
9848
.pdf
1)улучшение зернового состава путем выделения загрязняющих примесей;
2)увеличение прочности путем разделения разнопрочных материалов;
3)обогащение по форме зерен за счет выделения щебня кубовидной формы.
Способы улучшения зернового состава
МОКРЫЙ способ: - промывка исходных материалов – обезвоживание пульпы – осветление промывочной воды – подача готовой продукции на склад.
Обезвоживание выполняют в ковшовом обезвоживатиле или спиральном классификаторе.
Осветление воды производится в прудах-отстойниках или радиальных сгустителях, откуда вода вновь идет на промыв, а осевший шлам – в хвостохранилище. При этом используют вещества-флокулянты из расчета 2 л на 1 м3 пульпы. Сгущение пульпы осуществляют в гидроциклонах и сгустительных воронках.
СУХОЙ способ: - сушка материала в сушильных барабанах при Wмсх. 1,5- 3% - грохочение – сухая очистка в пневмоклассификаторах вертикального типа – обеспыливание в циклонах.
При выборе способа учитывают, что зимой мокрая очистка не выполняется, а при сухом необходима дополнительная сушка материала.
Обогащение разнопрочных материалов
1) избирательное дробление: слабые и хрупкие породы измельчаются быстрее и на следующую стадию поступают отдельно более крупные и прочные частицы.
Избирательность процесса-
I i iсл 1 - слабый материал дробится более интенсивно.
iпр
2) в двухбарабанном классификаторе:
Вибролоток и воронки регулируются путем настройки угла падения камня. Барабаны представляют собой цилиндры (диаметром 820 мм, длиной 4000 мм) и регулируются скоростью вращения.
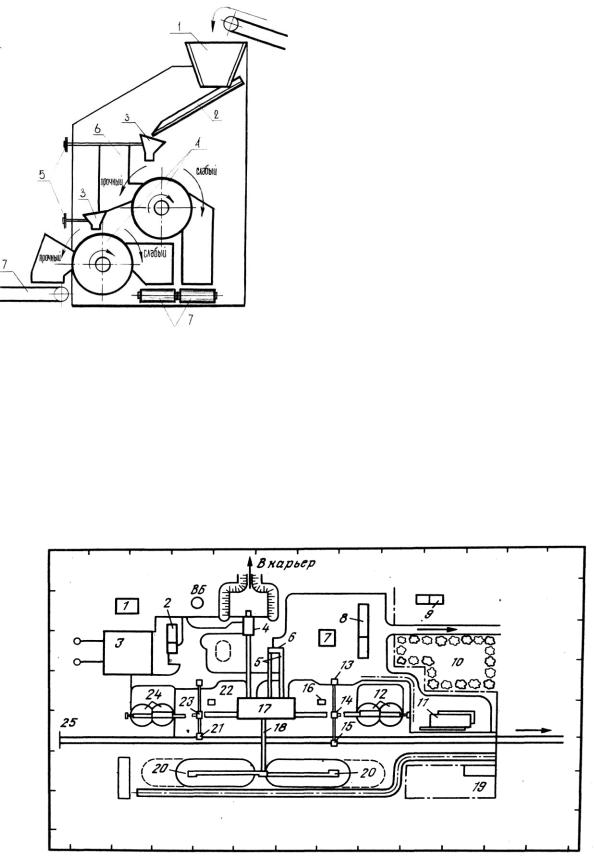
Рис. 12 Двухбарабанный классификатор
1 – питающий бункер; 2 – вибролоток; 3 – направляющая воронка; 4 – барабаны; 5 – регулировочные штурвалы; 6 – неподвижная течка; 7 – транспортеры.
При ударе о поверхность барабана слабые зерна увлекаются в сторону вращения, а прочные отскакивают в противоположную сторону (за счет большей упругости и меньшего сцепления с металлом). В процессе разделения получается материал трех сортов по прочности.
3) осаждение в тяжелых средах (в настоящее время на применяется).
Обогащение по форме
1)избирательное грохочение на щелевидных ситах;
2)грануляция щебня в дробилках ударного действия и барабанных грануля-
торах.
