
книги / Процессы обработки заготовок. Методы механической обработки поверхностей деталей машин-1
.pdf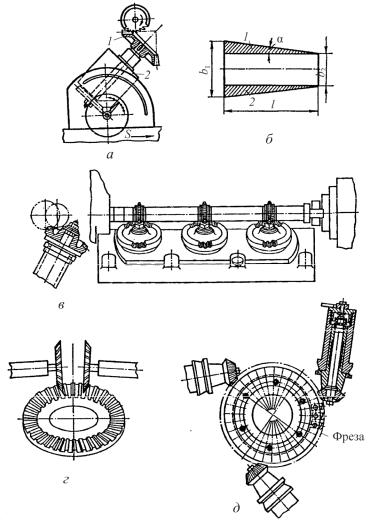
Рис. 8.13. Фрезерование конического зубчатого колеса: а – установка заготовки на оправке; б – схема фрезерования впадины между зубьями; в – одновременно трех заготовок; г – одной заготовки двумя дисковыми фрезами; д – трех заготовок специальной дисковой фрезой
161
При таком положении фрезеруют все левые бока зубьев (площадка 1 – см. рис. 8.13, б).
За третий ход фрезеруют все правые бока зубьев (площадка 2), для чего делительную головку разворачивают на тот же угол, но в противоположном направлении. Этот способ нарезания зубьев малопроизводителен, а точность обработки соответствует 10-й степени.
Для нарезания прямых зубьев точных конических колес в серийном и массовом производстве применяют более производительные станки – зубострогальные, на которых обработка зубьев производится методом обкатки. При обработке зубьев с модулем свыше 2,5 мм их предварительно прорезают профильными дисковыми фрезами методом деления; таким образом, сложные зубострогальные станки не загружают предварительной грубой обработкой, и следовательно, они лучше используются для точной обработки. На рис. 8.13, в показано предварительное фрезерование зубьев трех конических зубчатых колес одновременно на специальном или специализированном станке, применяемом в крупносерийном и массовом производстве. Станок снабжен устройством для автоматического деления и одновременного поворота всех обрабатываемых заготовок.
На рис. 8.13, г показано предварительное фрезерование зубьев двумя дисковыми фрезами на специализированном станке конструкции ЭНИМСа.
В крупносерийном и массовом производстве для предварительного (чернового) нарезания зубьев небольших конических зубчатых колес применяют зуборезные станки для одновременного фрезерования трех заготовок с автоматическим делением, остановом, подводом и отводом стола. На рис. 8.13, д изображена схема расположения шпинделей трехшпиндельного высокопроизводительного станка для одновременного фрезерования зубьев трех заготовок, расположенных вокруг специальной дисковой фрезы. Станочник поочередно устанавливает заготовки на оправках рабочих головок, подводит головку до упора и включает
162
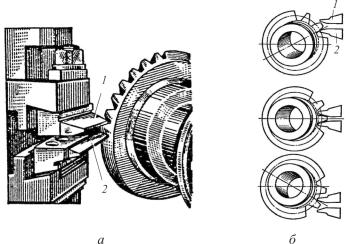
самоход. Все остальные движения производятся автоматически: рабочая подача, отход нарезаемого колеса и поворот его на один зуб, следующий подвод, выключение, когда две головки продолжают работать.
Окончательное чистовое нарезание зубьев 7–8-й степени точности производится строганием на зубострогальных станках
(рис. 8.14, а).
Рис. 8.14. Нарезание конического зубчатого колеса на зубострогальном станке: а – установка резцов; б – схема обработки; 1 и 2 – резцы
Эти станки работают методом обкатки (рис. 8.14, б): два строгальных резца (1 и 2) совершают прямолинейные возвратнопоступательные движения вдоль зубьев обрабатываемой заготовки; при обратном ходе резцы немного отводятся от обрабатываемой поверхности для уменьшения бесполезного изнашивания режущей кромки от трения; взаимная обкатка заготовки и резцов обеспечивает получение профиля эвольвенты.
Время нарезания зуба в зависимости от материала, модуля, припуска на обработку и других факторов колеблется от 3,5 до 30 с.
163
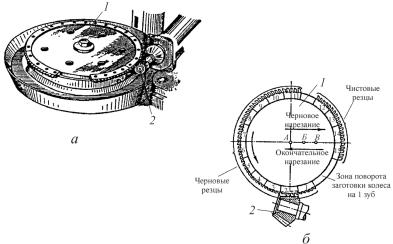
Для обработки прямых зубьев небольших конических зубчатых колес применяют производительный метод – круговое протягивание зубьев (рис. 8.15, а) на специальных зубопротяжных станках.
Режущим инструментом служит круговая протяжка 1 (рис. 8.15, б), состоящая из нескольких секций фасонных резцов (15 секций по пять резцов в каждой секции). Резцы с изменяющимся профилем расположены в протяжке в последовательном порядке для чернового, получистового и чистового нарезания зубьев. Каждый резец при вращении круговой протяжки снимает определенный слой металла с заготовки 2 в соответствии с величиной припуска.
