
книги / Материаловедение.-1
.pdfТемпературы, при которых происходят фазовые превращения, называются критическими точками. Они обозначаются буквой А с индексами: с – для нагрева, r – для охлаждения. Характеристика основных критических точек железоуглеродистых сплавов в равновесном состоянии приведена в табл. 2.
Таблица 2
|
|
Критические точки |
|
|
|
Обозначение |
Линия |
Превращение |
диаграммы |
||
Ac1 |
PSK |
Превращениеперлитаваустенит |
Ar1 |
PSK |
Превращениеаустенитавперлит |
Ac3 |
GS |
Полныйпереходструктурыдоэвтектоидныхсталей |
|
|
ваустенит(конецпревращенияферритаваустенит) |
Ar3 |
GS |
Началопревращенияаустенитавферритвдоэвтекто- |
|
|
идныхсталях |
Acm |
ES |
Полныйпереходструктурызаэвтектоидныхсталей |
|
|
ваустенит(конецрастворения цементитаваустените) |
Arm |
ES |
Началовыделенияцементитаизаустенитавзаэвтек- |
|
|
тоидныхсталях |
|
|
|
Пример. Описать превращения и построить кривую охлаждения для сплава, содержащего 4,3 % углерода.
Решение. Сплав, содержащий 4,3 % С, – эвтектический белый чугун. Данный сплав кристаллизуется при эвтектической температуре изотермически с образованием ледебурита, т.е. с одновременным выделением двух фаз: аустенита состава точки Е и цементита. При дальнейшем охлаждении концентрация углерода в аустените изменяется по линии ES вследствие выделения вторичного цементита и к температуре эвтектоидного превращения принимает значение 0,8 % С. При температуре линии PSK аустенит в ледебурите претерпевает эвтектоидное превращение в перлит. Таким образом, во время охлаждения расплава, содержащего 4,3 % С, в нем протекают следующие реакции:
1) Ж4,3 → Л4,3 (А2,14 + Ц6,67);
31
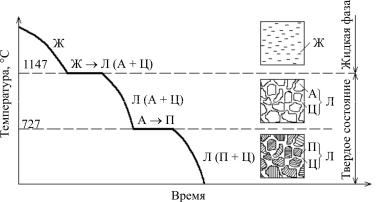
2)А2,14 → 0,8→ Ц6,67;
3)А0,8→ П0,8 (Ф0,02 + Ц6,67).
Кривая охлаждения данного сплава с иллюстрацией поэтапногоформированияструктурыприведенанарис. 13.
Рис. 13. Превращения в эвтектическом чугуне
Диаграмма состояния железо – цементит имеет большое практическое значение. Ее применяют для назначения режимов термической обработки и горячей обработки давлением железоуглеродистых сплавов, используют в литейном производстве для определения температуры плавления. Кроме того, диаграмма дает представление о структуре и фазовом составе любого сплава при различных температурах. Поскольку свойства всех составляющих известны, то, зная структуру и фазовый состав, можно прогнозировать механические и технологические свойства сплавов.
32
ТЕМА 5. ПРЕВРАЩЕНИЯ В СТАЛЯХ ПРИ НАГРЕВЕ И ОХЛАЖДЕНИИ
Воснове теории термической обработки лежат фазовые
иструктурные превращения, протекающие в сталях при нагреве
иохлаждении. Целью нагрева является получение аустенита, а основным превращением – превращение перлита в аустенит, поскольку в структуре всех сталей в исходном состоянии присутствует перлит. Превращение идет по реакции
Ф0,02 + Ц6,67→ А0,8.
В доэвтектоидных сталях после исчезновения перлита при нагреве от точки Ас1 до Ас3 избыточный феррит превращается в аустенит. В заэвтектоидных сталях в интервале температур Ас1–Асm избыточный цементит растворяется в аустените. Выше температур Ас3 и Асm идут только процессы гомогенизации и роста зерна аустенита. От размера зерна аустенита зависят механические свойства стали, главным образом ударная вязкость, которая значительно понижается с увеличением размера его зерна. Таким образом, при назначении температуры нагрева необходимо учитывать склонность к росту аустенитного зерна для конкретной стали.