2. Генеральный план камнедробильного завода (КДЗ)
Рис. 13 Генеральный план гравийно-песчаного камнедробильного завода:
1 – пожарный сарай; 2 – котельная, душ, гардероб; 3 – склад топлива, масла, бензозаправочные колонки; 4 – отделение первичного дробления; 5 – транспортер; 6, 14, 15, 23 – перегрузочные узлы; 7
– лаборатория; 8 – контора и диспетчерская; 9 – туалет; 10 – площадка отдыха; 11 – РММ; 12 – склад щебня; 13 – погрузочный бункер для автомобилей; 16, 22 – пульт управления; 17 – отделение вторичного дробления, промывки, сортировки; 18 – транспортер; 19 – охрана; 20 – склад песка; 21 – узел погрузки на железнодорожные платформы; 24 – склад гравия; 25 – железнодорожный тупик.
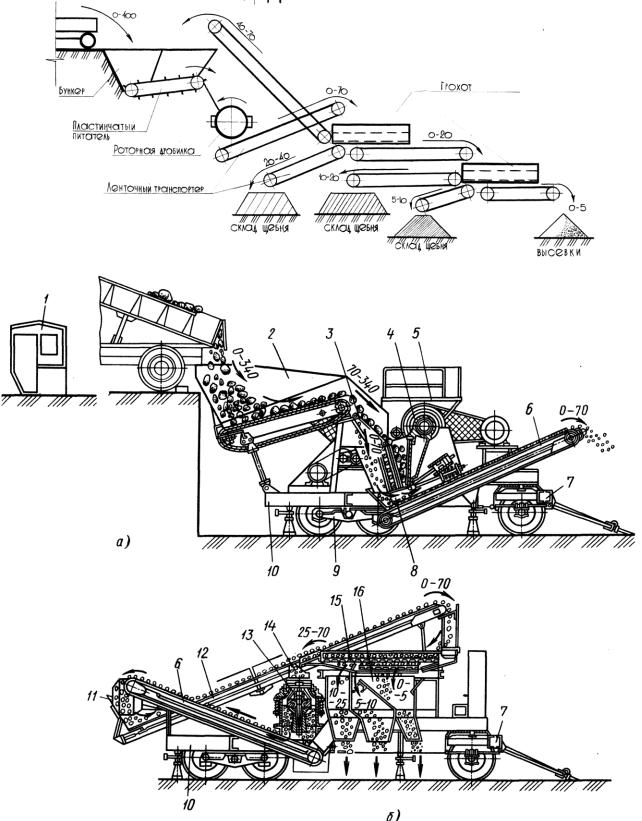
3. Технологические схемы переработки горных пород
При выборе технологической схемы учитывают:
-характеристику исходной горной массы;
-прочностной и зерновой составы;
-ассортимент готовой продукции;
-климатический условия.
а) переработка камня на ПДСУ в составе АБЗ
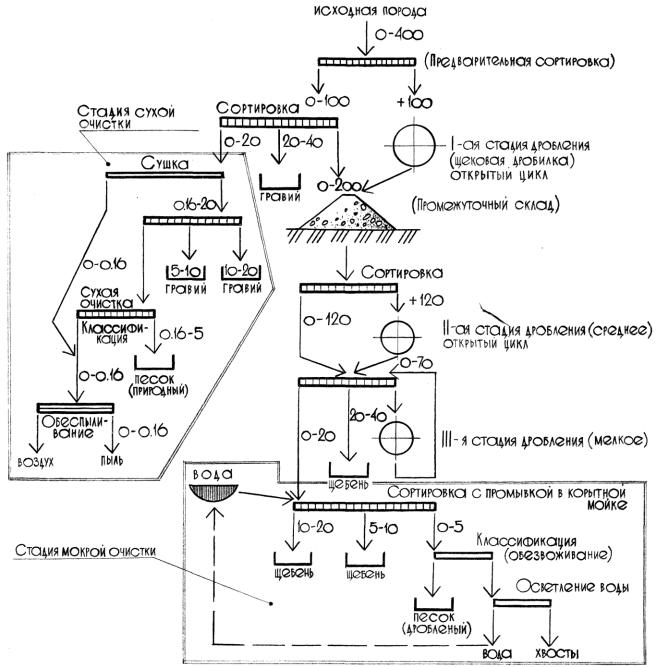
Рис. 14 Схема агрегатов первичного и вторичного дробления передвижной установки:
а) агрегат первичного дробления СМД-126; б) агрегат вторичного дробления СМД-127:
1 – кабина оператора с пультом управления, 2 – пластинчатый питатель, 3 – колосниковая решетка, 4 – щековая дробилка, 5 – площадка управления, 6, 12 – ленточный транспортер, 7, 9 – передняя и задняя тележки рамы агрегата первичного дробления, 10 – рама агрегата, 8 – течка, 11 – приемный бункер, 13 – конусная дробилка, 14 – загрузочная воронка, 15 – инерционный грохот, 16 – трехсекционный бункер.
