
10532
.pdf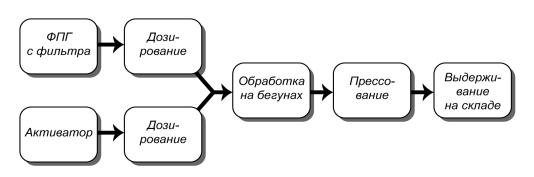
60
Влажность образцов через 24 часа хранения на воздухе составила 8,5 %, что позволяет исключить их сушку. Слеживания при хранении гранул на воздухе в течение 24 ч не наблюдалось.
Исследования, проведенные в лабораторных и опытно-промышленных условиях, показали, что предложенная технология может быть использована для производства из ФПГ как гранул, так и стеновых камней и блоков. Технологическая схема производства приведена на рис. 2.15.
Рис. 2.15 – Технологическая схема прессования ФПГ
2.4.2. Производство гранул методом пластического формования
Преимуществом метода пластического формования (на ленточном прессе) является более высокая производительность и надежность формовочного оборудования. Испытания показали, что для эффективной работы ленточного пресса необходимо, чтобы масса перед формованием имела пластическую прочность, равную приблизительно 0,07 МПа.
Влияние влажности формовочной смеси на её пластическую
прочность
Определена зависимость пластической прочности формовочных смесей, состоящих из сухого фосфополугидрата ВАЗ, от В/Т. Расход воды изменяли с таким расчетом, чтобы получить смеси с влажностью 10, 20, 30, 40 и 50 %. Определение пластической прочности проведено с использованием конического пластометра МГУ. Результаты исследований приведены в табл. 2.12.
С повышением влажности смеси её пластическая прочность сначала растет, а затем начинает снижаться. Рост пластической прочности связан с адсорбцией воды и слипанием зерен твердых фаз (жидкостное прилипание, по
61
Б.В. Дерягину). После достижения оптимума появляется свободная вода, что приводит к снижению пластической прочности смеси. Из табл. 2.12 также следует, что пластическая прочность исследованных смесей при изменении их влажности от 10 до 30 % (т.е. в пределах, характерных для фосфополугидрата ВАЗ) значительно ниже, чем у промышленных керамических масс.
Таблица 2.12 – Влияние влажности смеси на ее пластическую прочность
Влажность, % |
10 |
20 |
30 |
40 |
50 |
|
|
|
|
|
|
Пластическая |
|
|
|
|
|
прочность, |
0,013 |
0,015 |
0,016 |
0,020 |
0,010 |
МПа |
|
|
|
|
|
|
|
|
|
|
|
В лабораторных и опытно-промышленных условиях при формовании смесей с влажностью от 10 до 40 % после прохождения мундштука пресса масса рассыпалась (т. е. не обладала необходимой связностью). С повышением влажности (более 40 %) формовочная смесь становилась текучей.
Как было отмечено ранее, недостаточная связность и низкая пластическая прочность формовочных смесей обусловлена особенностями зернового состава попутного продукта ВАЗ, который является сравнительно грубодисперсным относительно монофракционным продуктом. Следовательно, формование гранул из фосфополугидрата ВАЗ невозможно без предварительной подготовки.
Известно, что при постоянном В/Т с увеличением дисперсности системы пластическая прочность формовочных смесей растет. С целью повышения пластической прочности и связности формовочных смесей нами вводилась добавка – пыль электрофильтров. Расход добавки изменяли в пределах от 5− 30 % от массы сухого фосфополугидрата. Ранее было установлено, что без механохимической активации введение добавки менее 5 % нецелесообразно. При изготовлении и испытании проб значения В/Т приняты равными 0,1; 0,2; 0,3; 0,4.
62
Исследования показали, что для получения формовочной массы с пластической прочностью 0,07 МПа необходимо ввести добавку-активатор в количестве 15− 17 % от массы сухого фосфополугидрата. Максимальная пластическая прочность достигается при расходе добавки – 20 – 28 %. При этом формовочная смесь имеет достаточную связность. Водоотделения при испытании не наблюдалось. Содержание химически связанной воды через одни сутки хранения формовочной массы над водой повысилось от 6,6 до 10,5– 13,0 % в зависимости от значения В/Т смеси. Как было отмечено ранее, повышение содержания в гранулах добавки-активатора нежелательно в связи с уменьшением содержания в них сульфата кальция. С целью снижения расхода добавки-активатора при формовании гранул на ленточном прессе намиопределено влияние механохимической активации фосфополугидрата на пластическую прочность формовочной смеси.