При охлаждении аустенит не сохраняется и претерпевает превращение. При этом в зависимости от скорости охлаждения могут протекать два превращения: аустенита в феррито-карбид- ную смесь (ФКС) или аустенита в мартенсит. Чем больше скорость охлаждения, тем дисперснее структура ФКС. Если при охлаждении подавляется диффузионная подвижность атомов, то происходит мартенситное превращение. Такое влияние скорости охлаждения связано с тем, что с увеличением скорости охлаждения аустенит может переохлаждаться до более низких температур. Чем больше скорость охлаждения, тем больше степень
33

переохлаждения, меньше диффузионная подвижность атомов железа и углерода и ниже действительная температура превращения аустенита. Таким образом, важнейшим фактором, влияющим на механизм и кинетику превращения аустенита при непрерывном охлаждении, а также на строение и свойства получающихся продуктов превращения, является степень переохлаждения аустенита.
Аналогичная зависимость характерна и для режимов изотермического охлаждения. Каждой действительной температуре изотермической выдержки соответствует определенное время начала и конца превращения (рис. 14). Диаграммы изотермического превращения аустенита для всех сталей приведены в справочниках, и с их помощью можно прогнозировать результаты обработки, т.е. определять структуру и твердость после конкретного режима охлаждения.
Рис. 14. Изометрическая диаграмма распада переохлажденного аустенита эвтектоидной стали: П – перлит; С – сорбит; Т – троостит; Б – бейнит; А – аустенит; ФСК – феррито-карбидная смесь
Пример. На диаграмму изотермического превращения аустенита для эвтектоидной стали, содержащей 0,8 % С, нанесите кривую изотермической обработки, обеспечивающей получение твердости 150 НВ. Укажите структуру после охлаждения.
34
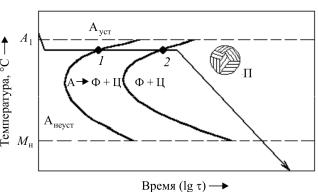
Решение. Для получения заданной твердости 150 НВ эвтектоидную сталь после аустенитизации необходимо охладить до температуры немного ниже критической точки А1 и выдержать при данной температуре для полного завершения превращения аустенита в феррито-цементитную смесь (рис. 15). Во время выдержки превращение начнется в момент времени, соответствующий точке 1, а закончится в точке 2. Структура, получаю-
щаяся при малой степени переохлаждения ( T = А1 – Tизотерм), имеет крупнопластинчатое строение и называется перлитом.
Время выдержки после завершения превращения и скорость последующего охлаждения на формирование структуры не влияют.
Рис. 15. Схема изотермического превращения эвтектоидной стали
Для условий непрерывного охлаждения существуют специальные термокинетические диаграммы, однако можно пользоваться и обычными изотермическими диаграммами, если на их поле нанести термические кривые охлаждения. Точки пересечения кривых охлаждения с линиями диаграммы показывают температуру ивремя распада аустенита на ФКС. При охлаждении со скоростью больше критической Vкр аустенит превращается в мартенсит по бездиффузионному механизму иФКСнеобразуется.
35
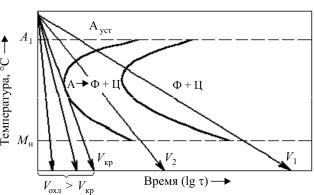
Пример. На диаграмме изотермического превращения аустенита для эвтектоидной стали покажите диапазон скоростей охлаждения, при которых получается мартенситная структура.
