
10372
.pdfТаблица 2.16 Удельное количество вредных веществ от гальванических ванн, zу, мг/(с·м2) и kТ
№ |
Технологические процессы |
Определяющее |
zу2), |
|
|
пп. |
вредное веще- |
kТ |
|||
гальванопокрытий1) |
мг/(с·м2) |
||||
|
ство |
|
|||
|
|
|
|
||
1 |
2 |
3 |
4 |
5 |
|
|
Электрохимическая обработка металлов в рас- |
|
|
|
|
|
творах, содержащих хромовую кислоту кон- |
Хромовый |
|
|
|
1 |
центрацией 150-300 г/л, при силе тока 1000 А |
10 |
2 |
||
ангидрид |
|||||
|
(хромирование, анодное декапирование, снятие |
|
|
||
|
|
|
|
||
|
меди и др.) |
|
|
|
|
|
Тоже, в растворах, содержащих хромовую кис- |
Хромовый |
|
|
|
2 |
лоту концентрацией 30-60 г/л (электрополиров- |
2 |
1,6 |
||
ангидрид |
|||||
|
ка алюминия, электрополировка стали и др.) |
|
|
||
|
|
|
|
||
|
Тоже, в растворах, содержащих хромовую кис- |
|
|
|
|
|
лоту концентрацией 30-100 г/л, при силе тока |
Хромовый |
|
|
|
3 |
500 А, а также химическое оксидирование |
1 |
1,25 |
||
ангидрид |
|||||
|
алюминия и магния (анодирование алюминия, |
|
|
||
|
|
|
|
||
|
анодирование магниевых сплавов) |
|
|
|
|
|
Химическая обработка стали в растворах хро- |
|
|
|
|
4 |
мовой кислоты и её солей при t > 50 °С (пасси- |
Хромовый |
5,5·10‒3 |
1 |
|
визация, травление, снятие оксидной пленки, |
ангидрид |
||||
|
|
|
|||
|
наполнение в хромпике и др.) |
|
|
|
|
|
Химическая обработка металлов в растворах |
Хромовый |
|
|
|
5 |
хромовой и её солей при t ≤ 50 °С (осветление, |
03) |
-4) |
||
ангидрид |
|||||
|
пассивация) |
|
|
||
|
|
|
|
||
|
Химическая обработка металлов в растворах |
|
|
|
|
|
щелочи (оксидирование стали, химическая по- |
|
|
|
|
|
лировка алюминия, рыхление окалины на ти- |
|
|
|
|
6 |
тане, травление алюминия, магния и их спла- |
Щелочь |
55 |
|
|
|
вов), при: |
|
|
|
|
|
- t > 100 °С |
|
|
1,25 |
|
|
- t ≤ 100 °С |
|
|
1,6 |
|
|
Электрохимическая обработка в растворах ще- |
|
|
|
|
7 |
лочи (анодное снятие шлама, обезжиривание, |
Щелочь |
11 |
1,6 |
|
лужение, снятие олова, оксидирование меди, |
|||||
|
|
|
|
||
|
снятие хрома и др.) |
|
|
|
|
|
Химическая обработка металлов, кроме алю- |
|
|
|
|
|
миния и магния, в растворах щелочи (химиче- |
|
|
|
|
8 |
ское обезжиривание, нейтрализация и др.), при: |
Щелочь |
03) |
|
|
|
- t > 50 °С |
|
|
1 |
|
|
- t ≤ 50 °С |
|
|
-4) |
|
9 |
Кадмирование, серебрение, золочение и элек- |
Цианистый |
5,5 |
2 |
|
тродекапирование в цианистых растворах |
водород |
||||
|
|
|
|||
|
Цинкование, меднение, латунирование, хими- |
Цианистый |
|
|
|
10 |
ческое декапирование и амальгамирование в |
1,5 |
1,6 |
||
водород |
|||||
|
цианистых растворах |
|
|
||
|
|
|
|
||
|
Химическая и электрохимическая обработка |
Фтористый |
|
|
|
11 |
металлов в растворах, содержащих фтористо- |
20 |
1,6 |
||
водород |
|||||
|
водородистую кислоту и её соли |
|
|
||
|
|
|
|
||
12 |
Химическая обработка металлов в концентри- |
Хлористый |
80 |
