
КР ПУТО
.pdfМинистерство образования Республики Беларусь
Учреждение образования
«БЕЛОРУССКИЙ ГОСУДАРСТВЕННЫЙ УНИВЕРСИТЕТ
ИНФОРМАТИКИ И РАДИОЭЛЕКТРОНИКИ»
Контрольная работа
по дисциплине «Программно-управляемое технологическое
оборудование»
Вариант № 16
Выполнил: Студентка 5-го курса заочного отделения группы Ромашкина А.П.
Гр. 990241
Минск, БГУИР 2023
|
Содержание |
|
1. |
Резистивный нагрев ........................................................................... |
3 |
2. |
Гидростатические преобразователи для измерения вакуума .......... |
9 |
3. |
Эжекторные и диффузионные насосы ............................................ |
20 |
Список литературы .................................................................................. |
25 |
2
1. Резистивный нагрев
Нагрев электропроводящего тела, обладающего высоким электрическим сопротивлением при прохождении через него электрического тока, называют резистивным. При этом, как правило, используют переменный ток. Согласно закону Джоуля — Ленца
Q = UIt = U2tIR = I2 Rt. |
(1.1) |
Для выделения тепла в твердом проводнике можно использовать постоянный и переменный электрический ток. Применение постоянного тока затруднено и экономически невыгодно из-за отсутствия источников (генераторов) большой силы тока и низкого напряжения, которые необходимы для выделения тепла в твердом проводнике, обладающем высокой электропроводностью. [1]
Способность переменного тока к трансформации позволяет получать требуемые напряжения. При переменном токе под сопротивлением проводника понимают активное сопротивление, которое больше сопротивления проводника постоянному току. Это объясняется наличием скин-эффекта, влияние которого возрастает с увеличением частоты f, диаметра проводника d, магнитной проницаемости μ и падает с ростом электрического сопротивления p.
Достоинства резистивного нагрева - высокий КПД, низкая стоимость оборудования, безопасность в работе (низкое напряжение на зажимах) и малые габаритные размеры. Факторами, ограничивающими применение испарителей с резистивным нагревом, являются возможность загрязнения наносимой пленки материалом нагревателя, а также малый ресурс работы из-за старения (разрушения) нагревателя, что требует его периодической (иногда довольно частой) замены. [2]
Испарители этого типа различных конструктивных вариантов могут быть с непосредственным или с косвенным нагревом испаряемого вещества.
В испарителях с непосредственным нагревом ток в несколько десятков ампер проходит непосредственно через испаряемый материал. Такой метод испарения может быть применен только для сублимирующихся металлов, т.е. металлов, температура плавления которых выше температуры испарения (хром, титан и др.).
Основное достоинство этих испарителей - отсутствие теплового контакта между их нагретыми элементами и испаряемым металлом, что обеспечивает высокую чистоту наносимой пленки. Однако они обеспечивают низкую скорость испарения, дают возможность испарять малое количество материала, который может быть использован только в виде ленты или проволоки, а также не позволяют испарять диэлектрики и большинство металлов. Сечение таких испарителей должно быть одинаковым на всем протяжении, иначе в месте утонения возникает перегрев и они перегорают.
3
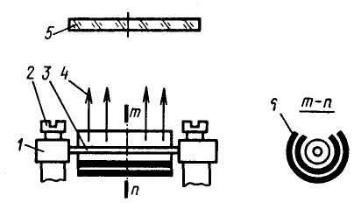
Испаритель с резистивным непосредственным нагревом показан на рисунке 1. Испаряемый материал 3 в виде проволоки или ленты вставляют в изготавливаемые из титана или нержавеющей стали и закрепляемые винтами 2 массивные контактные зажимы 1, к которым подводится электропитание. Для снижения тепловых потерь за счет излучения, а также ограничения потока пара 4 в направлении к подложке 5 служит многослойный экран 6.
1 - контактный зажим, 2 - винт, 3 - испаряемый материал, 4 - поток пара, 5 - подложка, 6 - многослойный экран
Рисунок 1 – Испаритель с резистивным непосредственным нагревом
Проволочные испарители применяют для испарения веществ, которые смачивают материал нагревателя. При этом расплавленное вещество силами поверхностного натяжения удерживается в виде капли на проволочном нагревателе. Проволочные испарители изготавливаются V - и W-образной формы, а также спирале - и волнообразной.