Решение. Для получения мартенситной структуры необходимо охлаждать с такой скоростью, чтобы подавить диффузионный распад аустенита на ФКС. Такая скорость охлаждения называется критической скоростью. При охлаждении со скоростью V1 (рис. 16) аустенит полностью распадается на феррит и цементит. Если охлаждать со скоростью V2, то часть аустенита превращается в мартенсит. При охлаждении со скоростью Vкр кристаллы феррита и цементита вообще не образуются и аустенит претерпевает мартенситное превращение. Дальнейшее увеличение скорости охлаждения уже не приводит к образованию каких-либо новых структур, кроме мартенсита. Таким образом, для получения мартенсита эвтектоидную сталь после аустенитизации необходимо охлаждать со скоростью больше критической: Vохл > Vкр. На практике из всех возможных скоростей охлаждения выбирают наименьшую, чтобы снизить уровень остаточных напряжений, неизбежно возникающих во время превращения аустенита в мартенсит.
Рис. 16. Кривые охлаждения эвтектоидной стали на диаграмме изотермического распада переохлажденного аустенита
36
ТЕМА 6. ОСНОВНЫЕ ВИДЫ ТЕРМИЧЕСКОЙ ОБРАБОТКИ СТАЛЕЙ
Различают предварительную и окончательную термическую обработку. Целью предварительной обработки является устранение нежелательных последствий от предыдущих технологических операций, а также подготовка структуры металла к окончательной термической обработке. Так, например, для уменьшения остаточных напряжений, измельчения зерна, снижения твердости перед правкой или обработкой резанием стальные заготовки (горячекатаные полуфабрикаты, поковки, штамповки, отливки) отжигают или нормализуют.
Для получения требуемых эксплуатационных свойств в дальнейшем проводят специальное термическое упрочнение, которое состоит из закалки и последующего отпуска. Температуру нагрева при всех видах термической обработки назначают с учетом критических точек (рис. 17), а охлаждение проводят с такой скоростью, чтобы получить заданную структуру и свойства. На практике применяют охлаждение с печью (отжиг), на спокойном воздухе (нормализация), в минеральном маслеиливводе(закалка).
Пример. Для того чтобы в эвтектоидной стали (0,8 % углерода) получить перлитную структуру с твердостью 150 НВ, необходимо после аустенитизации провести изотермическое охлаждение свыдержкой при температуре немного ниже точки А1. Как называется такой вид термической обработки? Можно ли такую же структуру и твердость получить другим способом? Как увеличить твердость стали?
Решение. Режим термической обработки, включающий аустенитизацию и последующее изотермическое охлаждение при температуре, обеспечивающей образование перлита, называется
изотермическим отжигом (рис. 18). Твердость 150 НВ опре-
деляется строением перлита, который получается при сравнительно высокой температуре (вблизи точки А1). Толщина
37
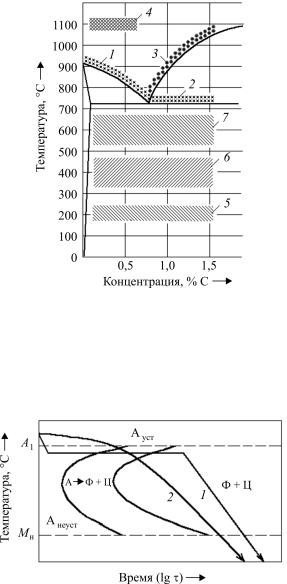
Рис. 17. Диаграмма состояния с интервалами нагрева углеродистых сталей: 1 – отжиг, нормализация, закалка доэвтектоидных сталей; 2 – отжиг, закалка заэвтектоидных сталей; 3 – нормализация заэвтектоидных сталей;
4 – диффузионный отжиг; 5 – низкий отпуск; 6 – средний отпуск; 7 – высокий отпуск
Рис. 18. Отжиг эвтектоидной стали: 1 – при изотермической выдержке; 2 – при непрерывном охлаждении
38
пластинок феррита и цементита, составляющих эвтектоидную смесь (перлит) зависит от скорости диффузии атомов, следовательно, от температуры превращения. Межпластиночное расстояние в перлите, образующемся при температуре 727–650 °С, составляет 0,5–0,7 мкм. Чем больше степень переохлаждения аустенита, тем дисперснее получающаяся ФКС и, как следствие, выше твердость. Структура, образующаяся в интервале температур 650–600 °С, называет-
ся сорбитом, 600–500 °С – трооститом, ниже 500 °С –
бейнитом (игольчатым трооститом).
