
3421
.pdf
9
тизированных аппаратах. К достоинствам напорного электролиза следует также отнести высокую компактность аппаратов, отсутствие пассивации электродов, увеличение массообмена реагирующих веществ, увеличение выхода вещества по току до 90% (в безнапорных около 60 %), возможность использования электролизера в качестве сатуратора, что позволяет отказаться от громоздких, низкоэффективных отстойников.
Для изучения параметров процесса в напорных электрокоагуляторах была разработана специальная конструкция электролизера лабиринтного типа. Общий вид аппарата приведен на рис. 2, схема электролизера на рис. 3.
Эффект очистки в напорных электрокоагуляторах составил: по фтору до 100%; по тяжелым металлам 98-99%; по ХПК - 60-70%. Затраты электроэнергии на обработку стоков снизились по сравнению с безнапорным режимом на40-60%.
В результате проведенных исследований получены математические зависимости эффекта очистки от основных параметров процесса. Оценка эффективности процесса определялась по основному загрязняющему параметру - фтор-иону. Эффективность очистки определялась по остаточной концентрации загрязнений (мг/л) в очищенной жидкости.
(6)
где KI, К2, Кз - размерные параметры, T - продолжительность процесса, с.
Значения параметров К1, К2, Кз, в зависимости от концентрации фторионов в исходной жидкости и величины тока на аноде, определяется по эмпи-
рическим формулам.
Зависимость дозы алюминия на обезвреживание фтор-ионов от продолжи-
тельности обработки и плотности тока аппроксимируется уравнениями
m = K1 . T + K3 |
m =К4 . T+ K5 |
, |
(7) |
|
|
|
где K4 , K5 - параметры, определяемые по эмпирическим формулам, полученным на основе аппроксимации данных экспериментов.

10
Таблица 1
Характеристики отдельных потоков фторсодержащих сточных вод.
Наименование |
Исходная |
Химическая |
Молек. |
Кол-во ки- |
|
концен- |
формула |
вес |
слорода на |
|
трация, |
|
|
окисление |
|
мг/л |
|
|
1 мг |
|
Механические примеси |
|
|
|
Стеклянная и абразивная |
0.2 |
|
|
|
пыль |
|
|
|
|
Окалина |
57.0 |
с |
|
|
Наждачная пыль |
10.0 |
|
|
|
|
Органические вещества |
|
|
|
Трихлорэтилен |
62.0 |
C2H3Cl3 |
131.4 |
0.67 |
Ксилол |
54.0 |
С6Н4(СН3)2 |
106.2 |
3.33 |
Диоксан |
127.0 |
C4H8O2 |
88.1 |
1.81 |
Ацетон |
1.0 |
C3H6O |
58.1 |
2.20 |
Сольвент-нафта |
56.0 |
- |
- |
- |
Краска ПФН-26 |
28.0 |
- |
- |
- |
Краситель |
9.4 |
- |
- |
- |
Фоторезист |
127.0 |
- |
- |
- |
Растворитель 647 |
57.0 |
- |
- |
- |
Нитроэмаль МЛ12 |
28.0 |
- |
- |
- |
ЛакХВ-784 |
30.0 |
- |
- |
- |
Масла (нефтепродукты) |
0.2 |
- |
- |
- |
Спирт |
0.83 |
C2H5OH |
46.0 |
- |
Бензин |
0.0023 |
- |
- |
- |
|
Минеральные вещества |
|
|
|
Соляная кислота |
140.0 |
HCl |
36.5 |
- |
Перекись водорода |
23.0 |
H2O2 |
34.0 |
- |
Аммиак |
11.0 |
NH4OH |
35.0 |
- |
Фосфорная кислота |
14.0 |
H3PO4 |
- |
- |
Азотная кислота |
10.0 |
HNO3 |
63.0 |
- |
Кремниевая кислота |
15.0 |
H2SiO3 |
- |
- |
Плавиковая кислота |
42.0 |
HF |
19.0 |
- |
Фтористый аммоний |
40.0 |
NH4F |
37.0 |
- |
Серная кислота |
180 |
H2SO4 |
98.0 |
- |
Hикель |
1.8 |
NiSO4 |
- |
- |
Цинк |
2.6 |
ZnSO4 |
- |
- |
Медь |
1.06 |
CuSO4 |
- |
- |

Al/ F
0.5А/Дм2
1.0А/Дм2
2.0А/Дм2
Т,с
Рис. 1. Изменение дозы алюминия при электрокоагуляции в зависимости от продолжительности
Расчетная продолжительность обработки жидкости в электрокоагуляционных аппаратах определена по уравнению.