1,25 |
180
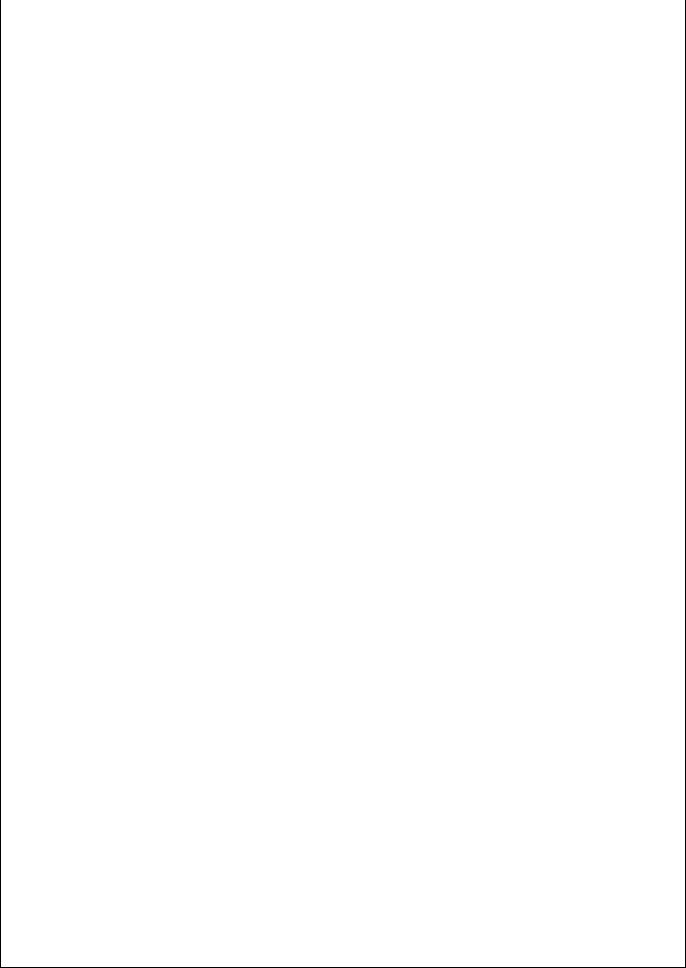
|
рованных холодных и разбавленных нагретых |
водород |
|
|
|
|
растворах, содержащих соляную кислоту (трав- |
|
|
|
|
|
ление, снятие шлама и др.) |
|
|
|
|
|
Химическая обработка металлов, кроме снятия |
|
|
|
|
13 |
цинкового и кадмиевого покрытия, в холодных |
Хлористый |
3·10‒1 |
-4) |
|
растворах, содержащих соляную кислоту концен- |
водород |
||||
|
|
|
|||
|
трацией до 200 г/л (травление, декапирование) |
|
|
|
|
|
Электролитическая обработка металлов в рас- |
|
|
|
|
|
творах, содержащих серную кислоту концен- |
|
|
|
|
|
трацией 150-350 г/л, а также химическая обра- |
Серная кисло- |
|
|
|
14 |
ботка в концентрированных холодных и нагре- |
7 |
1,6 |
||
та |
|||||
|
тых разбавленных растворах (анодирование, |
|
|
||
|
|
|
|
||
|
электрополирование, травление, снятие никеля, |
|
|
|
|
|
серебра, гидридная обработка титана и др.) |
|
|
|
|
|
Меднение, лужение, цинкование и кадмирова- |
Серная кисло- |
|
|
|
15 |
ние в сернокислых растворах при t ≤ 50 °С, а |
03) |
-4) |
||
та |
|||||
|
также химическое декапирование |
|
|
||
|
|
|
|
||
|
Химическая обработка металлов в концентри- |
|
|
|
|
|
рованных нагретых и электро-химическая об- |
|
|
|
|
16 |
работка в концентрированных холодных рас- |
Фосфорная |
5 |
1,6 |
|
творах, содержащих ортофосфорную кислоту |
кислота |
||||
|
|
|
|||
|
(химическая полировка алюминия, электропо- |
|
|
|
|
|
лировка стали, меди и др.) |
|
|
|
|
|
Химическая обработка металлов в концентри- |
|
|
|
|
17 |
рованных холодных и разбавленных нагретых |
Фосфорная |
6·10‒1 |
1,25 |
|
растворах, содержащих ортофосфорную кисло- |
кислота |
||||
|
|
|
|||
|
ту (фосфатирование и др.) |
|
|
|
|
|
Химическая обработка металлов в разбавлен- |
|
|
|
|
|
ных растворах, содержащих азотную кислоту |
|
|
|
|
|
(осветление алюминия, химическое снятие ни- |
Азотная кис- |
|
|
|
18 |
келя, травление, декапирование меди, пассива- |
лота |
|
|
|
|
ция и др.), при концентрации раствора: |
и окислы азота |
|
|
|
|
- выше 100 г/л |
|
3 |
1,25 |
|
|
- ниже 100 г/л |
|
03) |
-4) |
|
|
Никелирование в хлоридных |
Растворимые |
|
|
|
19 |
растворах при плотности тока |
1,5·10-1 |
2 |
||
соли никеля |
|||||
|
1-3 А/дм2 |
|
|
||
|
|
|
|
||
|
Никелирование в сульфатных |
Растворимые |
|
|
|
20 |
растворах при плотности тока |
3·10-2 |
1,6 |
||
соли никеля |
|||||
|
1-3 А/дм2 |
|
|
||
|
|
|
|
||
21 |
Меднение в этилдиаминовом |
Этилендиамин |
03) |
1 |
|
электролите |
|||||
|
|
|
|
||
22 |
Кадмирование и лужение в кислых электроли- |
Фенол |
03) |
1 |
|
тах с добавкой фенола |
|||||
|
|
|
|
||
23 |
Крашение в анилиновом красителе |
Анилин |
03) |
1 |
|
24 |
Промывка в горячей воде (t > 50 °С) |
Пары воды |
- |
0,5 |
|
|
Безвредные технологические процессы при |
|
|
|
|
25 |
наличии неприятных запахов, аммиака, клея и |
- |
- |
0,5 |
|
пр. |
|||||
|
|
|
|
||
|
|
|
|
|
Примечание.
