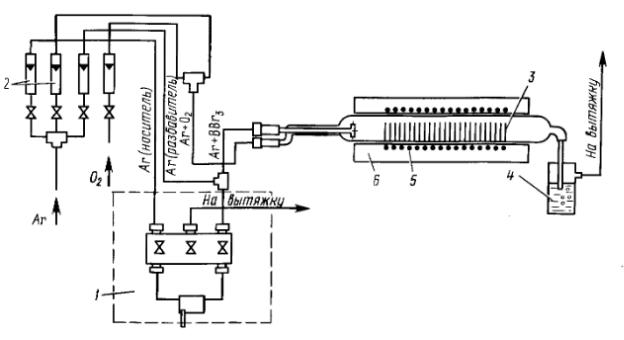
Технология осаждения боросиликатного стекла
Тонкие пленки боросиликатного стекла выполняют роль диэлектрика в МДП-приборах и изолятора в многоуровневой разводке, защищают поверхность полупроводника от внешних воздействий. Пленки боросиликатного стекла служат источниками диффундирующих примесей.
Традиционным методом осаждения окислов бора является процесс получения из сильно разбавленной инертным газом газовой смеси их галогенидов с кислородом при нормальном давлении. Осаждение основано на протекании химической реакций:
4ВВr3 + 3O2 = 2В2O3 + 6Вr2
и проводится в диффузионной печи, т. е. в кварцевом горизонтальном цилиндрическом реакторе с горячими стенками (рис. 1). Температура осаждения 800...1100 °С. Часть окислов бора при этих температурах восстанавливается кремнием: B2O3 + Si → SiO2 + B. При указанных температурах окислы находятся в состоянии, близком к температуре размягчения и перемешиваясь, образуют БСС (В2О3).
Рис. 1. Схема реактора осаждения боросиликатного стекла на поверхности полупроводниковых пластин: 1 – термостатированный блок испарителей ВВr3; 2 – ротаметры; 3 – пластины; 4 – жидкостный затвор; 5 – нагреватель; 6 – однозонная печь.
Таким образом, осаждают на пластины источники диффузии бора при локальном легировании кремния в процессах формирования структур
3
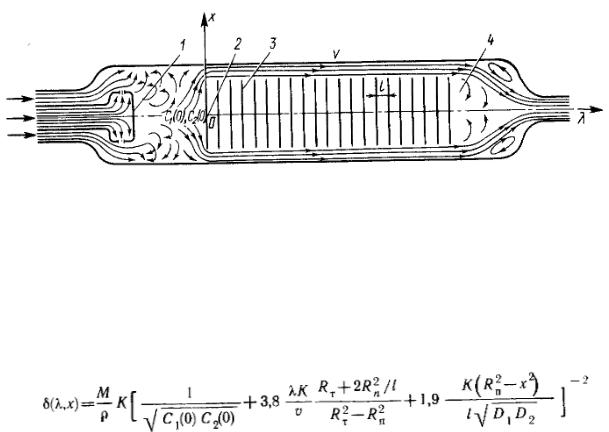
полупроводниковых приборов. Характер движения газового потока в диффузионном реакторе показан, на рис. 2.
Рис. 2. Схема горизонтального кварцевого цилиндрического реактора для осаждения БСС: 1 – смеситель; 2 – начало зоны осаждения; 3 – полупроводниковые пластины; 4 – конец зоны осаждения.
Взазор между пластинами компоненты газовой смеси поступают диффузионным путем. Скорость осаждения δ пленки боросиликатного стекла определяется формулой:
Вформулу входят параметры, определяющие кинетику реакции взаимодействия ВВr3 + О2: исходные концентрации реагентов в газовой фазе в начале зоны осаждения C1(0) и С2(0), константа скорости химической реакции К, средняя скорость газового потока в зазоре между стенками трубы и краями кремниевых пластин υ (см. рис. 2), коэффициенты диффузии реагентов в зазоре между пластинами D1 и D2. В неявном виде, через зависимости константы скорости химической реакции и коэффициентов диффузии от температуры, эта формула содержит зависимость скорости осаждения от температуры проведения процесса осаждения. В нее входят геометрические и конструктивные характеристики процесса осаждения: радиус пластин RП; радиус трубы реактора RТ; расстояние между пластинами l. Входят и физические константы осаждаемого окисла В2О3: р – плотность и М – молекулярная масса В2О3. Формула дает зависимость скорости осаждения пленки, а следовательно, и ее толщины h за время осаждения t (h = δt) от положения пластины относительно начала зоны осаждения λ и, в пределах этой пластины, от расстояния до ее центра х.