(8)
где K6, K7, K8, K9 определяются по эмпирическим формулам. Исследования по электрокоагуляции показали высокую эффективность
метода при очистке стоков от фтор-иона (ок.100%). Однако эффект очистки от органических веществ (по ХПК) даже в напорных аппаратах не превышал 70%, что не отвечает современным требованиям при создании оборотных систем водопользования. Эта задача может быть успешно решена путем электрохимической деструкции органических веществ в электрохимических аппаратах с нерастворимыми электродами. В опытах в качестве электродов использовались в основном аноды из графита и титана, покрытые смесью двуокиси титана и рутения. Исследования проводились в безнапорном и напорном режимах.

Подача исходной |
твод |
сточной |
жидкости |
жидкости |
|
Рис. 2. Схема напорного электрокоагулятора:
1 - входная камера; 2 - выходная камера; 3,4- патрубки подачи и отвода
жидкости; 5 - манометр.
Ввод реагента
Подача
исходной
жидкости
Отвод
обработанной
жидкости
Рис 3. Схема экспериментальной установки:
1 -усреднитель; 2 - насос; 3 - смеситель; 4 - напорный электрокоагулятор;
5 - выпрямитель.
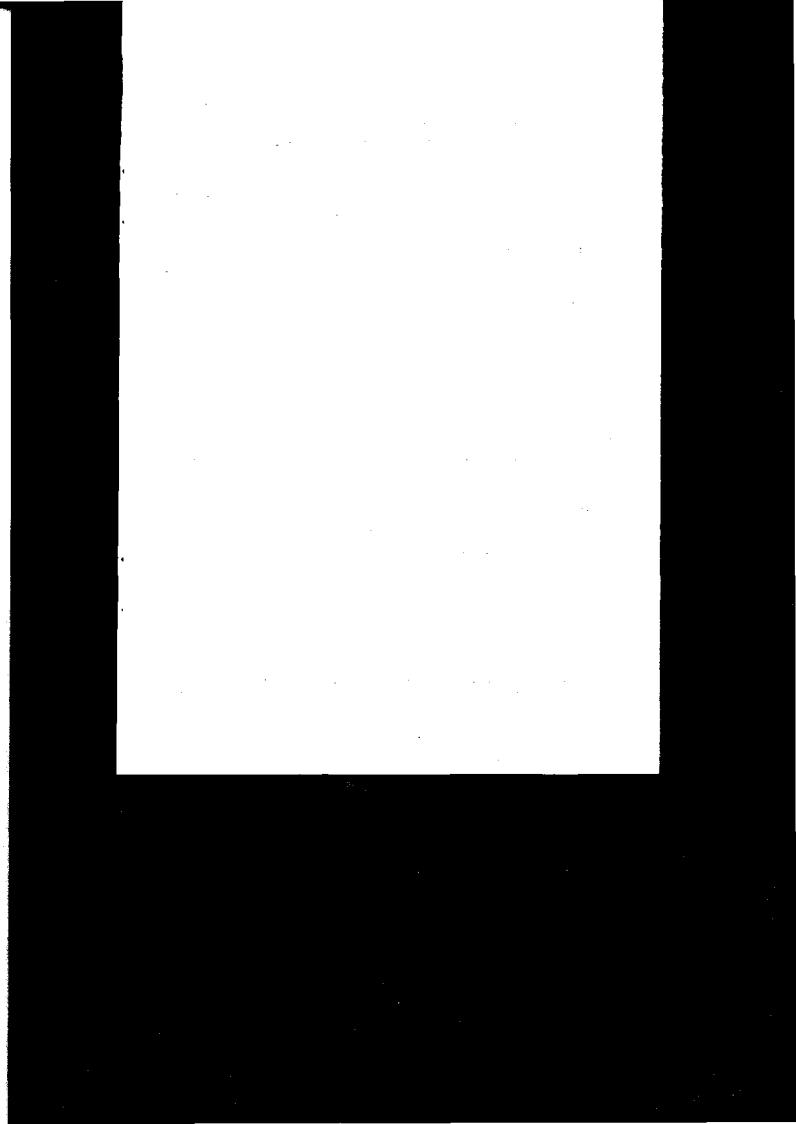
13
При электролизе протекают сложные окислительно-восстановительные процессы на электродах и в объеме обрабатываемой жидкости. Процесс интенсифицируется при наличии в обрабатываемой жидкости хлор-соединений, с образованием «активного» хлора. В результате электрохимических процессов, протекающих в электролизере, органические соединения подвергаются деструкции: легкоокисляемые разрушаются полностью, трудноокисляемые - частично.