1) Номер позиции из данной таблицы должен быть указан в технологическом задании на проек-
181

тирование системы вентиляции
2)Значения приведены при номинальной загрузке ванны для расчета максимальных разовых концентраций. Для определения среднесуточных значений следует учитывать коэффициент загрузки оборудования. При определении необходимости очистки вентиляционных выбросов и выборе очистных устройств следует учитывать выпадение аэрозоля на внутренних стенках отсосов и воздуховодов. Количество осевших вредных веществ определяется по рисунку 2.2.
3)Количество выделяющихся вредных веществ незначительно и при расчете вентиляционных выбросов может не учитываться.
4)Местный отсос не требуется. Установка местного отсоса необходима при наличии воздушного перемешивания раствора (kТ = 0,5).
Вслучае применения полностью укрытого технологического оборудования и высоте подачи воздуха более 6 м допускается сосредоточенный выпуск воздуха с обеспечением скорости его движения в рабочей зоне в пределах нормируемой, с применением воздухораспределителей типа ВЭС, серия I.494-17.
Вподвальном (техническом) этаже при размещении в нем отделений приготовления и корректировки растворов необходимо предусматривать общеобменную вентиляцию из расчета ассимиляции тепло- и влагоизбытков. При наличии местных отсосов количество удаляемого воздуха должно компенсироваться механическим притоком и обеспечивать не менее, чем трехкратный воздухообмен. В машинных отделениях вентиляцию рассчитывают на ассимиляцию теплоизбытков. В одноэтажных зданиях допускается использовать аэрацию во все периоды года. При расположении отделений в первых этажах многоэтажных зданий – вытяжка из верхней зоны через шахты, проходящие через выше расположенные этажи.
Помещения хранения цианистых солей и кислот требуется вентилировать отдельными приточными установками. Применение общей приточной установки должно быть технически обосновано. Местные отсосы от оборудования для обезжиривания деталей органическими растворителями следует объединять в самостоятельные системы. Для остальных гальванических процессов допускается объединение местных отсосов в общую вытяжную установку.
Внерабочее время следует обеспечивать вентиляцию помещения цеха из расчета ассимиляции влагоизбытков с целью защиты от разрушения строительных конструкций (предотвращение конденсации влаги). Для этого должны включаться части приточных или вытяжных установок с учетом круглосуточной работы вытяжных установок от ванн, если эти ванны не имеют укрытий.
Магистральные воздуховоды, кроме воздуховодов от местных отсосов ванн с органическими растворителями допускается прокладывать в подпольных каналах, изготовленных из кирпича или бетона. Воздуховоды в этом случае следует выполнять с противокоррозионной защитой изнутри и снаружи. Уклон горизонтальных участков сети должен составлять 0,005-0,01. В нижней части участков сети необходимо предусматривать сборник с устройством для спуска конденсата в канализацию. Для обеспечения возможности очистки воздуховодов на ближайших к источнику выделения вредных веществ участках (до 10 м) следует предусматривать съемные отводы или прямики с применением быстросъемных фланцевых соединений. Шахты вытяжных установок должны обеспечивать, как правило, факельный выброс. Над вытяжными шахтами зонты устанавливать не рекомендуется. Вентиляторы требуется применять в антикоррозийном исполнении, в нижней части кожуха вентилятора должны быть предусмотрены устройства для отвода конденсата в канализацию.
