
9459
.pdf21
2.3.3. Грохочение горячих материалов
Из сушильного барабана предварительно отдозированные, нагретые и просушенные материалы поступают в смесительный агрегат (рис.2.20), в состав которого входят:
-ковшовый элеватор 1;
-сортировочное устройство 2;
-бункера горячих материалов 3;
-дозаторы заполнителей и битума 4;
-смесительная установка 5;
-накопительный бункер.
«Горячий» элеватор вертикального или наклонного типа предназначен для подачи смеси песка и щебня от разгрузочного лотка сушильного барабана к сортировочному устройству, где происходит их дальнейшее разделение по фракциям.
Разгрохотка горячих каменных материалов производится на плоских вибрационных (рис.2.21) или барабанных (рис.2.22) грохотах. Виброгрохот состоит из рамы, сит и привода. Сита прикреплены болтами к продольным и поперечным элементам рамы. Натяжение сит производится с помощью натяжного устройства. Привод виброгрохота состоит из электродвигателя, клиноременной передачи и вала с дебалансами. Рама грохотов закреплена на пружинных амортизаторах, что обеспечивает ей вместе с ситами возможность колебательных движений с требуемой частотой. Параметры вибрации: частота - 750 об/мин., амплитуда – 10 мм. Виброгрохот как правило имеет многоярусную конструкцию из 3-4 сит (рис.2.23). Верхнее сито (решетка) служит для отделения негабарита в специальный бункер при помощи лотка. Остальные сита с отверстиями разной величины разделяют минеральные материалы по зерновому составу на четыре группы. Количество материала в каждой группе зависит от размера и формы отверстий на сите. Отверстия грохотов могут иметь круглую, квадратную, прямоугольную и продолговатую форму. Причем на одной сетке могут устанавливаться сита с разными размерами отверстий (более мелкие - ближе к элеватору, более крупные – непосредственно над накопительными бункерами).
В соответствии с ГОСТ 9128 зерновой состав смесей приведен применительно к ячейкам круглой формы. При использовании грохотов с отверстиями с квадратной формой следует руководствоваться переводной табл.2.2.
В процессе прогрохотки до 10% материала заданной крупности может проскочить свой отсек и оказаться в соседнем бункере вследствие явления «выноса», что связано с особенностями передвижения материалов по грохотам. Факторы, влияющие на процент выноса:
-количество материала, подаваемого на грохот («напор на грохот»);
-неравномерная подача минеральных материалов;
-засорение или повреждение отверстий сит;
-настройка грохота (угол, наклона и т.п.).
|
|
Переход от круглых сит к квадратным |
|
Таблица 2.2 |
|
|
|
|
|
Размеры отверстий, мм |
|
|
Круглые |
|
Квадратные |
|
40.0 |
|
31.5 |
|
35.0 |
|
28.0 |
|
30.0 |
|
24.0 |
|
25.0 |
|
20.0 |
|
20.0 |
|
16.0 |
|
15.0 |
|
12.0 |
|
10.0 |
|
8.0 |
|
5.0 |
|
4.0 |
-
Для стабильной работы грохотов требуется постоянный контроль за их состоянием на предмет наличия повреждений или засоренности отверстий. Возможные недостатки системы разгрохотки:
-зерна минерального материала выходят из контакта с поверхностью сит вследствие их провисания или «подпрыгивания» на опорах при центральном расположении вибратора, т.е. в горячей зоне;
-неправильное расположение сит в соответствии с величиной отверстий (крупные частицы закрывают про-
ход для мелких фракций, повышенный износ мелких сит).
Барабанный грохот представляет собой вращающееся цилиндрическое решето с отверстиями определенных размеров, установленное с наклоном. Рассеиваемый материал поступает внутрь барабана на сито с размером 10 мм, далее на участок без отверстий, а затем на сита с отверстиями 20 и 40 мм соответственно. Начальная часть дополнительно охвачена решетом с отверстиями 5 мм. Основной недостаток барабанного грохота – низкое качество прогрохотки вследствие сводообразования на 1/6 длины окружности цилиндра и проскока мелких частиц по длине барабана.
Бункеры горячих материалов служат для временного размещения разделенных по фракциям песка и щебня до их подачи в дозирующую систему. Бункеры оборудуются крышками и лотковыми устройствами для удаления излишков материала при переполнении отсеков, затворами для подачи заполнителя в дозаторы, теплоизоляцией, датчиками контроля за уровнем и температурой материала в бункере.