Электролиз фторсодержащих стоков обеспечивает весьма высокую степень очистки по ХПК (до 85-90% в напорных аппаратах).
Как показали исследования, при последовательной обработке фторсодержащих стоков электрокоагуляцией и электролизом достигается весьма высокий эффект: при электрокоагуляции эффективно удаляется фтор и металлы; при электролизе эффективно удаляется органика. То есть, каждый из методов решает свою специфическую задачу, но в целом требуемого результата не обеспечивает. В связи с этим были проведены исследования по комбинированнойсхеме.
Вбезнапорном режиме: электрокоагуляция - отстаивание - электролиз; электролиз — электрокоагуляция - отстаивание.
Внапорном режиме: электрокоагуляция - электролиз - флотация; электролиз - электрокоагуляция - флотация. При этом, процесс электролиз - электрокоагуляция и наоборот, проводился в одном двухкамерном аппарате, без
разрыва струи. Результаты испытаний приведенных схем представлены в табл. 2.
Представленные результаты испытаний свидетельствуют о наибольшей эффективности четвертой схемы: электролиз - электрокоагуляция - флотация. Промышленные испытания подтвердили этот вывод.
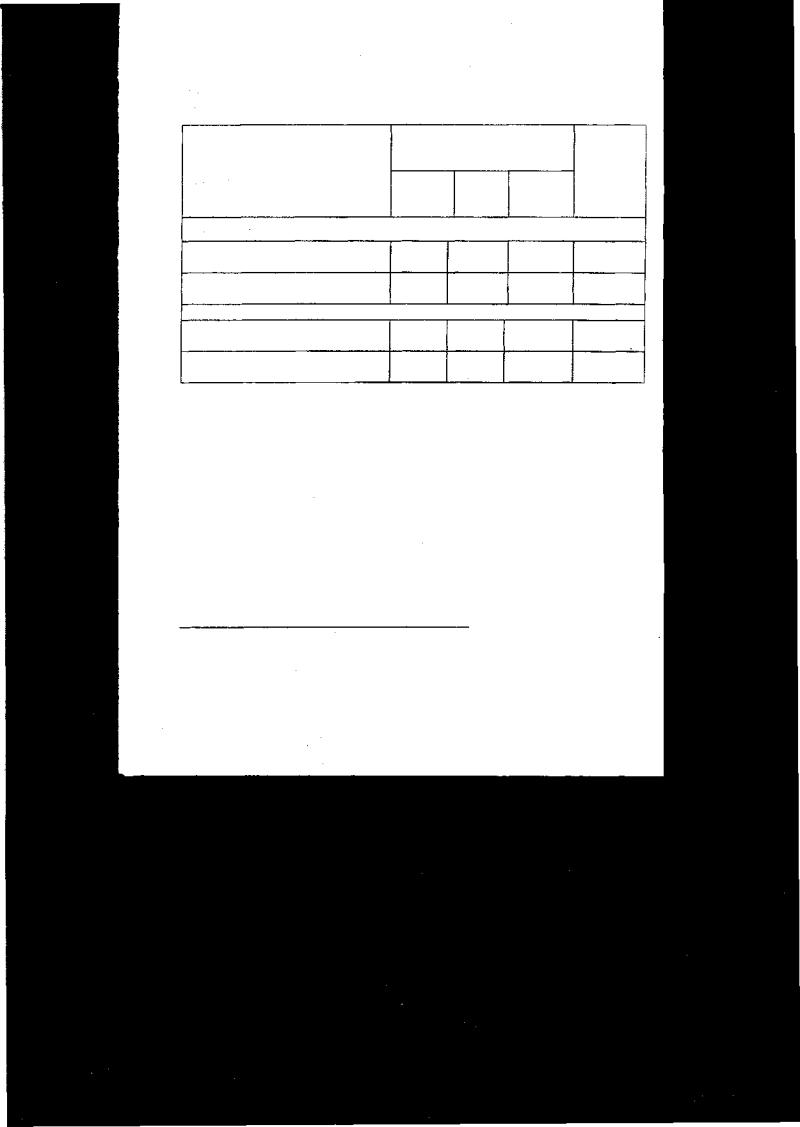
14
Таблица 2.