б) переработка песчано-гравийной смеси
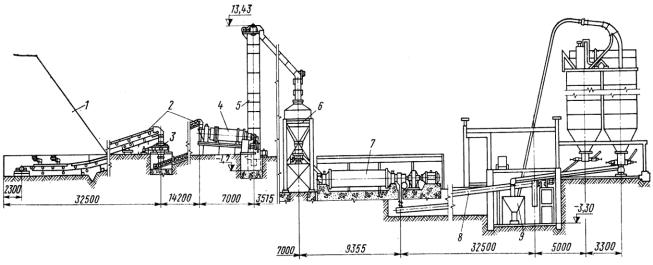
4. Производство минерального порошка.
Технологический производственный процесс включает: дробление, просушивание и размол каменного материала.
Дробление щебня производится на стационарных предприятиях (КДЗ с годовой производительностью Пр = 80-120 тыс. т). Используется камень известняковых и доломитовых пород с прочностью не ниже 20 МПа и содержанием примесей глины не более 5%. Крупность каменного материала – 0-20 мм (отсевы дробления).
Рис. 15 Схема приготовления минерального порошка:
1 – склад известнякового щебня; 2 – ленточный конвейер с вибролотками; 3 – валковая дробилка; 4 – сушильный барабан; 5 – ковшовый конвейер; 6 – перегрузочный бункер; 7 – шаровая мельница; 8 – винтовой конвейер; 9 – бункер перегрузки.
Помол осуществляется при влажности щебня W 2%.
Шаровая мельница имеет две камеры с колющими телами (шары диаметром 50, 70. 100 мм). Размол ведется с одновременной воздушной сепарацией материала, чем обеспечивается получение продукта заданной тонкости помола.
При необходимости дробление может быть многостадийным или вообще отсутствовать, если для производства минерального порошка используется готовое сырье.
Отсортированный материал поступает в расходный бункер, откуда направляется на просушивание и последующий помол. Готовая продукция хранится в силосах, загружаемых винтовым конвейером (элеватором) или пневмотранспортом.
Особенность приготовления активированного минерального порошка.
Помол каменных материалов ведут в присутствии активирующей добавки – смеси битума и ПАВ анионного типа в соотношении 1:1 в количестве 1,5 – 2,5%. Смешение каменного материала с активирующей добавкой ведут 1,5 мин. после просушивания в лопастном смесителе. Активирующую смесь готовят в битумоплавильных котлах (температура нагрева: битума 1200-1300С; ПАВ 700-800С).

Рис. 16 Технологическая схема производства активированного минерального порошка:
1, 3, 7 – транспортер; 2 – накопительный бункер; 4, 8 – приемный бункер; 5 – сушильный барабан; 6 – дозировочный бачок; 9 – тарельчатый питатель; 10 – шаровая мельница; 11 – элеватор; 12 – раздаточный бункер
Проектирование базы по приготовлению минерального порошка.
а) определение производительности базы (в зависимости от объемов работ – общая площадь покрытия расход асфальтобетонной смеси потребность в
минеральном порошке Qп фонд рабочего времени Ф Пр QФп );
б) подбор камнедробильного, сушильно-помольного, складского и др. оборудования.
4. Организация складского хозяйства
Входит в состав работ по снабжению строительства материальнотехническими ресурсами (МТР).
1. Порядок снабжения строительства МТР.
а) уточнение потребности строительства в материалах (на основе перспективных планов с учетом производственных норм расхода материалов);
б) установление хозяйственных связей по поставке материалов; в) нормирование производственных запасов; г) организация складского хозяйства; д) организация построечного транспорта;
е) функционирование складского хозяйства.