Общий объем бункеров должен быть пропорционален размеру смесительного агрегата (мешалки) и рассчитан на хранение не менее получасового запаса минеральных заполнителей при бесперебойной работе завода. Все бункеры имеют разные размеры. Относительное распределение объема бункеров: отсек №1 для фракции 0-5 мм – 40%, отсек
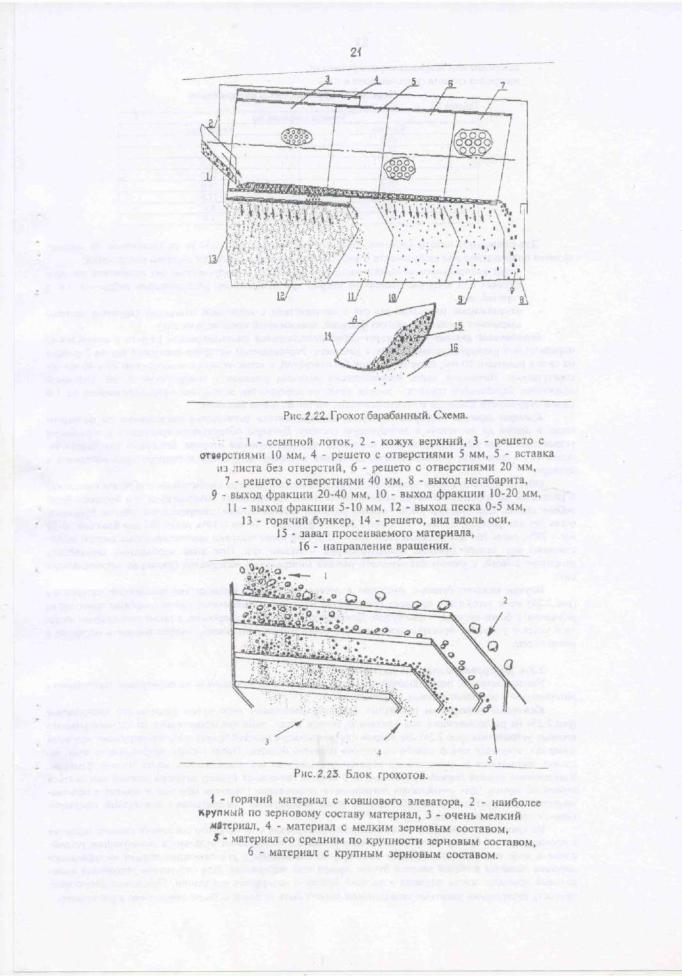
22
23
№2 для фракции 5-10 мм – 30%, отсек №3 для фракции 10-20 мм – 20%, отсек №4 для фракции 20-40 мм – 10%. При приготовлении крупнозернистых смесей задействованы все четыре бункера, мелкозернистых – только три. При этом необходимо пересчитать рецептуру смесей, с учетом фактического рассева минеральных материалов (размеров установленных сит).
Внутри каждого бункера, особенно в отсеке №1, может наблюдаться расслоение материалов (рис.2.24) из-за того, что в процессе прогрохотки мелкие фракции имеют прямолинейную траекторию движения, а более крупные – изогнутую. Для недопущения данного явления, а также скапливания мелочи в углах и у стенок, бункеры дополнительно оборудуются пластинами, направляющими материал в центр отсека.
2.3.4. Дозирование горячих материалов
Непосредственно перед подачей инертных заполнителей в смеситель их подвергают тщательному дозированию с помощью весовых устройств.
Каменные материалы различных фракций взвешивают либо путем раздельного дозирования (рис.2.25) на расположенных под каждым бункером весах, либо последовательно на «суммирующих» весовых устройствах (рис.2.26). Во втором случае сначала в весовой бункер-дозатор загружают крупный материал, открывая затвор одного из отсеков горячего бункера. После набора необходимого веса, заслонка закрывается и, аналогичным образом отгружаются все последующие более мелкие фракции. Взвешивание каждой порции происходит за 5 секунд. Расходный бункер дозатора должен заполняться строго по центру. Для уменьшения погрешности дозирования (главным образом в момент открытия-закрытия затворов) циферблатные головки весов оборудуются специальными контактами предварительной отсечки материалов.