Сравнительная оценка очистки фторсодержащего стока при
различной технологической организации электрохимической обработки.
Последовательность процесса обра- |
Эффект очистки, % |
Затраты |
||
ботки |
|
|
|
электро- |
|
|
|
|
энергии |
|
по F-иону |
поХПК |
по метал- |
в отно- |
|
|
(макс) |
лам |
сительных |
|
|
|
|
единицах* |
Безнапорныйрежим обработки |
|
|||
Электрокоагуляция- |
99 |
80.0 |
9100 |
1 |
электролиз-отстаивание |
|
|
|
|
Электролиз-электрокоагуляция- |
99 |
80.0 |
Ξ100 |
0.9 |
отстаивание |
|
|
|
|
Напорный режим обработки |
|
|
||
Электрокоагуляция- |
99 |
90.3 |
=100 |
0.84 |
электролиз-флотация |
|
|
|
|
Электролиз - |
99 |
92 |
=lOO |
0.60 |
электрокоагуляция - флотация |
|
|
|
|
В четвертой главе приводятся результаты исследований по изучению продуктов электрохимической деструкции загрязнений фторсодержащих промстоков. В ходе электрокоагуляции и электролиза за счет электродных и химических процессов, протекающих в объеме обрабатываемой жидкости, происходит деструкция органических веществ. Изучение продуктов электрохимической деструкции позволило выявить характер основных процессов, протекающих при электролизе, установить степень токсичности очищенных стоков и тем самым создать условия для оптимизации технологических параметров очистки и разработать рациональную схему очистки.
* относительные затраты электроэнергии для последовательной обработки электро- коагуляцией-электролизом-отстаиванием приняты равными 1, для остальных процессов в долях единиц.
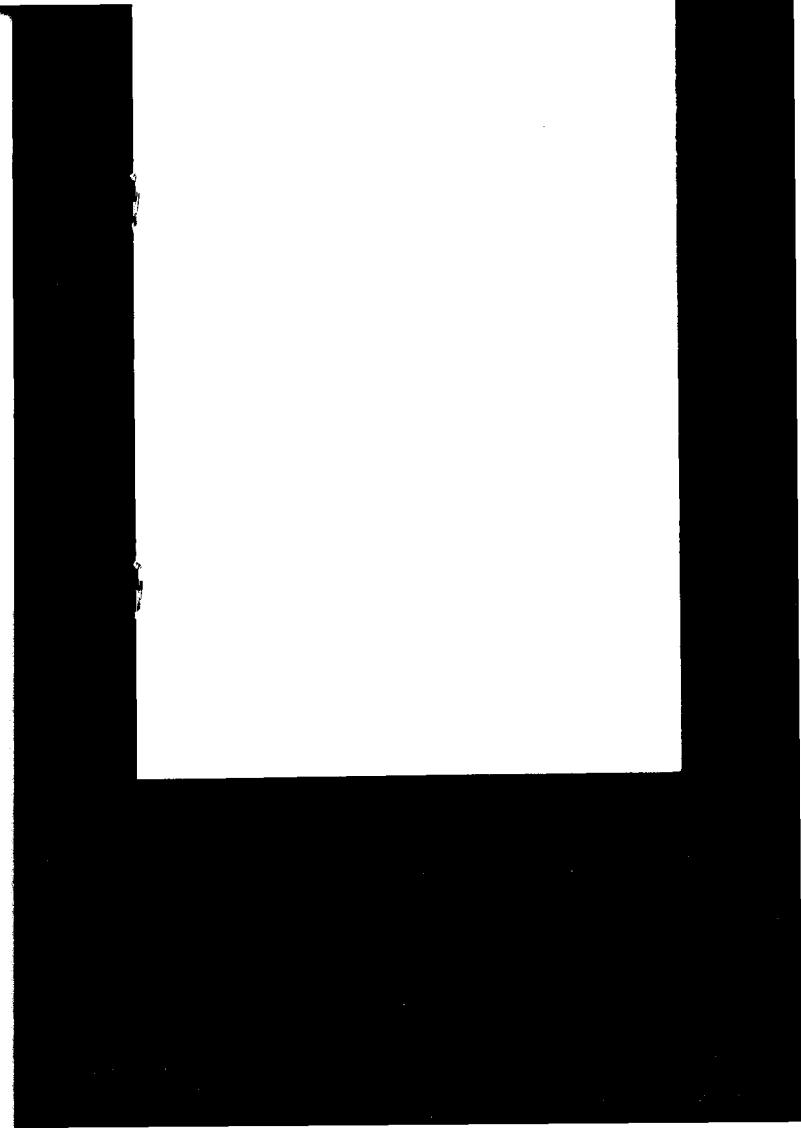
15
Исследования проводились на модельных растворах и реальных сточных водах. Объекты исследований подвергали электрохимической обработке в присутствии хлористого натрия (около 1 г/л). Концентрация органических веществ составляла по ХПК 140 - 200 мг/л. В обработанной жидкости определяли продукты деструкции. Извлечение и разделение продуктов деструкции производили методом тонкослойной хроматографии. Для разделения смеси образующихся веществ использовали адсорбционную, распределительную и ионообменную хроматографию. Идентификацию выделенных веществ, функциональных групп и сложных фрагментов молекул, а также внутримолекулярного и межмолекулярного взаимодействия осуществляли при помощи инфракрасной и ультра-