182
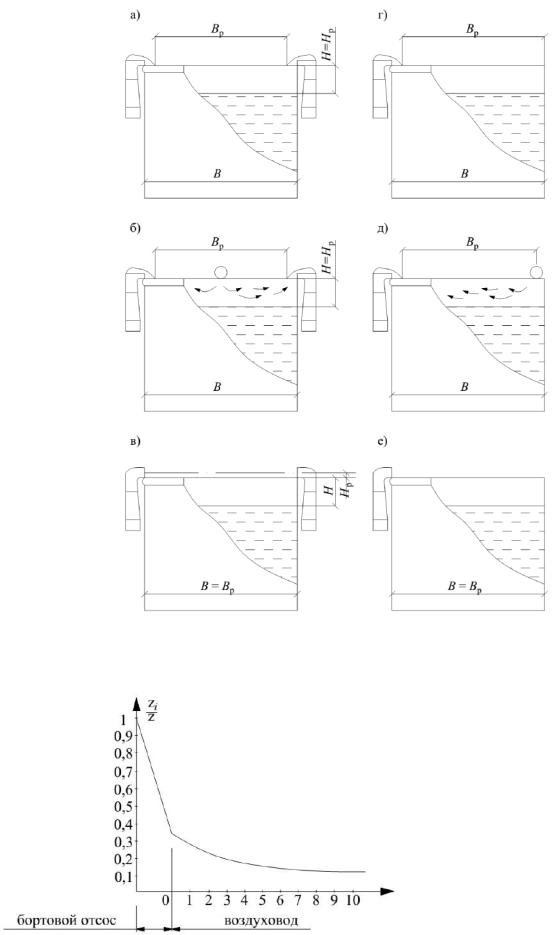
Рис. 2.1. Местные отсосы от гальванических ванн: двубортовые (а – без передувки; б – с передувкой; в – с вертикальной щелью всасывания); однобортовые (г – без передувки; д – с передувкой; е – с вертикальной щелью всасывания)
Рис. 2.2. График снижения относительного содержания аэрозоля вредных веществ в удаляемом воздухе по пути его движения
183
Вентиляционные выбросы гальванических и травильных цехов должны рассчитываться в соответствии с требованиями санитарных норм по защите воздушного бассейна на предприятии и воздуха населенных мест. Количество вредных веществ, содержащихся в вентиляционных выбросах приведено в таблице 2.16. Для вредных веществ, выделяющихся в виде аэрозолей, следует учитывать данные приведенные на рисунке 2.2.
Очистка вентиляционных выбросов не предусматривается, если концентрация вредных веществ в удаляемом воздухе не превышает предельно допустимые, установленные санитарными нормами для воздуха рабочей зоны. В остальных случаях требуется проведение поверочного расчета на рассеивание вредных веществ в атмосферном воздухе и при необходимости предусматривать очистку вентиляционных выбросов. Для очистки вентиляционных выбросов от вредных веществ, выделяющихся в виде аэрозолей, рекомендуется применять кассетные фильтры из полимерных материалов или пенные газопылеочистители интерсифицированные, (ПГП-И) со стабилизатором пены. В качестве кассетных фильтров следует применять фильтры, встроенные в бортовой отсос, обеспечивающие высокую эффективность очистки и предохранение магистральных воздуховодов от коррозии и зарастания продукта уноса. При технико-экономическом обосновании допускается применение кассетных фильтров, встроенных в коллектор или магистральный воздуховод от группы ванн с максимально возможным приближением к местным отсосам. Для очистки выбросов от цианистых соединений применяют фильтры ПГП-И.
Сборочно-сварочные цеха
Отопление и вентиляция сборочно-сварочных цехов проектируется в соответствии с рекомендациями [46]. Выделение вредных веществ и их распространение в воздушной среде производственных помещений заготовительных и сборочно-сварочных цехов должны предотвращаться в первую очередь соответствующей организацией технологического процесса, конструктивными решениями оборудования и специфическими объемно-планировочными и конструктивными решениями зданий.
Отопление сборочно-сварочных цехов требуется предусматривать воздушное, совмещенное с приточной вентиляцией. При технико-экономическом обосновании допускается применение воздушно-отопительных агрегатов из расчета возможного использования их для нужд дежурного отопления.
Количество выделений вредных веществ и теплоты при использовании различных сварочных и наплавочных материалов, для определения воздухообмена в производственных помещениях принимается по данным технологов, а при отсутствии данных принимается по справочной литературе. При одновременном расходовании материалов с различными вредностями воздухообмен необходимо рассчитывать по преобладающей вредности в смеси аэрозолей.