Из хранилища силосного типа минеральный порошок в не нагретом состоянии сначала подается в промежуточный бункер. Если смесительная установка оборудована отдельным дозирующим устройством в виде питателя или весового дозатора, то отвешенная с его помощью порция минерального порошка подается в общий весовой бункер поверх всех материалов. При отсутствии устройства минеральный порошок всегда подается в весовой бункер и дозируется последним. Предельно допустимая точность дозирования инертных заполнителей должна быть не более 3% по отношению к расчетному.
Тарирование дозирующей системы включает проверку правильности показаний весов в сравнении с эталоном. В качестве эталона на весы ставят набор грузов из 10 гирь массой по 25 кг каждая и сравнивают показания весов с истинными значениями. То же самое производится в случае тарировки битумных дозаторов весового типа. В обоих случаях относительная погрешность не должна превышать 0.5%.
2.3.5. Дозирование битума и ПАВ
Для дозировки битума и ПАВ используют объемные или весовые дозаторы, область применения которых зависит от технологической схемы приготовления асфальтобетонных смесей.
Типы битумных дозаторов:
-поплавковые (установки циклического действия);
-насосы-дозаторы с нерегулируемой и регулируемой производительностью (установки непрерывного действия);
-весовые (современные установки периодического действия).
Дозатор поплавкового типа (рис.2.27) работает по следующему принципу. Из расходной емкости битум по трубопроводу через кран 2 поступает в металлическую емкость 4, снабженную тепловой рубашкой для ее обогрева, подводящих и отводящих магистралей 5. Количество дозируемого битума определяется по шкале 7, соединенной стальным тросиком 6 с поплавком 3. Отдозированный битум через сливной кран 1 с помощью шестеренчатого насоса подается в смеситель. При этом шестеренчатый насос создает избыточное давление в обеих магистралях.
Насосы-дозаторы (рис.2.28) непрерывного действия бывают трех типов:
1 тип – насос переменного объема с постоянной скоростью электродвигателя; 2 тип – насос постоянного объема с переменной скоростью электродвигателя; 3 тип – насос постоянного объема с постоянной скоростью электродвигателя.
В первом случае количество откачиваемого из расходной емкости битума регулируется производительностью (объемом) насоса. Объем насоса устанавливается автоматически в зависимости от количества подаваемого в смеситель минерального материала. При отсутствии потребления битума последний циркулирует в системе насос – расходомер – клапан - (расходная емкость).
При второй схеме количество битума регулируется изменением числа оборотов электродвигателя, которое также пропорционально подаче минерального заполнителя.
Третий тип предполагает, что расход битума определяется положением дополнительного дозирующего клапана, установленного в цепь между насосом и расходомером. При этом клапан пропускает через расходомер требуемое количество битума в смеситель, а излишки отправляет назад в расходную емкость. Положение дозирующего клапана определяется расходом минеральных материалов. Измерение количества поданного битума во всех трех случаях производят с помощью расходомера.
С увеличением температуры нагрева резко уменьшается вязкость и соответственно увеличивается объем подаваемого битума. Поэтому для обеспечения точности дозировки вяжущего при использовании дозаторов объемного типа необходимо вводить поправку на температуру битума, определяющую его плотность в момент смешения с минеральным заполнителем. В России стандартной температурой считается 20оС по Цельсию (за рубежом 60 оС по
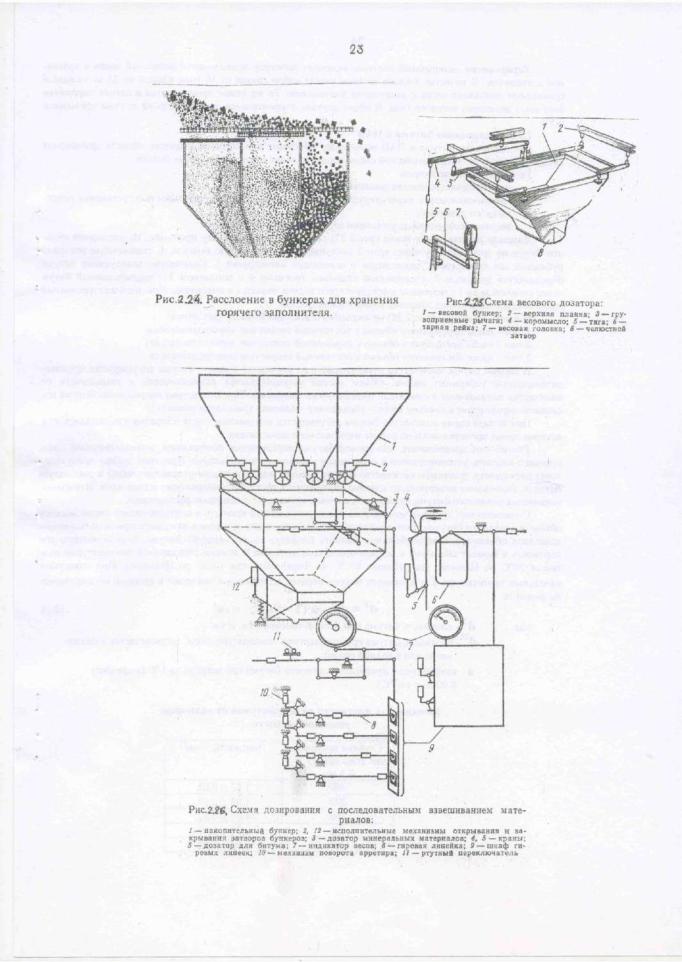
24
25
Фаренгейту иди 15 оС по Цельсию). При известных начальных температуре T и плотности битума перевод из объемных значений в весовые осуществляют по формуле:
|
dT = d20 – a (T – 20) , г/ см3 |
(2.1) |
где: |