Влияние механохимической активации на пластическую прочность
формовочных смесей
Формовочную смесь, состоящую из сухого фосфополугидрата ВАЗ, пыли электрофильтров вращающихся печей и воды, обрабатывали на бегунах в течение 15 мин, т.к. при более длительной обработке начинается образование крупных агрегатов. Расход воды затворения был принят равным 20 % массы сухих твердых компонентов, что соответствует среднему значению влажности остатка на фильтре в условиях ВАЗ. Расход добавки-активатора был принят равным 3 % массы сухого попутного продукта. В процессе обработки через определенные промежутки времени были отобраны пробы и определена пластическая прочность формовочной смеси. В дальнейшем кювету со смесью хранили в эксикаторе над водой при температуре 20 °C в течение 2 ч с целью определения изменения пластической прочности при хранении. Результаты испытаний приведены в табл. 2.13.
Из табл. 2.13 следует, что пластическая прочность формовочных смесей растет с увеличением продолжительности механохимической активации и хранения пробы. Варьируя время обработки смеси на бегунах, а также
63
продолжительность последующего хранения, можно регулировать реологические свойства формовочной смеси и получить смеси, пригодные для формования на ленточном прессе. Например, пластическая прочность формовочной массы, равная 0,070–0,075 МПа, достигается через 8– 9 мин обработки смеси на бегунах или после 5 мин обработки с последующим хранением смеси в течение 40– 50 мин. Это позволяет при производстве гранул методом пластического формования определить оптимальную продолжительность обработки на бегунах и последующего хранения с учетом минимальных затрат энергии.
Таблица 2.13 – Влияние механохимической активации на пластическую прочность формовочных смесей
Продолжительность |
Пластическая прочность активированных смесей, |
|||||
|
МПа, после хранения, мин |
|
||||
активации, мин |
|
|
||||
|
|
|
|
|
||
0 |
30 |
60 |
90 |
120 |
||
|
||||||
|
|
|
|
|
|
|
0 |
0,015 |
0,016 |
0,019 |
0,022 |
0,025 |
|
|
|
|
|
|
|
|
3 |
0,032 |
0,040 |
0,051 |
0,065 |
0,072 |
|
|
|
|
|
|
|
|
5 |
0,050 |
0,068 |
0,075 |
0,096 |
0,134 |
|
|
|
|
|
|
|
|
7 |
0,060 |
0,380 |
2,0 |
– |
– |
|
|
|
|
|
|
|
Вусловиях ЛЗКИ выпущена опытная партия гранул из фосфополугидрата на ленточном прессе, предназначенном для формования керамзита-сырца.
Взаводских условиях получены гранулы со следующей характеристикой: а) пластическая прочность смеси, МПа:
1)перед формованием – 0,06;
2)через 2 мин после формования – 0,07;
б) прочность при сжатии (через 24 ч после формования), МПа, — 10; в) содержание химически связанной воды, % от массы сухой смеси:
1)через 2 мин после формования – 9,2;
2)через 24 ч после формования – 15,7;
64
г) влажность гранул через 24 ч после формования, %, – 8,5; д) средняя плотность гранул, кг/м3, – 850–960.
Исследования, результаты которых приведены выше, показали, что для производства гранул и строительных изделий путем механической активации ФПГ можно использовать формовочное оборудование (ленточные прессы), которое применяется при производстве строительной керамики. Предложенная технологическая схема приведена выше (см. рис 2.15).
2.4.3. Влияние окускованного фосфополугидрата на свойства портландцемента
При производстве портландцемента фосфополугидрат рекомендуется использовать в качестве минерализатора с целью интенсификации процессов обжига сырья и как добавку при помоле клинкера портландцемента взамен природного гипсового камня для регулирования скорости процессов схватывания.