При проектировании общеобменной вентиляции следует предусматривать естественную вытяжную вентиляцию из верхней зоны, приточную – механическую, независимо от кратности воздухообмена. При применении механической вытяжной вентиляции из многопролетного цеха в теплый период года допускается естественный приток воздуха в крайние пролеты.
Заготовительные и сборочно-сварочные цеха, сообщающиеся со смежными цехами, где не производится сварка или резка металлов, должны иметь механическую вытяжную вентиляцию независимо от наличия фонарей.
При газопламенной обработке металлов сжиженными газами и отсутствии местных отсосов 2/3 воздуха следует удалить из нижней зоны (механическим путем) и 1/3 из верхней (естественным или механическим путем).
При технико-экономическом обосновании допускается применение механической вытяжной вентиляции из верхней зоны крышными вентиляторами.
Подача приточного воздуха должна осуществляться:
1) при сварке и резке на нестационарных местах – сосредоточенно в верхнюю зону с применением насадков, позволяющих регулировать направление воздушной струи в вертикальной плоскости, обеспечивая подвижность воздуха в рабочей зоне в пределах от 0,8 до 0,9 м/с при
184
электродуговой и газопламенной сварке и резке и не более 0,5 м/с при сварке в среде углекислого газа;
2) при сварке в среде инертных газов и наличии зональной вытяжки от мест сварки на конвейере, а также в цехах, где вытяжная вентиляция решается посредством стационарных местных отсосов рассредоточено в рабочую зону, обеспечивая подвижность воздуха на рабочих местах не более 0,3 м/с.
При разбросанности участков сварки и резки металлов и наличии между ними зон с меньшим загрязнением воздуха рекомендуется устройство вентиляции по участкам со схемой организации воздухообмена, предотвращающей перетекание вредностей. Количество вредностей, удаляемых местными отсосами, следует определять в зависимости от расхода сварочного или наплавочного материалов и принимается в размере 90 % для вытяжных шкафов и 75 % для других местных отсосов. Оставшееся количество вредностей (10 или 25 %) должно разбавляться до ПДК общеобменной вентиляцией.
Объем воздуха, удаляемый местными отсосами, на которые отсутствуют данные завода изготовителя, рекомендуется принимать следующим образом:
1)минимальная скорость воздуха во всасывающем факеле у источника выделения вредных веществ должна приниматься: при ручной электросварке на стационарных постах – 0,5 м/с; при сварке в среде углекислого газа – 0,5 м/с; при сварке в среде инертных газов – 0,3 м/с; при машинной резке на раскроечных столах титановых сплавов и низколегированных сталей – 2,2 м/с; тоже, алюминиево-магниевых сплавов и высоколегированных сталей – 3,0 м/с.
2)Скорость воздуха в рабочих проемах вытяжных шкафов при сварке мелких изделий рекомендуется принимать: при применении электродов – 0,6 м/с; при сварке свинца – 0,7 м/с.
Для вентиляции замкнутых и полузамкнутых объемов сборочно-сварочных цехов требуется предусматривать.
1)При сварке – вытяжную вентиляцию вакуум-насосными установками с малогабаритными приемниками, а при невозможности их применения – общеобменную вентиляцию за счет удаления загрязненного воздуха или путем подачи свежего воздуха вентиляторами высокого давления с гибкими рукавами облегченной конструкции.
2)При резке – общеобменную приточную вентиляцию. Расход воздуха также определяется из условия разбавления выделяющихся вредностей. Параметры воздуха на рабочем месте при общеобменной вентиляции замкнутых и полузамкнутых объемов должны быть: tв = 20-22 °C; vв = 0,5-1,5 м/с. При невозможности применения в замкнутых и полузамкнутых объемах местной или общеобменной вентиляции должна предусматриваться принудительная подача наружного воздуха под маску или полумаску специальной конструкции в количестве Lуд = 8 м3/ч с температурой не ниже 15 °C.
При рассредоточенной подаче воздуха в рабочую зону предусматривается вентиляция кабины крановщика с подачей наружного воздуха. В случае газопламенной обработки металлов с применением сжиженных газов установки местной вытяжной вентиляции выполняется во взрывобезопасном исполнении.
Пыль из заточных, шлифовальных и полировальных отделений удаляется местными отсосами от заточных, обдирочных, полировальных и шлифовальных кругов. Объем отсасываемого воздуха, обеспечивающий эффективность удаления пыли от кругов, зависит от окружной скорости вращения круга и расположения всасывающего отверстия кожуха по отношению направления образующегося факела пыли. Площадь всасывающего отверстия в кожухе принимается равной площади проекции открытой части круга.