Толщина пленки БСС, осажденной таким способом, оказывается неравномерной. Она уменьшается от края к центру каждой пластины (рис. 3, а) и от первой пластины, стоящей в начале зоны осаждения, к последней, стоящей в конце зоны (рис. 3, б). Неравномерность тем меньше, чем ниже
произведение концентраций реагирующих веществ, т. е. чем больше
4
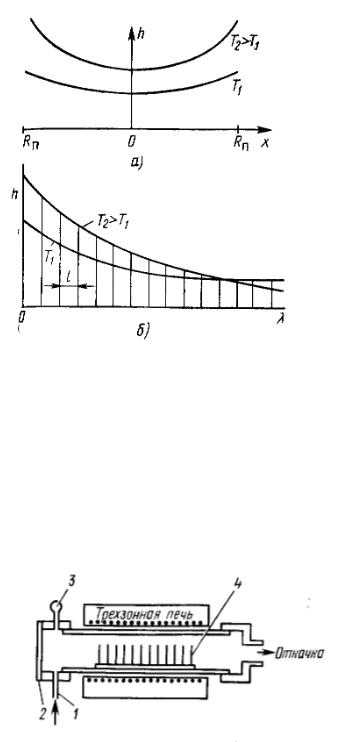
разбавление реакционной смеси инертным газом (Ar), чем ниже температура осаждения и больше расстояние между пластинами и скорость движения реакционной смеси в реакторе.
Рис. 3. Изменение толщины пленки осажденного БСС по диаметру пластины (а) и по партии пластин (б) при двух различных температурах осаждения.
Однородность осажденных таким методом пленок повышается, если процесс проводить не при нормальном, а при пониженном давлении (уменьшается исходная концентрация реагентов). Фактически только в процессах осаждения при пониженном давлении (10… 100 пА) удалось получить хорошее качество и равномерность по толщине ППК. Для этих процессов созданы специальные реакторы (Рис. 4) с регулируемым профилем температуры вдоль зоны осаждения.
Рис. 4. Конструкция реактора для осаждения пленок из газовой фазы при пониженном давлении: 1 – поступление реакционной газовой среды; 2 – шлюз; 3 – манометр; 4 – пластины.
5
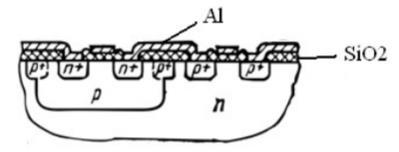
Маршрутный процесс формирования КМДП-структуры
1.Формирование партии пластин. Предусматривает подготовку партий по 25 пластин и их маркировку на установке лазерной маркировки «Импульс». Рабочий пластины 100 КЭС-0,01(111) толщиной 330 мкм.
2.Гидромеханическая отмывка. Предназначена для удаления механических загрязнений с помощью деионизованной воды марки А на линии "Кубок". Включает: очистку - 25 с, промывку 1-10 с, промывку 11-15 с; сушку-10 с.
3.Химическая обработка. Удаление органических и неорганических загрязнений в перекисно-аммиачном растворе при Т=750С, 10 мин. с последующей отмывкой в деионизованной воде.
4.Контроль качества химобработки. Производится невооружённым глазом и под микроскопом ММУ-3 или МИМ-7 при увеличении >240 крат.
Невооружённым глазом:
• рабочая поверхность пластин должна быть чистой;
• без пятен;
• подтёков;
• разводов и грязных полос.
Под микроскопом в темном и светлом полях в 5-ти точках не допускается:
• более 2-х светящихся точек;
• мелкая сыпь под скрытым слоем;
• структурные дефекты, которые светятся в темном поле и не исчезают
всветлом.
5.Окисление высокотемпературное (окисление I). Создание маскирующего защитного слоя SiO2. Операция проводится в несколько этапов:
6
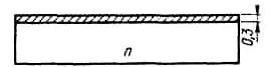
N" |
Наименовани |
Температура, |
Время, |
Состав, расход |
|
|
п/п |
е этапа |
°С |
мин. |
газа, л/ч |
Оборудование |
|
|
|
|
|
|
|
|
1 |
Загрузка |
900 |
10 |
сух.О2/НСl(15) |
|
|
2 |
Выдержка |
900 |
10 |
–"– |
Электропечь |
|
3 |
Нагрев |
до 1000 |
10 |
вл.O2/HCl(15) |
||
диффузионная |
||||||
4 |
Окисление |
1000 |
60 |
–"– |
||
СДОМ |
||||||
5 |
Выдержка |
1000 |
10 |
сух. О2 |
||
|
||||||
6 |
Охлаждение |
до 900 |
20 |
–"– |
|
|
7 |
Выгрузка |
900 |
10 |
–"– |
|
Толщина оксида - 0,3 мкм. Загрузка - 200 пластин.