При введении в сырьевую смесь до 3 % фосфогипса (в пересчете на сухое вещество) повышается коэффициент насыщения смеси, улучшаются условия эксплуатации футеровки вращающихся печей. Одновременно отмечено, что растет производительность печей, а удельный расход топлива снижается на 1– 3 %.
Портландцемент, полученный совместным помолом клинкера и гранулированного фосфополугидрата, по активности незначительно отличается от портландцемента, содержащего природный гипс. Вместе с тем отмечается, что использование попутного продукта приводит к замедлению процессов схватывания цементного теста.
Известно, что образование полугидрата при помоле клинкера и гипса может привести к ускоренному (ложному) схватыванию цементного теста и бетонных смесей. Ложное схватывание цементного теста отмечено нами при введении фосфополугидрата. При производстве гранул из фосфополугидрата предусмотрен переход полуводного гипса в дигидрат. Превращение полугидрата в двуводный гипс начинается в процессе механохимической активации и заканчивается при хранении гранул на складе. При этом следует
65
предусмотреть возможность неполной гидратации полуводного гипса перед использованием гранулированного попутного продукта. При использовании гранул, содержащих полуводный гипс, это позволит сократить транспортные расходы за счет повышенного содержания сернокислого кальция в добавке. В связи с этим исследовано влияние гранулированного фосфополугидрата ВАЗ на свойства портландцемента.
2.4.3.1. Определение ложного схватывания портландцемента
Для проведения исследований гранулы получены методом пластического формования на лабораторном ленточном прессе. Перед формованием смесь из сухого фосфополугидрата, добавки и воды обработали на бегунах в течение 5 мин. Влажность смеси принята равной 20 %. В качестве добавки-активатора использована пыль электрофильтров вращающихся цементных печей в количестве 3 % массы сухого ФПГ.
Сразу после обработки на бегунах проведено гранулирование активированной смеси на ленточном прессе. Полученные гранулы хранились над водой при температуре 20 °C. Через определенные промежутки времени отобраны 5 проб гранул. Содержание химически связанной воды в отобранных пробах попутного продукта составило 10,0; 12,2; 14,0; 16,1; 19,5 % массы сухой смеси. В дальнейшем гранулы использованы при помоле клинкера портландцемента. Проба портландцемента была также получена совместным помолом клинкера цементного завода и фосфополугидрата ВАЗ, высушенного сразу после отбора проб с фильтра карусельного цеха экстракции. Содержание химически связанной воды в пробе составило 6,8 %. При изготовлении портландцемента использован клинкер Волховского цементного завода. Помол клинкера и добавки-регулятора произведен до удельной поверхности 0,30− 0,32 м2/г, характерной для портландцемента ВАЗ. Определение ложного схватывания выполнено по методике, разработанной Гипроцементом. Расход гранул при помоле был принят равным 5 % массы клинкера, в соответствии с расходом гипсового камня, принятым на Волховском цементном заводе. Результаты исследований приведены в табл. 2.14.
66
Таблица 2.14 – Влияние фазового состава попутного продукта на ложное схватывание портландцемента
Содержание химически |
6,8 |
10,0 |
12,2 |
14,0 |
16,1 |
19,5 |
связанной воды, % |
|
|
|
|
|
|
|
|
|
|
|
|
|
Ложное схватывание |
есть |
есть |
есть |
нет |
нет |
нет |
|
|
|
|
|
|
|
Из табл. 2.14 следует, что при наличии в гранулах до 30 % полуводного гипса ложное схватывание портландцемента не наблюдается, т.е. при производстве гранул полное превращение полуводного сульфата кальция в дигидрат не является обязательным.
2.4.3.2. Влияние гранулированного фосфополугидрата на технические свойства портландцемента
Портландцементы приготовлены помолом клинкера Волховского цементного завода и гранулированного фосфополугидрата. Гранулы получены методом пластического формования на ленточном прессе. В качестве добавокактиваторов при грануляции использованы пыль электрофильтров, пыль пылевой камеры вращающихся печей и зола-унос. Расход добавок-активаторов принят в соответствии с результатами исследований, приведенными ранее, и для различных активаторов составил 3− 8 % массы сухого фосфополугидрата. Содержание химически связанной воды в гранулированном попутном продукте перед помолом составило 14− 16 %, в зависимости от состава смеси. С целью определения влияния добавки на свойства портландцемента при помоле клинкера расход гранулированного фосфополугидрата был принят равным 3,5 и 7,0 % массы клинкера.