Проволочный испаритель простейшей конструкции (Рисунок 2, а) используют для нанесения пленок алюминия, который хорошо смачивает вольфрамовый проволочный нагреватель - цилиндрическую проволочную спираль 2. Испаряемое вещество в виде скобочек (гусариков) 3 навешивают на спираль, которую отогнутыми концами 1 вставляют в контактные зажимы. По мере нагрева это вещество плавится и формируется на проволоке в виде капель. Снизу размещаются тепловой и ограничивающий экраны. Проволочные испарители предназначены для создания протяженного потока испаряемого материала, что достигается использованием одновременно нескольких навесок.
Наибольшее практическое распространение получили поверхностные, лодочные и тигельные, испарители прямого нагрева. В тиглях такого типа вещество помещают в лодочку, которая нагревается проходящим током. Такие испарители отличаются дешевизной, простотой изготовления и удобством эксплуатации.
Остановимся на наиболее распространенных поверхностных испарителях.
4
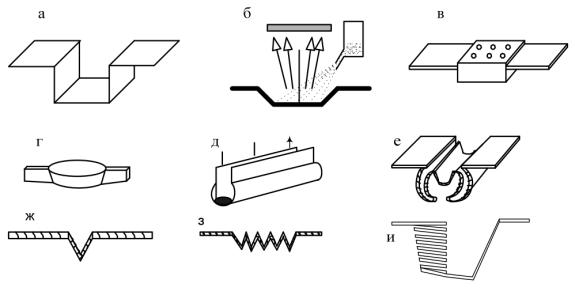
Поверхностные испарители изготовляются в виде лент, лодочек (рис. 2 а, г), а также проволочек из металлов с высокой температурой плавления и низким давлением паров (рис. 2 ж-и). Лодочки применяются для испарения широкого класса материалов: сульфидов и фторидов металлов, элементарных металлов и других веществ. Для испарения материалов, характеризующихся выбросом вещества, применяются лодочки, закрытые экранами с отверстиями, расположенными в шахматном порядке (рис. 2 в). Для испарения диэлектриков и металлов в больших количествах рекомендуется лодочка, изображенная на рис. 2 г. С изменением конструкции лодочек (рис. 2 д, е) обеспечивается узкая направленность потока пара.
Выбор конструкции испарителя зависит от того, в каком состоянии находится испаряемый материал (гранулы, слитки, порошок, проволока), а также от таких особенностей испарения вещества, как испарение из жидкой фазы или сублимация, смачиваемость испарителя, химическая активность к материалу испарителя и т.д.
При испарении веществ сложного состава и сплавов нередко один из компонентов является более летучим, что приводит к нарушению стехиометрии осаждаемого слоя. Для предотвращения этого применяют метод взрывного испарения. Порошкообразное вещество из вибробункера (рис. 2 б) малыми дозами поступает на разогретый испаритель и моментально испаряется с последующей конденсацией на приемной поверхности. Режим испарения, размер фракции, скорость подачи вещества и температура испарителя для получения пленок стехиометрического состава определяют эмпирически.
Рисунок 2 – Типы поверхностных испарителей прямого нагрева
Одним из недостатков испарителей в виде открытых лодочек является нагрев испаряемого вещества снизу, следствием чего нередко бывает разбрызгивание вещества из лодочки. Еще одно неудобство поверхностных испарителей заключается в том, что по мере испарения материала изменяется
5
индикатриса направленности. Естественно, это приводит к искажению спектров деталей на разных участках. В меньшей степени этот недостаток сказывается при испарении из расплава. Для предотвращения разбрызгивания вещества и стабилизации индикатрисы испарения некоторые исследователи предлагали закрывать поверхность тигля частично прозрачной сеткой. Так, например, автором данного учебника был предложен вариант лодочного испарителя, свободный от большинства перечисленных выше недостатков. Идея заключалась в том, что разогрев вещества происходит не снизу, со дна испарителя, а сверху. На поверхность тигля накладывается дополнительная сетка, выполненная из фольги, толщина которой больше толщины фольги, из которой выполнен испаритель. Это приводит к перегреву верхней части тигля. Величина перегрева контролируется толщиной фольги для дополнительной сетки. Реально использовался перегрев в (100-300)º С. В этом случае испарение вещества идет из замкнутой камеры между веществом и верхней сеткой, что обеспечивает постоянство индикатрисы излучения и отсутствия брызг из тигля. Наконец, толщина слоя остается постоянной при постоянстве тока, протекающего через тигель.