6. Контроль после окисления (или диффузии). Производится в 5-ти точках в темном поле при ув.>240 крат под микроскопом ММ У -3 (МИМ-7).
Не допускается:
•в поле зрения более 5-ти светящихся точек;
•структурные дефекты, которые светятся в тёмном поле и не исчезают
всветлом;
•неравномерный цвет окисла в местах соприкосновения пластины с кассетой;
•мелкая сыпь в местах разделительных дорожек;
•дефекты фотолитографии (островки окисла);
•наличие мелкой сыпи по всей поверхности пластины;
•мелкая сыпь в коллекторных и эмиттерных окнах.
7. Фотолитография "Карман". Предназначена для формирования окон в маскирующей плёнке фоторезиста для последующего ионного легирования бором через слои SiO2 и фоторезиста с целью создания р-областей. Используется автомат для нанесения фоторезиста 0.8 ФМ-75/2-002 и установка совмещения и экспонирования ЭМ-584 или ЭМ-584А:
• Марка фоторезиста |
ФП-РН-7 |
• Скорость вращения центрифуги, об/мин |
1500-10000 |
• Температура сушки, °С |
90-110 |
• Время сушки, мин |
6 |
• Температура задубливания, °С |
120-140 |
• Время задубливания, мин |
6-8 |
• Толщина плёнки фоторезиста, мкм |
0,8 |
• Время экспонирования при осв. 50000 лк, с |
20 |
• Время проявления, с |
10 |
7

Проявление производится с помощью 0.5% раствора КОН на автомате проявления фоторезиста 0.8ФП-75-4.
8.Ионное легирование бором. Доза - 2мкКл/см2, Е=100КэВ. На установке "Везувий-5".
9.Травление оксида кремния. Операция служит для удаление оксида с незащищённых фоторезистом участков. Проводится на установке химической обработки в травителе HF+Н2О.
Промывка в деионизованной воде 2 минуты до достижения удельного сопротивления воды на выходе из ванны р >3МОм∙см. Сушка 3 мни. при скорости вращения центрифуги 1000 об/мин.
10.Снятие фоторезиста. Удаление защитной маски фоторезиста после создания в пленке оксида рисунка требуемой конфигурации. Производится на установке химической обработки в травителе H2SO4+NH4NO3 (10:1) последовательно в двух ваннах: t1 = 7 мин. t2 = 3 мин. с последующей промывкой деионизованной водой в трехкаскадной ванне, t3 = 3мин. в каждом отсеке. Дополнительная отмывка 2 мин.
Сушка 3 мин. при скорости центрифуги 1000 об/мин.
11.Контроль пластин после фотолитографии. Производится на установке визуального контроля по двум диаметрам перпендикулярно базовому срезу.
Контролируется:
• чистота поверхности;
• качество травления;
• неровность края;
• качество совмещения;
• линейные размеры вскрытых областей и металлизированных дорожек.
12.Химобработка пластин. (См. п.3).
13.Контроль химобработки. (См. п.4).
14.Высокотемпературная обработка. (Окисление II). Операция предназначена для разгонки примесей в р-кармане и создания оксидной маски требуемой толщины.
N" |
Температура, |
Время, |
Состав, расход |
|
|
газа, |
Оборудование |
||||
п/п |
°С |
мин |
|||
л/ч |
|
||||
|
|
|
|
||
1 |
700 |
30 |
сух. О2/НСl |
Электропечь |
|
2 |
1000 |
20 |
–"– |
||
диффузионная |
|||||
3 |
1150 |
50 |
–"– |
||
СДОМ |
|||||
4 |
700 |
50 |
–"– |
||
|
8
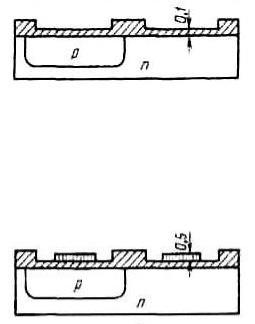
15.Снятие окисла (только с контрольных пластин). Линия "Ку6ок".