2. Нормирование производственных запасов.
Текущая потребность в дорожно-строительных материалах:
Зпр. = Зт + Зп + Зг , натур. изм., руб., дни
где: Зт – текущий запас (необходим для бесперебойной работы предприятия между двумя смежными поставками);
Зп – подготовительный запас (необходим для обеспечения начала работ и периода приемки очередной партии, включая разгрузку, сортировку, развозку и лабораторный анализ);
Зг – гарантийный (страховой) запас (необходим для устранения последствий от возможного отклонения в периодичности поставок).
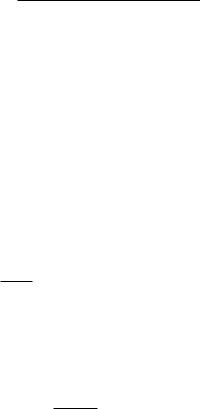
С учетом сезонности работ, а также при доставке материалов водным транспортом, создают сезонный запас (определяется расчетом).
3. Организация складского хозяйства.
а) создание хранилищ. Расчетная емкость склада:
Vск. = Qс·Тс или Vск. Пг q Зпр кп кразд.
кз Т
где: Qс – суточный грузооборот на складе с учетом неравномерности; Тс – срок хранения, сут.; Пг – годовая производительность предприятия, м3;
q – расход материала на единичный измеритель; Зпр. – запас материалов, дни;
кп = 1.01-1.04 – коэффициент потерь (естественная убыль);
кразд. = 1.15-1.20 – коэффициент увеличения объема склада за счет раздельного хранения материалов разного качества;
кз = 0.9-0.7 – коэффициент заполнения склада; Т – количество рабочих дней в году.
Площадь открытого склада: Sск Vск (кз )
где: – вместимость единицы площади склада, м3/м2 (зависит от типа склада
– 3.5-10 м3/м2).
б) расчет погрузо-разгрузочных работ.
Фронт разгрузки: L n l l1 (n 1) Nc l nп
где: n – число одновременно разгружаемых транспортных единиц; l – длина транспортной единицы;
l1 – расстояние между транспортными единицами;
Nс – число разгружаемых транспортных единиц в сутки; nп – число подач под разгрузку в сутки.
Производительность разгрузочной машины:
- периодического действия |
П |
|
к |
|
Т |
|
3600 |
qц |
|
р |
исп |
см |
tц |
||||||
|
|
|
|
|
|||||
|
|
|
|
|
|
|
|
||
- непрерывного действия |
Пр = кисп·Тсм·3600·F·v· |
где: qц – масса груза за один цикл работы машины;
F – площадь перемещаемого груза в сечении потока; v – скорость перемещения;
- насыпная плотность груза.
в) организация работы построечного транспорта.
Система перевозок - «от себя» (от базы). Централизованные перевозки – «внешний транспорт».

Внутренние перевозки – внутрипостроечный транспорт строительных организаций.
г) функционирование складского хозяйства.
приемка материалов в хранилища (осуществляется в соответствии с государственными стандартами для каждого вида материала, техническими условиями или дополнительными требованиями согласно договоров о поставках. При нарушении сроков поставки или несоответствии материалов (изделий) указанным условиям строительная организация обязана представить в установленном порядке заводам-поставщикам или транспортным организациям (или тем и другим) рекламации или другие санкции согласно действующего законодательства).
хранение с осуществлением контроля за состоянием запасов материалов по
системе «max-min»: Зпр. max=Зт+Зп+Зг - Зпр. min=Зп+Зг с соответствующим информированием руководства для принятия мер по доведению запасов до нор-
мального уровня.
отпуск материалов – ведут по лимитным картам, определенным на основе производственных норм с сопоставлением фактического расхода материалов на выполненный объем работ с потребностью в них согласно нормативам списания материалов по акту.
4. Склады дорожно-строительных материалов
а) Классификация:
- по способу хранения: открытые; закрытые; комбинированные.
- по форме и типу сооружения:
конусные |
штабельные |
- по способу образования: |
эстакадные (конвейерная загрузка); |
|
бестраншейные (экскаваторные); |
- по продолжительности действия: выгрузочные (погрузочные); резервные (аварийные); специализированные; универсальные.