Расчетная скорость во всасывающем отверстии кожуха принимается равной: 25 % от окружной скорости вращения круга при направлении пылевого факела непосредственно в отверстие; 30 % от окружной скорости вращения круга при направлении пылевого факела параллельно плоскости всасываемого отверстия. Расход воздуха, удаляемый от шлифовальных, заточных и прочих подобных станков L, м3/ч, определяется по формулам:
а) при устройстве укрытия в виде кожухов и при диаметре круга d <250 мм
L 2d , |
(2.26) |
185
тоже, 250 ≤ d ≤ 600 мм |
|
|
|
|
|
|
|
|
L 1,8d , |
|
|
|
|
(2.27) |
|||
тоже, d > 600 мм |
|
|
|
|
|
|
|
|
L 1,6d ; |
|
|
|
|
(2.28) |
|||
б) при установке воронок, улавливающих пыль |
|
|
|
|
|
|
|
|
L 3500 vначa |
2 |
|
|
K |
|
1,4 |
|
|
|
|
|
|
|
|
; |
(2.28) |
|
|
v |
/ v |
1 |
|||||
|
|
|
нач |
кон |
|
|
|
|
где: d – диаметр круга, мм;
vкон – необходимая конечная скорость вытяжного факела у круга, м/с, vкон = 2 м/с;
vнач – необходимая начальная скорость вытяжного факела, м/с, принимается равной скорости транспортирования отходов в воздуховодах;
a – рабочая длина вытяжного факела, м;
K – коэффициент, зависящий от отношения размеров воронки, принимается равным 7,7 для круглого отверстия и 9,1 для прямоугольного отверстия с соотношением сторон от 1:1 до 1:3.
Для полировальных кругов, м3/ч: L = 6d – матерчатых; L = 4d – войлочных.
Окрасочные цеха
Отопление окрасочных цехов и участков требуется предусматривать воздушное, совмещенное с приточной вентиляцией, а также посредством местных нагревательных приборов. При устройстве воздушно-тепловых завес допускается рециркуляция с забором воздуха из верхней зоны помещения вблизи ворот на высоте не менее 3 м от пола [48].
Вентиляция окрасочных цехов и участков проектируется приточно-вытяжной с механическим побуждением. Вытяжная вентиляция осуществляется с помощью местных отсосов от оборудования, предусмотренного в технологической части проекта. Расчетный воздухообмен в помещениях определяется количеством воздуха, удаляемого местными отсосами и не возмещенного притоком непосредственно в камеры и технологические установки. Этот воздухообмен должен быть также рассчитан на ассимиляцию теплоизбытков помещений. Кратность воздухообмена в помещениях краскоприготовления и лабораториях должна быть не менее 10 ч‒1. При кратности воздухообмена помещения окраски до 5 ч‒1 следует дополнительно предусматривать вытяжку из верхней зоны (непосредственно из-под кровли) из расчета однократного воздухообмена.
Для помещений высотой более 6 м количество удаляемого воздуха из верхней зоны допускается определять из расчета 6 м3/ч на м2 площади пола помещения. В помещениях краскоприготовления и лабораторий дополнительный воздухообмен для обеспечения кратности 10 ч‒ 1 предусматривается за счет вытяжки из нижней зоны помещения. Приточный воздух в помещения следует подавать выше рабочей зоны так, чтобы скорость движения воздуха у открытых проемов местных отсосов не превышала 75 % от скорости всасывания в этих проемов. Воздух, удаляемый общеобменной вентиляцией очистке не подлежит.
Вопрос очистки воздуха, удаляемого от технологического оборудования, рассматривается в технологической части проекта.
Окраска мелких изделий осуществляется в камерах или шкафах. При пульверизационной окраске камера должна быть достаточно глубокой (рис. 2.3) и оборудована гидрофильтром для очистки удаляемого воздуха. Кромки проема камеры должны быть наклонными и иметь отгибы, предотвращающие выбивание взвеси краски в помещение. При кистевой окраске могут быть использованы вытяжные шкафы (рис. 2.4) и витринные отсосы (рис. 2.5).
Объем удаляемого воздуха от камер определяется исходя из средней скорости воздуха в рабочем проеме vп, м/с, приведенной в таблице 2.17.