dT - плотность битума при данной температуре, г/ см3 ; |
|
d20- плотность битума при стандартной температуре, г/ см3 (определяется в пикнометре или в водной среде);
a - коэффициент изменения плотности битума при нагреве на 1 оС (в среднем
0.0006 г/ см3 оС).
Зависимость плотности вязких битумов от величины условной вязкости
Таблица 2..3
Глубина проника- |
Плотность, г/ см3 |
ния иглы при 25 оС, |
|
0.1 мм |
|
300 |
1.02 0.02 |
200 |
1.02 0.02 |
100 |
1.03 0.02 |
50 |
1.03 0.02 |
25 |
1.04 0.02 |
Современные расходомеры вместе с расходом измеряют температуру проходящего через них битума и направляют эту информацию на пульт управления (плотность вводится в компьютер заранее). Компьютер вычисляет объем битума, поступившего в смеситель, и преобразует это значение в вес с выводом на дисплей. В некоторых системах компенсация температурного расширения битума устанавливается непосредственно в расходомере и затем автоматически выводится на дисплей пульта управления.
Схема подачи битума в смеситель с помощью весового бункера-дозатора приведена на рис. 2.29.
Вне зависимости от системы дозирования битумный насос всегда соответствующим образом должен изменять объем проходящего через расходомер битума в зависимости от количества отдозированного минерального материала (либо агрегатом питания, либо весовым бункером-дозатором). Для этого в системе подачи битума устанавливается таймер задержки, обеспечивающий приведение в соответствие заданных объемов. Требуемая точность дозирования битума и ПАВ должна составлять не более 1.5%.
Причины возможных сбоев в системе дозирования битума (количество подаваемого в смеситель битума отличается от показаний на пульте управления):
-показания компьютера отстают от объема, пропускаемого расходомером (инерционность компьютера в учете температуры окружающего воздуха, в особенности в жаркую погоду);
-образование нагара и коксование битума в системе подачи битума (необходимость прочистки выжиганием,
промыванием, механическим путем и т.п.).
Тарирование битумных дозаторов производят путем закачивания битума в мерную емкость с заранее известным весом. Далее определяется фактический вес этого битума и сравнивается с показаниями расходомера, умноженными на температурную поправку. Система считается оттарированной при относительной погрешности не более 1%.
2.3.6. Смешение компонентов асфальтобетонных смесей
Объединение инертных заполнителей с битумом производят в смесителях циклического или непрерывного действия с принудительным (свободным) перемешиванием. Независимо от конструкции смесители должны обеспечивать быстрое и равномерное распределение материалов, составляющих асфальтобетонную смесь, качественное обволакивание битумом поверхности минеральных зерен при минимальной затрате энергии.
На асфальтобетонных заводах, работающих по традиционной технологии, как правило, установлены двухваль-
ные мешалки циклического действия с принудительным перемешиванием (рис.2.30) с внешним обогревом и емкостью рабочей камеры от 600 до 3000 кг. Вращение валов с укрепленными на них лопастями происходит в противоположных направлениях. Эффект смешивания зависит от конструкции лопастей и их компоновки на валу: угла
наклона лопаток к плоскости вращения , центрального угла между соседними лопастями по окружности, и шага
(расстояния) а между лопастями на самом валу (рис.2.31). Подобная конструкция обеспечивает поточно-контурное перемещение материала внутри мешалки с интенсивным массообменом составляющих смеси. Качество смешения повышается с увеличением скорости вращения валов с одновременной подачей битума под давлением в распыленном состоянии. Опыт эксплуатации показывает, что перемешивание материалов в данном случае заканчивается практически одновременно с окончанием поступления в смеситель битума. Выгрузка смеси производится через люк, расположенный в донной части смесителя.