б) Генплан выгрузочного склада:

в) склады каменных материалов
Способы доставки каменных материалов: железнодорожный, автомобильный, водный транспорт (10%).
Состав складского оборудования:
1)приемное устройство – осуществляет разгрузку транспортных средств, их обработку и выдачу материалов складским устройствам;
2)штабелирующий механизм – осуществляет складирование материалов.
|
ТИПЫ ПРИЕМНЫХ УСТРОЙСТВ |
|
(доставка железнодорожным транспортом): |
а) |
а. ПОВЫШЕННЫЙ ПУТЬ (гравитационный способ) |
|
Платформы, полувагоны, хопперы, думпкары – не ну- |
|
ждаются в средствах разгрузки. |
|
Доставка – щебень, песок |
|
Пр = 10 ваг./час. (лето) |
|
Недостатки: ручной труд – открывание и закрывание |
|
люков, зачистка, выгружаемый материал занимает зна- |
|
чительную территорию (35-50 м в обе стороны). |
б. ПОДРЕЛЬСОВЫЙ БУНКЕР |
б ) |
Достоинство – полная механизация всех |
|
процессов. |
|
Пр = 4 ваг./час. (лето) |
|
Пр = 2-3 ваг./час. (зима) |
|
Оборудование : маневровое устройство, |
|
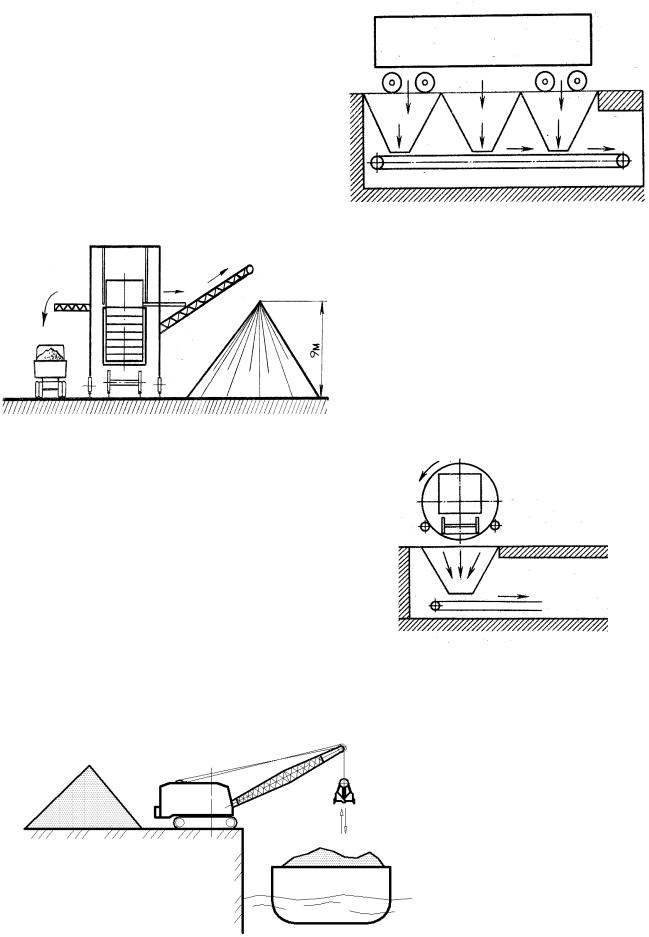
механизмы по закрыванию люков, зачистке и восстановлению сыпучести материала.
в ) |
в. САМОХОДНЫЙ РАЗГРУЗЧИК ТР-2 |
|
Разгрузочно-штабелевочная (конст- |
|
рукция Хабибулина) |
|
Пр = 3-4 ваг./час. |
|
Недостаток - большой объем зачист- |
|
ки (5% - в полувагоне, 3% - на плат- |
|
форме). |
г. РОТОРНЫЙ ВАГОНООПРОКИДЫВАТЕЛЬ |
г) |
Пр = 20-30 ваг./час. |
|
(при объемах 2-2.5 млн. т/год) |
|
(доставка водным транспортом)
д. ЭКСКАВАТОР С ГРЕЙФЕРНЫМ КОВШОМ
ТИПЫ ШТАБЕЛИРУЮЩИХ УСТРОЙСТВ 1) бульдозер, погрузчик, экскаватор