фиолетовой спектроскопии и ядерно-магнитного резонанса.
В ходе исследований установлено, что смесь деструктированных ве-
ществ состоит из двух групп: группа (А) менее полярная, включающая 5 ком-
понентов; группа (Б) - 20 - 25 компонентов. Весовое соотношение веществ составляло: неполярных 25%, полярных 75%. В процессе идентификации наиболее представительных (по массе) веществ определено несколько индивидуальных соединений, в частности: дициклогексил, бензидиновый эфир пропионовой кислоты, сульфонафталин. Хлорорганических соединений не обнаруже-
но.
На основании прогнозных расчетов определена концентрация индивидуальных продуктов деструкции загрязнений (100 мг/л по ХПК). Она составила: ароматических и алифатических углеводородов до 3 мг/л; сложных эфиров до 6 мг/л; карбоновых кислот жирного ряда 4 мг/л; фенолов до 2 мг/л. Концентрация каждого из этих веществ в обработанной жидкости не превышала ПДК для вод, направляемых на биохимическую очистку.
Пятая глава посвящена доочистке сточных вод, прошедших стадию электрохимической обработки, с целью создания оборотных систем водопользования. Задача доочистки заключалась главным образом в удалении остаточных взвешенных веществ, выносимых из отстойника или камеры флотации и дехлорирования. В качестве средств доочистки изучались механические фильт-
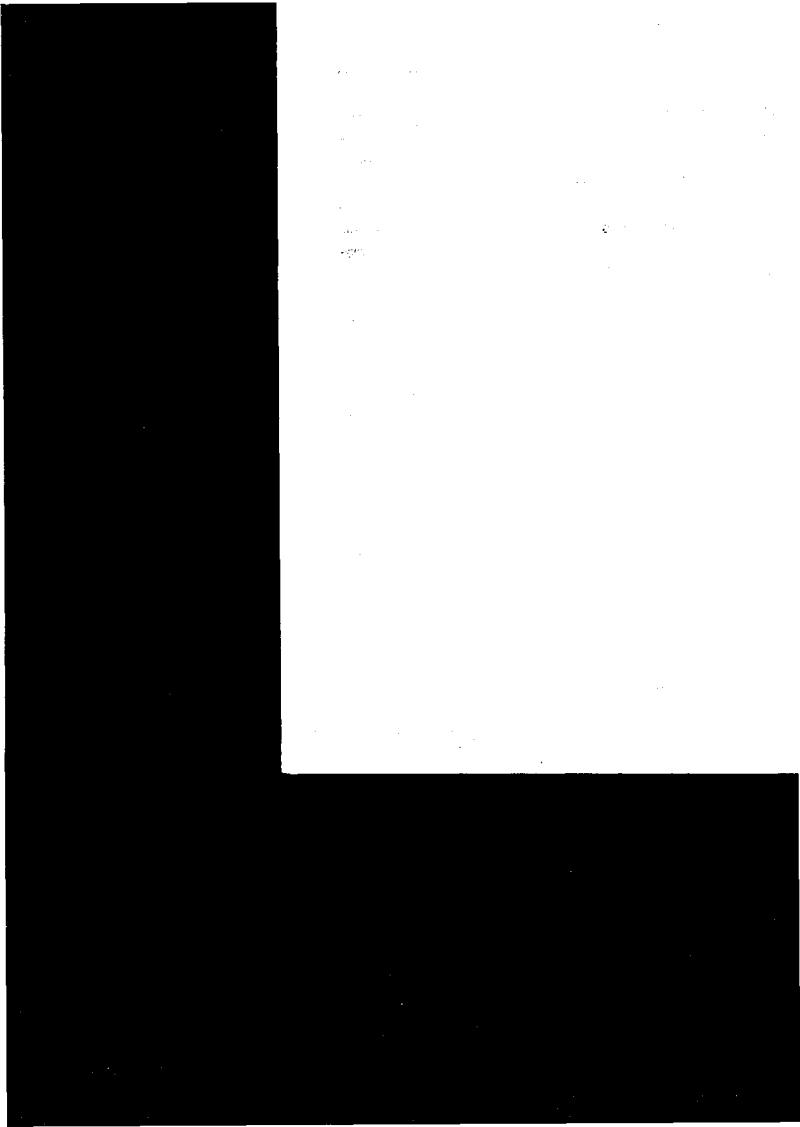
16
ры .из пористых тонкостенных металлических токопроводящих материалов. За основу взяты фильтры, разработанные в ННГАСУ. Основные задачи исследований заключались в следующем:
-определении оптимальных параметров процесса;
-разработке конструкции аппаратов, обеспечивающих их длительную работу без регенерации;