Материалами для проволочных и ленточных испарителей являются тугоплавкие металлы с высокими температурами плавления и низким давлением паров. Наиболее широко применяются вольфрам, молибден и тантал. Температуры плавления для этих металлов 3380º С, 2610º С и 3000º С соответственно.
Тигельные испарители (тигли) применяются в том случае, когда для нанесения слоев требуются большие количества материала. В качестве материала тигля выбирается такой, чтобы собственное давление паров тигля во время работы было пренебрежимо мало по сравнению с давлением испаряемого вещества. Часто это достигается путем дополнительного охлаждения тигля, который выполняется из материала с высокой теплопроводностью: меди, вольфрама, графита и т.д. Тигли для испарения могут быть изготовлены из металлов, графита, стеклоуглерода (стеклографита), нитрида бора, из тугоплавких окислов. Тигли из молибдена, например, используются для испарения Сu, Аg, Аu. Для испарения веществ, которые активно вступают в реакцию с тугоплавкими металлами, применяют тигли, изготовленные по керамической технологии из окислов. Обычно это тугоплавкие окислы ThO2, BeO, ZrO2, Al2O3, MgO, TiO2. Из керамических тиглей испаряют Sb, Аs, Вi, Те, Мn, Тe и другие элементы. Нагрев тиглей осуществляется за счет теплового излучения раскаленной нити, выполненной из тугоплавкого металла.
По конструкции испарители тигельного типа разделяются на открытые (обычно как на рис. 3) и замкнутые, дискретного действия, конструкция которых сугубо индивидуальна. Существенным недостатком испарителей тигельного и поверхностного типа являются потери испаряемого материала, пар из испарителя выходит, когда заслонка закрыта, и осаждение слоя не производится. От этого недостатка свободны замкнутые испарители
6
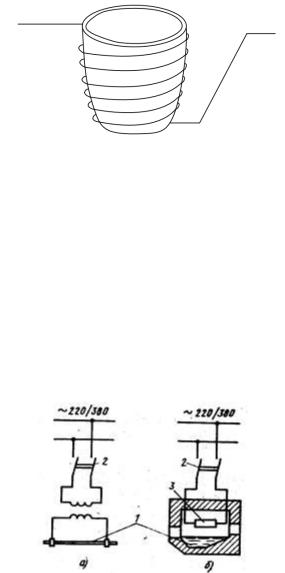
дискретного действия. Пар из этих испарителей выходит только тогда, когда поднят затвор, и в этот период производится осаждение материала на подложку. Инерционность подобных испарителей в 20—30 раз меньше, чем у резистивных испарителей с экраном. [2]
Рисунок 3 – Испарители с косвенным нагревом
Впечах сопротивления прямого нагрева ток подводится непосредственно к нагреваемому изделию. При расчете электрических параметров нагрева необходимо учитывать изменение в процессе нагрева сопротивления материала.
Впечах сопротивления косвенного нагрева в качестве рабочего тела используют специальные нагреватели, выполненные из высокоомных жаропрочных материалов. При этом передача тепла нагреваемому изделию осуществляется излучением. На рис. ниже показаны схемы печей сопротивления.
Рисунок 4 – Схемы электрических печей сопротивления: а — прямой нагрев; б — косвенный нагрев; 1 — нагреваемый материал; 2 — выключатель или магнитный пускатель; 3 —- электронагревательный элемент
В печах прямого нагрева достигается наибольшая эффективность, резистивного нагрева при значительной скорости и достаточной равномерности нагрева по сечению изделия.
Преимуществами печей сопротивления косвенного нагрева являются простота регулирования температуры и получения требуемого распределения температуры в печи. Материал нагревательного элемента должен обладать: возможно большим удельным электрическим сопротивлением, возможно
7
меньшим температурным коэффициентом сопротивления, высокой жаропрочностью, стойкостью к окислению, легкостью обработки и невысокой стоимостью. Для металлических нагревателей применяют сплавы на основе никеля, хрома, железа и алюминия, отличающиеся большим удельным электрическим сопротивлением при сравнительно малых температурных коэффициентах сопротивления. В печах с температурой 1000—1100° используют нихром (20% Сr и 80% Ni), мало подверженный окислению при высоких температурах за счет образования на поверхности тонкой и прочной защитной пленки окиси хрома.