Структуру перлита, обладающую минимальной для данной стали твердостью, можно получить и другим способом – непрерывным охлаждением с температуры аустенитизации. При этом скорость охлаждения должна быть такой, чтобы распад аустенита происходил при малой степени переохлаждения. Это возможно, например, при очень медленном охлаждении (вместе с печью), т.е. при проведении обычного (неизотермического) отжига. Увеличение скорости непрерывного охлаждения равноценно понижению температуры при изотермическом охлаждении. В связи с этим феррито-карбид- ная смесь, образующаяся в стали при нормализации, всегда более мелкая, чем при отжиге, а твердость – выше. Наибольшую твердость имеет мартенситная структура, которую можно получить только при проведении закалки.
Мартенситное превращение при закалке сталей, в отли-
чие от перлитного превращения при отжиге и нормализации, имеет бездиффузионный характер. При быстром охлаждении углерод не успевает выделиться из твердого раствора (аустенита) в виде частичек цементита, как это происходит при образовании перлита, сорбита и троостита. В этом случае происходит только перестройка кристаллической решетки γ-железа в решетку α-железа. Известно, что α-железо способно растворять очень небольшое количество углерода (до 0,02 %), в то же время в мартенсите всегда сохраняется столько углерода, сколько его содержится в аустените, поэтому мартенсит является пересыщенным по углероду α-твердым раствором. Чем больше кон-
39
центрация углерода в мартенсите, тем выше твердость закаленной стали. Так, например, для стали с содержанием 0,4 % углерода твердость мартенсита составляет 52–54 HRC, а для стали, содержащей 1,0 % углерода, – 62–64 HRC. Мартенсит имеет характерное игольчатое строение. При правильно проведенной закалке кристаллы мартенсита получаются очень мелкими. Мартенсит перегретой стали– крупнокристаллический, с повышенной хрупкостью.
Пример. Можно ли получить мартенсит в чистом железе? Решение. В общем случае мартенситом называют структуру, получен-
ную при бездиффузионной (сдвиговой) перестройке кристаллической решетки, поэтому мартенсит можно получить не только в железоуглеродистых сплавах. Для осуществления мартенситного превращения железо необходимо нагреть до температуры выше 911 °С, при этом образуется γ-железо с решеткой ГЦК, а затем очень быстро охладить (со скоростью больше критической). Мартенсит в чистом железе не содержит углерода, поэтому его твердость ниже, чем у любой стали. Однако по сравнению со структурой, полученной при медленном охлаждении железа, когда перестройка решетки
γ → α идет по нормальному механизму, мартенсит имеет более высокую твердость (28–30 HRC). Это связано с тем, что, как и в сталях, при образовании мартенсита значительно увеличивается плотность дислокаций (с 106–107 см–2 в равновесном состоянии до 1010–1012 см–2 после закалки). Повышенная плотность дислокаций является основной причиной упрочнения при образовании мартенсита; углерод дополнительно увеличивает твердость и прочность закаленных сталей.
Для превращения аустенита в мартенсит характерно то, что оно не идет в изотермических условиях, а происходит в интервале температур. Начинается превращение при температуре МН, а заканчивается при более низкой температуре МК (рис. 19), поэтому после закалки в структуре сталей наряду с мартенситом может присутствовать остаточный аустенит, особенно в высокоуглеродистых сталях (до 15 % Аост). Избавиться от остаточ-
40