
книги / Электронно-лучевая сварка
..pdf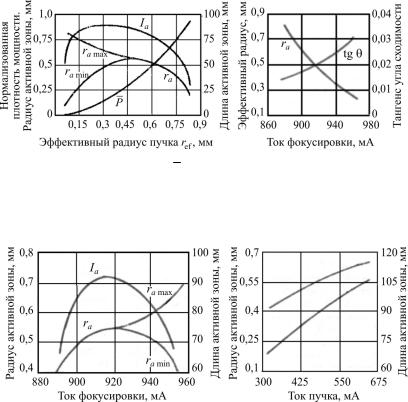
Из рисунка видно, что существует оптимальное значение тока фокусировки 915 мА, при котором активная зона имеет максимальную протяженность и перетяжка пучка в средней части отсутствует. В ходе экспериментов при ЭЛС образцов из высокопрочной стали с указанными параметрами режима были получены сварные швы с глубиной порядка 60 мм.
Рис. 2.22. Зависимости P ,
ra (ra max, ra min) и la от эффективного радиуса пучка ref
Рис. 2.23. Зависимости эффективного радиуса итангенса угласходимости электронного пучка оттока фокусировки
Рис. 2.24. Зависимости длины |
Рис. 2.25. Зависимости длины |
и радиуса активной зоны |
и радиуса активной зоны |
электронного пучка от тока |
электронного пучка от тока |
фокусировки при U = 60 кВ, |
пучка при U = 60 кВ, |
I = 425 мА |
Iфок = 915 мА |
201
На рис. 2.25 приведены зависимости длины и радиуса активной зоны электронного пучка от его тока, построенные на основе результатов работы [23]. Из графика видно, что с ростом тока электронного пучка и, соответственно, его общей мощности увеличивается и размер активной зоны пучка для одной и той же электронной пушки. Расчет проведен для U = 60 кВ, tgθ = 0,02 и тока фокусировки 915 мА. С возрастанием общей мощности электронного пучка растет и стабильность процесса ЭЛС, что подтверждается экспериментально.
Активная зона электронного пучка – это характеристика его потенциальных возможностей. Дело в том, что при расчете ее параметров не учитывается, что реальные значения плотности энергии, которая идет на нагрев, плавление и испарение металла, зависят от наклона элемента передней стенки канала проплавления в месте воздействия на нее электронного пучка. Кроме того, распределение энергии электронного пучка меняется при его взаимодействии с материалом свариваемого изделия. Нужно также отметить, что, как показано в работе [19], входное отверстие канала проплавления диафрагмирует электронный пучок и препятствует попаданию в канал периферийных электронов пучка, что меняет как длину, так и форму участка активной зоны пучка, участствующей в выделении энергии в корневой части канала (причем эти изменения зависят от того, имеем ли мы дело с недофокусированным или перефокусированным электронным пучком).
2.3.3.2. Положение фокуса электронного пучка при взаимодействии со свариваемым металлом в вакууме
Плотность тока в фокальном пятне электронного пучка при ЭЛС регулируется с помощью магнитной фокусирующей системы электронной пушки. В 1-й главе этой монографии было отмечено, что в связи с «размытостью» распределения электронного пучка в его периферийных зонах измерение диаметра
202
пучка связано с точностью регистрации минимальных значений тока. Измерение параметров распределения тока электронного пучка во всех точках в нескольких поперечных сечениях – достаточно трудоемкая задача, осуществимая только в лабораторных условиях. Очень грубая и субъективная оценка положения фокуса электронного пучка (обычно при небольших значениях тока пучка) может быть осуществлена оператором электронно-лучевой сварочной установки визуально по величине светящегося пятна на поверхности тестового образца из тугоплавкого металла, например вольфрама, нагреваемого электронным пучком. Иногда для повышения точности на поверхности тестового образца делают маленькое отверстие и меняют ток фокусирующей линзы до момента практического исчезновения света от зоны воздействия пучка на поверхности в результате его полного вхождения в отверстие. Среди методов измерения профиля пучка более широкое применение получили методы, использующие вращающийся зонд или узкую щель, периодически пересекаемую электронным пучком. Однако все эти методы контроля фокусировки электронного пучка осуществляются при прохождении пучка в вакууме.