186

Рис. 2.3. Камера для окраски мелких изделий: |
Рис. 2.4. Вытяжной шкаф для кистевой |
|||
1 – корпус камеры; 2 – решетка; 3 – поворотный |
окраски изделий: 1 – корпус шкафа; 2 – воз- |
|||
круг; 4 – гидрофильтр; 5 – отстойная ванна; 6 – |
духоприемная щель; 3 – рабочий стол |
|||
сепаратор |
|
|
|
|
|
|
|
Таблица 2.17 |
|
Средняя скорость воздуха в рабочем проеме |
|
|
||
|
|
|
|
|
Способ нанесения |
|
Применяемые |
vп, м/с |
|
лакокрасочного материала |
лакокрасочные материалы |
|
||
|
|
|||
Пневматическое распыление |
Содержащие свинцовые соединения |
1,3 |
|
|
или ароматические углеводороды |
|
|||
|
|
|
||
Пневматическое распыление |
Не содержащие ароматические |
1 |
|
|
углеводороды и свинцовые соединения |
|
|||
|
|
|
||
Безвоздушное распыление |
Содержащие свинцовые соединения |
0,7 |
|
|
или ароматические углеводороды |
|
|||
|
|
|
||
Безвоздушное распыление |
Не содержащие ароматические |
0,6 |
|
|
углеводороды и свинцовые соединения |
|
|||
|
|
|
||
Электроручное распыление |
Различные |
|
0,4-0,5 |
|
Для окраски изделий средней величины применяются окрасочные камеры с горизонтальным движением воздуха (рис. 2.6). Данные камеры состоят из корпуса гидрофильтра насосного агрегата и вытяжного вентиляционного агрегата.
Габаритные размеры камеры определяются размерами окрашиваемых изделий. Камеры могут быть проходными и тупиковыми. Рабочий размещается в области рабочего проема. В проходных камерах предусматривается один рабочий и два транспортных проема. Ширина рабочего проема должна быть не менее 1600 мм. Верхняя кромка рабочего проема располагается на 400600 мм выше окрашиваемого изделия. Размеры транспортных проемов зависят от габаритов окрашиваемых изделий и зазоров по контуру изделий, принимаемых порядка 100-150 мм. В тупиковых камерах предусматривается один проем с минимальными размерами 1600×1600 мм.
Объем удаляемого воздуха от камер определяется по средней скорости воздуха в рабочем проеме vп, м/с, приведенной в таблице 2.5, с учетом площадей предусмотренных рабочих и транспортных проемов.
Удаление воздуха от камер производится через гидрофильтр, воздухоприемное отверстие которого располагается против рабочего проема камеры, за изделием на высоте 700-800 мм от
187
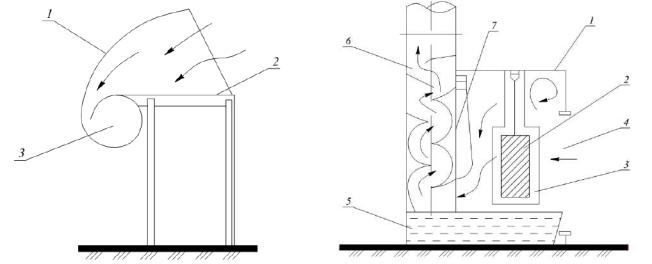
поверхности пола. Стенка камеры над воздухоприемным отверстием орошается водой, представляя собой водяной экран.
Рис. 2.5. Витринный отсос для кистевой |
Рис. 2.6. Камера для окраски изделий сред- |
окраски изделий с отсосом «улитка»: 1 – кор- |
ней величины с горизонтальным движением |
пус шкафа; 2 – рабочий стол; 3 – отсос «улит- |
воздуха (с боковым отсосом): 1 – корпус ка- |
ка» с переменной шириной щели |
меры; 2 – окрашиваемое изделие; 3 – транс- |
|
портный проем; 4 – рабочий проем для про- |
|
ведения окраски изделий; 5 – отстойная ван- |
|
на; 6 – гидрофильтр; 7 – экран для водяной |
|
пленки |
Для окраски крупных изделий применяют окрасочные камеры с вертикальным движением воздуха (рис. 2.7). Камера состоит из корпуса, вытяжной решетки, гидрофильтра, водоотстойника, и приточного короба. Удаление воздуха из камеры предусматривается через вытяжную решетку, занимающую площадь пола камеры. Объем удаляемого воздуха определяется исходя из удельногорасхода воздуха на 1 м2 площади пола камеры Lуд, м3/(ч·м2), приведенного в таблице 2.18.