Рис. 8.15. Круговое протягивание зубьев конического зубчатого колеса: 1 – круговая протяжка;
2 – нарезаемое колесо
Протяжка вращается с постоянной угловой скоростью и в то же время совершает поступательное движение, скорость которого различна на отдельных участках проходимого пути.
При черновом и получистовом нарезании протяжка имеет поступательное движение от вершины начального конуса к его
164
основанию, а при чистовом – в обратном направлении, от основания к вершине. За один оборот протяжки она полностью обрабатывает одну впадину зубчатого колеса.
Во время резания обрабатываемая заготовка неподвижна, для обработки следующей впадины она поворачивается на один зуб в то время, когда подходит свободный от резцов сектор круговой протяжки.
Круговое протягивание зубьев отличается высокой производительностью (в 2–3 раза более высокой по сравнению со строганием), в то же время точность обработки соответствует 8-й степени точности, а шероховатость поверхности Ra = 1,25...2,5 мкм. В качестве СОЖ обычно используют сульфофрезол или масло индустриальное И-20А.
Нарезание конических зубчатых колес с криволинейны-
ми зубьями производится на специальных станках, работающих методом копирования (врезания) и методом обкатки.
Режущим инструментом являются резцовые головки (рис. 8.16, а) преимущественно двух типов: цельные и со вставными резцами. Цельные головки изготавливают с номинальным диаметром от 12,7 до 50,8 мм для нарезания зубчатых колес малых модулей.
Резцовые головки от 80,9 до 457,2 мм изготавливают с вставными ножами.
Резцовые головки подразделяются по роду обработки, для которой они предназначаются, на черновые (для черновых проходов) и чистовые (для чистовых проходов). Различаются также одно-, двух- и трехсторонние резцовые головки.
Для чернового нарезания зубьев применяют двух- и трехсторонние резцовые головки.
Двусторонние головки применяют при нарезании зубьев методом обкатки и методом копирования, а трехсторонние – только при работе методом копирования.
Двусторонние головки режут наружными и внутренними резцами, расположенными поочередно.
165
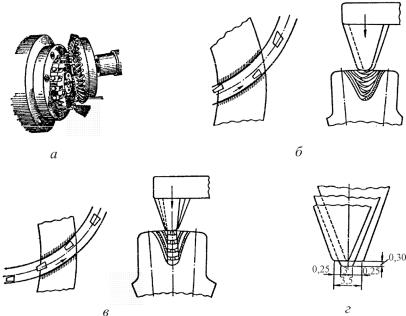
Каждый резец одновременно обрабатывает боковую поверхность зуба и часть впадины (рис. 8.16, б).
Трехсторонние головки в отличие от двусторонних имеют наружные, внутренние и средние резцы. Наружные и внутренние резцы обрабатывают только боковые стороны зуба, а средние резцы – только впадины зубьев (рис. 8.16, в, г).
Чистовые резцовые головки – одно- и двусторонние– используются главным образом для окончательного нарезания зубьев после чернового нарезания. У односторонних головок резцы все наружные или все внутренние. Наружные резцы служат для вогнутой стороны зуба, внутренние– для выпуклой. Резцы чистовых головок срезают металл только с боковых сторон зубьев.
Рис. 8.16. Нарезание конического зубчатого колеса
скриволинейными зубьями: а – односторонняя резцовая головка; б – схема работы двусторонней головки;
в, г – схема работы трехсторонней головки
166
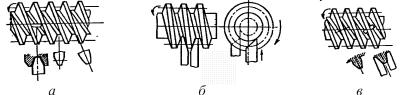
Черновое зубонарезание конических зубчатых колес с большим количеством зубьев производится методом копирования, когда обрабатываемая заготовка закреплена неподвижно, а вращающаяся резцовая головка перемещается вдоль оси и прорезает впадины поочередно. Этот метод более производителен, чем метод обкатки, применяемый для нарезания колес с малым количеством зубьев.
Чистовое нарезание зубьев конических колес обычно производится методом обкатки; колеса с большим количеством зубьев нарезаются обычно двусторонними головками, а с малым количеством – односторонними головками.
8.4. ОБРАБОТКА ЧЕРВЯКОВ
Червячные передачи бывают с цилиндрическим (геликоидальным) и глобоидным червяком.
Сечение витков цилиндрического червяка с осевой плоскостью представляет собой прямолинейную рейку, а у глобоидального червяка – круговую.
В современной технике распространение получили следующие червяки: архимедовы, эвольвентные, конволютные и глобоидные (рис. 8.17, а–в). Архимедовы червяки чаще всего нарезаются на токарных станках, при этом прямолинейные режущие кромки резцов располагаются в осевом сечении так же, как при нарезании трапецеидальной резьбы. Винтовая поверхность такого червяка
Рис. 8.17. Виды цилиндрических червяков
исхемы их обработки резцами:
а– архимедов; б – эвольвентный; в – конволютный
167
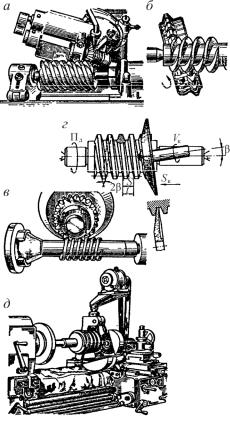
называется архимедовой, так как с торцовой поверхности она образует архимедову спираль. Такие червяки представляют обычный винт с трапецеидальной резьбой. Архимедов червяк в осевом сечении имеет прямобочный профиль с углом, равным профильному углу резца.