С углублением понимания процессов ЭЛС возникли обоснованные сомнения, что позиция фокуса, которую находят при прохождении электронного пучка в вакууме, не совпадает с позицией фокуса в условиях взаимодействия пучка со свариваемым материалом. Японский ученый Y. Arata [24] предложил компромиссный вариант измерения, заключающийся в получении расплавленных зон при прохождении вертикального электронного пучка через ряд вертикальных съемных металлических пластин, которые размещены в пазах рамки, расположенной под углом 35° к основанию двухкоординатного манипулятора элек- тронно-лучевой сварочной установки (рис. 2.26).
И действительно, при экспериментальных исследованиях на разных электронно-лучевых сварочных установках и при различных значениях мощности электронного пучка [25] срав-
203
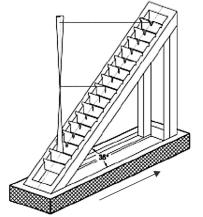
Рис. 2.26. Тест положения фокуса электронного пучка (поArata)
нение определенных позиций фокуса пучка по методу Arata и с применением щелевого метода (см. главу 1) показало существенное различие в полученных значениях, достигающее 30 мм. Это различие авторы работы объясняют наличием рассеяния электронного пучка и ионной фокусировкой в плазме паров обрабатываемого металла. Используя предложенную методику, авторы работы установили, что при мощности пучка 10 кВт положение фокальной плоскости находилось на расстоянии от торца электронной пушки, на 20 мм большем по сравнению
сизмерениями, проведенными при движении пучка в вакууме, а при мощности пучка 3 кВт (рис. 2.27, б) измеренная позиция фокуса находилась на расстоянии, большем на 30 мм расстояния, определенного при движении электронного пучка в вакууме (рис. 2.27, а). Макрошлифы представлены на рис. 2.27, в.
Положение фокуса электронного пучка, под которым понимают самое узкое сечение пучка (талию пучка), является очень важным параметром режима ЭЛС, так как фокусировка в значительной степени определяет глубину проплавления металла при заданной полной мощности электронного пучка. Одновременно
сположением фокуса электронного пучка по отношению к торцу
204
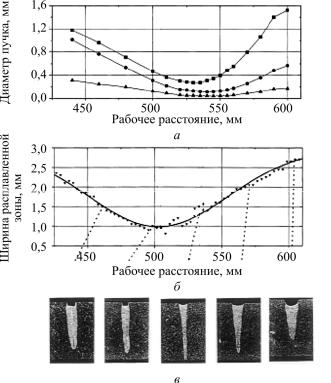
электронной пушки (или к плоскости расположения фокусирующей катушки электронной пушки) надо учитывать и расстояние от пушки до свариваемой поверхности (рабочую дистанцию). Разность этих величин дает позицию фокуса по отношению к поверхности свариваемого изделия, которая в большинстве случаев должна находитьсяниже поверхности изделия.
Рис. 2.27. Сравнение результатов определения положения фокуса электронного пучка: а – определенного по щелевому методу (кривая – ■ – построена при токе пучка, равном 90 % от тока пучка; кривая – ● – при токе, равном 50 % тока пучка; кривая – ▲ – при токе, равном 10 % тока пучка); б – значения ширины расплавленной зоны на металлических вставках тестаArata; в – макрошлифы расплавленных зон (ток электронного пучка 20 мА, ускоряющее напряжение 150 кВ)
205
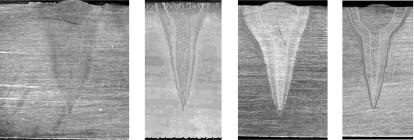
Конечной целью определения положения фокальной плоскости электронного пучка является определение тока фокусирующей линзы электронной пушки, при котором достигается максимальная глубина проплавления металла для заданного значения полной мощности электронного пучка, конкретной электронной пушки при выбранном рабочем расстоянии сварки. Это значение тока фокусирующей линзы часто называют острой фокусировкой электронного пучка. Соответственно, при положении фокуса пучка ниже этого значения пучок называют недофокусированным, а в случае положения фокуса выше положения острой фокусировки – перефокусированным.
