
книги / Электронно-лучевая обработка в сварке
..pdf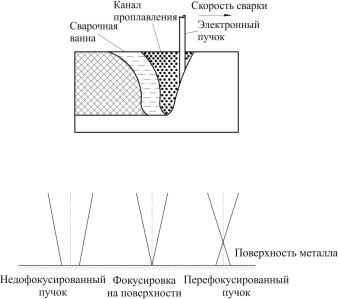
Зона максимального поглощения энергии располагается под поверхностью материала, что обеспечивает перегрев этой зоны, который не компенсируется отводом тепла теплопроводностью. В области перегрева возникает высокое давление паров металла и при большой концентрации мощности пучка происходит выброс перегретого металла. Эти процессы приводят к формированию в сварочной ванне канала проплавления практически на всю ее глубину (рис. 2.3).
Рис. 2.3. Канал проплавления, образуемый в металле при электронно-лучевой сварке
Рис. 2.4. Фокусировка электронного пучка при электронно-лучевой сварке
При электронно-лучевой сварке не вся подводимая с электронным пучком энергия непосредственно используется для процесса сварки. Существенные потери ее обусловлены отражением электронов.
На конфигурацию сварного шва существенно влияет фокусировка электронного пучка. Если фокус расположен над поверхностью детали, то пучок называют перефокусированным, а если фокус
31
расположен под ней, – недофокусированным (рис. 2.4). Положение фокуса влияет на глубину, ширину проплавления, а следовательно,
ина их соотношение, и на форму проплавления. Кроме того, от положения фокуса зависят процессы образования наружной и корневой частей шва. Для получения максимальной глубины проплавления следует выбирать положение фокуса, соответствующее 0,5...0,75 этой глубины. Положение фокуса при сварке отражается
ина ряде свойств сварного шва, и особенно наклонности образования в металле усадочных раковин.
Качество сварного шва при электронно-лучевой сварке, как
ипри любом способе сварки плавлением, определяется совокупностью технологических и энергетических параметров процесса. Поддержание на требуемом уровне энергетических параметров процесса сварки обеспечивает при неизменных технологических условиях постоянство эксплуатационных параметров сварного соединения: геометрических размеров, структурных, прочностных и других показателей. Однако возможность формирования зоны проплавления
с уникальной «кинжальной» формой вступает в противоречие с достижением стабильных эксплуатационных параметров сварного соединения.
Нарушение оптимального режима электронно-лучевой сварки зачастую ведет к появлению в швах дефектов, причем даже на хорошо свариваемых материалах. Некоторые дефекты в швах на толстолистовых металлах классифицируются как дефекты формирования. Они встречаются при любых способах сварки плавлением и хорошо известны: непровары, подрезы, провисание шва, а также повышенное разбрызгивание. Возникают и другие, специфические, дефекты: корневые дефекты, протяженные полости в объеме шва, «срединные» трещины и отклонение шва от стыка из-за остаточных или наведенных магнитных полей. Корневые дефекты шва – наиболее распространенный вид дефектов, которые могут иметь место при сварке различных материалов толщиной более 5 мм в режиме несквозного проплавления металла в любом пространственном положении.
Корневые дефекты шва присущи всем способам сварки высококонцентрированными источниками энергии. Они заключаются
32
в непостоянстве глубины проплавления (корневая часть шва имеет пичковую структуру) и в наличии полостей или несплавлений в корневых пиках. Корневые дефекты имеют гидродинамическую природу образования и обусловлены особенностями переноса металла в сварочной ванне.
Протяженные полости встречаются при сварке сталей, титановых и алюминиевых сплавов толщиной более 15 мм. Срединные трещины имеют место лишь при сварке сталей.
Технологические приемы сварки применяются для улучшения качества шва и повышения производительности процесса электрон- но-лучевой сварки. Эти приемы целесообразно разделить на три группы. К первой отнесены наиболее изученные и апробированные приемы: формирование шва с обязательным проплавлением; развертка и модуляция тока пучка; подача присадочного материала; сварка смешенным и расцепленным пучком. Вторая группа включает достаточно изученные и обоснованные приемы, но не получившие широкого применения, – тандемную сварку и сварку в узкую разделку. К третьей группе относятся приемы, целесообразность или возможность реализации которых либо не обоснованы, либо обоснованы недостаточно: осцилляция уровня фокусировки пучка; применение флюсов; двусторонняя сварка. Рассмотрим наиболее освоенные приемы.