В установках с принудительным перемешиванием непрерывного действия смесь перемещается непрерывным потоком с постоянной скоростью от загрузочного устройства к разгрузочному при вращении продольных валов. Из
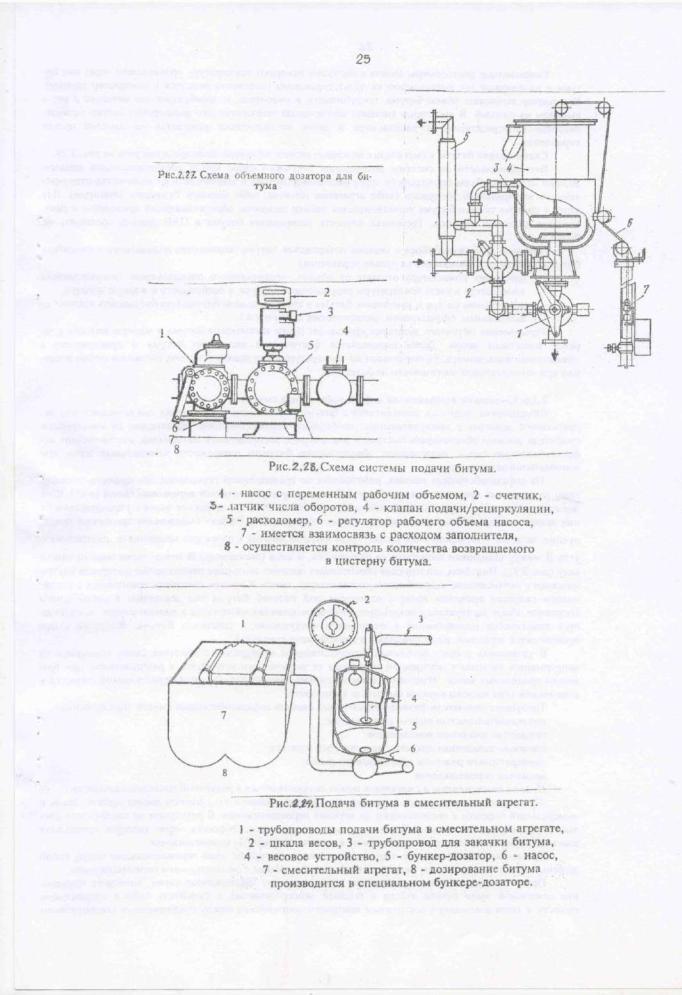
26
27
менение времени перемешивания регулируется перестановкой лопастей и изменением угла наклона корпуса смесителя к горизонту.
Требуемые показатели физико-механических свойств асфальтобетонных смесей определяются: последовательностью подачи компонентов; точностью дозировки компонентов; степенью заполнения емкости смесительного агрегата;
температурным режимом приготовления смеси; временем перемешивания.
Подача компонентов в смеситель может осуществляться в различной последовательности.
При использовании кислых пород (гранит, диорит, сиенит и т.п.) сначала вводят щебень, песок и минеральный порошок с последующим их «сухим» перемешиванием. В результате на поверхности кислых пород образуется тонкая оболочка из зерен минерального порошка, через которую происходит взаимодействие всех компонентов с битумом в процессе «мокрого» перемешивания.
Применяя основные горные породы (известняки), на первом этапе перемешиваются между собой щебень, песок и битум, а затем вводится минеральный порошок с окончательным перемешиванием.
Приготовление смесей на установках, работающих по традиционной схеме, возможно применение циклонной пыли сухого отбора с подачей непосредственно в смеситель либо в специальную емкость, а затем в мешалку с постоянным контролем соотношения между кондиционным (карбонатным) порошком и кислой пылью. При совместном использовании этих компонентов всегда сначала дозируется минеральный порошок.