В табл. 2.15 приведены результаты определения нормальной густоты и сроков схватывания цементного теста. Для сравнения были приготовлены портландцементы с введением гипса Новомосковского месторождения в количестве 3; 5 и 7,0 % массы клинкера.
Из табл. 2.15 следует, что портландцементы, содержащие фосфополугидрат, по срокам схватывания незначительно отличаются от портландцементов, содержащих природный гипс. При этом отмечено, что пыль
67
электрофильтров несколько сокращает время начала и конца схватывания цементного теста.
Пыль пылевой камеры вращающихся печей и зола-унос увеличивают время конца схватывания, по сравнению с аналогичным показателем портландцемента, содержащего природный гипс. Сроки схватывания испытанных цементов находятся в пределах требований ГОСТ 310.
Использование гранулированного фосфополугидрата при помоле клинкера позволяет снизить водопотребность портландцемента по сравнению с вяжущим, содержащим природный гипс.
Таблица 2.15 – Нормальная густота и сроки схватывания портландцементов, содержащих фосфополугидрат и природный гипс
|
Расход |
Нормальная |
Сроки схватывания, |
||
Тип добавки |
гранул при |
|
ч-мин |
||
густота |
|
||||
помоле, |
|
||||
|
теста, % |
начало |
|
конец |
|
|
% |
|
|||
|
|
|
|||
|
|
|
|
|
|
Пыль пылевой камеры |
3 |
23,8 |
3-00 |
|
8-30 |
|
5 |
23,0 |
3-10 |
|
9-00 |
|
7 |
19,5 |
3-30 |
|
9-30 |
|
|
|
|
|
|
Пыль электрофильтров |
3 |
24,5 |
2-30 |
|
5-00 |
|
5 |
24,0 |
2-35 |
|
5-20 |
|
7 |
20,0 |
2-50 |
|
7-20 |
|
|
|
|
|
|
Зола-унос |
3 |
21,5 |
3-00 |
|
9-30 |
|
5 |
20,5 |
3-15 |
|
10-05 |
|
7 |
20,2 |
3-05 |
|
10-40 |
Гипс Новомосковского |
3 |
26,2 |
2-45 |
|
8-30 |
месторождения |
5 |
25,0 |
4-00 |
|
5-10 |
7 |
24,2 |
5-10 |
|
7-20 |
|
|
|
||||
|
|
|
|
|
|
Испытания стандартных образцов проведены через 1, 3, 7 и 28 суток хранения в нормальных условиях.
Результаты испытаний приведены в табл. 2.16. Из табл. 2.16 следует, что замена природного гипсового камня гранулированным фосфополугидратом замедляет процессы твердения портландцемента в первые трое суток хранения стандартных образцов в воде. Минимальную скорость твердения в ранние
68
сроки имеет портландцемент, содержащий фосфополугидрат, гранулированный с золой-уносом.