На рис. 2.28 показаны поперечные макрошлифы сварных швов, полученных при ЭЛС образцов из хромомолибденовой стали при ускоряющем напряжении 60 кВ, токе пучка 50 мА и скорости сварки 5 мм/с, а в табл. 2.2 приведены значения их глубины и ширины. Ширина шва измерялась на уровне половины его глубины. Видно, что в диапазоне значений тока фокусирующей системы от 825 до 854 мА изменение глубины шва составляет около 15 %. На основании измеренной глубины проплавления для указанных режимов сварки и свариваемого материала острая фокусировка электронного пучка наблюдалась при токе фокусирующей линзы 835 мА.
а |
б |
в |
г |
Рис. 2.28. Изображения поперечных сечений швов, полученных при токах фокусирующей системы:
а – 825 мА; б – 835 мА; в – 840 мА; г – 854 мА
206
Таблица 2 . 2
Геометрические параметры поперечных сечений сварных швов
Ток фокусировки, мА |
825 |
833 |
835 |
840 |
847 |
854 |
Глубина шва, мм |
12,2 |
13,8 |
13,9 |
12,9 |
12,7 |
11,8 |
Ширина шва, мм |
1,13 |
1,39 |
1,92 |
1,84 |
1,1 |
0,94 |
При токе 825 мА позиция электронного фокуса находилась ниже острого фокуса и пучок был недофокусирован. При значениях тока фокусировки 840–854 мА положение фокуса находилось выше острого фокуса и пучок был перефокусирован.
2.3.3.3. Вторично-эмиссионный сигнал как источник информации для слежения за положением стыка свариваемых деталей и для контроля и управления процессом взаимодействия электронного пучка
с материалом свариваемого изделия
Эмиссия электронов из зоны взаимодействия маломощного электронного пучка с металлом – это прежде всего упруго и неупруго отраженные электроны со значениями энергии до 50 эВ и вторичные электроны с энергией ниже 50 эВ. Количество Оже-электронов очень мало в сравнении с другими группами электронов. Их энергия зависит от материала изделия, но превышает значение 50 эВ, и, следовательно, поток этих электронов является составляющей потока обратно отраженных электронов с аналогичными значениями энергии.
Распределение отраженных электронов зависит от угла падения электронного пучка на поверхность металла и от рельефа этой поверхности. При падении пучка перпендикулярно поверхности металла отраженные электроны имеют распределение по закону косинуса. Количество обратно отраженных электронов в зависимости от свариваемого металла и величины ускоряющего напряжения для падающего на поверхность электрон-
207
ного пучка достаточно велико – от 10 до 40 % от общего количества электронов пучка. При падении электронного пучка под углом 1°–7° ( типичные значения средних углов наклона передней стенки канала проплавления) обратно отраженные электроны формируют распределение с максимумом на величине угла, равной удвоенному значению угла падения пучка, и главный результат их действия – перенос энергии с бомбардируемой поверхности передней стенки канала на его заднюю поверхность. В результате наличия выступов на передней стенке канала проплавления и многократного отражения электронов от стенок канала канал покидает некоторое количество отраженных электронов с распределением, более узким, чем распределение по закону косинуса.
Распределение истинно вторичных электронов практически не зависит от энергии падающих электронов. Количество эмитируемых вторичных электронов также не зависит от температуры и состояния поверхности образца (твердое оно или жидкое), но величина их потока обратно пропорциональна энергии падающих электронов пучка. При взаимодействии электронного пучка с металлом на поверхности свариваемого изделия их достаточно много и они движутся по прямолинейным траекториям, а в случае формирования канала проплавления в металле они практически не покидают канал.