Номинальная емкость смесителя определяется его размерами (рис.2.32). Загрузка излишнего количества заполнителя приводит к тому, что материал, расположенный над лопастями, не перемещается в нижнюю часть мешалки
ине перемешивается с битумом (рис.2.33). Если материала недостаточно, то он разбрасывается лопастями по смесителю и также не перемешивается с битумом (рис.2.34). Количество подаваемого материала должно быть постоянным
исоответствовать оптимальному объему замеса (немного меньше номинальной емкости смесителя). При отсутствии бункера-накопителя объем замеса назначают по грузоподъемности автосамосвала, транспортирующего смесь к месту укладки. Например, при емкости смесителя 3 тонны и вместимости кузова 14 тонн объем замеса целесообразно принять в 2.8 тонны с загрузкой самосвала за 5 приемов. Постоянный объем замеса – важный фактор обеспечения стабильности характеристик выпускаемой смеси.
Температурный режим приготовления смеси определяется ГОСТ 9128 и ГОСТ 12801 (см. табл.2.1). При при-
менении битумополимерных вяжущих, а также приготовлении смесей для высокоплотного асфальтобетона допускается увеличивать температуру готовых смесей на 10-20 оС в целях обеспечения удобоукладываемости.
Оптимальное время перемешивания зависит от вида смеси и технических характеристик смесителя. Условия приготовления смесей в лаборатории существенно отличаются от производственного режима, что приводит, как правило, к разным результатам в подборе составов. В асфальтосмесителях время принудительного перемешивания значительно меньше, а эффективность объединения компонентов выше за счет влияния объемного фактора (емкость закрыта, отсутствует контакт битума с воздухом). Процесс перемешивания асфальтобетонных смесей делится на два этапа - «сухое» и «мокрое».
«Сухое» перемешивание исчисляется от начала объединения минеральных заполнителей до момента подачи битума в мешалку (7-15 сек). Основные цели данного этапа:
–дезагреграция частиц минеральных материалов;
–обеспечение теплообмена между горячим щебнем, песком и холодным минеральным порошком;
–заполнение емкости минеральными материалами с тем, чтобы битум не вытекал через заслонку в нижней
части смесителя.
«Мокрое» перемешивание начинается с момента подачи битума через распределительные устройства, расположенные по центру над валами мешалки. В зависимости от способа (под давлением с помощью насоса, самотеком) подача битума длится не более 5-10 сек. При удовлетворительном состоянии лопастей и оптимальной степени заполнения смесителя общее время мокрого перемешивания на современных установках не превышает 20-30 сек. В целях предотвращения коксования битума продолжительность мокрого перемешивания следует сводить к минимуму до полного обволакивания минеральных частиц. Экспериментально установлено, что в первые 10 секунд битумом покрываются частицы крупностью до 0.63 мм, за 20 секунд – до 5 мм, за 30 секунд – происходит полное перемешивание. Дальнейшее увеличение времени перемешивания может привести к ухудшению качества смеси (рис.2.35). Продолжительность перемешивания тесно связана с количеством вводимого битума: увеличивая время, необходимо снижать содержание вяжущего.
Рекомендуемое время перемешивания в смесительных |
|||
|
установках отечественного производства |
||
Таблица 2.4 |
|
|
|
Вид смеси |
|
Продолжительность перемешивания смесей, сек. |
|
|
«сухое» |
«мокрое» |
|
|
|
||
Песчаные |
|
15 |
45-60 |
Мелкозернистые |
|
15 |
30-45 |
Крупнозернистые |