-создание технологии безреагентной регенерации фильтрующих элементов на основе электрохимического метода;
-уточнение математических моделей процесса фильтрования с наложением электрического поля.
Схема экспериментальной установки приведена на рис. 4. Фильтровальная установка состоит из корпуса (13), выполненного из
органического стекла диаметром 75 мм. В корпус вмонтирован цилиндрический фильтровальный элемент (11) из пористой нержавеющей стали диаметром 30 мм, размер пор элемента 15 мкм, толщина мембраны δ=1.0 мм.
Вокруг фильтрующего элемента оксиально размещена сетка из нержавеющей стали (12). Сетка отделена от фильтрующего элемента изолирующим материалом. Фильтровальный элемент и сетка присоединены к полюсам источника постоянного тока (15). Пространство между фильтрующим элементом и корпусом фильтра может быть заполнено инертным зернистым фильтрующим материалом: крупнозернистым песком (dЭKB 1.5 мм) или гранулированным полистиролом (13). Загрузка может находиться в данной полости в плотной укладке и во взвешенном состоянии. Внутренняя полость фильтровального элемента может заполняться гранулированным активированным углем или дробленым антрацитом (dЭKB 2MM). Установки снабжены трубопроводами исходной воды (1 - 5), очищенной воды (7), подачи промывной воды (8), удаления газа (6) и отвода осадка (9).
Изучались следующие режимы работы.
Режим 1. Фильтрование производится только через фильтрующие эле-
менты.
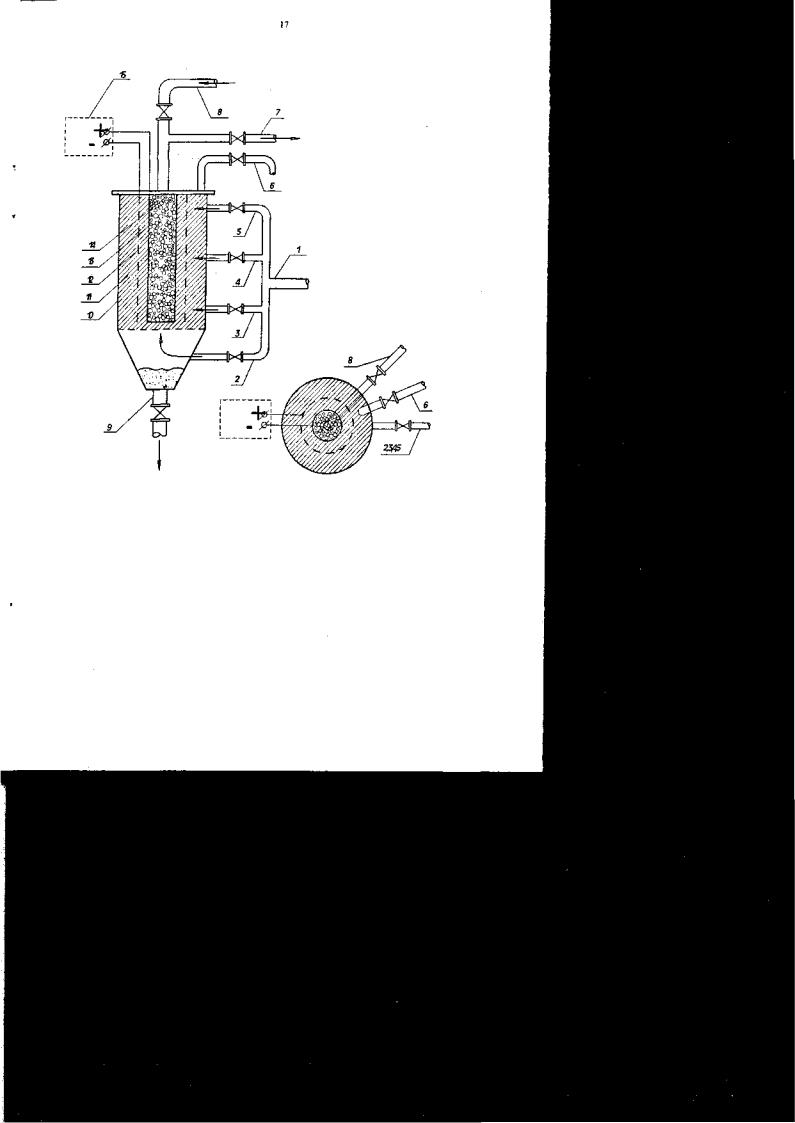
Промывка элементов
Сточная вода на доочистку фильтрацией
Рис. 4. Схема экспериментальной установки.
1,2,3,4- трубопроводы подачи воды на фильтр;
6 - трубки для удаления воздуха;
7 - трубопровод очищенной воды;
8 - трубопровод промывной воды;
9 - трубопровод для удаления осадка;
10 - корпус фильтра из оргстекла;
11 - цилиндрический фильтровальный элемент;
12 - цилиндрическая фильтровальная сетка;
13 - загрузка из инертного материала;
14 - загрузка из активированного угля; 15 - выпрямитель.

18