Проплавление свариваемого стыка – наиболее надежный и простой способ, позволяющий исключить корневые дефекты, свести к минимуму угловые деформации, уменьшить вероятность образования пор и раковин благодаря улучшению условий дегазации металла сварочной ванны. При сварке в нижнем положении данный прием применяется для соединения металлов толщиной до 40 мм, а при сварке горизонтальным электронным пучком – до 400 мм. В последнем случае для предотвращения вытекания жидкого металла из сварочной ванны иногда устанавливается ограничительная планка вдоль нижней кромки стыка.
Развертка электронного пучка осуществляется с использованием следующих траекторий: Х-образной, по окружности, эллипсу, дуге. Эффект от развертки проявляется в изменении мгновенного
33
иусредненного по периоду распределения плотности мощности электронного пучка. Соответственно меняются характер гидродинамических процессов и конфигурация сварочной ванны. Благодаря этому при сварке металлов больших толщин удается резко расширить диаметр и повысить устойчивость канала в сварочной ванне, что благоприятно сказывается на стабильности формирования швов: уменьшается разбрызгивание расплавленного металла, предотвращается вытекание расплава из ванны при сварке горизонтальным пучком. Вследствие изменения формы шва уменьшается склонность к образованию трещин и протяженных полостей.
Сварка наклонным электронным пучком применяется при большой толщине металла. При постоянном отклонении электронного пучка в направлении его перемещения по изделию имеет место благоприятная форма фронта кристаллизации, улучшаются условия дегазации расплавленного металла при сварке в нижнем положении
иобеспечивается отток жидкого металла из глубины ванны при сварке на подъем. Экспериментально установлено, что угол отклонения пучка должен составлять 5...7°. Такой прием позволяет уменьшить количество пор и несплошностей.
Модуляция тока электронного пучка применяется для уменьшения тепловложения при сварке тонколистовых (до 1 мм) материалов, а также осуществления точечной сварки. При шовной сварке частота импульсов и скорость сварки выбираются так, чтобы отдельные проплавленные участки перекрывали друг друга. Модуляция пучка применяется для предотвращения образования трещин и обеспечения возможности сварки на весу тонкостенных деталей.
Сварка с присадкой применяется для легирования металла шва или восстановления необходимой концентрации легкоиспаряемых
элементов в шве и достаточно широко – |
при больших зазорах |
в стыке. |
|
Для непрерывной подачи в процессе |
сварки используются |
в качестве присадочного материала прутки, ленты, сплошная или рубленая проволока, гранулы и порошок. Наибольшее промьшленное применение получила сварка с подачей присадочной проволоки
34
диаметром 0,8...1,6 мм. Обычно проволоку вводят в сварочную ванну позади электронного пучка под углом 15...45° к его продольной оси. При этом режим подачи выбирается так, чтобы часть проволоки расплавлялась в жидком металле ванны, а часть – непосредственно электронным пучком.
Возможна подача присадочного материала и спереди электронного пучка. При этом присадочный материал может подаваться как непосредственно в сварочную ванну, так и укладываться на стык перед зоной сварки.
Зачастую между стыкуемыми поверхностями деталей помещается тонкий слой другого, переходного, материала в виде ленты, гранул или порошка, предназначенных для легирования металла шва. Слой переходного материала может быть также нанесен способами напыления, осаждения или наплавки на стыкуемые поверхности. Толщина слоя переходного материала в виде вставки должна быть равна диаметру электронного пучка, а в случае наплавки может достигать 10 мм. Такая разновидность приема позволяет осуществить наиболее однородное легирование металла шва.
При сварке на легирующей подкладке одновременно обеспечивается выведение корневых дефектов в подкладку. Равномерное легирование шва достигается благодаря интенсивному переносу жидкого металла из глубины ванны к ее поверхности. Толщина подкладки должна составлять не менее 20...25 % общей глубины шва.
Сварка с постоянным поперечным смещением электронного пучка ведется при наличии разнородных металлов в стыке. При этом пучок смещают от стыка в сторону более тугоплавкого металла. Величина смещения либо рассчитывается, либо определяется экспериментально.
