
книги / Элементы гидравлических систем и объёмного гидропривода
..pdf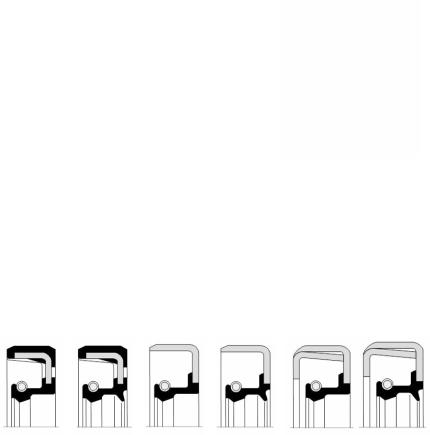
Армированная манжета (рис. 96)
вобщем случае состоит из внешней оболочки (статической части) 1, металлической арматуры 2, мембраны 3 с уплотняющей кромкой 6, браслетной пружины 4 и защитной кромки 5. Внешняя оболочка 1 уплотнения предназначена для статического уплотнения манжеты
вотверстии корпуса.
В современных конструкциях внешнюю оболочку выполняют как одно це-
лое с манжетой (рис. 97). Обрезиненная поверхность наружного диаметра обеспечивает надежное уплотнение даже в случае значительной шероховатости поверхности отверстий и при применении разъемных корпусов. Гладкая или ребристая наружная поверхность эффективно уплотняет и надежно фиксирует уплотнение в отверстии корпуса. Это наиболее часто встречающийся тип манжеты. Обозначение – форма A по DIN 3760.
Форма A Форма AS Форма B Форма BS |
Форма C Форма CS |
Рис. 97. Примеры армированных манжет по DIN 3760 (3761)
Манжета с металлической внешней оболочкой (форма B по DIN 3761) применяются при необходимости особо точной и устойчивой посадки в корпусе, особенно при больших диаметрах. Известны конструкции, когда манжета дополнительно оснащена внутренней металлической крышкой (форма C по DIN 3761), придающей конструкции большую радиальную жесткость. Применяют такие
241
манжеты при больших диаметрах и грубо обработанных посадочных отверстиях.
Отличительной особенностью манжет является наличие у них хотя бы одной уплотнительной мембраны с контактной кромкой. Благодаря мембране уплотняющая кромка плотно охватывает вал с силой, пропорциональной давлению, и прижимается к поверхности вала с некоторым усилием, действующим в радиальном направлении. Наличие подпружиненной кромки уплотнения способствует сохранению уплотняющей способности даже при значительном износе. Кромка уплотнения 6 имеет такую форму, что образует острый угол с сопряженной поверхностью. Сбалансированность кромки и гибкой части уплотнения 3 позволяет компенсировать динамический износ и перекос вала по отношению к отверстию корпуса.
Браслетная пружина 4 устанавливается в специально сформированное ложе и создает статическое давление уплотняющей кромки на вал. Браслетные пружины изготовляют из пружинной проволоки диаметром 0,2...0,5 мм и подвергают закалке и среднему отпуску,
защищают кадмированием, цинкованием или изготавливают их из бронзы. Браслетная пружина может быть заменена кольцом из упругого синтетика. Необходимая упругость гарантируется конструктивными элементами манжеты.
Первоначальный контакт уплотняющей кромки мембраны и уплотняемой поверхности, обеспечивающий герметизацию при нулевом и малом давлении среды, осуществляется в результате пружинящего действия манжеты, деформированной в радиальном направлении при монтаже. Контактная плотность этого соединения повышается с увеличением давления среды, которая прижимает контактную кромку манжеты к уплотняемой поверхности. Радиальное усилие прижатия уплотнительной кромки манжеты к валу существенно влияет на герметизирующую способность манжет. Металлическая арматура 2, выполненная в виде каркасных колен из листовой стали, придает манжете необходимую радиальную жесткость. Защитная кромка (пыльник) 5 предохраняет манжету от внешних за-
242
грязнений, но не создает дополнительное трение, вызывающее тепловыделение и энергопотери.
Манжеты изготовляют двух типов: однокромочные без защитной кромки и двухкромочные с защитной кромкой (пыльником). При умеренном загрязнении внешней среды необходимо применять манжеты с пыльником. При высокой степени загрязнения применяют кассетные и комбинированные уплотнения.
В обозначении манжет с защитной кромкой (пыльником) в конце добавляется буква S, например: AS по DIN 3760 или BS по
DIN 3761 (см. рис. 97).
Пластмассовые уплотнения быстровращающихся валов в отличие от резиновых манжет по ГОСТ 8752–79 сохраняют работоспособность в широком диапазоне изменения температуры от −60 до 200 °C, при снижении давления масла до 0,6 МПа, биении вала до
0,2 мм, скорости скольжения до 30 м/с, ударных нагрузках и вибрациях, наличии обратного перепада давления до 0,1 МПа, повышен-
ной загрязненности и влажности воздушной среды.