16.Измерение удельного сопротивления. Измерение производится на приборе ЦИУС-3; RS=2.6-2.8 кОм/□.
17.Определение толщины легированного слоя (р-кармана). Измерения проводятся на установке "Шар-Шлиф" с последующим травлением в хромовом травителе в течение 10 с. Толщина р-слоя h=1.0-1.4мкм.
Хромовый травитель: HNO3+HF+H2O+Cr(NO3)2.
18.Высокотемпературная обработка пластин (окисление III под нитрид). Операция предназначена для создания защитного слоя SiO2 на поверхности Si пластин для компенсации механических напряжений между Si и Si3N4. Операция проводится в несколько этапов:
N" |
Температура, |
Время, |
Состав, расход |
Оборудование |
°С |
мин |
газа, |
|
|
п/п |
|
|||
|
|
л/ч |
|
|
|
|
|
|
|
1 |
700 |
10 |
сух.О2/НСl(15) |
Электропечь |
2 |
1000 |
15 |
вл.O2/HCl(15) |
диффузионная |
3 |
1000 |
40 |
сух. О2(40-60) |
СДОМ |
Толщина окисла 0.05 - 0.1 мкм. 3агрузка - 200 пластин.
19.Наращивание нитрида кремния. Операция формирования плёнки Si3N4 осуществляется на установках "Планит" при пониженном давлении в парогазовой смеси (ПГС): SiCl2+HN4. Операция предназначена для формирования диэлектрического покрытия на поверхности SiO2, служащего для защиты поверхности Si в процессе создания изоляции локальным окислом hSi3N4 = 0.2 - 0.5 мкм.
20.Измерение толщины плёнки. Измерение толщины пленки нитрида кремния проводится на спектрофотометре фирмы Leitz: MPV-SP1.
21.Химическая обработка. (См. п.3).
22.Контроль качества химобработки. (См. п.4).Допускается оставить не более 30-ти дефектов по диаметру пластины, перпендикулярному базовому срезу.
Контроль осуществляется на трёх пластинах из 6-ти рабочих при увеличении 250 крат на микроскопе ММУ-3.
9

23. Фотолитография II (охрана - n +). Операция служит для создания рельефа фоторезистора требуемой конфигурации:
•обработка пластин в парах ГМДС (гексаметилдисилозан), затем нанесение фоторезиста h = 1.1 мкм;
•сушка Т1 = 80 °С, Т2 = 90 °С, T3 = 105 °С, t = 10 мин.;
•экспонирование на установке совмещения и экспонирования ЭМ-584
(ЭМ-584А, ЭМ-586 и ЭМ-5084);
•проявление в 0.9%-ном растворе KOH в течение 40с;
•задубливание фоторезиста от Т=85°С до 105°С в течение 8 мин. Операция проводится на установках линии "Лада-125".
24. Плазмохимическое травление нитрида (диэлектрика). Операция
служит для получения разделительных изолирующих областей в Si3N4 и проводится на установке плазмохимического травления "Плазма-Планар" в среде "Хладона-218" (C3F8).
25. Снятие фоторезиста с пластин. Операция проводится в два этапа:
•снятие фоторезиста в кислородной плазме (t = 15 - 25 мин.) на установке плазмохимического травления "Плазма-600";
•доснятие фоторезиста в жидкостном травителе "КАРО"
(H2SO4+H2O2).
26.Контроль пластин после фотолитографии. Контроль проводится под микроскопом ММУ-3 (ММР-3) в светлом поле микроскопа при ув.>250 крат. Не допускается более 18% дефектных модулей. Не должно быть: пятен, подтёков, остатков фоторезиста.
27.Химическая обработка. (См. п.3). Линия "Кубок", t=10-12мин.,
Т=75±5°С.
28.Контроль качества химобработки. (См. п.4). Допускается не более 10 светящихся точек над активными областями. Микроскоп ММУ-3.
29.Ионное легирование фосфором. Введение фосфора во вскрытые области с целью формирования охраны n+-областей "охранные кольца" (подлегирование подложки) Д = 0.15 мкКл/см2, Е = КэВ. Установка "Везувий-5".
30.Химическая обработка. Линия "Кубок", перекисно-аммиачный раствор, t = 10 – 15 мин, Т = 75±5 °С.
10