|
|
20-30 |
(пористый асфальтобетон) |
|
- |
|
|
30-50 |
||
(высокопористый асфальтобетон) |
|
|
|
|
|
|
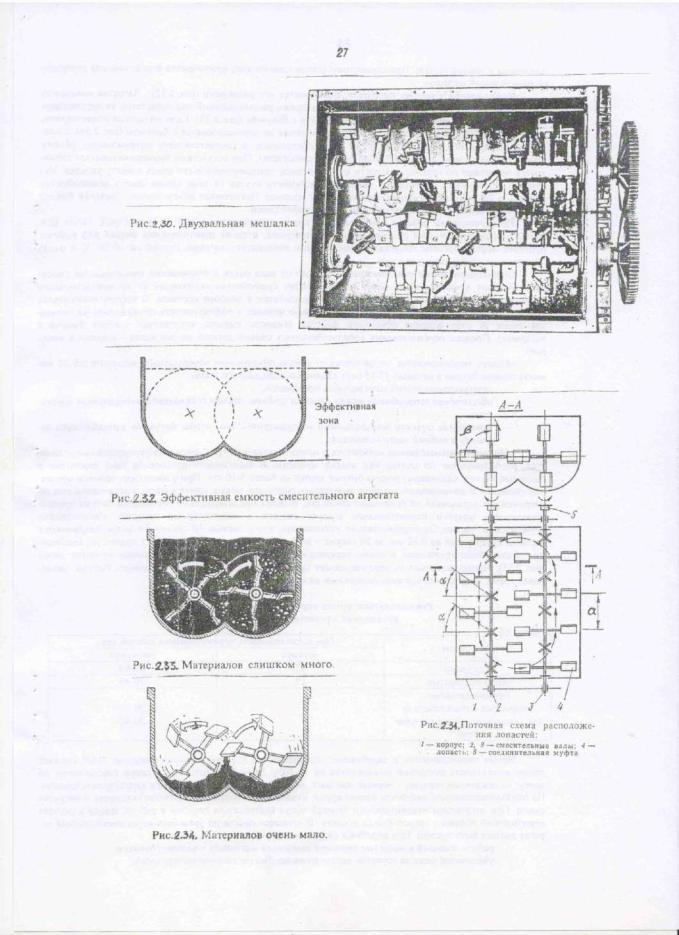
28
29
Время перемешивания в зарубежных смесителях в 1.5-2 раза меньше. Введение ПАВ снижает продолжительность смешения компонентов на 15-30%. Визуально готовность смеси определяется по цвету: на осадочных породах – черный матовый, на изверженных – коричневый с характерным блеском. На производительность смесителя влияет время, отводимое на открытие (закрытие) заслонок и выгрузку смеси. При отсутствии накопительного бункера могут наблюдаться перебои в работе завода в случаях неритмичной поставки транспортных средств. В процессе ожидания автосамосвалов смесительный агрегат должен быть пустым. При подобных ситуациях допускается:
-работа лопастей в холостом режиме с задержкой материала в весовом бункере;
-увеличение режима «сухого» перемешивания (без расслоения материалов); Категорически запрещается увеличивать время «мокрого» перемешивания.
2.3.7. Хранение готовых смесей
Для обеспечения бесперебойной (независимой от транспорта, режима укладки, погодных условий и т.п.) работы заводов, а также снижения энергоемкости производства и износа технологического оборудования, готовые смеси направляют для временного хранения в бункеры-накопители. К достоинствам бункеров следует отнести: возможность отгрузки смеси при поломке агрегатов, уменьшение времени простоя автосамосвалов, отпуск смеси в количествах, некратных замесу, увеличение производительности смесителя за счет сокращения операций по запуску и остановке машин.
Предельно допустимое время пребывания горячих смесей в бункерах зависит от вида, типа смеси и марки вяжущего, определяющих температуру нагрева. Согласно СНиП 3.06.03 продолжительность хранения смесей, предназначенных для укладки в нижний слой покрытия, и смесей типа А для верхнего слоя не должна превышать 1.5 часов, для всех других типов – 0.5 часа. Смеси на основе ПАВ, активированных порошков, полимеров допускается хранить до 2 и 1 часа, а приготовленные с применением битума БНД 40/90 – хранению вообще не подлежат. Подобные ограничения связаны с необратимыми термоокислительными процессами, происходящими с отечественными битумами при их длительном пребывании в диапазоне рабочих температур. Старение и ухудшение свойств битума происходит тем интенсивнее, чем выше его начальная вязкость. Кроме того, смеси на маловязких битумах склонны к дополнительному расслаиванию за счет стекания вяжущего в нижнюю часть бункера. Другим недостатком бункеровнакопителей является сегрегация минерального заполнителя при погрузо-разгрузочных работах.
Вместимость накопительного бункера должна составлять не менее объема часовой производительности смесительной установки. Бункеры размещают либо непосредственно под смесителем, либо рядом с ним. Количество отсеков может меняться от одного до семи в зависимости от конструктивных особенностей смесителя и завода в целом. В состав накопителя входят:
-транспортирующее (загрузочное) устройство;
-расходный бункер;
-разгрузочная воронка;
Подача асфальтобетонной смеси из мешалки в накопитель производится при помощи загрузочного устройства в виде скребковых или ленточных транспортеров (рис.2.36), ковшовых элеваторов, скиповых подъемников, вагонеток. Наибольшее распространение получили скребковые транспортеры, выполненные из металлических пластин, скреплённых в единую цепь, и ленточные – из жаростойкой прорезиненной ткани.