Эти высокие показатели достигаются благодаря использованию плавающего в посадочной канавке уплотнительного элемента из композиции фторопласта-4 с добавкой 15 % кокса и 5 % дисульфида
молибдена (Ф4К15М5, ТУ 6-05-1413–76) и поджимной стальной браслетной пружины. Уплотнения с двумя уплотнительными элементами обладают наибольшей надежностью за счет резервирования элементов.
При больших скоростях вращения ротора гидромашины широко применяются торцовые уплотнения, работающие при давлении до
1,0 МПа.
Торцовые уплотнения валов [10] являются узлом насосно-
компрессорного оборудования, перемешивающих устройств и химических аппаратов, позволяющим герметизировать вращающийся вал относительно неподвижного корпуса и разделить две среды. Данные уплотнения устанавливаются в камеру уплотнения (сальниковую камеру). Они сокращают утечки до минимума или полностью предот-
243
вращают их. Начиная с середины ХХ века торцовые механические уплотнения успешно конкурируют с сальниковыми уплотнениями. В табл. 12 приведены среднестатистические сведения о потерях рабочей среды в насосах в зависимости от типа уплотнения вращающегося вала. По данным табл. 12 видно, что торцовые уплотнения позволяют обеспечивать наилучшие показатели по герметизации вращающегося вала насоса.
|
|
Таблица 12 |
|
Потери жидкости через уплотнения насосов |
|||
|
|
|
|
Тип уплотнения |
Утечки, л/ч |
Потери, м3/год |
|
Сальниковое |
3...5 |
25...42 |
|
Торцовое, с кольцом из сальнико- |
0,1...0,25 |
0,9...2 |
|
вой набивки |
|||
|
|
||
Торцовое, с кольцами из твердых |
0,002...0,035 |
0,02...0,3 |
|
антифрикционных материалов |
|||
|
|
Применение торцового уплотнения взамен сальниковой набивки также способствует:
•защите насосного оборудования от повреждений;
•предотвращению разливов перекачиваемой среды через уплотнение, заражению местности ядовитыми и токсичными веществами;
•предотвращению потерь продукта перекачки через уплот-
нение;
•предотвращению повреждений от взрывов и пожаров объектов, находящихся в технологической цепочке с насосным оборудованием на насосных станциях (трубопроводы, емкости, печи, строения);
•значительному уменьшению сил трения в камере уплотнения, соответственно затрат на электроэнергию;
•уменьшению расходов, связанных со штрафами, больничными листами, отвлечением высококвалифицированного персонала на расследование и устранение последствий аварий;
244
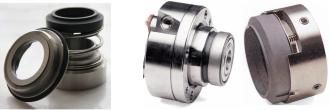
•повышению квалификации рабочего и инженерно-техническо- го персонала.
В зависимости от условий эксплуатации, параметров перекачиваемой среды торцовые уплотнения различаются по типам и модификациям. Различают следующие типы торцовых уплотнений:
•одинарное торцовое уплотнение;
•двойное торцовое уплотнение;
•одинарное картриджное уплотнение;
•двойное картриджное уплотнение;
•торцовое газовое уплотнение.
Наиболее распространенными являются одинарные торцовые уплотнения (рис. 98), непосредственно разделяющие атмосферную и перекачиваемую среду. Разнообразие конструкций и исполнение по материалам определяется назначением гидромашины.
Рис. 98. Одинарные торцовые уплотнения
Одинарное торцовое уплотнение применяется при перекачивании таких жидкостей, утечка которых в больших количествах во внешнюю среду недопустима. Это касается агрессивных, горячих, охлажденных, легкокипящих, органических и неорганических жидкостей. Этот тип уплотнения требует высокой точности изготовления, в том числе шлифовки и протирки торцовых уплотняющих трущихся поверхностей до шероховатости 0,01...0,15 мкм с зазором
не более 1,0 мкм. Внешние утечки при этом уплотнении минимальны.
В одинарном торцовом уплотнении используются основное уплотнение и вспомогательные (подвижные и неподвижные) уплотне-
245
ния, которые находятся в контакте с уплотняемой средой, позволяя вращающемуся элементу пройти через камеру уплотнения.
Основное уплотнение – это пара трения двух колец: подвижного и неподвижного. Для обеспечения необходимого контакта между подвижным и неподвижным кольцами применяется пружина или упругий сильфон. В процессе эксплуатации на торцовые поверхности действуют гидравлические силы, которые при избыточном давлении уплотняемой среды стремятся сжать пары трения, что увеличивает тепловыделение.