Таблица 2.16 – Зависимость прочности стандартных образцов от типа добавки и расхода гранул при помоле
Тип добавки |
Расход |
Предел прочности при |
Предел прочности при |
||||||||
|
|
гранул, |
изгибе, МПа, в возрасте, |
сжатии, МПа, в возрасте, |
|||||||
|
|
% |
|
сут |
|
|
|
|
сут |
|
|
|
|
|
1 |
3 |
7 |
28 |
1 |
3 |
|
7 |
28 |
Пыль |
пылевой |
3 |
1,2 |
4,9 |
5,9 |
6,6 |
17,5 |
27,0 |
|
27,0 |
34,0 |
камеры |
|
5 |
0,4 |
5,8 |
7,0 |
7,6 |
0,6 |
23,5 |
|
36,0 |
45,0 |
|
|
7 |
0,3 |
1,1 |
4,8 |
7,3 |
0,3 |
14,0 |
|
30,0 |
40,0 |
|
|
|
|
|
|
|
|
|
|
|
|
Пыль |
|
3 |
1,6 |
5,4 |
6,1 |
6,9 |
5,1 |
26,5 |
|
34,1 |
37,3 |
электрофильтров |
5 |
1,3 |
6,3 |
7,6 |
8,3 |
1,1 |
36,5 |
|
43,5 |
49,0 |
|
|
|
7 |
0,9 |
3,0 |
5,9 |
8,0 |
1,0 |
29,8 |
|
39,5 |
42,5 |
|
|
|
|
|
|
|
|
|
|
|
|
Зола– унос |
3 |
– |
4,3 |
6,0 |
6,0 |
– |
19,5 |
|
31,5 |
39,0 |
|
|
|
5 |
– |
5,6 |
7,0 |
7,35 |
– |
24,2 |
|
32,5 |
43,0 |
|
|
7 |
– |
3,9 |
6,0 |
6,15 |
– |
16,1 |
|
30,5 |
40,0 |
|
|
|
|
|
|
|
|
|
|
|
|
Гипс |
|
3 |
1,5 |
4,0 |
5,4 |
6,0 |
4,1 |
16,2 |
|
24,5 |
27,5 |
Новомосковского |
5 |
2,8 |
6,5 |
8,1 |
7,9 |
10,4 |
33,0 |
|
38,0 |
38,8 |
|
месторождения |
7 |
1,8 |
5,6 |
7,2 |
7,5 |
6,2 |
25,0 |
|
34,4 |
38,0 |
|
|
|
|
|||||||||
|
|
|
|
|
|
|
|
|
|
|
|
Через 1 сутки хранения над водой образцы-балочки разрушались при извлечении из формы. Через 28 суток хранения в воде предел прочности при сжатии образцов на основе портландцементов, содержащих фосфополугидрат, превышает прочность при сжатии образцов на основе портландцементов, полученных помолом клинкера с новомосковским гипсом, на 2,0–6,5 МПа. Из табл. 2.16 следует, что оптимальный расход гранулированного ФПГ при помоле, соответствующий максимальной прочности искусственного камня, составляет 5 % массы клинкера.
Исследовано влияние гранулированного фосфополугидрата на активность портландцемента при твердении стандартных образцов-балочек в воде в течение двух лет. С этой целью портландцемент приготовлен совместным помолом клинкера и гранулированного попутного продукта. Расход гранул и гипсового камня при помоле составил 5 % массы клинкера. Удельная
69
поверхность портландцемента принята равной 0,32 м2/г (метод воздухопроницаемости). В качестве добавки-активатора при гранулировании фосфополугидрата использована пыль электрофильтров вращающихся печей ВАЗ в количестве 3 % массы попутного продукта.
Через два года хранения активность портландцемента, содержащего попутный продукт, приблизительно на 7 МПа стала выше активности цемента, полученного помолом клинкера с природным гипсовым камнем.
Исследовано также влияние типа гипсосодержащего компонента на пластическую прочность цементного теста. Пластическая прочность определена на коническом пластометре МГУ. Цементное тесто нормальной густоты сразу после приготовления имеет пластическую прочность 0,01–0,02 МПа; в момент наступления начала схватывания – приблизительно 0,15 МПа; в момент наступления конца схватывания – 0,50 МПа.
Установлено, что портландцемент, содержащий фосфополугидрат и пыль электрофильтров, отличается максимальной скоростью процессов коагуляционного структурообразования, что подтверждается данными определения сроков схватывания цементного теста, представленными в табл. 2.15.
2.4.3.3. Влияние пропаривания на свойства портландцемента
В настоящее время значительная часть строительных конструкций изготовляется в заводских условиях. Для интенсификации процессов твердения портландцемента применяют различные способы тепло-влажностной обработки изделий. С целью определения влияния пропаривания на активность исследуемых портландцементов нами проведена термо-влажностная обработка стандартных образцов-балочек по режиму:
– |
подъем температуры, ч ........................................... |
2 |
– |
изотермическая выдержка, ч .................................. |
6 |
– |
охлаждение, ч .......................................................... |
2 |