Смещение электронного пучка применяется также в ряде случаев для компенсации его поперечного отклонения продольным магнитным полем, возникающим иногда при сварке разнородных металлов и сплавов.
Сварка «расщепленным» пучком позволяет одновременно сваривать отдельными точками или непрерывными швами два или более близкорасположенных стыка. При этом используется отклоне-
35
ние электронного пучка импульсным током прямоугольной формы, подаваемым в электромагнитную отклоняющую систему электронной пушки.
При шовной сварке период колебаний пучка выбирается из условия устойчивости канала проплавления в сварочной ванне, а время переброса пучка между стыками – из условия неоплавляемости поверхности изделия. В результате несовпадения оси отклоненного пучка и плоскости симметрии стыка такой прием можно применять только при сварке металлов малых толщин.
Тандемная и квазитандемная сварка также обеспечивают улучшенное формирование сварного шва. Тандемная сварка ведется одновременно двумя электронными пучками. Проплавление осуществляется основным пучком. Дополнительный пучок меньшей мощности направляется под небольшим углом к основному пучку в корень канала либо в хвостовую часть ванны. Тем самым можно достичь расширения нижней части канала либо удлинения хвостовой зоны ванны и ослабить влияние нерегулярности гидродинамических процессов в ванне.
Реализация квазитандемной сварки проще в аппаратурном плане. Функции основного и дополнительного электронных пучков выполняются одним и тем же пучком. С этой целью сварочный пучок периодически отклоняется так, чтобы занять положение дополнительного пучка, который используется при тандемной сварке. Отклонение пучка осуществляется дважды на разных уровнях. Распределение тепловложения в сварочную ванну регулируется соотношением времени существования основного и дополнительного электронных пучков.
Сварка в узкую разделку. Данный прием представляет собой многопроходную электронно-лучевую сварку. Сущность приема состоит в последовательной наплавке электронным пучком слоев присадочного материала в прямоугольной разделке хромок. Ширина указанной разделки в зависимости от толщины свариваемых металлов составляет 0,8...8 мм. Глубина разделки может быть неполной, в этом случае корневое соединение выполняется однопроходной электронно-лучевой сваркой. При сквозной разделке кромок
36
сварка ведется на подкладке из того же материала, что и соединяемые детали. Сварка выполняется в нижнем положении, непрерывно или с периодической остановкой процесса для охлаждения изделия. В качестве наплавляемого присадочного материала используется цельная или рубленая проволока.
Данный прием используется для соединения трудносвариваемых металлов толщиной до 200 мм. По сравнению с аналогичным способом дуговой сварки в узкую разделку электронно-лучевая сварка обеспечивает более высокую производительность процесса, меньшую ширину шва и лучшее качество металла шва.
Осцилляция уровня фокусировки пучка применяется для получения более равномерного распределения плотности мощности электронного пучка в его продольном направлении для уменьшения корневых дефектов и вероятности образования протяженных полостей. С этой целью в ряде случаев синхронно с осцилляцией уровня фокусировки осуществляют неглубокую модуляцию тока электронного пучка.
Двусторонняя сварка осуществляется путем одновременного проплавления электронным пучком двух противоположных сторон стыка с глубиной провара около половины толщины свариваемых деталей.
Одновременно сварку двумя электронными пучками можно осуществлять как с раздельными, так и общей ваннами. В последнем случае пучки направляются под углом друг к другу для исключения повреждения сварочных пушек проходящими частями пучков.
Этот прием применяют для обеспечения возможности элек- тронно-лучевой сварки изделий, более толстостенных, чем те, сварка которых обеспечивается имеющейся сварочной аппаратурой, а также во избежание дефектов шва, вероятность появления которых возрастает с увеличением глубины проплавления.
Кнедостаткам приема относятся внесение корневых дефектов
внесущую часть шва и дополнительное термическое воздействие на основной материал. При одновременной сварке двумя электронными пучками с общей сварочной ванной можно исключить корневые дефекты шва, но из-за перегрева ванны в области встречи пучков резко повышается вероятность образования трещин и раковин.