Нагревательные элементы изготавливают из проволоки или ленты. Проволочные нагреватели обычно выполняют из проволоки диаметром d=2— 8 мм. Средний диаметр спиралей из нихрома D=(5— 8)d. Шаг намотки h принимают равным (2— 4)d, так как при малом шаге происходит взаимное экранирование витков. Длину спирали L и число витков при известной длине проволоки l определяют по формулам
L = /h/(πD); n= 103 L/h. |
(1.2) |
Нагревательные элементы обычно изготовляют из лент толщиной а=1-2 мм и шириной b= (8—12)a.
Расчет нагревательных элементов включает выбор типа, количества и материала нагревательных элементов, определение их геометрических размеров и размещение внутри печи. Исходными данными для расчета являются суммарная мощность печи (Р), напряжение питания (U), размеры печи и ее рабочая температура.
Расчет необходимой мощности нагревателей проводится на основе данных теплового расчета по уравнению P=Qk, где Q — суммарный расход тепла в печи в единицу времени, Вт; k — коэффициент неучтенных потерь.
Для периодически работающих печей k =l,4 - l,5, для печей непрерывного действия k = 1,2-1,3. Расчет нагревательных элементов начинают с выбора материала для их изготовления по величине конечной температуры нагреваемого изделия, причем допустимая температура материала должна быть на 50—200°С больше конечной температуры. [1]
8
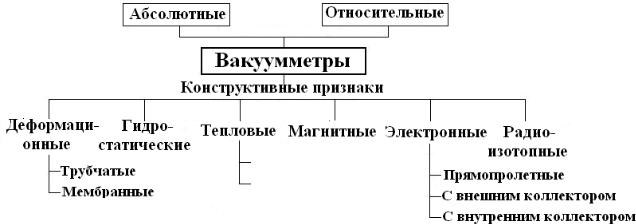
2. Гидростатические преобразователи для измерения вакуума
Область давлений, используемая в современной вакуумной технике, 105–10–12Па. Измерение давлений в таком широком диапазоне не может быть обеспечено одним прибором. На практике при измерении давления разреженных газов применяются различные типы преобразователей, отличающиеся по принципу действия и классу точности.
Приборы для измерения общих давлений в вакуумной технике называют вакуумметрами. Они обычно состоят из двух частей: манометрического преобразователя и измерительной установки. По методу измерения вакуумметры подразделяются на абсолютные и относительные (рис. 5). Показания абсолютных приборов не зависят от рода газа и могут быть заранее рассчитаны. В приборах для относительных измерений используют зависимость параметров некоторых физических процессов, протекающих в вакууме, от давления. Вакуумметры измеряют общее давление газов, присутствующих в вакуумной системе.
Термопарные
Преобразователи
сопротивления
Рисунок 5 – Классификация вакуумметров для измерения общих давлений
На рис. 6 показаны диапазоны давлений, измеряемые тем или иным видом манометрического преобразователя.
9

Рисунок 6 – Диапазоны давлений, измеряемых различными манометрическими преобразователями
К деформационным преобразователям относятся трубчатые и мембранные преобразователи. Трубка Бурдона – простейший деформационный преобразователь в виде спиральной трубки, скручивающейся под действием атмосферного давления в случае откачки внутренней полости за счет разных радиусов кривизны, а следовательно, и площадей наружной и внутренней поверхности трубки. В основу мембранных преобразователей положено изменение величины прогиба мембраны под действием давления. Диапазон изменения мембранных преобразователей 105– 10–1Па, но т. к. линейность показаний сохраняется только при небольших деформациях мембраны, то один прибор может измерять давления в пределах 2–3 порядков [3].
Простейшими гидростатическими преобразователями являются жидкостные манометры с открытым или закрытым коленом. Манометры с открытым коленом удобны для измерения давлений, близких к атмосферному. Показания такого манометра зависят от атмосферного давления, в отличие от преобразователей с закрытым коленом.
Действие этих манометров основано на изменении разности уровней жидкости в сообщающихся сосудах в зависимости от давления газов над поверхностью жидкости в этих сосудах.
Простейший U-образный манометр представляет собой изогнутую трубку, заполненную до половины высоты рабочей жидкостью. Трубка одним концом сообщается с атмосферой, а другим с измеряемой средой. Полученные результаты при температуре t следует привести к 0° С для ртути (или к 4° С для воды). Если рабочей жидкостью служит вода или спирт, то отсчет
10