Вспомогательные подвижное и неподвижное уплотнения комплектуются резиновыми кольцами и герметизируют все стыки торцового соединения с корпусом механизма и вала в камере уплотнения. Неподвижное вспомогательное уплотнение, как правило, герметизирует неподвижное кольцо с корпусом механизма и подвижное кольцо с валом. Подвижное вспомогательное уплотнение обеспечивает уплотнение между подвижным кольцом и валом или корпусом торцового уплотнения. Рабочая подвижность этого уплотнения зависит от точности изготовления подвижного кольца, торцового биения неподвижного кольца относительно вала (не превышает 0,2 мм)
и внешних сил, стремящихся раскрыть уплотнение.
Утечка в стыке уплотнительных колец зависит от статического зазора между этими кольцами, геометрии колец, вибрации, режима эксплуатации, внешних сил, раскрывающих кольца, правильности монтажа, свойств уплотняемой среды.
В торцовых уплотнениях используются стали черные (коррози- онно-стойкие), спецстали (хладостойкие, термостойкие, жаростойкие) и неметаллические материалы – графиты, резины, фторопластсодержащие материалы (флубоны, чистые фторопласты), герметики, минералокерамика.
Для изготовления корпусных и других деталей используются в основном металлы: стали марок 40, 20Х13, 30Х13, 40Х13, 95Х18, 12Х18Н10Т, 10Х17Н13М2Т, 06ХН28МДТ, ХН65МВ, 36НХТЮ; ти-
тан ВТ1-0, а также другие материалы.
246
Подвижное и неподвижное кольца изготавливают из различных материалов: углеграфитов, металлов, карбидов (карбид вольфрама со связками, карбид кремния), керамики (окислы металлов – Al2O3), пластмасс. Кольца могут быть из одного материала или из сочетания различных материалов, например, нержавеющая сталь – углеграфит, керамика – углеграфит.
В отечественной практике для изготовления колец трения используются антифрикционные углеродные материалы, такие как: графиты типа АО – углеродные обожженные с пропиткой, графитированные с пропиткой типа АГ. Появились новые марки графита группы ЕК, РК, РГ; композиции фторопласта-4 с добавками кокса или углеродистого волокна, например, Ф4К20, Ф4УВ15; металлические 40Х13, 95Х18 с термообработкой до твердости более 40 единиц НRC; минералокерамика ЦМ-332, силицированные материалы СГП, СГТ, СГМ, ГАКК 55/40, БСГ, твердый сплав ВК8 и карбиды вольфрама, карбидокремниевые материалы, например, SILKAR, ROCAR.
Углеродные антифрикционые материалы химически стойки во многих агрессивных средах: почти во всех кислотах, растворах солей, органических растворителях; ограниченно стойки в концентрированных растворах едких щелочей при высоких давлениях и температурах. Они работоспособны в условиях сухого, полусухого и жидкостного трения.
Преимущество графитовых материалов – это широкий диапазон рабочих сред: нефть, нефтепродукты, растворы органических и неорганических соединений, жидкие газы, пищевые продукты; работа без смазки, широкий диапазон температур, высокие антифрикционные свойства и теплопроводность, хорошая механическая прочность и износостойкость, высокая химическая стойкость к агрессивным средам.
Для изготовления вторичных уплотнительных элементов используются резины разных марок, отличающиеся по своим характеристикам. За последнее время появился целый ряд новых марок ре-
зин, таких как СБ-26, СБ-26М, СБ-26Ф, СБ-26ТФ, ПСБ-26,
ИЭ 06-02. Для производства уплотнительных деталей нефтегазодобывающих и нефтехимических производств созданы резины серий
247
Н-180, Н-260 и Н-400 на основе бутадиен-нитрильных каучуков раз-
ной полярности (соответственно |
СКН-18, СКН-26 и СКН-40 по |
ТУ 2512.003.45055793–98). Они |
предназначены для изготовления |
резиновых колец и манжет. От серийных аналогов отличаются расширенным температурным диапазоном, повышенным сопротивлением накоплению остаточной деформации, а антифрикционные варианты – большей износостойкостью.
Силицированный графит, состоящий из карбида кремния, углерода и кремния, обладает высокой эрозионной и коррозионной стойкостью, износостойкостью, жаростойкостью, стойкостью к многократным сменам температуры и агрессивным средам. Узлы трения из силицированного графита работоспособны при температурах до 350 °C, удельных давлениях до 15 МПа и скоростях скольжения до
100 м/с. Изделия из силицированного графита стойки к агрессивным
средам, таким как соляная, уксусная, фосфорная, серная, азотная, муравьиная, плавиковая кислоты, расплаву капролактама, метилхлориду, этилацетату и уксусному ангидриду.