37
3. ОБОРУДОВАНИЕ ДЛЯ ЛАЗЕРНОЙ ОБРАБОТКИ МАТЕРИАЛОВ
3.1. Структурная схема лазерной технологической установки
Для обработки и сварки материалов используются твердотельные и газовые лазеры. Независимо от типа применяемого лазера и назначения лазерные технологические установки состоят из ряда аналогичных функциональных узлов и имеют общую структурную схему (рис. 3.1). Основным источником энергии, обеспечивающим процесс обработки, является оптический квантовый генератор (лазер). Лазерное излучение формируется оптической системой в пучок с определенными пространственными характеристиками и направляется на обрабатываемый объект. При помощи оптической системы могут осуществляться также визуальный контроль положения обрабатываемого объекта относительно луча, наблюдение за ходом процесса обработки и оценка его результата. В лазерной технологической установке имеется также устройство для обеспечения перемещения обрабатываемого объекта в процессе обработки. Некоторые процессы обработки требуют подачи в рабочую зону той или иной технологической среды, например инертного газа, для чего в установке может быть предусмотрено соответствующее устройство. Иногда для получения необходимых технологических эффектов в зону обработки вводят дополнительную энергию (механическую, электромагнитную и др.). Для этого применяется источник вспомогательной энергии.
Примерами комбинированных методов могут служить газолазерная резка, лазерно-электроискровая обработка и др. Установка может быть также укомплектована программным устройством, управляющим перемещением обрабатываемого объекта и излуче-
38
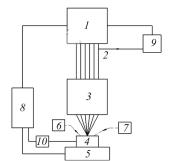
нием лазера. В технологической лазерной установке, как правило, имеются датчики контроля параметров излучения и параметров технологического процесса, таких как температура зоны обработки, состояние поверхности обрабатываемой детали, яркость свечения плазменного факела. Эти датчики могут использоваться как для контроля, так и для управления параметрами излучения лазера [3].
Рис. |
3.1. Структурная схема лазерной технологической установки: |
|
1 |
– |
оптический квантовый генератор (лазер); 2 – лазерное излучение; |
3 |
– оптическая система; 4 – обрабатываемый объект; 5 – устройство для |
перемещения обрабатываемого объекта; 6 – устройство для подачи защитного газа; 7 – источник вспомогательной энергии; 8 – программное устройство; 9 – датчик контроля параметров излучения; 10 – датчик
технологических параметров
3.2. Параметры лазерного излучения
Лазерное излучение характеризуется энергетическими и про- странственно-временными параметрами. Для импульсных лазеров основными параметрами являются энергия импульса, длительность импульса, скважность импульсов (при работе в частотноимпульсном режиме), частота следования импульсов, пиковая и средняя мощности.
Для твердотельных лазеров характерно существование нескольких режимов генерации излучения. Наиболее распространенными являются:
39
–режим хаотической генерации, при котором импульс лазерного излучения представляет собой набор отдельных «пичков» различной мощности продолжительностью около 1 мкс и следующих друг за другом с определенной скважностью;
–режим упорядоченной генерации, при котором мощность отдельных «пичков» почти одинакова;
–квазинепрерывный режим, характеризующийся отсутствием «пичков».
При модулировании добротности резонатора можно получить импульс большой мощности с длительностью порядка 10–8 с.
Частота следования импульсов f и скважность N соответственно равны:
f = |
1 |
, N = Tu |
, |
|
T |
||||
|
τ |
|
||
|
u |
u |
|
где Тu – период следования импульсов; τu – длительность импульса. Как для импульсных, так и для непрерывных лазеров важным параметром излучения, определяющим эффективность обработки, является длина волны лазерного излучения. Для современных лазерных систем, используемых для обработки материалов, длина волны излучения лежит в красной или инфракрасной области оптического спектра. Длина волны излучения определяет степень поглощения (отражения) лазерной энергии обрабатываемой поверхностью. С увеличением длины волны излучения отражательная спо-
собность большинства металлов возрастает (табл. 3.1).
|
|
|
Таблица 3.1 |
|
Значения коэффициента отражения некоторых металлов |
||||
|
|
|
|
|
Металл |
|
Длина волны, мкм |
|
|
0,7 |
1,06 |
10,6 |
||
|
||||
Алюминий |
0,87 |
0,93 |
0,97 |
|
Хром |
0,56 |
0,58 |
0,93 |
|
Медь |
0,82 |
0,91 |
0,98 |
|
Никель |
0,68 |
0,75 |
0,95 |
|
Серебро |
0,95 |
0,97 |
0,99 |
|
Сталь |
0,58 |
0,63 |
0,95 |
40