Задвижки (3,4, 5) закрыты. Загрузочные материалы в фильтре (13,14) отсутствуют, подача воды осуществляется по патрубку (2), отвод очищенной воды по патрубку (7). Регенерация фильтрующего элемента производится обратной подачей воды (гидравлическая) через патрубок (8) или кислотой (химическая) путем заполнения полости фильтра ее раствором.
Режим 2. Полости (11, 14) заполняются фильтрующим материалом. Фильтрование осуществляется через слои фильтрующей загрузки мембранного цилиндрического элемента. Подача воды на фильтрование осуществляется сосредоточенно через патрубок (2) или рассредоточение, через патрубки (3-5). Регенерация фильтрующего элемента осуществляется аналогично предыдущему режиму. При промывке инертной загрузки, открывается задвижка (2), отвод промывной воды в этом случае производится через патрубок (6).
Режим 3. В этом режиме к элементу (11) и сетке (12) подводится электрический ток. Ток может подводиться периодически, как в период регенерации фильтрующего элемента, так и постоянно в период фильтрования. Полости (13, 14) могут быть заполненными и незаполненными.
Исходная жидкость подводится по патрубку (1) под давлением до 0.2 МПа. Исследования показали, что грязеемкость мембран изменяется от 6 г/дм2 (при первой гидравлической промывке) до 1.5 г/дм2 (при последней). Снижение проницаемости мембран после каждой промывки составляет от 15 до 20% от начальной (режим 1). Продолжительность фильтроцикла колеблется, в зависимости от концентрации взвешенных веществ в исходной жидкости, от 1 часа (Cисх 300 - 350 мг/л) до 8 -16 часов (Сисх =20-30 мг/л).
Химическая регенерация в этом режиме осуществляется 0.1-1 % раствором соляной кислоты после 5-12 гидравлических промывок и обеспечивает восстановление мембран на 97 - 98%.
Исследования с заполнением полостей фильтрующего элемента различными материалами показали (режим 2) следующее:
- применение кварцевого песка или полистирола, приводит к резкому увеличению фильтроцикла и увеличению грязеемкости фильтра;