БСГ – боросилицированный графит, отличается повышенной теплостойкостью. ГАКК 55/40 – материал, состоящий из углерода, кремния, карбида кремния и добавок алюминия, отличается высокой стойкостью к щелочам.
Карбид кремния SILKAR по сравнению с силицированными графитами значительно больше содержит карбида кремния и меньше углерода по массе. Он обладает значительно более высокой прочностью, повышенным модулем упругости и коэффициентом теплопроводности. Его износостойкость в 2…3 раза выше, чем у СГП.
ROCAR по свойствам близок к материалам типа SILKAR.
РКК (реакционно спеченный карбид кремния) отличается высокими эксплуатационными характеристиками: эрозионной, термической и химической стойкостью, надежностью и долговечностью, прочностью, твердостью, высоким модулем упругости, низким коэффициентом линейного термического расширения, высокой теплопроводностью и превосходными трибологическими свойствами.
248

Минералокерамика ЦМ 332 имеет высокую стойкость ко многим химически активным средам, но обладает существенным недостатком – низкой устойчивостью к смене температуры и хрупкостью.
Двойное торцовое уплотнение (рис. 99) отличается от одинарного тем, что состоит из двух притертых уплотняющих поверхностей и специального подвода промывной (затворной) жидкости на проток.
Назначение этой жидкости – промыть первичное торцовое уплотнение от уплотняемой жидкости с целью предотвратить ее попадание во внешнюю среду, промыть пер-
вичное торцовое уплотнение от твердой фазы уплотняемой среды, уравновесить (запереть) и гидравлически разгрузить первичное торцовое уплотнение.
Двойные торцовые уплотнения применяются в основном для герметизации внутренних полостей гидромашин с химически активными, взрывоопасными и легковоспламеняющимися жидкостями. Эти уплотнения конструктивно исполняются «спина к спине» («back- to-back»), «лицом к лицу» («face-to-face») и тандемом.
В двойных уплотнениях (компоновка «спина к спине») давление затворной жидкости должно быть на 0,15...0,20 МПа выше давления
перекачиваемой жидкости, чтобы при выходе из строя уплотнения первой ступени перекачиваемая среда не попала в атмосферу.
Вуплотнениях типа «тандем» давление затворной жидкости
вбольшинстве конструкций равняется атмосферному. Циркуляция происходит за счет разности температур затворной жидкости и (или) с помощью встроенного в уплотнение импеллера. В случае разгерметизации основного уплотнения перекачиваемая среда попадает в затворную жидкость, увеличение ее уровня в бачке сигнализирует об аварийной ситуации.
Картриджная конструкция торцового уплотнения легко монтируется, что уменьшает возможность ошибки при его установке, и позволяет снизить затраты на монтаж и обслуживание. Возможна раз-
249
грузка уплотнения, обеспечение произвольного направления вращения вала, наличие встроенного холодильного агрегата.
Картриджные одиночные сильфонные торцовые уплотнения предназначены для уплотнения химически агрессивных жидкостей, с температурой среды до 425 °C.
Картриджные двойные сильфонные торцовые уплотнения предназначены для уплотнения горючих и легко воспламеняющихся химически агрессивных жидкостей, с температурой среды в зоне работы уплотнения до 425 °C. Двойные торцовые уплотнения сильфон-
ного типа могут работать как в двойном режиме (давление запирающей жидкости больше давления в камере уплотнения), так
ив тандемном режиме (давление запирающей жидкости меньше давления в камере уплотнения). Главным элементом таких торцовых уплотнений является сварной сильфон. Благодаря применению сильфонов, в конструкции торцового уплотнения не требуются резиновые вторичные уплотнения, что существенно расширяет температурный диапазон торцового уплотнения. По сравнению с торцовыми уплотнениями с пружинами сильфон отличается большей стойкостью к закоксовыванию и зависанию. Сильфонные торцовые уплотнения являются разгруженными, что уменьшает теплообразование.
Двойное картриджное уплотнение, как и двойное торцовое уплотнение, конструктивно исполняется «спина к спине» («back-to- back»), «лицом к лицу» («face-to-face») и тандемом.
Торцовые газовые уплотнения (газодинамические бесконтактные уплотнения) являются дальнейшим развитием торцовых механических уплотнений. Применяются с середины 80-х годов ХХ века. Конструкция газового уплотнения соответствуют обычному торцовому уплотнению с тем отличием, что поверхности скольжения шире
исмазываются не жидкостью, а газом. Принцип действия основан на создании тонкой газовой прослойки между кольцами торцового уплотнения при зазоре около 3 мкм. Стабильная газовая пленка в уп-
лотнительном зазоре возникает даже при минимальной скорости вращения. Газовый затвор образуется благодаря специальным V- или U-образным карманам с толщиной, сопоставимой с толщиной торцо-
250