Расходный бункер с крышкой оборудуются теплоизоляцией из минеральной ваты или другого пористого материала толщиной 70 мм. Корпус бункера не подогревается, а требуемая температура смеси поддерживается за счет тепла, полученного в процессе приготовления. Бункеры оборудуются датчиками наличия материалов с выводом сигнала на пульт управления. По форме бункеры бывают цилиндрические, овальные, эллиптические, прямоугольные и квадратные. Применение цилиндрических бункеров снижает эффект расслоения смесей.
Постоянному обогреву подлежит разгрузочная воронка с затвором, расположенным в ее нижней части. Обогрев производят с помощью электроэнергии или масляного теплоносителя. В зависимости от модели угол при вершине воронки составляет 55-70о для выгрузки смеси без расслаивания (уровень смеси не должен опускаться ниже уровня верха воронки). Смеси высыпаются самотеком через затвор, оборудованный шиберными или секторными устройствами. Для улучшения выгрузки и снижения коэффициента трения смеси о стенки бункера все сврные швы на его внутренней поверхности шлифуют.
Расслоение (сегрегация) смесей, в особенности крупнозернистых, может происходить как при загрузке, так и при разгрузке бункера. Подача материала в бункер должна производиться строго по центру или равномерно в разные части бункера с помощью щитков-рассекателей. Наилучший эффект наблюдается при использовании промежуточных бункеров. Промежуточный бункер (рис.2.37) имеет объем, равный нескольким замесам. При выгрузке за счет большей массы и соответствующей скорости падения компоненты смеси при контакте с накопительным бункером равномерно распределяются по всему сечению без образования конуса. Промежуточный бункер должен быть оснащен таймером для закрытия заслонок через определенные промежутки времени, чтобы в нем всегда оставалось небольшое количество смеси.
Во избежание расслоения смесей при выгрузке заслонки разгрузочной воронки должны легко и быстро открываться (закрываться). Прерывать выгрузку можно только для равномерно подачи в разные части кузова автосамосвала, т.е. за несколько приемов. Не рекомендуется выгружать асфальтобетонную смесь в кузов непрерывным потоком, медленно продвигая автосамосвал вперед. Оператор должен уметь определять время, необходимое для отгрузки каждой порции визуально. Не следует отгружать смесь маленькими порциями, непрерывно открывая и закрывая заслонки, в особенности при расположении бункеров над взвешивающей платформой. Это чаще всего практикуется при необхо
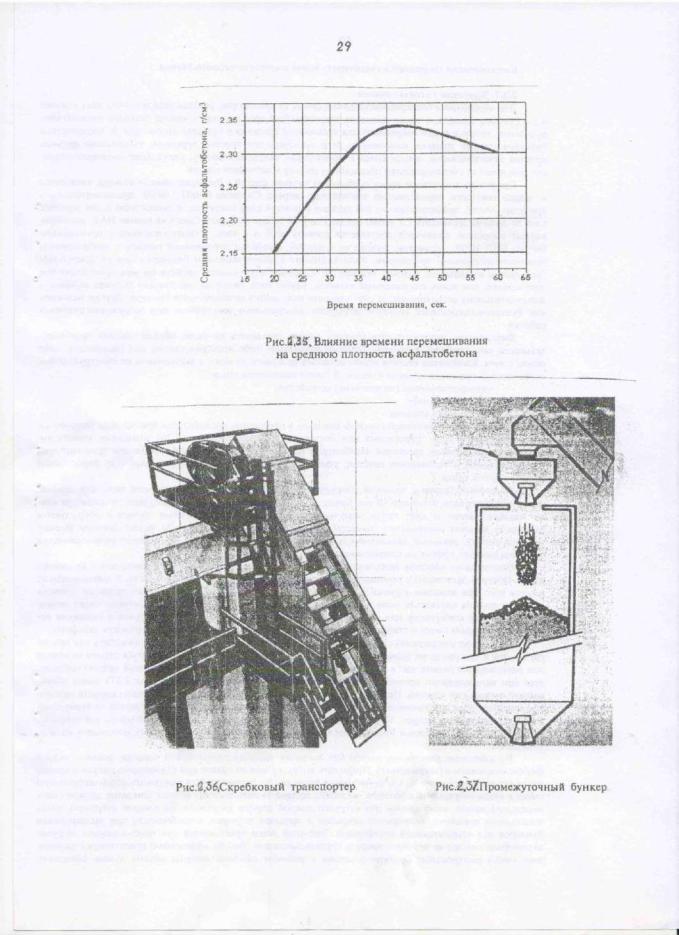
30