Рис. 8.18. Обработкачервяков:
а– дисковойфрезой; б– фрезой-улиткой;
в– долбяком; г– шлифовальнымкругом;
д– специальное устройстводля шлифованиячервяковнатокарномстанке
При крупносерийном производстве архимедовы червяки фрезеруют дисковыми фрезами (рис. 8.18, а)
скриволинейными режущими кромками. Шлифование таких червяков осуществляется дисковым конусным или тарельчатым шлифовальным кругом (рис. 8.18, г) с припуском от 0,1 до 0,2 мм на сторону в зависимостиотмодуля червяка.
Шлифование червяков с малым модулем производят на резьбошлифовальном или токарном станке со специальным устройством (рис. 8.18, д).
Крупносерийное и массовое производство профилей витков червяка
смодулем более 3 мм осуществляется на специальном червячно-шлифоваль- ном станке коническим шлифовальным кругом большого диаметра (800 мм и более).
168
Этот метод обеспечивает высокую производительность. Таким кругом можно получить разные профили червяка путем его перемещения в горизонтальной плоскости. Шлифование производится при трех движениях: вращении круга, медленном вращении червяка и поступательном перемещении круга на величину одного шага (хода для многозаходных червяков) за один оборот изделия. Для отделки витков червяков ответственных передач применяют притирку червяков чугунными или фибровыми притирами, имеющими форму червячного колеса. В качестве абразивного материала применяют микропорошки с маслом, а для получения низкой шероховатости поверхности – пасты ГОИ.
Эвольвентные червяки (см. рис. 8.17, б) нарезают на токарных станках с раздельной обработкой каждой стороны витка при смещении прямолинейных режущих кромок резцов на величину радиуса основного цилиндра винтовойэвольвентной поверхности.
Если червяк правый, то левую сторону боковой поверхности витков нарезают резцом, поднятым над осью, а правую – опущенным. При левом червяке оба резца соответственно меняют местами. Указанным способом эвольвентные червяки нарезают редко ввиду неблагоприятных условий резания резцами, поднятыми или опущенными по отношению к осевой линии. Такие червяки обычно фрезеруют фасонными дисковыми или пальцевыми фрезами, а также фрезами-улитками (рис. 8.18, б), а шлифуют их плоской стороной тарельчатого шлифовального круга. Эвольвентный червяк можно рассматривать как цилиндрическое зубчатое колесо
смалым числом спиральных зубьев, имеющих большой наклон.
Вкрупносерийном и массовом производстве архимедовы и эвольвентные червяки нарезают обкаточными дисковыми резцами, подобными зуборезным долбякам (рис. 8.18, в), на специальных станках. Подача осуществляется инструментом в осевом направлении заготовки червяка при вращении червяка и резца.
Червяк с прямосторонним профилем в нормальном сечении витка называют конволютным (см. рис. 8.17, в). Нарезают его резцами, расположенными нормально к боковым поверхностям витка.
169
Нарезание глобоидальных червяков требует применения специальных устройств на зубофрезерных станках. Предварительное фрезерование глобоидального червяка производится за один или два прохода с припуском от 0,3 до 0,5 мм на толщину витка. Окончательное нарезание осуществляется универсальной или специальной многорезцовой головкой. После нарезания витков глобоидальный червяк обычно подвергают термообработке с последующим шлифованием опорных шеек и витков. Отделку глобоидальных червяков осуществляют притиркой либо обкаткой закаленным роликом.
8.5.ЧИСТОВАЯ ОБРАБОТКА ЗУБЧАТЫХ КОЛЕС
Сувеличением быстроходности машин возникла настоятельная необходимость в бесшумно работающих зубчатых колесах. Шум, вызываемый зубчатыми колесами, часто обусловлен ненормальными условиями работы зубчатой передачи, влекущими за собой ускоренное ее изнашивание. Шум вредно влияет на человеческий организм. Весь комплекс причин возникновения шума при работе зубчатых колес изучен недостаточно полно, но в основном проблема шума зубчатых передач связана
сточностью и качеством изготовления элементов зубчатых колес. Улучшение качества зубчатых колес, способствующее умень-
шению шума, достигается: нарезанием зубчатых колес с точностью, выражаемой сотыми и тысячными долями миллиметра; термической обработкой с применением цианирования и газовой цементации, дающих значительно меньшую деформацию зубьев зубчатых колес, чем цементация в твердом карбюрюзаторе и закалка; применением рациональных способов окончательной чистовой обработки зубьев, позволяющих достигнуть точности зубчатых колес до 2–3 мкм; применением специальных высокопрочных малодеформируемых в процессе термической и химико-терми- ческой обработки сплавов, в первую очередь высокопрочных сталей, и неметаллических материалов (пластмасс, текстолита и др.).
170