При взаимодействии слаботочного электронного пучка с поверхностью металла наличие неоднородностей на поверхности изделия (в том числе и стыка свариваемых кромок) приводит к изменению амплитуды и распределения вторичной электронной эмиссии, что позволяет при осцилляции пучка и регистрации эмиссионного сигнала с помощью установленного над изделием коллектора электронов получить на экране дисплея изображение поверхности свариваемых деталей до и после сварки или следить за положением стыка. Существует несколько типов систем для слежения за положением стыка свариваемых деталей [26–28]. Обычно это следящая система, в которой
208
используется слаботочный электронный пучок. Такой пучок может формироваться в процессе сварки путем снижения тока пучка в короткие промежутки времени для осуществления сканирования стыка свариваемых деталей перед зоной сварки. В некоторых случаях используют проход слаботочным электронным пучком по всему стыку перед сваркой с выполнением процесса обучения (т.е. занесение в память системы наведения пучка на стык координат стыка, по которым будет позиционироваться пучок при совершении сварочного прохода).
При мощности электронно-лучевой сварочной установки до 5 кВт возможно слежение за стыком без периодического уменьшения тока пучка с увеличением на короткий промежуток времени скорости его движения. В процессе слежения за стыком производится сканирование стыка, при этом электронный пучок движется перпендикулярно стыку по линии, по растру, иногда по кругу. В результате на экране дисплея наблюдают линейный контур или изображение поверхности.
На рис. 2.29 показана система слежения за стыком, при которой электронный пучок малой мощности 1 на короткое время покидает зону сварки W и сканирует стык свариваемых деталей 7 с предварительно подготовленными кромками в виде канавки 6. Отраженные от поверхности канавки электроны регистрируются коллектором отраженных электронов 4, установленным над зоной сварки, при пересечении стыка создают сигнал меньшей интенсивности, чем при движении по поверхности свариваемых деталей, который используется как метка положения стыка. Перед коллектором отраженных электронов установлен электрод 5, находящийся под отрицательным потенциалом и препятствующий движению к коллектору истинно вторичных, плазменных и термоэлектронов. В процессе работы системы движение электронного пучка 1 по линии WАВW выполняется с большой скоростью.
На рис. 2.30 приведен другой вариант системы слежения за стыком свариваемых деталей при ЭЛС [27]. Два коллектора
209
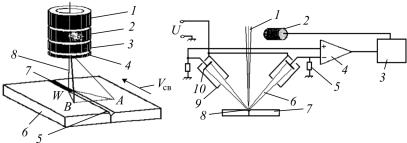
Рис. 2.29. Система слежения |
Рис. 2.30. Система слежения за |
|
за стыком при ЭЛС: 1 – |
фоку- |
стыком при ЭЛС с двумя датчиками: |
сирующая система; 2 – |
откло- |
1 – электронный пучок; 2 – отклоня- |
няющая система; 3 – коллектор |
ющая система; 3 – блок управления; |
|
электронов; 4 – отрицательно |
4 – дифференциальный усилитель; |
|
заряженный электрод; 5 – сва- |
5 – резистор нагрузки; 6 – отраженные |
|
риваемый стык; 6 – сваривае- |
электроны; 7 – свариваемые детали; |
|
мые детали; 7 – сварной шов; |
8 – свариваемый стык; 9 – экрани- |
|
8 – электронный пучок |
рующий корпус; 10 – коллектор |
|
|
|
отраженных электронов |
отраженных электронов 10, расположенные в экранирующих корпусах 9, регистрируют сигнал от стыка, который снимается с резисторов нагрузки 5. На экранирующие корпусы 9 коллекторов отраженных электронов подается отрицательный потенциал 40–100 В, обеспечивающий попадание на коллектор только высокоэнергетических отраженных электронов. Дифференциальная система усиления сигнала формирует его значение, равное нулю, при нахождении электронного пучка на линии стыка свариваемых деталей и максимальную величину сигнала при нахождении пучка вне области стыка. При этом блок управления 3 вырабатывает сигналы наведения электронного пучка на стык свариваемых деталей. Преимуществом этой системы слежения является наличие двух датчиков стыка и как следствие – отсутствие необходимости сканирования стыка свариваемых деталей электронным пучком.
210