|
|
|
Таблица 2.18 |
|
Удельный расход воздуха через площадь пола окрасочной камеры |
|
|
||
|
|
|
|
|
Способ нанесения |
Применяемые |
|
Lуд, |
|
лакокрасочного материала |
лакокрасочные материалы |
|
м3/(ч·м2) |
|
Пневматическое распыление |
Содержащие свинцовые соединения |
|
2200 |
|
или ароматические углеводороды |
|
|
||
|
|
|
|
|
Пневматическое распыление |
Не содержащие ароматические |
|
1800 |
|
углеводороды и свинцовые соединения |
|
|
||
|
|
|
|
|
Безвоздушное распыление |
Содержащие свинцовые соединения |
|
1500 |
|
или ароматические углеводороды |
|
|
||
|
|
|
|
|
Безвоздушное распыление |
Не содержащие ароматические |
|
1200 |
|
углеводороды и свинцовые соединения |
|
|
||
|
|
|
|
Подача воздуха в камеру предусматривается равномерно по всей площади потолка через слой фильтрующего материала, что сводит к минимуму циркуляцию воздуха в камере. Фильтрующий материал закладывается в специальные кассеты. В качестве фильтрующего материала может быть использовано стекловолокно, толщиной не менее 20 мм, а также промышленные ячеистые фильтры типов ФЯР, ФЯП и пр.
188
Для окраски изделий могут также использоваться стенды бескамерной окраски (рис. 2.8), которые включают в себя напольную вытяжную решетку, подрешетчатое пространство и гидрофильтр, и может быть использован при окраске изделий высотой до 2 м лакокрасочными материалами, не содержащими свинцовых соединений. Напольная решетка должна превышать габариты окрашиваемых изделий на 300 мм по периметру. При этом меньшая сторона решетки должна составлять не менее 0,75 высоты окрашиваемого изделия. В исключительных случаях при техни- ко-экономическом обосновании допускается бескамерная окраска изделий высотой более 2 м с обязательным применением экранов по свободному периметру напольной решетки высотой на 0,5 м более высоты изделия. Объем удаляемого воздуха через напольную решетку определяется исходя из удельного расхода воздуха на 1 м2 площади пола решетки Lуд, м3/(ч·м2), приведенного в таблице 2.19.
|
|
Таблица 2.19 |
|
Удельный расход воздуха через напольную решетку |
|
|
|
|
|
|
|
Способ нанесения |
Применяемые |
Lуд, |
|
лакокрасочного материала |
лакокрасочные материалы |
м3/(ч·м2) |
|
|
- содержащие ароматические |
2500 |
|
Пневматическое распыление |
углеводороды |
|
|
- не содержащие ароматические |
2200 |
|
|
|
|
||
|
углеводороды |
|
|
|
- содержащие ароматические |
1700 |
|
Безвоздушное распыление |
углеводороды |
|
|
- не содержащие ароматические |
1350 |
|
|
|
|
||
|
углеводороды |
|
|
|
- содержащие ароматические |
1100 |
|
Гидростатическое |
углеводороды |
|
|
- не содержащие ароматические |
900 |
|
|
|
|
||
|
углеводороды |
|
|
Пневмоэлектростатический |
содержащие или не содержащий |
900 |
|
ароматические углеводороды |
|
|
|
|
|
|
Подрешеточное пространство проходным или полупроходным по размерам напольной решетки с уклоном в сторону гидрофильтра. Положение гидрофильтра должно обеспечивать удобные условия его эксплуатации (очистку внутренних поверхностей воздухоприемного канала). Окрасочный стенд должен иметь самостоятельный комплект вентиляционного оборудования, работа которого блокируется с работой системы подачи краски в красораспылители и системой водоснабжения гидрофильтра. Для контроля концентрации взрывоопасных веществ следует предусматривать сигнализаторы, размещаемые в подрешеточном пространстве на высоте 0,5 м от его пола. Сигнализаторы должны быть настроены на концентрацию 20 % от нижнего предела взрывоопасности и сблокированы с обслуживающим вентиляционным оборудованием.
Гидрофильтры (рис. 2.9), входящие в состав окрасочных камер, предназначены для очистки воздуха, удаляемого от окрасочных камер или стендов от красочной пыли, а также паров растворителей. Очистка воздуха осуществляется в S-образном воздухораспределительном канале, проходя через ряд образующихся водяных завес. Пропускная способность гидрофильтра по воздуху определяется скоростью воздуха в живом сечении промывного канала, принимаемая в пределах vп = 5-6,5 м/с. Удельный расход циркулирующей воды принимается в пределах 2-3 кг на 1 м3 воздуха. Добавление свежей воды составляет до 2 % от расхода циркулирующей.
Коэффициент очистки воздуха от красочной пыли ηк, определяется по следующей зависи-
мости:
к 65 5vп . |
(2.29) |
189